The beast 3d printer forum
CYBORG BEAST HAND – Enabling The Future
The “Cyborg Beast” hand has been created as a collaboration between Jorge Zuniga, Ivan Owen and Peter Binkley.
All files for this design can be found on Thingiverse, HERE.
Instructions:
Cyborg Beast Instructions: HERE
Which Files Should I Download and Print?
Currently, the latest version of the Cyborg Beast is v1.45, which has a file name of Cyborg_Beast_1.45_Marc_Petrykowski_07-1-14.zip
The ZIP file can be downloaded directly using the link above. When you open this ZIP file, you will find the following files inside:
- CB_Finger (bumps) Non-Manifold 1.45.stl
- This is the distal finger phalange (furthest from the palm). This version has bumps on the finger pads to improve grip surface, but has some non-manifold issues that may cause problems with some slicing software.
- This is the distal finger phalange (furthest from the palm). This version has bumps on the finger pads to improve grip surface, but has some non-manifold issues that may cause problems with some slicing software.
- CB_Finger (no bumps) 1.45.stl
- This is the distal finger phalange (furthest from the palm). This version has no bumps on the finger pads, but it is fully manifold and should slice cleanly in any slicing software.
- CB_Gaunt (no tensioner) 1.45.stl
- This is the gauntlet (the part that fits over the arm) without a tensioner block (in case you want to add a different kind of tensioner).
- CB_Gaunt (tensioner) 1.45.stl
- This is the gauntlet (the part that fits over the arm) with an integrated tensioner block.
- CB_Hex 1.45.stl
- This is the hex sleeve part that fits into the tensioner block. The non-flexible cords will be attached to these parts, which will then be inserted into the tensioner block and held in place with screws.
- CB_palm 1.45 (left).stl
- This is the palm for a left hand.
- This is the palm for a left hand.
- CB_palm 1.45 (right).stl
- This is the palm for a right hand.
- CB_Phalange 1.45.stl
- This is the proximal finger phalange (closest to the palm).
- CB_Thumb_Finger (bumps) Non-Manifold 1.45.stl
- This is the distal portion of the thumb (furthest from the palm). This version has bumps on the finger pads to improve grip surface, but has some non-manifold issues that may cause problems with some slicing software.
- CB_Thumb_Finger (no bumps) 1.45.stl
- This is the distal portion of the thumb (furthest from the palm). This version has no bumps on the finger pads, but it is fully manifold and should slice cleanly in any slicing software.
- CB_Thumb_Phalange 1.45.stl
- This is the proximal thumb phalange (closest to the palm).
For a standard Cyborg Beast, you’ll need to print the following:
- 4 x CB_Finger (bumps) Non-Manifold 1.
45.stl OR CB_Finger (no bumps) 1.45.stl
- 1 x CB_Gaunt (tensioner) 1.45.stl
- 5 x CB_Hex 1.45.stl
- 1 x CB_palm 1.45 (left).stl OR CB_palm 1.45 (right).stl
- 4 x CB_Phalange 1.45.stl
- 1 x CB_Thumb_Finger (bumps) Non-Manifold 1.45.stl OR CB_Thumb_Finger (no bumps) 1.45.stl
- 1 x CB_Thumb_Phalange 1.45.stl
ACCEPTANCE
By accepting any design, plan, component or assembly related to the so called “e-NABLE Hand”, I understand and agree that any such information or material furnished by any individual associated with the design team is furnished as is without representation or warranties of any kind, express or implied, and is intended to be a gift for the sole purpose of evaluating various design iterations, ideas and modifications. I understand that such improvements are intended to benefit individuals having specific disabilities and are not intended, and shall not be used, for commercial use. I further understand and agree that any individual associated with e-NABLE organization shall not be liable for any injuries or damages resulting from the use of any of the materials related to the e-NABLE hand.
Like this:
Like Loading...
Build – Tom's 3D printing guides and reviews
tomBuild, Tips and Tricks
Okay, you all know how 3D printing works. You start out by creating a 3D model, export that as stl or 3mf, then import that into a slicer, which then creates the gcode that the printer understands. Except that it doesn’t have to be that way. Enter Full Control GCode. This is actually the result of a research paper by Dr. Andrew Gleadall, and it lets you skip modeling and slicing and instead provides you with a scripting interface that controls every single printing move. You get full control. AndContinue reading
tomBuild
TL,DR: “forum.toms3d.org” is being taken offline. It was way too big of a challenge to run and didn’t provide much value. I recommend using the RepRap forum instead. It’s time. forum.toms3d.org is going offline. The forum was originally started as a means to sharing thoughts, ideas and helping others, independent from my YouTube channel. At the time, it was looking like the trusted RepRap wiki and forum were not too well maintained and were going to buckle under the load eventually, so I wanted to have a backup at hand,Continue reading
tomBuild
Today we find ourselves in my former printcave – the printers have moved on to the studio, but I’m keeping the dirtier tools here in the basement. And one of those tools is the Sienci Labs Mill One CNC, which for the rest of the video, I’ll call Bob for stupid, but obvious reasons. Bob is a moving-bed CNC router, kinda similar to the Carbide 3D Nomad, and as-is, it was ok, it was usable for light wood cutting and so on, but there were a few things that wereContinue reading
tomBuild
I need a 3D printer that’s always ready to print. That’s just always set up, always ready to go, so that when I have an idea for something that I want to print, I spend five or ten minutes designing it and then can send it right off to the machine without having to hunt for slicer profiles, load filament, prepare the bed or do whatever little naggy job to get the machine working. A good while back, I had a Mendel90 just set up with OctoPrint, it had ABSContinue reading
tomBuild
Today I want to share this tool that I made – and even though it’s a super simple tool, this sort of stuff is why I’m still excited about 3D printing and the possibilities it opens up. This week I was putting down some new decking on my balcony and I needed this tool for it – and while you can buy these on Amazon I didn’t want to have to wait that long, Amazon already has a banner up that deliveries might take longer than usual, and as itContinue reading
tomBuild
Today I’m finally finishing a project that I started well over two years ago. You know, now is a great time to get all that half-finished stuff done and just get it off your mind. Originally, this was supposed to be a full set of 5.1 surround satellite speakers for my TV, or if you want to call it a “home cinema” setup, but this project hit so many snags that I ended up just getting way too frustrated with it and just kept putting it off. But I think,Continue reading
tomBuild
So this is the hot new product in 3D printing right now – it’s the E3D Herm.. Hem… Hemera. It’s the Hemera. It’s a hotend – extruder combo that I think does pretty much everything right. So let’s check out what’s new and what’s different compared to what else is out there.
tomBuild
E3D just announced their new Hemera toolhead. Naturally, I’ve been using it for a few weeks, and my first impressions are that it’s quite a beast of an extruder. And yes, it’s now called the Hemera. Apparently some INTERNATIONAL company was concerned about the HERMES brand and “kindly asked” E3D to change the name. So it’s now the E3D Hemera, other than the name, it’s the exact same toolhead.
Questions and Answers for 3D printers and 3D printing
This section contains all the most frequently asked questions and answers about 3D printers and 3D printing. If you didn't find the answer to your question in this section or using the portal search, ask it in blogs and get answers from community members: /questions/
- 1 Frequently Asked Questions
- 1.1 Bought a 3D printer - what's next?
- 1.2 3D printer does not see/print STL file
- 1.3 Which program is used to prepare an STL file for printing?
- 1.
4 What is a 3D printer and how does it work?
- 1.5 What is the kinematics of a 3D printer?
- 1.6 What are stepper motors and drivers?
- 1.7 What is 3D printer firmware and where is it uploaded?
- 2 Defects and 3D printing questions
- 2.1 Related Articles
- 2.2 PLA does not choke and the extruder clicks
- 2.3 Waves appear on the walls when printed.
- 2.4 At the start of printing, the table/carriage starts banging against the wall.
- 3 Questions about adhesion (sticking the model to the table)
- 3.1 Plastic does not stick to the table.
- 3.2 The part is very stuck during printing and cannot be removed from the table.
- 3.3 Bends corners when printing.
- 4 Consumable questions
- 4.
1 How to print with PLA
- 4.2 How to print with ABS
- 4.3 Plastic has uneven diameter
- 4.4 Foreign inclusions are observed in the plastic.
- 4.5 Plastic tangles occur when printing
- 4.6 Is ABS plastic harmful?
- 4.7 Why does the bar feed stop after several layers when printing with soft plastics (Flex)?
- 5 3D printer assembly and calibration questions
- 5.1 Axle moves in the wrong direction
- 5.2 When replacing stepper motor drivers from A4988 to DRV8825, do I need to change something in the firmware?
- 5.3 After installing the TMC2100/2208/2130, layer shifts occur during printing.
- 6 3D printer firmware questions
- 6.1 Can't figure out Marlin
- 7 Preparing the model for printing. Slicers
- 7.
1 CURA program - how to use it
- 7.2 KISSlicer - how to use it
- 7.3 Repetier-Host program - how to work with it
- 7.4 Simplify3D - how to use it
- 7.5 Slic3r - how to use it
- 7.6 Craftware - how to use it
- 8 Questions about G-CODE
- 8.1 What is G-CODE?
- 9 3Dtoday Help
- 9.1 how to use the portal and what is there?
- 9.2 Where can I read information about 3D printers and 3D printing?
- 10 Search for questions and answers on the portal
FAQ
Bought a 3D printer - what next?
answer: read the article - For the little ones: how to start typing
3D printer does not see/print STL file
answer: almost all 3D printers should not see or print STL files (although there are exceptions) as a result of polygonal modeling or export from CAD programs. STL files are loaded into the program for preparing the model for printing (slicer) and converted into a control code (g-code) for the printer. The resulting "slicing" file is what the 3D printer sees. Details here
What program is used to prepare the STL file for printing?
answer: To prepare an STL file for printing, you need to use a slicer - a program with which you set the print settings for the model for the printer. Such a program (slicer) can be either common and not tied to a specific printer, for example, Cura, slic3r, KISSlicer, etc., or individual for a specific 3D printer (supplied with the printer). In this program, many parameters are set - print speed, layer thickness, temperature, and many others. Information on slicers here
What is a 3D printer and how does it work?
answer: read the article - what is a 3D printer
What is the kinematics of a 3D printer?
answer: read the article - 3D printing for the newest. From A to Z. Kinematics.
What are stepper motors and drivers?
answer: read the article - 3D printing for the newest. From A to Z. Steppers, drivers and some magnetic field.
What is 3D printer firmware and where is it uploaded?
answer: read the article - 3D printing for beginners. From A to Z. Boards and firmware.
Questions about defects and 3D printing issues
Related articles
Most questions and answers are given in the articles. Please read:
- 3D Printing Defects - Let's try to classify
- The 20 Most Common 3D Printing Problems (Part 1)
- The 20 Most Common 3D Printing Problems (Part 2)
PLA does not choke and the extruder clicks answer: The problem is insufficient cooling of the thermal barrier of the extruder.
Waves appear on walls when printed.
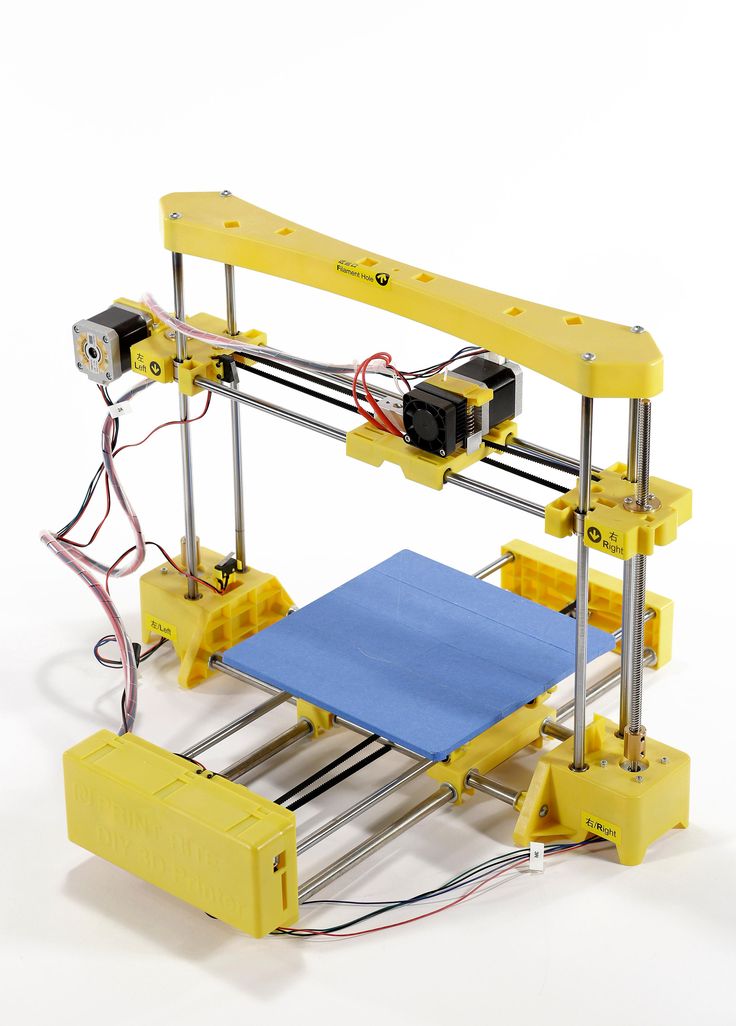
At the start of printing, the table/carriage begins to knock against the wall.
answer: To fix the problem, you need to check the limit switch, whether it is pressed by the carriage / table and the integrity of the switch wires.
Adhesion questions (sticking the model to the table)
Plastic does not stick to the table.
answer: when printing on glass surfaces, to improve adhesion, it is necessary to use various adhesives (for example, glue from The 3D or Picaso, you can use glue stick or BF-2). Printing is recommended on glass surfaces (preferably mirrors) due to their flat surface, which ensures an even first layer.
A part is stuck to the printout and cannot be removed from the table.
answer: the problem is related to a very small gap when printing the first layer, and it "smeared" into the glass surface. You need to increase the clearance. And to remove the part from the glass, it can be placed in the freezer of the refrigerator.
Part curls up when printing.
answer: when printing, it was necessary to close it from drafts. The bending of the corners is associated with a strong shrinkage of the material when it is cooled. For uniform shrinkage, which all plastics have, it is necessary to maintain a stable temperature using a heat chamber. A box with which you can cover the printer, as well as installing a door in the printer can serve as a thermal chamber.
Questions about consumables
How to print with PLA
Answer: PLA has operating temperatures ranging from 200 to 230 degrees (depending on the composition of the material used by the manufacturer). If your 3D printer has a heated table, then no additional funds are required to stick the model to the table. If your table is not heated or the model does not stick to the table, then check the table calibration and use adhesion agents (varnish / glue for printing, etc.).
How to print with ABS plastic
answer: ABS plastic has printing temperatures from 230 to 250 degrees (depending on the composition of the material used by the manufacturer). Printing with ABS plastic implies the presence of a heated table and means for adhesion (varnish / glue for printing, ABS juice, etc.).
Plastic has an uneven diameter
answer: Diameter fluctuations of more than 0. 05 mm are considered defective. In this case, it is necessary to contact the manufacturer with a request to replace the coil with a quality one.
There are foreign inclusions in the plastic.
answer: this is a defect, you must contact the manufacturer with this defect. Such defects can lead to clogging of the printer nozzle.
When printing, plastic entanglement is observed
answer: the so-called overlap is due to the fact that during operation you relaxed the coil winding, and the upper turns fell under the lower ones. We recommend unwinding part of the coil to a place with even winding and carefully winding it back, observing the tension.
Is ABS plastic harmful?
Answer: When printed, ABS emits an unpleasant odor and the room must be ventilated. There is no harm, the discharge does not exceed the MPC (maximum permissible concentration).
Why does the bar feed stop after several layers when printing with soft plastics (Flex)?
Answer: If your printer has a Bowden bar feed system, the soft plastics are experiencing too much resistance as they pass through the tube to the print head. Try increasing the nozzle temperature to keep the resistance to a minimum.
3D printer assembly and calibration questions
Axis moves in the wrong direction
answer: if the movement occurs in the wrong direction, then you need to turn the stepper motor connector 180 degrees.
When replacing stepper motor drivers from A4988 to DRV8825, do I need to change something in the firmware?
answer: If you want to use them with the same divisor (1/16), then nothing is needed. If you want to use it with a 1/32 divider, then in the firmware you need to double the number of steps on those axes where these drivers are installed. Also, do not forget about the correct adjustment of the driver current.
After installing the TMC2100/2208/2130, layer shifts occur during printing.
Reply: This type of driver requires good cooling and fairly accurate Vref regulation.
Questions about 3D printer firmware
I can't figure out Marlin
answer: read articles about firmware:
- Set up Marlin firmware and upload it to the 3D printer
- Firmware and printer setup Mar0
Preparing the model for printing. Slicers
CURA program - how to work with it
answer: read articles written especially for you. List:
- What is Cura, how to prepare it and what it is eaten with.
- "CURA" is your caring assistant in the world of printing.
- The path to excellence. Cura
KISSlicer program - how to use it
answer: read articles written especially for you. List:
- KISSlicer - learning to work. Part 1.
- KISSlicer - learning to work. Part 2.
- KISSlicer - learning to work. Part 3.
- KISSlicer (user's manual) Part1
- KISSlicer (user's manual) Part2
Repetier-Host program - how to use it
answer: read articles written especially for you. List:
- Let's help beginners: Repetier-Host - first steps.
- Let's help beginners: Repetier-Host - first steps. Slic3r settings. Part 2
- Let's help beginners: Repetier-Host - first steps. Cura settings. Part 3
Simplify3D program - how to use it
answer: read articles written especially for you. List:
- Simplify3D “For Dummies”. Part 1. “Program interface”
- Simplify3D “For Dummies”. Part 2 “Creating a workflow”
- Getting started with Simplify3d or I learned what a slicer is, and what's next?
- Using different print settings for different parts of the model in Simplify3D, print acceleration
Slic3r - how to use it
answer: read articles written especially for you. List:
- Slic3r. advanced. Detailed instructions
- Fine-tuning the printing process in Slic3r. Settings window: part and modifier
- slic3r tweaks for small parts
Craftware program - how to work in it
answer: Read articles written especially for you. List:
- Craftware. Simple and friendly slicer.
- Craftware. Slicer settings. Basic tab.
Questions about G-CODE
What is G-CODE?
answer: read the articles written especially for you. List:
- GCODE: Basics
- GCODE: Pavlushka Buns
3Dtoday Help
how to use the portal and what is there?
answer: read the portal help - /wiki/func/
where can I read information about 3D printers and 3D printing?
answer: use our encyclopedia - /wiki/
Search for questions and answers on the portal
If you did not find the answer to your question in this section of the help, use the search on the site. Maybe a similar question has already been discussed in blogs. Search form here - /search/
Medical 3D printer application overview
Contents:
- Medical 3D printing equipment use
- Benefits of using 3D printers
- The main directions of the use of additive technologies in medicine
- Manufacture of surgical and other medical instruments
- Dentistry and prosthetics
- Student education and preparation for surgery
- 3D bioprinting of organs and tissues
- Production of medicines on a 3D printer
- Creating ovaries
- Making a model of the heart of a 4-year-old patient on a three-dimensional printer Zortrax M200
- Creation of a cranial implant
- Use of individual sensors
- Treatment of extensive wounds
- Creation of artificial corneas
- Manufacture of the Volt Bipolar Surgical Forceps for Laparoscopic Operations
- Hip replacement
- Fabrication of dental crowns
- Reconstruction of the auricle (cartilage fabrication)
- Production of dental impressions
- Construction of a medical exoskeleton
- Fabrication of a model of the cardiovascular system
- Creation of prostheses
Medical use of 3D printing equipment
3D printing was first used in the medical field to print dental implants in the early 2000s. Since then, the field of medical application of this electronic technology has expanded significantly and continues to develop. Now with its help, elements of the respiratory tract (nose, etc.) and the skeleton (jaw, joints, etc.), cell cultures, blood vessels, some parts of the eyes, organs (kidneys, bladder, etc.), tissues, medicines are produced. , layouts of biomolecules, bacteria, viruses and more.
Printable 3D files enable users and researchers around the world to share their own scientific developments over the network, discuss interesting cases and the opinions of colleagues. And also independently or jointly with partners to improve three-dimensional prototypes without spending months and years reproducing objects from scratch.
Working on additive projects requires the integration of technologies from different scientific fields, including cell biology, medicine, mathematics, physics, engineering, biomaterials science, and industries.
Advantages of using 3D printers
Medical 3D printing has the following advantages:
- material and labor savings;
- 3D printing of structures of the highest level of complexity, completely similar to prototypes, lightening their weight;
- high print speed;
- high accuracy and detail, taking into account the anatomical parameters of a particular patient;
- a large number of innovative high-tech materials, including a wide range of consumables that are suitable for implantation in the body;
- cost reduction of medical products;
- reduction of production terms and, as a result, timely provision of medical care.
The main areas of application of additive technologies in medicine
The use of 3D printers in medicine can be divided into the following categories:
- Manufacturing of medical instruments.
- Printing of orthopedic products, frameworks and implants.
- Printing of 3D anatomical models for educational purposes and in preparation for operations.
- Creation of organs and tissues.
- Pharmaceutical research.
Manufacture of surgical and other medical instruments
In order to perform surgical interventions with minimal trauma for patients, surgeons try to use personalized instruments that are anatomically suitable for a particular person. 3D printing makes it possible to produce customized instruments and templates for surgery in just a few hours.
Additive technologies allow surgeons to customize finished instruments to the right shape and size for more productive, comfortable and safer work. Dentists have the opportunity to create, for example, personal guiding instruments in front of the patient to protect healthy teeth from damage when installing prostheses.
Dentistry and prosthetics
Three-dimensional technologies have become a real breakthrough in the development of the medical products market and the field of dentistry in particular. First of all, they made it possible to scan the oral cavity in a three-dimensional format as accurately and in detail as possible. Secondly, with the help of 3D printing, it is possible to produce dental prostheses in full accordance with the anatomy of patients without additional fitting. A significant reduction in manual labor when working on veneers, bridges and crowns made it possible to expand the list of materials for prosthetics, reduce the required manufacturing tolerances and improve the quality of work in general.
Additive manufacturing is widely used in medicine to work on projects of complex individual and serial products: surgical implants, prostheses of any geometry, auxiliary structures, etc. Such structures are made by converting CT, MRI or X-ray images into three-dimensional models for 3D printing devices using specialized software. 3D technologies are especially in demand when it comes to the urgent production of non-standard prostheses and implants. The fact is that standard models often do not correspond to the specifics of the anatomy of patients. For example, neurosurgeons often face such a problem: human skulls have a unique shape, so it is extremely difficult to create a standard cranial implant. Before the advent of three-dimensional technologies and 3D-printed models, doctors finalized and customized implants, sometimes right during the operation. Now you don't need to do this. The most important advantage of printed prostheses is a perfectly precise connection with the body with virtually no risk of rejection.
Student education and preparation for surgery
3D models are a much better medium for teaching and training medical students than human cadavers. 3D mock-ups are more accessible, and 3D modeling helps to reproduce a wide range of pathologies relevant to the topic under study. For example, neuroanatomical 3D models are very useful for future neurosurgeons, as they provide the most complete picture of the most complex structures of the body, which cannot be achieved by studying two-dimensional images.
Three-dimensional models printed on a 3D printer based on the results of hardware studies allow taking into account the patient's anatomy when rehearsing operations. The use of a tangible three-dimensional model of the patient's organ gives the surgeon the opportunity to more thoroughly study the pathology or simulate surgery, which significantly reduces the risk of medical errors.
Production of organs and tissues by 3D bioprinting
Bioprinting is one of the types of 3D printing in medicine. Instead of metal or plastic, special printers use a syringe dispenser to apply "biological ink" (tissue spheroids), that is, layers of living cells or a structuring base for them, creating an artificial living tissue. For the "printing" of some tissues, stem cells, seaweed or porcine collagen protein are taken.
Organic materials obtained in this way are a good alternative to donor tissues and a valuable tool for medical research. They can be used for tissue regeneration, and in the future, for the restoration of organs directly in the patient's body.
3D bioprinting can be done using different technologies: inkjet, laser or extrusion. The most common method is 3D inkjet printing, where multiple printheads can be used to print different types of cells (muscle tissue, blood vessels, organ-specific cells). These cells are essential for building heterocellular organs and tissues.
Manufacture of medicines on a 3D printer
3D technologies are used in personalized medicine and pharmaceutical research. With the help of 3D printing, you can fully control the dosage of various drugs and the composition of dosage forms with prolonged action and complex release profiles of active substances. Pharmacists have the opportunity to effectively analyze the pharmacogenetic profile of patients and other parameters. For example, gender, age and weight, to determine the optimal dose of drugs and their regimen. Based on the clinical response, the dosage may be adjusted if necessary.
Additive printing allows the production of personalized medicines according to new formulations, for example, complex multilayer tablets or capsules containing several active ingredients, and many other useful things.
Examples of the use of 3D printers in medicine
Ovarian printing
In 2017, American doctors and scientists at Northwestern University Chicago (USA) developed an artificial ovary that opens up opportunities for the full restoration of female reproductive function. During the study, a 3D-printed ovarian prosthesis was implanted into the body of an infertile laboratory mouse. As a result of the experiment, the “patient” acquired offspring, moreover, the mice turned out to be completely viable and after that they were also able to produce offspring.
It is currently unknown whether such an artificial ovary could be implanted in a woman, as human follicles grow much faster than mouse follicles.
Making a model of the heart of a 4-year-old patient on a Zortrax M200 3D printer
A team of experts from the Department of Pediatric Cardiology and Congenital Heart Diseases, together with colleagues from the Department of Radiology and Cardiac Surgery of the Medical University of Gdansk (Poland), used the Zortrax M200 3D printer to prepare for the execution surgery for the treatment of complex congenital heart disease in a four-year-old patient - tetralogy of Fallot.
The modern method of treating this pathology involves the supply of an artificial valve for implantation to the heart through a special catheter inserted through the femoral vein. This is an extremely complex operation that requires the surgeon to have the most complete and detailed knowledge of the anatomical characteristics of a real patient.
Previously, doctors could only rely on a three-dimensional computer model developed from MRI and CT images. However, these images were not enough to form a complete picture of the state of the organ and the likely problems that could occur during surgery. The use of a highly detailed physical copy of an organ (heart with cells, chambers, ventricles, blood vessels) can play a decisive role in the planning of the operation and be the main factor in its success.
The model of the heart was printed in the laboratory in 24 hours. Z-Ultrat material was used for 3D printing of the heart, and Z-Glass material was used for vessels. The operation was successful. The model was then handed over to the University for use as a teaching tool for students.
Creation of a cranial implant
Titanium bone implants are printed in single copies. It is when working with them that the advantages of 3D printers using selective laser melting (SLM) technology are best manifested. This method allows you to print implants of any shape with the highest accuracy in just a few hours.
Use of custom sensors
In 2016, scientists from Washington University in St. Louis (USA) conducted a study on the use of flexible and movable silicone custom sensors. They printed three-dimensional copies of scanned models of the hearts of experimental animals and placed sensors around them. Three-dimensional sensors can be removed from the prototype and fixed to the human heart. With their help, you can monitor the work of the heart muscle in order to prevent the occurrence of strokes, heart attacks and other serious diseases. Individual sensors are used so far only outside the body, but scientists suggest that in the future it will be possible to introduce them into the human body.
Treatment of extensive wounds
Scientists at the Wake Forest Institute of Regenerative Medicine have developed a mobile 3D printer that can print skin cells grown from patient tissue directly over a wound.
Major burns are traditionally treated by grafting the patient's healthy skin over damaged skin. This method is quite traumatic, in addition, it cannot be applied in the absence of healthy skin on the body.
The ZScanner Z700 handheld scanner, developed by scientists, will determine the depth and size of the wound. Based on this data, 3D bioprinting equipment creates epidermal, dermal and subcutaneous skin cells at appropriate depths, completely covering the wound. The 3D printer consists of an extruder (print head) with eight nozzles with a diameter of 260 microns with independent dispensers, moving along three axes. Especially for this model of a 3D printer, scientists have developed a bioink based on epidermal keratinocytes and autologous dermal fibroblasts in a hydrogel carrier.
Printing of artificial corneas
A group of scientists from the School of Medicine of Kungpuk National University and Pohang University of Science and Technology in South Korea has developed a technology for 3D printing of an artificial cornea from a patient's tissue material (stem cells and decellularized corneal stroma) on a Nano Master SMP-III 3D bioprinter with microextrusion technology. The cornea, made on a 3D printer and filled with biomaterial, is cultivated for four weeks in an incubator at a temperature of 37 degrees.
The resulting material can completely replace the donor cornea. Its main advantage is full compatibility with the patient's tissues. Cellular 3D printing reproduces the natural microenvironment of the eye as closely as possible, allowing for natural transparency. Unlike traditional artificial corneas made of synthetic polymers and recombinant collagen, this material takes root just fine. In addition, its use will help reduce the waiting time for surgery, which is on average 6 years (for example, South Korea).
Manufacture of the Volt Bipolar Surgical Clamp for Laparoscopic Operations
In 2016, Bite developed a miniature 3D printed laparoscopic instrument for clamping and coagulating tissues and vessels, designed for minimally invasive surgery. The clamp has been successfully tested on porcine liver. The design of the instrument allows easy adjustment of the geometry of the tip and shaft, taking into account the anatomy of the patient and the specifics of the surgical intervention.
Hip prosthesis print
Employees of the Institute of Traumatology and Orthopedics. R.R. Vreden, together with colleagues from LETI (St. Petersburg), worked on the design of a titanium prosthesis of the hip joint. First, scientists made a model of the bone out of plastic based on computed tomography. Then the implant was designed and its positioning on the bone was corrected. The next step was planning the operation on a mock-up and, to top it off, printing the prosthesis on a 3D printer. The implant was successfully implanted in a patient with an almost completely destroyed hip joint, as a result of which the person regained the ability to walk independently.
Production of dental crowns
Using the Farsoon FS121M 3D printer, working on SLM technology, allows you to simplify and speed up the printing of dental crowns and other objects of complex shape. The equipment can print 160 metal crowns in just 3 hours. The highest precision of products is achieved through the use of a laser beam with a spot diameter of 40 microns and a fine powder.
Reconstruction of the auricle (cartilage production)
Using Rokit Dr. 3D printer. Invivo 4D Premium with a syringe dispenser and consumables such as copolymer of glycolic and lactic acids (PLGA) and hydroxyapatite (HAp) can print the flexible structures needed for cartilage reconstruction. This technology is used in reconstructive surgery of the outer ear.
Dental Impression Printing
Raise3D Pro2 3D printer with FDM technology allows you to make dental impressions for orthodontics. The huge advantage of this technique is the reduction of time spent with the patient. A 3D model is created using a volumetric scanner in just 1 minute. On its basis, a plastic prototype is printed, which is used by orthodontists for subsequent work. The technology is widely used by physicians at the French hospital Ortho 34.
Creation of a medical exoskeleton
Barlomiej Gaczorek Design Studio specialists have developed a model of a complex supporting exoskeleton for hands and printed its details on a Sinterit Lisa 3D SLS printer. The use of SLS selective sintering technology made it possible to achieve the highest precision of structural elements.
Making a model of the cardiovascular system
In rare forms of cardiovascular diseases, especially in newborns, the risk of making mistakes in the preparation of a therapy regimen is too high, which requires a detailed development of a treatment program. Specialists at the University Clinical Center in Gdansk (Poland) use the Sinterit Lisa SLS printer to work with complex diagnoses. Doctors have created a three-dimensional model of the cardiovascular system, designed for a detailed study of the anomaly and preparation for surgery.
Creation of prostheses
The use of FDM printers is indispensable in situations where it is necessary to facilitate and reduce the cost of manufacturing exclusive prostheses. Canadian designer Albert Fung has developed a 3D digital model of a prosthesis that has become the basis for the production of prosthetic hands for Sierra Leoneans affected by the civil war.