Elastomer 3d printing
Elastomer 3D Printing Material is a New World of Possibilities
Elastomer 3D Printing Material is a New World of Possibilities - Stratasys Stratasys Invests in Axial3D to Make Patient-Specific 3D Solutions Available to All - Learn MoreUSA & Canada
Select your country and region
- Americas
- English
- Español (México)
- Português (Brasil)
- EMEA
- English (United Kingdom)
- Deutsch
- Español
- Français
- italiano
- APAC
- 中文(简体)
- 日本語 (日本)
- 한국어(대한민국)
- English (India)
USA & Canada
A new world of possibilities.
TPU 92A, thermoplastic polyurethane is the all new elastomer from Stratasys, available on the F123 Series 3D printer. Durable yet flexible, this FDM material, allows you to 3D print superior rubber-like parts, across a huge range of applications. Produce complex parts that elongate and compress. Accurately. And at speed.
Get a sample today or ask us how you can reduce your costs across a wide range of applications with TPU 92A on the F123 3D printer series.
Watch the webinar
Go large. Go complex.
Design for purpose without constraints. Our F123 3D Printer Series now comes with the best flexible filament on the market. With TPU 92A you can create large parts and overhangs. Or incorporate cavities and complex geometries. Precisely. Repeatably. As close as it gets to the finished part.
Ask one of our experts if elastomer could be right for your application.
Ask an expert
We test so you don't have to.
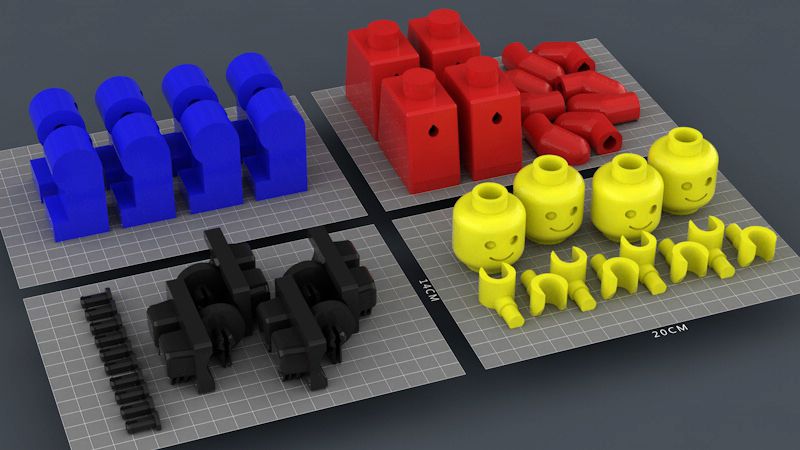
Over 30,000 hours of testing have helped us create 3D printing materials that outperform your expectations. Our flexible filament went through the same rigorous testing – giving you the elongation, superior toughness and extreme durability you’d expect from a 92 Shore A elastomeric material. A better material, for better results.
Request a sample and see for yourself.
Request a sample
Less cost. More output.
Workflow is transformed with elastomer and the F123 Series, the best 3D printer for maximum savings, with up to 40% on average saved on print costs. Load designs using our GrabCAD software then let the machine run. You’ll return to a perfect part every time. With minimal print prep, efficient printing and easy post-processing with our soluble support material, you're free to do more of what you do best.
See how we beat the competition on cost per part for TPU.
Read more
Resilient, Flexible, Thermoplastic
FDM TPU 92A is a resilient thermoplastic polyurethane combining flexibility and stretch with abrasion and tear resistance. 3D printing with FDM TPU 92A provides a superior alternative to less optimal TPU 3D printing technologies and eliminates expensive and time-consuming molding or casting methods to produce elastomer parts.
Performance properties
Tensile Strength
16.8 MPa (XY Axis)
17.4 MPa (XZ Axis)
Elongation At Break
552% (XY Axis)
482% (XZ Axis)
Tear Strength
84.6 N/mm (XY Axis)
Shore Hardness
92 Scale A
Soluble support. Dissolves cost.
Achieve complex geometries and cavities with our exclusive soluble support material: a support structure that's 3D printed around the part, so there’s no compromise on design. Plus, no hands-on removal to reduce costs and simplify the prototype-to-product journey.
See soluble support in action
Downloads
TPU 92A product data sheet
Download
Creating Elastomeric Parts with 3D Printing and Molding
Types of Elastomers
Rubber is the stuff of tires, engine hoses, and more—but here we’re talking specifically about silicone rubber, which is technically a viscoelastic (short for viscous and elastic) polymer. Condense that term a bit more and you get elastomer. Elastomers are strong and (usually) flexible, and available in an array of grades that offer enhanced mechanical, chemical, and optical properties. Protolabs offers the following types of elastomeric materials:
Injection Molding | 3D Printing |
---|---|
LSR | Digital Photopolymers |
LSR (Fluorosilicone) | TPU (also for injection molding) |
LSR (Optical) | TPE/TPV |
TPU (also for 3D printing) |
This design tip digs further into the details of using elastomers for designing parts that require flexibility, and also explores which manufacturing processes are applicable to each elastomer.
This optically clear part for a high-performance LED silicone fog light was produced for an automotive OEM using a liquid silicone rubber (LSR) molding process.
Elastomers for Injection Molding
If you’ve ever mixed up a little two-part epoxy for a household repair project, you’re already familiar with how liquid silicone rubber (LSR) parts are made. Using equipment similar to but in some ways the exact opposite of plastic injection molding, LSR molding forces equal parts of a chemical catalyst together with liquid silicone rubber into a chilled mixing chamber. From here it is injected into the mold cavity, which in the case of LSR is heated to speed the vulcanization process.
The design rules of LSR molding are quite forgiving. Worries over wall thickness, draft angles, undercuts, and corner radii can largely be tossed out the window. That’s because LSR has the consistency of water as it enters the mold—there are no problems with sink, knit lines, and voids at sharp corners or around deep ribs (assuming the mold has been properly gated and vented, of course). Nor is part ejection a problem—LSR parts generally remain flexible enough to pull from even the most straight-walled of molds. About the only thing designers need to be concerned with is flash—because LSR has such low viscosity, clean and consistent parting lines should be used wherever possible.
Deploying PolyJet industrial 3D printing allows designers to build multi-material prototypes with flexible features, and can also provide the ability to combine material properties into a single build.
At Protolabs, four types of LSRs are available. All play by the same basic set of design rules, but each offers fairly distinct characteristics:
- LSR—Elastosil LR 3003 series comes in five durometer levels, from 30 to 70 Shore A, and, like most LSRs, plays well with pigment. Suitable applications include automotive electrical components, seals and gaskets for the food industry, and anywhere a flexible, durable, temperature agnostic polymer is required.
- LSR (Fluorosilicone)—Silastic FL is very resistant to harsh environments.
It’s a good choice for seals, gaskets, and membranes used around solvents and chemicals, or anywhere cold temperatures (down to -86°F) are a concern.
- LSR (Medical)—Dow Corning has developed its QP-1 LSR specifically for the medical industry. It’s a favorite for surgical and dental parts, health care products, and anywhere contact with humans is expected. QP-1 also demonstrates exceptional tear strength—up to 52.4 kN/M—the highest available at Protolabs.
- LSR (Optical)—Need to make a clear but durable lens or other transparent part? Many injection molders might first opt for polycarbonate, but optical-grade LSR is eminently more moldable and has better optical qualities, second only to glass. It too is biocompatible, and at 72 Shore A ranks among the hardest of LSRs.
This stethoscope is an example of 3D printing (PolyJet) elastomers to build two-material prototypes.
TPE and TPV materials are used regularly for those looking for molded elastomeric parts but they really come into play during two-material molding processes like overmolding. For instance, when you’re ready to take your PolyJet (3D printing) prototype to the next phase of development, Protolabs offers many grades of elastomeric materials that all belong to the TPE/TPV (thermoplastic vulcanizate/thermoplastic elastomer) family. For example, Santoprene 111-45 TPV has excellent resistance to fatigue and would make a good cover for your smartphone. Similarly, Santoprene 101-73 works well for steering column boots and speaker surrounds.
On the TPE end of the spectrum, Versaflex OM 1040X-1 has a soft feel, excellent aesthetic appearance (can be colored), and bonds well to polycarbonate or ABS, making it a good choice for gripping surfaces on medical devices. Another colorable TPE is Versaflex OM 6240-1, known for its affinity to nylon. And then there’s Hytrel 3078, which some might consider the Eveready bunny of elastomers thanks to its ability to flex, bend, and pull far longer than standard rubber material.
The design guidelines for all of these materials falls somewhere between the “almost anything goes” of LSR and those associated with traditional thermoplastics. When in doubt, upload your CAD model to Protolabs automated quoting system and pay close attention to the resulting design for moldability analysis.
Elastomeric parts are frequently used in the medical industry, including the example here. A liquid silicone rubber (LSR) molding process was used to create this part that provides an airtight seal for blood samples.
Elastomers for 3D Printing
PolyJet 3D printing uses a special type of “sprayable” liquid photopolymer with a hardness that can be tweaked on the fly and in the same build, making it a great choice for prototyping parts that will at some point be overmolded—a soft, grippable handle for a power tool, for example, or a weatherproof, gasketed cover for a scientific instrument housing. Digital photopolymers in white, black, and clear/translucent are available, and Shore A hardness levels range from 30 durometer to fully rigid. If you want to validate an overmold design, this is probably a good place to start, just be sure to check with Protolabs that your 3D-printed part is also suitable for molding—some designers paint themselves into an additive manufacturing corner, only to find that their design can’t be manufactured en masse in a cost-effective manner.
Until recently, another 3D printing process, selective laser sintering (SLS), was limited to nylon-like polymers in white, black, and glass-filled variants. That’s not a bad thing, but sometimes people want additional material choices, especially with an additive process as flexible and robust as SLS. Enter thermoplastic polyurethane, or TPU. In the plastic injection molding world, polyurethane is one of the go-to polymers, offering excellent mechanical properties, a wide hardness range and—depending on whether the TPU is polyester-based or polyether-based—a variety of desirable attributes including chemical, microbial, hydrolysis, and abrasion resistance.
That’s why Protolabs now includes TPU—an elastomer that stretches with the best of them—in its lineup of SLS polymers. Need to prototype some ergonomic bicycle grips but don’t want to invest in a quick-turn mold? How about a set of strong and durable hoses for a packaging machine design? Go ahead and 3D print some samples. And even though the parts come out soft and flexible, there’s nothing especially different about the SLS process itself, so no need to learn a new set of design criteria. Again, upload the CAD file and review the design feedback.
As always, feel free to contact one of our applications engineers with any questions at 877-479-3680 or [email protected].
Supersoft 3D Printable Resins Obtained
1354
Bookmark
New material can be 3D printed objects that have unusual softness and elasticity - mechanical properties very similar to those of tissues human, scientists say Science Advances. News appeared on the website University of California at Santa Barbara (USA).
Conventional elastomers, i.e. rubbers, rubber, are stiffer than many biological tissues. This is due to the size and shape of the components. their polymers, which are long linear molecules that stick together easily, like overcooked spaghetti. At new polymers have additional polymers attached to linear basis, which allows you to create a structure that is more like on a bottle brush that we can find in our kitchen. The polymer structure of the "bottle brushes" makes it possible obtain extremely soft elastomers.
Polymers are folded into such a structure at the nanoscale. The material is initially in a semi-solid state and retains its shape, like butter or toothpaste, but when it pressure, it liquefies and becomes so soft so that it can be squeezed out through a syringe. The team uses this property to create ink for 3D printing. Researchers can adjust material flow at different pressure to obtain ink according to the desired processing conditions.
After the object is printed, it is sent ultraviolet light to activate crosslinkers, which scientists have synthesized and incorporated into ink. Cross-linking agents can bind nearby polymers, in resulting in a super soft elastomer. In this moment the material becomes durable - it will no longer soften under pressure and elasticity.
“The elastic modulus of our material is a thousand times less than that of rubber band, - the authors of the work note. - He's super soft the touch is very similar to human tissue. It can stretch becoming about three to four times longer.
New ultra-soft elastomers can be used to create biomimetic tissues and highly sensitive electronic devices: touch panels, sensors and actuators. They can also be printed biocompatible implants that will reduce the risk of inflammation and rejection from the body, since the mechanical properties the implant will match the natural tissue.
[Illustration: ISABELLE CHABINYC]
Author Material Designed by Tatyana Matveeva
3D printing 3D printer biocompatible implants biocompatible materials polymers super soft polymers elastomers
Source: www.news.ucsb.edu
Information provided by the Information Agency "Scientific Russia". Mass media registration certificate: IA No. ФС77-62580, issued Federal Service for Supervision of Communications, Information Technology and Mass Communications on July 31, 2015.
Science Children
The scientist of Moscow State University received a prestigious premium for outstanding achievements in space geophysics
15:30 / Astrophysics, Cosmology
in the Perm Polytechnic learned to more accurately evaluate the strength of large structures
9000 14:35 / Engineering 9000 9000 100 years of Vavilovskaya Vavilovskaya 100 years Vavilovskaya 100 years flax collections: deep analysis - wide application14:30 / Biology
Astronomers have figured out how the super-Earth in the Copernican system became a hot planet
14:00 / Astronomy
Viktor Sadovnichi opened the new Simulation Center of the Faculty of Fundamental Medicine of Moscow State University
13:30 / Medicine
Fian at the Basovsky and Voronezh State Universities
12:30 / Physics
Animalistics A. Animalism A. M. Belashova
11:32 / Leisure
Scientists from Moscow State University and the Moscow Department of Health have developed a neural network for diagnosing MRI machines
11:30 / Mathematics, Medicine
Eternal struggle
11:29 / Leisure
International Animal Rights Day
11:24 / Leisure
In memory of the great scientist. Science in the global world. "Obvious - incredible" broadcast 05/10/2008
03/04/2019
In memory of the great scientist. Nanotechnologies. "Obvious - incredible" broadcast 08/3/2002
03/04/2019
Remembering Sergei Petrovich Kapitsa
14.02.2017
See all
Most Extensible 3D Printing Elastomer / 3D Printing / 3Dmag.org
A group of researchers from Singapore and Jerusalem have made a breakthrough in the field of elastomers for 3D printing. They have created a material belonging to the SUV (UV curing) group, which is able to stretch by 1100% - the highest rate among currently existing substances.
Elastomers, high tensile polymers, have proven invaluable in a wide range of industries including flexible electronics, biomedical devices, robotics and more. But for 3D printing, there was a significant limitation in applicability due to the need for thermal curing of the product. However, a group of scientists managed to create a material that does not lose its elastic properties after this process. “Our new elastomers can be elongated up to 1100%, more than five times the elongation at break of any commercially available UV-based 3D printing elastomer.”
During testing, scientists were able to obtain complex geometric lattices and structures using high-resolution 3D printing. The limitations associated with geometry are a thing of the past. There is also a significant gain in terms of time. Compared with traditional molding and casting methods, using SUV elastomer 3D printing, production time is reduced from many hours and days to several minutes. And, finally, the last advantage of the novelty is the good properties of mechanical repeatability. When tested, the switch in the shape of a buckyball, even after 1000 clicks, retained all the necessary properties and shape.
Related entries:
-
just4fun
3d printing → New materials from Huntsman for the footwear industry 0 -
hedin
3d printing → Luminescent Coating Printing 0 -
hedin
3d printing → A new method of high-resolution laser 3D printing 0 - Learn more