Space hulk 3d print
3d Printed Space Hulk Terrain (stl files from Printable Scenery) – OnTableTop – Home of Beasts of War
Recommendations: 233
About the Project
I've been inspired lately by the community focus surrounding Space Hulk and having more or less printed enough buildings for a fantasy town board, I can now redirect the printer (a Flashforge Finder 3d printer)
This Project is Active
View Oldest Entries First
Nov 23 2018
Tutoring 5
Skill 5
Idea 7
4 Comments
Got the game setup to play for the first time and I’m really please with it.
Should have read the instructions an I would have had the right starting squads, but hey ho.
Ironically the printers are still going, and will complete 2 parts of the ship while the game is playing – that’s M2 technology right there.
I’ll keep going with this past the deadline as it’s been epic and I ‘ll probably look to do more on the painting / customising side. Producing all the parts in the timeframe has been the big constraint on the project but it was great fun to do.
Space Hulk 3d Printed Board
Space Hulk 3d Printed Board
Space Hulk 3d Printed Board
Space Hulk 3d Printed Board
Space Hulk 3d Printed Board
Space Hulk 3d Printed Board
Space Hulk 3d Printed Board
Space Hulk 3d Printed Board
Space Hulk 3d Printed Board
Space Hulk 3d Printed Board
Nov 23 2018
Tutoring 5
Skill 3
Idea 5
No Comments
Getting the last of the painting done. The doors now have their main colour down, there aren’t enough of them , so we’ll use a few from the main box.
The black door at the back is hot off the press – no time to paint, but we’ll use it anyway
We have a number of the plastic rafts as a left over from the so we can draw some squares on these and use them in place of the corridor sections that we don’t have.
The Doors the we have so far
Plastic Rafts - a byproduct of the printing Process
Flashforge Finder Producing and dead end back wall
Flashforge Adventurer 3 producing a door
Nov 23 2018
Tutoring 3
Skill 3
Idea 5
No Comments
Some of the Space Hulk Board Parts Stacked Up
So this is really the last night before the deadline. I have enough parts to play a game, not enough to complete the board, but roughly 75-80% of it at a rough estimate.
Having the second printer (the Adventurer 3) helped boost the project, but it took longer than anticipated to get it to find it’s rhythm in printing parts with low duds – it doesn’t really like the filament that I’ve been using for the Finder.
The finder became super reliable later in the project (essentially as soon as I ordered the 2nd one and it ended up printing most of the parts.)
you have a lot of time to find other stuff to do before you can really paint terrain sets I’ve looked at models and I think I have enough of those I’ve built some scouts using reivers and metal devastator weapons for the ultramarine game. I’ve looked into Tyranid attack and started looking at warriors.
I’ve added the image gallery below with some pics from the final push….
Prospero Minis on the Space hulk board
Deathwatch Overkill minis on the Space Hulk terrain
Custards on a Space Hulk board
I’ve spent a bit of time just swapping the minis for different ones – Prospero, Calth, Deathwatch overkill, Dark Imperium, ‘Ultra Marines’ [scouts] event the Ravening (I should add that I was just being silly here, but I can kitbash the stl files to make wider corridors and I do have the Speed Freaks set) and each time you do , the lore swaps with it, an ti becomes a whole different game.
I had a lot of fun just swapping minis and thinking, what if….. anyway I’ve run out of layouts that I can add to this post so I guess I’ll have to leave it here.
What are the Ravenwing doing here?
Even the Deathguard want in on the action
Nov 21 2018
Tutoring 2
Skill 3
Idea 4
No Comments
Thess so far based on the updated list.
3x Corridor 5 [3/3 built]
3x Corridor 3 (17 hours Each Estimated, 20 hours Actual) [3/3 built]
7x Corridor 2 [5/7 built]
2x Corridor 1 (7 hours Each) [4/6 built]
5x Corridor + (17 hours Each [Actual])[1/5 built]
5x Corridor T [4/5 built]
4x Corridor Corner [4/4 built]
4x Dead End [1/4 built]
2x Chutes / Lifts [0/2 built]
1x Offset Crossing [0/2 built needs designed]
2x T Room (4 parts, A=9 h, B=11 h, C= 11 h, D= 14 h Total = 45 Hours)
1x + Room [2/1 built]
1x ortho-Room [2/1 built]
1x para-Room [0/1 built]
1x 3×4 Room ( we can kitbash this from the regular single door room in FlashPrint) [0/1 built]
Nov 11 2018
Tutoring 3
Skill 2
Idea 3
No Comments
Thess so far based on the updated list.
3x Corridor 5 [3/3 built]
3x Corridor 3 (17 hours Each Estimated, 20 hours Actual) [3/3 built]
7x Corridor 2 [2/7 built]
2x Corridor 1 (7 hours Each) [0/2 built]
5x Corridor + (17 hours Each [Actual])[1/5 built]
5x Corridor T [4/5 built]
4x Corridor Corner [0/4 built]
4x Dead End [1/4 built]
2x Chutes / Lifts [0/2 built]
1x Offset Crossing [0/2 built needs designed]
2x T Room (4 parts, A=9 h, B=11 h, C= 11 h, D= 14 h Total = 45 Hours)
1x + Room [2/1 built]
1x ortho-Room [0/1 built]
1x para-Room [0/1 built]
1x 3×4 Room ( we can kitbash this from the regular single door room in FlashPrint) [0/1 built]
Printing progress 11/ November
Box of Space Hulk parts so far
Nov 10 2018
Tutoring 3
Skill 5
Idea 5
No Comments
There were a number of alternative / spin-off games and expansions for the Space Hulk Game system / components, including Ultra Marines, Tyranid Attack, Deathwing, Genestealer (with Space Crusade in the mix as well)
I’m going to prepare the the models to play some of the other games as well with the terrain set.
This will allow me to keep going with the models while the 2 printers are fed PLA and ABS 24/7 to get the models out.
Ultra Marine Board Game Box
Ultra Marine Board game Contents
Ultra Marine Gameplay Image
To Play the game (or a modernised version of it) needs the following models:
- 1 Squad of Ultramarine Scouts
- 1 Squad of Blood Angels Scouts
- 1 Squad of Dark Angels Scouts
- 1 Squad of Space Wolves Scouts
All Squads are made up of the following
- 1 Sargent with bolt pistol / Chainsword
- 1 Scout with a Heavy bolter and Combat knife
- 3 Scouts with a bolt pistol and Combat Knife
I never liked the old scout models, so we are going to start the models off with some Primaris Reivers and convert them.
I ordered some of the old metal shoulder-mounted heavy weapons for this conversion of of ebay. as below, using some spare arms and shoulderpads from the intercessors kit I converted them to the models below.
Prima
Space Marine Boxed Game Components that are ready to go.
I have 3 Reivers already done for the Ultramarines in my metallic scheme, so just the 2 more to do.
I’m just going to proxy the heavy weapons as I do quite like the las cannon and the Heavy Plasma which will be fire for me.
I am on the lookout for a digital copy of the rule book for this game, and I will probably need to get a s/h set tor really play, however I can get the board and minis ready in advance of that.
Nov 5 2018
Tutoring 2
Skill 5
Idea 5
No Comments
I’ve got another dozen or so parts printed and have laid them out – it’s starting to take shape.
The bulk of the parts are still being printed by the Finder, I’m still getting used to the Adventurer 3, it’s essentially contributed the 3 parts of the room and the doors. ( I said I would leave these, but they are actually quite good, there are alternative models for open doors and destroyed doors that I haven’t really touched on – I need 18 doors for the layout, this represents many of them (I think there is 9ish printed) I would probably get away with 12 open and 4 destroyed for most games.
Printed Parts so far (5th December)
3d Printed Space Hull Corridor with Terminators and Broodlord
Space Hulk Terminator in Corridor
Space Hulk Terminaotor Close Up
Space Hulk Terminator with Broodlord
Space Hulk Heavy Flamer in corridor
Space Hulk Scale Comparison - Landraider with 5-square corridor
Oct 29 2018
Tutoring 6
Skill 2
Idea 5
1 Comment
So just a quick update on progress.
I now have 8 parts printed and am getting ready to start on the a few of the rooms.
Space Hulk Corridors
Space Hulk Mission Map
Getting started with the new printer
The new printer arrived today so I’m just testing it out with a door print before I get it started on the rooms.
Flashforge Adventurer 3 Printing a Door
The first thing I’ll need is a 1kg reel adaptor, so I have got a design for that from thingiverse and have started the other printer on printing that out.
This should work better than with the finder as the material feeds through the end-of-material sensor (with the finder there was not way to do this and you had to just make sure there was enough left on the reel – or wind the material onto the smaller reels that fit inside the cartridge slot (or disable the sensor)
FlashPrint Buid Estimate for a 1KG spool adaptor for the FlashForge Adventurer 3
Oct 25 2018
Tutoring 4
Skill 3
Idea 2
No Comments
I’ve the first 2 Pieces printed out and have Used some the following colours:
- Stynlrez Black Primer
- Stynlrez Grey Primer
- Vallejo Ger C Beige
- Vallejo Deck Tan
- Vallejo Ivory
Next stages would be a 50% Grey wash and a white drybrush.
Not sure if it’s light enough though – might go heavier on the Ivory before I do the last few stages.
Oct 25 2018
Tutoring 4
Skill 2
Idea 4
1 Comment
I’ve been considering for a while what the best way to solve the print capacity issues are for terrain printing the Finder on it’s own would probably have to run, 24/7, constantly monitored and fed with stc (opps, I mean stl) files to get close to the desired timeline.
It’s not just this project, during the last one (fantasy terrain board buildings), the rate of producing components using a single printer was a significant project constraint – essentially I’m finding 2-3 months is too long to print the components for a board, and I have generally lost interest by the time the parts are ready.
I’ve had a look at commercial options, but they seem geared towards rapid prototyping rather than low-cost wargames terrain production. I tried the insta-quotes on a few of the more popular on-line printing websites I founds that most didn’t offer options like Infill or scaling on the site, and most could not handle the upload of stls greater than 50MB easily.
The best quote I could obtain was £50 is at 100% scale, so that would be £70 at 140% which isn’t really cost effective. (though I’d Imagine these would be at a higher resolution than I can do.)
I looked at adding an extra finder, but new ones weren’t cost effective compared with other models and second hand ones on ebay had an asking price too close to the recently discounted new price.
So the decision I made was to add a Flashforge Adventurer 3 (@ £340), with a view to running both and essentially double the rate that I can produce the parts without killing myself keeping them running.
This should allow me to build the terrain density that I want at the notice I want.
FlashForge Adventurer 3 - Adding extra printing capacity
Oct 25 2018
Tutoring 2
Skill 4
Idea 4
No Comments
We have our first board piece printed, with a build time of 20 hours.
It’s come out rather well. I’ve taken a few pics with minis – the Primaris as the are the better models that I own feature in these shots.
I’m really pleased with how the pieces have scaled up – this not only allows you to use 40mm bases, There is also room to get my hands in without demolishing everything.
I’ve already got the next piece underway before I put this post together so as not to waste any printer time.
The Next piece is going to be a crossroads as below:
Oct 25 2018
Tutoring 2
Skill 2
Idea 4
No Comments
To try an reduce the warping, we’ve added a few draught shields to our Finder to see if that makes a difference.
As you can see, only the highest grade parts were used in the this mod and in no way did we stick 2 kitchen towels on the sides with masking tape.
FlashForge Finder with makeshift draught excluders
We had an issue with the first print attempt for the 3-square corridor section which failed at 10ish hours – this sometimes happens when you have the usb cable connected and the pc goes into sleep mode – the printer stops and goes immediately off.
The prints are below at the 140% scale I mentioned earlier and the minis pictured are on 40mm bases.
The things to take away from this are:
- Remember to unplug the USB cable when printing
- Try to keep the door closed when starting off jobs as this helps with draughts (which leads to uneven drying and warping)
- take a bit of care removing the print from the bed in particular the OpenLOCK connector as I broke one of them pulling the print off the bed – running the plastic card underneath should do for this, but I wasn’t being careful as the print failed.
Failed Print with Warping and 40mm bases
Failed Print with Warping and 40mm bases
I also managed to sit on this guy while I was taking the pics and really he didn’t stand a chance. (This is completely optional and not recommended for your own projects.)
Oct 23 2018
Tutoring 4
Skill 4
Idea 5
No Comments
Traditional colour schemes for space hulk are usually in line with the board tiles and are grey / gunmetal.
I’ve painted a few vehicle interiors in the last few years with lighter, schemes, with brown’s and creams, built up to white, then a black wash, so I’m thinking that might be an interesting idea.
I would probably try out some chipping and light damage to the edges. I think I would avoid rust (as it needs water and air and in space, there isn’t really very much of either) but corrosion around pipework and dirty / grime would be cool.
Oct 23 2018
Tutoring 5
Skill 4
Idea 4
No Comments
Breaking up larger pieces to print on the smaller print bed is relatively straight-forward to do with the bundled software.
Since we know that 3×3 squares will fit on our print bed we just need to break the room into 4 pieces in a way that makes it easiest to hide the join when we glue the pieces together.
With the tiling system that we are using, cutting between the floor squares should give us the best results.
Flash Print - Resize and rotate the Image to make it easier to setup the cut
Flash Print Setting the x-axis cut to go along panel lines
Flash Print - The Room cut into 4 pieces that can fit on the print bed
With all the cuts made, the 4 pieces are saved as separate files so they can be estimated separately and printed later.
Flash Print Build Estimate for the first Room Piece
Oct 23 2018
Tutoring 7
Skill 5
Idea 6
1 Comment
Well, nobody said it was going to be quick – 17 hours will be the longest single part I have printed, but we are underway and that’s the main thing.
3 Tile Coridor in Flashforge Visualiser
With the raft in place the print bed is entirely consumed with the print.
The OpenLOCK Socket is visible on the left side under the floor.
Planning the Next Pieces
While this is running, I’m going to do a little bit to plan some of my prints – essentially, I don’t have the luxury of leaving this running when I am at work, or when I go to bed, so I need to really organise them so I can run them with 4-5 hour blocks (when I get home after work) and probably some 10 hour blocks (for weekends)
Let’s take a look at the traditionally smallest section for Space Hulk.
It looks like this is estimated at 6:45 (which probably means it will take 8 hours to print.)
Flash Print scaling parts to 140% to allow for modern base sizes
Flash Print build estimate for single square corridor
Corruption's Heart Mission Map
From the Mission Map above, it looks like we are going to need a lot of Pieces.
3x Corridor 5
3x Corridor 3 (17 hours Each Estimated, 20 hours Actual) [1/3 built]
7x Corridor 2
2x Corridor 1 (7 hours Each)
5x Corridor + (17 hours Each [Actual])[1/5 Built]
5x Corridor T
4x Corridor Corner
4x Dead End
2x Chutes / Lifts
1x Offset Crossing
2x T Room (4 parts, A=9 h, B=11 h, C= 11 h, D= 14 h Total = 45 Hours)
1x + Room
1x ortho-Room
1x para-Room
1x 3×4 Room ( we can kitbash this from the regular single door room in FlashPrint)
From the very early build estimates it is starting to look as if there isn’t any chance of the board being complete in the 6 or so weeks remaining for the project, so it looks like we’ll need to try and save some time and scale back some of the plans a bit.
If we use the original doors from 4th edition, that will save some printer time.
If we use a 2d laser printer, we can print out 140% tiles for the main space hulk board pieces, then we can move the finished parts (however many we end up with) around so that they are always in the active area – this should give the project as a whole a degree of robustness.
Oct 22 2018
Tutoring 5
Skill 5
Idea 7
3 Comments
I have a number of models that are pre painted and ready to go for once the scenery is in place.
The cultists from the Deathwatch Overkill board game are good to go (well, they could have been more finished, but that what I have, anyway, I’ll be too busy with the scenery to paint the minis.)
The bases for the models are from the Sci-Fi Deck range from Dark Arts Miniatures, should anyone be wondering.
Rules for Hybrid Models (Genestealer Cults)
Rules were added for the models included inside the Deathwatch Overkill box in an Issue of White Dwarf – I have tracked down a pdf of these rules and included them below.
I’ve included a screenshot of one of the pages below – see the pdf for the complete rules set.
Oct 22 2018
Tutoring 7
Skill 4
Idea 6
2 Comments
I’ll be using the Flashforge Finder for this Project
The finder has a 140mm x 140mm (unheated) print bed and prints using PLA only. The only modification that has been made is that an external printer reel has been added to allow me to use the 1kg reels that I can get off Amazon Subscribe and Save. I’ll be using natural white PLA.
In terms of Preparation, I use the purple ‘disappearing’ glue, (which turns clear when dry) on the print bed to help with adhesion and reduce warping
In terms of the printer settings, I am printing with a raft, and a temp setting of 190°C and the standard infill of 10%. Cutting down the temp from 220°C as this helps reduce warping. ( a small degree of warping is ok – it usually just affects the outside edge, not the inside, so you can just fill with milliput.
I use the old loyalty card to prise the print from the bed without scratching the build surface (I did already scratch the surface while using a scalpel – this is to stop it getting worse until I can get a new build surface at a not ridiculous price).
Thick and Thin Superglue – The thick stuff really helps gluing the big blocks together, then you can fil the gaps using the thin stuff for extra rigidity.
Oct 22 2018
Tutoring 8
Skill 5
Idea 9
1 Comment
I used models from Printable Scenery with my fantasy terrain project and have printed 10 buildings for that using their models.
I’ve found the models I’ve already used from Printable Scenery easy to get going with, the models thus far have printed with just a brim and no need for support structures which need clean up or a raft, so I’m happy to continue with this. Also worthy of note is the extra support for small printers, with extra copies of the objects pre-cut to work with smaller print beds – this is useful for me as it meant that I could print the objects without having to learn how to slice them up (though this is actually pretty easy with the software that comes with the printer) .
The models seem very Space Hulk focussed – that is the corridor tiles seem to fit neatly on a tile-for-square along the original board lines and the rooms and corridor pieces all seem to be covered. Boarding Rams introduced in 4th Edition are also modelled.
The tiles are scaled at 30mm in this set – a decision that I will have to make is whether to print as is, and use the models at that size or to print them at 133% (or so depending on tolerances) and use terminators at their modern base sizes.
The 3d objects are (Barges aside for obvious reasons) OpenLOCK compatible, which allows the pieces to be connected together with clips that you also print. This system is also used on dungeon crawlers and I have seen it appear as a feature on a number of 3d printable Terrain over the last 6 months.
Creating a 3D Space Hulk board in Terrain Tinker
Back in 1989 Games Workshop released the first edition of its widely popular Space Hulk board game. Over 30 years and four editions, The story-driven boarding actions continue to entertain wargamers and board gamers alike. As great as it is, the game can be massively improved by replacing the cardboard corridors with fully 3D components. Now with Terrain Tinker’s latest Space Port Kickstarter, it’s easy to design and print yourself a fully 3D printable Spacehulk set.
Terrain Tinker
For those unfamiliar with it, Terrain Tinker lets you combine OpenLOCK tiles into larger models ready to export and print. The exclusive ‘Spaceship’ set from the current Kickstarter is perfect for recreating the hulk. Using 2×2 floor tiles for each square of the cardboard components, map out the various corridors.
From here, just get creative with the different combinations of 2×1 and 1×1 interior walls available in the set. The exterior walls are not necessary, but help to ramp up the Space Hulks cool factor. once satisfied, you can export the designs as combined sections for the 3D printer. Or, for those gaming digitally, export your creations as 3D assets for use in online board game simulators.
Painting the corridors
Once printed, with a little bit of drybrushing you can get the components painted quickly to a table-ready level. All the paints below, excluding Citadels Typhus Corrosion, can be found in the Army Painter range.
- Basecoat the entire model with Gun Metal spray, making sure to get underneath the interior walls overhangs.
- Once completely dry, heavily dry-brush the exterior with Army Painter ‘Spaceship Exterior’ and interior walls with Drake Tooth.
- Pick out some of the external panels with Vampire Red, don’t color in too many panels, and try to keep it random.
- pick out some of the exterior details, open internal panels, and switches with Gun Metal.
- speckle patches Typhus Corrosion technical paint with a relatively dry brush on the walls and floors. use an old brush for this step, as the small particles of grit in the paint will ruin a good brush.
- Wash the entire model with a 1:1 ratio of Vallejo black wash and water.
If you want to take it one step further, before speckling the Typhus Corrosion, lightly air-brush thin lines of Vallejo Air Charred Brown between the exterior panels and on the edges of the floor squares.
Ready to play Space Hulk!
With the models in play, the corridors and rooms look fantastic. You could even fill an entire board with corridors for boarding-action games of Warhammer 40K or Horus Heresy.
It’s never been easier to build and print cool parts and buildings for your home games. Upgrading your Space Hulk is but one of many options available in Terrain Tinker’s latest Kickstarter. These sets are the first Exclusive to the platform, so recommend getting in quick to get the best deal on them.
STL file She-Hulk interior
Wound Tracker Preliminary Support
€1.90
Industrial sector - Modular relief system
€17.11 -25% 12.83 €
Free
Necron Gauge
Free
Inspiration Token
Free
Monster token for board games
Free
Modular area - industrial area | Sample file
Free
Best 3D printer files in Game category
Link Goddess Sword (without painting)
Free
nerf bouncing target for toy shooting spinners TARGET
Free
Secret design
WWI Allied officers pack.
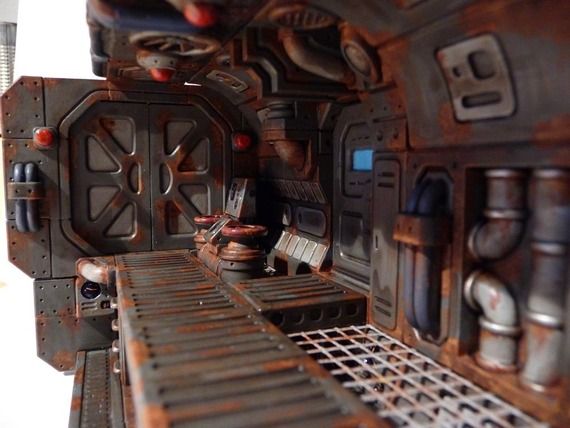
€5.30
Tabaxi Sailor - Tabletop Miniature
Free
Residual Evil 4 rocket launcher handle
Free
Wingspan Insert -- Sleeved Cards
Free
Controller holder under table
Free
Bestsellers in the Game category nine0035
She-Hulk interior - boarding operations and terrain for the kill team
8.08 €
Flying unicorn
1.77 €
Tordeir Stormfolk
9.50 €
Heavy Imperial Fire Support Weapon [Preliminary Support]
5 €
Articulated dragon
3. 79 €
WARFORGED VOIDWALKER EXOSUIT UPGRADE KIT
9,50 €
Destroyers of Nehron Lochust
3 €
USS EnterSurprise - printable game container for tiny F14 jet fighters
3.79 €
Batman's crossbow weapon / Seal in place
2,50 €
Octopus 2.0
3.79 €
Voidwalker Exosuits Truescale
14.83 €
Beaky Boyz Builder: PF_MK-Six
12.36 €
Army Jeep
2 €
Imperial Heavy Weapons & Regimental Flags [OFFERED]
3 €
Enourmous Imperial Heavy Tank
10 €
Nintendo Switch Crystal Dock - classic and OLED version
3. 15 €
Do you want to support Cults?
Do you like Cults and want to help us continue our journey on our own ? Please note that we are a small team of 3 people, so supporting us in maintaining activities and creating future developments is very easy. Here are 4 solutions available to everyone:
-
AD: Disable your AdBlock banner blocker and click on our banner ads.
-
AFFILIATION: Shop online with our affiliate links here Amazon. nine0006
-
DONATIONS: If you want, you can donate via PayPal here.
-
* INVITE FRIENDS: * Invite your friends, discover the platform and great 3D files shared by the community!
The small firm that started the 3D printing revolution in space
3D printing continues to make its way into the rocket industry. For example, back in 2014, SpaceX used a 3D printed part of the main oxidizer valve. And Blue Origin uses 3D printed components in its powerful BE-4 engine. nine0006
But one of the organizations with the most experience with 3D printed parts is Rocket Lab based in New Zealand and the US. Founded in 2006 by Peter Beck, Rocket Lab is today the leader in small satellite launches with its Electron rocket. So far, there have been successful launches of six of these rockets – each powered by nine Rutherford engines, built primarily from 3D printed metal parts. In addition, there are a number of other elements obtained using 3D printing technology on board these rockets. nine0006
In the traditional subtractive manufacturing approach, the final products are cut from a block of material. 3D printing technology, known as additive manufacturing, allows you to create the desired shape of the part layer by layer. This makes it possible to obtain lighter objects with a complex internal structure that cannot be created in any other way.
Today, Beck, who became President and Chief Engineer of Rocket Lab, discusses with us the company's decision to invest heavily in 3D printing technology and how this technology is being used in the rocket industry today. nine0006
How do you see the role of 3D printing in the development of rocket science from the moment you decided to use it to create your engines?
When we started using metal 3d printing, we were among the first to use this technology. I remember when we first announced the Rutherford engine at the National Space Symposium four years ago, everyone looked at it and said, "this is very strange." But today, if at least part of your engine was not created on a 3d printer, then you are considered behind the times. nine0006
We've sent over 50 Rutherford engines into space - that's more 3D printed engines than anyone in history has done. You can do it once, but succeeding 50 times in a row is another level of process understanding and quality control required.
Can you use off-the-shelf commercial equipment or did you have to build your own?
First, we bought ready-made 3d printers and improved them. We have modified them to meet our requirements. We print parts in such a shape that even today most industries using 3d printers will tell you that such geometry cannot be printed. Even today, a large number of our components go beyond the conventional boundaries of what is possible. nine0006
Have there been any fundamental changes in the design of rockets that you were able to implement only through the use of additive manufacturing?
Of course. I mean, the Rutherford rocket engine, at least as far as we know, is the most successful liquid oxygen and kerosene engine in America, and it performs better than SpaceX's Merlin 1D engine. This is partly due to 3d printing. We 3D print all injectors and we can 3D print the injector geometry that gives us the best mixing and best performance. This cannot be achieved using other manufacturing processes. It's really hard to get a small engine with really big efficiency. nine0006
Do you think that 3d printing offers any advantages specific to rocket science?
Yes, of course. The same can be said about any industry. When very complex components are used, you can chain them together to make more efficient subsystems or higher-level components—more cost effective, or better performing.
But this is where I saw how it's done wrong. Someone will definitely try to make a bracket on a 3d printer. And it will just be a waste of time. It makes no sense to 3d print the bracket. After all, the point is in the technology itself, and not in getting excited about it, and starting to make everything that comes to mind on 3d printers. You need to choose complex components that can be combined together, and there are a lot of such components in a spaceship. nine0006
If you 3D print the entire support structure, and inside it has a bracket that connects not one, but 50 components along the fuel tanks, then this is exactly what we are talking about. This will be a really useful application of this technology.
Was it difficult to attract customers with a 3D printed engine?
Not very good. One such test was a NASA mission flight. NASA very carefully checks every detail of all systems of launch vehicles, and of course they spent a lot of time on the Rutherford engine, understanding the 3D printed components used in it, and the whole technology in general. But everything has been carefully reviewed. nine0006
Do you think early adopters have an advantage when it comes to launching small satellites and 3D printing?
Undoubtedly. Today, a large number of small launch vehicles are being developed. And at the same time, they all focus on the same consumers. Therefore, we predict a truly tough consolidation in the market for small launch vehicles. Right now, this can definitely be considered an inflating bubble. I think that this direction will experience really difficult times in the next 12-18 months.