Rubber like 3d printing
3D Print Rubber - 3D Printing Gaskets
Rubber and rubber-like materials are everywhere in modern industry. Soft materials like latex, silicone, and thermoplastic elastomer are useful in applications that demand flexibility and durability for industrial parts and consumer goods alike.
While rubber manufacturing has historically been the domain of casting and injection molding, modern advances in 3D printers and 3D printed materials have made additive manufacturing the ideal solution for producing small to medium quantities of rubber-like parts.
Our 3D printed rubber services can manufacture high-quality rubber-like parts in as few as two days―all you need is a 3D model! Start your project by getting a quote or keep reading to learn more.
Get a quote for your project using our quoting tools. Our engineers will review your project and get back to you 24 hours or less. 3D printed rubber parts ship in as few as two days!
3D Printed Rubber Applications, From Prototyping to Production
3D printed rubber parts can be used in place of molded rubber for just about any application. Like other methods of 3D printing, rubber prints accurately produce complex internal geometries like lattices and tubes at no extra cost, easily achieving designs that would be impossible with other types of manufacturing.
And because 3D printing doesn’t require any costly molds or tooling, 3D printed rubber parts can be manufactured in just a few days compared to multiple weeks of lead time for injection molding. This combination of high agility and no start-up costs allows rubber 3D printing to excel for both prototyping and small- to medium-sized production runs.
3D printed rubber is ideal for:
Prototypes
Gaskets
Seals
Hoses
Grips
Lids
Plugs
Connectors
Footwear
Tires
Medical Devices
Sporting Goods
Advantages of 3D Printed Rubber vs.
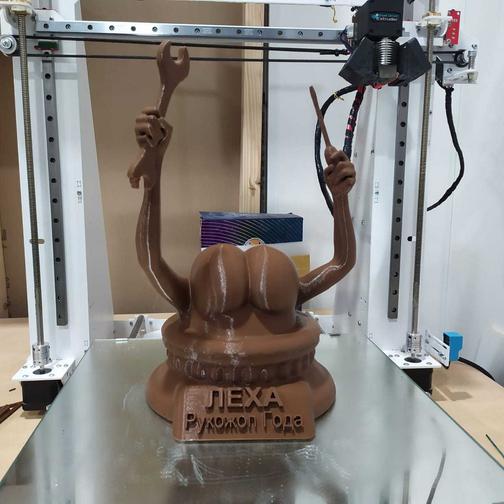
Traditionally, rubber manufacturing has required injection molding, casting, or sheet lamination. Rubber-like materials are far too soft to machine, and 3D printing was restricted to harder plastics for most of its development. Now, new developments in 3D printers and materials have opened up a wide range of new possibilities for 3D printed rubber products. So how does 3D printing compare to casting or injection molding for manufacturing rubber?
Short Lead Times and No Setup Costs
Injection molding requires machined metal molds that cost tens of thousands of dollars and take months to produce. Any design changes require new tools, making adjustments extremely expensive and time-consuming.
In contrast, 3D printing requires no tooling or other setup costs and can begin production immediately. This leads to parts that can be manufactured in as little as one day and much greater affordability at low quantities, making 3D printing Moreover, design changes are easy and can be executed at no additional cost.
The Best Choice for Rubber Prototypes
When it comes to product development, 3D printed rubber is a godsend. Even under the most ideal conditions, traditional technologies take weeks of lead time and tens of thousands of dollars for each new design.
Because 3D printing doesn’t require any tooling or setup, 3D printed parts can quickly be designed and redesigned at no additional cost. This agility has made 3D printing an indispensable part of prototyping and product development.
A Question of Quantity
As a result of these differences in lead times and setup costs, 3D printing is much more economical for small- to medium-volume production, while casting and injection molding provide greater value for productions of 1000 parts or more.
Although metal molds are expensive, molded parts become very cheap to produce once the tooling is made. When those initial costs are spread out over thousands of parts, individual part costs plummet, making injection molding the least expensive technology around for high-volume manufacturing.
3D printing, on the other hand, generally stops providing additional per part savings once part quantities exceed the capacity of a single machine. As a result, 3D printing has a much flatter cost curve that makes it a great option for small to medium quantities but significantly less economical for large production runs.
Unlimited Design Possibilities
Rubber 3D printing can easily achieve complicated designs that would simply not be possible with other manufacturing technologies. From interior cavities and lattices to variable wall thicknesses, organic shapes and built-in hoses—all of which are difficult or impossible to create with injection molding—3D printed rubber parts unlock endless new design options. You can even combine multi-part assemblies into single pieces, saving costs and improving functionality.
Plus, 3D printed parts can be highly customized, down to single parts at a time, without additional costs. This is especially useful for industries like medicine or athletics that have a high demand for products customized to each individual user. Needless to say, this would be extraordinarily expensive with casting or injection molding.
To learn more about the unique design capabilities of 3D printing, check out our Design for Additive Manufacturing (DfAM) Guide.
Is It Really Rubber?
3D Printed Rubber Materials
The answer to whether 3D printed rubber is really rubber depends who you ask. There are a lot of materials that are referred to as rubber: thermoplastic polyurethane, thermoplastic elastomer, silicone, and, of course, natural rubber!
Natural rubber, also known as latex, cannot be liquefied and re-solidified in the manner required by 3D printers. However, thermoplastic elastomers can achieve similar levels of flexibility and softness to rubber and have the thermal properties necessary for 3D printing.
The most effective rubber-like materials for 3D printing are thermoplastic polyurethane (TPU) and thermoplastic elastomer (TPE). It’s important to note, however, that both TPU and TPE refer to multiple materials. In fact, TPU is really a type of TPE―distinguished by its use of polyurethane and increased hardness.
Thermoplastic Polyurethane (TPU)
Thermoplastic polyurethane (TPU) is valued by engineers for its flexibility and strength. Not only does TPU’s hardness (Shore 85A to 95A) make it easier to print than TPE, but it also provides higher abrasion, chemical and thermal resistance. Moreover, its resistance to oil and grease makes it a great fit for hoses, gaskets and seals. While not as soft as natural rubber, printed TPU can achieve thinner walls than molded parts to create a similar level of flexibility.
TPU can be 3D printed with Multi Jet Fusion or selective laser sintering and is widely used in transportation, medicine, home goods, consumer electronics, and more.
Thermoplastic Elastomer (TPE)
Thermoplastic elastomer (TPE) is softer than TPU―Shore 40A to 70A—and offers moderate abrasion, chemical and thermal resistance. TPE parts can be trickier to print than TPU due to the material’s softness, but it offers a smoother finish.
Nylon TPE is available for selective laser sintering and is used in many of the same industries as TPU. However, because softer TPE materials are not yet available for Multi Jet Fusion, TPE parts are more expensive and slower to produce.
Rubber Printing Services
Multi Jet Fusion (MJF)
Multi Jet Fusion 3D printing is the fastest, most affordable, and most effective option for most 3D printing projects. It is also the newest printing technology to allow rubber printing, with TPU01 options available in black or gray.
MJF prints combine industrial strength, accurate fine details and a high-quality finish to create parts that are equally suited to industrial parts and commercial products. With lead times as little as one day, MJF is the premier printing option for prototypes and small- to medium-sized production runs.
Selective Laser Sintering (SLS)
Selective laser sintering prints nylon TPE parts with excellent mechanical strength but is more expensive and slower than MJF. SLS parts have a medium-quality finish and larger surfaces can warp.
This technology scales relatively well at medium volumes and is generally cheaper than FDM at those quantities. SLS can achieve slightly larger part sizes than MJF.
Start Rubber 3D Printing Today
If you need rubber manufacturing for your business, RapidMade can help you take your projects from 3D models to high-quality 3D printed rubber parts in as few as two days. When you work with RapidMade, you get a team of 3D printed experts dedicated to helping you succeed.
Learn more about our 3D Printing Services and get started today by requesting a quote. We’ll review your project and get back to you within one day!
Is 3D Printing with rubber possible? – Beamler
Note: this is an article from 2018. Since this article was published 3D printing with silicone has become possible. Read more about it in our article:
Is 3D Printing with Silicone possible?
July 15, 2020
One of the greatest breakthroughs in the field of 3D printing materials in recent years was the launch of a process that makes 3D printing
Read More »
At Beamler, we often get inquiries from customers interested to know whether 3D printing with rubber is possible. Unfortunately, this is not possible because rubber cannot become fluid controllably – which is a requirement to 3D print a material.
About Rubber
Rubber is an organic material with a gummy texture. Being organic means that its properties cannot be influenced by an external factor. It is true that we can shape rubber at high temperatures by using molds. However, once it goes through vulcanization, the material will never be on its fluid state again. Actually, by applying heat into vulcanized rubber would simply burn it.
Nonetheless, just like Silicone, the production of rubber parts through traditional techniques requires the usage of inject molding. This is extremely expensive for the production of small batches due to the high cost of preparing the molds.
Rubber-like 3D printing materials
The good news is that it is possible to 3D print parts with a rubber-like material. In fact, these 3D printing materials are excellent substitutes for rubber. Thermoplastic elastomers, also known as TPE’s, are basically a type of plastic that has been engineered to mimic the crucial qualities that made rubber so attractive. TPE’s combine flexibility with durability, bending and compressing just like rubber. These 3D printing materials allow engineers to determine which properties from rubber they want to simulate at the desired levels, whether it is heat resistance, abrasion or others.
Rubber-like materials are suitable for the production of seals, soft gripe handles or also, for instance, multi-material prototypes that need shock absorption.
Rubber-like materials on Beamler’s Database
Agilus30 Black FLX985 & Agilus30 FLX935
This material developed by Stratasys for Polyjet printers is a great option for verifying advanced designs and prototyping. Available in black and transparent, it simulates the look & feel as well as the functionality of rubber-like goods.
Applications: Overmolds, coatings, jigs and fixtures, grips and many others.
DuraForm Flex
Developed by 3D Systems to be printed using SLS technologies, this tear-resistant rubber-like material can resist harsh environments while ensuring long-term stability. Available in white, this material is suitable for durable prototypes.
Applications: Ear molds, sports footwears, hoses and many others.
E-Model Flex Series
EvisionTEC developed this material for SLAs printers. It is a great choice for a wide range of dental and orthodontic models that require highly precise details.
Applications: Dental models, production-quality design prototypes and end products.
Somos 201
Developed for SLS printers by 3D systems, this material allows engineers to quickly produce complex prototypes.
Applications: Gaskets, flexible prototypes, demonstration models
3D printer in tire making.
Creativity
Subscribe to the author
Subscribe
Don't want
116
Many of my friends are still trying to convince me of the uselessness of a 3D printer, they say, 'well, you can print cubes, snakes, and all sorts of bushings and get bored'. But nifiga, not tired =). I found another use for a 3D printer in another detail.
A long time ago I made tires from silicone, by pouring into an epoxy matrix. About how the matrix was made is a completely different story.
Well, that's it. There is a 3D printer ... but, so that, I think not to print a matrix on it? Ay, yes.
We model the tire, cut the tread and in the halves of the matrix with the 'indent' element we make the drawings on it.
We make an insert between the halves to select an extra volume and make the tire profile.
Due to the specific shape of the insert, I made the supports myself. Width 0.3. I have long understood that in such models it is better to do supports yourself than to watch how the corners of the model lie between the grids / support lines (and this is on filling the support with 40% !sic)
A little background, to the current version:
Initially I tried to print a treadless donut with a selection inside. Everything worked out, the result pleased.
In the last one, I already decided to pour a solid tire with a transparent sealant. The thin profile turned out to be too thin and wrinkled a lot. But after pulling it out of the matrix, there were sprues on the tire, like on real tires =)
Something like a ship mine...
...let's return to the current upgraded tire model:
Dip the brush into the starch and smuggle the entire matrix. The starch will act as a separator. We mix silicone with starch
Put it into the mold and tighten it all with screws. Cool worms crawled out
Silicone with starch hardens (polymerizes) to moderate hardness in 40 minutes. It's always humid there. You can also pour water into it
The disk for the tire can be made in any shape you like, it all depends on the imagination. I made a simple blank and put a tire on it so that it would be fun to ride it all.
Of course, this tire is not reinforced and is not designed for high speeds. The speed was checked by touching the grinding wheel, the tire was already visually inflated at 4k rpm. There is an idea to make tires with sickle reinforcement, at least along the layer under the tread. Then it should be less inflated.
Small performance characteristics of tires:
- diameter - 70 mm
- weight - 37 g
- width 25 mm
- plastic left - 47m
) Kamaz model or similar.
Here is another use of a 3D printer in an intermediate stage and without the use of flex.
I bow out for this, I still have things to do =)
eleven
Subscribe to the author
Subscribe
Don't want
Hi all.
Finished an order from fans of the "alien" universe. Made with great pleasure...
Read more
Egen_M
Loading
11/15/2022
817
eight
Subscribe to the author
Subscribe
Don't want
2023 according to the Slavic calendar is the year of the Fireman Horse (7031 summer). and not to forget and support...
Read more
176
Follow the author
Subscribe
Don't want
Hello again, dear colleagues!
I'll start my story with a joke of hum...
read more All services
- Volunteer assistance
- Courier Services
- Cleaning Services
- Home master
- Transport and warehouse services
- Furniture robots
- Equipment repair
- Recreational robots
- Budivelni roboti
- Pobutov's services
- Photo and video services
- Jobs on the Internet
- Advertising and marketing
- Development of sites and addenda
- Services for creatures
- Translation Bureau
- Holy organization
- Services of tutors
- Services of trainers
- Services of beauty and health
- Business services
- auto repair
- Services for Prom.
ua
- Logo design
- Interior design
- Website design
- Printing design
- Little ones and illustrations
- Banner design
- 3D design
- Exploration of infographics
- UX/UI design
- More in design
- Druk on T-shirts
- Druk on cups
- Druk polygraphy
- Druk on canvas
- Druk on plastic and skl
- Other services to a friend
Our 3D printing studio will help you solve your problems related to the production of parts as quickly and profitably as possible.