3D printed animatronic
Grant Imahara Uses Digital Modeling & 3D Printing to Make Adorable Animatronic Baby Yoda - 3DPrint.com
I do love a good Star Wars 3D print, and I know many others do as well. A popular character in the Star Wars universe is obviously Jedi Master Yoda, and many people around the world were excited to see him in a new light when The Mandalorian live action series premiered on Disney+ this fall. While the adorable character on the show is simply called the Child, the collective fandom knows him as Baby Yoda.
(Image: Lucasfilm)
“Two things in life are certain: One, you’re going to die. Two, Baby Yoda will forever dominate people’s hearts and the internet with his cuteness,” a Nerdist post proclaims.
Former Mythbusters star Grant Imahara, a Disney Research consultant and mechanical designer at Spectral Motion, is a fan of 3D printing and robotics…and, as it turns out, Baby Yoda. He used both of these technologies, along with digital modeling, during a three-month project to make an animatronic Baby Yoda that is so cute, the engineer says that “everyone melts” when they see it.
“Pleased to present my newest creation: a fully animatronic Baby Yoda,” Imahara wrote in a Facebook post. “He’s a personal project that I started in early December. I did all the mechanical design, programming, and 3D printed the molds.”
In a recent interview with CNET, Imahara said he knew he wanted to make his own Baby Yoda after only the third episode of The Mandalorian.
“I was an animatronics engineer in the ILM model shop before MythBusters, and worked on the Star Wars prequels as well as the Energizer Bunny, so I had the required skill set,” Imahara said.
Project 842 created the digital model of Baby Yoda, and then Imahara got to work on the robot’s first mechanical system: the eyes. The goal was to fit everything in the head, though this proved quite difficult, as the character has a tiny noggin and huge eyes. Those eyes can move up and down, left and right, and even blink, while the neck can tilt side to side and move forward and back.
“Since they carry the weight of the head, these servos had to be larger and I placed them in the body,” Imahara explained.
After adding a simple mouth flap that could easily handle making the character’s signature pouting movement, he moved onto a less simple mechanism – the ears.
“They’re huge levers and the silicone skin acts as a spring, resisting movement, so I upgraded these servos several times, adding more and more torque (and size) until everything moved smoothly.”
Imahara revealed that he 3D printed almost everything in the robot’s head, along with the molds to make the skin. In his Facebook post, the engineer gave a shout out to his friend Lauren Markland, a prop maker at Universal Studios, who cast, seamed, and painted the silicone skin, as well as completing a very tedious task.
“The hair on his head is individually punched one at a time with a tiny needle, which took days to complete.
”
Movie costumer Lindsay Hamilton, another friend of Imahara’s, was enlisted to make Baby Yoda’s coat and jumpsuit, which I’m guessing wasn’t terribly difficult because his clothing pretty much resembles a potato sack, but what do I know?
Speaking of things I don’t know, Imahara explained how he was able to get his Baby Yoda to move around and blink, which you can see happening in the video below.
“Programming the animation is a pretty tedious process because it has to be done with keyframes, but you build up the sequences a little at a time, adding more quirks and little movements to help with the illusion,” he said. “Once I got the animation sequence to a point where I could loop sleepy/grumpy/happy, I loaded that into the servo controller so that it would loop continuously.”
The animatronic robot can’t speak at the moment, but Imahara is working on a solution for this problem, noting that the “servo controller board has several available outputs that can be configured to trigger an external sound board. ”
“Eventually, I will be able to have the Baby do a basic keep-alive sequence (blinking eyes, looking around) but also be able to remotely trigger special sequences like happy, sad, grumpy or sleepy.”
One of the best things about this project is that it’s not-for-profit. Next month, Imahara will begin touring children’s hospitals with his amazing Baby Yoda for charity.
“Baby Yoda is universally cute, hands down,” he said, stating the obvious. “He’s a happiness maker. Everything about him is designed to trigger the human nurturing instincts.”
Discuss this story and other 3D printing topics at 3DPrintBoard.com or share your thoughts in the comments below.
(Images: Grant Imahara, unless otherwise noted)
Stay up-to-date on all the latest news from the 3D printing industry and receive information and offers from third party vendors.
Tagged with: 3d print star wars • 3d printed animatronics • 3D printed Baby Yoda • 3d printed molds • animatronic • digital model • Grant Imahara • star wars • yoda
Please enable JavaScript to view the comments powered by Disqus.
3d printing — How To Make Animatronics — Poorman's Guide To Animatronics
/ MimiIt looks like I will be cutting back on the time I spend on writing blogs posts for a while, so I thought I would outline some of the ideas I have for future posts. Just so you know I am thinking of you.
This is a mash up of my 3d printed Crawling Terminator Hand, from six or eight posts ago, and the Endoarm posted to Grab Cad by Simo83. Simo83 saved me a huge amount of work by creating a beautiful model of the classic Terminator Arm and posting it online. Yay for Simo83.
https://grabcad.com/library/endoarm-stl-1
I modified the Endoarm design by making the fingers mechanically functional and then 3d printed the whole thing up in order to create a replica of the T-800 Terminator arm capable of dragging itself along by its fingertips.
I got myself a 3d scanner awhile back and put it through its paces to see what it could do. It could do quite a bit until it stopped working just as its warranty had expired. That’s what I get for being an early adopter but I learned a lot. I will demonstrate the process I went through to create a 3d model of my hand and how I was able to use that data to create a custom fit, 3d printed Telemetry Glove.
The use of practical creature effects for film and television has become so “old-school” that there is a whole new generation of filmmakers who don’t know how to best utilize it. I am going to create a primer on some of the basic techniques involved in the process of filming the performances animatronic puppets.
A few years back a videographer friend of mine and I made a short film featuring animatronic puppets called The Escape. A wide range of techniques came into play during filming and I am going to deconstruct the whole process and explain how all the various shots were made to work.
Stay tuned!
/ Mimi/ 2 Comments
how to animatronics, 3d printing, 3d scanning
/ MimiNow that the parts are electroplated, it is time to put everything together.
The NeckThe neck is the heart of the Brave New Pink Flamingo. It is a 2-stage tentacle mechanism with a 1/8th inch diameter speedometer cable as its core.
When I started seriously considering the use of 3d printing for animatronics, my first thought was “how awesome would it be to just print up a mechanism and all I needed to do was drop the servos in?”. Well, it never really worked out that way, but I made a good attempt at that goal with this system. The body was 3d printed as three different layers, and when screwed together, accomodated three servos with pulleys and cable housing terminations, and integrated perfectly with the neck mechanism.
Ther servos I chose for this project were three Hitech 805bb servos. They are fairly strong and really cheap (~ $40 each). There are servos out there that are two thirds the size and are three times as strong, but they cost four times as much. So there you go.
The LegsFlamingos have long legs and the Brave New Pink Flamingo is no different. This part of the project actually ended up being a tremendous lesson for me in the structural limitations of 3d printed parts.
Aw Snap! I designed and printed the components meant to serve as the legs and hips of the BNPF. After assembling these parts I didn’t like what I saw. So I gave it the “I wonder how easily I can break it” test. Oops, too easily. Back to the drawing board.
One of the great things about 3d printing is the ability it grants to try out different iterations of and idea without a lot of man hours involved. In the picture above you can see where the first leg structure failed and how I beefed it up in the second. If I had spent the time machining these parts and had this kind of failure, there would have been much wailing and gnashing of teeth. As it was, it was more a matter of “huh, look at that…”. It was a good learning experience.
Designing for the MaterialWhen one learns to design mechanical systems made out of metal, like I did, there are certain things one takes for granted, like strength and durability. So, moving forward with this project, I had to make it a point to stop and think about what I was asking the materials to do. It’s not a difficult thing to do, but it was an interesting process, at the time.
Here is an example of the shift that took place in my design approach. The project called for the whole body and neck assembly to elevate 120 degrees on a .25” diameter steel shaft suspended between the hips of the BNPF. The idea was to use a .5” bore metal shaft collar to clamp down on a printed plastic hub in order to hold that steel shaft. On the left, is the first hip hub part and the off-the-shelf shaft collar I intended to clamp down over the part. On the right is the redesigned hip hub with a much beefier seat for a much bigger shaft collar. The new shaft collar was something I had to custom make.
In my new found paranoia about breaking plastic components, I was very concerned about my plan to press fit bronze bushings into my 3d printed parts. I am pleased to announce that, yes, you can press fit bronze bushings into 3d printed parts.
Here is a good work around for the fact that 3d printed parts cannot be threaded: press fitted nuts in hexagonal recesses. Works great!
Body Elevation MechanicsRaising and lowering the body of the BNPF was accomplished with a linear actuator from C.K. Design Technology Inc.
http://www.ckdesigntech.com/wseriesfb.html
It was during the construction of this part of the BNPF that my 3d printer started giving me problems. I had gotten most of the plastic parts I needed so I didn’t it slow me down and continued on using more traditional/old-school machining techniques. In terms of the levers, cranks, and clamps needed for this part of the project, there wasn’t much 3d printing was going to do for me, anyway.
Head MechanicsThe head is a relatively simple yet critical aspect of the BNPF. It is actually made from a model of the jaws of a dragon fish. How cool is that?
The neck had to be completely installed and cabled before the head could be dealt with. There is a lot that goes into a 2-stage neck mech, especially if there is going to be a cable actuated head mounted on the end of it.
The BaseTo facilitate bringing all the various elements together, the BNPF needed to be mounted on its base. I wanted this critter to stand stand fairly high in relation to the eye line of its viewers, so I chose to mount it upon a metal pedestal that was once part of a decorative lamp post. It is to be displayed in a group art show and these things need to be considered.
In addition to supporting the BNPF and displaying it to its best advantage, the base houses all the various electronics needed to bring this project to life (power, microcontroller, sensors, motor control) . So, it not only needs to be sturdy and look good, it’s interior needs to be accessible while the electronics are installed. The enclosure for the electronics actually required a surprising amount of work.
The electronics for the BNPF required two different power supplies and they needed some sort of decorative enclosure. I modified an old radio I picked up at a flea market to serve that purpose.
The Control ElectronicsAs an art piece the BNPF looked really cool. However, it was meant to be an interactive, robotic art piece, and as such, it was less than ideal. The problem was that I was using a Basic Stamp 2 as a microcontroller and its capabilities were just too limited. At the time, it was the microcontroller I knew best. The inherent limitations of the Basic Stamp 2, as well as the fact that I had run up against the deadline for the art show, meant that its performance was less than satisfactory. Ah well.
The system I had put together to control the performance of the BNPF consisted of the Basic Stamp 2, a motion sensor, and an array of three sonar range finders. The idea was that the motion sensor would alert the Basic Stamp 2 of the presence of people, the array of sonar sensors would located the location of the nearest target within range, and then the BNPF would respond with some behavior appropriate to the direction and proximity of the nearest target. I have some success in the past with this exact system with animatronic tentacle creatures, but alas, the BNPF was just a bit too complex for it to work well. It needed to be able to respond to its environment with the same level of interactivity as a pet parrot on a perch, which it really didn’t.
I was discussing this situation with Jon McPhalen, who is a big proponent of the Parallax Propellor microcontroller and he has me convinced that the Propellor is the way to go with this kind of interactive, robotic sculpture. Microcontrollers like the Basic Stamp and the Arduino are capable of doing only one thing at a time: check the sensors, move a servo position, move another servo position, check the sensors again, ect… not really what was needed. The Propellor has parallel processing, which basically means it has 8 individual processors working simultaneously. That means sensors could continuously be scanning the surroundings of the BNPF, servos could be going through complex little behavioral subroutines, and multiple emotional states could be qued up and ready to go once the sensory inputs indicated it was appropriate. Sound great right?
I know people who seemingly eat new computer languages for breakfast. I am not one of them. I have sat down a number of times with a chunk of time set aside for learning to program the Parallax Propellor in the Spin language, and every time it was a miserable experience. I found the learning curve for Spin to be brutal. The Brave New Pink Flamingo stands lobotomized in a corner of my studio to this day. So sad.
/ Mimi/ 3 Comments
animatronics, mechatronics, robotic art, 3d printing, electroplating
/ MimiAfter that loonnng series of posts I just finished (Wonderful World of Tentacle parts 1 through 5) I thought it would be nice to keep this one short and sweet. This project I am about to describe features a tentacle mechanism, but I cover new information such as the the use 3d printed mechanical parts and how to strengthen printed parts with electroplating.
The Brave New Pink Flamingo was originally created to be part of the Conjoined 5 group art show curated by Chet Zarr at the Copro Gallery in Santa Monica. It was inspired by the tacky pink plastic flamingos people sometimes use to decorate their yards. “Wouldn't it be so much cooler if they were robotic,” I thought to myself, and so was born the Brave New Pink Flamingo.
The ConceptThe original concept started off as a retro-futuristic-rocket-ship-looking robot flamingo featuring 3d printed pink parts. However, it evolved into something scarier, probably because I was binge listening to the H.P. Lovecraft Literary Podcast while I was building it. So it goes.
At the time, I was still getting to know my 3d printer and what it could do. I decided the Brave New Pink Flamingo (BNPF) was going to feature a servo operated tentacle mechanism. I like tentacle mechs because they are relatively simple yet can be very expressive. This was for an art piece so simple and expressive were desirable features. In addition to the tentacle mech neck, I wanted it to have jaws. A robotic sculpture with a long, sinuous neck and big, toothy jaws trying to bite people: how cool is that?
I had the opportunity to try out a new material: carbon fiber-filled PLA from Proto Pasta. It seemed like a good choice for mechanical components. I also experimented with electroplating as a way to strengthen and stiffen the 3d printed parts. Electroplated plastic works really well for mechanisms as well as art. Not only does it strengthen and stiffen the parts it gives it a beautiful and durable finish. Most of the animatronic art pieces I've done over the years have featured electroplating. I just can’t seem to help myself.
A microcontroller and an array of an electronic sensors were incorporated into the BNPF to give it some robotic interactivity. Animatronics for use in film usually involves an operator/puppeteer but as a stand-alone art piece I wanted this to be a robot, not a puppet. Alas, this was probably the least successful aspect of this project due to my limitations as a programmer. Improving my programming skills in order to bring the Brave New Pink Flamingo to life is still very much on my bucket list.
3d Printing the PartsAll of the printed parts for this project we're created on Woody, my Type A Series 1 3d printer. One look at the photo will tell you why I named it Woody. As a material for mechanical components, carbon fiber-filled PLA has some nice characteristics, primarily it's stiffness and it seems to warp less than regular PLA. However, the main drawback is the wear-and-tear the carbon fiber PLA inflicts upon all the metal parts of the printhead. I managed to get most of the way through two rolls of the filament before the little knurled wheel that feeds the filament through the hot end of the 3d printer was worn smooth. That's not a huge deal if one is prepared to replace printer parts on a regular basis for the sake of using carbon fiber-filled PLA, but I was still unfamiliar with the technology and I was up against a deadline. So, the experience of being in the final phase of the project and having all my prints unexpectedly turn into crap pretty much turned me off to carbon fiber-filled filaments. I ended up resorting to more traditional machining and model-making techniques to finish this project. Specifically, the feet, the head, and the body shell are fabricated by methods other than 3d printing. They turned out pretty cool, but the added aggravation was not appreciated.
A common misconception amongst people unfamiliar with 3d printing is that the parts come out of the printer in pristine condition. This is not the case. There is still a considerable need for what machinists call benchwork. In 3d printing there tends to be loose strands of filament, wonky edges where the parts were adhered to the print bed, and all the holes end up being a little bit undersized. These issues all require some trimming, standing, drilling, and filing. The great part about 3d printing mechanical components is how accurate the fabrication process is. The holes may be a little undersized but they all line up perfectly with each other. I love that.
Another underappreciated aspect of the 3d printing process is the characteristic texture that everything ends up with. There may be some really high-end machines out there that can make some beautifully smooth and flawless prints, but I don't own one of those. When I first started working in the film industry I was introduced to the concept of “if you can't hide it, feature it”. In the case of 3d printing, this means you should learn to love that funky texture because it is not worth the hassle of getting rid of it.
I was probably 90% of the way through the printing needed for this project when the prints began to fail. I didn’t realize it at the time, but the carbon-fiber-filled PLA really wears upon any metal components of the print head it comes in contact with. The benefits of using carbon fiber-filled filament are just outweighed by this fact, in my humble opinion. The filament strands are indeed strengthened by the addition of little chopped up pieces of carbon fiber but the inherent weakness between the layers of the printed part is not mitigated in any way. The junction between these layers are where the parts are weakest, so there is no real benefit gained by using the carbon fiber-filled PLA filament, though I have to admit, I do like the matte black color of the finished parts.
The Machined Parts
As useful as 3d printed parts are, there are certain applications that require metal. Specifically, anything in the body of the BNPF that is going to have threads cut into it will be made of aluminum. Printed plastic parts can be tapped but it won't take too much tightening for a screw to just rip those threads out. There are certain applications where one can get away with that, but for the most part, I try to avoid tapping plastic.
For the BNPF project I turned some simple standoffs on a lathe for securing the various components of the body together. I probably could have used off the shelf threaded standoffs but a little lathe work seemed like a nice change of pace. Additionally, I drilled and tapped a bunch of small aluminum gear blanks for mounting the tentacle segments. The gear blank modifications in particular were a little labor-intensive: lots of little holes to drill and tap. For future 3d printed tentacle projects I have figured out different mounting techniques involving the use of heat set threaded inserts that eliminate the need for the gear blanks, but that is for another project.
In addition to the aluminum standoffs and the modified gear blanks there are other mechanical components machined from metal. These were the parts involved with moving the whole body and needed to be particularly strong. We'll discuss these when we get to the body elevation aspect of the project.
The Pre-Assembly ProcessA pile of parts is pretty uninspiring. So I find it helpful and informative to assemble the components as they are produced, even though I know full well I'm going to have to take everything apart again. The fact is, the more complicated the mechanism, the more assembly and disassembly will take place. One of the guys who taught me how to do animatronics, way-back-when, told me that a project isn't done until you’ve taken it apart and put it back together at least 8 times. And 20+ years later I pretty much have to agree. It's best to keep it to a minimum, for the sake of one's own sanity, not to mention that of your employer, but a certain amount of it is unavoidable. But it's pretty damn cool to see your stuff coming together during that initial pre-assembly.
Servos were used to drive the neck of the BNPF. The servos I chose were three HiTec hs-805BB servos because they are strong, durable, inexpensive, and have nylon gears instead of metal gears. Nylon gears are not as strong as metal gears but they have better wear characteristics and will last longer if not put under too much load. The design of the 3d printed body framework is laid out so as to provide a place to mount the neck, hold the servos in place in relation to the neck, and to provide a structural pivot point for the elevation of the body. This should all become more clear as all the components come together. The elements of the body structure are designed in layers to facilitate the 3d printing process. The the aluminum standoffs connect these different layers together.
Once I am satisfied with how the various body and neck elements go together I then have to take it all apart for the electroplating process. Yay.
I have seen examples online of people electroplating 3d printed plastic parts but never for the purpose of making them more structural: only to make the parts prettier. I have utilized electroplating in the past with cast resin parts to make them both stronger and yes prettier. There is a huge opportunity or making lightweight 3d printed parts more suitable for use in mechanisms, and now I am going to let you in on the secret.
Primarily, the individual components of the neck and the neck strut will be electroplated. These comprise the most visually dominant elements of the BNPF and would benefit the most from being strengthened and stiffened. Some of the other visual elements will also be plated but the neck and the strut are the most mechanically crucial parts to undergo the process.
Once the components are cleaned up, the first step of the electroplating process is to give them a coat of primer. I use an automotive primer as it is of a better quality than the more generic types of primer available from your local hardware store. After the primer is applied, a fairly heavy gauge (18 to 16 gauge) of copper wire needs to be attached in order to suspend the parts in the electroplating solution. The plastic parts will want to float in the plating solution so the copper wire needs to be strong enough to keep the parts submerged during the plating process. Then, a layer of electrically conductive paint is applied to the part. Electrically conductive paint is available from plating supply companies online.
I have found it helpful to apply the conductive paint with an airbrush for anything but the smallest objects. Airbrushing helps to apply the paint evenly but it can be tricky. The conductive paint needs to be thinned down enough to pass through an airbrush but not so thin that it becomes non-conductive. My approach to this is to thin the paint just enough to be able to spray it with an airbrush and no more than that. The texture of the paint can get a little stippled, adding some roughness to the final finish of the metal plate, but I have learned to live with it. The alternatives to applying the paint with an airbrush is to use a paint brush (very labor intensive and inconsistent) or to dip the parts in conductive paint (requiring a lot of paint).
My electroplating system does really well with copper. Copper is the base metal for any plating operation weather it is for gold jewelry or chromed hot rod parts. I allowed the copper layer to build up on the parts for about 12 hours.This creates a layer that is plenty strong for the purposes of the BNPF.
I also had a small amount of nickel plating solution that I thought I'd make use of, though the finish has never been quite as bright and shiny as it might have been. Don't know why, but it always comes out a little funky. We're making art here not a hot rod; I have embraced the funk. The nickel plate was allowed to go on for about 30 minutes. It came out of the plating tank looking brown and funky, but with some buffing with a soft wire wheel in a dremel tool it shined up fairly well. However, it still retained some of that funky stuff. In future projects, the funkiness increased to the point where the solution just became useless. Perhaps some chemical element was becoming depleted in the solution. Don’t know. Not worried about it. Moving on.
/ Mimi/ 4 Comments
animatronics, mechatronics, electroplating, 3d printing, carbon fiber pla
/ MimiI was always interested in 3d printing for the purpose making functional mechanisms. I still had all my mechanical drawings from that previously mentioned Terminator project and decided to 3d print an articulated robot hand. Not just any robot hand, but something capable of dragging itself along under its own power. I wanted to see what 3d printed mechanisms could do.
The Terminator hand design was based upon the T-800 Endoskeleton Arm that used to be available from Sideshow Collectibles. That model was apparently molded directly from a working terminator arm made at Stan Winston Studios for use in the movies. It had the screw heads and accommodations for finger linkages already laid out and the dimensions were exactly what they needed to be to recreate the functional mechanism.
The mechanisms for the T-800 hands were originally fabricated using traditional machining techniques ( of course). This meant there were plenty of places to grip the parts in a vise or a 4 jaw chuck for the machining process. These features translated well to the technology of FDM 3d printing, where it is desirable to have flat surfaces to attach to the print bed.
/ Mimi/ 1 Comment
Projects
3d printing, terminator, T-800 Endoskeleton Arm
/ Mimi
We live in interesting times.
3d printing is becoming a mature technology and can be very useful and making mechanisms. I once heard 3d printing described as a lifestyle enhancement. Speaking as someone who is tired of expending my valuable hours planted in front of a lathe or milling machine, I heartily agree.
Man hours are expensive. Robot hours not so much. The more work that can be delegated to some form of CNC (computer numerical control) machine, the better.
3d printing has its strengths and it has its weaknesses. The trick is to play up its strengths and avoid the weaknesses. Over the past several years I've been experimenting with 3d printing parts for animatronics mechanisms with mixed results. Sometimes plastic just won't do and metal fabrication comes back into the picture. However, there is a lot plastic can do.
The New and Improved Thrashing Torso:
Since I built the original thrashing torso, all those years ago, a few things have changed.
3d printing is one of these changes. Another change is the introduction of new off-the-shelf products meant for use in Halloween haunted attractions. I've recently been introduced to the Spider Joint from Spider Hill Prop Works. It is a versatile plastic joint used in conjunction with 1 inch pvc pipe to create body armatures. The new Thrashing Torso also uses a 12-volt motor from Frightprops, another haunted attraction oriented business. Additionally, a plastic halloween skeleton is used. Some modifications are required and this proved to be the most time-intensive part of the build.
A few other refinements have been incorporated into the design. Bungee cord is used instead of springs and clothesline from the hardware store is used instead of steel cable.
All of these changes make the finished mechanism much easier to make, the parts are easier to acquire, and everything is much lighter.
The Breakdown:
Man Hours Required: ~30 hrs.
I spent about a half a day designing the mechanism in Fusion 360 and I estimate another half a day setting up for the 3d printing and cleaning up the parts as they came out of the printer. Only another day was spent assembling the mechanism. Modifying and mounting the plastic skeleton took the better part of two more days, which includes futzing around with clearances and tensioning the bungee cords. Considering how much time the first Thrashing Torso took to build, this is great.
Cost: ~$158 (total)
Plastic Skeleton $40
Fright Props motor $25
Spider Joints (x8) $28
Misc. Components and Fasteners ~$40
ABS Printer Filament Roll $25
Some Thoughts on 3d Printing:
There has been quite a bit of hype about 3d printing over the past few years. 3d printing is incredibly useful but let me come right out and say that it can be a pain in the ass. The technology is getting better and better all the time, but like any fabrication technique, it takes time to master. This is especially true when 3d printing functional mechanisms. In the next post (or three) I am going to discuss 3d printing and its applications to making animatronics, as well as some of the pitfalls you may be able to avoid.
/ Mimi/ 1 Comment
Projects, ThrashingTorso2
animatronics, Halloween props, 3d printing, ThrashingTorso2
Animatronic 3D Printing - "Reveal Yourself!"
Application
Subscribe author
Subscribe
Don't want
10
Article applies to printers:
UP Plus 2Zihua Creative is China's first online educational resource. It contains a huge amount of videos on photography, art, design, music and other areas of creativity that are aimed at stimulating online learning. nine0003
Recently, Zihua Creative collaborated with Goodstein advertising agency, international animation company Pixomondo and 3D printing studio IDEARP to create a creative short film that describes the process of the emergence and development of an idea, called "Unbox yourself" (original "Unbox yourself" - Unbox yourself) . Tiertime's flagship desktop 3D printer, UP Plus 2, was used to create it.
One of the ideologists, the founder of IDEARP, says that the decision to use the UP printer for the project was made due to the high stability and quality of its work. nine0003
Designer Shen Jersey notes: “This car really did a great job of capturing the overall art design of the project. We deliberately used the relatively low precision of the print in order to convey a sense of texture and style to the video.”
It took 11 UP Plus 2 3D printers and 240 hours of work to make a 1 minute video, every second frame was printed and photographed with a digital camera. As a result, 688 figures of various shapes and sizes were obtained. The number and total running time was without a doubt the biggest challenge for Tiertime's machines. The developers note very good performance and high stability during long continuous operation of UP Plus 2 printers. In total, the project took about 42 coils and almost 30 kg of ABS plastic, of which almost half went to support. nine0003
Compared to traditional materials for this kind of animation: clay, fabric, metal, 3D printing allows you to achieve better results in a much shorter time. Each subsequent frame should differ from the previous one by millimeters, and this is easy to achieve with a 3D printer and plastic, unlike other materials.
The developers of the film assure: “With the advent of 3D printing, the anime industry will move to a new round of development. The accuracy of a 3D printer allows the viewer to better feel and understand the idea of the picture, perceive the emotions of the characters and the scenes in which they participate. Also, this innovative method allows you to attract more creative people to the animation, who can create their own characters not only in 2D. “To feel” the fruits of their imagination is very important for them and perfectly motivates them for further
accomplishments.”
Pablo Picasso once said: "Every child is born an artist, the only difficulty is to remain one after leaving childhood. " And 3D printing can help make that happen.
Follow author
Follow
Don't want
10
Article comments
More interesting articles
7 nine0003
Follow author
Follow
Don't want
While it's night outside and I can't sleep, I'll tell you about one more auto-apply...
It...
Read more
1
Subscribe author
Subscribe
Don't want
The glass industry has its own unique criteria for quality control. ..
Read more
258
Subscribe to the author
Subscribe
Don't want
Hello dear community!
In this topic, I would like to deviate a bit from the 'home...
Read more
Read blogs
From bunkhouses to palaces: ten 3D-printed buildings
iPhone-priced garbage houses and palaces printed in a few days. We tell how 3D printing has transformed the construction industry and what modern printers are capable of
Amsterdam Elemental Shelter - Sq. 8 m
In 2015, the Dutch bureau Dus Architects built a tiny house of 8 square meters. m. It is located in the industrial area of Amsterdam, and anyone can rent it. Despite the small area, the shelter has a veranda and a sofa that converts into a double bed. The bathroom, also created on a 3D printer, is taken outside. The shelter was built from bioplastic based on linseed oil. To make a stable house without heavy frames, the engineers designed the walls in the form of a honeycomb. nine0003
Photo: DUS Architects
Urban Retreat is part of a temporary functional housing project. The Dutch authorities hope that 3D printing will help provide housing for victims of natural disasters in the future.
Garbage and Clay Houses - 30 and 60 sqm
Italian company WASP printed a tiny 30 sqm house m, the cost of which was only about $ 1,000. The building received the symbolic name Gaia - in honor of Gaia, the ancient Greek goddess of the Earth, since only natural materials were used in the construction. nine0003
Engineers believe the cost-effective technology can be used to build temporary shelters for victims of natural disasters or refugees. The house became part of the Shambhala Village project, the first settlement in the world where all buildings will be printed.
Photo: WASP
Another WASP project is the futuristic Tecla house created in 2021 with Mario Cucinella Architects. Residential building with an area of 60 sq. m printed in 200 hours.
Photo: dezeen
The company's printer can use both concrete and a biodegradable mixture of clay, straw, rice husks and hydraulic lime as "ink". Construction takes place in two stages: first, the concrete frame of the wall is printed, and then the printer fills its inner layer with clay. The main advantage of the technology that WASP uses is the absence of construction debris. nine0003
Printed house in the suburbs - 37 sq. m
An unusual house in Stupino near Moscow is one of the first projects of Apis Cor, a Boston startup with Russian roots. The construction of the building was completed in the winter of 2017. House of 37 sq. m was built in 20 hours, and its cost was ₽590 thousand. The material sets only at temperatures above 5°C, so the construction site was covered with a tent. At the same time, the finished building can withstand temperatures down to minus 35°C. For construction, an industrial printer weighing 2. 5 tons was used, which allows you to design up to 100 square meters. m of housing per day. nine0003
Unlike most competitors, Apis Cor prints its buildings on site rather than assembling them from prefabricated blocks. The house in Stupino became an advertisement for startup technology: Apis Cor founder Nikita Chen-yun-tai intended to sell printers, not houses. The idea of the Russian startup was successful - even Time wrote about an innovative house in the Moscow region.
Homes for the homeless - 38 and 45 sq. m
Icon is an American robotics startup focused on 3D printing of large-scale objects. For example, together with NASA, they designed a prototype rocket landing pad, and are now planning a project for a printed lunar space station, Olympus. But the company is also engaged in more mundane buildings. nine0003
Together with design firm Logan Architecture, Icon printed six houses for the poor in 2020. Each area is 38 sq. m. For construction, a Vulcan II 3D printer and special concrete were used. All buildings have an equipped kitchen, living room, bedroom and bathroom. The 3D quarter was built on the territory of an already existing community for the former homeless, where more than two hundred people now live.
Photo: Shane Reiner-Roth / The Architect's Newspaper
In Mexico, Icon is partnering with New Story, a foundation that raises donations to build safe, affordable housing for the poor. In 2019th project organizers said they plan to print 50 houses, each of which will have two bedrooms, a bathroom, a kitchen and a living room. The area of Mexican houses is 45 square meters. m.
Photo: Icon
Because 3D-printed houses are built many times faster and cheaper than usual, they can be a lifesaver for the homeless.
"Lotus House" - 60 sq.m. m. It was designed by students of the University of Washington as part of the Solar Decathlon China 2018 competition. The task of the participants was to create an environmentally friendly building that would run on alternative energy sources.
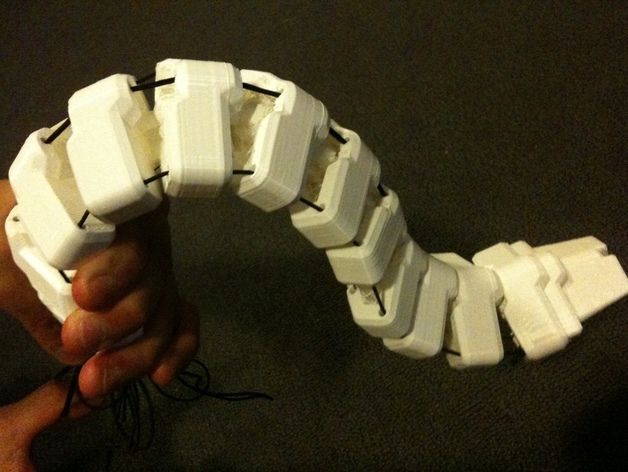
The building itself is only partly 3D printed. On it, engineers made molds for casting concrete walls. The advantage of this approach is that the printed designs can be used at least a hundred times. In conventional construction, wooden molds are used, which wear out after only two castings.
The building itself was made in the shape of a lotus - the designers said that they wanted to emphasize the beauty and delicacy of Chinese culture in the design.
Photo: Liam Otten / Archinect
Germany's first two-story printed house - 80 sq. m
A two-story villa printed in North Rhine-Westphalia is an example of the use of 3D printing in the construction of luxury housing with custom design. The living area of the building was 80 sq. The 3D villa is a joint project of MENSE-KORTE ingenieure+architekten and developer PERI GmbH.
Photo: Mense-Korte
The villa was built using a unique BOD2 3D printer that can print pipes. This feature gives designers a free hand: complex engineering solutions on BOD2 can be completed faster and cheaper than with standard construction. ArchDaily writes that an innovative printer used in the construction of a German villa can print 1 sq. m wall in just five minutes. nine0003
Curve Appeal Ecosystem House - 240 sq. m
Another example of conceptual 3D printing is the Curve Appeal 240 sq. The building belongs to WATG Urban Architecture Studio. The printing of the building was completed in 2020.
Construction lasted three years. The building project was created back in 2016, and then won first place in The Freeform Home Design Challenge. Designers received $8,000 from the organizers to implement the concept.
Photo: WATG
Curve Appeal is made from 28 printed panels. The unusual design maintains the microclimate of the house: according to the designers, the temperature inside the building does not depend on the weather outside.