Iron man 3d printer
Ironman best 3D printing models・Cults
IRONMAN TOOTHPASTE
€1.88
IRONMAN CAlAVERA
€0.97
Stark Industries Marvel Poster
€1.90
Iron Man Mark 50 Reactor
€4.10
Venom Mask From Marvel Comics - Fan Art 3D print model
€30
Killmonger Golden Jaguar
€3.20
Avengers Age of Ultron
€3.20
Venom Mask From Marvel Comics - Fan Art 3D print model
€30
DareDevil Mask
€3.20
Green Goblin Mask
€3.20
Iron Man - Hulkbuster Armor
€3. 21
Danielle Moonstar X-man
€16.91 -30% €11.84
Super Hero Robots
Free
Low Poly Iron man Bobblehead
Free
lego ironman
€2 -15% €1.70
Pym particle vial ends
€3.94
Wasp Helmet - Fan Art 3D print model
€30
Venom Mask From Marvel Comics - Fan Art 3D print model
€30
Iron-man helmet
€13
KEYCHAIN IRONMAN
Free
Captain America
€3. 99
Iron man bust
€2.99
Spider-man
€4.99
Dark deadpool
€4.99
Deadpool
€4.99
Mbaku mask
€3.76
Shang Chi Rings
€3.76
The Avengers Loki Crown for Cosplay
€14.90
Bike aerobar BTA bottle cage mount
Free
Ghost Rider Mask From Marvel comics - Fan Art 3D print model
€30
Tanos
€3.99
Ironman Toybiz 1994 cannons replacement parts
€1.87
Abomination Mask From Marvel Comics - Fan Art 3D print model
€30
DISNEY IRONMAN KEY
€2. -45% €1.38 50
Sliver Surfer
€3.99
Iron man keycap
€2
Capitan Marvel
€3.99
Mjolnir thor
€3.99
Stand like reactor Iron Man
Free
ironman mask
€3.99
ironman ver 6
€4.99
ironman ver 5
€4.99
ironman ver 3
€3.99
ironman ver 2
€3.99
iron man
€3.99
ironman
€3. 99
Marvel/Advenger Christmas balls
€0.53
HAMMER DRONES - Ironman 2 - low poly 3d print
€3.76
Iron Man 3d Print - Etsy.de
Etsy is no longer supporting older versions of your web browser in order to ensure that user data remains secure. Please update to the latest version.
Take full advantage of our site features by enabling JavaScript.
Find something memorable, join a community doing good.
(700 relevant results)
Iron Man Helmet (Motorized): Part 1
Application
I completely unbelted, and well, oh, for a long time I did not write anything, from the word 'completely'.
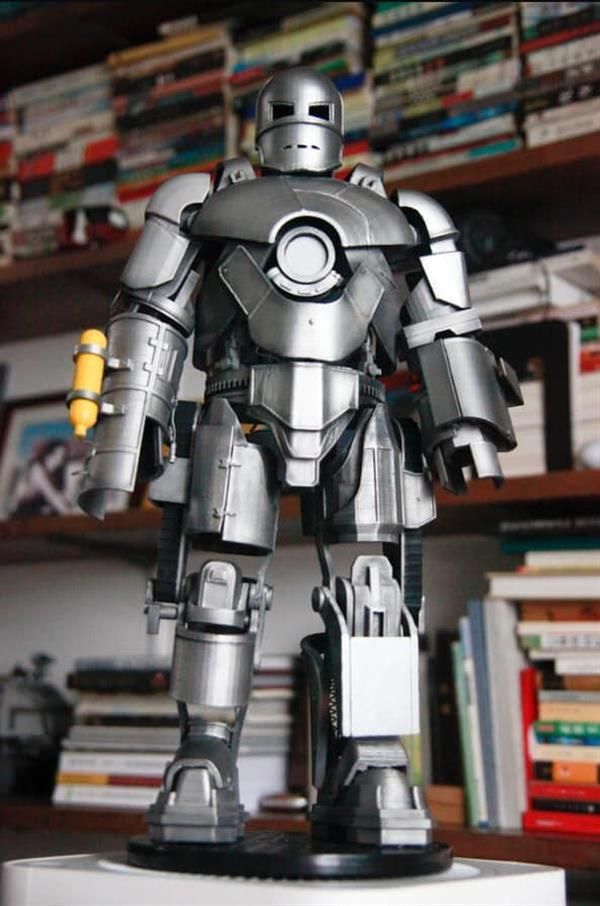
It all started with the fact that the helmet does not fit in my print area. Even a relatively small visor in height does not want to get up, well, no way. I had to urgently add to my knowledge of netfabb, knowledge of Mesh Mixer. Someday, in the near future, I will definitely make a video guide on cutting with a section selection, netfabb can't do that xD. But now is not about that.
The visor is cut into 8 pieces to minimize the number of supports. It was printed in pairs (left plus right) in 5 runs for 8 hours (ugly!!!). The chin is divided into 5 parts and everything is also not fast there: 8 + 8 + 4 hours. The main part of the helmet - 8 parts and 4 times 12 hours. Well, it's a long time! nine0003
All printed with layer 0.2 and PLA 'Ninja Turtle' by FDplast. Why green? Yes, because I have it. The last two parts were not enough and the 'Terminator' went into action.
And it all started with the visor, and as you can see from the first photo, at the moment, it is the best processed, relative to the rest of the helmet.
Parts glued together. I shed the seams with super glue, sometimes adding soda. Then a long and tedious process of grinding with fine sandpaper in a bowl of water. After grinding - I apply a layer of white paint - I will have it for the place of the soil and to indicate the irregularities and flaws in the grinding. I'm sanding again. nine0003
Sanded the paint, filled in the bumps, sanded, painted. And so several times, until the result begins to suit. The next photo shows how to fill small chips and holes with super glue. It is fluid enough to flow inside and securely close the defect. Then it remains only to wipe with sandpaper.
When the result began to suit me at least somewhat, I filled the visor with white paint and solemnly took a picture. There are still defects on it, so I then cleaned it again, but they are difficult to notice with the eye. The stripes on the visor are elements of the model, it's kind of worn xD. nine0003
My chin gave me a lot of pain. There was a half-millimeter step, which I grinded for probably an hour. PLA is extremely reluctant to be processed by abrasives.
The chin is far from finished, some seams are missed and still not sanded. Then the rest of the helmet was printed and glued to the chin.
Here, in general, in the Garden with Gomorrah, there are a lot of seams and many of them are large. I decided not to translate the precious glue, but to use the precious Tamiya putty. Putty is still on the way, and the helmet is already being measured on the head. Damn it, it's too small for me, it hurts my ears! Okay, I'm not doing it for myself, but for one good friend, her head is narrower and smaller - it fits her. nine0003
And next time I will talk about how the alignment and stitching process was completed, how to paint such a bandura and not screw it up, as well as how to attach electronics to it to control the lifting of the visor. But it looks like it will be another 2-3 weeks, it is very hard to saw.
Subscribe to author
Subscribe
Don't want
29
Mythbuster Adam Savage 3D-printed Iron Man
4408 views Posted on: 06/13/2019
Author: 3D4U. COM.UA
Adam Savage, American special effects artist and former co-host of the popular Discovery Channel show MythBusters, finally got his own 3D printed Iron Man suit. It looks like the titanium ensemble was made for the new series Savage Builds.
However, Savage's Iron Man project was not entirely solo. The suit was produced by the Colorado School of Mines, leading 3D printer manufacturer EOS, ceramic 3D printer specialist Lithoz, Hollywood cinematic effects specialist Legacy Effects, and Gravity, which was behind the original version of The Real Iron Man. nine0003
The final result will be presented in a show showing the steps taken to assemble the suit as well as a short flight demonstration integrated with Gravity outboards.
Richard Browning, co-founder of Gravity, is the person people often think of when they talk about "real life Iron Man." Ever since his company started in 2017, the Gravity team has been working tirelessly to build hand-mounted rocket motors. This could give people the ability to levitate and travel on land and water. Through countless public appearances, Browning has showcased the accomplishments of the Gravity team, gliding effortlessly across parking lots and fields, and making a commercial version available to buyers at Selfridges in London. nine0003
In 2017, Gravity got a place on Savage's YouTube channel, which confirmed some of the subtleties of the wetsuit design. In 2018, EOS also confirmed its participation in the wetsuit project at Gravity, giving Formnext attendees a demo of the technology.
At the Colorado School of Mines, Craig Bryce, professor of mechanical engineering and director of the university's advanced manufacturing program, oversaw the production of Savage's Iron Man suit. Explaining his reasons for joining the project, Bryce said: “Who says no to Adam Savage making an Iron Man suit out of titanium? I felt it was a great learning moment." nine0003
"Thanks to the engineering approach to the entertainment project, we actually created a usable suit.
"
First getting the design right, with resolution and official 3D models from Marvel, Bryce and his team sent the suit to the EOS 3D Printing Factory in Texas for production.
The final version of the costume is an assembly of 250 individual parts, 3D printed from lightweight titanium. The promo video also shows the suit paired with Gravity thrusters to get as close to the real Iron Man as possible. nine0003
The signature "arc reactor" at the center of Tony Stark's suit is reproduced using a Lithoz ceramic 3D printer at the ADAPT lab.
3D printing is in high demand in the cosplay and fanart industry. No other technology gives such scope for imagination and subsequent implementation.
Photo taken from the official Youtube channel of Adam Savage
Related Products
-
CR-10S PRO 3D Printer Creality
Price: Rs.
-
Flashforge Guider II 3D Printer
Price: 70,800 ₴
FlashForge Guider II is an improved version of the popular Guider 3D printer with.
..
Related articles
- Top 20 interesting toys for children on a 3D printer.
Category: 3D printing
02/15/2022 nine0003
12180 views
What kind of toys can be created on a 3d printer? What are the advantages of 3d printing toys at home? In this article you will find...
Read more - 12 common 3D printing mistakes to avoid.
5170 views
As an industry, 3D printing is evolving every day, so it's important to know all aspects of this technology today. In this...
Read more - 9 romantic 3D printed gifts for Valentine's Day. nine0002 Category: 3D printing
02/09/2022
1945 views
3D printing can help you create unique and personalized gifts for your significant other. Compilation 9...
Read more - What can be printed on a 3D printer?
Category: 3D printing
03.
Learn more