3D printing bellevue
3D Printing Service for Bellevue, Washington
CapabilitiesCustom Online 3D Printing ServiceWashingtonBellevue
High Quality Bellevue, Washington 3D Printing | 60+ Materials Available
Endless Options
Choose from millions of possible combinations of materials, finishes, tolerances, markings, and certifications for your order.
Easy to Use
Get your parts delivered right to your door without the hassle of sourcing, project management, logistics, or shipping.
Quality Assurance
Our number one job at Xometry is making your custom parts to your specifications.
Your Bellevue, Washington 3D Printing Service: 3D Prototypes and Production Parts
A Global Leader in Industrial-Grade 3D Printing
Xometry is an industry-leading 3D printing service. Whether you need prototypes or production parts, we can make them for you in as fast as a day. We are your one-stop-shop for accurate, precise custom 3D printed parts at a low cost. Upload your 3D CAD file to get a quote and lead time within seconds. We use the latest additive manufacturing processes to build affordable functional prototypes & end-use parts in over 60 metals and plastics.
We offer eight high-quality 3D printing processes including selective laser sintering, fused deposition modeling, stereolithography, direct metal laser sintering, polyjet, Carbon DLS, binder jet metal, and HP Multi Jet Fusion. We use commercial and industrial-grade printers such as Stratasys Fortus 900mc and Fortus 450 FDM, EOS Polymer Laser Sintering (SLS) and DMLS, Concept Laser, SLM Solutions, 3D Systems, ExOne, and more.
Xometry's High Quality 3D Printing Services
Selective Laser Sintering (SLS)
Selective Laser Sintering (SLS) is a powerful 3D printing technology that produces highly accurate and durable parts that are capable of being used directly in end-use, low-volume production, or for rapid prototyping.
An additive manufacturing layer technology, SLS involves the use of a high power laser (for example, a carbon dioxide laser) to fuse small particles of plastic powders into a mass that has a desired three-dimensional shape. The laser selectively fuses powdered material by scanning cross-sections generated from a 3-D digital description of the part (for example from a CAD file or scan data) on the surface of a powder bed. After each cross-section is scanned, the powder bed is lowered by one layer thickness, a new layer of material is applied on top, and the process is repeated until the part is completed.
Download the SLS Design Guide.
Stereolithography (SLA)
Stereolithography (SLA) is a robust 3D printing technology that produces extremely accurate and high-resolution parts that are capable of being used directly in end-use, low-volume production, or for rapid prototyping.
SLA is an additive manufacturing process that focuses an ultraviolet (UV) light on a vat of photopolymer resin. It offers higher resolution printing than many other 3D printing technologies, allowing customers to print parts with fine details and surface finishes. SLA 3D printing is a highly-versatile platform for making custom parts in prototype and production settings; often acting as a stand-in for injection-molded plastic parts.
Xometry offers both standard and high-resolution options for fine detail parts, and can also print larger sized parts and products, with some materials offering up to a 58" inch build area. In addition, Xometry's manufacturing partner network allows us to offer a larger variety of materials than other 3D printing companies - we offer a wide range of both Accura and Somos brand materials.
Download the SLA Design Guide.
Fused Deposition Modeling (FDM)
Fused Deposition Modeling (FDM) is a 3D printing technology widely known for its speed, accuracy, and competitive cost. A machine precisely extrudes melted plastic filament to create a part. Parts are very rigid, especially compared to Selective Laser Sintering (SLS), which makes them a great fit for projects with a rigidity requirement. Xometry's FDM solution offers large build volumes up to 24″ x 36″ x 36″, a variety of colors, and a diverse selection of production-grade thermoplastics — from ABS to Polycarbonate to Ultem.
Download the FDM Design Guide.
HP Multi Jet Fusion (HP MJF)
HP Multi Jet Fusion is a new 3D printing technology that produces highly accurate and durable parts that are capable of being used directly in end-use, low-volume production, or for rapid prototyping. Since the process uses well-established 2D printing ink-jetting, it has remarkably fast layer times compared to other powder bed fusion technologies.
Download the HP Multi Jet Fusion Design Guide.
PolyJet 3D (PJ3D)
PolyJet 3D is a 3D printing technology known for its customizable material properties and excellent surface finish. It works by jetting UV curable resin onto a build tray in a process that is somewhat similar to inkjet printing. PolyJet 3D printing offers one of the most advanced industrial 3D printing solutions available, producing parts with incredible precision and speed. It also supports a wide variety of build materials including rigid and rubber-like plastics. Xometry's PolyJet solution has a maximum build envelope of 19. 3 × 15.4 × 7.9 in. (490 × 390 × 200 mm) in a variety of colors and materials.
Download the PolyJet 3D Design Guide.
Direct Metal Laser Sintering (DMLS)
Direct Metal Laser Sintering (DMLS) is an 3D metal printing technology that builds prototype and production metal parts from a CAD file using a laser to selectively fuse a fine metal powder in either stainless steel or aluminum materials. A DMLS machine is capable of producing highly complex features and all-in-one assemblies using metal materials that would be difficult to achieve with subtractive manufacturing techniques.
Our DMLS metal 3D printing service typically offers build volumes up to 250 x 250 x 325 mm, but we may be able to accommodate larger part volumes upon request in the quote. (See our Manufacturing Standards for more details) A good first step is to find out the cost of the parts you need using DMLS and compare them to other 3D printing processes and CNC machining.
Download the DMLS Design Guide.
Carbon DLS™
Carbon DLS™ uses digital light projection, oxygen-permeable optics, and programmable liquid resins to produce products with end-use durability, resolution and surface finish. This 3D printing technology is called Digital Light Synthesis™, or DLS for short. Another legacy term for the process is Continuous Liquid Interface Production (CLIP). Along with Carbon’s custom liquid resins, DLS unlocks new business opportunities and product designs previously impossible, including mass customization and on-demand inventory of end-use products.
Carbon bridges, and sometimes substitutes, for processes like Urethane Casting and Injection Molding service production, because the materials are urethane-based or epoxy-based, giving excellent mechanical properties. There are even elastomer and silicone resins that outperform most additive manufactured rubber-like materials.
The typical build area is 7.4” x 4.6” x 12.8”. Parts with dimensions exceeding 4” x 4” x 6” will require manual review.
Download the Carbon DLS Design Guide.
Metal Binder Jetting
With binder jetting, an inkjet print head quickly deposits a bonding agent onto a thin layer of powdered particles -- either metal, sand, ceramics or composites. This process is repeated, layer-by-layer, using a map from a digital design file, until the object is complete. Binder jetting is offered through our Digital RFQ Marketplace through Xometry's partnership with ExOne.
Download the Binder Jetting Design Guide.
Locations near Bellevue, Washington
Redmond
WashingtonSeattle
WashingtonTacoma
WashingtonYakima
WashingtonPortland
OregonSalem
OregonCorvallis
OregonSpokane
WashingtonEugene
OregonMeridian
IdahoBoise
IdahoHelena
MontanaBozeman
MontanaReno
NevadaSparks
NevadaCarson City
NevadaSacramento
CaliforniaElk Grove
CaliforniaBillings
MontanaStockton
California
Ready to start making custom 3D printed parts?
Contact GoEngineer in Bellevue, WA
800-688-3234
Hours: Monday – Friday: 8:00am-5:00pm PTRequest More Information About GoEngineer Bellevue
GoEngineer
Bellevue, WA
:
11130 NE 33rd Pl, Suite 110
Bellevue, WA 98004
Phone:
425-529-9250
Toll Free:
1-800-688-3234
SEE ADDITIONAL GOENGINEER LOCATIONS
Take Advantage of GoEngineer’s Extensive Knowledge Base and Resources
Find a Solution
Our robust Knowledge Base contains over 12,000 resources to help answer your product design questions.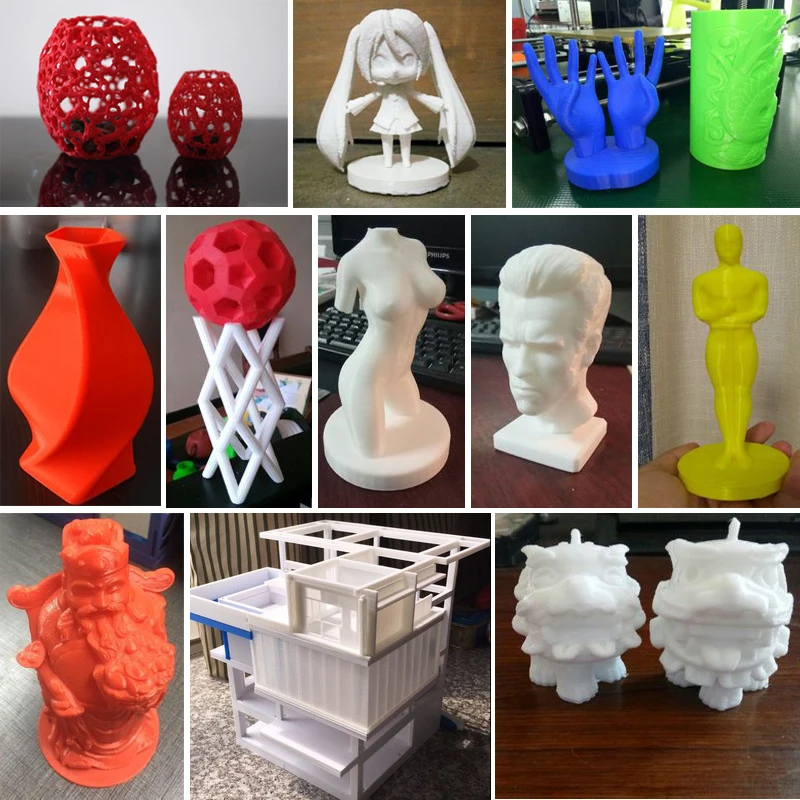
PROFESSIONAL TRAINING
Improve your skills with professional training and certifications in SOLIDWORKS, CAM, 3D Printing, and 3D Scanning offered four ways: self-paced, online, on-site, or in-classroom. Certified Training Courses
BLOG
#1 Technical Resource Worldwide - Right at your fingertips. Search or browse through hundreds of SOLIDWORKS tips & tricks, additive manufacturing product developments, announcements, how-to guides, and tutorials. Blog
YouTube Channel
Our YouTube channel hosts hundreds of educational tutorials, product demonstrations, recorded webinars, and best practices for all of our products and services.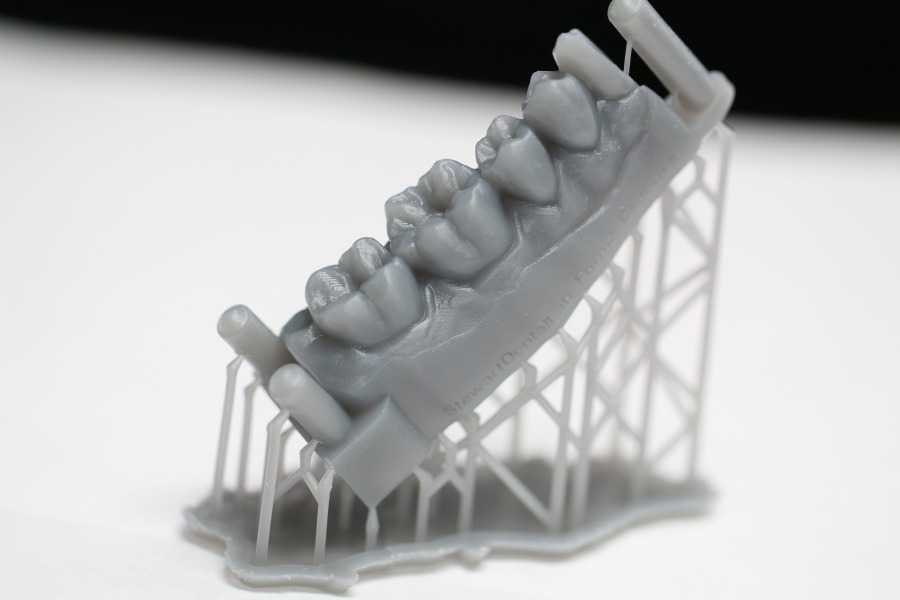
ONLINE STORE
Order 3D printing materials and consumables, enroll in SOLIDWORKS training classes, and buy official GoEngineer gear directly from our online store. Online Store
FREE SOLIDWORKS Tools
Enjoy this collection of small ‘macros’ that were tailored to help our customers. These free SOLIDWORKS tools are for you to use, review, and modify. SOLIDWORKS Automation Tools
WEBINARS
Our engineering webinars are hosted by some of the top experts in the industry. They are always recorded, always free, and always offer a live Q&A.
3D Printing Services
Need to 3D print a part? Our Additive Manufacturing experts will 3D print your part and deliver it to you using the latest technology on one of our professional FDM, PolyJet, SL, or Metal 3D printers. 3D Printing Services3D printing of organs in Germany: growing bones and blood vessels
Reading: 4 min Published: Updated:
The claim of 3D internal organs is no longer science fiction, because today it is science fiction scientific fact - 3D printing of human organs is used in medicine: 3D printed organs are already being used as training aids for future surgeons. But the creation of functioning human living tissues will be the next step in the development of this innovative technology. nine0007
The idea of growing human organs in the laboratory was put forward by scientists many years ago, and continuous developments in this area have given a positive result. Now there is bioprinting (printing three-dimensional objects from biological material) that allows you to create human organs. However, scientists continue to actively develop the capabilities of 3D printing technology of organs , because many questions in this area have not been answered. The main problem remains the unsolved problem of establishing blood supply to artificial tissues. nine0007
Arteries, veins and capillaries are simply necessary for all organs for proper functioning, because with their help, nutrients in the blood are delivered to various tissues, which allow maintaining the life and health of organs. Printing blood vessels is very difficult due to their specific shape, length and width.
Researchers of the University Hospital Freiburg (Germany) have undertaken to solve this problem. They are currently developing a printing technique that makes it possible to produce fully functioning bones from cells and blood vessels. Vascular cells should improve tissue circulation by connecting to the patient's circulatory system. For the development of this technique, the German Research Society (DFG) allocated a grant of 460,000 euros to Freiburg scientists for a period of three years. If this experiment is successful, then in the future it will be possible to print larger samples of artificial tissue up to entire organs. Scientists believe that in medical practice such a "cellular printer" will be used in five to seven years. nine0007
The uniqueness of the development lies in the fact that the goal of scientists is to print not just an internal organ, but a bone equipped with blood vessels. This choice was made because the bone has a complex blood supply system, and if it is possible to create bone tissue together with blood vessels, this will be an ideal solution to the problem. If they fail to do this, then the range of sizes and types of samples produced will be significantly limited.
It is now known that the supply of artificially produced tissues with blood can be improved with the help of endothelial cells. They line blood vessels and are able to independently form new vessels. However, most bone cells die from a lack of oxygen even before the endothelial cells have time to form vessels. This problem will be solved by scientists. As a result, soon after the operation, the vessels of the artificial tissue should begin to fuse with the vessels of neighboring healthy tissues and, thereby, provide blood supply to the artificial ones. nine0007
What will the development of an innovative idea for 3D printing of living bone and blood vessels bring? Practical application:
1) Transplantology.
There is a huge shortage of donor organs in the world and the creation of organs from the body's own cells will help solve this problem. The ability to create new organs directly from the patient's own cells cannot be overestimated.
2) Bone replacement.
Combined with 3D scanning, 3D printers can create any bone in the human body. Creating bones that are ideally matched to the patient significantly improves recovery after transplantation, reduces discomfort from using a prosthesis from one's own tissues, while predicting the absence of adverse reactions of the body. nine0007
3) Testing of medicines.
Now absolutely all medicines are controlled and tested on animals and humans. This is accompanied by rather large problems and significant costs. With the help of printed organs, it will be possible to check for side effects or negative reactions to any drug. Also, this technology contributes to the continuous development of medicine.
This technique, with the success of this study, will be available by the end of the decade, which will greatly facilitate the problem of bone and bone tissue transplantation, help in prosthetics and provide a better quality of life for patients in the future. Company Treatment abroad » will continue to follow all the new developments that are continuously being carried out in best clinics in Europe . We will always help you in the selection and selection of a specialized medical facility to address the issue of health.
Like this article? Share:
Reviews
Review score 5 points | Patient: Maria L., 31 years old Diagnosis: epilepsy Clinic: Vogtareuth Clinic, Vogtareuth, Germany / University Hospital, Bonn. Germany I have frequent epileptic seizures after suffering viral meningoencephalitis. Faced with the fact that I can not choose the drug and calculate the right one ...... More
News
29.12.2022 Intervertebral hernia: the possibilities of innovative treatment abroad, minimally invasive operations
29.12.2022 Gliwhobostoma: unique operations, neuronavigation, modern radiosurgery abroad
222222222222222222222222222222222222222222. 20 treatments - from targeted drugs to minimally invasive spinal surgery
22.12.2022 Liver transplant in Turkey: modern transplant center at Florence Nightingale Clinic
12/22/2022 Glaucoma: surgeries with drain implants, minimally invasive surgery, laser surgeries abroad
artificial organs, smart prostheses, heart valves and 3d skin
Medical 3d printing was once only an ambitious pipe dream, however, progress and investment are making it more and more real. The first 3D printing methods appeared in 1986. In recent decades, they have become widespread.
Contents
- What is bioprinting
- Applications for 3D printing
- Specific advances
- The future of 3D printing in medicine
What is bioprinting
3D printing is a process by which a three-dimensional solid object of almost any shape is created from a digital model.
It all starts with the selection of the target anatomy and the development of the 3d geometry. Of great importance in 3D printing is good visualization, which is created on the basis of CT or MRI medical images. The original images are the thinnest sections and are necessarily carefully checked by the radiologist and the attending physician. Next comes the choice of 3d printer and materials. During the printing process, the original digital model is "cut" into cross sections. Then, in the same layer by layer, the 3d printer reproduces the object. As a result of printing, the raw materials undergo changes - they harden. nine0007
The choice of material is determined by the purpose of the 3D printing as well as the model itself: for example, the easiest biological tissue that can be 3D printed is bones, as they are rigid. As for soft tissues, the gap between the 3D printed anatomical model and real human tissues is still significant, and in-depth research is needed in this direction. To date, success has been achieved in the reproduction of cartilaginous tissues, arteries, liver segments, and heart valves. nine0007
Applications for 3D printing
Every year, 3D printing technology opens up more and more applications in the medical field, helping to save and improve people's lives in revolutionary new ways. It is difficult to overestimate the growth rate of the bioprinting market in the coming years: the demand for donor organs far exceeds the "supply", especially the need for soft tissues used in reconstructive operations - after injuries, burns, after infectious diseases, removal of tumors, with congenital malformations. By some estimates, an average of 21 people die each day due to lack of implants. nine0007
This visualization makes it possible to select implantable devices and surgical instruments individually for each patient, optimizing the surgical process and reducing its cost. One of the first areas of application for 3D printed anatomical models created on the basis of CT, MRI or 3D ultrasound of a patient was the development of surgical techniques with training of the necessary skills. Until recently, rare anomalies could only be seen on autopsy specimens. Today, any anatomical models can be printed on demand using in vivo CT of patients. Accurate development of surgical treatment tactics, taking into account the individual characteristics of the patient, can potentially reduce the time of the operation and lead to fewer complications. In the long term, this will reduce the time of postoperative hospital stay, reduce the frequency of relapses and, ultimately, reduce healthcare costs. nine0007
Bioprinting is also proving useful in the field of medical education: 3D printed models contribute to faster and more productive learning, no matter what specialization future doctors choose. 3D models are precisely reproducible, safe: thanks to a huge set of images, they are able to model a wide variety of pathological anatomy and physiology.
3D printing could be used in implant medicine – printing “substitutes” for biological tissues is already under development. The transition to the "printing" of whole organs for the needs of transplantation is difficult, but the foundation for it is already being laid. Research is currently underway to enable 3D printing of blood vessels. nine0007
3D printing has made it possible to automate the production of hearing aids and dentures. For example, the algorithm for the production of hearing aids involves scanning the ear in the first step to obtain an accurate image of the ear canal; then, based on the resulting image, a model is created, which is subsequently reproduced using a 3d printer with the highest accuracy. At the same time, the speed of manufacturing such prostheses can reach 65 prostheses per hour.
3D printing technology provides pharmaceutical and medical companies with ample opportunities to create new forms of drugs: printed “desktop” organ models are successfully used to test new drugs, including alternative dosage forms, select an individual dose of a drug, etc.
Bioprinting can also be used to test cosmetic, chemical and other products. For example, with the help of heart valve remodeling, it is possible to control stiffness.
It is often difficult for patients to understand 2d images representing 3D anatomy. In this case, 3D printing clearly demonstrates the anatomical model, which greatly improves communication between the doctor and the patient. Also, the use of 3d samples is also possible in resolving emerging litigation: a 3d model can easily demonstrate various anatomical anomalies that may be difficult to understand in transverse imaging. nine0007
Finally, in the future, bioprinting organs will replace animal models used to test new drugs. 3D printing is a full-fledged alternative to the methods of surgical training used today on animal organs and cadavers. At the same time, the use of artificial models removes many ethical issues.
Specific achievements
Today, in one form or another, 3D printing is used in the following areas of medicine: cardio and thoracic surgery, cardiology, gastroenterology, neurosurgery, maxillofacial surgery, ophthalmology, otolaryngology, orthopedics, plastic surgery, pediatrics, pulmonology , radiology, transplant surgery, urology, vascular surgery and others. nine0007
To date, the list of objects that have already been successfully printed in medicine demonstrates the potential that this technology has:
Scientists have made great strides in the bioprinting of blood vessels by developing a special structural material that can function like blood vessels.
-
Dentures
Traditional dentures are very labor intensive. Being a material foreign to the body, they can cause destruction of cells and tissues. Thanks to 3D printing, cheap and easily customizable prosthetic sockets can be made quickly. nine0007
-
Medicines
University of Glasgow chemists use 3D printing to assemble chemical compounds at the molecular level. Currently, this technology is used to create biocompatible drugs against cancer.
Based on the scanning of animal hearts, it became possible to develop electronic sensors for monitoring the level of blood saturation with oxygen and carbon dioxide, filling the chambers of the heart, pressure, and temperature. Thanks to this technology, for example, blocked arteries can be detected. nine0007
The use of printing models of cancer tumors allows scientists and doctors to understand and predict the development and spread of tumors, and further develop effective anti-cancer drugs.
-
Bone
At present, it is already possible to use bone scaffolds to promote the growth of bones of any shape. Due to the uniform dissolution and mixing with the biological tissues of the musculoskeletal system, the lost structures and functions are restored. In particular, there is a successful experience of replacing part of the skull with a special plastic implant. nine0007
-
Artificial leather
A separate area in medicine is skin transplantation in patients with burns. By directly scanning the wound, the printer can produce tissue with the appropriate number of layers to fill the wound perfectly. This technology has been successfully tested in the US Army for the treatment of wounded soldiers and is gradually being introduced into clinical practice.