Price of stratasys 3d printer
Stratasys F370CR Composite Ready FDM 3D Printer
SEE CURRENT 3D PRINTING PROMOTIONS
A Composite Ready Industrial FDM 3D Printer
800-688-3234
high strength composite printingThe Stratasys F370CR allows you to meet deadlines and stay on budget, with high strength composite printing.
- Equipped with hardened components to operate with composite materials
- Print carbon fiber-reinforced materials like ABS-CF10 and Nylon CF10
- Ideal for workholding fixtures, soft jaws, and component parts
with composite 3D printing - Print parts in a fraction of the time and cost
it takes to machine a metal equivalent.
Explore your Options. Get pricing on a Stratasys F370CR
unmatched uptime
F123CR printers are built on the same platform as the proven F123 Series, with a verified 99%- uptime and a 99%-dimensional repeatability performance
Simple setup, and GO
You don’t need special training to operate F123CR printers. Job setup simply involves importing the part’s CAD file using GrabCAD Print™ software and initiating the print.
Open materials
The open material platform enhances versatility by allowing you to expand your application space with new materials you develop or ones developed by Stratasys and third party partners.
Support
Stratasys invented FDM Technology, and has been perfecting it for over 30 years. GoEngineer's Stratasys technicians and application engineers know how to maximize your printer
investment.
-
ABS-CF10
- Potential Applications:
– Tooling
– Jigs and fixtures
– Production and assembly
– Drill guides -
ABS-CF10 Combines standard ABS material with 10% carbon fiber by weight . This makes for a 50% stiffer than standard ABS 3D printing material and 15% stronger than standard ABS 3D printing materials.
- Learn More >
-
ABS-ESD7
- Potential Applications:
– End-use components
– Electronic products
– Industrial equipment
– Jigs & fixtures
-
ABS-ESD7 standard FDM thermoplastic works with soluble support technology, so support removal is hands-free and complex parts require no extra effort.
- Learn More >
-
ABS-M30
- Potential Applications:
– Conceptual models
– Functional prototypes
– Manufacturing tools
– Production parts -
ABS-M30 FDM material enables you to prototype quickly and efficiently.
This strong, familiar material lets you explore more ideas, test frequently, work iteratively – and ultimately take better products to market faster.
- Learn More >
-
ASA
- Potential Applications:
– Conceptual models
– Functional prototypes
– Manufacturing tools
– Production parts -
Mechanical strength and UV stability make ASA a great choice for functional prototyping. Ease of use makes it a top pick for iterative design. Outstanding aesthetics and ten fade-resistant colors make it an all-around favorite, even for end-use parts.
Learn More >
-
Diran
- Potential Applications:
– Tooling
– Jigs & fixtures -
Displaying functional properties of chemical resistance, high-impact strength, and a low coefficient of friction this material is well-suited for jigs and fixturing applications where non-marring robust tooling is desired.
Learn More >
-
FDM TPU 92A
- Potential Applications:
– Hoses, tubes, air ducts
– Protective covers & seals
– Vibration dampeners
– Prototype and end-use parts -
Thermoplastic polyurethanes otherwise known as TPU’s are flexible elastomers found in products that require a soft touch, shock absorption, or a comforting grip. They are commonly co-molded or over-molded onto ABS and Polycarbonate substrates in sunglasses and phone/tablet cases.
- Learn More >
-
Nylon CF10
- Potential Applications:
–Metal forming dies
– Press brakes
– End effectors
– Alignment and assembly fixtures -
3D printing with carbon fiber material lets you build strong, stiff, lightweight tools and parts.
FDM Nylon CF10 combines nylon and carbon fibers to achieve a high flexural strength and stiffness-to-weight ratio.
- Learn More >
-
pc-abs
- Potential Applications:
– Conceptual models
– Functional prototypes
– Manufacturing tools
– Production parts -
For functional prototyping, tooling, and low-volume manufacturing that requires superior impact strength, FDM Technology works with PC-ABS thermoplastic. PC-ABS also exhibits excellent feature definition and surface finish.
Learn More >
Request More Information about Materials for the Stratasys F370 CR 3D Printer
System Size and Weight
- 1626 x 864 x 711 mm (64 x 34 x 28 in.
)
- 227 kg (500 lbs.)
BUILD ENVELOPE
- 355 x 254 x 355 mm (14 x 10 x 14 in.)
MATERIALS
- ABS-CF10, ABS-M30, ABS ESD7, ASA, Diran, FDM Nylon-CF10, FDM TPU 92A, PC-ABS, QSR Support material, (*Diran requires SUP4000B support material)
MATERIAL DELIVERY
- 4 material spool bays, 2 for model, 2 for support located in a drawer on the front of the unit
ACHIEVABLE ACCURACY
- Parts are produced within an accuracy of +/- .200 mm (.008 in), or +/- .002 mm/mm
(.002 in/in), whichever is greater
SOFTWARE
Operator Attendance
- Limited attendance for job start and stop required
OPERATING CONDITIONS
- Operating temperature: 15 – 30 ºC (59 – 86 ºF), Humidity: 30 – 70% RH
- Storage temperature: 0 – 35 ºC (32 – 95 ºF), Humidity: 20 – 90% RH
POWER REQUIREMENTS
- 100-132V/15A or 200–240V/7A.
50/60 Hz
operating System
- Windows 10 (64 bit only) and Window 11 with a minimum of 4GB RAM
(8GB or more recommended)
Regulatory Compliance
- CE (low-voltage and EMC directive), FCC, EAC, cTUVus, FCC, KC, RoHs, WEEE, Reach, RCM
Wireless Network Connectivity
- Wired: TCP/IP protocols at 100 Mbps minimum 100 base T, Ethernet protocol, RJ45 connector
- Wireless-ready: IEEE 802.11n, g, or b; Authentication: WPA2-PSK, 802.1x EAP Encryption:
CCMP, TKIP
Request More Information on the Stratasys F370CR 3D Printer Specifications
GrabCAD Print
Professional 3D Printing Made Easy and Accessible
GrabCAD Print is the most complete solution for Stratasys 3D printers on the planet. The intuitive, easy-to-use software allows for simplified preparation, scheduling, monitoring, and reporting of print jobs. With the ability to read and understand CAD files natively, GrabCAD Print offers an efficient workflow that streamlines job management in shared office and model shop environments.
LEARN MORE
INSIGHT SOFTWARE
OPTIMIZE BUILD OUTPUT FOR 3D PRINTING
(ONLY AVAILABLE ON F370)
Insight software prepares your CAD program’s STL output for 3D manufacturing on a Fortus machine by automatically slicing and generating support structures and material extrusion paths. For maximum control, users can manually edit parameters that determine the look, strength, and precision of parts as well as the speed and material use of the FDM process.
- Optimize build orientation for maximum strength and smoothest surface finish
- Customize supports for fast, easy removal and best use of materials
- Program pauses into the build for any reason, such as to embed hardware or circuitry
- Manipulate tool paths for advanced control over part properties
Included with Insight is Control Center. This sophisticated software application communicates with user workstations and Fortus systems, to manage jobs and monitor production status. Design, engineering, and manufacturing teams can network and share 3D manufacturing capacity to maximize efficiency and throughput.
*Compatible with GrabCAD Print for use with job reports, scheduling, and remote monitoring.
Request More Information on Insight 3D Printing Software
F-SERIES
View the Entire F-Series office friendly addditive manufacturing product line available from Stratasys. F-Seriesl 3D Printers
3D Printing Services
AWARD WINNING TECHNICAL SUPPORT
GoEngineer’s extensive technical knowledge can assist with your additive manufacturing needs. Our Award winning team is ready to help. Reach out and see why GoEngineer is the #1 reseller of SOLIDWORKS and Stratasys systems in the world!
LEARN MORE
ADDITIVE MANUFACTURING TRAINING
Learn to utilize all features and tools of Stratasys commercial 3D printers with GoEngineer additive manufacturing on-boarding training. Take advantage of our 3D printing team of experts to help launch all your 3D printing capabilities.
LEARN MORE
3D Print and Part Design
No matter your size, quantity or complexity of part(s) needed, GoEngineer can help you! Take advantage of our 3D Printing and Part Design Services to help your organization produce the best parts and prototypes available on the market.
LEARN MORE
Additional Resources
Take Advantage of GoEngineer’s Extensive Knowledge Base and Resources
Find a Solution
Our robust Knowledge Base contains over 12,000 resources to help answer your product design questions. From basic CAD questions to in-depth guides and tutorials, find your solution here. Find a Solution
PROFESSIONAL TRAINING
Improve your skills with professional training and certifications in SOLIDWORKS, CAM, 3D Printing, and 3D Scanning offered four ways: self-paced, online, on-site, or in-classroom.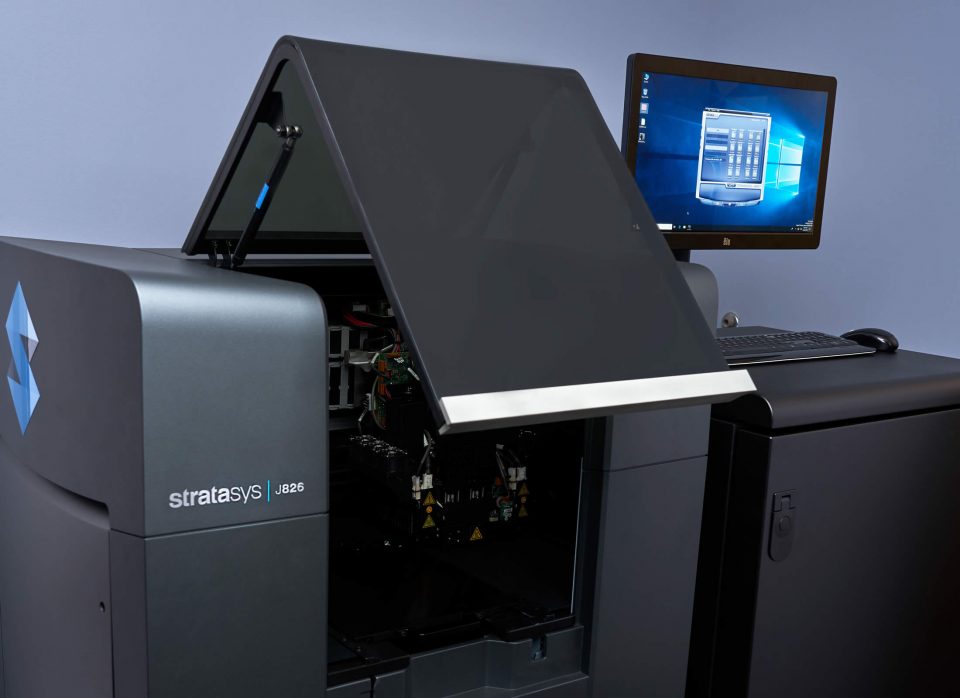
BLOG
#1 Technical Resource Worldwide - Right at your fingertips. Search or browse through hundreds of SOLIDWORKS tips & tricks, additive manufacturing product developments, announcements, how-to guides, and tutorials. Blog
YouTube Channel
Our YouTube channel hosts hundreds of educational tutorials, product demonstrations, recorded webinars, and best practices for all of our products and services. GoEngineer's YouTube Channel
ONLINE STORE
Order 3D printing materials and consumables, enroll in SOLIDWORKS training classes, and buy official GoEngineer gear directly from our online store.
FREE SOLIDWORKS Tools
Enjoy this collection of small ‘macros’ that were tailored to help our customers. These free SOLIDWORKS tools are for you to use, review, and modify. SOLIDWORKS Automation Tools
WEBINARS
Our engineering webinars are hosted by some of the top experts in the industry. They are always recorded, always free, and always offer a live Q&A. WEBINARS
3D Printing Services
Need to 3D print a part? Our Additive Manufacturing experts will 3D print your part and deliver it to you using the latest technology on one of our professional FDM, PolyJet, SL, or Metal 3D printers.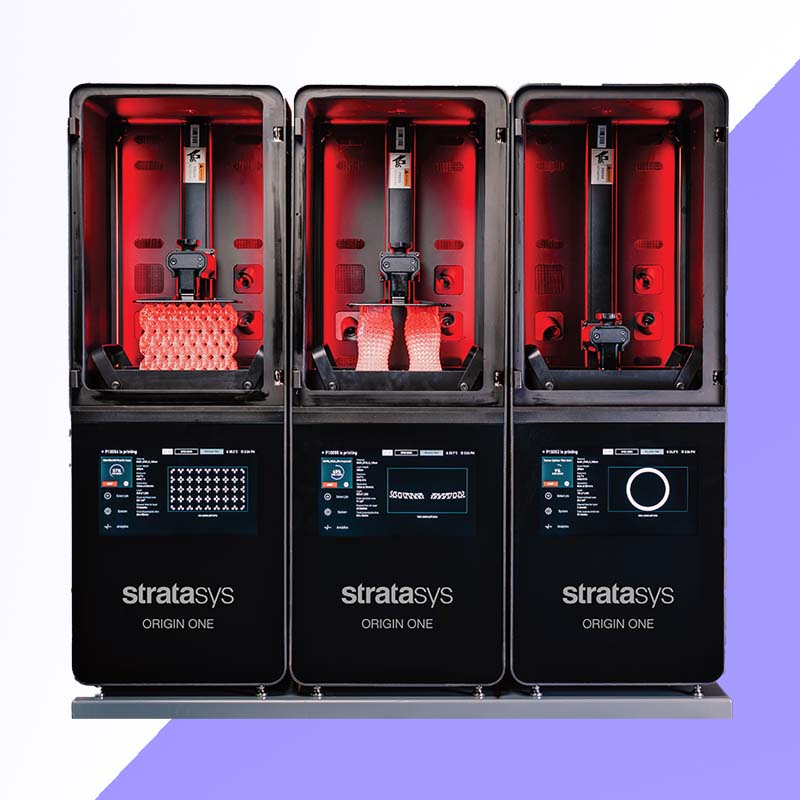
Stratasys F190CR Composite Ready FDM 3D Printer
SEE CURRENT 3D PRINTING PROMOTIONS
A Composite Ready Industrial FDM 3D Printer
800-688-3234
high strength composite printingThe Stratasys F190CR allows you to meet deadlines and stay on budget, with high strength composite printing.
- Equipped with hardened components to operate with composite materials
- Print carbon fiber-reinforced materials like ABS-CF10 and Nylon CF10
- Ideal for workholding fixtures, soft jaws, and component parts
with composite 3D printing - Print parts in a fraction of the time and cost
it takes to machine a metal equivalent.
Explore your Options. Get pricing on a Stratasys F190CR
unmatched uptime
F123CR printers are built on the same platform as the proven F123 Series, with a verified 99%- uptime and a 99%-dimensional repeatability performance
Simple setup, and GO
You don’t need special training to operate F123CR printers. Job setup simply involves importing the part’s CAD file using GrabCAD Print™ software and initiating the print.
Open materials
The open material platform enhances versatility by allowing you to expand your application space with new materials you develop or ones developed by Stratasys and third party partners.
Support
Stratasys invented FDM Technology, and has been perfecting it for over 30 years. GoEngineer's Stratasys technicians and application engineers know how to maximize your printer
investment.
-
ABS-CF10
- Potential Applications:
– Tooling
– Jigs and fixtures
– Production and assembly
– Drill guides -
ABS-CF10 Combines standard ABS material with 10% carbon fiber by weight . This makes for a 50% stiffer than standard ABS 3D printing material and 15% stronger than standard ABS 3D printing materials.
Learn More >
-
ABS-M30
- Potential Applications:
– Conceptual models
– Functional prototypes
– Manufacturing tools
– Production parts -
ABS-M30 FDM material enables you to prototype quickly and efficiently. This strong, familiar material lets you explore more ideas, test frequently, work iteratively – and ultimately take better products to market faster.
- Learn More >
-
ASA
- Potential Applications:
– Conceptual models
– Functional prototypes
– Manufacturing tools
– Production parts -
Mechanical strength and UV stability make ASA a great choice for functional prototyping.
Ease of use makes it a top pick for iterative design. Outstanding aesthetics and ten fade-resistant colors make it an all-around favorite, even for end-use parts.
- Learn More >
-
FDM TPU 92A
- Potential Applications:
– Hoses, tubes, air ducts
– Protective covers & seals
– Vibration dampeners
– Prototype and end-use parts -
Thermoplastic polyurethanes otherwise known as TPU’s are flexible elastomers found in products that require a soft touch, shock absorption, or a comforting grip. They are commonly co-molded or over-molded onto ABS and Polycarbonate substrates in sunglasses and phone/tablet cases.
Learn More >
-
Nylon CF10
- Potential Applications:
– Metal component replacement
– Production parts
– Tooling -
3D printing with carbon fiber material lets you build strong, stiff, lightweight tools and parts.
FDM Nylon CF10 combines nylon and carbon fibers to achieve a high flexural strength and stiffness-to-weight ratio.
Learn More >
Request More Information about FDM Materials
System Size and Weight
- 1626 x 864 x 711 mm (64 x 34 x 28 in.)
- 227 kg (500 lbs.)
BUILD ENVELOPE
- 305 mm x 254 mm x 305 mm (12 x 10 x 12 in.)
MATERIALS
- ABS-CF10, ABS-M30, ASA, FDM Nylon-CF10, FDM TPU 92A, QSR Support material
MATERIAL DELIVERY
- 2 material spool bays, 1 for model, 1 for support located in a drawer on the front of the unit
ACHIEVABLE ACCURACY
-
Parts are produced within an accuracy of +/- .
200 mm (.008 in), or +/- .002 mm/mm
(.002 in/in), whichever is greater
SOFTWARE
Operator Attendance
- Limited attendance for job start and stop required
OPERATING CONDITIONS
- Operating temperature: 15 – 30 ºC (59 – 86 ºF), Humidity: 30 – 70% RH
- Storage temperature: 0 – 35 ºC (32 – 95 ºF), Humidity: 20 – 90% RH
POWER REQUIREMENTS
- 100-132V/15A or 200–240V/7A. 50/60 Hz
operating System
-
Windows 10 (64 bit only) and Window 11 with a minimum of 4GB RAM
(8GB or more recommended)
Regulatory Compliance
- CE (low-voltage and EMC directive), FCC, EAC, cTUVus, FCC, KC, RoHs, WEEE, Reach, RCM
Wireless Network Connectivity
- Wired: TCP/IP protocols at 100 Mbps minimum 100 base T, Ethernet protocol, RJ45 connector
-
Wireless-ready: IEEE 802.
11n, g, or b; Authentication: WPA2-PSK, 802.1x EAP Encryption:
CCMP, TKIP
Request More Information on the Stratasys F190CR 3D Printer Specifications
GrabCAD Print
make 3D printing easy, with thoughtful features:
- Automatically corrects files and reduces print time with automatic tray arrangement.
- Calculates the time and material resources needed for production before printing.
- 3MF file supported – significantly simplifies color assignment in your workflow.
- New feature alerts the user if there has been cross-contamination with a biocompatible material.
- Schedule and monitor the print job remotely from your mobile device or browser.
- Get automatic alerts remotely when the job is printing and finished.
LEARN MORE
F-SERIES
View the Entire F-Series office friendly addditive manufacturing product line available from Stratasys.
3D Printing Services
AWARD WINNING TECHNICAL SUPPORT
GoEngineer’s extensive technical knowledge can assist with your additive manufacturing needs. Our Award winning team is ready to help. Reach out and see why GoEngineer is the #1 reseller of SOLIDWORKS and Stratasys systems in the world!
LEARN MORE
ADDITIVE MANUFACTURING TRAINING
Learn to utilize all features and tools of Stratasys commercial 3D printers with GoEngineer additive manufacturing on-boarding training. Take advantage of our 3D printing team of experts to help launch all your 3D printing capabilities.
LEARN MORE
3D Print and Part Design
No matter your size, quantity or complexity of part(s) needed, GoEngineer can help you! Take advantage of our 3D Printing and Part Design Services to help your organization produce the best parts and prototypes available on the market.
LEARN MORE
Additional Resources
Take Advantage of GoEngineer’s Extensive Knowledge Base and Resources
Find a Solution
Our robust Knowledge Base contains over 12,000 resources to help answer your product design questions.
PROFESSIONAL TRAINING
Improve your skills with professional training and certifications in SOLIDWORKS, CAM, 3D Printing, and 3D Scanning offered four ways: self-paced, online, on-site, or in-classroom. Certified Training Courses
BLOG
#1 Technical Resource Worldwide - Right at your fingertips. Search or browse through hundreds of SOLIDWORKS tips & tricks, additive manufacturing product developments, announcements, how-to guides, and tutorials. Blog
YouTube Channel
Our YouTube channel hosts hundreds of educational tutorials, product demonstrations, recorded webinars, and best practices for all of our products and services.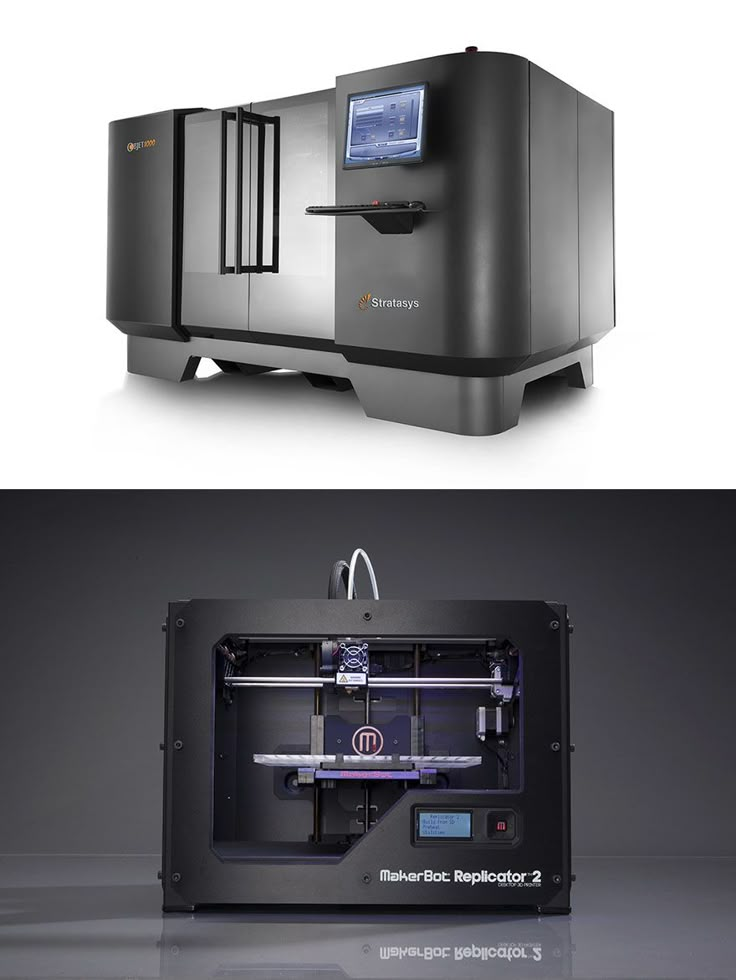
ONLINE STORE
Order 3D printing materials and consumables, enroll in SOLIDWORKS training classes, and buy official GoEngineer gear directly from our online store. Online Store
FREE SOLIDWORKS Tools
Enjoy this collection of small ‘macros’ that were tailored to help our customers. These free SOLIDWORKS tools are for you to use, review, and modify. SOLIDWORKS Automation Tools
WEBINARS
Our engineering webinars are hosted by some of the top experts in the industry.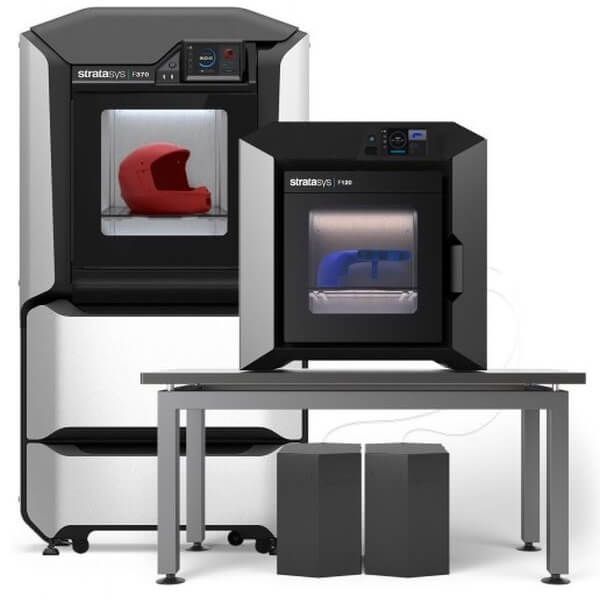
3D Printing Services
Need to 3D print a part? Our Additive Manufacturing experts will 3D print your part and deliver it to you using the latest technology on one of our professional FDM, PolyJet, SL, or Metal 3D printers. 3D Printing ServicesHistory of 3D printing
In this section, we wanted to trace the history of 3D printing from its inception to the present day, as well as give a forecast regarding the future development of technology.
The first 3d printer was invented by the American Charles Hull, he worked on the technology of stereolithography (SLA), a patent for the technology was issued in 1986. The printer was a fairly large industrial installation. The installation "grew" a three-dimensional model by applying a photopolymerizable material to a moving platform. The basis was a digital model pre-modeled on a computer (3D model). This 3d printer created three-dimensional objects, rising by 0.1-0.2 mm - the height of the layer. Despite the fact that the first device had many disadvantages, the technology has received its application. Charles Hull is also the co-founder of 3dsystems, one of the world's leading manufacturers of industrial 3D printers.
Charles Hull was not the only one to experiment with 3D printing technology, as in 1986 Carl Deckard invented Selective Laser Sintering (SLS). You can learn more about the method in another article, briefly: a laser beam sinters a powder (plastic, metal, etc.), while the mass of the powder is heated in the working chamber to a temperature close to the melting point. The basis is also a digital model pre-modeled on a computer (3D model). After the laser passes through the horizontal layer, the chamber is lowered to the layer height (usually 0. 1-0.2 mm), the powder mass is leveled with a special device and a new layer is applied.
However, the most famous and widespread 3D printing method today is layer-by-layer direction (FDM). The idea of technology belongs to Scott Crump (Scott Crump), the patent dates back to 1988. You can learn more about the method in another article, in short: material (usually plastic) is fed from the heated nozzle of the print head using a stepper motor, the print head moves on linear guides along 1 or two axes, and the platform moves along 1 or 2 axes . The basis of the movement is also a 3D model. The molten plastic is laid on the platform along the established contour, after which the head or platform is moved and a new layer is applied on top of the old one. Scott Crump is one of the founders of Stratasys, which is also one of the leaders in the production of industrial 3D printers.
All the devices described above belonged to the class of industrial devices and were quite expensive, so one of the first 3d Dimension printers from Stratasys in 1991 cost from 50 to 220 thousand US dollars (depending on the model and configuration). Printers based on the technologies described above cost even more and until very recently, only a narrow circle of interested specialists knew about these devices.
Everything began to change since 2006, when the RepRap project (from the English Replicating Rapid Prototyper - a self-replicating mechanism for rapid prototyping) was founded, with the goal of creating a self-copying device, which was a 3D printer working on technology FDM (layer by layer deposition). Only, unlike expensive industrial devices, it looked like a clumsy invention made from improvised means. Metal shafts serve as a frame, they also serve as guides for the print head. driven by simple stepper motors. The software is open source. Almost all connecting parts are printed from plastic on the 3D printer itself. This idea originated among English scientists and aimed at spreading available additive technologies so that users can download 3D models on the Internet and create the necessary products, thus minimizing the production chain.
Leaving aside the ideological component, the community (which exists and develops to this day) managed to create a 3d printer accessible to the "ordinary person". So a set of unprinted parts can cost around a couple of hundred US dollars and a finished device from $500. And even though these devices looked unsightly and were significantly inferior in quality to their industrial counterparts, all this was an incredible impetus for the development of 3D printing technology.
As the RepRap project developed, 3D printers began to appear, taking as a basis the base laid down by the movement in technical and, sometimes, ideological terms (for example, commitment to the concept of open source - OpenSource). The companies that made printers tried to make them better both in terms of performance, design and user experience. The first RepRap printers cannot be called a commercial product, since it is not so easy to manage (and even more so to assemble) and it is not always possible to achieve stable work results. Nevertheless, companies tried to close the more than significant gap in quality, leaving a significant gap in cost whenever possible.
First of all, it is worth mentioning the MakerBot company, which started as a startup, took RepRap ideas as a basis and gradually turned them into a product of a new quality.
Their flagship product (and in our opinion the best to this day) remains the MakerBot Replicator 2 3D printer. The model was released in 2012 and later discontinued, but remains one of the most popular 3D printer models to this day " personal" segment (according to 3dhubs). The word "personal" is in brackets because this printer, which cost $2,200 at the time of release, was (and is) primarily used for business purposes, but falls into the personal segment due to its cost. This model differs from its progenitors (RepRap), being, in fact, a finished commercial product. Manufacturers abandoned the concept of OpenSource, closing all sources and software codes.
In parallel with the release of equipment, the company actively developed the Thingiverse resource, which contains many models for 3d printing, available for download for free. During the development of the first printer and beyond, the community has helped the company a lot, testing the product and offering various upgrades. After the release of the Replicator 2 (and the closure of development), the situation has changed. You can learn more about the history of MakerBot and other companies and people associated with 3d printing by watching the film Print the legend.
This film also highlights the history of Formlabs, one of the first companies to launch an affordable 3D printer based on SLA (Strereolithography) technology. The company raised funds for the first FORM 1 model through crowdfunding, encountered production difficulties, but eventually released an affordable and productive 3D printer, closing the quality gap described above.
And although the 3D printers described above were far from perfect, they laid the foundation for the development of affordable 3D printing technology, which continues to this day. At the moment, the quality of FDM and SLA printers is increasing, but there is no significant price reduction, rather, on the contrary, it is growing slightly. Along with FDM and SLA, many companies are developing in the field of powder sintering (SLS), as well as metal printing. Despite the fact that such printers cannot be called affordable, their price is much lower in comparison with analogues from the professional segment. It is also worth noting the development of the line of materials, in addition to the standard ABS and PLA plastics, today many different materials are used, including nylon, carbon fiber and other durable and refractory materials.
Personal 3d printers of today are very close to professional devices, the development of which also does not stop. In addition to the "founders" of the technology (Stratasys, 3dsystems), many small companies specializing in industrial 3D printing technologies (metal in particular) have emerged. 3D printing is also attracting the attention of large corporations, which, with varying degrees of success, are striving to take their place in a growing market. Here it is worth highlighting HP, which recently released the HP Jet Fusion 3D 4200 model, which has gained popularity among 3d printing professionals (as of 2018, it is at the top of the ranking of professional 3D printers in the quarterly reports of the 3dhubs portal).
However, 3D printing technologies are developing not only in breadth, but also in depth. One of the main disadvantages of 3D printing, compared to other production methods, is the low speed of creating models. A significant advance in terms of accelerating 3D printing was the invention of CLIP technology by CARBON, printers operating on this technology can produce models 100 times faster than classic SLA technology.
There is also a constant expansion of the range, properties and quality of materials and post-processing of products. All this accelerates the transition to the use of 3d printers in production, and not just as prototyping devices. Today, many large and not only companies and organizations are closely using a 3D printer in their production chain: from consumer goods manufacturers NIKE and PUMA to BOEING and SPACE X (the latter prints engine parts for its rockets that could not be made in any other way) .
In addition to the "classic" scope of 3D printing, today more and more often you can see news about how a house or some organ (or rather, a small part of it) was printed on a 3D printer from bio-material. And this is true, several companies around the world are testing or already partially using 3D printing in the construction of buildings and structures. This mainly concerns the contour pouring of walls (similar to the FDM method) with a special composite concrete mixture. And in Amsterdam there is a 3D printed bridge project and this list will only expand over time, since the use of 3D printing in construction can significantly reduce costs and increase the speed of work at certain stages.
With regards to medicine, here 3D printing also finds application, but at the moment it is not printing organs, but rather the use of technology in prosthetics (of various kinds) and bone replacement. Also, 3D printing technology is widely used in dentistry (SLA technology). Regarding the printing of organs, this is still far in the future, at the moment bio-3D printers are experimental facilities in the early stages, the success of which is limited to printing a few limited-viable cells.
Looking to the future, it is safe to say that 3D printing technology will expand both in breadth and depth, improving technology, speeding up processes, improving quality and improving material properties. 3D printers will increasingly replace old methods in production chains of various scales, and world production, due to this, will move towards the “on demand” scheme of work, increasing the degree of product customization. Perhaps someday, 3D printers will be widely used at the household level for the production of necessary things (the dream and goal of the RepRap movement), but this requires not only the development of technology, but also a paradigm shift in social thinking, as well as the development of a powerful design ecosystem ( 3d modeling) products (which is often forgotten).
3d printing of houses (and other structures) will no doubt also develop, reducing costs and production time, which, together with the development of new approaches in architecture and urban planning (such as modular construction and the prefabricated method), will give a tangible impetus to development the industry as a whole.
Biological 3D printers will be an important tool in scientific research. However, before they appear in hospitals and clinics, where they will print new organs, it is still very, very far away (in fact, this is science fiction).
Sealing 3D models made of plastic using FDM technology on the 3D printer
Overview
In many applications, the use of FDM parts can provide significant cost savings and time-to-market. FDM technology is an additive process for building plastic parts in layers based on data from CAD files. The use of FDM also allows you to significantly expand the horizons of applicability, since it is less dependent on the geometry of the part. However, FDM parts are characterized by porosity, which is an obstacle to their use in functional prototypes and direct digital manufacturing, where sealing for gases and liquids is required. To address this issue, a number of different compaction methods have been tried, bringing the benefits of FDM technology to a wide range of new applications.
Application Contours
There are many methods for sealing FDM parts and many factors to consider when choosing the right approach. To assist in selection, Stratasys evaluated the cost, time, difficulty, geometry limitations, maximum part size, toughness, accuracy retention, chemical resistance, and temperature sensitivity of five common sealing methods.
Smoothing Station
Finishing Touch Smoothing Station densifies the surface of a part by exposing it to the evaporating smoothing agent inside the chamber. When using a smoothing station, the integrity of geometric dimensions is well preserved. Its use is limited to applications where the pressure is not higher than atmospheric pressure and the temperature is not higher than 100 degrees. The smoothing station is often chosen when electroplating parts that are used as templates for investment casting or the production of functional prototypes for sealed containers such as bottles or cooling lines in molds.
Epoxy
Material Hysol E-20HP is a two component epoxy resin that is applied to small areas of the part. This method does not require any investment in equipment and the end results are well suited to harsh environments. The coating will maintain an airtight seal up to 448 kPa, can withstand temperatures that meet or exceed those for FDM materials, and is resistant to many chemicals. Large and complex parts may be difficult to seal with epoxy. Inaccessible elements such as internal channels cannot be sealed. The thickness of the epoxy layer, combined with manual application, reduces the geometric accuracy of the part. Hysol E-20HP can be used with any FDM material currently available.
Epoxy Infiltration
BJB Epoxy Resin (TC-1614) penetrates the surface of porous and semi-porous parts. The FDM parts are immersed in the resin and a vacuum is applied to infiltrate the resin into the part. In addition to the vacuum chamber, an oven is required to preheat and prepare the epoxy. Epoxy infiltration offers a hermetic seal for water and air up to 448 kPa. Parts sealed with this method also withstand high temperatures and are chemically resistant. The densification process is simple and can be done in less than three hours, but is somewhat expensive due to the cost of the epoxy. When using epoxy infiltration, the geometric dimensions change slightly. The BJB TC-1614 can be used with any FDM material currently available.
Immersion
Solvent immersion of FDM parts can replace the use of the Smoothing Station when it is not available or the part is larger than its working chamber. All characteristics are similar except that the geometric accuracy is lower. The melting action of the solvent is fast and aggressive, so geometric accuracy is difficult to control. As with the Smoothing Station, use of this method should be limited to low temperature and low pressure applications. Immersion is suitable for all FDM materials based on ABS.
Painting and filling
When only part of the surface of an FDM part needs to be sealed, a light coat of paint or putty can be used as an inexpensive method. Since this is a manual operation, the accuracy and quality of the final product depends on the skill and care of the technician. The advantages of this option include low cost, short time and ease of application. Its disadvantages include the lack of tightness and resistance to temperatures and chemical environments. This method can be used to reduce the porosity of FDM tools used for example in thermoforming.
Customer Experience
The 3D Innovation Center provides high quality rapid prototyping and rapid manufacturing services. Recently, a manufacturer of air intakes and other automotive parts entered the market looking to improve the manufacturing process. She had run computer simulations of fluid flow through an air intake and wanted to test prototypes of various designs that seemed promising. A common method for building a prototype air intake is to machine a solid piece of aluminum, which is expensive and time consuming.
The main difficulty of this task was that the surface of the part must be compacted before being used for functional testing.