Resin tank 3d printer
Resin vs. Filament 3D Printer: Which is Best for You?
Research Hub > Resin vs. Filament 3D Printer
June 27, 2022
Article
4 min
Resin and filament are the two most common materials used in 3D printing. But which is better for your project, and what equipment do you need?
What's Inside
- What is Stereolithography (SLA) 3D Printing?
- What is Digital Light Processing (DLP) 3D Printing?
- What is Fused Deposition Modeling (FDM) 3D Printing?
-
Filament vs.
Resin Printers
- Which 3D Printer Should You Buy?
SLA and DLP are two different types of resin 3D printers, while FDM are filament 3D printers. Read our breakdown below to compare.
What is Stereolithography (SLA) 3D Printing?
Stereolithography (SLA) is the oldest form of 3D printing. It works by exposing a layer of photosensitive liquid resin to a UV-laser beam; the resin then hardens in the desired pattern, and the object is built layer by layer until it is complete. This allows you to print a model with extremely fine detail.
Objects printed by SLA 3D printers have smooth surfaces, but often the quality depends upon the printer type. SLA resin printers tend to have smaller build plates, so you can't make larger pieces on them. Printing via SLA involves a longer process as printed objects need to be rinsed using a solvent and then put into an ultraviolet oven to complete processing.
What is Digital Light Processing (DLP) 3D Printing?
Digital Light Processing (DLP) is the fastest of all 3D printing methods. A layer of hardened material can be printed in a few seconds and quickly transferred to allow for printing of the next layer. Like SLA, DLP 3D printers use liquid plastic resin, but instead of a UV-laser beam, the resin is melted with arc lamps. This light source causes the impressive printing speeds because the amount of light allows the resin to quickly harden. DLP is a robust technology that produces high-resolution models every time, even allowing you to use cheaper materials for complex and detailed objects.
What is Fused Deposition Modeling (FDM) 3D Printing?
Fused Deposition Modeling (FDM) is filament 3D printing, the most popular and readily available form of 3D printing available on the market. Developed and originally implemented in the 1980s, FDM allows you to print operational prototypes as well as ready-to-use products as such LEGO, plastic gears and much more
All components printed with FDM can go in high performance and engineering-grade thermoplastic, which makes this technology useful for mechanical engineers and manufacturers. Printed pieces have excellent mechanical strength and heat resistance. FDM printers construct 3D objects layer by layer, starting at the bottom and moving upwards by heating and extruding thermoplastic filament. This form of 3D printing is useful in all fields, from new product development to prototyping to end-product manufacturing.
Filament vs. Resin Printers
There are several key factors to consider when deciding whether an FDM or SLA/DLP printer is the right choice for you.
- Cost - When purchasing a 3D printer, it is not only the printer cost that you must take into account; it is the filament or resin cost, as well as other accessory and time demands. On printer cost, FDM printers easily win over SLA/DLP printers at every level. Especially for novices, budgetand entry-level SLA/DLP printers are few and far between.
In addition, you must consider the upkeep of the printer. A spool of filament will cost you $25 or less, with infrequent nozzle replacement given regular cleaning and maintenance. With resin printers, you will need to replace both resin and resin tanks frequently. A tank costs $40 or so, and a liter of resin is around $80.
When comparing costs, an FDM printer is far more affordable.
- Quality - A major consideration in 3D printing is the quality of objects that you will be printing. FDM printers rely on several factors, such as extruder precision, nozzle size and adhesion between layers. Warping, shrinkage and shifting are not uncommon as the layers are slowly squeezed together. However, these issues can be cleaned up in post-processing.
On the other side, SLA/DLP printers provide superb quality because the laser determines fine details, leading to extremely precise, high-quality print jobs. When comparing finished products, resin 3D printing yields better final results.
- Ease of Use - There is a definite learning curve no matter if you choose a filament or resin 3D printer. For filament printers, you will need to remove the final print from the print bed using a palette knife and then perform some post-processing snipping off of excess plastic, as well as a bit of sanding.
For resin printers, removing the final print is a bit more cumbersome as there is a lot of excess resin leftover. In addition, objects will need to be wiped with isopropyl alcohol and sometimes put into an ultraviolet oven for final processing. Both printer types require postprocessing, though filament printers might be a little easier to use.
- Durability - Both types of printers have been shown to form pieces offering high durability. Alternatively, materials such as PETG and ABS can be exposed to heat and UV rays, adding more durability to filament printing. This means that anything from a children’s toy to an outdoor coaster can be printed and they will stay intact if left outside for an extended period.
- Build Volume - Resin printers can vary from smaller build volume to much bigger based on the printer. Many of the entry level printers are standardized at 130 x 80 x 160 mm, printing anything an individual or business could need. 192 x 120 x 150 mm is a smaller size in which more advanced resin printers can produce products at, much smaller than that of your everyday resin printer.
- Print Speed - For most resin printers, a print speed of around 100mm/hour is a good speed if an individual or business has the time on their hands and does not worry too much about efficiency. DLP and SLA printers can achieve a top speed of 720 mm/hour if the details do not matter as much. Those printers tend to be the most effective amongst the rest, so normally the job will be done at a high rate of print speed and look great.
Conclusion: Which 3D Printer Should You Buy?
Choosing the 3D printer that is right for you depends on your needs and the objects that you are creating. Filament and an FDM printer is the right choice for hobbyists and makers, those building low-cost materials, when strength and durability are important or when precision and surface finish aren’t crucial. Resin and an SLA/DLP printer is the right choice when high precision and smooth finish is of utmost importance and cost isn't a factor.
Looking for a 3D printer? Find what you need on CDW.com.
3d Printed Tank - Etsy.de
Etsy is no longer supporting older versions of your web browser in order to ensure that user data remains secure. Please update to the latest version.
Take full advantage of our site features by enabling JavaScript.
Find something memorable, join a community doing good.
(1,000+ relevant results)
Formlabs Form 3 Resin Tray lifetime.

When buying a 3D printer DISCOUNT on plastics and polymers up to 10%
Formlabs Form 3 resin tray service life
06/01/2021 Max Gusev
Formlabs Form 3/Form 3B resin tray service life
One of the most important parameters to control in Formlabs 3D printers is resin bath life. The tray is also called the resin tank - this is one of the design elements of the Formlabs Form 3 or Formlabs Form 3B 3D printers. The required amount of photopolymer resin is automatically loaded into this reservoir, and the material is laser-cured layer by layer through a double transparent film. As a result, a given model is built up on the construction platform.
In Formlabs 3D printers, the resin tank is a consumable item and needs to be replaced periodically. Each tray has its own service life, which will depend on the following parameters:
- time spent on printing;
- type of photopolymer used;
- geometry of products that were printed in this tray;
- resin exposure time, i.
e. the time during which the resin was in the tank, regardless of where the tank itself was stored;
- physical damage;
- temperature.
So when does the resin tank need to be replaced?
The manufacturer recommends that the resin bath in a Form 3 or Form 3B 3D printer should be changed as soon as one of the following occurs: to about 600-800 hours in print. Flexible film wears out, which invariably affects print quality. With repeated printing of the same model in the same place, the film wears out quickly in the tray. It is also possible in cuts, punctures, clouding of the film, gouges and wrinkles.
The tank has reached its maximum service life. Resins vary in composition and some can degrade components in tanks over time. As a result, this can cause resin leakage as well as damage to the 3D printer itself. To avoid this, the bath should be replaced when the maximum service life is reached. If the bath is intact, that is, not damaged, then the 3D printer will notify you that your tank is approaching the recommended maximum service life.
It is very important to replace the bath if it is damaged or when it reaches maximum life, whichever comes first
Estimated life of baths in Formlabs Form 3 / Form 3B 3D printer
Photopolymer type | Form 3/3B V2 Resin Pot Model | Form 3/3B V2.1 Resin Pot Model | |
Tough 2000 Resin Elastic 50a Resin Rigid 4000 Resin Grey Pro Resin Rigid 10k Resin | not compatible weeks (75 days) in contact with resin 250 hours printed | ||
Draft Resin V2 Flexible 80A Resin Dental LT Clear Resin V2 Biomed Clear Resin | Compatible Maximum service life: 35 weeks (250 days) when contact with a resin of 600 hours of print | ||
CASTABEL WAX 4000 RESIN IBT Resin | Not compatible | Not compatible | Compatible No maximum life. |
All other resins | Compatible No maximum life. Estimated life: 600-800 hours of printing. The actual service life depends on the presence of physical damage to the film. |
Reservoir life monitoring
Form 3 or Form 3B 3D printers are equipped with software features that monitor the life of the resin reservoir. The printer displays a warning and also beeps at startup about the remaining life.
0%
At the start of printing, the printer warns that the reservoir has reached its maximum life. Leakage and damage to the 3D printer may occur. The tank should be discarded and replaced immediately.
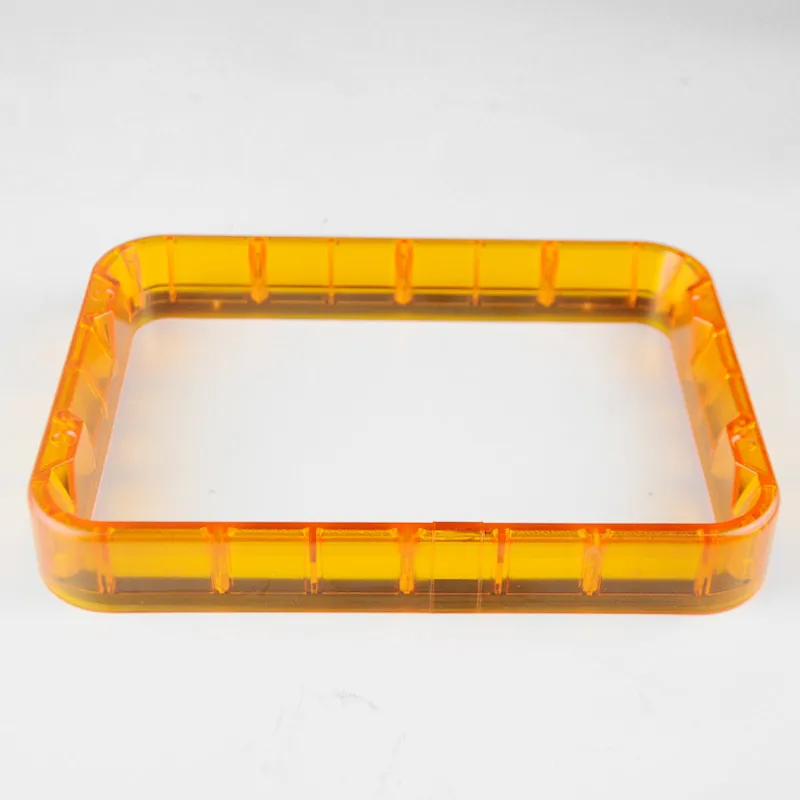
Accessories for 3D printer Formlabs
In the chosen
compare
Fast View
in the basket
In the chosen ones
Fast View
9000 9025 in the basket of5 B.0003
Compare
Quick View
9000 CompareQuick view
Add to cart
Do you need help choosing equipment?
Leave your e-mail or phone and our specialists will contact you.
Recommended Articles:
DLP and LCD 3D Printers: What's the Difference?・Cults
Resin 3D printing is a popular technology in the 3D printing industry, and each market has a number of these 3D printers in its product range. It finds wide application in various industries and its development is a priority to improve print quality, financial viability and access to a wider user group.
DLP and LCD are two of the most prominent technologies in resin 3D printing. Both work on a similar principle and are comparable in many ways. However, there are also some obvious differences that users should be aware of before purchasing a resin 3D printer.
In this blog, we will focus on DLP and LCD 3D printers. We will discuss the main technologies used, their individual advantages and disadvantages, and how they suit your specific 3D printing needs.
Resin 3D printing belongs to the broad category of vat light curing, which is considered one of the main types of 3D printing technologies. The concept is based on the ability of light-sensitive resins in the liquid phase to solidify under the influence of light radiation.
Resin 3D Printing uses this ability to create 3D objects from liquefied resins that are selectively exposed to light to cure desired areas of the resin. Only those parts of the resin that have solidified under the influence of the light source become part of the 3D printing, while the rest remain liquid.
A typical configuration for resin 3D printing includes a tray, or reservoir (in technical terms), that is filled with liquid resin, a light source, and a mechanism for directing the light source to a specific point in the resin to be cured.
In addition, there is a build platform that can move up and down inside the tank with amazing precision. For each new layer, the building platform is lowered to the bottom of the tank, leaving only a tiny gap (0.5 mm in most cases) in which the layer adjacent to the platform is built. For subsequent layers, the platform continues to rise slightly each time, while each new layer fits into the resulting gap and is bonded to the top layer. The 3D printed resin model is built upside down as light passes through the bottom of the tank.
That's what resin 3D printing is all about! Now let's move on to two interesting technologies that we want to talk about.
Digital Light Processing, or DLP, uses a digital light projector as a light source to cure resins. This light source is characteristic of this technology and is the main difference between it and LCD displays.
The projector projects light onto a unique device called DMD (Digital Micromirror Device), which consists of a very large number of very small mirrors, each of which is capable of deflecting light from the projector in different directions. For each layer, these mirrors are arranged in a specific orientation that reflects the digital light beam from the projector onto the tank in the exact shape of the printed layer/layer.
Mirrors cannot change the nature of the light source in any way, they only direct it. This means that the number of pixels produced on the build platform is the same as the number of pixels on the projector. So if the layer is slightly smaller than the projector's beam, the image is actually slightly sharper and more accurate than what is being projected! However, this also has a downside. The opposite happens if the printed piece is larger than the projector screen. In this case, the resolution is reduced, and there is also a risk of distortion at the edges, since the light is refracted too far (like an elephant's foot when printing with filament).
Modern, more expensive DLP 3D printers use advanced technology to minimize this distortion problem and maintain layer quality despite being enlarged. As a result, these DLP 3D printers can safely be considered professional products.
DLP technology has been around for a long time due to the age of the light source: projectors are century old devices widely used in movie theaters. Therefore, the technology is tried and tested.
LCD 3D printing, also known as MSLA 3D printing, is a relatively new technology compared to DLP technology. As mentioned above, it uses a non-DLP light source: UV LEDs that shine through the LCD screen.
Although LCD also creates full layers at the same time as DLP 3D printers, the quality of the layers depends on the screen resolution. The higher the pixel density of the LCD screen, the better the print quality. In addition, there are no problems with distortion, as the print created on the LCD is transferred to the resin unchanged without deviation. Since the original projection size on the LCD screen does not change, the print area is limited by the screen area, so larger prints require a larger screen.
Cost is a tricky issue when it comes to LCD 3D printers. The material is cheap because the LCD screens used in these devices are practically the same as in smartphones. The problem, however, is that they need to be replaced frequently to maintain quality. The idea that LCD 3D printers are cheap is true, but you need to be aware of the running costs involved.
DLP and LCD are similar in many ways: technology, print quality, speed, applications, etc. Are they the same? But are they the same? No.
There are a few things to consider before choosing one or the other. First, let's talk about print quality. As mentioned above, it is comparable for both 3D printers. The finish is smooth, the layers are indistinguishable. However, DLP has an edge in this regard. Cheaper options compare well with LCD printers, but if you consider mid-range DLP 3D printers (which support layer distortion and warp), the build quality is much more detailed and subtle.
In terms of cost, LCD is the cheapest option. Even if the screen has to be changed, the technology itself is so accessible and cheap that DLP is still more expensive. But this comes at the expense of quality, which must be known.
Compatibility with the resin material is another factor to consider. Most resins can be used with both DLP and LCD 3D printers, but some are only suitable for one or the other. It depends on the energy intensity of the light source. The LCD uses a low power light source, so resins that cure quickly are suitable. If any other resin is used, it will not cure properly and the structural integrity of the model will be compromised. Naturally, DLP is compatible with resins that take some time to cure due to the high density of the energy source.
In general, it all depends on the specific application. People who require professional-grade quality and who have a large budget should always choose DLP as it is better suited for detailed work. Consumers who are just starting out or have low-precision tasks on a budget should consider LCD 3D printers, which are also very good in many ways.