Local motors 3d print
3D Printed Car Company Local Motors Shuts Down - 3DPrint.com
Multiple automotive and tech news sites have reported that Local Motors (LM), the manufacturer of the Olli 3D printed shuttle, has ceased operations. The main source of information comes from LinkedIn posts from former employees. The news comes after the vehicle firm made numerous pivots over the past decade, finally landing on autonomous shuttles made with 3D printing.
Prior to embracing additive manufacturing (AM), the company began with an interesting concept: crowd sourced vehicle designs. Once you purchased one, you were actually able to go to the LM site in Arizona and build it yourself with the LM team. Crowdsourcing then led to 3D printing, as the company sourced ideas for what would become its first 3D printed car.
The Rally Fighter featured a unique crowdsourced design with aftermarket parts and occasional 3D-printed upgrades. Image courtesy of Local Motors.
With Oak Ridge National Laboratory and Cincinnati Incorporated, LM participated in the development of a large-scale polymer 3D printer called the Big Area Additive Manufacturing (BAAM) system. The BAAM is able to deposit carbon fiber reinforced plastic at amazing rates within a massive envelope, a concept that spurred other machine manufacturers like Thermwood and Ingersoll to create their own versions of the technology.
It also led to the creation of the Strati, a car with a chassis that was entirely 3D printed. Though it could only move at the speed of a golf cart, it generated enough hype that LM decided to pursue “the first road-ready, 3D printed car”. Another crowdsourced design, the resulting LM3D never actually did become road ready, despite LM providing a sticker price of $53,000 and accepting pre-orders.
The 3D printed Strati car. Image courtesy of Danielle Matich/Volim Photo.
Meanwhile, LM had pivoted from the Rally Fighter to 3D printed cars to crowdsourced projects for corporations via a social media platform called Launch Forth. Using the same model that had created its previous vehicles, LM partnered with firms like HP and the U.S. Marine Corps to ask the public for input on Martian habitats and all-terrain vehicles. It was with the launch of this program that it became apparent that LM was searching for the proper business model and hoping that corporate sponsors might help keep the company going.
This project faded away, too, much like the Rally Fighter and the LM3D. When asked what happened to the LM3D product line, former LM CEO Jay Rogers explained that he had reconsidered his vision for mobility around the world. It wasn’t personal vehicles, but smart, connected, and electric public transit. To take part in this emerging trend, LM shifted entirely to an autonomous shuttle called Olli. Uniquely, 80 percent of Olli’s body was 3D printed using BAAM machines. Rogers told me at the time:
“We launched a challenge to design a highway-capable vehicle that Local Motors then created a proof of concept of and debuted at the SEMA show in 2015. Our R&D team is continuing the materials testing and validation through 3D printing, now on the world’s largest composite 3D printer, located in our Knoxville microfactory.
The highway car is not a current product offering, but that’s not to say it won’t be in the future! We are currently focused on Olli, our low-speed, self-driving, EV shuttle, as we see an immediate and future need for alleviating congestion and pollution, while providing a more accessible, sustainable transportation solution for all.”
Given the ingenuity of each product developed by LM, one wouldn’t be faulted for believing in each pivot. The vision was there, as was the technology, to an extent. However, even as it focused on Olli alone, there were issues. For one, the much-touted IBM Watson platform that initially powered the shuttle’s artificial intelligence (AI) was replaced in 2019 with AI from another provider.
Olli 2.0, the mostly 3D printed, autonomous electric shuttle. Image courtesy of Local Motors.
More importantly, as a Toronto test program for the vehicle began at the end of 2021, Olli crashed into a tree, critically injuring its human attendant. According to The Drive, the closure of the business was not related to the crash, though the trial run was paused due to the accident and COVID-19 health guidance. With Olli moving at such slow speeds, one would think that LM had found a sweet spot for autonomy, but the world may just not be quite ready for transport that drives on its own.
Autonomous bus has crashed into a tree in Whitby!
How is a driverless bus safe for public use??#Toronto #TOpoli #Scarborough #ScarbTO #Metrolinx #TTC #Whitby #DRT #DurhamTransit #AutonomousBusCrash #PublicSafety pic.twitter.com/aA80PEY5Wu
— Brian Connolly (@bconnolly00) December 17, 2021
From the potential dangers of autonomous vehicles to a shaky business model, it seems that Local Motors couldn’t exactly find its footing during an economically unstable period of time. That doesn’t mean that it won’t re-open operations or that its former CEO, who moved to an advisory role last year, won’t re-emerge with a unique, new business idea. After all, Divergent’s Kevin Czinger was unable to launch an electric vehicle company his first go-around and is now on the verge of announcing a new partnership related to 3D printed cars.
Stay up-to-date on all the latest news from the 3D printing industry and receive information and offers from third party vendors.
Tagged with: 3D printed cars • 3D printed shuttle • 3d printed vehicles • autonomous vehicles • electric vehicles • local motors • Olli • Olli 2.0
Please enable JavaScript to view the comments powered by Disqus.
Vehicle from Local Motors is 80% 3D-printed
In an interview with the website
Ride, the president of Local Motors talks about the company’s autonomous vehicle- January 17, 2020
- Article
- Additive Manufacturing
- Join Discussion
Local Motors President Vikrant Aggarwal says the Olli shuttle represents the evolution of the company’s 3D-printed vehicle technology. Image provided by Local Motors
Following is an excerpt from an interview with the president of Local Motors, Vikrant Aggarwal, about one of the company’s 3D-printed vehicles. The interview was posted to Ride, a website powered by Kelley Blue Book that’s devoted to transportation technology.
As a leading pioneer in the space of 3D-printed, autonomous vehicles, Local Motors is poised to help transform the business model for electric vehicles while helping to drive the wider adoption of the technology. Since its inception, Local Motors has debuted three “firsts”: the world’s first co-created vehicle; the world’s first 3D-printed car; and Olli, the world’s first co-created, self-driving electric vehicle.
During a recent Q&A with Ride, Vikrant Aggarwal discussed some of the benefits of its 3D-printed Olli.
Ride: How does Local Motors’ 3D printing technology help to address some of the challenges associated with electric vehicle production?
Aggarwal: I would use the word opportunity. I think the opportunity is more different whether you’re 3D printing an electric vehicle or a nonelectric vehicle. It’s much more economically energy efficient. It’s (also) easier to make changes to the product.
Ride: The Olli started as a vehicle which was about 30% 3D-printed. The vehicle is now 80% 3D-printed. What has Local Motors learned during that evolution?
Aggarwal: The key thing is that process control is extremely important, because you are dealing with a huge printer. So, how you control the parameters, how you manage them, (and) how you do quality control is extremely important, from an operations standpoint.
If you look at traditional automotive models, it’s a five- to seven-year process to go from one model to the other, and hundreds of millions of dollars of investments. But from a 3D printing perspective, we went from the older version of Olli to the newer version in one year.
Ride: Clearly, safety remains a primary concern when discussing any kind of autonomous vehicle technology. As a company centered around 3D-printed vehicles in the autonomous space, how is Local Motors working to ease those concerns?
Aggarwal: We’ve completed hundreds of thousands of rides across the globe. Once you sit in those shuttles, ride them, the experience you get speaks for itself. The second is you rely on test data … that shows how it is safe. The third is you go through technical discussions with people to give them a sense of the safety of the shuttles. You can demonstrate that it is a safe and reliable product.
Local Motors operates two microfactories—one in Knoxville, Tenn., and the other in Chandler, Ariz. Image provided by Local Motors
Ride: Are there any limitations to 3D-printed electric vehicles, when compared to other 3D vehicles? If so, what are they? And what is Local Motors doing to be able to push the technology beyond those limitations?
Aggarwal: I think one of the biggest is the evolution of the technology, how it develops and how it can be deployed in a much broader network. Let’s say that someone wants to make a 50-passenger shuttle; how would we use 3D printing? I don’t think they are limitations. I think they are learning, learning the technology as it evolves and learning how you deploy that technology in different sizes and segments of the applications.
As an example, I suspect that three years ago, if someone said, “We’re going to 3D-print a shuttle like Olli,” which carries eight people, some people would have said, “No way.” That’s the progressive attitude we’ve taken.
The entire interview can be found at the Ride website.
REC Wiki » Who makes money on 3D printing and how
Are you ready to make money with direct hands and a 3D printer? Okay, but before diving head first into the business, it would be nice to understand exactly how 3D printing is changing the face of the industries around us in order to find its niche. Let's watch.
The market is growing
From Bugatti to Adidas, 3D printing is making its way into one industry after another, influencing not only design processes but also manufacturing processes. Even the pandemic did not stop the development of the additive market. The situation turned out to be twofold: on the one hand, many manufacturers of 3D printers and consumables suffered losses due to reduced demand, but already bounced back in 2021, as more and more enterprises began to resort to localized additive manufacturing of components due to problems with global logistics . It's time to join the trend and row money with a shovel. A shovel, by the way, can also be printed. nine0003
The main applications of 3D printing technologies are prototyping and additive manufacturing. As a prototyping tool, 3D printing helps speed up the development and refinement of products, and as an additive manufacturing tool, it allows you to make final products. Prototyping with 3D printing greatly accelerates the work of designers, providing low-cost, functional prototypes for enterprises of all sizes. In manufacturing, 3D printing is used for mass customization, on-demand production, and even distributed production. nine0003
3D printing is everywhere you look
As the subtitle suggests, there is no hiding from 3D printing, it is already everywhere. On the other hand, adoption rates vary from industry to industry. 65% of the use of additive technologies is in engineers working on the creation of new industrial and consumer products.
Example: Three-quarters of American and German automotive companies, including BMW, Ford, Volkswagen, Audi, Porsche, Mercedez-Benz and General Motors, are already actively using 3D printing technology in the mass production of tooling, parts and spare parts. But the matter is not limited to cars alone: medicine, the service industry, architects, artists, and so on and so forth have picked up an additive fever. And what do they do, you ask? Now let's show. nine0003
Construction
3D printing is a new word in construction. "Office of the Future" is a demonstration project in Dubai carried out by the Chinese company WinSun in 2016. Six meters high, thirty-six long, twelve meters wide, plus 50% savings on labor. For everything about everything, including decoration and landscaping - seventeen days. The emirs have big plans: the same Saudi Arabia intends to build one and a half million houses to solve the housing crisis, actively attracting developers of construction 3D printers. It is understandable, because the salaries of local builders are high, and the economy should be economical. nine0003
The Dubai 3D printing office was just one of the first wake-up calls, and now, six years later, construction 3D printing is being mainstreamed by companies such as ICON, Apis Cor, COBOD, AMT-Spetsavia. The illustration above shows a series of low-income homes built by Texas-based ICON in their native Austin. The houses are small, only thirty-seven square meters each, but are equipped with a bedroom, a living room, a fully equipped kitchen and a bathroom.
And this is one of the projects of the Russian company 3D4art: a pavilion with a 3D printed concrete cat was erected on a private plot in Yaroslavl and serves as a summer kitchen. 3D4art uses 3D printers developed by the local company AMT-Spetsavia, which is also engaged in construction, in parallel with the production of additive technology. Now AMT-Spetsavia is busy building a whole 3D-printed village, in total it is planned to build twelve houses according to individual projects. nine0003
“From a hardware point of view, a construction 3D printer is not much different from conventional 3D printing with molten plastic. These are the same CNC machines, only construction 3D printers are larger. However, they allow realizing any architect's fantasy: the printer doesn't care what to print - a simple rectangular building or a house with curved facades, turrets and columns. And to automate the process as much as possible, thanks to which the time for construction is reduced by one and a half times compared to the traditional one,” said Alexander Maslov, General Director of AMT-Spetsavia. nine0003
Tissue engineering and organs
No one has yet learned how to print working livers, but the process is underway. For example, Prellis Biologics is working on methods for 3D printing of functional organs, including hearts, livers, kidneys and lungs, and the Russian company 3D Bioprinting Solutions has already conducted several bioprinting experiments in space.
Even if the technology is not yet ready for 3D printing of organs for transplantation, it is already useful, allowing the growth of living tissue samples for toxicological research in the development of new pharmaceuticals, as well as research in the treatment of various dangerous diseases, such as cancer. nine0003
Cars and motorcycles
Finding and buying a four-wheeled classic is not that difficult, if you have the money. It is more difficult to bring the often rusty collection of no longer produced parts up to standard. Mercedes has found a simple solution by offering owners of older cars, including the legendary 300 SL coupe, 3D printed parts. Ride for health.
The Russian studio Box3D went in a slightly different direction, customizing cars and motorcycles. In some cases, the company immediately prints parts on 3D printers using durable composites, such as REC X-Line filaments, in others, it prints master models from PETG, from which matrices are removed, and carbon or fiberglass parts are made from matrices. The illustration above is one example. This is a custom motorcycle Giotto 31 based on Harley-Davidson V-Rod. All plastic parts are printed in PETG with fiberglass reinforcement. nine0003
And this is a very extreme example from the USA - the Czinger C21 hypercar with a structure made of carbon fiber and 3D-printed titanium parts made using selective laser metal powder fusion (SLM) technology. The machine is equipped with a hybrid power plant based on a turbocharged V-engine with a capacity of 925 hp. With. with the main drive to the rear wheels and auxiliary to the front. From zero to one hundred kilometers per hour Czinger C21 accelerates in just 1.9 seconds. Last year, the prototype set a new lap record at Laguna Seca and improved the previous best time set by the McLaren Senna by a full two seconds. The company plans to produce just eighty of these cars, costing about $1.7 million each. nine0003
Shoes and fashion in general
Sooner or later the day will come when you will put on freshly printed underpants in the morning. Think this is a joke? Perhaps. However, the same Adidas brand is already actively pursuing the idea of mass distributed additive manufacturing of shoes. Each has its own size, its own shape, its own color, and even at the place of residence. The company has already released several sneaker models with comfortable and resilient 3D printed soles made on Carbon's high-speed photopolymer 3D printers. nine0003
Bicycles
This is the Arc Bicycle, a 3D printed bicycle designed by Delft University of Technology students and manufactured by MX3D. And the uncle on a bicycle is the Minister of Economy of the Kingdom of the Netherlands Henk Kamp, who tested the novelty at the Innovation Expo in Amsterdam. It's a well-known fact: the Dutch love 3D printers and bicycles. Especially when 3D printers are printing bicycles, for the perfect synergy. The frame of this two-wheeled vehicle was printed by an industrial multi-axis robotic arm that fuses metal wire. nine0003
And this e-bike has a carbon fiber composite frame, but also 3D printed. Such bikes are produced under the Kimoa brand, founded by the famous racing driver Fernando Alonso. The production is carried out by the Californian company Arevo, which has developed a special 3D printer: an additive system prints a combination of thermoplastics and continuous reinforcing fibers.
Instead of a thermal block, a laser emitter is responsible for melting the polymer, and immediately after application, the melt and the reinforcing thread are pressed by a roller, increasing the isotropy. Thanks to the multi-axis positioning system, the reinforcing threads can be overlapped, and the high power-to-weight ratio of the system makes it possible to work even with refractory structural thermoplastics such as polyetheretherketone (PEEK). nine0003
Food
Who wants a delicious cake? Only cakes are not simple, but made according to intricate 3D printed forms. These sweets were invented by a former Ukrainian architect, and now a confectioner Dinara Kasko. The unusual shape of the cake was obtained using a silicone mold made from a 3D printed master model. With 3D modeling in Grasshopper 3D, Dinara was helped by a friend, Ukrainian artist Andrey Pavlov, who is engaged in general and architectural design.
Fashion
Let's get back to our clothes. Dutch designer Anouk Wipprecht knows the safest way to ride the subway. This 3D-printed "spider" outfit not only flatters the figure, but can tear apart anyone who will unravel their hands. We have warned you. But there are other options: go to the store in such a dress, elegantly lean on the counter and ask: “How much?” Discount guaranteed. nine0003
And now to space
When someone enthusiastically mentions "space technology", they mean 3D printing. Seriously. We have already mentioned 3D Bioprinting Solutions, but NASA has long appreciated the possibilities of 3D printing, operating the second FDM 3D printer on board the ISS and even funding the development of 3D printers for printing in outer space. The Russian "space" polymer 3D printer (pictured above) is due to leave for the ISS on June 3, 2022.
SpaceX's rockets and spacecraft are powered by 3D printed engines, and California-based startup Relativity Space is already gearing up to launch the first 3D printed orbital launch vehicle.
Relativity Space relies on at least two 3D printing technologies: for example, engines are manufactured using selective laser sintering technology using industrial 3D printers from the German company Electro Optical Systems (EOS GmbH), and fuel tanks are printed by an additive system of our own design - a robotic complex Stargate on hybrid technology of laser-plasma deposition of welding wire. Through the use of robotic manipulators, the system is easily scaled up, allowing you to create large-sized products. nine0003
The first flight of an experimental Terran 1 rocket with a payload mock-up is scheduled for June 2022. The company estimates the cost of one launch at twelve million dollars, and the production time for serial samples is only two months.
Architecture
And I'm walking, walking on… a 3D printed bridge. Not so unexpected: 3D printed bridges have been built in Spain, the Netherlands and China. These are all reinforced concrete structures, although there are also plastic ones, but the engineers of the already mentioned Dutch company MXD3 designed an all-metal steel bridge. nine0003
The bridge was installed in the center of Amsterdam in the summer of 2021. The opening ceremony turned out to be quite funny: Her Majesty Queen Maxima deigned to press the big green button, thereby graciously giving the red ribbon to be torn to pieces by a robot-manipulator armed with scissors. Why such an honor fell to the robot is quite understandable: the robots did the bulk of the physical work, armed with welding machines.
This 3D printing technology is called Wire Arc Additive Manufacturing (WAAM for short) and uses conventional welding wires, in this case steel. nine0003
Food again
Dutch engineers from byFlow are ready to print delicious treats in any shape, as long as the starting material is in paste form. These guys even managed to feed the Australians with 3D printed meat rolls.
There are many options, it would be a fantasy. There is a demand, but the main problem is that potential customers often do not know that they need the services of printers, not understanding the possibilities of additive technologies. And then it's up to you - show, tell, earn. Just don't print bitcoins. Seriously, it won't work. nine0003
over 10 projects to look out for in 2021
Exploring space has never been so exciting! Check out these examples of 3D printing in space, from rockets to moon bases.
What was once thought impossible in space could become a reality with 3D printing (Source: NASA)
for space exploration ever since humans first set foot on the moon. nine0003
Our projections for the 2020s are promising: space tourism will become a reality, the first woman will reach the moon, a permanent lunar base will be built, exploration of our solar system will boom, the first human mission will reach Mars, and commercial production in space will begin. Technology will move beyond today's limitations and we will see additive manufacturing, including 3D printing, rapidly evolve to meet growing needs. nine0003
The launch systems (rockets), thrusters and satellites we send into space are increasingly being built using 3D printing, resulting in some of the largest and most complex 3D printed manufacturing facilities in the world.
Once in space, 3D printing plays several key roles: the zero-g environment in space orbit opens the door to printing materials that are impossible under the influence of Earth's gravity, parts and spare parts can be printed on demand, and structures can be built without withstanding the stress of starting up. nine0003
Farther away, on the surface of the Moon and Mars, structures must be built using local materials, and large-scale 3D printing is also a key part of this solution.
We'll take a closer look at each of these areas and select representative projects, highlighting the key role of 3D printing and highlighting what we need to focus on in 2021 and beyond.
CATEGORY: SPACE JOURNEY
Relativity Space builds the world's first 3D printed rocket (Source: Relativity Space) more account.
3D printing is revolutionizing launch vehicle design by reducing the number of components, integrating complex geometries into lightweight structures, and speeding up the entire design and manufacturing cycle. All this is vital in the relentless quest to reduce the cost per kilogram sent into space. nine0003
NASA, the European Space Agency (ESA) and the space agencies of Russia, China and India are actively exploring and already using 3D printing to achieve their research, scientific, security and commercial purposes. There is a particular focus on rocket engines, and 3D printed parts are already playing a key role in virtually every new satellite launch. Both SpaceX and Boeing, for example, have literally hundreds of 3D printed components in their new manned capsules. nine0003
3D printing has also enabled dozens of private start-up firms to quickly implement new solutions, from entire launch systems to tools and equipment used by astronauts.
Consider four representative projects covering the range of solutions mentioned above.
1. SPACE 3D PRINT
Terran Rocket and Stargate
Stargate is the world's largest 3D printing facility (Source: Relativity Space)
Relativity Space leads the development of what they call the software factory of the future. They combine additive manufacturing, artificial intelligence and autonomous robotics to create the Terran, the world's first 3D printed rocket, with Aeon engines, which are also primarily 3D printed.
Stargate's manufacturing facility houses the world's largest metal 3D printers and uses DED (Directed Energy) technology and proprietary alloys to make rocket bodies. 3D printing allows the rapid development of integrated components that reduce the number of parts by 100 times compared to traditional launch vehicles. It also reduces weight and improves reliability, which is critical to the economics of space launches. nine0003
Technology developed by Relativity can be transferred to other industries. The way they combine 3D printing with automated assembly and intelligent design is likely to have a huge impact on the aerospace industry and beyond.
- Company: Relativity Space
- Notable technologies: The world's largest metal 3D printers and smart factories.
- Follow: Launch of Terran, the world's first 3D printed orbital launch vehicle, in 2021. nine0170
2. SPACE 3D PRINT
Missile Laboratory: Rutherford and Hypercurie
revolutionary 3D-printing engine Rutherford (source: Rocket Lab) 9000 9000
Rocket Lab- leader in the field of commercial sheets of satellites. Its founder, Peter Beck, called 3D printing “a revolutionary technology in space propulsion,” and he can attest to this with impressive results. nine0003
The Rutherford rocket engine was first tested in late 2016 and since then over 200 game-changing models have been produced. Their combustion chambers, injectors, pumps and main fuel valves are 3D printed using electron beam melting. The result is a simple, reliable and lightweight engine (only 35 kg or 77 pounds), making it ideal for low-cost space launches. The new Curie and HyperCurie engines used outside the Earth's atmosphere are built using the same principles. These engines have already powered more than 20 launches. In 2021, they will be organizing the first private lunar mission to place the experimental CubeSat navigation satellite into lunar orbit for NASA, a clear sign of the technology's maturity. nine0003
- Company: Rocket Lab
- Notable Technology: 3D Printed Cathode Beam Motors
- Keep a close eye on: the first private mission to the Moon in 2021 and a private mission to explore Venus in 2023, all using 3D printed engines.
3D PRINT IN SPACE
NASA: RAMPT
9 909003
5 Hot test of a 3D printed nozzle (Source: NASA)
NASA's own 3D printing efforts are slightly behind in terms of technology, but are being implemented on a much larger scale. Their Rapid Analysis and Manufacturing Propulsion Technology (RAMPT) project advances the development of additive manufacturing technologies for 3D printing huge rocket combustion chambers, thrust chambers and nozzles. They may seem simple, but they are actually very complex and traditionally take a long time to make - often over a year. nine0003
For example, the injectors of an engine are connected by tubes through which the fuel passes to preheat before combustion. 3D printing allows them to be manufactured as a single component with all channels built in, which can significantly reduce production time, reduce costs and lighten parts.
Technologies under investigation include large-scale 3D printing using direct energy and powder (blown-powder directed-energy deposition) and new printable copper-based alloys. nine0003
Progress has been rapid and we can look forward to incorporating the development into the Artemis project that will take NASA back to the Moon, to infinity and beyond!
- Company: NASA
- Notable Technology: Direct Energy and Powder Large Scale Printing
- Watch out for: 2021 production use announcements
4. SPACE 3D PRINT
SpaceX: Starman Helmet
SpaceX helmets are printed on 3D printer (source: Obri Dzheminani via NASA)
SPECIDARY ASTRONASS IS ASTRONAUS INSTRICATION DAY DAY DAY DAY DAY DAY DAY DAY Attention.
They were designed by Hollywood costume designer José Fernandez, who worked on Captain America and Batman v Superman, but they serve a much more important role than just looking cool! They protect the crew from fire or depressurization, regulate temperature and oxygen levels, and are individually designed for comfort. nine0003
SpaceX has kept details of many of the core technologies under wraps, but a spokesperson noted that "the helmet is custom-made using 3D printing technology and includes built-in flaps, visor retract and lock mechanisms, and microphones within the helmet structure." The material is assumed to be PEKK, a variant of PEEK that provides high temperature and chemical resistance, as well as the ability to withstand high mechanical loads. nine0003
Hopefully SpaceX will share more production information next year. In the meantime, you can print your own copy at home.
- Company: SpaceX
- Known Technology: PEKK 3D Printing - TBD
- Stay tuned: Detailed information about this and other sets of astronauts will be released in 2021
CATEGORY: SPACE 3D PRINTING
Refabricator recycles plastic materials and 3D prints using filament (Source: Emmett provided via NASA)
3D printing in space brings its own challenges and opportunities. Technologies that work in an environment with gravity may not work in zero gravity. On the other hand, the absence of gravity allows us to find new solutions that may not work on the surface of our planet.
Several 3D printing techniques and materials have been experimented with on the International Space Station (ISS) for more than five years. The results have been very positive, so new cutting-edge projects are underway to expand materials, capabilities and scope. There are three main streams in the broad field known as "manufacturing in space" (ISM) or "manufacturing in orbit" (OOM). nine0003
The first is to use 3D printing to make objects in orbit rather than launch them from the surface. This reduces the need to stock spare parts and allows astronauts to respond faster to new requirements. An interesting twist is to recycle materials, including the packaging of items sent into space, into raw materials (filament) used for 3D printers. The ISS has already tested "Refabricators" to recycle plastic for this purpose.
Secondly, to produce items for which printing is beneficial without gravity. Among the most interesting avenues being explored are bioprinting, where the globular shapes of a liquid can be better manipulated to create complex biostructures, and ceramic printing, where the absence of gravitational stress in production can lead to stronger products. nine0003
There is growing interest in how to produce structures in space that are too large or fragile to withstand launch. Large items printed in space do not need to support their own weight or have complex and heavy folding and unfolding mechanisms. Combined with other technologies (such as robotic assembly), it is a key component of what is known as Orbital Service, Assembly and Manufacturing (OSAM).
All major space agencies are exploring these areas and many projects are currently underway, of which we have selected five to highlight key areas. As NASA's 3D Printing Research and Development Group says, "Don't take it, do it!" nine0003
5.
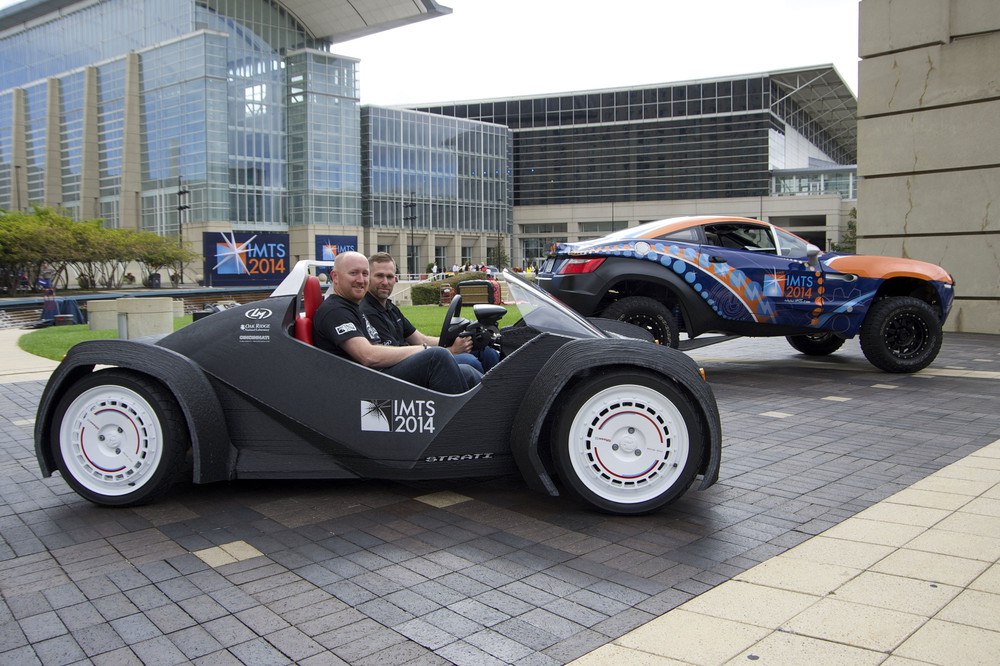
Made in Space: Ceramic Manufacturing Module (CMM)
Ceramic component made with zero acceleration (Source: Redwire).
A wide range of plastic, metal and carbon fiber 3D printing has been successfully tested in space. However, ceramic printing had particular challenges and also revealed new possibilities. nine0003
In 2020, MKS tested the Ceramic Manufacturing Module (CMM) using SLA-based ceramic 3D printing. The idea is that by printing in a zero acceleration environment, the resulting product is subjected to less and more evenly distributed internal stress and can therefore be made lighter and stronger. The first test samples have been created and are being tested.
If successful, there is a potential market for ultra high performance turbine blades manufactured in a specially designed orbital plant. During long missions, this technology will also help repair heat shields and other critical parts. nine0003
- Company: Made in Space
- Notable Technology: 3D printing with SLA ceramic
- Follow: plans to expand space production of valuable ceramic components
6. SPACE 3D PRINTING
Techshot: BioFarbrication Facility (BFF)
NASA astronaut Drew Morgan operating the BioFabrication Facility on ISS (Source: NASA)
Bioprinting uses human cell-based "bio-ink" and the nutrients and materials needed to repair body tissues such as skin, bone, and cartilage. Space applications of this technology are of interest for two reasons.
First, the micro or zero gravity environment allows for printing that is impossible on Earth. In the future, replacement tissues and organs could be printed in orbit and brought back to the surface for use. The second is intended for the treatment of astronauts and researchers during autonomous long-term missions. nine0003
Last year, Biofabrication (BFF) aboard the ISS 3D printed a human meniscus, as well as other test materials. Very encouraging results form an additional mission using a 3D bioprinter in combination with other biodevices on the ISS.
The practical and commercial use of bioprinting in space has significant potential benefits.
- Company: Techshot
- Known Technology: 3D Bioprinting
- Expect: Next generation BFF to launch in 2021 or 2022
7. SPACE 3D PRINTING
Tethers Unlimited: OSAM-1 (Spider & Makersat)
Makersat will produce carbon fiber (Source: Tethers Unlimited) 9000
Development of decisions for service, assumptions and derivatives and derivatives ) is potentially critical for future missions to the Moon and Mars, and is supported by both the China Space Administration and NASA. nine0003
The NASA OSAM-1 mission will refuel and upgrade an existing satellite, as well as test important technologies. On board will be a payload called Agile Robot for Space Infrastructure (SPIDER), which is a great starter combination of robotics and additive manufacturing. The
SPIDER will contain a module known as the MakerSat that will 3D print a 10m carbon fiber composite structure. If successful, the concept will be multiplied to create huge space structures, including antenna arrays and solar array fields. nine0003
- Company: Tethers Unlimited
- Known Technology: Structural carbon fiber printing.
- Expect: the payload will be completed at the end of 2021 and launched in 2022.
8. SPACE 3D PRINTING
Made in space: OSAM-2 (Archinaut One)
Archinaut One will be the first additive assembly test in orbit (Source: Made in Space)
Another NASA mission, OSAM-2, will test part of a concept called Arichnaut developed by Made in Space orbital 3D printing pioneers. Archinaut has evolved into a family of additive, robotic and artificial intelligence solutions aimed at creating large structures in zero gravity.
This initial mission will print cradles to deploy flexible solar panels on both sides of the satellite. The supports will be printed using an undisclosed technology, combined with a robotic arm to create electrical connections, move printed mechanisms, and more. At the same weight as traditional designs, the printed ones are expected to generate five times more power. nine0003
- Company: Made in Space
- Known Technology: Undisclosed
- Expect: The cargo will be completed in 2021 for launch in 2022 by Rocket Lab.
9. SPACE 3D PRINTING
Tethers Unlimited: Next Generation OrbWeaver
Early concept image of space building (Source: Tethers Unlimited via Space)
Our last “project” in this area is actually more speculative and conceptual at this stage, there is a lot of interest in it, and, as they say, “from the street” we can see pilot work in 2021 or 2022.
A 2018 DARPA-funded project (OrbWeaver) to recycle space materials that would otherwise burn up on reentry involved a small machine that chews up metal parts and uses them to print or mold new designs. On the ISS, two Refabricator projects have successfully tested the processing of plastic materials into 3D printed objects. nine0003
Extending this idea to metallic materials in space debris, defunct satellites, or depleted launch vehicles (instead of spending many thousands of dollars to transport new materials into space) is both attractive and intriguing. At the first level, contracts are awarded to study the transformation of scrap metal into raw materials for 3D printing, so technologies in this area are sure to develop rapidly.
NASA and the Russian agency Roscosmos are very interested in this idea, and with many other developments in this area, we may soon see a resurgence of the OrbWeaver or similar projects. nine0003
- Company: Tethers Unlimited and others
- Known Technology: Confidential
- Follow: Potential Pilot Project to Recycle Metal as Raw Material for Printing in Space
CATEGORY: MOON AND MARS
Runner-up team in 3D-Printed Habitat Challenge AT (Source: Joel Kowski via 9)0003
NASA and China's national space agency CNSA have committed to establishing permanent lunar bases with a view to visiting and living on Mars.
Living and working in such remote places requires more materials, fuel and water than can actually be delivered from Earth. Using what can be obtained locally becomes vital, a practice known as In-Place Resource Utilization (ISRU). This is especially true for large-scale housing and other structures. nine0003
ESA groundbreaking work laid many of the (3D printed!) foundations for structures using "regolith" (fine deposits of dust, rocks and minerals found on the lunar surface) back in 2013. NASA subsequently ran a series of highly publicized competitions to design 3D printed lunar and Martian dwellings.
While actual deployment is still a long way off, practical research into technology development is ongoing and we are already seeing side effects for terrestrial applications. nine0003
10. SPACE 3D PRINTING
AI SpaceAfactory: Marsha
The Marsha Concept West Patrilation Competition (Source: AI SPACEFACTORY) Silly Space-9000 9000 AI Spacefactory won the 3D competition for 3D competitions. brilliant "Marsha" design. This was more than a conceptual exercise; it had a deep technical focus on building in a hostile alien environment millions of miles away. nine0003
"While structures on Earth are designed primarily for gravity and wind, Martian conditions require structures optimized to withstand internal atmospheric pressure and thermal stresses." Heavy-duty radiation-resistant buildings are required, and an innovative blend of basalt fiber extracted from Martian rock and a renewable bioplastic derived from plants grown on Mars has been developed for 3D printing. The resulting material was certified two to three times stronger than concrete in compression and five times more durable than concrete under freeze-thaw conditions. nine0003
Many lessons were learned that were taken into account in further research projects and the development of a future mission to Mars. They are also already being used on Earth, and terrestrial versions are becoming commercially available.
- Company: AI SpaceFactory
- Notable Technology: Regolith structural 3D printing
- Follow: Above ground by-products for 3D printed houses
11.3D PRINTING IN SPACE
icon: Olympus
ICON and partners are developing advanced technologies for construction on the Moon (source: BJARKE Ingles Group through ICON)
9000Although before that is still far away, NASA (and other agencies) aim to continue developing and testing ISRU solutions for buildings and dwellings, both on the Moon and on Mars. At the end of 2020, a major contract was awarded to Icon Technology to develop an "off-world construction system". nine0003
The result is the Olympus project, which is being developed in collaboration with two award-winning architecture firms: Bjarke Ingels Group (BIG), renowned for its iconic international architecture, and Space Exploration Architecture (SEArch+), a company recognized worldwide for its innovative solutions.