Elastic 3d printing
Ultimate Materials Guide - 3D Printing Flexible Filament
Overview
Flexible filaments are made of Thermoplastic Elastomers (TPE) which are a blend of hard plastic and rubber. As the name suggests, this material is elastic in nature allowing the plastic to be stretched and flexed easily. There are several types of TPE, with Thermoplastic polyurethane (TPU) being the most commonly used among 3D printing filaments. In many cases, these terms are used interchangeably, along with popular brand names such as Ninjaflex. The degree of elasticity in the plastic depends on the type of TPE and the chemical formulation used by the manufacturer. For example, some filaments can be partially flexible like a car tire but others can be elastic and fully flexible like a rubber band. This guide will cover tips to help you with both of these variations of flexible filaments.
- Flexible and soft
- Excellent vibration dampening
- Long shelf life
- Good impact resistance
- Difficult to print
- Poor bridging characteristics
- Possibility of blobs and stringing
- May not work well on Bowden extruders
Hardware Requirements
Before 3D printing with flexible filaments, make sure your 3D printer meets the hardware requirements listed below to ensure the best print quality.
Bed
Temperature: 45-60 °C
Heated Bed Optional
Enclosure Not Required
Build Surface
PEI
Painter’s Tape
Extruder
Temperature: 225-245 °C
Direct Drive Extruder Recommended
Cooling
Part Cooling Fan Required
Best Practices
Flexible filaments come with many unique challenges that you want to be aware of. These tips will help you reduce the chances of common 3D printing issues such as clogging, kinking, and stringing.
Use Direct Drive Extruders
While some partially flexible filaments work fine with Bowden Extruders, most fully flexible filaments require a Direct Drive extruder for best results. The distance between the drive gear and the melt zone of the hot-end needs to be as short as possible to efficiently feed the filament into the nozzle. Additionally, the pathway through which the filament travels into the melt zone should have tight tolerances to prevent the filament from kinking or coiling inside. For these reasons, it is typically much easier to print flexible filaments with a Direct Drive extruder versus a Bowden extruder. If you are unsure about your 3D printer’s capabilities, you may want to check with the manufacturer to see if the extruder has been approved for use with flexible filaments.
Use Slow and Consistent Feed Rates
Flexible filaments typically print best using a slow and consistent feed rate. Because the material is elastic, it can be very difficult to control sudden changes in the print speed. Higher print speeds can cause the filament to compress and will most likely result in a jam. Slow and steady is the best approach. Simplify3D provides all of your feed rate settings on the Speeds tab of your process settings so that you can easily configure these values. Finding the optimal print speed for your material can take several attempts based on trial and error. We have seen that speeds of 1200 mm/min (20 mm/s) can be a good starting point for most materials.
Reduce Resistance from the Filament Spool
A few tweaks to your material spool can also make a big difference with flexible materials. Typically, your extruder will pull the filament into the nozzle, forcing the filament spool mounted on your printer to unwind a bit of plastic in the process. However, because flexible materials are elastic, this will stretch the filament out as it is being pulled in and can actually result in under-extrusion. Try mounting the spool above your printer so that the filament unwinds in a downward direction which can reduce the resistance. It can also be incredibly helpful to mount the spool’s hub on a bearing to allow the spool to spin as freely as possible.
Tune Your Retraction Settings
The elastic nature of flexible filament makes it sensitive to quick movements such as retractions. In order to successfully print the filament, you will need to optimize your retraction settings to reduce these movements. While you are first starting with this material, we would recommend disabling retraction completely. You can make this change in Simplify3D on the Extruders tab of your process settings. With retraction disabled, you can focus on finding the perfect speed and extrusion rates that allow you to reliably print your models. After you are more confident in these settings, you may wish to add a very small amount of retraction with a slower retraction speed to help with any potential oozing from the hot-end. Simplify3D also includes a unique option called Coasting, which will automatically help lower the pressure in the nozzle when you approach the end of a segment, which can significantly reduce blobs and stringing with these materials. If you want more information about other options that can help reduce hairs and stringing on your prints, we have an entire section on our Print Quality Guide dedicated to that issue: How to Reduce Stringing and Oozing.
Optimize Your Travel Movements
Retractions can be particularly troublesome for flexible materials, so it is typically best to minimize the number of retractions required for your print. Simplify3D has a great feature that was built specifically for this situation. Instead of moving in a straight line from point A to B, the software will actually choose a completely new path when moving between these points, with the goal of staying within the interior of your object so that there won’t be any oozing or stringing. With this unique feature enabled, you can greatly reduce the amount of retractions required for your print and significantly improve your print quality. To use this feature, click on the Advanced tab of your process settings, and enable the “Avoid crossing outline for travel movement” option.
Pro-Tips
- Optimize the feed rate by printing at lower layer heights in the 0.1mm – 0.2mm range. The lower layer height requires less plastic, so it allows your extruder to use a lower feed-rate, relieving the burden on the filament.
- Try to avoid using rafts with flexible materials, as the base layers of the raft have higher extrusion rates which may create issues.
- If you are designing a flexible part that needs to fit on top of another object, try using a negative tolerance between the parts so that the flexible part will need to stretch to fit over the other object snugly.
Get Started with Flexible Filaments
Now that you’re ready to start printing with flexible materials, we have a few tips to help you get started. View some typical applications below, try out a few of our sample projects, or choose a popular filament brand to purchase for your next project.
Common Applications
- Vibration dampening
- Grip Sleeves
- Phone cases
Sample Projects
- RC Car Tire
- Phone case
- Bike Handle
Popular Brands
- NinjaTek Ninjaflex, Armadillo, Cheetah
- Polymaker PolyFlex
- eSun TPE
- Sainsmart Flexible TPU
A Resilient, Soft, and Flexible 3D Printing Material
Formlabs is pleased to announce Elastic Resin, the latest addition to our library of soft and flexible 3D printing resins for Formlabs desktop stereolithography (SLA) 3D printers.
Elastic Resin is the most pliable of our Engineering Resins, with a Shore durometer of 50A as well as high elongation and energy return. Parts printed in this material look and behave like a molded silicone part, and are durable enough to use for multiple cycles.
Order Elastic Resin Now Request a Free Sample Part
Read on to learn how using Elastic Resin can cut down on lead time and costs in engineering, healthcare, and more, and why it’s now possible to directly 3D print flexible and soft materials like this one on the desktop.
Sample part
Request a free sample part to feel Elastic Resin for yourself. Elastic Resin has a Shore durometer of 50A, while our harder flexible 3D printing resin, Flexible Resin, has a Shore durometer of 80A.
Request a Free Sample Part
Typically, soft silicone and urethane parts for applications like wearables, medical models, robotics, and special effects props are produced through moldmaking techniques or outsourcing.
Some soft materials for direct 3D printing have started to appear, but parts printed in these materials might only last for one or two cycles, and don’t offer the feel expected from a “silicone-like” part. Developing soft stereolithography (SLA) resins can be challenging. Parts must be highly elastic, yet strong enough not to tear during printing—two properties that are typically diametrically opposed.
Elastic Resin is suitable for directly printing soft flexible prototypes and models that once needed to be produced with moldmaking.
Producing quality elastic materials was once only possible for expensive industrial equipment, but with affordable, industrial-quality 3D printers like the Form 3+ and the large-format Form 3L, it’s possible to produce elastic parts on the desktop in a matter of hours.
Looking to manufacture real silicone parts? Read our in-depth guide on silicone 3D printing and its alternatives.
With Formlabs SLA 3D printers, it’s possible to produce flexible parts in-house in a matter of hours to replace outsourcing and molding of silicone, urethane, and rubber parts.
Our family of Flexible and Elastic Resins include:
-
Elastic 50A Resin is a soft material that’s suitable for prototyping parts normally produced with silicone. This 50A Shore material is ideal for parts that will bend, stretch, compress, and hold up to repeated cycles without tearing, and spring back quickly to their original shape. Choose Elastic 50A Resin for applications like wearables (straps), stretchable enclosures and casings, compressible buttons, or soft tissue anatomy in healthcare.
-
Flexible 80A Resin is a stiff soft-touch material with an 80A Shore durometer to simulate the flexibility of hard silicones, as well as rubber or TPU. Balancing softness with strength, Flexible 80A Resin can withstand bending, flexing, and compression, even through repeated cycles. It is ideal for prototyping applications like handles, grips, overmolds, cushioning, damping, shock absorptions, seals, gaskets, and masks, or cartilage, tendon, and ligament anatomy in healthcare.
For companies like NeoSensory, a designer of wearables that create novel sensory experiences, and RightHand Robotics, a designer of robotic grippers for manufacturing lines, the ability to rapidly prototype silicone parts before manufacturing is key to successful development of final products with the potential to change an industry.
The ReFlex Hand, a robotic gripper designed by RightHand Robotics, and a prototype finger 3D printed on a Formlabs SLA 3D printer using Elastic Resin.
Engineers and product designers have traditionally used moldmaking techniques (such as RTV molding, transfer molding, and injection molding) to create short runs of prototype parts in silicone. Directly printing these parts saves time and labor, allowing for deeper iteration and shorter product development cycles.
Use Elastic Resin to 3D print batches of small to moderately sized soft and flexible parts with the ability to make changes to design between and within batches. Moldmaking may be preferable for producing larger numbers of the same part, or for using the final production material during later stages of development.
“We had been looking for a softer material with higher elongation for prototyping of grips and frame protection pieces. Until now we were urethane casting these soft parts in 3D printed molds. The parts we have printed in Elastic Resin simulate 50-60A TPU very well. Printing these parts directly will be a big cost and time saver. Elastic Resin is a great addition to our material library.”
—Jeremy Mikesell, Engineering Manager, Research at Cycling Sports Group
View Technical Data Sheet (PDF)
Surgeons, researchers, radiologists, and other healthcare professionals depend on patient-specific medical models to better prepare for complex cases and operations. Models facilitate better communication both within surgical teams and between practitioners and patients. We’ve heard many requests from healthcare professionals for a clear flexible material to support cases in cardiac surgery, neurosurgery, surgical oncology, and other specialties.
An anatomical model of a prefrontal cortex 3D printed in Elastic Resin on a Formlabs SLA 3D printer. Model provided by Embodi3D.
Notice: Parts printed with Elastic Resin are not biocompatible.
Historically, medical models from service providers and traditional industrial machines have been prohibitively expensive, with slow turnaround times. The ability to quickly and affordably 3D print educational and preoperative planning models on demand expands access across the industry, and we’re excited to see the future impact of Elastic Resin on doctors, researchers, and patients.
“Elastic Resin's opacity illuminates internal cavities well and its durability means that educators, trainees, and clinicians can handle and examine models without worry of breakage. This material will be of particular interest to cardiovascular surgeons and interventional radiologists, as well as those conducting fluid dynamics studies and working in catheterization labs. It is relatively cost effective when compared with other similar materials on the market, which can only help accelerate adoption of 3D printing in medicine.”
—Sanjay Prabhu, MBBS, FRCR; Pediatric Neuroradiologist and Clinical Director, SIMPeds3D, Boston Children’s Hospital
White Paper
Download our white paper for a practical walkthrough for physicians and technologists to get started creating 3D printed anatomicals models from patient scans, reviewing best practices for setting up a CT/MRI scan, segmenting datasets, and converting files to a 3D-printable format.
Download the White Paper
We’ve worked to develop and test a material that will print to the high quality standard you’ve come to expect from Formlabs materials. However, 3D printing flexible and soft materials in general requires denser support structures and attention to specific design guidelines before you print.
Read our “Using Elastic Resin” support article for a deeper look at how to support and orient parts for printing with this material.
Help Center: Using Elastic Resin
As 3D printers and their subsystems evolve, so does access to new materials. With the launch of Elastic Resin, we’re excited to continue evolving our library of Engineering Resins and open up new possibilities in product design, healthcare, and beyond. Order our soft 3D printing material now or request a free sample part to see the quality firsthand.
Order Elastic Resin Now
Request a Free Sample Part
A toy RC car (right), alongside prototype tires printed in Elastic Resin (left).
Soft, stretchy 3D printing material
Formlabs is pleased to introduce Elastic Resin, the latest addition to our library of engineering resins for Formlabs stereolithography (SLA) desktop 3D printers.
Elastic Resin is the most ductile of our engineering resins with a hardness of 50 Shore A, high elongation and shape recovery. Parts printed with this material look and feel like silicone; They are durable enough to be used multiple times.
Order Elastic Resin Now Request a Sample
Find out how using Elastic Resin can save time and costs in development, healthcare, and more, and why it's now possible to print soft materials like this on a desktop 3D printer.
Sample
Request a free sample to feel Elastic Resin yourself. Elastic Resin has a hardness of 50 Shore A, while the stiffer elastic material, Flexible Resin, has a hardness of 80 Shore A.
Request a Free Sample
Typically, soft silicone and urethane parts for applications such as apparel, medical models, robotics and special effects props are produced using mold making techniques or outsourced.
Soft materials for 3D printing have already begun to appear, but parts printed from these materials can only withstand one or two cycles and do not give the feeling expected from a “silicone-like” part. Developing polymers for soft stereolithography (SLA) can be challenging. Parts must have high elasticity, but be strong enough not to tear during printing: these two properties are usually diametrically opposed.
Elastic Resin is suitable for direct printing of soft flexible prototypes and models that once had to be made with injection molding.
Production of quality elastic materials was once only possible with expensive industrial equipment, but with the advent of inexpensive industrial quality 3D printers such as the Form 3, it is possible to produce elastic parts on a desktop in a matter of hours.
Elastic Resin requires Resin Tank LT for Form 2 printer and Resin Tank V2 for Form 3 printer.
For companies such as NeoSensory, a developer of wearable devices that create new sensations, and RightHand Robotics, a developer of robotic grippers for production lines, the ability to quickly prototype silicone parts before production starts is the key to successfully developing end products that can bring about changes in industries.
ReFlex Hand, a robotic grip developed by RightHand Robotics and a finger prototype 3D printed at Formlabs SLA using Elastic Resin
Engineers and developers have traditionally used mold making techniques (such as RTV, transfer molding, and injection molding) to create low-volume silicone prototypes. Printing these parts directly saves time and labor by allowing you to step through the process and reduce product development cycle times.
Use Elastic Resin to 3D print batches of soft and flexible parts in small to medium sizes, while still being able to make design changes during batch production and between batches. Mold making may be advantageous when manufacturing a large number of identical parts or for using finished product material in later development stages.
“We were looking for softer, higher elongation materials to prototype grips and frame guards. Until today, we have cast these urethane parts into 3D printed molds. The parts we printed in Elastic Resin mimic 50-60 A TPU very well. Printing these parts directly will save a lot of time and money. Elastic Resin is a major addition to our material library.”
– Jeremy Mikesell, Chief Research Engineer, Cycling Sports Group
View datasheet (PDF)
Surgeons, researchers, radiologists, and other healthcare professionals rely on personalized patient models to better prepare for complex surgeries. Models promote better understanding both within surgical teams and between practitioners and patients. We have received many requests from medical professionals for a transparent flexible material that can help with cardiac surgery, neurosurgery, oncology and other operations.
Anatomical model of the prefrontal cortex printed in Elastic Resin on a Formlabs SLA 3D printer. Model courtesy of Embodi3D.
Parts printed with Elastic Resin are not biocompatible.
In the past, medical models made by service providers using traditional industrial settings were prohibitively expensive and time-consuming to manufacture. Fast, affordable 3D printing for training and surgery planning models is gaining momentum across the industry, and we're excited to see how Elastic Resin is impacting the way clinicians and researchers treat patients.
“Elastic Resin's transparency allows good illumination of internal cavities, and its durability means educators, trainees and clinicians can work on models without fear of breaking them. This material will be of particular interest to cardiovascular surgeons and interventional radiologists, as well as those who study fluid dynamics or work in the catheterization laboratory. Compared to other similar materials on the market, this material is more cost-effective, which can only accelerate the adoption of 3D printing in medicine,”
- Sanjay Prabhu, MBBS, FRCR; Pediatric Neuroradiologist and Clinical Director, SIMPeds3D, Boston Children's Hospital
White paper
Download our white paper on 3D printed anatomical models to learn how to get started creating 3D anatomical models from patient scan data.
Download white paper
We've been working to develop and test a media that can be used to print to the quality standards expected of Formlabs media. However, before 3D printing a part from soft materials, you should pay special attention to certain recommendations for its design, in particular, a denser arrangement of supports.
Check out our help article "Using Elastic Resin" for more information on how to use supports and orient parts when printing with this material.
Help Center: Using Elastic Resin
As 3D printers and their subsystems evolve, access to new materials also increases. With the release of Elastic Resin, we continue to expand our technical polymer library and open up new opportunities for manufacturing, healthcare and other industries.
Order Elastic Resin
Request a free sample
Radio controlled toy car (right) next to tire prototypes printed in Elastic Resin (left).
Choosing a liquid photopolymer for a 3D printer.
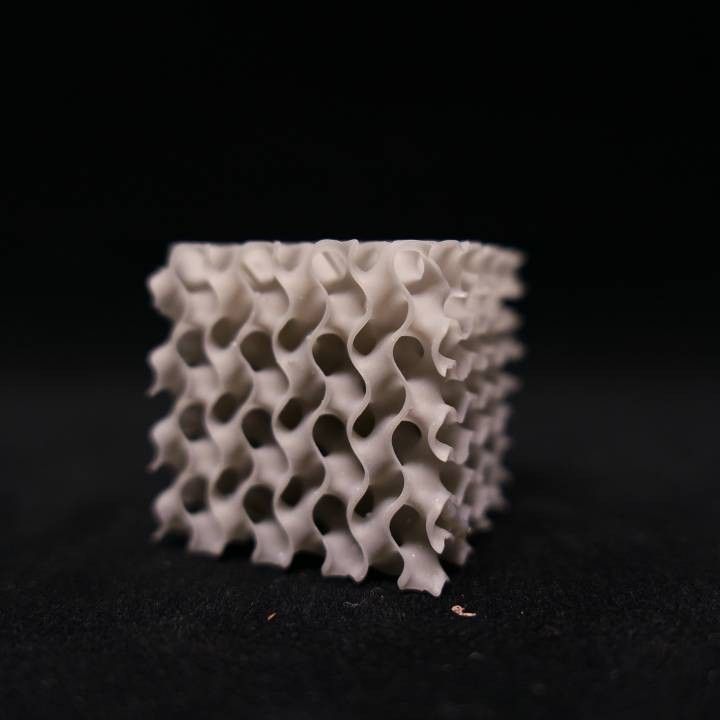
Contents:
- Introduction
- SLA Overview
- SLA standard resins
- Standard photopolymer resin - Standard
- Clear Photopolymer Resin - Clear
- Engineering photopolymer resins
- Rigid photopolymer resin - Tough (like ABS)
- Durable photopolymer resin - Durable (PP-like)
- Heat resistant photopolymer resin - Heat resistant
- Rubber-like photopolymer resin - Rubber-like (Elastic)
- Ceramic photopolymer resin - Ceramic filled (Hard)
- How to choose the right resin for your application
- Dental and medical SLA resins
- Medical Device Photopolymer Resin - Custom Medical Appliances (Class I Biocompatibility)
- Dental Long Term Biocompatible Resin (Class IIa Biocompatible)
- Class I biocompatibility vs Class IIa biocompatibility
- Cast SLA resins
Detailed review of the Formlabs Form 3 3D printer
Introduction
The stereolithography prints plastic parts with high resolution, good fine detail, and a smooth surface. Due to the variety of photopolymer resins available for SLA, this technology is used in many different industries:
-
"Standard" photopolymers are used for prototyping
-
Engineering photopolymers have certain mechanical and thermal properties
-
Dental and medical photopolymers have biocompatibility certificates.
-
Cast photopolymers have a zero ash content after burning.
SLA 3D Printing Resin Overview
SLA uses a laser to cure a liquid photopolymer resin. This process is called photopolymerization. Various combinations of polymers and other additives that are part of the resin allow you to get different material properties.
The main advantages and limitations that are common to all resins in SLA 3D printing are:
Benefits:
Weaknesses:
Base photopolymers for SLA
Post-Processing SLA/DLP 3D Printing Article
Standard resins produce parts with high stiffness, detail and a smooth surface. The low cost of resins, from $250 per liter, makes them ideal for prototypes.
The color of the resin also affects its properties. For example, in FormLabs products, gray resin is suitable for models with fine details, and white resin for parts that require the smoothest possible surface.
Benefits of using Standard grade resins:
Cons Standard:
Also included in the class of "Standard" photopolymer resins from FormLabs is the Color KIT - a set of special dyes and "Color Base" photopolymer resin for mixing and obtaining a variety of color solutions.
This eliminates the need for painting parts after 3D printing.
FormLabs Engineering Photopolymer Resins
Engineering resins have a range of properties for injection molded plastics.
All engineering resins require additional UV curing, such as using the Form Cure, to achieve their maximum properties.
Tough resin was developed for models that need to withstand high loads and be durable.
This material produces strong, shatter-resistant parts and functional prototypes such as snap-on housings.
Pros:
Cons:
Ideal for: functional prototypes, mechanical parts
Durable resin is a wear-resistant and flexible material with mechanical properties similar to polypropylene.
Durable photopolymer produces models with a smooth glossy surface and high resistance to deformation.
Durable Resin is ideal for:
- Bushings and bearings;
- Various functional compounds
Pros:
Cons:
-
Not suitable for thin wall parts (recommended minimum wall thickness 1mm)
-
Low heat distortion temperature
-
Low flexural strength (lower than hard resin)
Ideal for: functional prototypes.
The heat resistant resin is ideal for parts that require high temperature resistance and operate at high temperatures.
Formlabs High Temp Resin provides the highest melting point (HDT): 238°C at 0.45 MPa.
The resin should be used to print detailed, accurate prototypes with high heat resistance.
Pros:
Cons:
Rubber-like resin allows flexible parts to be made. This material has a low tensile strength and high elongation at break and is well suited for parts that will be bent or compressed.
It can also be used to add ergonomic features to multi-material assemblies such as: dies, wearable prototypes, handles, pads and grips.
Pros:
-
High flexibility (high elongation at break)
-
Low hardness (simulates 80A durometer rubber)
-
High impact resistance
Cons:
-
Doesn't have all the properties of real rubber
-
Requires extensive support structures
-
Material properties deteriorate over time as the part is exposed to ultraviolet radiation (sunlight)
-
Not suitable for thin wall parts (recommended minimum wall thickness 1mm)
Ideal for flexible prototyping.
This resin is reinforced with glass, which provides very high rigidity and a polished surface. The polymer is very resistant to deformation and is excellent for 3D printing thin elements.
Ideal for: molds and tooling, jigs, manifolds, retainers, electrical and automotive fixture housings
Thermal management components printed with SLA ceramic (hard) resin. Image credit: Formlabs
How to choose the right resin for your application
The table below shows the main mechanical properties of photopolymers for SLA:
Source: Formlabs
Standard resin ( standart ) has high tensile strength but is very brittle (very low elongation at break) so it is not suitable for functional parts. The ability to create a good part surface makes it ideal for visual prototypes and art models.
durable ( durable ) resin has the highest toughness and elongation at break of any other SLA material. Best suited for prototyping parts with moving parts and latches. It lacks, however, the strength of thermoplastic 3D printing materials such as SLA nylon.
tough tough resin is a compromise between the material properties of tough and standard resin. It has a high tensile strength, so it is best suited for rigid parts that require high hardness.
heat resistant resin ( heat resistant ) can withstand temperatures above 200 o o C, but has poor impact strength and is even more brittle than standard resin.
ceramic ( ceramic reinforce ) resin has the highest tensile strength and flexural modulus, but is brittle (poor elongation at break and toughness). This resin is preferred for thin wall parts that require increased rigidity.
The graphs below compare the mechanical properties of the most common SLA materials visually:
Comparison chart for elongation at break and toughness for common SLA printing specifications and standard media. Image courtesy of Formlabs.
Stress-strain curves for conventional SLA technologies and standard materials. Image credit: Formlabs
Comparative chart of material properties of various technical resins. Image credit: Formlabs.
Dental and medical resins
Pros:
Cons:
- Moderate wear and tear resistance
Ideal for: Surgical aids and appliances
These resins are specially formulated for long term dental fixtures.
Class 2A biocompatible resins can come into contact with the human body for up to a year.
High resistance to breakage and wear make this resin ideal for making rigid cotter pins or retainers.
Pros:
Cons:
-
High price
Ideal for: durable dental instruments, fracture and wear resistant medical parts, rigid cotter pins, retainers
Class 1 biocompatibility rules apply to materials that are allowed to be used for:
-
non-invasive devices that come into contact with intact skin
-
devices for temporary use or short-term use in the mouth or ear canal or in the nasal cavity
-
reusable surgical instruments
Class 2a biocompatibility rules apply to materials that are allowed to be used for:
-
devices that come into contact with bodily fluids or open wounds
-
devices used to introduce substances into or remove substances from the human body
-
invasive short-term devices such as invasive surgical items
-
long-term implantable devices placed in the teeth
Photopolymer resins in SLA 3D printing for jewelers
This material allows you to print models with fine details and a smooth surface without leaving ash or residue after burning.
Learn more
-