How accurate is a 3d body scanner
Weight Scales vs. 3D Body Scanning for Measuring Success
Gym owners have a challenge on their hands: how to measure the success of their weight loss programs and determine whether they are effective. The compelling idea is to use a modern approach that will give a more precise measurement of body composition rather than just weight loss or gain alone.
A traditional form of measurement for this purpose has been using weight scales, but weight scales have limitations. While these two methods can deliver valuable information about the progress of a fitness program, studies show that they come with different sets of advantages and disadvantages.
Keep reading to learn which one is right for your clients.
The Use of Weight ScalesThe popularity of weight scales to measure body weight has been on a steady decline. As being overweight is now being recognized as having health risks, tools that can help accurately monitor body fat composition have become widely embraced by fitness professionals, personal trainers, and their clients.
The downside of weight scales is that they just give information on how much a person weighs. They do not provide data on body fat percentage. Thus, while weight scales can inform an individual whether they are losing or gaining weight, they cannot be used to monitor the effectiveness of fat loss programs.
In addition, traditional weight scales do not provide a measurement for fat distribution.
While weight scales are suitable for monitoring the amount of weight lost, they give no information on the types and amounts of fat that were actually reduced.
Benefits of 3D Body Scanning
For these reasons, more fitness professionals and health clubs across the world have been using 3D body scanning technology to monitor their client's progress.
3D body scanning is a scientifically proven method that helps measure body composition, including weight, lean muscle mass, and fat. This method can also help monitor changes in body fat composition over time.
This form of body composition measuring is considered the gold standard in the fitness community. It is also considered to be the most accurate form of measuring, with a margin of error of less than 2%.
A 3D body scanner works by taking horizontal, cross-sectional images of a person's body. It can then determine where fat is located and how much there is. The technology can show changes in more detail than weight scales since it enhances the accuracy by about 5 times compared to traditional methods.
This method gives more information on what types of tissue are more prevalent in an individual, especially after some time has passed following the initial scan when changes in lifestyle habits become evident.
For example, if an individual had just started working out, weight scales would not be able to give any indication that muscle mass was increasing or the fat was being lost. 3D body scanning, on the other hand, can provide this information.
Accuracy of 3D Body ScanningThe accuracy of 3D body scanning can be attributed to the visual representation it offers. It shows not only weight loss but also the changes that are happening in various parts of the body due to the effects of fat reduction or muscle-building programs.
For example, a 3D body scan would show an increase in measurements for biceps, chest size, and legs.
Additionally, it could measure changes in other areas, including waist circumference, because this indicates shifting fat distribution, indicating an improved health condition.
Leverage Body MeasurementsIn comparison to weight scales, 3D body scanning technology is a much more effective way of tracking fat loss and gaining muscle.
When taken by a professional in a gym setting, this process creates an accurate representation of one's body weight and composition.
In fact, the results from this assessment can be used as a guide when designing workout plans or personalized programs based on what the client wants to achieve with their exercise routine.
Why 3D Body Scanning Is Becoming So Popular Among Fitness Professionals
The popularity of 3D body scanning is mainly due to the following:
- It offers precise and accurate measurements, unlike weight scales.
- It allows measuring goals like waist circumference reduction, lean muscle gain, etc.
- Personalized plans can be developed based on the client's goals.
3D body scanning technology captures more than just one's weight; it provides information that will help determine the effectiveness of a fitness program and how clients progress under these programs.
Thus, this approach offers several benefits such as:
- ability to predict future obesity issues
- identification of problem areas which aids in prioritizing workouts
- understanding of lifestyle patterns for better weight management decisions
- identifying possible health risks early so steps can be taken to reduce them.
Some experts believe that 3D body scanning technology is the future of fitness assessment. It's a no-brainer why professionals prefer this method to weight scales for helping their clients reach their goals and make healthier lifestyle choices.
3D Body Scanning vs. Weight Scales: Which is Better?
No doubt, 3D body scanning technology has proven to be more accurate than weight loss scales in measuring various aspects of one's life, including fat composition and lean muscle gain.
However, if you're still not convinced that this method can provide better results, here are several points to consider about why it might be time to switch from weight scales to 3D body scanning:
-Clients receive personalized plans based on their health, lifestyle and preferences instead of following the same weight loss program as everyone else.
- The assessment is non-intrusive because it uses infrared light technology (the same light in a t.v. remote control) to scan the body.
- 3D body scanners allow capturing measurements quickly and efficiently, so clients don't have to wait around long before receiving their results.
While both weight scales and 3D body scanning can provide valuable information about one's health status, this latest method of assessing fitness progress offers more benefits than just reading numbers on a scale which makes it very useful in helping professionals design programs that are efficient for their clients who are serious about losing weight and gaining muscle mass.
Here are some tips to consider when using 3D body scanners for measuring your clients' progress:
- Make sure you explain the process clearly beforehand, so clients know what to expect.
- Allow time for them to change into workout clothing they will be wearing during their assessment.
- Ensure that all of their clothes are form-fitting since this makes it easier to analyze the accurate results.
- Explain what each measurement means and how it can help reach their weight loss goals more efficiently.
Remember, 3D body scanners are only helpful if they're used correctly and in the right direction.
Tips for Communicating 3D Body Scanning Results With Your Clients
There are many benefits to communicating 3D body scanning results with your clients. For instance, you can encourage them to reach their goals more efficiently by showing them the following:
- Areas in which they need to work harder through weight training or cardio exercises to improve their overall fitness levels.
- How much progress they have made since starting their program.
- How well you know them and how results might be different if they were working with someone else who was not as invested in their health.
Before giving out results, explain that these numbers are only estimates based on the technology used during their assessment since no two bodies are alike. When offering constructive criticism, use wording like saying "these measurements indicate that..." rather than "you need to do this or that."
In the end, 3D body scanners are a great way for fitness professionals to help their clients make better decisions in reaching their weight loss and muscle gain goals. With the right direction and education in using these machines, you can expect them to bring more positive outcomes in your sessions together.
To get a more reliable body composition measurement, people must turn to 3D body scanning technology, which goes beyond checking weight loss progress.
3D body scanning is seen as an upgrade from weight scale measurements because it is more precise in assessing changes in fitness levels over time. While both tools offer accountability and progress reports, which motivate people to continue working toward their goals, fitness professionals everywhere are already taking notice of how 3D body scanner technology can help their clients improve physical appearance and overall wellness.
At its core, 3D body scanning technology is an efficient tool that should be incorporated into your gym's fitness assessment process because it not only helps monitor changes in physique but also assesses specific areas of concern clients may have.
3D Body Scanners vs. Body Fat Calipers Which is Better
One of the best ways to have honest and productive conversations about a client's overall health is to show them an analysis of their body composition. This analysis determines how much of their body is fat and how much is muscle. The results of these analyses can be used to create personalized fitness plans that drive the results that your clients want to see.
But how do you go about acquiring a body composition analysis? The two most popular and effective tools to do this are body fat calipers and 3D body scanners.
The battle of 3D body scanners vs. body fat calipers can be a tricky one to wade through. But once you understand what each instrument actually is, how they work, and the pros and cons of each, you can make an informed decision about which instrument is right for your gym.
What Are Body Fat Calipers?
A body fat caliper, or skinfold caliper, is a device that measures the thickness of subcutaneous fat. That's the fat that lays just beneath the skin.
Measurements are taken at three to seven sites on the body. The three-site method is the most popular. These sites differ slightly between men and women.
For a three-site measurement in women, measurements are taken at the triceps, suprailiac (also called the iliac crest), and the front of the thigh. For a seven-site measurement, the chest, areas near the armpit, and areas beneath the shoulder blade are also measured.
For a three-site measurement in men, measurements are taken at the chest, abdomen, and front thigh. For a seven-site measurement, additional measurements are taken at the triceps, the areas beneath the scapula, the areas near the armpit, and the areas beneath the shoulder blade.
After the measurements are taken, the results are plugged into an equation or calculator. The final read-out provides a relatively accurate estimate of an individual's total amount of body fat.
This process must be completed by a trained professional in order to ensure accuracy. There are many variables that come into play when taking skinfold measurements. The person administering the test must know how to do it properly.
Pros
Using body fat calipers offers people a much better assessment of their overall health than a scale or BMI results. They are also a very reliable way of measuring body fat change over time.
This is incredibly useful for people who are embarking on fitness journies and need to see numerical results of their efforts. If a trainer can show someone that their body fat numbers are going down, they will be more motivated to continue working out.
Measuring the thickness of subcutaneous fat is particularly useful for bodybuilders and people who are exercising to achieve a particular body image. Fat that lies directly beneath the skin is typically the type that people want to trim down.
Skinfold calipers are also relatively inexpensive and portable. They typically cost between $100 and $500, depending on the model.
Cons
Body fat calipers only measure an individual's subcutaneous fat. They are not able to provide a total assessment of their body composition.
What's more, they are only able to make a prediction of body fat. This prediction heavily relies on the person's age. The three-site Jackson-Pollock Equation makes inherent assumptions about the effect age may have on body density.
Body fat calipers' accuracy also has a 5% error rate. The results are heavily influenced by the person administering the readings. That person must be extremely precise when taking the measurements
Each measurement site must be located exactly and marked with an X to ensure proper jaw placement. You can't eyeball the location. The person administering the test must use a tape measurer to locate each site.
This is only the first hurdle. There are also variances between how the jaws of the caliper must be placed on each skinfold.
For example, when pinching the shoulder blade site, the upper jaw must be placed directly on the X mark. With the tricep pinch, both jaws must be placed on either side of the X. These differences may seem small, but they can drastically affect the final results.
The CDC's guidelines for using body fat calipers specify that readings can only be taken after pinching the skin, holding it, and waiting three seconds. If the person administering the test doesn't follow these guidelines exactly, it can further skew the results.
Caliper equations also make a lot of assumptions about body fat distribution. Particularly, how much of the body fat is made up of subcutaneous fat and how much is comprised of visceral fat (the fat that lies between your abdominal organs).
With the rise in obesity, these assumptions have become increasingly inaccurate. This is particularly true for people who are overweight.
What Are 3D Body Scanners?
As the name would suggest, 3D body scanners are a new technology that scan's a person's entire body in a 360-degree view. It uses those scans to create a complete 3D image of the person. This image is used to analyze their body composition.
To use a 3D body scanner, a person steps on the rotating plate and holds still for 35-45 seconds. The body scanner uses digital tape measures to record body mass and measure body fat composition.
The scanner creates a 3D avatar of the person that they can use to see their exact measurements. It also displays metrics such as body fat percentage and lean muscle mass. These readings are used to create a targeted workout and diet plan.
Repeated body scans allow clients to see their physical development in real-time. It analyzes the body's entire composition to provide a holistic look at a person's physical health.
Pros
A 3D body scanner's accuracy is significantly higher than that of body fat calipers. They can calculate total body composition with an error rate of only .5%. This is drastically lower than skinfold calipers' rate of error.
Body scanners are also significantly less invasive than body fat calipers. To have an assessment done with calipers, clients have to strip down to their underwear and let a professional circle their body and pinch skinfolds. For customers who are self-conscious about their bodies, this can be an incredibly intimidating process.
3D body scanners can be used without clients stripping down. Form-fitting clothing works best for accuracy and helps customers feel more comfortable with the process.
Our body scanners also have a self-scanning mode. This allows clients to scan themselves without a professional in the room with them. It allows an extra level of privacy for those who desire it.
Once the scan has been completed, the client is then presented with an interactive 3D representation of their body. Coaches can rotate, pan, and zoom to view the body from any angle. This is a more engaging and visual tool to use when having conversations with clients about their fitness.
Body scanners also tell users the exact type and location of their body fat. The system can illustrate how fitness and nutrition programs impact their overall body composition. Trainers can use these results to build customized workout and nutrition plans to target specific areas where body fat is present.
Our body scanners are also lightweight and portable. You can pack them up and take them to other locations. This frees you from the restriction of operating in a single facility and allows you to perform fitness assessments wherever you want.
Cons
When it comes to body scanner pros and cons, the price point tends to be the biggest issue for fitness center owners. 3D body scanners can be a costly investment. It's up to you to decide whether that investment is worth it for your fitness center.
Many gym owners chose to charge clients for body scans. Typically, the options are to have a body scan done individually, or have it included in a personal training package. The price can turn some clients away, particularly those who don't want to spend more than they have to at the gym.
Analyzing the readout of a body scanner also requires training. You need a coach who understands what the numbers mean and how to communicate the scanner's information to your clients. Fortunately, this training is typically very intuitive and easy to complete.
3D Body Scanners vs. Body Fat Calipers
If you are looking to provide body composition analyses to your clients, 3D body scanners or body fat calipers are the two best options.
Skinfold calipers are a less expensive option but rely heavily on outdated assumptions to make their equations work. They must also be operated with extreme precision in order to ensure accurate results.
3D body scanners come at a significantly higher price point but are much more accurate than body fat calipers. They provide a more interactive and holistic look at an individual's overall body composition. The results of 3D body scans can also be used to customize fitness plans for your clients.
In the battle of 3D body scanners vs. body fat calipers, you're the one who gets to decide the victor. At the end of the day, you have to make the decision about which instrument is right for your fitness club.
Now that you know how each instrument works, as well as the pros and cons of each, you can make the best and most informed decision for your gym. For more tips on running your fitness center, check out some of our other articles today.
how to quickly create prostheses and other unique products
Reverse engineering
Implementation stories
Medicine
Author: Aleksey Chekhovich
Author: Aleksey Chekhovich
Video: Real-time 3D Face Scan | Order a free test scan | 3D scanner helps victims | 3D scanning of the human body in great detail
Creating prostheses using 3D technologies: the era of new possibilities
As technology improves and becomes more accessible, there are new opportunities to solve the most complex medical problems. A team of researchers from the company Chabloz Orthopedie (France) managed to create a unique and truly revolutionary prosthesis.
Chabloz Orthopédie worked with Denis Gauthier, who had his forearm amputated. First, the experts performed a 3D scan of the patient's healthy arm using a peel 3d scanner to obtain its mirror image. This was done so that the designed product ideally repeated the proportions of a healthy limb. The rest of the amputated arm was also scanned to achieve a comfortable and ergonomic fit for the prosthesis.
Denis Gaultier with finished prosthesis
The team then proceeded to design a CAD model and develop a myoelectric prosthesis. Batteries, sensor cables and an artificial hand were integrated with the fabricated forearm. The prosthesis itself was designed in CAD and printed on a 3D printer. HP Jet Fusion technology was used to print various components of the forearm. After manufacturing, all parts were finished and painted.
The use of 3D scanning and 3D printing guarantees not only the correct fit of the fixture, but also gives complete freedom of movement. A new approach to prosthesis design allows professionals to develop solutions that are lightweight and highly customizable. Did you know that 3D printed parts are 20% lighter than their carbon or fiberglass counterparts? Such products also have the necessary rigidity, hardness and durability.
Later, this innovative prosthesis was combined with the BeBionic hand, one of the most advanced bionic limbs, and a state-of-the-art myoelectric forearm and hand was custom-made. Gauthier's case is a great example of the innovative use of 3D measurement and 3D printing technologies.
The video shows the complete process of digitizing the face and ears using the Creaform Go!SCAN 20 portable 3D scanner (its analogue in white peel 2 is now being produced). This solution provides a detailed digital model for use in areas such as plastic and reconstructive surgery, in particular, facial prosthetics.
Order a 3D test scan for free!
3D scanner helps victims
Unfortunately, tragedies inevitably occur around the world, and those affected need help. But, fortunately, there are organizations such as Médecins Sans Frontières (Doctors Without Borders) that do their best to provide them with the necessary treatment and care. Since 2016, the organization has been working tirelessly to solve the problem of providing prostheses to those in need around the world. The goal is to help amputees regain independence. The solutions that are used in this case are 3D technologies.
Upon completion of the medical examination of the patient, doctors determine his needs and expectations. Using the peel 3d scanner, with minimal discomfort for the victim, a high-precision digital model of the injured limb is created. Compared to traditional impression making, 3D scanning is significantly faster and does not require contact. The result of the 3D scan is then transferred to the virtual sleeve and prosthesis design software. The developed component is made on a 3D printer and installed on the patient's limb. If necessary, during the installation process, the prosthesis and sleeve are finalized. After three months of use, the patient is invited to evaluate the comfort of the prosthesis.
MSF has also developed a similar procedure to create compression masks for burn patients. Here, the use of non-contact technology also provides significant advantages over traditional plaster bandages, not only making the procedure less painful for the patient, but also speeding it up, allowing for a much larger number of people in needy countries to be treated.
Physiotherapist Pierre Moreau scans a patient with head burns. Then, based on the scan, a transparent pressure therapy mask is created / Photo: Elisa Oddone, Al Jazeera
Pierre Moreau, a physiotherapist from Médecins Sans Frontières, says: “The purpose of the 3D project is to help patients in need of special rehabilitation care. We launched this project in Amman in 2017, where we started providing upper limb amputees with 3D printed prostheses. But simply printing a prosthesis is not enough - we try to understand the needs of the victims, find individual solutions and keep them in their new position for as long as possible. We are assisted by an interdisciplinary team of rehabilitation workers and engineers. Then our specialists helped more than 30 patients in Jordan.
In 2018, we began to use the technology in another direction - for patients with burns, especially on the face and neck. Skin complications are a very serious problem for burn victims. Hypertrophic scars may form, and pressotherapy is needed. This requires transparent masks, but they are quite difficult to produce on site. Therefore, we started to explore 3D scanning, 3D printing and computer modeling in an attempt to help our team in the production of these devices for patients who so desperately need them. Now we provide more than 50 transparent facial orthoses.
When I think about this project, I always remember one story that demonstrates its development. In 2017 in Jordan, we had a small patient with burns and an amputation - she had no arm, and the condition of her remaining part was too complex to develop a prosthesis. Then we couldn't help her. But she came back the following year and we were finally able to make a prosthesis for her. For the first time, she was able to use her hand. This is one of our best memories of the project and a measure of its success.”
3D scanning of the human body in great detail
There are already more than 7.5 billion people on Earth, and although some are very similar to each other, there are no completely identical people. With such a variety of faces, it is not at all surprising that in the process of evolution the human brain became masterfully recognizing the smallest details that help to distinguish them. To get as close as possible to the original, the 3D scan of the statue must be extremely accurate and have a high geometric resolution.
3D copies: 2013 Kinect scan (left figure) and peel 3d (right figure)
To improve the quality of scanning, the Canadian company USIMM has begun using peel 3d. The company specializes in the machining of non-metallic materials and is constantly involved in artistic projects. The main goal was to show the evolution of CNC machining by comparing the results of a 3D version of one employee made a few years ago with current results.
According to USIMM's Leia Lepage, scanning a living person is not an easy task: “Scanners are usually quite sensitive to the smallest movements, even if it's just breathing. Scanning a person is very difficult.” In order to accomplish such an extraordinary task, the USIMM team needed a 3D scanner that was immune to certain movements - but at the same time had high resolution and accuracy. Peel 3d possesses such qualities: a resolution of up to 0.5 mm and a volumetric accuracy of 0.5 mm/m.
The team scanned the same employee in the same pose as they did a few years ago. The resulting 3D scan data was sent to a five-axis CNC machine, and then a full-size replica of a person was created from polystyrene. The results were incredible.
The scan results obtained earlier by the Skanect device did not stand next to the peel 3d results. “The difference between the past and current results of the project is enormous,” commented Lea Lepage. The new copy turned out to be much more realistic and more accurately conveyed the original.
Materials provided by Creaform. Screensaver photo © Elisa Oddone, Al Jazeera
Article published on 12/08/2020, updated on 03/03/2022
All about 3D scanners: from varieties to applications
The 3D scanner is a special device that analyzes a specific physical object or space in order to obtain data about the shape of an object and, if possible, its appearance (for example , about color). The collected data is then used to create a digital three-dimensional model of this object.
Create 3D-scanner allows several technologies at once, differing from each other in certain advantages, disadvantages, as well as cost. In addition, there are some restrictions on the objects that can be digitized. In particular, there are difficulties with objects that are shiny, transparent or have mirror surfaces.
Don't forget that 3D data collection is also important for other applications. So, they are needed in the entertainment industry to create films and video games. Also, this technology is in demand in industrial design, orthopedics and prosthetics, reverse engineering, prototyping, as well as for quality control, inspection and documentation of cultural artifacts.
Functionality
The purpose of the 3D Scanner is to create a point cloud of geometric patterns on the surface of an object. These points can then be extrapolated to recreate the shape of the object (a process called reconstruction). If color data were obtained, then the color of the reconstructed surface can also be determined.
The 3D scanners are a bit like regular cameras. In particular, they have a cone-shaped field of view, and they can only receive information from surfaces that have not been darkened. The differences between these two devices is that the camera transmits only information about the color of the surface that fell into its field of view, but The 3D scanner collects information about distances on a surface that is also in its field of view. Thus, the "picture" obtained using the 3D scanner describes the distance to the surface at each point in the image. This allows you to determine the position of each point in the picture in 3 planes at once.
In most cases, one scan is not enough to create a complete model of the object. Several such operations are required. As a rule, a decent number of scans from different directions will be needed in order to obtain information about all sides of the object. All scan results must be normalized to a common coordinate system, a process called image referencing or alignment, before a complete model is created. This whole procedure from a simple map with distances to a full-fledged model is called a 3D scanning pipeline.
Technology
There are several technologies for digitally scanning a mold and creating a 3D model of a object. However, a special classification has been developed that divides 3D scanners into 2 types: contact and non-contact. In turn, non-contact 3D scanners can be divided into 2 more groups - active and passive. Several technologies can fall under these categories of scanning devices.
Coordinated-measuring machine with two fixed mutually perpendicular measuring hands
Contact 3D scanners
Contact 3D-scanners 3D-scanners 3D-scanners 3D-scanners 3D-scanners 3D-scanners 3D 3D-scanners 3D 3D-scanners study (probe) The object is directly through the physical contact, while the subject itself is in the subject itself in the subject itself is the subject itself in the subject on a precision surface plate, ground and polished to a certain degree of surface roughness. If the scanned object is uneven or cannot lie stably on a horizontal surface, then a special vise will hold it.
The scanner mechanism comes in three different forms:
- Carriage with a fixed measuring arm positioned perpendicularly, and measurement along the axes occurs while the arm slides along the carriage. This system is optimal for flat or regular convex curved surfaces.
- Fixed component manipulator with high precision angle sensors. The location of the end of the measuring arm entails complex mathematical calculations regarding the angle of rotation of the wrist joint, as well as the angle of rotation of each of the joints of the arm. This mechanism is ideal for probing recesses or interior spaces with a small inlet.
- Simultaneous use of the previous two methods. For example, a manipulator can be combined with a carriage, which allows you to get 3D data from large objects that have internal cavities or overlapping surfaces.
CMM (coordinate measuring machine) is a prime example of the contact 3D scanner . They are used mainly in manufacturing and can be ultra-precise. The disadvantages of CMM include the need for direct contact with the surface of the object. Therefore, it is possible to change the object or even damage it. This is very important if thin or valuable items such as historical artifacts are being scanned. Another disadvantage of CMM over other scanning methods is slowness. Moving the measuring arm with the probe in place can be very slow. The fastest result of CMM operation does not exceed a few hundred hertz. At the same time, optical systems, for example, a laser scanner, can operate from 10 to 500 kHz.
Another example is hand-held measuring probes used to digitize clay models for computer animation.
The Lidar device is used to scan buildings, rocks, etc., which makes it possible to create 3D models of them. The Lidar laser beam can be used in a wide range: its head rotates horizontally, and the mirror moves vertically. The laser beam itself is used to measure the distance to the first object in its path.
Non-contact active scanners
Active scanners use certain types of radiation or just light and scan an object through the reflection of light or the passage of radiation through an object or medium. These devices use light, ultrasound, or x-rays.
Time-of-Flight Scanners
Time-of-Flight Laser Scanner The 3D scanner is an active scanner that uses a laser beam to examine an object. This type of scanner is based on a time-of-flight laser range finder. In turn, the laser rangefinder determines the distance to the surface of the object, based on the time of flight of the laser back and forth. The laser itself is used to create a pulse of light, while the detector measures the time until the light is reflected. Given that the speed of light (c) is a constant value, knowing the time of flight of the beam back and forth, you can determine the distance over which the light has moved, it will be twice the distance between the scanner and the surface of the object. If (t) is the round-trip flight time of the laser beam, then the distance will be (c*t\2). Laser beam time-of-flight accuracy of the 3D scanner depends on how accurately we can measure the time itself (t): 3.3 picoseconds (approximately) is needed for the laser to travel 1 millimeter.
The laser distance meter determines the distance of only one point in a given direction. Therefore, the device scans its entire field of view in separate points at a time, while changing the direction of scanning. You can change the direction of the laser rangefinder either by rotating the device itself, or using a system of rotating mirrors. The latter method is often used, because it is much faster, more accurate, and also easier to handle. For example, time-of-flight 3D scanners can measure distance from 10,000 to 100,000 points in one second.
TOF devices are also available in 2D configuration. Basically, this applies to time-of-flight cameras. Triangulation scanners Two positions of the object are shown.
A point cloud is created using triangulation and a laser stripe.
Triangulation laser scanners 3D scanners are also active scanners that use a laser beam to probe an object. Like the time-of-flight 3D scanners, triangulation devices send a laser to the scanned object, and a separate camera fixes the location of the point where the laser hit. Depending on how far the laser travels across the surface, the dot appears at different locations in the camera's field of view. This technology is called triangulation because the laser dot, the camera and the laser emitter itself form a kind of triangle. The length of one side of this triangle is known - the distance between the camera and the laser emitter. The angle of the laser emitter is also known. But the camera angle can be determined by the location of the laser dot in the field of view of the camera. These 3 indicators completely determine the shape and size of the triangle and indicate the location of the corner of the laser point. In most cases, to speed up the process of obtaining data, a laser strip is used instead of a laser dot. Thus, the National Research Council of Canada was among the first scientific organizations that developed the basics of triangulation laser scanning technology back in 1978 year.
Advantages and disadvantages of
scanners Both time-of-flight and triangulation scanners have their own strengths and weaknesses, which determines their choice for each specific situation. The advantage of time-of-flight devices is that they are optimally suited for operation over very long distances up to several kilometers. They are ideal for scanning buildings or geographic features. At the same time, their disadvantages include measurement accuracy. After all, the speed of light is quite high, so when calculating the time it takes for the beam to overcome the distance to and from the object, some flaws (up to 1 mm) are possible. And this makes the scan results approximate.
As for triangulation rangefinders, the situation is exactly the opposite. Their range is only a few meters, but the accuracy is relatively high. Such devices can measure distance with an accuracy of tens of micrometers.
The study of the edge of an object negatively affects the accuracy of the TOF scanners. The laser pulse is sent one, and is reflected from two places at once. The coordinates are calculated based on the position of the scanner itself, and the average value of the two reflections of the laser beam is taken. This causes the point to be defined in the wrong place. When using scanners with high resolution, the chances that the laser beam hits the exact edge of the object increase, but noise will appear behind the edge, which will negatively affect the scan results. Scanners with a small beam can solve the edge scanning problem, but they have limited range, so the beam width will exceed the distance. There is also special software that allows the scanner to perceive only the first reflection of the beam, while ignoring the second.
At 10,000 dots per second, low resolution scanners can do the job within seconds. But for scanners with high resolution, you need to do several million operations, which will take minutes. It should be borne in mind that the data may be distorted if the object or the scanner moves. So, each point is fixed at a certain point in time in a certain place. If the object or scanner moves in space, then the scan results will be false. That's why it's so important to mount both the object and the scanner on a fixed platform and keep the possibility of vibration to a minimum. Therefore, scanning objects in motion is practically impossible. Recently, however, there has been active research on how to compensate for the effect of vibration on data corruption.
It is also worth considering that when scanning in one position for a long time, a slight movement of the scanner may occur due to temperature changes. If the scanner is mounted on a tripod and one side of the scanner is exposed to strong sunlight, then the tripod will expand and the scan data will gradually distort from one side to the other. However, some laser scanners have built-in compensators that counteract any movement of the scanner during operation.
Conoscopic holography
In the conoscopic system, a laser beam is projected onto the surface of an object, after which the beam is reflected along the same path, but through a conoscopic crystal, and is projected onto a CCD (charge-coupled device). The result is a diffraction pattern from which frequency analysis can be used to determine the distance to the surface of an object. The main advantage of conoscopic holography is that only one beam path is needed to measure the distance, which makes it possible to determine, for example, the depth of a small hole.
Handheld laser scanners
Handheld laser scanners create a 3D image using the triangulation principle described above. A laser beam or stripe is projected onto an object from a hand-held emitter, and a sensor (often a CCD or position-sensitive detector) measures the distance to the surface of the object. The data is collected relative to the internal coordinate system and therefore, to obtain results, if the scanner is in motion, the position of the device must be accurately determined. This can be done using basic features on the scanned surface (adhesive reflective elements or natural features) or using the external tracking method. The latter method often takes the form of a laser tracker (providing a position sensor) with a built-in camera (to determine the orientation of the scanner). You can also use photogrammetry, provided by 3 cameras, which gives the scanner six degrees of freedom (the ability to make geometric movements in three-dimensional space). Both techniques typically use infrared LEDs connected to the scanner. They are observed by cameras through filters that ensure the stability of ambient lighting (reflecting light from different surfaces).
Scan data is collected by a computer and recorded as points in 3D space, which after processing are converted into a triangulated grid. The computer-aided design system then creates a model using a non-uniform rational B-spline, NURBS (a special mathematical form for creating curves and surfaces). Handheld laser scanners can combine this data with passive visible light sensors that capture surface texture and color to create or reverse engineer a complete 3D Models .
Structured light
Structured light 3D scanners are a projection of a light grid directly onto an object, the deformation of this pattern is a model of the scanned object. The grid is projected onto the object using a liquid crystal projector or other constant light source. A camera positioned just to the side of the projector captures the shape of the network and calculates the distance to each point in the field of view.
Structured light scanning is still an active area of research, with quite a few research papers devoted to it each year. Ideal maps are also recognized as useful as structured light patterns that can solve matching problems and allow errors to be corrected as well as detected.
The advantage of the Structured Light 3D Scanners is their speed and accuracy. Instead of scanning one point at a time, structured scanners scan several points at the same time or the entire field of view at once. Scanning the entire field of view takes a fraction of a second, and the generated profiles are more accurate than laser triangulations. This completely solves the problem of data corruption caused by motion. In addition, some existing systems are capable of scanning even moving objects in real time. For example, the VisionMaster, a 3D scanning system, has a 5-megapixel camera, so each frame contains 5 million dots.
Real-time scanners use digital edge projection and a phase-shifting technique (one of the techniques for applying structured light) to capture, reconstruct, and create a high-density computer model of dynamically changing objects (such as facial expressions) at 40 frames per second. A new type of scanner has recently been created. Various models can be used in this system. The frame rate for capturing and processing data reaches 120 frames per second. This scanner can also process individual surfaces. For example, 2 moving hands. Using the binary defocusing method, the shooting speed can reach hundreds or even thousands of frames per second.
Modulated light
When using 3D scanners based on modulated light, the light beam directed at the object is constantly changing. Often the change of light passes along a sinusoid. The camera captures the reflected light and determines the distance to the object, taking into account the path that the light beam has traveled. Modulated light allows the scanner to ignore light from sources other than the laser, thus avoiding interference.
Volumetric techniques
Medicine
Computed tomography (CT) is a special medical imaging technique that creates a series of three-dimensional images of an object, a large three-dimensional image of the internal space. Magnetic resonance imaging works on a similar principle - another imaging technique in medicine, which is distinguished by a more contrast image of the soft tissues of the body than CT. Therefore, MRI is used to scan the brain, the musculoskeletal system, the cardiovascular system, and to search for oncology. These techniques produce volumetric voxel models that can be rendered, modified, and transformed into a traditional 3D surface using isosurface extraction algorithms.
Production
Although MRI, CT or microtomography are more widely used in medicine, they are also actively used in other areas to obtain a digital model of an object and its environment. This is important, for example, for non-destructive testing of materials, reverse engineering or the study of biological and paleontological samples.
Non-contact passive scanners
Passive scanners do not emit light, instead they use reflected light from the surrounding area. Most scanners of this type are designed to detect visible light, which is the most accessible form of ambient radiation. Other types of radiation, such as infrared, may also be involved. Passive scanning methods are relatively cheap, because in most cases they do not need special equipment, a conventional digital camera is enough.
Stereoscopic systems involve the use of 2 video cameras located in different places, but in the same direction. By analyzing the differences in the images of each camera, you can determine the distance to each point in the image. This method is similar in principle to human stereoscopic vision.
Photometric systems typically use a single camera that captures multiple frames in all lighting conditions. These methods attempt to transform the object model in order to reconstruct the surface for each pixel.
Silhouette techniques use contours from successive photographs of a three-dimensional object against a contrasting background. These silhouettes are extruded and transformed to get the visible skin of the object. However, this method does not allow you to scan the recesses in the object (for example, the inner cavity of the bowl).
There are other methods that are based on the fact that the user himself discovers and identifies some features and shapes of the object, based on many different images of the object, which allow you to create an approximate model of this object. Such methods can be used to quickly create a three-dimensional model of objects of simple shapes, for example, a building. You can do this using one of the software applications: D-Sculptor, iModeller, Autodesk ImageModeler or PhotoModeler.
This 3D scan is based on the principles of photogrammetry. In addition, this technique is in some ways similar to panoramic photography, except that the photographs of the object are taken in three-dimensional space. Thus, it is possible to copy the object itself, rather than taking a series of photos from one point in three-dimensional space, which would lead to the reconstruction of the object's environment.
Reconstruction
From point clouds
The point clouds generated by the 3D Scanners can be used directly for measurement or visualization in architecture and engineering.
However, most applications use non-homogeneous rational B-spline, NURBS, or editable CAD models (also known as solid models) instead of polygonal 3D models. shapes curved surfaces consist of many small flat surfaces with edges (a striking example is a ball in discotheques). Polygonal models are very in demand for visualization in the field of CAM - an automated system for technological preparation of production (for example, mechanical processing). At the same time, such models are quite « heavy" (accommodate a large amount of data) and are quite difficult to edit in this format. Reconstruction into a polygonal model involves searching and combining neighboring points with straight lines until a continuous surface is formed. For this, you can use a number of paid and free programs (MeshLab, Kubit PointCloud for Au toCAD, 3D JRC Reconstructor, ImageModel, PolyWorks, Rapidform, Geomagic, Imageware, Rhino 3D, etc.).
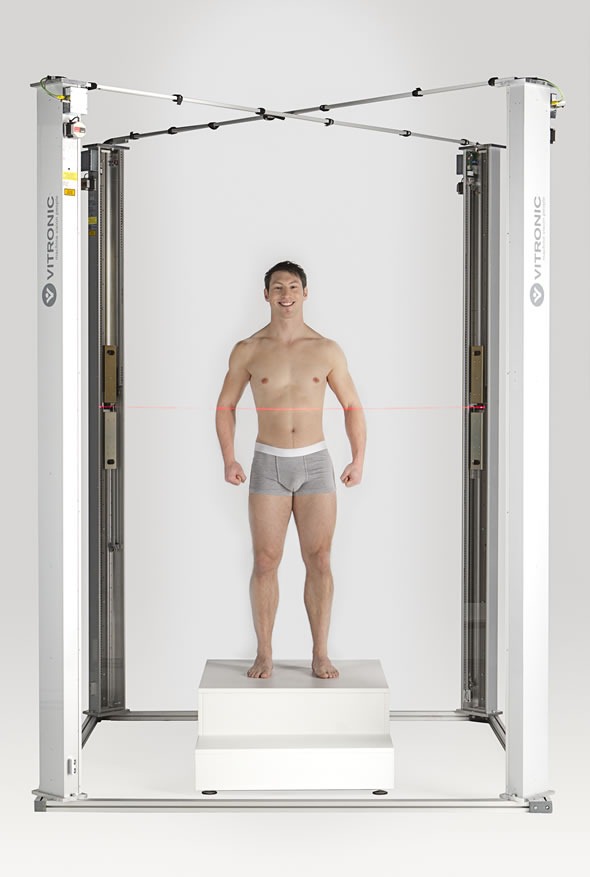
These CAD models don't just describe the shell or shape of an object, but they also enable design intent (ie, critical features and their relationship to other features). An example of design intent that is not expressed in form would be the ribbed bolts of a brake drum, which should be concentric with the hole in the center of the drum. This nuance determines the sequence and method of creating a CAD model, so the engineer, taking into account these features, will develop bolts tied not to the outer diameter, but, on the contrary, to the center. Thus, to create such a CAD model, you need to correlate the shape of the object with the design intent.
There are several approaches to get a parametric CAD model. Some involve only exporting a NURBS surface, leaving the CAD engineer to complete the modeling (Geomagic, Imageware, Rhino 3D). Others use the scan data to create an editable and verifiable function model that can be fully imported into CAD with an intact fully functional tree, providing a complete fusion of shape and design intent of the CAD model (Geomagic, Rapidform). However, other CAD applications are powerful enough to manipulate a limited number of points or polygonal models in a CAD environment (CATIA, AutoCAD, Revit).
From 2D
Their peculiarity is that the areas on which air is displayed, or bones with a high density are made transparent, and the sections are superimposed in a free alignment interval. The outer ring of biomaterial surrounding the brain is made up of the soft tissues of the skin and muscles on the outside of the skull. All sections are made on a black background. Since they are simple 2D images, when added one-to-one when viewed, the borders of each slice disappear due to their zero thickness. Each DICOM image is a slice about 5 mm thick.
CT, industrial CT, MRI or microCT scanners do not create a cloud of points, but 2D slices (referred to as a “tomogram”) that are superimposed on each other, resulting in a kind of 3D model. There are several ways to do this scan, depending on the desired result:
- Volume rendering: Different parts of an object usually have different thresholds and grayscale densities. Based on this, a three-dimensional model can be freely designed and displayed on the screen. Several models can be made from different thresholds, allowing different colors to represent a specific part of an object. Volumetric rendering is most often used to render a scanned object.
- Image segmentation: When different structures have similar threshold or midtone values, it may not be possible to separate them simply by changing volume rendering parameters. The solution to the problem will be segmentation - a manual or automatic procedure that will remove unnecessary structures from the image.
Special programs that support image segmentation allow you to export segmented structures to CAD or STL format, which will allow you to continue working with them.
- Meshing based on image analysis: When 3D image data (CFD and FEA) is used for computer analysis, simple data segmentation and meshing from a CAD file can be quite time consuming. In addition, some typical image data may not be inherently suitable for a complex topology. The solution lies in image analysis meshing, which is an automated process for generating an accurate and realistic geometric description of the scanned data.
Application
Material Handling and Manufacturing
3D Laser Scanning describes a general way to measure or scan a surface using laser technology. It is used in several areas at once, differing mainly in the power of the lasers that are used and the results of the scan itself. Low laser power is needed when the scanned surface should not be influenced, for example, if it only needs to be digitized. Confocal or 3D laser scanning are methods that provide information about the scanned surface. Another low power application involves a projection system that uses structured light. It is applied to solar panel plane metrology involving voltage calculation with a throughput of more than 2,000 plates per hour.
The laser power used for laser scanning of industrial equipment is 1W. The power level is typically 200mW or less.
Construction industry
- Robot control: Laser scanner acts as the eye of the robot
- Executive drawings of bridges, industrial plants, monuments
- Documenting Historic Sites
- Site modeling and layout
- Quality Control
- Measurement of works
- Reconstruction of highways
- Marking an already existing shape/state to identify structural changes after extreme events - earthquake, ship or truck impact, fire.
- Creation of GIS (Geographic Information System), maps and geomatics
- Scanning of subsurface in mines and karst voids
- Court records
Benefits of 3D scanning
Creating a 3D model by scanning has the following benefits:
- Makes working with complex parts and shapes more efficient
- Encourages product design when needed to add a part created by someone else.
- If CAD models become outdated, 3D scanning will provide an updated version
- Replaces missing or missing parts of
Entertainment
3D scanners are widely used in the entertainment industry to create 3D digital models in film and video games. If the model being created has a counterpart in the real world, then scanning will allow you to create a three-dimensional model much faster than developing the same model through 3D modeling. Quite often, artists first sculpt a physical model, which is then scanned to get a digital equivalent, instead of creating such a model on a computer.
Reverse engineering
Reverse engineering of mechanical components requires a very accurate digital model of the objects to be recreated. This is a good alternative to converting many points of a digital model to a polygon mesh, using a set of NURBS flat and curved surfaces, or, ideally for mechanical components, creating a 3D CAD model. A 3D scanner can be used to digitize objects that freely change shape. As well as the prismatic configuration, for which a coordinate measuring machine is usually used. This will allow you to determine the simple dimensions of the prismatic model. This data is further processed by special programs for reverse engineering.
3D printing
3D scanners are also actively used in the field of 3D printing, as they allow you to create fairly accurate 3D models of various objects and surfaces in a short time, suitable for further refinement and printing. In this area, both contact and non-contact scanning methods are used, both methods have certain advantages.
Cultural heritage
An example of copying a real object through 3D scanning and 3D printing. There are many research projects that have been carried out using the scanning of historical sites and artifacts to document and analyze them. The combined use of 3D scanning and 3D printing makes it possible to replicate real objects without the use of a traditional plaster cast, which in many cases can damage a valuable or delicate cultural heritage artifact. The sculpture of the figure on the left was digitized using a 3D scanner, and the resulting data was converted in the MeshLab program. The resulting digital 3D model was printed using a rapid prototyping machine that allows you to create a real copy of the original object.
Michelangelo
There are many research projects that have been carried out using scanning of historical sites and artifacts to document and analyze them.
In 1999, 2 different research groups started scanning Michelangelo's statues. Stanford University, along with a team led by Mark Levoy, used a conventional laser triangulation scanner built by Cyberware specifically to scan Michelangelo's statues in Florence. In particular, the famous David, "Slaves" and 4 more statues from the Medici chapel. Scanning is performed with a dot density of 0.25 mm, sufficient to see the traces of Michelangelo's chisel. Such a detailed scan involves obtaining a huge amount of data (about 32 gigabytes). It took about 5 months to process them.
Around the same time, a research group from IBM was working, led by H. Raschmeyer and F. Bernardini. They were tasked with scanning the Florentine Pieta sculpture to obtain both geometric data and color information. The digital model obtained from a Stanford University scan was fully used in 2004 to further restore the statue.
Medical applications CAD/CAM
3D scanners are widely used in orthopedics and dentistry to create a 3D patient shape. Gradually, they replace the outdated gypsum technology. CAD/CAM software is used to create prostheses and implants.
Many dentistry uses CAD/CAM as well as 3D scanners to capture the 3D surface of a dentifrice (in vivo or in vitro) in order to create a digital model using CAD or CAM techniques (e. g. , for a CNC milling machine (computer numerical control), as well as a 3D printer). Such systems are designed to facilitate the process of 3D scanning of the drug in vivo with its further modeling (for example, for a crown, filling or inlay).
Quality assurance and industrial metrology
The digitization of real world objects is of great importance in various fields of application. 3D scanning is very actively used in industry to ensure product quality, for example, to measure geometric accuracy. Predominantly all industrial processes such as assembly are quite complex, they are also highly automated and are usually based on CAD (computer-aided design data). The problem is that the same degree of automation is required for quality assurance. A striking example is the automated assembly of modern cars, because they consist of many parts that must match exactly with each other.
Optimum performance levels are guaranteed by quality assurance systems. Geometrical metal parts need special checking, because they must be of the correct size, fit together to ensure reliable operation.
In highly automated processes, the results of geometric measurements are transferred to machines that produce the corresponding objects. Due to friction and other mechanical processes, the digital model may differ slightly from the real object. In order to automatically capture and evaluate these deviations, the manufactured parts must be rescanned. For this, 3D scanners are used, which create a reference model with which the received data are compared.
The process of comparing 3D data and a CAD model is referred to as CAD comparison and can be a useful method for determining mold and machine wear, final assembly accuracy, gap analysis, and the volumetric surface of a disassembled part. Currently laser triangulation scanners, structured light devices and contact scanning are the leading technologies used in industrial applications. Contact scanning methods, although they are the slowest, but the most accurate option.