The future of 3d printing in medicine and dentistry
The Future of 3D Printing in Medicine
Introduction
There has always been a desire to manifest ideas into physical objects, and three-dimensional (3D) printing has brought us closer than ever to that goal. Although 3D printing was conceptualized in the 1970s and has been available since the 1980s, it has not truly had as large an impact as it had in the last few years. This has been due to the price decrease in 3D printers and printers that are now produced commercially, which enables them to be used by an increasing number of people.
Early adopters of this technology were enthusiasts and finding people with technological experience in setting up and running 3D printers was challenging. As the printers became more user friendly, the amount of software developed to improve user experience adoption increased. 3D printing was found in health care, from researchers to front liner staff during COVID-related printing, which included items, such as protective equipment and other applications in various specialities that are found in the literature.
Although it has proven to be a valuable tool, the current technology has limitations in applications with printing time and materials that impact its practicality. In this article, an insight into the various 3D printing technologies currently available will be provided and some of the applications in various specialities of medicine will be discussed and how they impact current practice and future directions.
Technologies currently available for 3D printing
Subtractive
Computer numerical controlled (CNC) milling uses various tools, such as drills, routers, and lasers, to remove material from a solid object until the desired shape is obtained. This technology; however, has the disadvantage of creating complex internal structures.1
Additive
Multiple technologies are available, including:
Stereolithography (SLA) utilizes a laser to heat a liquid photopolymer substrate into a solid layer of the desired shape.2
Selective laser sintering (SLS) uses a laser to heat a solid powder, fusing it into a solid structure.
3
Fused deposition modeling (FDM) or fused filament fabrication (FFF) that utilizes spools of thermoplastic material extruded through a heated nozzle in layers along the z-axis into a 3D structure.4
Material jetting printers that place a thin layer of resin in the desired design, which is then immediately cured by powerful ultraviolet light before the next layer of material is added.5
Binder jet printing is an additive manufacturing process in which an industrial printhead selectively deposits a liquid binding agent onto a thin layer of powder particles, such as metal, sand, ceramics, or composites.6
Digital light processing (DLP) is similar to SLA; the difference is that SLA machines use a laser that traces a layer, whereas a DLP machine uses a projected light source to cure the entire layer at once.7
Continuous liquid interface printing (CLIP) uses photopolymerization to create smooth-sided solid objects of a wide variety of shapes using resins.
8
Medical specialities that have attempted to utilize 3D printing, due to its versatility, convenience, and low cost, include cardiology, plastic surgery, neurosurgery, and urology.
Applications of 3D printing in medicine
Medical education
Cadaveric teaching has been the gold standard, and 3D printing has been increasingly used in medical education across various fields. In a study by Zhen Ye et al., students in the 3D printed group had better learning satisfaction and advantages in accuracy and answering time compared with the outcomes of students in the conventional group.9
In orthopedics, 3D printed models have helped trainees practice their surgical maneuvers and that were prepared and more confident in a surgical theater.10 In addition, 3D models are being used as preoperative planning tools to try out various procedures and maneuvers for complex pathologies in spinal cases.11 In urology, 3D models and 3D printing have been used to simulate various procedures, such as percutaneous nephrolithotomy, partial nephrectomy, renal transplantation, laparoscopic pyeloplasty, prostate brachytherapy, transurethral resection of bladder tumors, ureterovesical anastomosis simulation devices, laparoscopic trainers, and robotic surgery phantoms. 12 The ability of 3D printers to provide on-demand models means that training institutes no longer have to rely on prefabricated models from various suppy chains, which makes the models an invaluable teaching tool. In addition, most models that were available were of normal anatomy, and pathological models were not very common; however, now real cases from Digital Imaging and Communications in Medicine (DICOM) files of real cases can be made into physical 3D models. This provides educators with the ability to have models of rare pathologies for demonstration in teaching. 3D printing in neurosurgical education encompasses a variety of neurosurgical subspecialties, including vascular, skull base, endoscopy, craniosynostosis, skull lesions or skull defects, intrinsic brain tumors, and others, with vascular and skull base specialities accounting for half of the 3D-printed models.13 In cardiac surgery, 3D models have been used to elucidate coronary heart disease (CHD) anatomy after cardiac surgery.
14 The models provided were used as an adjuvant to other teaching methods and helped to make the training experience more comprehensive for the trainees.
These are a few examples of the applications and specialities, and from the review of the literature, 3D printing was used in multiple specialities and has been used at undergraduate and postgraduate levels.
Patient care
From the literature, 3D printing is utilized at various points in patient care. In critical care, 3D printing is used in wound care, personalized splints, and patient monitoring.15
In dentistry, various technologies of printing and materials are utilized to create restorations (e.g., crowns, bridges, veneers, and partial denture frameworks or denture bases), physical models, surgical guides or implants, and orthodontic aligners or retainers.16 Dentistry is no stranger to 3D modeling and fabrication, and as early as the 1990s, people in the field were using wax to make models; therefore, making 3D printing a natural evolution in the field. Implant modeling and fabrication have been used for various reconstructive specialities, including maxillofacial surgery,17 neurosurgery for cranial implants,18,19 and plastic surgery to produce anatomic models, surgical cutting guides in reconstruction, and patient-specific implants.20 Orthopedic surgeons have found 3D printing useful in their practice for tasks from forming scaffolds to aid in bone repair,21 to forming patient-specific lightweight splints, implants, and biomodels.22 In addition, a wide range of prostheses have been 3D printed, which, although not necessarily low cost versus injection molding, provides a promising possibility for individualization and custom fitting.23
There are various applications for 3D printing in a variety of settings, including surgical and nonsterile patient care. The commercial availability of the technology has allowed individuals with knowledge of 3D computer-assisted design (CAD) and experience with 3D printing to utilize this important tool in their practice to enhance individualized patient care. These factors influence patient satisfaction directly and indirectly.18,19,24
Equipment modification or fabrication
3D printing is being utilized in various manufacturing industries, including the automotive industry. As the technology improves and printed parts are of better quality, with a wider range of printable materials, 3D printing has been incorporated into an increasing number of manufacturing processes. In a study carried out by the Metal Powder Industries Federation, the researchers compared the outcomes of 17 steps of subtractive manufacturing that were required to produce a truck gear versus 6 steps to achieve the same goal using additive manufacturing.25 Their research demonstrated that changes in the design of the materials used in subtractive manufacturing could improve reproducibility by additive manufacturing when maintaining the same function. These reductions could translate into more efficient and sustainable manufacturing in the medical industry.
The medical equipment industry is no stranger to 3D printing. The recent COVID-19 pandemic helped to overcome supply shortages in airway consumables, personal protective equipment,26 and nasopharyngeal swabs.27 A total of 22,135 items were manufactured were manufactured by 59 companies in 18 sectors to overcome problems in the global supply chain (e.g., airway consumables and personal protective equipment).26 In addition, the modification of medical equipment was possible due to the adoption of 3D printing,28 and these were modifications made by medical professionals rather than large corporations, which allowed more people to be innovative; therefore, driving medical innovations forward by allowing more personalized and cost-efficient solutions that helped to overcome previous obstacles, such as long procedure times, difficult modeling, and high cost.19
Making 3D printing mainstream allowed individuals innovate various fields of medical practice and produce prototypes that they could physically hold and study; this was seen in the advent of 3D printing for neurosurgical implants. 18,19 The production of customized wound dressings and even tissue printing for grafts29 could provide better solutions for patients. 3D printing could benefit medical equipment companies, because the price of 3D printing decreased and its efficiency and versatility increased. Manufacturers could open multiple manufacturing locations on hospital grounds, which required a smaller footprint than regular factories and required fewer employees. Moreover, ordering a custom implant could be as easy as having it designed in the headquarters and then printed remotely in the hospital that ordered it. The cost to set up one regular factory could fund hundreds of these in-hospital printing stations. The printing process, because it requires no molds or custom manufacturing equipment, would make it cost-effective to customize induvial medical implants and prosthetics and produce custom-fitted products without major changes to the production line.
In addition, 3D printing is revolutionizing the pharmacological industry toward the production of customized medicines; however, there is still a need to explore the aspects of cost, flexibility, and bioequivalence. 30 These aspects could open the door to customized drug delivery systems, on-demand manufacturing, and dose flexibility.31 Aprecia (Aprecia Pharmaceuticals - Corporate HQ, 10901 Kenwood Rd, Blue Ash, OH 45242) recognized the commercial potential of 3D printed pharmaceuticals early on and received US Food and Drug Administration (FDA) approval for its Spritam epilepsy medication in 2015. Since then, the company has collaborated with the non-profit R&D firm Battelle to increase manufacturing output and move its ZipDose 3D printing system from clinical supply to commercial sale.32 However, the printing time is long compared with the time required for methods such as injection molding, which require printing farms of multiple 3D printers to operate simultaneously. Printing failures are detrimental to the production line due to the long printing time, and the multiple 3D printers that are required for mass production increase the initial costs and cost per unit, which makes them useful for low-volume production (10-100 parts) but impractical in large-scale manufacturing.
33
3D printing and research
3D printing has been a topic of research and a tool to help research. Research into implants of various materials for maxillofacial,34 neurosurgical,18,19 and orthopedic35,36 studies are found in the literature. The availability of consumer-grade low cost 3D printers offset an otherwise large cost, which is another obstacle to this type of research, and allows more people to attempt similar studies as individuals rather than requiring studies to be conducted in large institutes and without substantial company funding; therefore, preventing bias.
Regarding tissue bioprinting, techniques such as inkjet printing, laser-assisted printing, extrusion, and cell electrospinning37 have been used to try to produce tissues from individual cells in an attempt to produce complex tissues or even organs. Significant research is ongoing into the 3D printing of tissues and organs. This might have multiple implications when positive results are reached. In pharmaceuticals, these printed models might help to study the organ effects of pharmaceuticals, which could overcome the high cost and ongoing controversy that surrounds animal testing.38 These organs could be used for tissue or organ regenerative engineering to help with the shortage and incompatibility of organ donors.39 In laboratories, 3D printing could be used in bioanalytical and diagnostic testing research,40 to help create extremely complex architectures that are similar to those of biosensor arrays, which were not readily available to the average laboratory in the pre-3D printing era. Printing of customized equipment and equipment modifications in laboratories could help to reduce costs and time compared with other fabrication methods.41
Models of diseased organs could be used for research into new surgical techniques or equipment to determine their efficacy and possible side effects. 42 3D-printed mannequins and radiological models have been used as phantom simulations for CT-guided procedures.43 As these models improve, and with the possible advent of tissue printing, these models might replace current methods for research. The availability of these models might drive research faster and further, because they might provide an alternative to human participants in the future.
Future directions
The use of 3D printing in medical applications has great promise for the future; however, significant barriers exist to successful implementation, regardless of scientific knowledge. The goal of research is to successfully 3D print organs for transplant, and soon there might be breakthroughs that allow autologous 3D printed organs that use a patient’s cells. However, 3D printing the complex cytoarchitecture of organs remains difficult. Furthermore, 3D printing could be used more as a teaching tool. For pharmacology, research into 3D printed patient-specific medicine is expected to expand, and companies, such as Curifylabs have developed an automated digital technology (Curify MiniLab) to 3D print medicines; however, the potential of multiple formulations in one tablet is unknown. For medical companies, research into modifying existing products to facilitate 3D printing, and expanding the range of materials that can be 3D printed, would be a logical direction for research, in addition to improvements in the efficiency and speed of 3D printing.
Conclusions
3D printing is an amazing and exciting tool and has had a significant impact on various industries over the last decade. Improvements in traditional techniques and research by incorporating newer and more efficient additive manufacturing methods could increase the utilization of this valuable tool.
Although 3D printing of fine details was initially challenging compared with other manufacturing techniques, technology, such as SLS has in-market printers that can layer heights as low as 0.05 mm and can produce details from 0.15 mm, and they are improving. The commercialization of 3D printers has helped increase the rate of improvements and has improved the user experience and ease of use. In addition, it requires less troubleshooting, which makes it more accessible to individuals.
Numerous medical specialities have utilized 3D printing in their practice, and applications are appearing continuously in the literature. The practicality of having physical 3D models on-demand has helped in training, surgery planning, and research and has led to improvements in medical equipment. It is not difficult to imagine medical equipment companies using 3D printing centers in large hospitals as in-house tools to provide their customized products, outsource designs, and develop new customized manufacturing chains. Perhaps requesting a custom implant in the future would be as easy as sending a 3D file to the printer for printing.
The technology is not perfect, it requires experience with troubleshooting the software and equipment. In addition, prolonged printing times mean that printing failures are detrimental and time-consuming. Despite the wide range of printable materials, many other types of material cannot be utilized in 3D printing; moreover, special preparations are required before the materials can be used, and 3D printing of very large items (i. e., hospital beds) is still not currently a practical means of manufacturing. It is exciting to see the future of 3D printing and the innovations in technology and applications in medicine, and as some experts predict, the industry is only getting started.44
Abbreviations
- 3D:
three-dimensional
- COVID-19:
coronavirus disease 2019
- CNC:
Computer numerical controlled
- SLA:
Stereolithography
- SLS:
Selective laser sintering
- FDM:
Fused deposition modeling
- FFF:
fused filament fabrication
- UV:
ultraviolet
- DLP:
Digital light processing
- CLIP:
Continuous liquid interface
- DICOM:
Digital Imaging and Communications in Medicine
- CAD:
computer-assisted design
- CHD:
Coronary Heart Disease
- FDA:
Food and Drug Administration
Declarations
Acknowledgement
I would like to acknowledge the Department of Neurosciences at Salmaniya Medical Complex, Bahrain for their help and support.
Funding
None.
Conflict of interest
The authors have no conflicts of interest related to this publication.
Authors’ contributions
Study concept and design (MM), acquisition of data (MM, AMS), analysis and interpretation of data (MM, AMS), drafting of the manuscript (MM, AMS), critical revision of the manuscript for important intellectual content (MM, AMS), administrative, technical, or material support (MM, AMS), and study supervision (MM). All authors have made a significant contribution to this study and have approved the final manuscript.
The Future of 3D Printing in Dentistry Services
Introduced three decades ago, 3D printing is transforming dentistry. The market for 3D-printed dental products is expected to reach $930 million by the end of 2025, driven by greater commercialization of printing systems, the need to customize dental products, and the availability of contract 3D printing services.
Dental products are customized and time-consuming and expensive to produce. With on-demand 3D printing services, dentists experience faster turnaround time on dental products, such as retainers and night guards, than traditional fabrication methods. 3D printing in dentistry continues to improve with better production processes and a greater range of materials, increasing the number of service offerings.
The Present and Future of 3D Printing in Dentistry
3D printing can easily create patient-specific products with little to no post-processing. Multiple dental products can also be printed on a single machine. With greater flexibility and more efficient processes, 3D printing will become the dominant dental production technology in the future.
3D Printing Dental Applications
3D printing is used to produce a number of dental products and aid various dental procedures. Here are some examples:
- Restorative dental implants.
Also known as “digital dentures,” crowns and replacement teeth are accurately produced with 3D printing. With the on-demand production of prosthetics, patients do not have to wait long for restorative implants and can expect a better product fit.
- Personal protective equipment (PPE). With strained supplies of PPE, the industry is rapidly adapting to 3D printing to produce face shields and other surgical accessories.
- Night guards and retainers. 3D printing night guards and retainers eliminates the thermoforming and trimming steps, reducing labor and time to develop a customized product.
- Surgical guides. FDA-compliant and more accurate oral surgical guides, such as tooth-borne, mucosal-borne, and bone-borne, can be 3D printed with rapid turnaround times and minimal material cost.
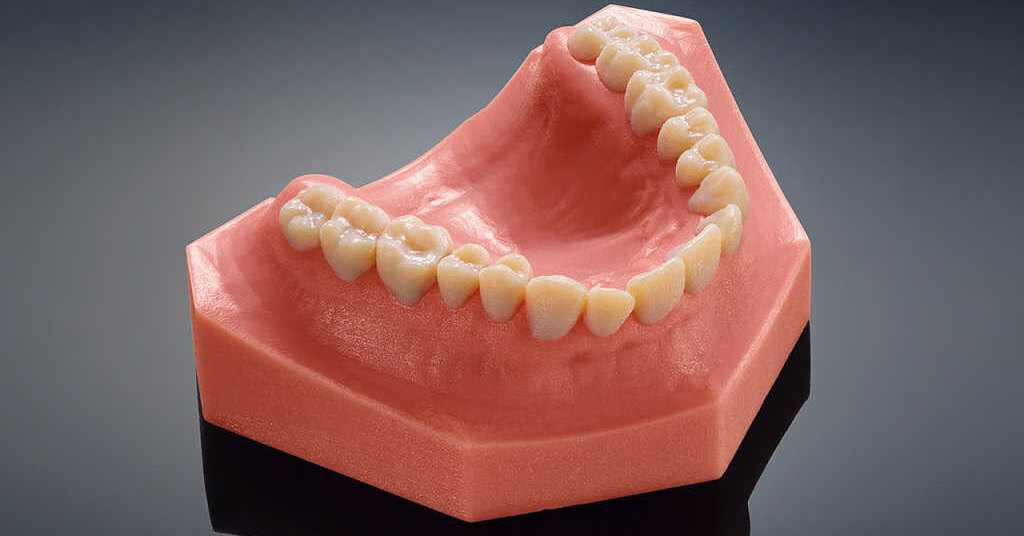
3D Printing Innovation in Dental
Innovation in 3D printing processes and systems is driving change in the dental industry.
- More advanced materials. Research in new 3D-printable materials will produce dental products that are stronger and more durable than ones manufactured with traditional materials, such as porcelain, while still being biocompatible.
- Broader applications and products. With more advanced materials, the quality and number of applications for 3D-printable dental products will expand. 3D-printed implantable teeth can eventually be easily manufactured to match a patient’s original teeth as well as improve the long-term biocompatibility.
- Greater accessibility. 3D printing is becoming widely available and the dominant manufacturing process for dental products. With greater flexibility, 3D printing is enabling a high mix of dental products to be made on-demand and more cost-effectively.
Why Use 3D-Printed Dental Products?
The flexibility of 3D printing systems makes it easier to produce customized products like dental night guards, retainers, prosthetics. The major advantages of 3D-printed dental products are:
- Customization without thermoforming and trimming. Dentists don’t need to create a mold for thermoforming and trimming. Instead, mouth scanners are used to create a digital model, and then the final product is directly printed.
- Reduced waste. 3D printing eliminates the need for a throwaway thermoforming mold and material lost during the grinding and buffing steps. Material waste is reduced by up to 80% with additive manufacturing.
- Competitive materials. 3D printed products are competitive with products made with traditional materials, such as thermoformed acrylics, epoxies, and ceramics, in terms of strength, color, durability, and value.
- Quick turnaround.
By eliminating the thermoforming and trimming steps, the final 3D printed product can be quickly printed and shipped with almost no labor.
Reducing material waste, eliminating post-processing steps, and improving materials translate into higher quality 3D products that are also cost-competitive with dental products manufactured with traditional methods and materials. Today’s advanced 3D printing technology can directly print a transparent product, eliminating the grinding and buffing required with older 3D-printed dental products.
3D printed dental models and implants can be extremely accurate and provide a more comfortable fit for patients.3D Print Dental Products with the Right Manufacturing Partner
Most dentists do not have 3D printers in their offices. With, on-demand 3D printing services, dentists can quickly order custom 3D-printed dental products without having to buy equipment that sits inactively between orders.
If you’re ready to experience the future of 3D printing in dentistry, LuxCreo offers an easy way to make production dental products on-demand. As an FDA-approved 3D printing service for night guards and retainers, LuxCreo can help you get dental products into production with a cloud-connected smart factory. You can print and ship customized products to your office or directly to patients.
To learn more about our processes and services for 3D printing at scale, visit our contact page or call (650) 336-0888.
3D printing dentist - the future of dentistry and prosthetics
3D printing dentist
We have already written a lot about where and how 3D printers and 3D technologies can be used. Another area where 3D printers are becoming indispensable is dentistry and prosthetics. 3D printers are used by dentists to create prostheses, models, braces and implants.
3D printing dentist
3D printers are increasingly used in dental clinics, dental laboratories, research centers. With their help, the quality of implants, prostheses and services has improved, as well as significant time and cost savings. But most importantly, 3D printers guarantee the highest precision of finished products. nine0004
3D printing dentist
The unique shape of each tooth of each patient is very difficult to reproduce using manual fabrication or a milling machine. The work of dental technicians is very laborious and takes a lot of time to get a good result.
3D printing dentist
Implants, prostheses, enameling, etc. must be made individually, because. each has its own structure of teeth and jaw. Therefore, technicians create separate models. To do this, the plates are filled with sodium alginate, silicone or polyester. Patients bite into the plate and leave impressions of the teeth. After that, based on the shape, the dentist adjusts the tooth and the prosthesis so that they are suitable. 3D printing guarantees high precision and quality. nine0004
3D printing dentist
3D printers allow you to remove a rather complicated and time-consuming stage - manual modeling of prostheses, crowns and other products. This ensures a reduction in waiting times, the number of fittings and fittings, from the first visit of the patient to the installation of the final design.
Thanks to 3D technologies and 3D printers, the process is reduced to:
- scanning the patient's mouth using a scanner, MRI or CT. nine0033
3D printing dentist
- data processing with special software,
- print the required model or shape on a 3D printer,
- fabrication of a finished prosthesis using an electronic model,
3D printing dentist
- installing an implant for a patient.
The patient receives a perfectly fitting crown or prosthesis in the shortest possible time. nine0004
The latest 3D technology and the most advanced materials deliver finished products much faster than ever before. And models, prostheses and implants made on a 3D printer exactly repeat the individual characteristics of each patient.
Due to the high precision of manufacturing and the mechanical properties of ceramics, the service life of a tooth restored using 3D technologies is significantly increased.
To summarize, there are several main advantages of using 3D printers in dentistry and prosthetics:
- the ability to store all anatomical data of patients in digital form, instead of impressions and samples;
- significant acceleration of the production of the necessary prototypes and models;
- fully automatic printing process that eliminates possible errors and inconsistencies;
- increase in production without increasing staff;
- the highest manufacturing precision, which eliminates the possibility of errors;
- The use of the latest 3D technologies will make it possible to improve the image of the company, which means it will increase the number of customers. nine0033
In our online store you will find a large selection of 3D printers for dentistry, photopolymer resins, 3D pens, 3D plastics, 3D scanners and everything you need for 3D printing.
Back to Home
3D Printing in Dentistry
- home
- Blog
- Application of 3D Printing in Dentist... nine0033
Today, 3D printing is firmly embedded in this area and is perfectly combined with innovative methods of dental care.
Advantages of 3D printers
Modern dental 3D printers allow you to quickly and with less labor produce high-quality, durable models of bridges, crowns, veneers and other structures. The use of this equipment has the following advantages:
- A wide choice of materials - allows you to solve almost any problem.
- High fidelity - improves the quality of treatment, saves time and money.
- Short production times. Creating a three-dimensional digital model using an intraoral scanner takes only a few minutes, and its printing on a 3D printer is many times faster compared to making a plaster model.
- There is no need to organize a separate technical room - a three-dimensional printer and a computer with the necessary software take up a minimum of space. nine0033
- Ability to simulate a large number of instances in one go.
- Save digital models as files for future remanufacturing.
- Aesthetics - A functional temporary can be quickly fabricated for the patient while the main bridge or crown is being fabricated.
- Reducing the cost of work compared to analog production.
What types of 3D printing are used in dentistry?
Consider 3D printing technologies used in dentistry and their features:
- DLP - digital LED projection. The radiation of a digital projector selectively affects the liquid photopolymer resin, which is in a special container, through the print area. There is a layer-by-layer hardening of the resin in the places of impact and the gradual construction of a three-dimensional model. The differences of this technology are a relatively small working area, high printing speed, a large selection of compatible consumables.
Due to the specifics of illumination by LEDs, voxel lines-layers can form on the surface of the figure. nine0033
- SLA (SL) - stereolithography. The printing process is similar to DLP technology, but a laser beam is used as a light source. Compared to DLP, the method is more economical in price, provides a better surface quality, but takes more time. SLA printers have a large footprint and are compatible with a wide range of media for a variety of applications. To switch to another material, you only need to change the cartridge and the bath with the polymer. Due to the affordable price, simple operation and compact size, SLA equipment is ideal for dental laboratories. nine0033
- SLM - laser melting of metal powder. These technologies make it possible to work with a biocompatible titanium alloy and print, for example, ready-made elements for replacing parts of the jaw. The created models have a homogeneous non-porous structure and high mechanical strength without additional firing.
- MJP (MJM) - multi-jet printing based on the layer-by-layer construction of parts made of photopolymer or wax. The technology was developed by 3D Systems and is used to create high-precision models and objects of any complexity with fine detail and a perfectly smooth surface. With its help, melted, burnt, conceptual, test or functional models, prototypes are made. The construction accuracy is 16 microns, which is significantly higher than that of DLP and SLA technologies. MJP printers and their consumables are the most expensive in their class. nine0033
- LFS is a low strength stereolithographic laser print that is a hybrid of SLA and DLP technologies. LFS equipment uses linear illumination and a flexible tank to deliver the highest print accuracy and incredible surface quality. Reduced building effort makes it easier to remove load-bearing structures. This method opens up great opportunities for improving production materials.
- Polyjet - 3D inkjet printing with liquid resins that harden when exposed to light.
The printed models are highly accurate and the surface quality is not inferior to parts made using the SLA method. Polyjet technology is rarely used in dentistry, because of the expensive patented consumables, it is suitable for the production of a limited range of products. nine0033
DLP and SLA printers are ideal for everyday tasks in dental clinics. EBM and SLM equipment is relevant for large laboratories. And the MJP and Polyjet technologies are gradually becoming a thing of the past.
Popular dental model programs
- 3Shape is the most advanced system that requires an annual license renewal fee.
- Maestro 3D Ortho Studio is a fully open Italian software with a perpetual license. Additional modules with new functionality can be purchased separately. The output is always an STL file. nine0033
- Avantis 3D is a Russian program with an inexpensive license but no file creation. Ready-made digital models are transferred directly to the manufacturing company for printing on their own branded equipment.
You can also buy a module for generating STL files.
- Implant Assistant is an inexpensive software with Russian support, tailored to work with implants.
- Dental CAD is a program that allows you to recreate bridges, crowns, clasp prostheses and other models based on scans, place supports on them and position them on the printing table. nine0033
Which dental models can be 3D printed?
A wide range of dental structures are produced using 3D printers:
- bases for bridges and crowns, caps, inlays, clasp prostheses;
- models for sectoral reproduction of the lower and upper jaws in the occlusion, demountable, demonstration models of the jaw;
- custom mouth guards, implant guides, maxillofacial guides, etc. nine0033
Currently, the printing of bases for removable dentures, temporary and permanent orthopedic structures is being actively developed.
Main applications of 3D printers in dentistry
3D printing techniques are increasingly used in orthodontics, surgery and prosthetics.
Let's take a closer look at what dental products are made with it.
Aligners
Clear aligners are used to correct malocclusion. The process of their manufacture using 3D technologies consists of several stages:
- Scanning of an impression (plaster or made through two-component silicone).
- Loading the impression file into the virtual dentition simulation software from the initial position to the ideal position of the teeth at the end of the treatment.
- Printing a simulated course of treatment on a printer.
- Vacuum molding of mouthguards on printed models.
3D printed aligners have the following advantages:
- high profitability of production;
- reduction of production time - you can start treatment the very next day after taking scans;
- saving time for adjustment - the procedure takes a minimum of time and does not interfere with treatment (a long break can negatively affect the entire course of treatment).
Bracket systems
The use of 3D technology in the manufacture of brackets allows you to achieve predictable results. Using the printer, template-conductors are printed - positioning spoons for installing bracket systems. Thanks to these devices, all elements of the braces are positioned and fixed exactly in the right places. nine0004
Surgical templates
These are special guide elements through which you can quickly and accurately drill holes for implants in the bone at the desired angle.
Operative interventions are planned in advance and performed after the preparation of the cast and CT scan. This is a very delicate work: due to the slightest mistake, bone tissue will have to be restored, which can take from 2 months to 1 year. The use of surgical templates avoids such negative consequences of operations as drilling at the wrong angle or at a shallower/greater depth, inaccurate positioning. nine0004
Dental Models
When performing any dental procedure, a real fitting is performed on the model. Instead of the traditional method of making models from plaster from casts, modern three-dimensional technologies are increasingly being used today: 3D scanning of the oral cavity and volumetric printing of the resulting digital model.
Direct manufacturing
Traditionally, dental products are manufactured by milling or casting (obsolete). Layer-by-layer 3D printing with fine spherical powder with a fraction of 10-40 microns is a completely new production technology that offers the following advantages:
- High production speed.
- Manufacture of complex structures with a high level of precision. For comparison: it is impossible to obtain too thin and small parts using milling, and when casting, some elements may turn out to be insufficiently elastic and strong.
- Solidity, uniformity of printed objects. Finished products do not have pores, which is of great importance in the manufacture of ceramic crowns. The slightest cavity sooner or later causes damage to the prosthesis.
The use of 3D printing avoids such consequences. nine0033
- Minimum waste. During printing (laser melting of metal powder), a conglomerate of fused particles is formed, the volume of which does not exceed 15%.
- Possibility of simultaneous production of a large number of models (about 80 units on a medium-sized platform).
Stages of direct production of dental structures on a 3D printer:
- Development of a digital model in a CAD program and its cutting into layers. Most dental software is a slicer at the same time, so model creation, support generation and print preparation are all done in one program. nine0033
- Printing a product on a metal 3D printer. It is carried out necessarily in a protective environment - argon or nitrogen. When using argon, it is necessary to bring and connect cylinders with this gas to the equipment. And in the case of nitrogen, the chamber can be filled with gas using a nitrogen generator.
- Removing supporting elements.
- Sandblasting, finished part finishing.
Prospects for the use of 3D printing in dentistry
There is a steady trend in the use of digital CAD/CAM protocol in dentistry. Three-dimensional scanning, three-dimensional modeling and printing make it possible to avoid many painful procedures, reduce the time of a visit to the doctor and provide dental services at a higher level, including in terms of aesthetics. nine0004
The cost of 3D printers and 3D printing consumables has dropped significantly in recent years. Simultaneously with the price reduction, the productivity of 3D equipment increased several times and the quality of the created objects improved. Thanks to this, equipment with technical characteristics that were previously available only for expensive printers has become available to specialists in many dental laboratories and clinics.
Only the complexity of mastering specialized equipment hinders the maximum introduction of new 3D printing technologies.