Laser metal sintering 3d printer
Direct Metal Laser Sintering [DMLS] Parts On Demand
Direct Metal Laser Sintering [DMLS] Parts On Demand - Stratasys Breaking The Sound Barrier Webinar With Our Guest Boom Supersonic - Click Here to RegisterUSA & Canada
Select your country and region
- Americas
- English
- Español (México)
- Português (Brasil)
- EMEA
- English (United Kingdom)
- Deutsch
- Español
- Français
- italiano
- APAC
- 中文(简体)
- 日本語 (日本)
- 한국어(대한민국)
- English (India)
USA & Canada
Parts On Demand
What Is Direct Metal Laser Sintering?
Direct Metal Laser Sintering (DMLS) is a direct metal laser melting (DMLM) or laser powder bed fusion (LPBF) technology that accurately forms complex geometries not possible with other metal manufacturing methods.
DMLS Part Strength
DMLS parts are stronger and denser than investment casted metal parts, and they can help you get to market first with faster turnaround times.
Metal 3D printing is an ideal process for complex oil and gas components, custom medical guides, part-consolidated aerospace parts and tough functional prototypes.
Streamlined Metal Parts with DMLS
Utilize the design freedom of DMLS and produce accurate metal components in less time than other manufacturing methods.
How Does Direct Metal Laser Sintering Work?
DMLS uses a precise, high-wattage laser to micro-weld powdered metals and alloys to form fully functional metal components from your CAD model.
DMLS parts are made with powdered materials like aluminum, stainless steel and titanium, as well as niche alloys like MONEL® K500 and Nickel Alloy 718.
Finishing DMLS Parts
Raw DMLS parts have a surface finish comparable to a fine investment casting part, and expert finishing services are sometimes needed.
Stratasys Direct offers a full suite of professional finishing operations, including precision machining, media blasting, surface grinders and milling.
Direct Metal Laser Sintering Quality Controls
To maintain critical quality control standards, we use a range of tools to inspect and ensure customer specifications. With international certification standards ISO 9001 and AS9100, we have stringent systems in place to guarantee quality and consistently are met.
We utilize tools like coordinate measuring machines, probes, cutup metallography processes and flow benches, hydrostatic pressure testing machines to guarantee quality is consistently met. DMLS materials build fully dense, corrosive resistant and highly robust metal parts that can be further treated through heat, coating and sterilization.
DMLM Products
Essentials
- The fastest way to manufacture with DMLM technology
- Produce geometries with high-strength metal alloys in one fluid build
- Hand-finishing with media blast
- Manufacture in Stainless Steel 316L or 17-4, Aluminum (AlSi10Mg), Cobalt Chrome, Nickel Alloy 625, and Titanium (Ti64)
A.
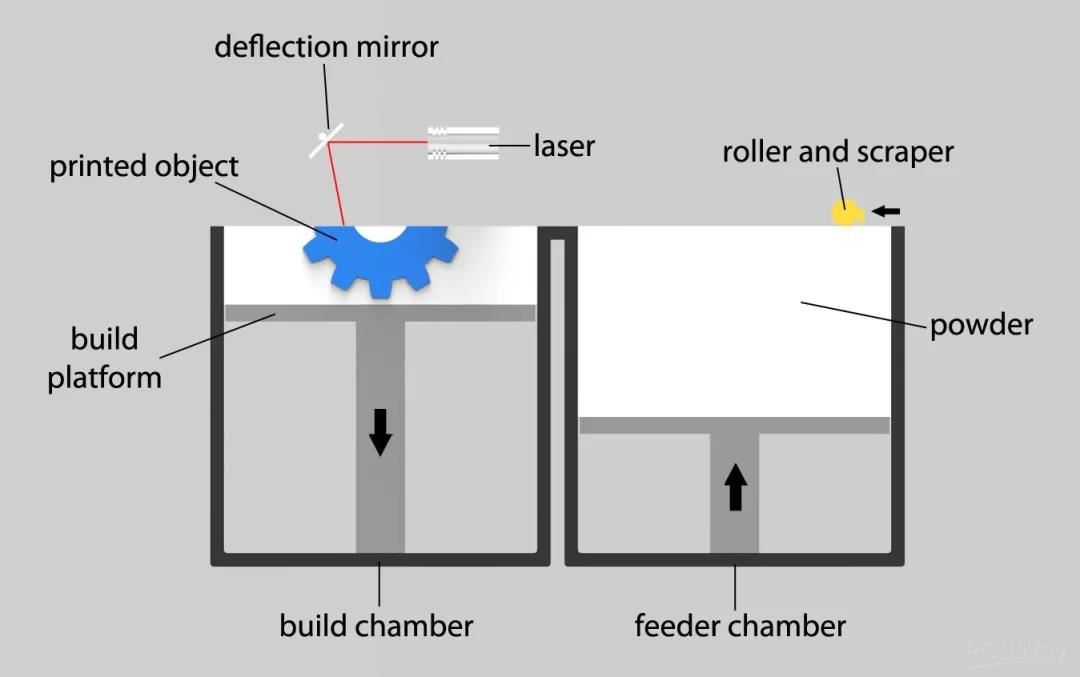
- No spec? No problem! Our Additive Metal Process Spec provides production metal parts with DMLM technology
Customer Specification
- Adhering to customer-provided statement of work and process, material, and/or machine specifications. The ultimate level of control for your project and product
DMLM Discover
We’re ready to take on any challenge and push the boundaries of what’s possible with DMLM Discover – our custom solution for new and novel additive alloys and designs.
- Access materials in the early stages of development for DMLM
- Test custom manufacturing parameters for your project
Materials for 3D Printing Parts with DMLS
Stainless Steel 17-4 PH (As Built)
SS17-4PH is characterized by excellent weld-ability, good corrosion resistance, and mechanical properties
Learn more
Stainless Steel 316L (As Built)
SS316L is characterized by very good weld-ability, corrosion resistance, and mechanical properties including excellent ductility.
Learn more
Aluminum AlSi10Mg (As Built)
Casting grade alloy
Learn more
Nickel Alloy 625 (As Built)
Nickel based superalloy
Learn more
Nickel Alloy 718 (As Built)
High strength nickel base superalloy
Learn more
Nickel Alloy K500 (As Built)
Age-hardenable Nickel-Copper alloy
Learn more
Titanium Ti64 (As Built)
Titanium alloy
Learn more
Cobalt Chrome CoCrMo (As Built)
Metal alloy of cobalt and chromium
Learn more
Metal 3D Printing Applications of DMLS
PRODUCTION PARTS
Produce low-volume production metals parts with DMLS.
Read More
Functional Prototyping
Build tough and hardworking metal prototypes to test components in real-world applications.
Read More
Thermal Control Systems
Advance your thermal management capabilities with complex heat exchangers and heat pipes manufactured with DMLS.
DMLS Parts from 3D Printing Pioneers
Making a quality 3D printed part takes more than just a machine. It takes a responsive team behind the technology, running tests and working tirelessly to validate materials and processes.
At Stratasys Direct, our services are backed by more than the largest fleet of machines in North America; we have nearly thirty years in the industry and a team of engineers ready to assist with every step of your project.
DMLS Expertise You Can Trust
Years of experience with DMLS has led us to develop proprietary build styles, post-processing methods, and even led us into material development exploration.
Whatever your project need, we won’t rest until your requirements are met.
Frequently Asked Questions About DMLS
Are DMLS parts as strong as traditionally manufactured metal components?
Yes. The parts created with DMLS have mechanical properties equivalent to a cast metal part. Detailed information can be found on the DMLS materials page.
What is the porosity of DMLS parts?
DMLS parts can reach a 99.5% density. In fact, 3D printed metals are above industry standards for density testing.
What level of detail can be obtained with DMLS?
DMLS is available in several resolutions. At its highest resolution, the layer thickness is 0.0008” – 0.0015” Z and the X/Y resolution is 0.012” – 0.016”.
The minimum hole diameter is 0.035” – 0.045”. Read the DMLS design guidelines to learn more.
Small Metal 3D Printer specialized for Medical Products
10_filigreeSmall laser spot for complex and delicate parts
12_laser200-watt fiber laser for consistent part quality
60_resp_peopleEspecially suitable for medical applications
The power stability of the 200-watt fiber laser ensures optimal and consistent processing. The small laser spot with excellent detail resolution is ideal for manufacturing highly complex, delicate parts.
With its small build space on a round construction platform of 100 mm in diameter, the system is primarily geared towards cost-efficient production in small quantities.
Setup and cleanup are possible in just a few minutes thanks to the modular inner structure and the powder bed container. The material is easy to switch and maintenance is quick to perform.
Construction Volume | Ø 100 x 95 mm (Ø 3.9 x 3.7 in) (height incl. build plate) | |
Laser Type | Yb-fiber laser; 200 W | |
Precision Optics | F-theta-lens; high-speed scanner | |
Scan Speed | up to 7.![]() | |
Focus Diameter | 40 µm (0,0016 in) | |
Power Supply | 200 - 240 V | |
Power Consumption | max. 1.7 kW / average 0.60 kW | |
compressed air supply | max. 4,000 hPa, 50 l/min | |
Machine Dimensions (W x D x H) | 800 x 950 x 2,250 mm (31 x 37 x 89 in) | |
Recommended Installation Space | min. 1.00 x 3.00 x 2.5 m (3 x 10 x 8 ft) | |
Weight | 580 kg | |
Software | EOSPRINT, EOS RP Tools, Cambridge or Materialise Magics Metal Package and modules |
The EOS M 100 system is part of the portfolio of additive metal systems that we use ourselves for development. The system is characterized by ease-of-use when handling powder and exchanging powder components. It has great potential for reducing set-up times, increasing productivity and improving ergonomics and safety for machine operators.
Michael Keane | Head of Technical Process Development | Boston Scientific
EOS M 100 Building Platform with Dental Job
EOS Application Dental Crowns
EOS Dental Crowns and Bridges
EOS Dental Building Process
01
02
03
04
53_individual_production Metal Materials for the EOS M 100
EOS CobaltChrome
Cobalt-chrome is often used in aerospace and medical applications. Two of these materials are certified for dental restoration, e.g. crowns, bridges, and denture components. The chemical and mechanical properties of our alloys meet various international material standards.
EOS StainlessSteel 316L
Parts show a high level of corrosion resistance, toughness and ductility as well as a high resistance to acids.
EOS Titanium Ti64
Titanium’s material characteristics make it ideal for many high-performance applications in aerospace, automotive & medical.
Tungsten W1
The refractive materials family of powders encompasses EOS Tungsten W1, a pure tungsten alloy, which is designed and tested for use on EOS’ metal systems.
13_automation Software
EOSPRINT 2
EOSPRINT is an intuitive, open and productive CAM tool for EOS systems that enables the assignment and optimization of build parameters for your CAD data. Together with data preparation software like SIEMENS NX or Magics, it offers an extensive additive manufacturing CAM environment for a smooth 3D printing process.
3D Printing in Medicine
Example Applications and References
find out more
Direct Metal Laser Sintering (DMLS)
- 1 DMLS Technology
- 2 Advantages and disadvantages
- 3 Application
- 4 Materials
- 5 3D Printing Technologies
DMLS Technology
Direct Metal Laser Sintering (DMLS) is a metal additive manufacturing technology developed by EOS in Munich. DMLS is often confused with the similar technologies of selective laser sintering ("Selective Laser Sintering" or SLS) and selective laser melting ("Selective Laser Melting" or SLM).
The process involves using 3D STL models as blueprints to build physical models. The three-dimensional model is subject to digital processing for virtual separation into thin layers with a thickness corresponding to the thickness of the layers applied by the printing device. The finished "construction" file is used as a set of drawings during printing. As a heating element for sintering metal powder, fiber-optic lasers of relatively high power, about 200 W, are used. Some devices use more powerful lasers with faster scanning (i.e. moving the laser beam) for higher performance. Alternatively, it is possible to increase productivity by using multiple lasers.
DMLS allows you to create one-piece metal parts of complex geometric shapes
Powder material is fed into the working chamber in the quantities required to apply one layer. A special roller levels the fed material into an even layer and removes excess material from the chamber, after which the laser head sinters fresh powder particles between themselves and with the previous layer according to the contours defined by the digital model. After the completion of the layer drawing, the process is repeated: the roller feeds fresh material and the laser starts to sinter the next layer. An attractive feature of this technology is the very high print resolution - about 20 microns on average. For comparison, the typical layer thickness in hobby and consumer printers using FDM/FFF technology is on the order of 100 microns.
Another interesting feature of the process is that there is no need to build supports for overhanging structural elements. The green powder is not removed during printing, but remains in the working chamber. Thus, each subsequent layer has a supporting surface. In addition, unused material can be collected from the build chamber after printing is completed and reused. DMLS production can be considered virtually waste-free, which is important when using expensive materials such as precious metals.
The technology has practically no restrictions on the geometric complexity of construction, and the high accuracy of execution minimizes the need for mechanical processing of printed products.
Advantages and disadvantages
DMLS technology has several advantages over traditional manufacturing methods. The most obvious is the possibility of rapid production of geometrically complex parts without the need for machining (the so-called "subtractive" methods - milling, drilling, etc.). Production is practically waste-free, which distinguishes DMLS from subtractive technologies. The technology allows you to create several models at the same time with a limitation only on the size of the working chamber. Building models takes about several hours, which is incommensurably more profitable than the casting process, which can take up to several months, taking into account the full production cycle. On the other hand, parts produced by laser sintering do not have solidity, and therefore do not achieve the same strength values as cast samples or parts produced by subtractive methods.
At the moment, DMLS machines are used only in a professional environment due to the high cost.
DMLS is actively used in industry due to the possibility of building internal structures of one-piece parts, inaccessible in terms of complexity to traditional production methods. Details with complex geometry can be made as a whole, and not from component parts, which favorably affects the quality and cost of products. Since DMLS does not require special tools (such as molds) and does not generate large amounts of waste (as is the case with subtractive methods), the production of small batches with this technology is much more profitable than with traditional methods.
Application
DMLS technology is applied to the production of small and medium-sized finished products in various industries, including aerospace, dental, medical, etc. The typical size of the construction area of existing plants is 250x250x250mm, although there are no technological restrictions on size - it is only a matter of cost devices. DMLS is used for rapid prototyping, reducing the development time of new products, as well as in production, reducing the cost of small batches and simplifying the assembly of complex geometric shapes.
Photos of Super Draco rocket engine parts released by Space X founder Elon Musk
Northwest Polytechnic University of China uses DMLS systems to produce aircraft structural components. Research conducted by EADS also indicates cost and waste reductions when using DMLS technology to produce complex designs in single or small batches.
On September 5, 2013, Elon Musk posted photos of a Super Draco rocket motor part made from Inconel nickel-chromium superalloy using an EOS printer.
Materials
Almost all metals and alloys in powder form can be used as consumables. To date, stainless steel, cobalt-chromium alloys, titanium and other materials have been successfully used.
3D Printing Technologies
- Mask Stereolithography (SGC)
- Multi-Jet Simulation (MJM) Technology
- Color Inkjet (CJP)
- Digital LED Projection (DLP)
- 3D Inkjet Printing (3DP)
- Selective Laser Sintering (SLS)
- Selective laser melting (SLM)
- Stereolithography (SLA)
- Selective heat sintering (SHS)
- Lamination of objects (LOM)
- Electron Beam Melting (EBM)
- Electron Beam Fusion Manufacturing (EBFȝ)
- Fused Deposition Modeling (FDM)
Go to the main page of the Encyclopedia of 3D printing
How metal 3D printers work. Overview of SLM and DMLS technologies. additive manufacturing. 3D metal printing.

Metal 3D printing. Additive technologies.
SLM or DMLS: what's the difference?
Hello everyone, Friends! 3DTool is with you!
BLT metal 3D printer catalog
Selective laser melting ( SLM ) and direct metal laser sintering ( DMLS ) are two additive manufacturing processes that belong to the family of 3D printing , using the powder layering method. The two technologies have much in common: they both use a laser to selectively melt (or melt) metal powder particles, bonding them together and creating a pattern layer by layer. In addition, the materials used in both processes are metals in granular form.
The differences between SLM and DMLS come down to the basics of the particle bonding process: SLM uses metal powders with a single melting point and completely melts the particles, while in DMLS the powder consists of materials with variable melting points.
Specifically:
SLM produces single metal parts while DMLS produces metal alloy parts.
Both SLM and DMLS technologies are used in industry to create final engineering products. In this article, we will use the term "metal 3D printing" to summarize the 2 technologies. We will also describe the main mechanisms of the manufacturing process that are necessary for engineers to understand the advantages and disadvantages of these technologies.
There are other manufacturing processes for producing dense metal parts, such as electron beam melting (EBM) and ultrasonic additive manufacturing (UAM). Their availability and distribution is rather limited, so they will not be presented in this article.
How metal 3D printing SLM or DMLS works.
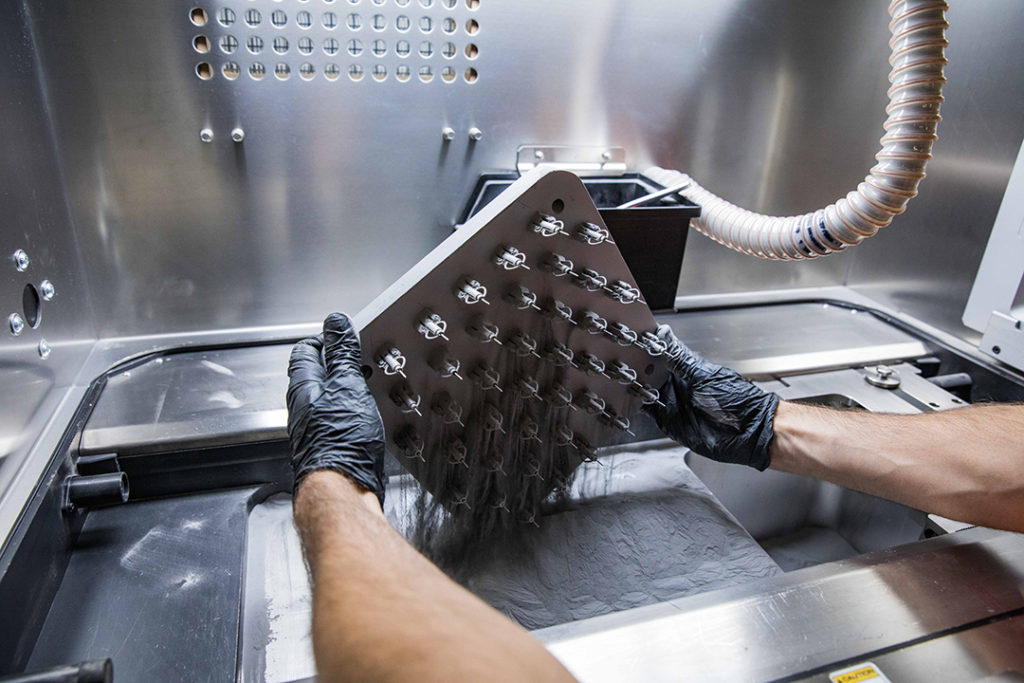
How does metal 3D printing work? The basic manufacturing process for SLM and DMLS is very similar.
1. The printing chamber is first filled with an inert gas (such as argon) to minimize the oxidation of the metal powder. It then heats up to the optimum operating temperature.
2. A layer of powder is spread over the platform, a powerful laser makes passes along a predetermined path in the program, fusing the metal particles together and creating the next layer.
3. When the sintering process is completed, the platform moves down 1 layer. Next, another thin layer of metal powder is applied. The process is repeated until the entire model is printed.
When the printing process is completed, the metal powder already has strong bonds in the structure. Unlike the SLS process, parts are attached to the platform via support structures. The support in metal 3D printing is created from the same material as the base part. This condition is necessary to reduce deformations that may occur due to high processing temperatures.
When the 3D printer's chamber cools down to room temperature, excess powder is removed manually, such as with a brush. The parts are then typically heat treated while they are still attached to the platform. This is done to relieve any residual stresses. They can then be further processed. The removal of the part from the platform occurs by means of sawing.
Scheme of operation of a 3D printer for metal.
In SLM and DMLS, almost all process parameters are set by the manufacturer. The layer height used in metal 3D printing varies from 20 to 50 microns and depends on the properties of the metal powder (fluidity, particle size distribution, shape, etc. ).
The basic size of the print area on metal 3D printers is 200 x 150 x 150 mm, but there are also larger sizes of the working area. Printing accuracy is from 50 - 100 microns. As of 2020, metal 3D printers start at $150,000. For example, our company offers 3D metal printers from BLT.
metal 3D printers can be used for small batch production, but the 3D printing capabilities of such systems are more like those of mass production on FDM or SLA machines.
The metal powder in SLM and DMLS is recyclable: typically less than 5% is consumed. After each impression, the unused powder is collected and sieved, and then topped up with fresh material to the level required for the next production.
Waste in metal printing, are supports (support structures, without which it will not be possible to achieve a successful result). With too much support on the manufactured parts, the cost of the entire production will increase accordingly.
Adhesion between coats.
3D metal printing on BLT 3D printers
SLM and DMLS metal parts have almost isotropic mechanical and thermal properties. They are hard and have very little internal porosity (less than 0.2% in 3D printed condition and virtually non-existent after processing).
Metal printed parts have higher strength and hardness and are often more flexible than traditionally made parts. However, such metal becomes “tired” faster.
3D model support structure and part orientation on the work platform.
Support structures are always required when printing with metal, due to the very high processing temperatures. They are usually built using a lattice pattern.
Supports in metal 3D printing perform 3 functions:
• They form the base for creating the first layer of the part.
• They secure the part to the platform and prevent it from deforming.
• They act as a heat sink, removing heat from the model.
Parts are often oriented at an angle. However, this will increase the amount of support required, the printing time, and ultimately the overall cost.
Deformation can also be minimized with laser sintering templates. This strategy prevents the accumulation of residual stresses in any particular direction and adds a characteristic surface texture to the part.
Since the cost of metal printing is very high, software simulations are often used to predict how a part will behave during processing. These topology optimization algorithms are otherwise used not only to increase mechanical performance and create lightweight parts, but also to minimize the need for supports and the likelihood of part distortion.
Hollow sections and lightweight structures.
An example of printing on a BLT 3D printer
Unlike polymer powder melt processes such as SLS, large hollow sections are not typically used in metal printing as the support would be very difficult to remove, if at all possible.
For internal channels larger than Ø 8 mm, it is recommended to use diamond or tear-shaped cross-sections instead of round ones, as they do not require the construction of supports. More detailed recommendations on the design of SLM and DMLS can be found in other articles on this topic.
As an alternative to hollow sections, parts can be made with sheath and cores, which in turn are machined using different laser power and pass speeds, resulting in different material properties. The use of sheath and cores is very useful when making parts with a large solid section, as it greatly reduces printing time and reduces the chance of warping.
The use of a lattice structure is a common strategy in metal 3D printing to reduce part weight. Topology optimization algorithms can also help design organic lightweight shapes.
Consumables for 3D metal printing.
SLM and DMLS technologies can produce parts from a wide range of metals and metal alloys, including aluminum, stainless steel, titanium, cobalt, chromium and inconel. These materials meet the needs of most industrial applications, from aerospace to medical applications. Precious metals such as gold, platinum, palladium and silver can also be processed, but their use is of a minor nature and is mainly limited to jewelry making.
The cost of metal powder is very high. For example, a kilogram of 316 stainless steel powder costs approximately $350-$450. For this reason, minimizing part volume and the need for supports is key to maintaining optimal manufacturing cost.
The main advantage of metal 3D printing is its compatibility with high-strength materials such as nickel or cobalt-chromium superalloys, which are very difficult to machine with traditional methods. Significant cost and time savings can be achieved by using metal 3D printing to create a near-clean shape part. Subsequently, such a part can be processed to a very high surface quality.
Metal post-processing.
Various post methods. treatments are used to improve the mechanical properties, accuracy and appearance of metal printed products.
Mandatory post-processing steps include the removal of loose powder and support structures, while heat treatment (heat annealing) is typically used to relieve residual stresses and improve the mechanical properties of the part.
CNC machining can be used for critical features (such as holes or threads). Sandblasting, plating, polishing, and micro-machining can improve the surface quality and fatigue strength of a metal printed part.
Advantages and disadvantages of metal 3D printing.
Pros:
1. Metal 3D printing can be used to produce complex custom parts, with geometries that traditional manufacturing methods cannot provide.
2. Metal 3D printed parts can be optimized to increase their performance with minimal weight.
3. Metal 3D printed parts have excellent physical properties, metal 3D printers can print a wide range of metals and alloys. Includes difficult-to-machine materials and metal superalloys.
Cons:
1. Manufacturing costs associated with metal 3D printing are high. The cost of consumables is from $ 500 per 1 kg.
2. The size of the working area in metal 3D printers is limited.
Conclusions.
• Metal 3D printing is most suitable for complex, one-piece parts that are difficult or very expensive to manufacture using traditional methods, such as CNC.
• Reducing the need to build supports, will significantly reduce the cost of printing with metal.
• 3D printed metal parts have excellent mechanical properties and can be made from a wide range of engineering materials, including superalloys.
And that's all we have! We hope the article was useful to you.
Catalog of 3D printers for metal BLT
You can purchase metal 3d printers, as well as any other 3d printers and CNC machines, by contacting us:
• By email: Sales@3dtool.