Nylon for 3d printer
Ultimate Materials Guide - 3D Printing with Nylon
Overview
Nylon (a.k.a. Polyamide) is a popular material in the plastics industry, known for its toughness and flexibility. Nylon filaments typically require extruder temperatures near 250 ºC, however, some brands allow printing at temperatures as low as 220 ºC due to their chemical composition. Many printers do not include a hotend that can safely reach 250 ºC, so these lower-temperature versions can be useful and potentially save you from needing to upgrade your hotend. One big challenge with Nylon filaments is that they are hygroscopic, which means they readily absorb moisture from their surroundings. Printing Nylon after it has absorbed moisture will lead to several print quality issues, thus filament storage becomes very important and requires special attention.
- Tough and partially flexible
- High impact resistance
- No unpleasant odor while printing
- Good abrasion resistance
- Prone to Warping
- Air-tight storage required to prevent water absorption
- Improperly dried filaments can cause printing defects
- Not suitable for moist and humid environments
Hardware Requirements
Before 3D printing with Nylon make sure your 3D printer meets the hardware requirements listed below to ensure the best print quality.
Bed
Temperature: 70-90 °C
Heated Bed Required
Enclosure Recommended
Build Surface
Glue Stick
PEI
Extruder
Temperature: 225-265 °C
May require All-Metal hotend
Cooling
Part Cooling Fan Not Required
Best Practices
These tips will help you reduce the chances of common 3D printing issues associated with Nylon such as warping and moisture absorption.
Filament Storage
One of the challenging aspects of using Nylon is the need for a special storage system. Unlike other filaments, you cannot keep the filament spool exposed to the air for extended periods of time. Nylon easily absorbs moisture from the environment. Printing the moist filament will result in print quality issues like a foggy rough surfaces or even tiny holes or bubbles on the exterior. These printing issues can also significantly decrease the strength and performance of the printed parts. The typical solution for this issue is to remove the Nylon spools from the printer once you are done, and store the spools in an air-tight container along with some desiccants to remove the moisture from within. If you do not want to constantly mount and remove your filament spool, there are also commercially available storage containers that will keep the filament dry, while allowing it to feed out of a hole in the container.
Use an Enclosure to Prevent Warping
Some high-temperature Nylons are prone to warping due to the large temperature change between the extruded plastic and the ambient environment. Heated beds can reduce the warping to a some extent, but using a printer that has a heated chamber or enclosure would be the ideal solution. Keeping the air around your part at a temperature of about 45 ºC will help eliminate warping by reducing this temperature variation. If your printer doesn’t include a heated chamber and you aren’t able to add an enclosure, there are other tips that you can use to help prevent warping. Our Print Quality Guide has an entire section devoted to this issue which summarizes other common techniques: How to Prevent Warping.
Using Brims and Rafts
In situations where adding an aftermarket enclosure may not be an ideal option, consider using a brim or a raft to help with first layer adhesion. Adding a brim will add several loops around the bottom layer of your model, creating a larger surface area to hold down the edges of your print. Version 4.0 of Simplify3D introduced a completely new raft design that can also be very useful if you continue to have printing difficulties. For more information on the differences between rafts, skirts, and brims, please consult our in-depth article on this topic.
Pro-Tips
- If you do not have air-tight containers for storing your filament, you can dry the spools just before use by running them through a Food Dehydrator. A few hours in this device will dry the filament significantly.
- Nylon makes a good filament for cleaning your nozzle. You can use a technique called “cold pulling” where you allow the Nylon to bond to debris within the nozzle, and then after it partially cools, you pull the filament (and debris) out of the hotend.
Get Started with Nylon
Nylon can be a great material once you have mastered the basics. Once you’re ready to give it a try, here are some tips to help you get started.
Common Applications
- Plastic Gears
- Screws, nuts, bolts
- Cable ties
Sample Projects
- Cable ties
- Nut, Bolt, Washer
- Servo Gears
Popular Brands
- Taulman Nylon
- Matterhackers PRO Nylon
- HobbyKing Nylon
- GizmoDorks Nylon
Everything you need to know about Nylon 3D printing
Before you get started with Nylon 3D Printing, we’ve compiled some of the basic information you’ll need to know. Read on to learn the advantages, disadvantages, history and applications of Nylon 3D printing
Nylon Filament and 3D Printed Gear
When it comes to 3D printing materials, Nylon has to be mentioned as one of the most popular materials for professional users. This can be attributed in large part to its popularity outside of 3D printing. Nylon has a wide range of applications thanks to its unique properties and the benefits of 3D printing mean that parts can be made on the fly easily and inexpensively.
That said, desktop Fused Deposition Modeling (FDM) 3D printing technology, which is one of the most widely-used types of 3D printing, can sometimes involve a lot of trial and error. Some materials are easy to print with while others have a comparatively bigger learning curve.
Through this article, we will share everything you should know about Nylon 3D printing. Nylon can be 3D printed using three different technologies, namely FDM, Selective Laser Sintering (SLS), and MultiJet Fusion (MJF). However, the scope of this article is focused around FDM 3D printing.
UNDERSTANDING NYLON AS A MATERIAL
Chemical Composition
Nylon was first synthesized by DuPont, the American chemical company, in 1935. It developed the material for commercial usage and since then Nylon has become a common feature in numerous industries.
Nylon refers to a group of plastics known as polyamides. They are mostly semi-crystalline and generally very tough materials. It is found in many variants but the most common ones are Nylon 6, Nylon 6-6, and Nylon 12. It is a thermoplastic material, i.e., it becomes soft on heating or liquid when heated beyond its melting point and hardens on cooling. This process of heating and cooling can be carried out multiple times without significantly affecting its inherent chemical or mechanical properties.
Nylons can be easily blended with numerous other plastics to form composites, enhancing their performance parameters. This is widely done in automotive industries and some common composites in 3D printing are glass-filled nylon and carbon-fiber-filled nylon. Nylon is a versatile material and is suitable for almost all types of manufacturing operations like injection molding, extrusion, and additive manufacturing (in FDM, SLS & MJF).
Some of the most popular applications of nylon material are:
➜ In the textiles industry, nylon is used in the manufacturing of fishing lines, and food packaging.
➜ In the fashion industry, nylon is used as a fabric to manufacture products like hosiery, lingerie, raincoats, windbreakers, and athletic wear used in sports.
➜ In the electronics industry, nylon is used as insulators and switch housings.
➜ In the automotive industry, nylon is used in the production of parts such as intake manifolds, door handles, and radiator grills.
In consumer products, nylon is used in sporting goods such as ski bindings and skateboard wheels.
➜ In manufacturing machinery for moving parts such as gears and rollers.
NYLON in 3D PRINTING
In the same way that nylon has become a go-to material in traditional manufacturing, nylon has become a popular material to use with 3D printers. 3D printing provides the added benefits of unlimited geometries, iteration and customization, and low-volume affordability.
Nylon’s flexibility and durability help in 3D printing parts with thin walls. Its low coefficient of friction with a high melting point makes it especially resistant to abrasion and enables it to be used in printing for parts such as functional interlocking gears.
Nylon exhibits mechanical properties comparable to ABS (another widely used material in traditional & additive manufacturing). ABS is defined by its strength but Nylon’s resistance to wear and fatigue makes it superior for applications requiring such properties.
Apart from the advantages, nylon has one major drawback that can often hamper its printing performance – hygroscopicity, i.e., its moisture absorption property. This property is detrimental in delivering predictable performance. But this same property helps nylon in easy post-processing with fabric dyes and spray paints thereby making it suitable for use in the printing of aesthetic (display) models.
There have been successful cases of a patient receiving a titanium pelvis implant, another getting a new titanium lower jaw. A motorcyclist patient whose face had been seriously injured in a road accident had it rebuilt with 3D printed parts.
Bioprinting allows for the 3D printing of artificial organs, helping solve organ failure issues in patients faster, important to both the patient and his/her family and to healthcare systems.
3D printed tissues have been developed for pharmaceutical testing as a cost-effective and ethical means of helping identify the side effects of drugs and validating safe dosages.
Pills can be produced, using the 3D printing process of Binder Jetting. The process allows the pills produced to be very porous, therefore enabling high dosages in a single pill that can be dissolved quickly and easily digested, useful for treating conditions such as epilepsy.
FUSED DEPOSITION MODELING (FDM) NYLON 3D PRINTING
As mentioned earlier, nylon 3D printing in FDM is a bit difficult but with the right tools it can be used to produce consistent results. We will start with some of the common challenges with nylon 3D Printing.
Common Challenges with Nylon 3D Printing
One challenge in nylon 3D printing is that nylon is highly hygroscopic. Even short-term exposure to high humidity can result in “wet” filament which, when printed, can lead to inconsistency in dimensional accuracy and part strength. Due to this property, it is critical to store the nylon filament in a dry place. Professional FDM 3D printers are enclosed so moisture can be safely avoided but for new users working with DIY or cheaper desktop printers, the material is exposed to air while printing. This makes it prone to moisture. The moisture absorbed by nylon gets heated up when it passes through the heater and the moisture forms bubbles only to burst during the heating process. This bursting leaves visible gaps in the 3D printed parts, leading to poor output.
Additionally, nylon is prone to warping issues. Warping occurs when there is uneven cooling of the print and the print curls from the build plate, distorting the printed part. This can be avoided by efficient gluing of the print bed and using a heated bed to keep the bottom layer of the print mildly heated so that it sticks to the bed for the duration of the print. As an extra precaution, the cooling fans can be switched off (all slicers have options to switch off fans during printing) while printing with nylon.
It is also recommended that printing nylon is conducted in a well-ventilated area due to its chemical composition.
Solutions to Nylon 3D Printing
Luckily, there are professional 3D printers such as the MakerBot METHOD that are both affordable for businesses, and have features that enable easy and consistent 3D printing with nylon. One example of these advanced professional features is an enclosed heated build chamber, which minimizes warping and inconsistent cooling during the print, and can also be used before printing to dry the filament on the spool. Another such feature is sealed material bays, which prevents the material from contact with the surrounding environment. These two additions almost entirely solves the problems associated with nylon 3D printing and might be worth considering during purchase if nylon is a preferred 3D printing material.
FDM NYLON MATERIAL PROPERTIES
PARAMETER | Imperial | Metric |
---|---|---|
Heat Deflection (ASTM 648, 66 psi) | 196°F | 91°C |
Flexural Modulus (ASTM D790, 15 mm/min) | 250,000 psi | 1,700 MPa |
Flexural Strength (ASTM D790, 15 mm/min) | 14,000 psi | 97 MPa |
Tensile Strength at yield (ASTM D638, 50 mm/min) | 9500 psi | 66 MPa |
Tensile Modulus (ASTM D638, 50 mm/min) | >320,000 psi | >2,200 MPa |
Strain at Yield - Elongation (%) | >10% | >10% |
Notched Impact Strength (ASTM D256) | >3.![]() | >187 J/m |
(Specifications for MakerBot Nylon)
ADVANTAGES
➜ Mechanical Properties
➀ High impact resistance - Durable in situations where parts are constantly banging together or being dropped.
➁ Abrasion resistant - Nylon’s low coefficient of friction allows nylon to be used in applications with moving parts that would otherwise wear on each other
➂ Flexible - In thinner geometries nylon can be flexed repeatedly without fracturing
➜ Post-Processing: Nylon is hygroscopic and this property helps it to be easily post-processed by absorbing fabric dyes and spray paints.
DISADVANTAGES
➜ Hygroscopic: Nylon is hygroscopic, i.e., it absorbs moisture from the air which can affect its print quality and ultimately the part performance.
➜ Pre-Drying: Nylon should be pre-dried to remove any moisture it has absorbed. This requires extra effort, extra equipment, and extra time. And if the drying is insufficient, then the print shows
➜ Warping: Nylon is prone to warping and thus can distort the part.
WHERE TO BUY?
Nylon material can either be bought from filament manufacturers or 3D printer manufacturers.For the MakerBot 3D METHOD, we recommend use of MakerBot Nylon as it is optimized to deliver great results.
Looking for a professional 3D printing platform that works with a variety of manufacturing-grade materials? Learn more at makerbot.com/method.
Related Posts
3D Printable Nylon
- 1 Description
- 2 Specifications
- 3 Advantages and disadvantages of nylon
- 3.1 Features
- 3.2 Disadvantages
- 4 3D printing use
- 5 Use of available materials
Description
Nylon is attractive as a material for 3D printing due to its high wear resistance, affordability and excellent slip coefficient, which allows the use of nylon in bearings and other similar mechanisms, often without the use of lubricants.
An example of a model created using Stratasys Nylon 12
Despite the widespread use of nylon in the industry, the use of this material in 3D printing is quite limited due to certain technological difficulties. However, in recent years, specialized nylon consumables have appeared, focused on use with SLS and FDM printers.
Taulman and Stratasys nylon threads are the most popular examples.
Specifications
Taulman 618 | Taulman 645 | Stratasys Nylon 12 | |
Density | 1.134 g/cm³ | – | – |
Hygroscopicity | 3.09% | 3.09% | – |
Tensile strength | 65.![]() | 85.68 MPa | 48.26-53 MPa |
Elongation at Break | Over 300% | Over 300% | 9.5-30% |
Melting point | 218°C | 214°C | 178°C |
Glass transition temperature | 49.4°C | 68.2°C | – |
Extrusion temperature | 235-260°C | 235-260°C | – |
Pyrolysis temperature | 350-360°C | 350-360°C | – |
Stratasys Nylon 12 is designed for use with Fortus brand 360mc, 400mc and 9 professional rigs00mc, while Taulman's nylon filaments are designed to work with any home and office 3D printer optimized for the popular ABS plastic. In addition, Taulman is testing a range of laser sintered nylon materials, including a powder version of Taulman 618.
Advantages and disadvantages of nylon
Advantages of
- High wear resistance
- High elasticity
- Resistant to most organic solvents
- High temperature resistance
- Easy to machine
Disadvantages
- High hygroscopicity
- Release of toxic fumes during pyrolysis
- Taulman brand nylon threads available in 1.75mm and 3mm diameters
3D printing use
Taulman brand nylon filaments are available in 1.75mm and 3mm diameters
Nylon printing technology is similar to ABS printing, but with some differences. Like ABS, nylon is prone to twisting and warping when cooled unevenly, requiring the use of a heated bed.
The nylon layers have excellent adhesion, which minimizes the chance of delamination of models. Users of Taulman plastics note the durability of models at the level of analogues made by traditional injection molding.
Nylon is almost impossible to bond, which makes it difficult to manufacture large-sized parts from components. Alternatively, it is possible to connect nylon parts by melting the surfaces to be joined.
Nylon can be dyed with acid-based dyes.
Nylon does not adhere to glass or other smooth surfaces, so it is recommended to apply painter's tape to the desktop or use a wood backing when printing.
Due to the high hygroscopicity of nylon (the ability to absorb moisture), it is recommended to dry the nylon filament immediately before printing. Otherwise, water vapor may be released from the nozzle, which is not catastrophic for the extruder, but may affect print quality.
Use of scrap materials
Some hobbyists prefer to use inexpensive nylon line for printing, which is fraught with some unpleasant consequences. As a general rule, trimmer line is preferred, available in 3mm diameter, which is the same diameter as commercially available ABS filaments for FDM printing. However, these "nylon threads" are not pure nylon, which is evident due to their excessive stiffness, which is not characteristic of nylon. The reason for this is additives - usually in the form of fiberglass. Additives are designed to both increase stiffness and reduce the cost of the material. It should be borne in mind that the melting point of fiberglass is much higher than the melting point of nylon and, in fact, exceeds the pyrolysis temperature of nylon. Thus, it is impossible to achieve complete melting of such composite materials. As a result, tough glass fiber particles will contribute to increased wear and clogging of the extruder nozzle.
Go to the main page of the Encyclopedia of 3D Printing
Features 3D printing Nylon plastic (nylon)
3DPrintStory    3D printing process    Features of 3D printing Nylon plastic (nylon)
Nylon is a polyamide that is often (though not always) found in PA 11 and PA 12 variants. Nylon is a very strong and durable material, providing some flexibility in thin walls. Since Nylon has a high melting point and a very low coefficient of friction, it is mainly used for 3D printing of functional assemblies that have good strength.
Another important property of Nylon plastics is hygroscopicity, in other words, it absorbs moisture. This property can be useful as 3D printed models are easily processed with fabric and spray paints. But it also makes Nylon prone to picking up moisture from the air, which affects its performance and causes problems during direct 3D printing.
Nylon 3D printing can be realized with Fused Deposition Modeling (FDM), Selective Laser Sintering (SLS) and MultiJet Fusion (MJF).
Standard 3D printer settings for printing Nylon plastic
- Nozzle temperature: 220° C to 270° C
- Table temperature: 75° C to 90° C
- Print speed: approx. may differ)
- Soluble: No
- Hygroscopic: yes
- Fatigue resistance: Yes
- Temperature resistant: Yes
- Impact resistant: Yes
- Flexibility: Yes (thin-walled)
- Deformation: moderate
3D printing technologies used for Nylon plastics you use FDM 3D printing, but if you use SLS and MJF 3D printing options, then these problems will not be relevant for you, so below we will look especially at 3D printing with nylon using various technologies.
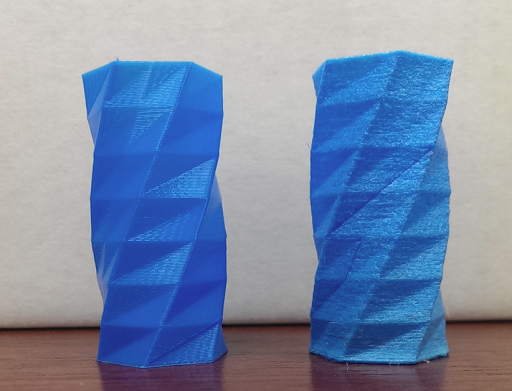
FDM 3D printing
Nylon is highly hygroscopic, meaning it absorbs moisture from the air. Therefore, nylon should be stored in a dry place with silica gel. In practice, it absorbs about 10% of its weight in the form of water. When the material is heated during 3D printing, moisture rushes out, affecting not only the substrate and layer adhesion, but also giving the surface an unwanted roughness.
Therefore, it is recommended to dry it before 3D printing. Oven drying is one of the best options for successful printing.
Nylon also has problems with first coat adhesion. When 3D printing with nylon, it is recommended to use a heated table. In addition to heating the table, you should also think about applying glue to its surface. Avoid using cooling fans.
Nylon oven drying instructions. Before inserting the plastic, the oven must be preheated to the desired temperature. Make sure the temperature is set correctly as overheating can cause the plastic to melt.
General drying settings. Typically preheating temperature: 70° C to 80° C. Required time: 4 to 6 hours. After completion of the drying process described above, the nylon should be placed in a sealed container with a desiccant.
IMPORTANT. Set the drying temperature so that it is below the glass transition temperature (Tg) otherwise you may ruin the plastic.
Selective Laser Sintering (SLS)
SLS is the most suitable technology for nylon 3D printing. 3D printing nylon mainly exists as PA 11 and PA 12 or as composite materials such as carbon fiber nylon and glass fiber. Nylon PA 11 is more flexible than PA 12, while the latter has excellent mechanical properties ideal for functional prototypes.
When printing with SLS, nylon is added as a powder. This technology produces excellent 3D models with excellent material properties, albeit with a slightly rough surface.
Standard Nylon SLS Print Settings:
- Tolerance: ± 0.3% (min: ± 0.
Learn more