Origin 3d printing
Origin – Manufacture the impossible
Video Player is loading.
Current Time 0:00
Duration -:-
Loaded: 0%
Stream Type LIVE
Remaining Time -0:00
This is a modal window.
The media could not be loaded, either because the server or network failed or because the format is not supported.
Beginning of dialog window. Escape will cancel and close the window.
TextColorWhiteBlackRedGreenBlueYellowMagentaCyanTransparencyOpaqueSemi-TransparentBackgroundColorBlackWhiteRedGreenBlueYellowMagentaCyanTransparencyOpaqueSemi-TransparentTransparentWindowColorBlackWhiteRedGreenBlueYellowMagentaCyanTransparencyTransparentSemi-TransparentOpaque
Font Size50%75%100%125%150%175%200%300%400%Text Edge StyleNoneRaisedDepressedUniformDropshadowFont FamilyProportional Sans-SerifMonospace Sans-SerifProportional SerifMonospace SerifCasualScriptSmall Caps
End of dialog window.
We’ve joined forces with Stratasys to usher in the next era of additive manufacturing.
Featured In
THE LATEST NEWS
Exceptional Accuracy and Consistency
Programmable Photopolymerization (P³) precisely orchestrates light, temperature, and other conditions, automatically optimizing prints in real-time for the best possible results. Produce features less than 50µm in size with high-accuracy materials.
Big Build, Small Footprint
An optimized build volume (192mm x 108mm x 350mm), compact footprint (400mm x 450mm x 1100mm), and minimal power requirements enable manufacturers to efficiently maximize production capacity per sq ft.
Welcome to Open Additive Manufacturing
World-Class
Materials
Incorporate new application-specific materials from our open network of partners.
Commercial-Grade
Parts
Exceed injection molded strength, consistency, and durability at a competitive cost.
Additive Mass
Production
Seamlessly test, iterate, and scale production with our open approach and modular system.
World-Class Materials
Resilient elastomers, heat-resistant polymers, biocompatible formulations, and other high-performance materials from our open network of material partners.
Video Player is loading.
Current Time 0:00
Duration -:-
Loaded: 0%
Stream Type LIVE
Remaining Time -0:00
This is a modal window.
The media could not be loaded, either because the server or network failed or because the format is not supported.
Beginning of dialog window. Escape will cancel and close the window.
TextColorWhiteBlackRedGreenBlueYellowMagentaCyanTransparencyOpaqueSemi-TransparentBackgroundColorBlackWhiteRedGreenBlueYellowMagentaCyanTransparencyOpaqueSemi-TransparentTransparentWindowColorBlackWhiteRedGreenBlueYellowMagentaCyanTransparencyTransparentSemi-TransparentOpaque
Font Size50%75%100%125%150%175%200%300%400%Text Edge StyleNoneRaisedDepressedUniformDropshadowFont FamilyProportional Sans-SerifMonospace Sans-SerifProportional SerifMonospace SerifCasualScriptSmall Caps
End of dialog window.
Built for Volume
Materials engineered to be easy to handle, rapidly post-processed, and exhibit extended shelf life.
Priced for Scale
A cost-per-kilogram that starts low and drops as volume scales.
Lower Risk
Redundant sourcing of critical materials lowers the chance of supply interruptions.
Commercial-Grade Parts
Origin's production system uses Programmable Photopolymerization (P3) to turn materials into isotropic parts and products ready for end-use.
Hand Pump Thread AdapterDIMENSIONS
2.9" x 2.9" x 1.82"
TOTAL PRINT & POST-PROCESSING TIME
46 min
TOLERANCES
+/- 50µm
TENSILE STRENGTH
61 MPa
Additive Mass Production
High throughput, combined with unmatched part-to-part consistency, helps you expand production without delays, so you can launch faster and respond flexibly to shifts in demand while maintaining minimal inventory.
Video Player is loading.
Current Time 0:00
Duration -:-
Loaded: 0.00%
Stream Type LIVE
Remaining Time -0:00
This is a modal window.
The media could not be loaded, either because the server or network failed or because the format is not supported.
Beginning of dialog window. Escape will cancel and close the window.
TextColorWhiteBlackRedGreenBlueYellowMagentaCyanTransparencyOpaqueSemi-TransparentBackgroundColorBlackWhiteRedGreenBlueYellowMagentaCyanTransparencyOpaqueSemi-TransparentTransparentWindowColorBlackWhiteRedGreenBlueYellowMagentaCyanTransparencyTransparentSemi-TransparentOpaque
Font Size50%75%100%125%150%175%200%300%400%Text Edge StyleNoneRaisedDepressedUniformDropshadowFont FamilyProportional Sans-SerifMonospace Sans-SerifProportional SerifMonospace SerifCasualScriptSmall Caps
End of dialog window.
Smart Sensing
Computer vision and sensors monitor print progress to provide real, in-process QA, alerting you to potential issues to optimize production.
Massive Throughput
Print technology and materials optimized for speed and batch-processing that scales up at predictable and competitive costs.
Modular Hardware
Compact design and modular stacking with the best production capacity per square foot of available production space.
We’ve recently added to our network of material partners
THE LATEST NEWS
Origin – Manufacture the impossible
STRATASYS COMPLETES ACQUISITION OF ORIGIN, ACCELERATING EXPANSION INTO MASS PRODUCTION ADDITIVE MANUFACTURING
Origin’s resin based Programmable PhotoPolymerization (P3) technology addresses fast-growing demand for tooling and end-use parts across multiple applications
EDEN PRAIRIE, Minn. & REHOVOT, Israel, January 5, 2021 – Stratasys Ltd. (NASDAQ: SSYS) announced today it has completed the acquisition of Origin, effective as of Dec. 31, 2020. The acquisition adds Origin’s software-centric additive manufacturing solution that offers best-in-class printing technology based on digital light processing for production-oriented polymer applications.
“The completion of this acquisition marks an important milestone for Stratasys, positioning us to generate meaningful incremental revenue from a wide range of new market opportunities for mass production,” said Stratasys CEO Yoav Zeif. “I’m confident that Origin’s innovative solutions will be a key contributor to strong company growth beginning in 2021 and help us further realize our strategic goal to fortify our leadership position as the ‘first choice’ for polymer 3D printing.”
As previously indicated on December 9, 2020, the impact of the acquisition on Stratasys’ diluted non-GAAP earnings per share is expected to accelerate the company’s growth rate and be slightly dilutive to non-GAAP earnings per share in 2021, and accretive to non-GAAP earnings per share by 2023.
Based in San Francisco, Origin is pioneering a new approach to additive manufacturing of end-use parts. Origin One, the company’s manufacturing-grade 3D printer, uses Programmable PhotoPolymerization to precisely control light, heat, and force, among other variables, to produce parts with exceptional accuracy and consistency. The company works with a network of partners to develop a wide range of commercial-grade materials for its system, resulting in some of the toughest and most resilient materials in additive manufacturing. The company was founded in 2015 and is led by alumni from Google and Apple. Investors include Floodgate, DCM, Mandra Capital, Haystack, TDK Ventures, Stanford University, and Joe Montana. Learn more at www.origin.io.
Stratasys is a global leader in additive manufacturing or 3D printing technology and is the manufacturer of FDM®, PolyJet Technology™, and stereolithography 3D printers. The company’s technologies are used to create prototypes, manufacturing tools, and production parts for industries including aerospace, automotive, healthcare, consumer products and education. For more than 30 years, Stratasys products have helped manufacturers reduce product-development time, cost, and time-to-market, as well as reduce or eliminate tooling costs and improve product quality. The Stratasys 3D printing ecosystem of solutions and expertise includes 3D printers, materials, software, expert services, and on-demand parts production.
To learn more about Stratasys, visit www.stratasys.com, the Stratasys blog,Twitter, LinkedIn, or Facebook. Stratasys reserves the right to utilize any of the foregoing social media platforms, including the company’s websites, to share material, non-public information pursuant to the SEC’s Regulation FD. To the extent necessary and mandated by applicable law, Stratasys will also include such information in its public disclosure filings.
Stratasys, FDM, and PolyJet Technology are trademarks of StratasysLtd. and/or its affiliates. Origin is a registered trademark of Origin. All other trademarks are the property of their respective owners, and Stratasys assumes no responsibility with regard to the selection, performance, or use of these non-Stratasys products.
Cautionary Statement Regarding Forward-Looking Statements
The information contained in this press release may include “forward-looking statements” within the meaning of the Private Securities Litigation Reform Act of 1995, Section 27A of the Securities Act of 1933, and Section 21E of the Securities Exchange Act of 1934. Forward-looking statements are often characterized by the use of forward-looking terminology such as “may,” “will,” “expect,” “anticipate,” “estimate,” “continue,” “believe,” “should,” “intend,” “project” or other similar words, but may be identified in other ways as well. These forward-looking statements may include, but are not limited to, statements relating to the anticipated completion of the acquisition of Origin by Stratasys, Stratasys’ objectives, plans and strategies with respect to Origin following its acquisition, statements that contain projections of results of operations or of financial condition with respect to Origin and Stratasys after the acquisition, and all statements (other than statements of historical fact) that address activities, events or developments that Stratasys intends, expects, projects, believes or anticipates will or may occur in the future. Forward-looking statements are not guarantees of future performance and are subject to risks and uncertainties. Stratasys has based these forward-looking statements on assumptions and assessments made by its management and, in certain cases, by Origin’s management in light of their experience and their perception of historical trends, current conditions, expected future developments and other factors they believe to be appropriate.
Important factors that could cause actual results, developments and business decisions to differ materially from those anticipated in these forward-looking statements include, among other things: any potential obstacles to closing the acquisition of Origin; the degree of success of Stratasys in efficiently and successfully integrating the operations of Origin into Stratasys after the acquisition; the general economic environment and the economic environment for 3D printing and Stratasys’ customers in particular; the impact of competition and new technologies; general market, political and economic conditions in the countries in which Stratasys operates, particularly in respect of the ongoing COVID-19 pandemic; government regulations and approvals; changes in customers’ budgeting priorities; litigation and regulatory proceedings; and those factors referred to under “Risk Factors”, “Information on the Company”, “Operating and Financial Review and Prospects”, and generally in Stratasys’ annual report on Form 20-F for the year ended December 31, 2019 filed with the U.
S. Securities and Exchange Commission, or SEC, on February 26, 2020, and in other reports that Stratasys furnishes to or files with the SEC from time to time, including, most recently, the report of foreign private issuer on Form 6-K reporting Stratasys’ results for the quarter and nine months ended September 30, 2020, furnished to the SEC on November 12, 2020. Readers are urged to carefully review and consider the various disclosures made in Stratasys’ SEC reports, which are designed to advise interested parties of the risks and factors that may affect its business, financial condition, results of operations and prospects. Any forward-looking statements in this press release are made as of the date hereof, and Stratasys undertakes no obligation to publicly update or revise any forward-looking statements, whether as a result of new information, future events or otherwise, except as required by law.
Media Contacts
Stratasys Corporate &North America[email protected] +1 612-716-9228 | Europe, Middle East, and Africa Jonathan Wake / Miguel Afonso, Incus Media [email protected]+44 1737 215200 | Asia Pacific and Japan Alice Chiu [email protected]+852 9189 7273 |
Stratasys Corporate &North America[email protected] +1 612-716-9228 | Europe, Middle East, and Africa Jonathan Wake / Miguel Afonso, Incus Media [email protected]+44 1737 215200 | Asia Pacific and Japan Alice Chiu [email protected]+852 9189 7273 |
History of 3D printing
In this section, we wanted to trace the history of 3D printing from its inception to the present day, as well as give a forecast regarding the future development of technology.
The first 3d printer was invented by the American Charles Hull, he worked on the technology of stereolithography (SLA), a patent for the technology was issued in 1986. The printer was a fairly large industrial installation. The installation "grew" a three-dimensional model by applying a photopolymerizable material to a moving platform. The basis was a digital model pre-modeled on a computer (3D model). This 3d printer created three-dimensional objects, rising by 0.1-0.2 mm - the height of the layer. Despite the fact that the first device had many disadvantages, the technology has received its application. Charles Hull is also the co-founder of 3dsystems, one of the world's leading manufacturers of industrial 3D printers. nine0003
Charles Hull was not the only one to experiment with 3D printing technology, as in 1986 Carl Deckard invented Selective Laser Sintering (SLS). You can learn more about the method in another article, briefly: a laser beam sinters a powder (plastic, metal, etc. ), while the mass of the powder is heated in the working chamber to a temperature close to the melting point. The basis is also a digital model pre-modeled on a computer (3D model). After the laser passes through the horizontal layer, the chamber is lowered to the layer height (usually 0.1-0.2 mm), the powder mass is leveled with a special device and a new layer is applied. nine0003
However, the most famous and widespread 3D printing method today is layer-by-layer direction (FDM). The idea of technology belongs to Scott Crump (Scott Crump), the patent dates back to 1988. You can learn more about the method in another article, in short: material (usually plastic) is fed from the heated nozzle of the print head using a stepper motor, the print head moves on linear guides along 1 or two axes, and the platform moves along 1 or 2 axes . The basis of the movement is also a 3D model. The molten plastic is laid on the platform along the established contour, after which the head or platform is moved and a new layer is applied on top of the old one. Scott Crump is one of the founders of Stratasys, which is also one of the leaders in the production of industrial 3D printers. nine0003
All the devices described above belonged to the class of industrial devices and were quite expensive, so one of the first 3d Dimension printers from Stratasys in 1991 cost from 50 to 220 thousand US dollars (depending on the model and configuration). Printers based on the technologies described above cost even more and until very recently, only a narrow circle of interested specialists knew about these devices.
Everything began to change since 2006, when the RepRap project (from the English Replicating Rapid Prototyper - a self-replicating mechanism for rapid prototyping) was founded, with the goal of creating a self-copying device, which was a 3D printer working on technology FDM (layer by layer deposition). Only, unlike expensive industrial devices, it looked like a clumsy invention made from improvised means. Metal shafts serve as a frame, they also serve as guides for the print head. driven by simple stepper motors. The software is open source. Almost all connecting parts are printed from plastic on the 3D printer itself. This idea originated among English scientists and aimed at spreading available additive technologies so that users can download 3D models on the Internet and create the necessary products, thus minimizing the production chain. nine0003
Leaving aside the ideological component, the community (which exists and develops to this day) managed to create a 3d printer accessible to the "ordinary person". So a set of unprinted parts can cost around a couple of hundred US dollars and a finished device from $500. And even though these devices looked unsightly and were significantly inferior in quality to their industrial counterparts, all this was an incredible impetus for the development of 3D printing technology.
As the RepRap project developed, 3D printers began to appear, taking as a basis the base laid down by the movement in technical and, sometimes, ideological terms (for example, commitment to the concept of open source - OpenSource). The companies that made printers tried to make them better both in terms of performance, design and user experience. The first RepRap printers cannot be called a commercial product, since it is not so easy to manage (and even more so to assemble) and it is not always possible to achieve stable work results. Nevertheless, companies tried to close the more than significant gap in quality, leaving a significant gap in cost whenever possible. nine0003
First of all, it is worth mentioning the MakerBot company, which started as a startup, took RepRap ideas as a basis and gradually turned them into a product of a new quality.
Their flagship product (and in our opinion the best to this day) remains the MakerBot Replicator 2 3D printer. The model was released in 2012 and later discontinued, but remains one of the most popular 3D printer models to this day " personal" segment (according to 3dhubs). The word "personal" is in brackets because this printer, which cost $2,200 at the time of release, was (and is) primarily used for business purposes, but falls into the personal segment due to its cost. This model differs from its progenitors (RepRap), being, in fact, a finished commercial product. Manufacturers abandoned the concept of OpenSource, closing all sources and software codes. nine0003
In parallel with the release of equipment, the company actively developed the Thingiverse resource, which contains many models for 3d printing, available for download for free. During the development of the first printer and beyond, the community has helped the company a lot, testing the product and offering various upgrades. After the release of the Replicator 2 (and the closure of development), the situation has changed. You can learn more about the history of MakerBot and other companies and people associated with 3d printing by watching the film Print the legend. nine0003
This film also highlights the history of Formlabs, one of the first companies to launch an affordable 3D printer based on SLA (Strereolithography) technology. The company raised funds for the first FORM 1 model through crowdfunding, encountered production difficulties, but eventually released an affordable and productive 3D printer, closing the quality gap described above.
And although the 3D printers described above were far from perfect, they laid the foundation for the development of affordable 3D printing technology, which continues to this day. At the moment, the quality of FDM and SLA printers is increasing, but there is no significant price reduction, rather, on the contrary, it is growing slightly. Along with FDM and SLA, many companies are developing in the field of powder sintering (SLS), as well as metal printing. Despite the fact that such printers cannot be called affordable, their price is much lower in comparison with analogues from the professional segment. It is also worth noting the development of the line of materials, in addition to the standard ABS and PLA plastics, today many different materials are used, including nylon, carbon fiber and other durable and refractory materials. nine0003
Personal 3d printers of today are very close to professional devices, the development of which also does not stop. In addition to the "founders" of the technology (Stratasys, 3dsystems), many small companies specializing in industrial 3D printing technologies (metal in particular) have emerged. 3D printing is also attracting the attention of large corporations, which, with varying degrees of success, are striving to take their place in a growing market. Here it is worth highlighting HP, which recently released the HP Jet Fusion 3D 4200 model, which has gained popularity among 3d printing professionals (as of 2018, it is at the top of the ranking of professional 3D printers in the quarterly reports of the 3dhubs portal). nine0003
However, 3D printing technologies are developing not only in breadth, but also in depth. One of the main disadvantages of 3D printing, compared to other production methods, is the low speed of creating models. A significant advance in terms of accelerating 3D printing was the invention of CLIP technology by CARBON, printers operating on this technology can produce models 100 times faster than classic SLA technology.
There is also a constant expansion of the range, properties and quality of materials and post-processing of products. All this accelerates the transition to the use of 3d printers in production, and not just as prototyping devices. Today, many large and not only companies and organizations are closely using a 3D printer in their production chain: from consumer goods manufacturers NIKE and PUMA to BOEING and SPACE X (the latter prints engine parts for its rockets that could not be made in any other way) . nine0003
In addition to the "classic" scope of 3D printing, today more and more often you can see news about how a house or some organ (or rather, a small part of it) was printed on a 3D printer from bio-material. And this is true, several companies around the world are testing or already partially using 3D printing in the construction of buildings and structures. This mainly concerns the contour pouring of walls (similar to the FDM method) with a special composite concrete mixture. And in Amsterdam there is a 3D printed bridge project and this list will only expand over time, since the use of 3D printing in construction can significantly reduce costs and increase the speed of work at certain stages. nine0005 With regards to medicine, here 3D printing also finds application, but at the moment it is not printing organs, but rather the use of technology in prosthetics (of various kinds) and bone replacement. Also, 3D printing technology is widely used in dentistry (SLA technology). Regarding the printing of organs, this is still far in the future, at the moment bio-3D printers are experimental facilities in the early stages, the success of which is limited to printing a few limited-viable cells. nine0003
Looking to the future, it is safe to say that 3D printing technology will expand both in breadth and depth, improving technology, speeding up processes, improving quality and improving material properties. 3D printers will increasingly replace old methods in production chains of various scales, and world production, due to this, will move towards the “on demand” scheme of work, increasing the degree of product customization. Perhaps someday, 3D printers will be widely used at the household level for the production of necessary things (the dream and goal of the RepRap movement), but this requires not only the development of technology, but also a paradigm shift in social thinking, as well as the development of a powerful design ecosystem ( 3d modeling) products (which is often forgotten). nine0003
3d printing of houses (and other structures) will no doubt also develop, reducing costs and production time, which, together with the development of new approaches in architecture and urban planning (such as modular construction and the prefabricated method), will give a tangible impetus to development the industry as a whole.
Biological 3D printers will be an important tool in scientific research. However, before they appear in hospitals and clinics, where they will print new organs, it is still very, very far away (in fact, this is science fiction). nine0003
Alcom | History of 3D printers
May 13, 2018
Since the beginning of the new millennium, the concept of "3D" has firmly entered our daily lives. First of all, we associate it with cinema, photography or animation. But there is hardly a person now who has not heard about such a novelty as 3D printing at least once in his life.
What is it and what new opportunities in creativity, science, technology and everyday life bring us 3D printing technologies, we will try to figure it out in the article below. nine0003
But first, a little history. Although there has been a lot of talk about 3D printing in the last few years, in fact, this technology has been around for a long time. In 1984, Charles Hull developed a 3D printing technology for reproducing objects using digital data, and two years later named and patented the stereolithography technique.
At the same time, this company developed and created the first industrial 3D printer. Subsequently, the baton was taken over by 3D Systems, which developed in 1988 printer model for 3D printing at home SLA - 250.
In the same year, fused deposition modeling was invented by Scott Grump. After several years of relative calm, in 1991 Helisys develops and markets a technology for the production of multilayer objects, and a year later, in 1992, the first selective laser soldering system is released at DTM.
Then, in 1993, Solidscape was founded, which began mass production of inkjet-based printers that are capable of producing small parts with an ideal surface, and at a relatively low cost. nine0003
At the same time, the University of Massachusetts patents a 3D printing technology similar to conventional 2D inkjet technology. But, perhaps, the peak of development and popularity of 3D printing still fell on the new, 21st century.
In 2005, the first 3D printer capable of printing in color appeared, this is the brainchild of Z Corp called the Spectrum Z510, and literally two years later the first printer appeared that could reproduce 50% of its own components.
Currently, the scope and scope of 3D printing is constantly growing. Everything turned out to be subject to these technologies - from blood vessels to coral reefs and furniture. However, we will talk about the areas of application of these technologies a little later. nine0003
So, what is printing on a 3d printer?
In short, this is the construction of a real object according to a 3D model created on a computer. Then the digital three-dimensional model is saved in the STL file format, after which the 3D printer, to which the file is output for printing, forms a real product.
The printing process itself is a series of repetitive cycles associated with the creation of three-dimensional models, applying a layer of consumables to the desktop (elevator) of the printer, moving the desktop down to the level of the finished layer and removing waste from the surface of the table. nine0003
The cycles follow one after another continuously: the next layer of material is applied on the first layer, the elevator is lowered again and so on until the finished product is on the working table.
How does a 3D printer work?
The application of 3D printing is a serious alternative to traditional methods of prototyping and small-scale production. A three-dimensional or 3D printer, unlike a conventional one that prints two-dimensional drawings, photographs, etc. on paper, makes it possible to output three-dimensional information, that is, to create three-dimensional physical objects. nine0003
At the moment, this class of equipment can work with photopolymer resins, various types of plastic filament, ceramic powder and metal clay.
What is a 3d printer?
The principle of operation of a 3d printer is based on the principle of gradual (layered) creation of a solid model, which, as it were, is “grown” from a certain material, which will be discussed a little later. The advantages of 3D printing over the usual, manual methods of building models are high speed, simplicity and relatively low cost. nine0003
For example, to create a 3D model or any part manually, it can take quite a long time - from several days to months. After all, this includes not only the manufacturing process itself, but also preliminary work - drawings and diagrams of the future product, which still do not give a complete vision of the final result.
As a result, development costs increase significantly, the period from product development to its mass production increases.
3D technologies, on the other hand, allow you to completely eliminate manual labor and the need to make drawings and calculations on paper - after all, the program allows you to see the model from all angles already on the screen, and eliminate the identified shortcomings not in the process of creation, as is the case with manual production, but directly during development and create a model in a few hours. nine0003
This virtually eliminates the possibility of manual errors.
What is a 3d printer: video
There are various 3D printing technologies. The difference between them lies in the way the product layers are applied. Let's consider the main ones.
The most common are SLS (selective laser plexus), HPM (molten material overlay) and SLA (stereolithiography).
The most widely used technology due to the high speed of building objects is stereolithography or SLA. nine0003
SLA Technology
The technology works like this: a laser beam is directed onto a photopolymer, after which the material hardens.
The photopolymer is a translucent material that deforms when exposed to atmospheric moisture.
Once cured, it can be easily glued, machined and painted. The working table (elevator) is in a container with a photopolymer. After the laser beam passes through the polymer and the layer hardens, the working surface of the table moves down. nine0003
SLS Technology
Sintering powder reagents under the action of a laser beam - it is also SLS - the only 3D printing technology that is used in the manufacture of molds for both metal and plastic casting.
Plastic models have excellent mechanical properties, which make them suitable for making full-featured items. SLS technology uses materials that are similar in properties to the brands of the final product: ceramics, powdered plastic, metal. nine0003
The 3D printer device looks like this: powder substances are applied to the surface of the elevator and sintered under the action of a laser beam into a solid layer that corresponds to the parameters of the model and determines its shape.
DLP Technology
DLP technology is new to the 3D printing market. Stereolithographic printers are positioned today as the main alternative to FDM equipment. This type of printer uses digital light processing technology. Many people wonder what the 3d printer of this sample prints with? nine0003
Instead of a plastic filament and a heating head, photopolymer resins and a DLP projector are used to create three-dimensional figures.
Below you can see how the 3d printer works video:
Having heard about a DLP 3d printer for the first time, what it is is a completely reasonable question. Despite the intricate name, the device is almost no different from other desktop printers. By the way, its developers, represented by
QSQM Technology Corporation, have already launched the first samples of high-tech equipment into a series. It looks like this:
EBM Technology
It should be noted that SLS/DMLS technologies are far from the only ones in the field of metal printing. Currently, electron beam melting is widely used to create metal three-dimensional objects. Laboratory studies have shown that the use of metal wire for layer-by-layer deposition in the manufacture of high-precision parts is ineffective, so engineers have developed a special material - metal clay.
nine0002 The metal clay used as ink during electron beam melting is made from a mixture of organic glue, metal shavings and a certain amount of water.
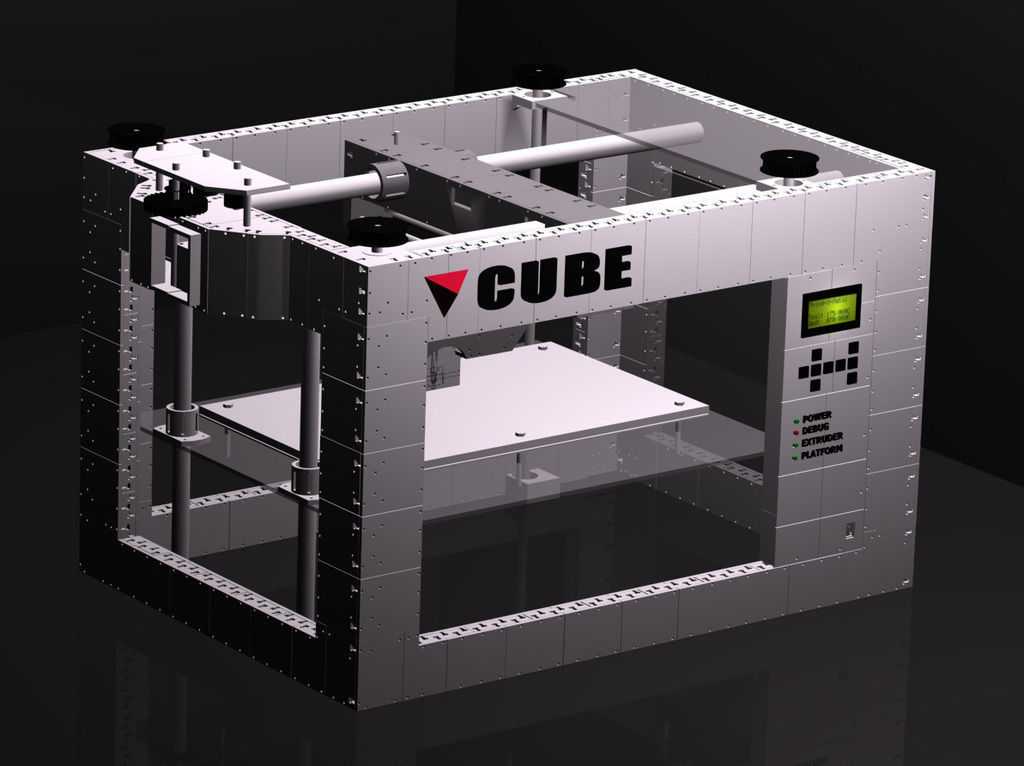
EBM 3d printer: how
worksIt is noteworthy that this principle is also used when working with SLS printers. But unlike them, EBM machines generate directed electron pulses instead of a laser beam to melt metal clay. I must say that this method provides high print quality and excellent drawing of small details. nine0003
Today, only industrial printers using EBM technology are sold. Here is what one of them looks like:
The video below demonstrates the capabilities of a 3d printer adapted for electron beam melting:
HPM Technology (FDM) HPM
Allows you to create not only models, but also final parts from standard, structural and high-performance thermoplastics. It is the only technology that uses production grade thermoplastics to provide unparalleled mechanical, thermal and chemical strength to parts. nine0003
HPM Printing stands out for its cleanliness, ease of use and suitability for office use. Thermoplastic parts are resistant to high temperatures, mechanical stress, various chemicals, wet or dry environments.
Soluble auxiliary materials allow the creation of complex multi-level shapes, cavities and holes that would be problematic to obtain with conventional methods. HPM 3D printers create parts layer by layer by heating the material to a semi-liquid state and extruding it according to computer-generated paths. nine0003
HPM printing uses two different materials - one (main) will consist of the finished part, and an auxiliary, which is used for support. The filaments of both materials are fed from the 3D printer bays into the print head, which moves based on changes in the X and Y coordinates and fuses the material, creating the current layer, until the base moves down and the next layer begins.
When the 3D printer has finished creating the part, it remains to separate the auxiliary material mechanically, or dissolve it with detergent, after which the product is ready for use. nine0003
Interestingly, not only automatic desktop HPM printers are popular these days, but also manual printing devices. Moreover, it would be correct to call them not printing devices, but pens for drawing three-dimensional objects.
Pens are made in the same way as printers using fusing technology. The plastic thread is fed into the pen, where it melts to the desired consistency and is immediately squeezed out through a miniature nozzle! With proper skill, these original decorative figures are obtained:
And of course, just like technologies, printers themselves differ from each other. If you have a printer that works according to SLA, then it will be impossible to apply SLS technology on it, i.e., each printer was created only for a certain printing technology.
3D printing applications
3D printing has opened up great opportunities for experimentation in areas such as architecture, construction, medicine, education, clothing design, small-scale production, jewelry, and even in the food industry. nine0003
In architecture, for example, 3D printing allows you to create three-dimensional models of buildings, or even entire neighborhoods with all the infrastructure - squares, parks, roads and street lighting.
Thanks to the cheap gypsum composite used, the cost of finished models is low. And more than 390 thousand CMYK shades make it possible to embody any, even the most daring, imagination of an architect in color.
3d printer: construction application
In construction, there is every reason to believe that in the near future the process of erecting buildings will be much faster and easier. Californian engineers have created a 3D printing system for large objects. It works on the principle of a construction crane, erecting walls from layers of concrete.
This printer can build a two-story house in just 20 hours.
After that, the workers will only have to carry out finishing work. 3D House 3D printers are gradually gaining a strong position in small-scale production. nine0003
These technologies are mainly used for the production of exclusive products, such as art, role-playing game characters, prototype models of future products or any structural parts.
In medicine, thanks to 3D printing technologies, doctors have been able to recreate copies of the human skeleton, which allows them to more accurately practice techniques that increase the guarantee of successful operations.
3D printers are increasingly being used in the field of prosthetics in dentistry, as these technologies allow much faster production of prostheses than with traditional manufacturing. nine0003
Not so long ago, German scientists developed a technology for obtaining human skin. In its manufacture, a gel obtained from donor cells is used. And in 2011, scientists managed to reproduce a living human kidney.
As you can see, the possibilities that 3D printing opens up in almost all areas of human activity are truly endless.
Printers that create culinary masterpieces that reproduce prostheses and human organs, toys and visual aids, clothes and shoes are no longer a figment of the imagination of science fiction writers, but the realities of modern life.