3D print tires
Michelin’s Uptis airless tire takes to the road with 3D printing
0Shares
The 2021 3D Printing Industry Awards shortlists are open for voting, have your say now.
French tire manufacturer Michelin has reached a new milestone in the development of its airless Uptis (Unique Puncture-proof Tire System) tire, having carried out successful road tests.
As part of Michelin’s VISION concept, if Uptis goes to market in 2024 as planned, drivers would be able to 3D print the tread and adapt the tires according to their driving, seasonal weather conditions, and to self-maintain the general health of the tire.
3D printing has already been used to create the prototype of the tire, however further details on the additive manufacturing technologies involved and the extent to which they will be used in the future, remain to be seen.
Michelin’s Uptis tire is airless to eliminate the risk of punctures. Photo via Michelin.An airless, biodegradable concept
Michelin first proposed the Uptis concept tire at its International Mobility Summit, Movin’On, in 2017. The tire was designed to be airless in order to eliminate punctures while being biodegradable and equipped with sensors for real-time monitoring.
The tire’s airless interior design is based on an alveolar structure such as that found in lungs, which feature intricate internal geometries suited to 3D printing. To create the prototype for the show, Michelin worked with automotive manufacturer General Motors to 3D print the concept tire.
Ultimately, Michelin is seeking to reduce the number of tires thrown away due to punctures, which, according to an in-house “scrapyard survey”, amounts to some two million tons, or 200 times the weight of the Eiffel Tower. The firm believes its Uptis tire could avoid this waste altogether thanks to its airless nature and “rechargeable” potential.
The tire’s “rechargeable” concept is the most interesting element of the design from an additive manufacturing perspective, and could see drivers reprint their tire treads by the roadside.
The Uptis tire is scheduled to come to the market in 2024.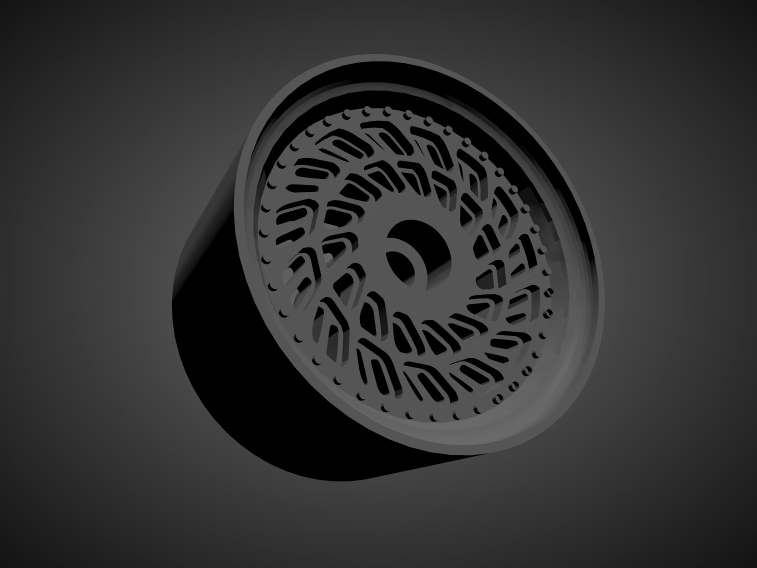
Uptis’ rechargeable tread
Through its VISION concept, Michelin is aiming to make mobility safer, cleaner, more efficient, and universally accessible. The concept demonstrates how the company’s sustainable development model hopes to transform tire manufacturing between now and 2050, the date by which the EU aims to be climate-neutral.
The four pillars of VISION are Airless, Rechargeable, Connected, and 100 percent Sustainable. To meet its Airless goal, Michelin is developing technology that eliminates the risk of flats and rapid pressure loss to improve safety and comfort, while reducing the environmental impact of tire wastage.
The Connected element of VISION sees the Uptis equipped with numerous sensors to usher in a “new era” of service, comfort, and safety for motorists, while its Sustainable pillar sees Uptis manufactured by biosourced and recycled materials in order to ensure the environmental footprint of the tire’s lifecycle is minimal.
Finally, and hailed by Michelin as one of the “most revolutionary” aspects of its VISION concept, is the Rechargeable commitment. According to the company, having a tire with a 3D printed tread makes it possible to deposit just the right amount of rubber compound, therefore reducing the use of raw materials.
The tire can subsequently be “recharged” using a 3D printer that reprints the tire tread according to the needs of motorists. For instance, drivers might want to adapt their tires to winter or summer conditions, or simply upkeep the general health of their tires as a result of wear and tear.
With 3D printing, Michelin says these adjustments could be made quickly and easily via an on-demand service that could see drivers 3D print new treads for their tires by the roadside. While further details are still to come regarding which 3D printing technologies would be used, and in what capacity, it seems 3D printed roadside repairs could become reality when the tire comes to the market in 2024.
Michelin already uses metal 3D printing to design and create multiple products, including the components of tire molds. Going forwards, the company will leverage this expertise further to explore rubber 3D printing to offer its recharging concept for tire treads.
The tire’s tread could be “recharged” using 3D printing. Photo via Michelin.Test driving the Uptis
The latest development in Michelin’s VISION has seen the Uptis transfer from concept to the road. Automotive YouTubers Mr. JWW and Gercollector were brought in to test the prototype Uptis in real-life conditions on public roads.
Both offered substantial praise for the tire, said Cyrille Roget, Michelin Group Technical and Scientific Communications Director: “Our greatest satisfaction came at the end of the demonstration when our passengers said they felt no difference compared with conventional tires.”
Subscribe to the 3D Printing Industry newsletter for the latest news in additive manufacturing. You can also stay connected by following us on Twitter and liking us on Facebook.
Looking for a career in additive manufacturing? Visit 3D Printing Jobs for a selection of roles in the industry.
Subscribe to our YouTube channel for the latest 3D printing video shorts, reviews and webinar replays.
Featured image shows Michelin’s Uptis tire is airless to eliminate the risk of punctures. Photo via Michelin.
Tags Cyrille Roget General Motors Gercollector Michelin Michelin Uptis Michelin VISION Movin'On Mr JWW
Hayley Everett
Hayley is a Technology Journalist for 3DPI and has a background in B2B publications spanning manufacturing, tools and cycling. Writing news and features, she holds a keen interest in emerging technologies which are impacting the world we live in.
Tires best 3D printer files・Cults
US Mags C-Ten 22"
€6.24
Centerline Billet Saber 18"
€4.80
Nova Restomod 19/20
€6.24
US Mags Slasher 22"
€6.24
LOSI SBR 2.0 - SNOW/SAND PADDLE TIRES - V2.0
€2.16
wheels volk racing
€1.59
Wheel Rims
Free
Toyo r888r Proxes Rims
€6 -20% €4.80
wheels bbs
€1. 59
1/24 18" Nismo LM GT4 with Yokohama style tire
€3.76
BORBET-T RIM
€4
313mm Wheelbase Tonka Winnebago Styled Body For RC
€26.66
BIG Bobby Car Classic Tyre -TPU -Silent
Free
DR!FT Racer Storm Child Porsche TS Master S1 Wheel Set
€4.99
1/18 TIRES 235X40 R17 FOR RIMS 17 INCH X 8,5J
€0.63
1/18 Tires 235x35 R18 for rims 18 inch x 8.5J
€0.63
DR!FT Racer storm child wheel set US classic
€2.99
DR!FT Racer Storm Child Wheel Set TS 5-Star
€2.49
Sturmkind DR!FT - Felgen - Rims 2-teilig
Free
TIRE REMOVAL MACHINE
€4. 80
Scx24 Beadlocks
€2.64
Spare Tire for TRX #3
€4.71
Spare Tire for TRX #2
€4.71
Spare Tire for TRX #1
€4.71
Spare Tires for TRX6 Three in one
€11.08
Budnik Groove 20/22"
€6.24
Chevy N96 Mag 19/20
€6.24
Buick Rally 19/20
€6.24
Rally Rims R/C scale 1/10
Free
Star Rims Type C R/C - Scale 1/10
Free
TIRE STORAGE BOX
Free
1/24 Tires 265x30 R21 for rims 21 inch x10J
€0. 63
1/24 Tires 265x30 R19 for rims 19 inch x10J
€0.63
Axial SCX6 Anti-Foams 2.9"
€9.61
Rc 1/8 Buggy Truggy Skipes for Tire and wheel
€1.33
1/24 Tires 325x25 R20 for rims 20 inch x 12J
€0.63
1/24 Tires 275x30 R20 for rims 20 inch x 10,5J
€0.63
1/24 Tires 255x35 R18 for rims 18 inch x 9,5J
€0.75
Small wheels and tires
Free
Landmaster Tri Star Wheels
€3.84
1/18 Tires 205x60 R15 for rims 15 inch x7J
Free
1/18 Tires 315x25 R22 for rims 22 inch x12,5J
€0. 63
1/18 Tires 305x25 R21 for rims 21 inch x12J
€0.63
1/18 Tires 265x30 R21 for rims 21 inch x10,5J
€0.63
1/18 Tires 265x30 R20 for rims 20 inch x10,5J
€0.63
1/18 Tires 255x30 R22 for rims 22 inch x10J
€0.63
1/18 Tires 255x30 R21 for rims 21 inch x10J
€0.63
1/18 Tires 255x30 R20 for rims 20 inch x10J
€0.63
3D printer in tire making.
Creativity
Subscribe to the author
Subscribe
Don't want
116
Many of my friends are still trying to convince me of the uselessness of a 3D printer, they say, 'well, you can print cubes, snakes, and all sorts of bushings and get bored'. But nifiga, not tired =). I found another use for a 3D printer in another detail.
A long time ago I made tires from silicone, by pouring into an epoxy matrix. About how the matrix was made is a completely different story.
Well, that's it. There is a 3D printer ... but, so that, I think not to print a matrix on it? Ay, yes.
We model the tire, cut the tread and in the halves of the matrix with the 'indent' element we make the drawings on it.
We make an insert between the halves to select an extra volume and make the tire profile.
Due to the specific shape of the insert, I made the supports myself. Width 0.3. I have long understood that in such models it is better to do supports yourself than to watch how the corners of the model lie between the grids / support lines (and this is on filling the support with 40% !sic)
A little background, to the current version:
Initially I tried to print a treadless donut with a selection inside. Everything worked out, the result pleased.
In the last one, I already decided to pour a solid tire with a transparent sealant. The thin profile turned out to be too thin and wrinkled a lot. But after pulling it out of the matrix, there were sprues on the tire, like on real tires =)
Something like a ship mine...
...let's return to the current upgraded tire model:
Dip the brush into the starch and smuggle the entire matrix. The starch will act as a separator. We mix silicone with starch
Put it into the mold and tighten it all with screws. Cool worms crawled out
Silicone with starch hardens (polymerizes) to moderate hardness in 40 minutes. It's always humid there. You can also pour water into it
The disk for the tire can be made in any shape you like, it all depends on the imagination. I made a simple blank and put a tire on it so that it would be fun to ride it all.
Of course, this tire is not reinforced and is not designed for high speeds. The speed was checked by touching the grinding wheel, the tire was already visually inflated at 4k rpm. There is an idea to make tires with sickle reinforcement, at least along the layer under the tread. Then it should be less inflated.
Small performance characteristics of tires:
- diameter - 70 mm
- weight - 37 g
- width 25 mm
- plastic left - 47m
) Kamaz model or similar.
Here is another use of a 3D printer in an intermediate stage and without the use of flex.
I bow out for this, I still have things to do =)
Loading
11/01/2022
5608
90
Follow the author
Subscribe
Don't want
For several years I have been working at the intersection of such genres as modeling and miniature and have contributed to this. ..
Read more
kenst69
Loading
11/13/2022
3439
39
Subscribe to the author
Subscribe
Don't want
Good time. Article for inspiration) In the process of printing, it is often necessary to process in every possible way...
Read more
300
Subscribe to the author
Subscribe
Don't want
Hi all!
For a long time I did not write on the Portal, because the Chukchi in the majority of their roles ...
Read more
3D printed medical splints help children breathe normally
Glen Greene, a pediatric otolaryngologist and researcher at the University of Michigan, has made significant strides in the use of 3D printing. Using a 3D printer, he makes custom-fitted small spacer splints to help babies born with airway defects breathe easier.
About one in 2,000 babies is born with weakened bronchi, which can collapse and prevent normal breathing. Fortunately, in most of these children, the disease resolves on its own by the age of three, as the airways develop and strengthen. However, if the bronchi are severely affected, it can be life-threatening for the child. That is why Green and his colleagues have developed a unique airway splint that is produced on a 3D printer. The splint is made from a special material that expands as the body grows and then dissolves when it is no longer needed.
In 2013, Green's team achieved their first success by applying their technology to help Kaiba Jonfrido. The boy, who was born with weakened bronchi, is already three years old, and he breathes perfectly on his own. The tire that helped him breathe gradually dissolves, as the scientists intended. After a successful experience with Kaiba, tires designed by Green were fitted to two more newborns and may have helped save their lives.
At the age of five months, Ian Orbich was in intensive care, and his breathing constantly stopped. Specialists in Pittsburgh no longer knew how to treat the boy, but his mother, Megan Orbich, read an article about research being conducted in Michigan and contacted Green. Fitting spacers inside Ian's airway failed, so Green worked with biomedical engineer Scott Hollister to design an external splint that attaches externally to widen the boy's airway.
To create custom splints, Green and Hollister measure each patient's CT scans and laser sinter tubes with holes on one side. The spacer is ready within a day, and the material from which it is created is biodegradable and begins to dissolve after about three years, just when the patient's airways are sufficiently strengthened. After the spacer is 3D printed, it is sterilized for surgery. Surgeons then place a splint on the weakened area of the airway and thereby widen it. Surprisingly, material costs for unique tires are only $10 a piece.
It is hoped that the resulting low cost of the material will also reduce the cost of the operation and make it accessible to more families. In addition to Kaiba and Ian, Green's team at the University of Michigan is working with another child, Garrett. The condition of all three patients has improved significantly, two of them are already living without mechanical ventilation. Ian still needs the procedure, but his mom is hopeful that the operation will continue to improve his condition. “He's holding up very well. This chance is just a miracle for us,” she says.
When it comes to small children, the time factor is especially important. Now that medical 3D printing is accessible through innovative materials and technologies, the possibilities are wide open. Green is very excited about the progress that the team of scientists has made.