Nscrypt 3d printing
3Dn Series – nScrypt
3Dn Series
Specifications
The 3Dn Series Factory in a Tool (FiT) is a powerful and robust high-speed, high-precision motion platform for 3D manufacturing products, not just parts, in one machine with automatic tool changes, a palette of 10,000+ materials, and post-processing options. For example, this user-configurable direct digital manufacturing system can go from CAD to fully functioning finished electronic product with automatic tool changes, 3D printing the structure and housing with our nFD material extrusion tool head, conformally microdispensing and embedding conductive traces into the structure with our Smartpump™ tool head (pentip as small as 10um, printed lines as small as 20um, and dots as small as 50um (material dependent)), picking and placing electronic components with our PNP tool head, and micro-milling fine surface features with our nMill tool head. This system controls and synchronizes multiple tool heads, which we call gizmos, in series or in parallel.
User Configurable
Gantry Platform with Linear Motors
- 1 to 5 tool heads, in any combination
- 300, 500, 700, 1000, 1500 mm travel in XY
- Standard or High-Precision (10nm resolution, 500nm repeatability, 1 micron accuracy)
- 150, 200 mm travel in Z
- 3 axis standard; add a rotary stage for 4 axis; add a trunnion on the Tabletop model for 5 axis
Tabletop Model: Precision Ball Screw Motion Platform
- 1 to 4 tool heads, in any combination
- 300 x 150 mm travel in XY
- Standard or High-Precision (10nm resolution, 500nm repeatability, 1 micron accuracy)
- 100 mm travel in Z
Single, Dual, Quad, and Penta-Head
- Microdispensing
- 3D Printing (Material Extrusion, aka FDM or FFF)
- Micro-Milling, Drilling, and Polishing
- Pick and Place
Options
- Laser Processing, Sintering, Heating, UV and Photonic Curing
- nVision and nVision Pro Real-Time Process View
- Mapping and Machine Vision
- Z Tracking and Conformal Printing
- 3D Mapping Pre and Post Print
- Automatic Calibration Pit
- Rotary Stage
- HEPA Filtration
- Heated Bed and Vacuum Chuck
- Customer Laser Integration
- Plasma Pen
Brochure Downloads
nScrypt granted patent for 3D printed electronic personalized therapy devices
0Shares
What are the 3D printing trends to watch in 2022? Read insights and analysis from over 40 additive manufacturing experts.
Florida-based microdispensing specialist nScrypt’s research arm, Sciperio, has been granted a US patent for a personalized electronic therapeutic training device of which some or all of the device, circuitry, and sensors are 3D printed.
The wording of the US patent (no. 10,926,1136) is “Health Monitoring with 3D Printed Sensors”, and covers not only the device itself, but also how it communicates data in real-time to a video game for therapeutic training, as well as the device’s method of performing personalized therapy and tracking training data.
The device in question could take the form of a personalized oro-motor device, brace, wrap, bandage, or skin applique, with medication or motion inducers able to be 3D printed onto the device and dispensed to the patient.
“This patent is an example of the great things 3D manufacturing can do; making complete, mechanically and electrically functioning wireless devices, with minimal labor, that never existed before and that couldn’t exist before because of the limits of traditional manufacturing,” said Dr. Ken Church, CEO of nScrypt and Sciperio.
The nScrypt tool changer. Photo via nScrypt.“We can now make devices that are highly customized in what they can do and highly personalized to the patient, for highly individualized observation, feedback, training, therapy, or rehabilitation.”
Factory in a Tool electronics 3D printing
nScrypt has continued to build a reputation for itself in the microdispensing space with its Factory in a Tool (FiT) 3D printers, which are designed to provide an all-in-one manufacturing engine with 3D printing, milling, polishing, pick-and-place, and post-processing capabilities.
The firm’s portfolio includes its 3Dn Series, 3Dn-DDM Series, and nRugged systems, which are all compatible with nScrypt’s entire tool head suite, including its SmartPump. This functionality makes its systems well suited for production applications within electronics, defense, aerospace, energy, and bioprinting.
Last year, nScrypt continued to build on the capabilities of its microdispensing technology through achieving 6-axis 3D printing with its 3Dn-Axis FiT 3D printer. This functionality provides nScrypt’s users with a new level of geometric control when designing parts. Shortly afterward, the firm released its new 3D printing machine control software, nStudio, which offered improved user-friendliness alongside several advanced features, and in September, announced a new ability to 3D print multi-axis electronics onto curved and irregular surfaces.
nScrypt’s new patent
The electronic therapeutic training device covered by nScrypt’s new US patent can be highly personalized to fit an individual patient in terms of size, shape, and sensor shape and positioning. This is achieved by 3D printing some or all of the device, its circuitry, and its sensors according to a 3D model of a patient.
Potential devices covered by the patent include customized oro-motor devices, which primarily aid speech, chewing, and biting, as well as braces, wraps, bandages, and skin appliques such as medicine-dispensing patches.
The patent also covers the device’s method of performing therapy through measuring the patient, allowing for the device to be customized to the patient by means of additive manufacturing, and by using data from the device in a video game scenario for therapy training.
Data can also be obtained and sent from a database of patient data to determine whether training thresholds are met, and to send alerts when they are. Additionally, the device’s data can be analyzed by comparing data from different patients using a data mining process.
“By making devices that exactly fit the specific area of a patient’s body where therapy is needed, such as inside the mouth, therapists and trainers can use very specific strategic sensing for training and therapy,” said Church.
The patent, which features four independent claims and 16 dependent claims, further covers a method of tracking and comparing therapeutic training for chewing, bending, or twisting by leveraging data from a personalized 3D printed oro-motor mouthpiece. The mouthpiece contains an intelligent sensor system and data-mined oro-motor data, physical therapy data, or real-time medication release data.
nScrypt’s new patent is available for licensing under “mutually favorable” terms, Church explains: “We want to see printed electronics and 3D manufacturing move forward as an industry, with innovation lifting all boats, without patents getting in the way.”
nScrypt’s nRugged 3D printer. Photo via nScrypt.The rise of 3D printed electronics
While still in its early stages, the field of 3D printed electronics field has given way to numerous innovative developments in recent months. In line with this progress, the likes of nScrypt and several others are seeking to establish themselves as leaders in the space.
Electronics 3D printer manufacturer Nano Dimension is one of them, having recently made significant progress with the unveiling of its DragonFly IV system and FLIGHT software platform, after partnering with Fraunhofer IPA to advance freeform printing capabilities. Most recently, the firm acquired Global Inkjet Systems in a deal worth up to £28.8 million with intentions to upgrade its product line.
Elsewhere, the likes of industrial 3D printer manufacturer Optomec has received a $2 million order from a leading electronic systems manufacturer in the aerospace and defense sectors for six of its Aerosol Jet 3D Electronics printers. The company recently developed the capabilities of its Aerosol Jet Printing (AJP) technology through patenting a UV illumination technology, enabling the more precise production of 3D microstructures.
Another player in the 3D printed electronics space is Neotech AMT, which is currently further developing its “fully additive” electronic devices and working on a scalable 3D printing process for 4D mechatronic systems.
Subscribe to the 3D Printing Industry newsletter for the latest news in additive manufacturing. You can also stay connected by following us on Twitter and liking us on Facebook.
Looking for a career in additive manufacturing? Visit 3D Printing Jobs for a selection of roles in the industry.
Subscribe to our YouTube channel for the latest 3D printing video shorts, reviews and webinar replays.
Featured image shows nScrypt’s nRugged 3D printer. Photo via nScrypt.
Tags 3Dn Series 3Dn-Axis 3Dn-DDM series Fraunhofer IPA Global Inkjet Systems Ken Church Nano Dimension Neotech AMT nRugged nScrypt nStudio optomec Sciperio
Hayley Everett
Hayley is a Technology Journalist for 3DPI and has a background in B2B publications spanning manufacturing, tools and cycling. Writing news and features, she holds a keen interest in emerging technologies which are impacting the world we live in.
NovaCentrix and nScrypt receive a grant to develop electronics 3D printing
News
Existing 3D printers are limited in material selection to a few plastics or metal powders.
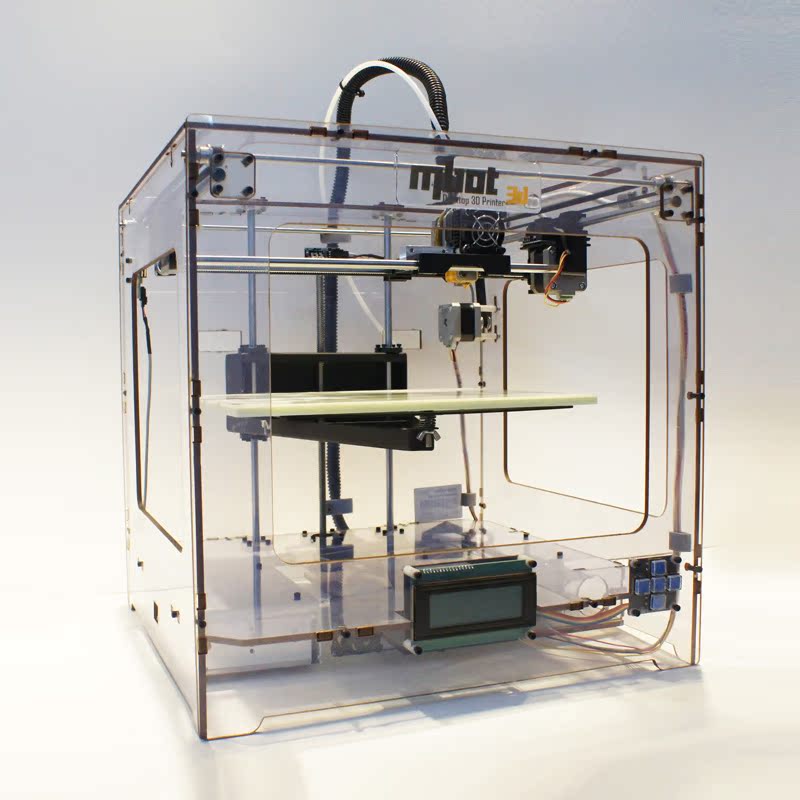
The new system should be able to build hybrid circuits on embossed surfaces as well as devices on flexible and rigid substrates. The equipment must be able to combine several existing instruments within the same system. The device will be equipped with five working nozzles, including a manipulator, three micro-dispensers and one print head. Additionally, the system will be equipped with lighting equipment. Apparently, it means printing with hybrid photopolymer resins. The finished system will be able to print, switch consumables and expose finished parts at speeds that are not possible with today's machines.
NovaCentrix, based in Austin, Texas, is a leader in printed electronic devices. The most sophisticated PulseForge system is able to print circuits on flexible substrates like paper or plastic by sintering and then final lighting.
nScrypt is a company specializing in the development of micro-dispensers for use in electronics manufacturing, biomedicine and even organic tissue 3D printing.
"The collaboration between nScrypt and NovaCentrix on this project is the best way to complete the project successfully," said Michael Sjesinski, president and CEO of the FlexTech Alliance. "nScrypt has already created some of the most advanced 3D printing tools, while NovaCentrix is constantly adding the devices needed to revolutionize electronic circuit printing."
Kenneth Church, CEO of nScrypt, said: “We are well aware that 3D printing has the potential to revolutionize the industry. Although such technologies are initially expensive and complex, the ability to increase manufacturing flexibility and reduce costs will facilitate widespread adoption. Funding from FlexTech will enable nScrypt, a 3D printing technology company with over 15 years of experience, and NovaCentrix to combine expertise and demonstrate the potential of digital 3D printing to change the rules of industrial manufacturing.”
“The new integrated module will be the next step in the inevitable introduction of 3D printing into electronics manufacturing. The range of consumables will expand significantly, and the creation of electronic components will be possible in previously unseen forms,” added Stan Farnsworth, vice president of marketing at NovaCentrix.
The system will be the first commercially available version of an additive manufacturing facility capable of creating functional, one-piece 3D electronic devices, and will enable engineers and designers to print electronic components including antennas, sensors and cell phone circuit boards.
Incidentally, FlexTech is partnering with US Army research labs interested in rapid prototyping of new electronic components. Although the planned setup is quite modest, building arrays from it should not be too difficult.
Video showing the prototype arm in action:
0043
7
Subscribe to the author
Subscribe
Don't want
The F2 Gigantry system will allow manufacturing companies, in particular aerospace companies, to...
Read more
four
Follow author
Follow
Don't want
0003
Read more
59
Subscribe to the author
Subscribe
On October 2, another 3D printer will go to the International Space Station, this time the first space-based stereolithographic additive system developed by Made in Space. The equipment will be used in experiments on 3D printing of turbine blisk blanks from ceramic matrix composite materials.
Until now, the use of additive manufacturing in space has been limited to FDM 3D printers and bioprinters for living cell 3D printing experiments. Currently, the International Space Station is equipped with the second-generation FDM system Additive Manufacturing Facility, Refabricator and Braskem Recycler plastic waste recycling devices, as well as two bioprinters - the BioFabrication Facility system developed by the American companies Techshot and nScrypt and the Organ.Avt magnetic bioprinter authored by Russian laboratory 3D Bioprinting Solutions. The new system, called the Ceramic Manufacturing Module (CMM), relies on laser stereolithography technology - 3D printing with liquid photopolymer resins cured by a laser emitter.
The experiment has a specific goal: the developers intend to test the additive production of ceramic products using the example of turbine blisks - monolithic wheels with blades. Photopolymer resins with the addition of ceramic precursors will be used as consumables. As Made in Space explains, in the case of parts for turbines, nuclear power plants or internal combustion engines, even a one or two percent increase in strength characteristics can provide an increase in service life, measured in years, if not decades. In addition, ceramic matrix composites can operate at temperatures hundreds of degrees higher than the most advanced heat-resistant superalloys.
Researchers are interested in how positive the effect of microgravity will be: 3D printing with similar materials on Earth is complicated by the gradual precipitation of the filler, while in zero gravity it will be possible to achieve a more uniform distribution of the filler. Annealing and sintering of blanks into finished products will be carried out already on Earth.
California-based companies HRL Laboratories and Sierra Turbines are participating in the research program with the assistance of NASA's Lyndon Johnson Space Center. The manufacturer of stereolithographic 3D printers B9 helped with the development of additive equipment and testing of the system in artificial microgravity during flights along a parabolic trajectory.Creations.
As Sierra Turbines CEO Roger Smith explains, his company is considering two possible applications for the new technology. The first is the production of parts for spacecraft with increased resistance to high-energy particles and atomic oxygen. The second is the manufacture of parts for use on Earth, such as high-temperature turbine blades.
Monolithic turbine blisks offer significant advantages over existing prefabricated structures used in aircraft engines. Products made from ceramic matrix composites are typically 30-50% lighter than their counterparts made from high-temperature alloys and are able to withstand operating temperatures in excess of 1100°C, which can help improve fuel economy and overall aircraft engine efficiency. Successful experiments in the production of blanks of ceramic-matrix parts under zero gravity conditions can help realize additional bonuses in the form of a reduction in mass and residual stresses, as well as an increase in the mechanical fatigue threshold.