Prosthetics 3d printing
3D printing prosthetics in 2021: The great revolution
3D Learning Hub
See all categories
Contents:
- Introduction
- Overview of 3D printing in the medical sector
- Why is using 3D printing for prosthetics so interesting?
- They used 3D printing to develop prosthetics
- What is next?
Introduction
Overview of 3D printing in the medical sector
The medical sector benefits from the wide range of advantages offered by Additive Manufacturing. Thanks to the mass-customization opportunities and the flexibility of the manufacturing and design processes, 3D printing becomes a real alternative for this sector. In the future, this manufacturing technology could be used to replace human organ transplants, significantly speed-up surgical procedures, but also produce cheaper and more adaptable versions of required surgical tools. Using technology to rethink and improve the way we produce medical devices leads to great opportunities.
This technology can also improve the lives of those reliant on prosthetic limbs. That is a fact, we can notice a growing interest in adapted orthopedic insoles, orthosis, and prosthetics manufactured using additive manufacturing.
Why is using 3D printing for prosthetics so interesting?
Manufacturing prosthetic is expensive
Thanks to the constant evolution of 3D printing technologies, the medical industry is facing new challenges. In its own way, 3D printing is revolutionizing the field of rehabilitative medicine and tackling a particular issue: prosthetics. According to NGO LIMBS, only 5% of the nearly 40 million amputees in the developing world have access to prosthetic devices or assistance. Many companies such as Unyq are using the advantages of generative design and additive manufacturing to create a brand new approach to prosthetics both in terms of form and functionality. Indeed, some companies are focusing on bringing these advantages to the developing world, to the amputees in environments that lack the medical infrastructure or resources. The goal here is to support the labor-intensive and expensive prospect of traditional prosthetic manufacturing.
Manufacturing adapted and quality devices for amputees is actually a struggle all over the world, as these prosthetics are expensive and most of the time, poorly adapted to the patient’s particularities. New technologies such as this one can also be a major advantage for prosthetists, helping them in the development of customizable prostheses. From the creation of 3D printed prosthetic hands to functional wrists, solutions can be offered with additive manufacturing. Engineers and researchers are opening new possibilities for prosthetics
Advantages of 3D printing prosthetics
- Innovation: Innovate without worrying about the limitations of traditional manufacturing
Thanks to 3D printers, rapid prototyping has never been so easy. Iterate your ideas and projects faster thanks to this technology. Going further than traditional prosthetics manufacturing will enable great future developments.
- Customization: Create adapted prosthetics
The customization part is the most important argument here. Getting adapted devices and prosthetics will benefit the patients and improve their quality of life during a limb loss. Customizable functional prostheses creation is now possible thanks to 3D printers.
- Cost: Why are 3D printed prosthetics cheaper?
Once again, developing such a complex project as prosthetics is expensive with traditional manufacturing techniques. Especially if you want to adapt it to the morphology of the patient, additive manufacturing appears to be the most efficient technique to get low-cost prosthetics. It is becoming a life-changing solution to produce prosthetics in areas where the access to such devices is complicated, or impossible.
No minimum of order, no need to build an expensive mold, you only need a 3D file to print your project. Prosthetics are better, and more efficient while custom-made. However, customization is quite expensive with traditional manufacturing.
They used 3D printing to develop prosthetics
Several 3D printed prosthetics projects have already been developed all around the world. See how 3D printing materials and technologies are helping to create functional artificial limbs. Here are a few examples of 3D printed prosthetics:
3D printed prosthetic arm providing feedbacks
Lorenzo Spreafico is a student at the University of Leeds. He created a prosthetic arm with vibrotactile feedback.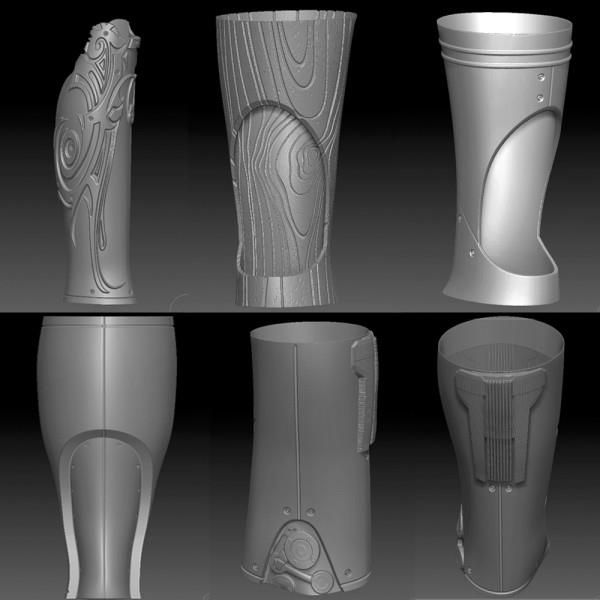
Hand prosthetics
This might not come as a surprise to you, but it is a topic worth mentioning. According to research done by Amputee Coalition, on average there is an amputation done every 30 seconds, and life after such a procedure is hard. But there are people out there using the latest technology innovations to help others. E-nable is a global network of passionate volunteers who help amputees.
Leg prosthetics
Looking absolutely stunning and even impossible Exo by William Root breaks the boundaries of logic. He brings a new level of the esthetics of prostheses. His prosthetic leg is not only beautiful but also fully functional. First of all the designer improved the time-consuming process of manufacturing a prosthesis. Normally, the amputee had to have a mold done of his limb, then a cast was made, vacuum form, check for fit, assembly, and then adjustments were done.
Hero Arm
Hero Arm is a project developed by Open Bionics, who aims to turn disabilities into superpowers with 3D printed bionic arms for children and adults. Using Selective Laser Sintering 3D printing, with Nylon PA12, they develop prosthetics covers inspired by superheroes such as Iron Man, or fictional universes such as Star-Wars or Frozen.Manufacturing prosthetics in remote areas
Guillermo Martínez is the founder of Ayúdame3D, he went from building robots to building prosthetics hands. At first, it was just for fun, and now, Guillermo Martínez helps people in Kenya by developing prosthetic limbs helping amputees living a more normal life.
Millie: the first-ever dog with a 3D printed prosthetic leg in Australia
People are not the only ones whose lives changed thanks to Additive Manufacturing. We already talked about a few animals such as a penguin and a duck with a prosthesis, now it’s time for Millie, the greyhound from Australia. She’s a rescue dog, which was kicked out because of a bad paw. Unfortunately, professional prosthetics cost 10 000$ and they are not as personalized. The owners turned to Autodesk, a leader in 3D modeling and CAD software. With Fusion 360 they designed a new, ideally-fitting prosthesis and then 3D printed it.
What is next?
The future of 3D printed prosthetics
It is definitely bright! As you’ve seen in this article, the presented examples show how beneficial Additive Manufacturing is to the medical industry. 3D printing prosthetics are cheaper by thousands of dollars. They are also much more comfortable, fitting exactly the limb, not causing pain to the user, and they are highly customized. This level of personalization has never been achievable before.
Do you have a prosthetics manufacturing project?
Using an online service bureau such as Sculpteo, there is no minimum order quantity, from a single object to 10 000+ parts, you can 3D print the exact amount of parts you need. With 10+ years of expertise in additive manufacturing for production and prototyping, Sculpteo is also offering rigorous quality control. With our online 3D printing service, you get professional 3D printing at your fingertips with +75 materials and finishes to develop your most ambitious projects, such as prosthetics. We’ll take care of the rest in our industrial ISO 9001 factory.
Upload your 3D file and get your free instant quote!
Any question? Feel free to contact us to discuss your project, our 3D printing expert are here to help you develop your project.
Related Topics
- Return to Top
Get the latest 3D printing news delivered right to your inbox
Subscribe to our weekly newsletter to hear about the latest 3D printing technologies, applications, materials, and software.
Top Examples of 3D Printed Prostheses
Published on April 7, 2022 by Niru K.
When it comes to industries adopting 3D printing, one of the earliest and most fervent supporters of the technologies is of course the medical sector. Indeed, AM is becoming a crucial tool in healthcare thanks to a variety of factors. This is especially the case when it comes to prosthetics. With 3D printing, the benefits are two-fold. First, of course, the prostheses can be perfectly fit to the patient thanks to the ability to customize the part. But additionally, 3D printing enables lower-cost, local production of prostheses. As the World Health Organization estimates that 30 million people worldwide are in need of prosthetics, this can help increase availability for many especially in remote regions. We took a look at some of the top examples of 3D printed prosthetics currently available.
The E-nable association
E-nable, also known as Enabling the future , is an association created in the United States by Jen Owen. The idea behind this project is to bring together makers and enthusiasts to create a network of models of prostheses in the world that can obviously be printed in 3D. The main objective is to “give a hand” to the people who need it most, thus avoiding the high cost of a traditional prosthesis. Since its creation in 2013, the association has donated 3D printed prostheses to hundreds of people around the world.
Bionico Hand, an Open-Source 3D Printed Prosthesis
The Bionico Hand project is the brainchild of Frenchman Nicolas Huchet who has used a bionic hand since he was 18 years old. After making his own, he launched Bionicohand as a way to make more for himself and others. Essentially, what he has conceived is a myoprosthesis, his own term for a myoelectric prosthetic, that can repair itself. He aims to create something designed by and for amputees that will be available open source so anyone can make their own. The project is not yet ready, though it has been in development for a number of years now. However, the proof of concept was produced in October 2021 and the goal is to transform it into a functional prototype by the end of 2022.
Photo Credits: Bionico Hand
Make Your Own 3D Printed Robotic Arm with Youbionic
Created by Federico Ciccarese, Youbionic is a platform that is a little different from many on our list. It is not technically designed to create prosthetics for those in need, but rather a way for young people to enter into the robotics industry. Essentially, buyers will receive a kit with everything they need to create their very own robotic arms, including 3D printing part files. These files have been designed to be easy to print as well as oriented to obtain the best results. And best of all? There are not many parts that make up an Avatar Full Arm (one of the largest available projects), leaving users will less assembly than they might expect. On the company’s website, they have a variety of cool projects that you can buy, including full arms, hands, double hands and more.
Photo Credits: Youbionic
Unlimited Tomorrow – The Name Says it All
Unlimited Tomorrow was founded in Colorado in 2011 by Easton LaChapelle who had been working on robotic limb development for a few years. However, she decided to launch into this project after meeting a little girl who wore a prosthetic limb that had limited capabilities while still being expensive. Thus, the idea of Unlimited Tomorrow and improved prosthetics was born. It aims to support people with upper limb disabilities by using additive manufacturing to produce high quality, high value, low cost bionic prosthetic arms. 3D printing allows for the process to be customizable. This happens as after the user answers a few questions, they are then sent a 3D scanner to scan the residual limb. Based on this, the prosthesis, which can also be personalized, is produced with the 3D printer.
Photo Credits: Unlimited Tomorrow
A Distinct Prosthesis with UNYQ
3D printing is used at UNYQ to use mass production to create innovative, customized prostheses. In addition to being able to develop next-generation products, additive manufacturing is also used for aesthetically pleasing and practical features. Prostheses for above and below the knee amputees offer patients revolutionary personalization in terms of color and design. Currently, they are even working on manufacturing an entire leg. UNYQ provides its patients with an app to create the 3D-printed prostheses: Color, design and surface can be selected, then measurements are taken in a clinic to finally print the prosthesis using additive manufacturing.
3D Printed Foot Prostheses from Mercuris
Mecuris is a German company dedicated to the development of CAD/CAM software solutions that, together with 3D printing, make it possible to create foot prostheses. Thanks to a digital platform, called Mecuris Solution Platform, users can create and customize their individual models to their liking, saving time and money. In fact, thanks to 3D technology and its flexibility, the company is able to reduce production costs by 75%. With this, Mecuris’ goal is to convert traditional craftsmanship into digital tools and workflows that are easy to use according to the needs of each individual, and accompanying customers in every step of the process.
LimbForge Offers Prostheses in Remote Regions
LimbForge, a US-based non-profit organization, works on creating software, design and innovative manufacturing with 3D scanning and 3D printing. With these tools they are able to develop and deliver high quality and affordable custom prosthetics. LimbForge has developed and implemented a platform that allows clinicians to spend less time customizing devices and more time treating a greater number of patients. Its platform provides more realistic designs that help patients integrate and thrive, reduces costs and also offers ultralight prosthetics. The Limbforge platform can be used to size and implement other designs beyond its existing catalog. In fact, once a prosthetic design is in the database, it can be easily configured to fit almost any human anatomy. Notably, the platform is being used to help amputees in developing countries to gain access to high quality prostheses.
Photo Credits: Limbforge
3D Printing the Prostheses of the Future
Evan Kuester is an engineer, artist and designer currently working as a Senior Advanced Applications Engineer at 3D Systems. In addition to that, Kuester is pursuing a number of interesting projects using additive manufacturing. Among them is the development of prosthetics with extremely modern and futuristic designs. For example, in the photo below we see the JD-2 prosthesis model, created with the intention of further exploring the possibilities available to designers with SLS 3D printing technology. Its inner mesh-like structure is intended to reduce the weight of the prosthesis as well as to achieve a more pleasing aesthetic.
“Hero Arm”, a Hero for Life
Open Bionics was the first company in the world to launch a 3D printed bionic arm that would not only be clinically tested but also medically certified. This 3D printed arm is called “Hero Arm” and combines functionality, comfort and design. It is customizable and includes sensors to detect muscle movements, thus providing more ease to move. It would even be able to lift up to 8 kilos, a rather high weight when we know that the prosthesis is put and removed quickly. Open Bionics offers complete customisation of the prosthesis, a real advantage for the person who wears it, who can then create it in his own image. A particularly attractive point for children who often choose a prosthesis with the image of their hero!
3D Prostheses for the Needy
In Africa, many countries have a healthcare system that is unable to treat injuries caused by traffic accidents or infections, so it continues to experience a large number of amputations. That is why there are several non-profit organizations that want to bring printing technologies to anyone in need and anywhere in the world. One example is Ayúdame 3D, a Spanish organization that promotes the social value of technology through technological-social awareness programs in order to help vulnerable groups around the world. Both it and 3D Sierra Leone create 3D printed arms, free of charge, for people with disabilities. Thanks to this, they manage to improve their quality of life and that of their environment, reduce the inequality they face and provide them with greater opportunities for schooling and employability.
Naked Prosthetics and Resin 3D Printing
Based in the United States, Naked Prosthetics (NP) is a company dedicated to the development of functional prosthetic devices for hands and fingers. To do so, they rely on resin 3D printing, specifically stereolithography, with which they create these customized models adapted to the needs of each user. Thanks to 3D printing, Naked Prosthetics is able to deliver the prosthetic devices within a few weeks. As they state on their website, NP’s mission is to help people with partial amputation of fingers and hands, to change their lives positively through functional and high quality prostheses.
Photo Credits: Naked Prosthetics
A Fully 3D Printed Ocular Prosthesis
We recently learned of the UK case of Steve Verze, a Londoner, who became the first person in the world to receive a fully 3D printed ocular prosthesis. The printed prosthesis is part of a collaboration between several players in the UK and Europe, and was led by researchers at UCL and Moorfields Eye Hospital NHS Foundation Trust. The result? A prosthetic eye is impressively realistic thanks to its clearer definition and lifelike depth which was made possible with eye socket scans to ensure a good match.
Lattice Medical, Fighting Breast Cancer with 3D Printing
Taking on breast cancer – that’s what Lattice MEdical, a company founded in Lille, aims to do. Founded in 2017, the company has produced a bioprosthesis called MATTISSE, which could offer an alternative to the silicone prostheses commonly used to help treat breast cancer patients. The silicone prostheses commonly used have to be replaced about every 10 years for safety reasons, which is why the MATTISSE bioprosthesis is made of an absorbable material that can be optimally adapted to the patient’s morphology thanks to the use of additive manufacturing. Lattice Medical uses FDM technology to be able to create the natural reconstruction as they regenerate the patient’s own fatty tissue.
Photo Credits: Lattice Medical
What do you think of these 3D printed prostheses? Let us know in a comment below or on our Facebook and Twitter pages! Sign up for our free weekly Newsletter, all the latest news in 3D printing straight to your inbox!
3D printing in prosthetics - Center for 3D printing and prototyping
3D printing prosthetics3D printing in prosthetics
3D printer is a universal peripheral device with which you can create various physical objects of almost any orientation. Thanks to layered technology, the device allows you to print three-dimensional objects from various types of plastic, metal, plaster, etc. Recent discoveries have led to the fact that the printer for creating three-dimensional models began to be used in prosthetics. Although the direction itself is not new: prostheses printed in this way have already been used in dentistry. The device allows you to easily print the missing body part from a convenient and environmentally friendly material. Developments in this area were carried out for more than one year. The main goal of the researchers was to learn how to create an ideal prosthesis that will fit in all respects, including comfort and appearance.
The need for a perfect prosthesis
An ideal prosthesis is one that will provide functionality to the missing limb without looking intimidating. Printing prostheses on a 3D printer has many advantages. One of the indisputable advantages is the speed of printing. Compared to the conventional process, the time that specialists spend on making a prosthesis using a 3D printer is much less. In addition, this approach also makes it possible to reduce the cost of manufacturing products. This is because the amount of manual labor is significantly reduced.
Features of prostheses created on the printer
Of course, such prostheses differ from the usual ones in many ways. If this is a high-quality product, then the process of its manufacture has certain difficulties, because the design itself is a complex mechanism, which is usually assembled by hand after manufacture. Modern possibilities make it possible to create not only reliable prostheses, but also durable ones. In addition, the decisive factor is the appearance. To do this, specialists need a digital layout in which they need to accurately prescribe the necessary parameters. Only in this way will an ideal prosthesis be created that maximally repeats the anatomy of the human body. To analyze physical data, a 3D scanner can be used, and based on the data obtained, create the prosthesis itself already on the printer.
Finally, we can highlight the main advantages of prostheses created on a 3D printer.
If you are interested in the articles on our website, then maybe you should subscribe to the newsletter? Then you can receive our articles directly to your inbox. We promise you that we will not spam your inbox. Our tactic is different - to interest a person in our field in order to expand the circle of our potential like-minded people and clients.
Benefits of 3D printed prostheses
- Price;
- Strength;
- Appearance;
- Manufacturing speed;
The cost of high-quality prostheses used in medicine is quite high, but further development of this direction will make it possible to make products more massive and significantly reduce their price. The price of domestic prostheses printed on a 3D printer is much lower than their foreign counterparts, which makes it possible for a middle-income family to purchase them.
9Ol000 footwear productionDo you think a prosthesis printed on a 3D printer can fully perform the necessary functions?
Maybe
Can not
Related videos:
3D printing of individual prostheses
Implementation stories
Medicine
Author: Semyon Popadyuk
Author: Semyon Popadyuk
The possibilities of additive technologies are invaluable for medicine: among other things, 3D printers make it possible to create highly precise and complex shapes for the development of prostheses that fully comply with the anatomical features of the patient. Let's consider two cases from surgical practice, when 3D printing helped patients to restore their health and return to normal life.
Using 3D Printing to Repair a Complex Postoperative Defect
A few years after shoulder arthroplasty on the left scapula, a 64-year-old man still had serious complaints. He suffered from a type II central defect with atypical ossification around the glenoid. Prof. Stefan Neiss, Head of the Department of Traumatology at the Leuven University Hospital (Belgium), took up this case and performed a revision surgery. Given the complexity and unusual size of the defect in the patient's humerus, Dr. Neiss decided to work with Materialize's experts and use the Glenius prosthesis. He performed the operation in two stages, first removing the previous prosthesis and placing a spacer, and then installing the Glenius prosthesis.
Contact iQB Technologies: we will help you choose a profitable 3D solution for medical institutions, as well as create accurate models of organs and body parts to prepare for surgery:
Book a consultation with 3D experts
Successful operation
The two-stage operation went smoothly and according to plan. There were no incidents during the removal of the components. It took about an hour to remove the spacer, clean the area, and take a tissue sample to rule out infections, after which the operating team was ready to place the prosthesis. The insertion of the prosthesis also went well due to its compactness and the appropriate size of the incision.
Customized medical templates helped determine the right location. Professor Neiss rechecked the correct position of the prosthesis by testing it on a bone model. He then quickly set the prosthesis into position despite the smooth surface of the defect. Finally, he tightened the screws using 3D printed guides. Before installing the screws, the depth of the holes was checked. Four screws were placed as intended, but the fifth was difficult due to unstable anchorage to the second outer layer of bone. However, by correctly predicting the length of the previous screws, Neiss used the same length for the fifth screw.
Shoulder model and guides on the operating table
The placement and fixation of the glenoid lining took about 20 minutes - 10 minutes less than expected. The operating team removed the guides and set about preparing the humerus for sawing. To restore the normal situation, a significant part of it had to be removed. For the prosthesis, a one-piece stem was used in conjunction with a thin (3 mm) and highly movable liner. After a trial restoration of the normal position, a cobalt-chromium alloy glenosphere was installed. All components were installed approximately 2 hours after the start of the operation.
iQB Technologies experts recommend the article: 3D printing in surgery: creating a perfectly accurate model of the spine and trachea
The value of individual solutions
As already mentioned, 3D printing allows the production of precise and complex shapes and is therefore optimal for the design of individual components. In addition, it makes it possible to create fragile porous structures, which is an important feature of the Glenius prosthesis. The plastic models and guides that were used during this operation were printed from polyamide using selective laser sintering (SLS) and the metal prosthesis was made using selective laser melting (SLM). Depuy Synthes Delta Xtend components were used for the humeral stem and liner.
Neiss really liked the extra support on the back of the drill guide and how smooth the operation went. Customized instruments designed for glenoid prosthetics have made it possible to accurately execute the 3D preoperative plan.
A postoperative report, one and a half years after the procedure, showed that the prosthesis and screws were still in proper position. There are only minor differences between the planned position and orientation and the actual result.
To date, there have been no further revisions. Almost two years after the second operation, the patient is still satisfied. Shoulder mobility improved and the patient regained independence.
81-year-old patient enjoys life again after hip surgery
aMace custom prosthesis used for surgery
The 81-year-old patient suffered from a Paprosky Type 3B acetabular defect and had already undergone several revision surgeries before being referred to Orthopedic Surgeon Douglas Dunlop, FRC, Emeritus Professor of Orthopedics at the University of Southampton. This is not the only such case. The combined registry data shows that 27% of audits are repetitive and fail three times as often as initial audits.
This patient's previous revision reconstructions (cemented polyethylene liner with cranial metal mesh) had failed due to calyx loosening and displacement to the posterior cranial region. This has resulted in bone loss, especially in the posterior cranial region, which complicates acetabular repair.
Everyone who knows my father and knows how weakened he was before the operation is amazed at the transformation: he seemed to be 20 years younger and regained his independence. As his daughter, I am very pleased to see him enjoying life again.
Benefits of 3D planning and 3D printing of the hip prosthesis
Materialize offers 3D printing software and services, including the development of custom prosthetics such as aMace. aMace allows you to take into account all the medical features of the patient and the complex mechanical requirements for this important moving part of the human body. The complex porous structure of the posterior part of the aMace prosthesis, which allows for bone ingrowth, is another feature that can be easily reproduced with 3D printing.
It all starts with a CT scan. It allows you to plan the operation correctly, up to the definition of specific fixation points. Each Materialize aMace prosthesis comes with a detailed 3D analysis. Careful planning, along with templates and models, will help to ensure a successful operation.
Set with a model of an individual hip prosthesis used for a patient
Quality of care improved with custom hip replacement
In collaboration with Materialise clinical engineers, Dunlop was able to carefully plan the operation ahead of time and design the aMace hip prosthesis, custom 3D printed to match the defect. Thanks to this, the prosthesis helped to achieve the desired degree of recovery and fixation. Before the operation, the plastic bone model and the trial sample of the prosthesis served as a guide for the surgeon in preparing the operating room and the correct position of the prosthesis.
Guides were used to place the screws according to the plan. The prosthesis helped to restore the center of rotation to the desired location and orientation, and also provided sufficient support despite the limited amount of bone material (especially in the posterior cranial region). After the operation, a plastic model of the bone was given to the patient, who told his friends and family about the operation.
iQB Technologies Experts Recommend Article: 3D Printing Industry Stands Up to Fight Coronavirus
Additional advantages of the solution were the planning and custom shape, which helped to achieve stability after reconstructive surgery, even taking into account the absence of bone material in the anterior cranial region. This approach resulted in a successful revision surgery and a satisfied patient who, according to his daughter, became independent of outside help again: “My father's quality of life has improved to an incredible degree. He said that even if he won the lottery for a huge amount, he would not be so happy!”
Research by Mr.