Jerk control 3d printing
How to Get the Perfect Jerk & Acceleration Setting – 3D Printerly
You’ve tried countless solutions for your bad quality prints but nothing seems to be working. You’ve now stumbled upon these magical settings called the jerk and acceleration and think it might just help out. This is definitely a possibility and it has helped many people get high quality prints.
How do I get the perfect jerk & acceleration settings? Based on trial and error it’s been found that a jerk setting of 7 for the x and y-axis and an acceleration of 700 works very well for most 3D printers to solve printing issues. This is a good baseline to start from but it could take some tweaking on your 3D printer to get the settings perfect.
This is the short answer for your jerk and acceleration settings that should get you prepared. It’s a good idea to keep reading to learn some key information about these settings such as what they actually change, what problems they solve and more.
Whether you are looking for the best jerk and acceleration settings for an Ender 3 V2 or similar 3D printer, this should be a good starting point.
I wrote an article about 8 Ways to Speed Up Your 3D Prints Without Losing Quality which you can find useful for your 3D printing journey.
If you are interested in seeing some of the best tools and accessories for your 3D printers, you can find them easily by clicking here (Amazon).
What is the Acceleration Setting?
The Acceleration setting measures how fast your print head speeds up, limited by your designated 3D printer speed in your slicer settings.
The higher the setting, the quicker the print head will get to its maximum speed, the lower the setting, the slower the print head will get to its maximum speed.
A lot of times your top speeds won’t be reached when 3D printing, especially smaller objects because there is not much distance travelled to make full use of the acceleration.
It’s very similar to a car’s acceleration, where if a car can go a maximum of 100 kph, but there are a lot of turns in your journey, you’ll find it hard to get to the maximum speed.
In the Cura slicer, they state that enabling ‘Acceleration Control’ can reduce printing time at the cost of print quality. What we can hopefully do on the other side is improve our Acceleration at the benefit of increasing print quality.
Your slicer doesn’t actually have much to do with acceleration, in so far as emitting G-code to say where the print head should go and at what speed. It’s the firmware which sets limits to speed and deciding how fast to accelerate to a given speed.
Each axis on your printer can have different speeds, acceleration and jerk settings. The X and Y axis settings are generally the same; otherwise your prints can have different features dependent on part orientation.
There are limits on how high you can set acceleration, especially when printing at angles larger than 45 degrees.
What is the Jerk Setting?
It’s quite a complex term and has different descriptions based on what firmware you are using. It’s basically an approximation value that specifies the minimum speed change that requires acceleration.
The Jerk setting measures the speed at which your print head moves from its still position. The higher the setting, the faster it will move off from a stable position, the lower the setting, the slower it will move off from a stable position.
It can also be known as the minimum speed your print head will slow down before initiating speed in a different direction. Think of it like a car driving straight, then slowing down before a turn.
If Jerk is high, your print head won’t slow down as much before making the directional change.
When the print head is told to change speed and direction in the G-code, if the difference in speed calculations is less than the specified Jerk value, it should happen ‘instantaneously’.
Higher Jerk values gives you:
- Reduced printing times
- Fewer blobs in your prints
- Increased vibrations from rapid changes in direction
- Smoother operation around corners and circles
Lower Jerk values gives you:
- Less mechanical stresses to your printer
- Smoother movements
- Better adhesion for your filament at direction changes
- Less noise from your printer
- Less lost steps as you may get with higher values
Akeric found that having a Jerk value of 10 gave the same printing time at 60mm/s speed as a Jerk value of 40. Only when he increased the printing speed past 60mm/s to around 90mm/s did the jerk value give real differences in printing times.
High values for Jerk settings basically mean the change of speed in each direction is too fast, which usually results in extra vibrations.
There is weight from the printer itself, as well as from the moving parts so a combination of weight and fast movement doesn’t go too well for print quality.
The negative print quality effects that you’ll see as a result of these vibrations are called ghosting or echoing. I’ve written a quick article on How to Solve Ghosting & How to Fix Banding/Ribbing which goes through similar points.
Which Problems Do Jerk & Acceleration Settings Solve?
Adjusting your acceleration and jerk settings has a whole host of issues that it solves, even things that were not known to you as an issue.
It can solve the following:
- Rough print surface
- Removing ringing from prints (curves)
- Can make your printer a lot quieter
- Eliminate the Z-wobble in prints
- Fixing the layer line skips
- Stop your printer from running too violently or shaking too much
- Many print quality issues in general
There are plenty of people who went and adjusted their acceleration and jerk settings and got some of the best print quality they’ve ever had. Sometimes you don’t even realize how good your print quality can be until you actually get it for the first time.
I’d definitely recommend trying this fix out and seeing if it works for you. The worst thing that can happen is it doesn’t work and you just change your settings back, but with some trial and error you should be able to reduce issues and increase print quality.
The video below by The 3D Print General goes into the effects Jerk & Acceleration settings have on print quality.
How Do I Get the Perfect Acceleration & Jerk Settings?
There are certain configurations which are tried and tested in the 3D printing world. This is great because it means you have to do very little testing to get the best settings for yourself.
You can use these settings as a baseline, isolate either acceleration or jerk, then increase or decrease it little by little until you get your desired quality.
Now for the settings.
For your Jerk setting you should try 7mm/s and see how it goes.
Jerk X & Y should be at 7. Acceleration for X, Y, Z should be set to 700.
You can go directly into your menu on your printer, select the control setting, then ‘motion’ you should see your acceleration and jerk settings.
- Vx – 7
- Vy – 7
- Vz – can be left alone
- Amax X – 700
- Amax Y – 700
- Amax Z – can be left alone
If you would rather do it in your slicer, Cura allows you to change these values without going into your firmware or control screen.
You’ll just have to go into Cura settings and click advanced settings, or custom settings to view your Cura jerk and acceleration values. It’s similar in PrusaSlicer, but the settings are in the “Printer Settings” tab.
Usually you want to do this one by one. It’s good to start off with the jerk setting.
If lowering your jerk makes things too slow, you can up your print speed somewhat to compensate. If just lowering the jerk doesn’t fix your problem, then lower the acceleration and see what difference it makes.
Some people leave the Jerk settings at 0 & have an acceleration of 500 to get good prints. It really depends on your printer and how well-tuned and maintained it is.
Binary Search Method for Getting Good Jerk & Acceleration
The binary search algorithm is commonly used by computers to search programs and it can be used in many applications such as this one here. What it does it give a reliable calibration method by using ranges and averages.
How to use the binary method:
- Establish a value that is too low (L) and one that’s too high (H)
- Work out the middle value (M) of this range: (L+H) / 2
- Try printing at your M value and see the results
- If M is too high, use M as your new H value and vice versa if too low
- Repeat this until you get your desired result
It can take some time but once you find the settings that work best for your printer, it can make the world of a difference. You’ll be able to be proud of your prints and not have weird, wavy lines and artifacts plaguing your print quality.
It’s a good idea saving them as a default profile in your slicing software. So, the next time you come to slice your next print, it will be automatically input into the settings.
I advise you to write down what the settings were before you change it so you can always change it back in case it doesn’t work. If you forgot to it isn’t a big deal because there should be a default setting to make it go back to the original settings.
Jerk & Acceleration settings do vary from printer to printer because they have different designs, weights and so on. For example, 3D Printer Wiki says to set Jerk to 8 and the Acceleration to 800 for the Wanhao Duplicator i3.
Once you’ve tuned your settings, use this Ghosting Test to analyze the levels of ghosting and whether it’s better or worse.
You want to look for ghosting of sharp edges (on the letters, dimples and corners).
If you have vibrations on your Y-axis, it will be seen on the X side of the cube. If you have vibrations on your X-axis, it will be seen on the Y side of the cube.
Slowly test and adjust to get the settings just right.
Using Arc Welder to Improve 3D Printing Curves
There’s a Cura Marketplace Plugin called Arc Welder that you can use to improve printing quality when it comes to 3D printing curves and arcs specifically. Some 3D prints will have curves to them, which when sliced, translates into a series of G-Code commands.
3D printer movements are mainly made up of G0 & G1 movements which are a series of lines, but Arc Welder introduces G2 & G3 movements which are actual curves and arcs.
Not only does it benefit printing quality, but helps to reduce print imperfections like Ghosting/Ringing in your 3D models.
Here it looks when you install the plugin and restart Cura. Simply find the setting in Special Modes or by searching for “Arc Welder” and check the box.
It brings up a few other settings that you can adjust if needed, based mainly on improving quality or firmware settings, but defaults should work just fine.
Check out the video below for more details.
If you love great quality 3D prints, you’ll love the AMX3d Pro Grade 3D Printer Tool Kit from Amazon. It is a staple set of 3D printing tools that gives you everything you need to remove, clean & finish your 3D prints.
It gives you the ability to:
- Easily clean your 3D prints – 25-piece kit with 13 knife blades and 3 handles, long tweezers, needle nose pliers, and glue stick.
- Simply remove 3D prints – stop damaging your 3D prints by using one of the 3 specialized removal tools.
- Perfectly finish your 3D prints – the 3-piece, 6-tool precision scraper/pick/knife blade combo can get into small crevices to get a great finish.
- Become a 3D printing pro!
How to Set Them – 3dprintscape.com
If your 3D printer is shaking everything around it and the extruder head comes to an abrupt stop every time it needs to move to a new position your jerk settings are probably to blame. I had a similar issue when I was first setting up my 3d printer and was able to solve it by enabling jerk control in Cura and cutting speeds in half. Jerk is the maximum instantaneous speed change of the print head.
In Cura 4.X jerk control is disabled by default, which means your printer will fall back to what’s on its firmware. You can override this at the printer console but I prefer to have all the settings in the G-code file as it provides less room for error. On my 3D printer, I set the Travel Jerk speed to 30 mm/s and all other jerk control setting to 20 mm/s. This significantly reduced the abrupt stops for me but you may need to play with the settings some to see what works best for your printer.
In 3D printing, different speed settings can be used to suit specific sections of the print.
Jerk settings describe the speed of the print head before a hard stop and following change of print direction and velocity. This means that while printing, the print head makes a complete halt at certain points of the printing process before continuing to print a different section.
If the change is made at high speeds, the move is damaging to the printer head and the quality of the print. A high-speed jerk can be noticed from vibrations of the printer head and a screeching sound.
Think of a high-speed jerk in the analogy of the brakes of a car. If braking is done at high speed, the ride is uncomfortable and the brake parts are compromised.
Read on to understand jerk setting among other speed settings and also explore enabling Cura jerk settings.
Jerk Setting Among Other Speed Setting
Because 3D printing takes a lot longer than normal document printing, Cura offers several settings to control print speed. A general rule of thumb is higher quality 3D printers can print faster, without issues, than cheaper made ones.
Print speed is measured in mm/s. It is the velocity of the print head while printing is in motion. Print speed settings are found in the Speed option of the Custom settings. The default Cura print speed is 60mm/s. Note, this value may differ based on the printer profile selected.
I recommend you review the documentation for your printer to see if they have any recommendations on speed and jerk settings or if they provide a printer profile that you can import into Cura with the settings already defined.
When printing speed is high, shorter printing time is expected and vice versa. But high printing speed can compromise quality if other factors are not considered. For example, if printing speed is increased, the filament may not melt at the same rate. This means that the temperature must also be amplified to ensure that the filament melts fast enough to keep up with the increased printing speed.
Increased print speed also makes the printer head to jerk and vibrate, compromising print quality.
To create a balance, Ultimate Cura has different speed settings depending on the specific aspect of the printing task. They include:
Travel speed
The speed of the print head when in motion from one point to another (when not extruding). High-speed travel gives a cleaner print by preventing filament leak. If too high, the nozzle can overprint on already printed sections.
Initial layer print speed
It specifies the print speed for the first layer. Low speed allows the print to stick better.
Initial layer travel speed
It defines the travel speed for the first layer and should be kept low.
Skirt speed
Also known as brim speed and specifies the printing speed of the skirt. It should be the same as the initial layer speed.
Maximum Z-speed
The setting that alters the speed for the built plate movement. It should be set at maximum.
Number of slower layers
Specifies the number of layers needed to obtain the print speed from the bottom layer. Set at a higher value, this setting reduces the possibility of warping even though printing time is increased.
Equalize filament flow
The setting allows higher speeds when printing thin walls.
Enable acceleration control
Enabling acceleration control allows you to adjust firmware settings for speed. For example, you can reduce firmware speed for accurate printing at lower speeds. If you opt for maximum acceleration, it’s enough to disable the option.
Jerk control
As indicated earlier, jerk settings control the speed before a hard stop.
Cura Jerk Settings: Enable Jerk Control
3D printers come with a firmware jerk setting. Usually, this setting is high implying a minimum jerk. As a rule, however, Cura software settings override firmware settings.
Cura jerk settings decrease the speed settings of the firmware. This makes the printing slower but increases print quality and accuracy.
If the jerk setting is disabled, a maximum jerk is activated. As a general principle, the Cura ‘Enable Jerk Control’ option should always be enabled.
When you start Cura, click the Preferences menu and then the Setting option. The Settings option has all the different sub-options including Quality, Shell, Infill and Speed. Under speed, choose the Enable Jerk Control.
Under the Enable Jerk Control are all the specific jerk settings that you can choose depending on the specifics of your printing. They include:
- Print jerk
- Infill jerk
- Wall jerk
- Top service skin jerk
- Support jerk
- Travel jerk
- Skirt/brim jerk
Enabling the jerk settings under Preferences allows Settings Visibility when you get to the Custom Print setup. Enable Jerk Control settings here will typically override the settings defined in the printer’s firmware and will give you more control over your print.
With the jerk control settings in place, Cura will add the G-code to effect these settings every time printing requires it. If they are not set, then the printer goes for the firmware jerk settings.
Related Articles
- Create a Temperature Tower Using Cura – The Easy Way
- Cura First Layer Settings
- Cura Profiles
- How to Remove the Disallowed Areas in Cura
Summary
Cura offers many options to control the jerk settings and speed of your printer. I set the Travel Jerk speed to 30 mm/s and all other jerk control settings to 20 mm/s. This has worked well with my printer but it’s not a one size fits all setting as no two printers are completely alike.
If the above settings don’t work well with your printer, I recommend reviewing the documentation to see if they have any recommendations or if they provide a printer profile that you can import into Cura with the settings already defined. If you’re looking for a new 3d printer, I recommend one of the Creality ones. I have owned a couple of them and they are great for the price.
Also, if your printer is producing good quality prints with jerk control disabled in Cura I would not mess with it. I like to follow the “ifs it’s not broken don’t fix it” rule. Though if that was the case you probably wouldn’t have ended up coming across, or reading, this article.
Make sure you check out our YouTube channel, and if you would like any additional details or have any questions, please leave a comment below. If you liked this article and want to read others click here.
13 notes about 3D printing, after 3 years of owning a 3D printer / Habr
This article will be, first of all, of interest both to those who have directly dealt with 3D printing, that is, who owns a 3D printer, but also to those who are just about to join the ranks of 3D printers and are thinking about buying their own printer.
In the framework of this article, I want to present my observations, as a direct owner of a 3D printer, for more than 3 years.
Despite the fact that 3D printers have been known for a long time and, in my memory, have become widely used, judging by the information on various resources, starting around 2010 (I may be wrong, these are my subjective observations), for a long time I ignored this area, it’s hard to say why…
Probably thought it was some kind of "childish pampering", another hype topic for which there is simply not enough time...
The turning point happened when one of the wheels on my travel suitcase wore out. You know, a big plastic suitcase, with four spinning wheels on the bottom. Unfortunately, it is a “rather disposable thing”, due to the lack of bearings on the wheels, which is why the wear of the friction point of the axle and wheel allows the suitcase to last no more than one or two seasons.
And it’s like “lightning flashed in the middle of the day: 3D printer!” It is with his help that I can fix this problem! Looking ahead, I’ll say that I didn’t succeed in fixing the suitcase in this way, so I had to use a different approach . ..
As a result, I “upped” it - installing wheels from unnecessary roller skates. Thanks to this “up”, the suitcase has become a real all-terrain vehicle and, even being very loaded, it rides easily - pushed forward even with “one finger”. And even in the snow, 5-6 cm thick. A tank, not a suitcase turned out! By the way - I took spinning wheeled "units" in Leroy. Then he took off and threw out his native plastic wheels from there, inserting from roller skates:
But this thought itself became a kind of trigger that allowed me to finally join the world of printers and buy my first 3D printer.
Like many, before buying it, I studied various forums and sites for a long time, delving into all the subtleties. And for some reason, I immediately liked the type of printer called the delta printer. Probably because during operation it looks like some kind of "alien device".
If at your leisure you like to sit “looking into the carpet”, then with the advent of such a printer you will have a much more interesting activity, even hypnotizing, one might say :-))
And this, in fact, is my delta (if anyone is interested), which went through, let's say, the "ultimate up": all the electronics are placed upstairs, on a self-made welded frame, covered with polyethylene and a magnetic door is made. The coil with a bar is installed at the top, on the frame. The axis on which the coil is put on is machined on a lathe from aluminum and a bearing from the VAZ timing is inserted into it. As a result, the coil - "rotates even from the passage of a fly nearby":
Well, yes, I won’t argue for a long time, let’s start reviewing the main facts that I have accumulated as a result of owning this car ... The facts are purely subjective and may differ from your vision. In any case, I will be glad to comments, clarifications, etc.
▍ NOTE 1. Delta is good, but...
Here I should give a number of my observations regarding the delta printer:
- It contains a completely finished frame of the future box, which makes it easy to form a heat chamber. I understand that many printers are made in the form factor of a “certain box” (but this point cannot be ignored), which greatly facilitates the process of wrapping this box with heat-insulating material.
In my case, as such a material, I used a plastic film.
- Already thanks to its design, delta allows you to work at much higher speeds than XY printers. By the way, it is on the delta principle that many modern high-speed industrial robots are built to sort various parts directly on the conveyor belt:
However, this plus does not allow to fully realize the occurrence of parasitic vibrations, even despite their suppressors:
Thus, accurate printing is possible, only at speeds (at least that was the case for me), no more than 60 mm per second. A complex procedure for aligning the movement of the head parallel to the table, which is why, for many, the so-called "lens" appears. People struggle with it with varying degrees of success, but I have not encountered this on my printer and for me, therefore, the “lens” has never been a problem. At the same point, it is worth noting the calibration of the table, which was initially absent on the first deltas, and I had to use an external third-party solution from one American do-it-yourselfer called EZBED. This solution was a hardware-software complex that allows you to quickly and easily calibrate the printing table, that is, to let the printer understand its geometry. Modern printers do not have this issue as they come with a built-in calibration solution. It is worth noting that I solved this problem by attaching a limit switch to the print head, and using the Marlin-1.1.9 firmware.
▍ NOTE 2. "Size doesn't matter..." :-)
When I got the printer, I was impressed by the possibility of huge printouts, a la the handguards of some futuristic rifles, huge body parts, etc.
However, if you try to analyze the results of your many years of practice, it turns out that in most cases, rather small objects were printed that easily fit in the palm of your hand, a maximum of two palms. Despite such a seemingly small size, the printing of these details took a significant amount of time. Of course, this very much depends on which nozzle you print with. But, despite this, it is difficult to disagree with the fact that most of the printed parts will be quite utilitarian and small in size.
Therefore, to be honest, the need for a printer that allows you to print "Venus de Milo in life size" is not obvious.
Of course, you can object to me that “I’m going to buy a printer, I’ll get used to it a little and I’ll get started!!!”
One simple point must be taken into account here: there are no universal things. And in order to understand how much 3D printing in general and your printer, in particular, you will need to solve your problems, and how much it will be able to solve such problems, you just need to first try the 3D printing method personally and then a lot will become clear to you .
Therefore, for a beginner, I recommend taking a small printer that allows you to print extremely small items that fit in the palm of two. With such a device, you will definitely never lose, as it will always be needed. In addition, with its help you will be able to get used to the printing process and, if necessary, purchase a larger device, already clearly understanding its capabilities and ability to solve your set of tasks.
▍ NOTE 3. "What type of printer to get."
Based on the foregoing, I do not recommend taking a delta printer and this can be said right away.
Not because it is bad, in fact, it prints quite accurately, its main problem (in my opinion) is the inability to print rectangular flat, fairly large case components, as well as the inability to fully realize high-speed work, since the quality drops critically. Here it turns out to be a rather offensive situation - the printer can work quickly, but this cannot be done, since the quality will be “nothing”.
And then what kind to take? Depending on the budget and capabilities, I recommend taking any cube printer, for example, the same Core XY (the head moves, and the table goes down as the model “grows”, from top to bottom):
Image source: thingiverse.com
Such a printer allows you to easily print fairly large flat parts of cases, has good speed and accuracy. In addition, the presence of a rigid box-shaped frame allows it to be easily covered with polyethylene to create a sealed heat chamber. In addition, the very fact that the table does not move while working reduces the number of problems with model peeling.
However, the advantages of this printer will not be fully revealed if it has a direct extruder. On the one hand, it will allow printing with rubber-like materials, on the other -
large inertia and head weight. And these are parasitic vibrations, wear of the fur. parts, etc. (like everything in life, “we treat one thing and cripple another” :-))
At the initial stages, this may not be necessary, but in the future it may be necessary to print, for example, tires for your homemade car. And with this, the Bowden extruder has obvious problems. Although, in fairness, printing with such a rubber-like material is far from a daily need. However, whoever seeks will always find: over time, I found a way to “upgrade” my printer with a Bowden extruder to print with flexible materials. "Crutches" of course. But even so.
By the way, there are printers of a cheaper type, the so-called "drygostol", printing by moving the table and head:
They are inexpensive, moderately accurate, but they require a sufficiently high-quality gluing of the printed model to the table, because the table moves, and the model can come off when the table is jerked sharply. When printing large models, this can be a problem.
▍ NOTE 4. What to print with?
It's only a matter of taste and purpose. That is, if your printout will only stand on a shelf and should differ in some kind of aesthetic appearance, these are some requirements, if the printout is an engineering part that will be operated under conditions of increased mechanical load, these are different requirements. That is, in the first case, you can use any PLA, SBS plastics, and others with similar properties.
For engineering parts, for example, I only use ABS. It combines high hardness, strength and low price. Although I understand that now this last statement will cause a storm of comments in the style of “no! - there is even stronger, even better, the same PETG, etc. ":-)
Just here I wanted to say that thanks to the low price and the practical experiments that I conducted with ABS plastic, I realized that it is completely meets all my requirements.
However, the fact that ABS plastic releases carcinogenic substances when heated is quite annoying and forces you to take measures to prevent poisoning. For this, my printer prints completely closed and on an open balcony. After printing, the printer chamber opens, and it remains open in this form until it is completely ventilated and cools down.
▍ NOTE 5. "ABS is difficult to type on, it flakes, peels off the table, etc..."
With a properly configured printer (in my case, at a print temperature of 205 degrees, a thermal chamber and a desktop temperature of 100 degrees), the use of auxiliary techniques, for example, among which, one can name the so-called ABS juice (which is ABS- plastic dissolved in acetone), you can create wear-resistant and durable things, without any hypothetical problems.
For example, my printer has been printing for many hours at temperatures well below freezing. And this happened more than once, not twice, not three! And the print quality was excellent:
12-hour ABS printing at -4 C
▍ NOTE 6. Acetone for post-processing and ABS juicing
At one time, I wrote a fairly detailed article on this topic and I will try to give the main excerpts from it. The essence of the issue here is as follows: due to the fact that different GOSTs are used for the production of acetone, acetone differs in quality. Despite the fact that it would seem that “acetone is also acetone in Africa,” nevertheless, one type of acetone can differ significantly from each other. For example, ordinary acetone, which can be bought at any hardware store, such as "1000 little things", "store near the house" and the like, is very low quality acetone, smells disgusting (although someone like it, maybe someone likes its pleasant building aroma and "aftertaste" :-))).
In contrast to it, there is a much higher quality acetone, which, however, is not found at all in any household stores, even large chain stores, such as Auchan or Leroy Merlin.
This type of acetone is found exclusively in shops that sell varnishes and paints for automotive work, i.e. these are highly specialized shops for car workshops:
Acetone, which can be purchased there, is of excellent quality, smells almost like alcohol, quickly disappears,
:-) - this is a joke, of course, don't even try it.
However, its main advantage, compared to household type acetone, is that it perfectly dissolves ABS plastic and does not allow it to precipitate. For me personally, it was a very surprising observation when the same ABS plastic was perfectly dissolved with acetone from an auto shop, and completely precipitated when I tried to use household acetone (I just ran out of good acetone, and I had to use "what is ").
Therefore, if you want your results to always be excellent, then here is the right acetone. It should be labeled "for professional use":
▍ NOTE 7. What about ABS juice?
"ABS juice" is what printers call a mixture of acetone and pieces of ABS plastic dissolved in it. This mixture is smeared on the surface of the desktop before printing and allowed to dry. Thanks to this spread, the model easily sticks to the desktop and does not peel off during the printing process. After printing is completed and the platen has cooled down, the model can be easily separated.
All that needs to be said here is that, after trying different approaches over time, I settled on using flexible metal spatulas, also called "Japanese type spatulas":
According to the results of many tests, this method of spreading turned out to be one of the most convenient options, such spatulas can be cleaned very quickly and easily after work. In other words, highly recommended!
▍ NOTE 8. "Yes, nothing sensible can be done on it, I indulged a little and decided to sell it - you can't use it for anything good anyway"
I absolutely disagree with the statement above, which is periodically heard from newcomers to 3D printing. You can even say more: at the moment I can’t even imagine how I used to live without a 3D printer! Since it is he who makes it possible for any do-it-yourselfer to significantly expand their capabilities and make piece products, almost of factory quality! Of course, for this, appropriate hands must be applied to the 3D printer, but that’s another question… and take on things that I would never have thought to take on before!
For example, among my homemade products, the following can be listed:
- Heated sole for boots, which is a hose integrated into the insole (and filled with household silicone from a household store), through which water flows, heated with a catalytic type hand warmer.
Water is pumped using a small peristaltic pump. The engine with a metal gearbox, which is used in the creation of this pump, allows you to develop a force of 3 kg, which is even redundant for this homemade product. The engine is powered by Peltier elements mounted next to the catalytic heater. The project is currently in progress.
- Centrifugal water pump mounted on the shaft of an internal combustion engine that drives a high pressure wearable air compressor with a pressure of 500 bar. The pump pumps coolant through the casing of the high pressure pump, or rather its second stage. Despite the fact that the pump is 3D printed and runs at over 6000 rpm, nothing “fell apart, fell apart, didn’t break.” As you can see in the photo, the pump is installed instead of the “starter”, that is, the armstarter. The compressor scheme as a whole is as follows: 2 engines. Connected by clutch. One is heavy duty. The second is modified and turned into a high pressure compressor:
Yes, before assembling this, I also did not believe that this was possible. Moreover, even when I collected it, I did not believe my eyes :-))). However, it is a fact…
- I printed a number of Rank-Hilsch test tubes, the essence of which I have described in detail in this article.
- Printed mass of parts, more than 100 pieces, to create 10 web-controlled robots. There was also a detailed article about this here.
Well, and a bunch of all sorts of useful and not very crafts. As you can see from my crafts above, I have a special passion for creating some useful things, a utilitarian direction. That is, so that the printout is useful, and does not belong to the type “yyy breathe, Mikola, what am I doing here” :-), and then put it on the shelf and that's it. Although, engineers are also not alien to beauties, and this will be my next fact below.
▍ NOTE 9 Proper placement of the model when printing is half the battle
It would seem an obvious fact, but many underestimate it. Here I mean the following: by experience, I accidentally discovered that when printing various statues (in which I, completely unexpectedly for myself, discovered another passion of mine), it is advisable to place the statues at an angle to the printing table.
This allows the layers in the printout to run at an angle of approximately 45-50 degrees to the model. The result of this is that the printed model is almost completely invisible layers and the model looks like it has been post-processed, but at the same time retains a deep matte color, which, to my personal taste, is more like a marble than a glossy result of processing in an acetone bath :
An additional advantage of this method is that the layers going at an angle of 45-50 ° to the model give it additional strength. This is especially true for printing statues, which contain many thin elements that are easily chipped when the statue is accidentally dropped from a table or shelf (learned from bitter experience, this happened to me many times, and ruined some fairly decent prints).
That is, the layers going across the model, if the model has a large length in height, does not allow it to maintain sufficient strength. For better understanding, I tried to illustrate this point in the figures below:
▍ NOTE 10. Bleeding must be taken into account when printing, especially if the model is composed of separate parts and must be assembled by joining these parts to each other, entering into each other, etc.
I tried to illustrate this point in the figures below. The implication here is that if you're printing a composite model, you need to correct for the amount of bleed on the plastic (I'm not sure what it's called, but at least I tried to convey what I mean). If this is not taken into account, then the model will not fit.
For example, in my case this correction is 0.2 mm per diameter - if I want the model to fit more tightly; if I need a free joint, without excessive density, then 0.3 mm per diameter:
That is, suppose that the blue part has a size of 10x10mm. So it must be modeled in a CAD program as 9.8x9.8 mm (if we want it to sit tight) or 9.7x9.7 mm (to sit freely). Well, or expand the hole in the green part, and leave the blue one as it is.
This is often a problem when you download a prefabricated model from the Internet - but it is not going to, even if you crack! And because no amendments have been made…
For your particular case, the amendments may be different.
▍ NOTE 11. What if...
In fact, this note complements note number 8. Using a 3D printer allows you to create metal parts using a printed 3D model. For this, the casting method is used according to the lost wax or burnt model. In our case, we will deal mainly with metal casting on a burnt model.
Briefly, it looks like this: printing a 3D model (using PLA plastic) → pouring it with plaster → burning PLA plastic, simultaneously with burning the mold, in a conventional stove oven → pouring the resulting mold with molten metal (melted in a conventional microwave) .
Image source: 3dtopo.com
I told about a simple method of melting metals in a home microwave oven here.
There was even a good article about casting on Habré.
▍ NOTE 12. Durability?
Despite the fact that ABS plastic is called exposed to ultraviolet radiation and, accordingly, burns out, losing its strength in the sun, in my practice, even printouts that are constantly exposed to the sun have not lost their strength and color at all, continuing to be successfully used and Currently.
It should also be added here that printouts are constantly exposed not only to the rays of the sun, but also work continuously in damp conditions!
As such printouts, I can give an example of winglets for technical cranes, which I printed out, but, unfortunately, did not photograph this process; as well as fasteners on shoes that I use “both in the snow, and in the heat and in the pouring rain, and in general are always with me”:
▍ NOTE 13.
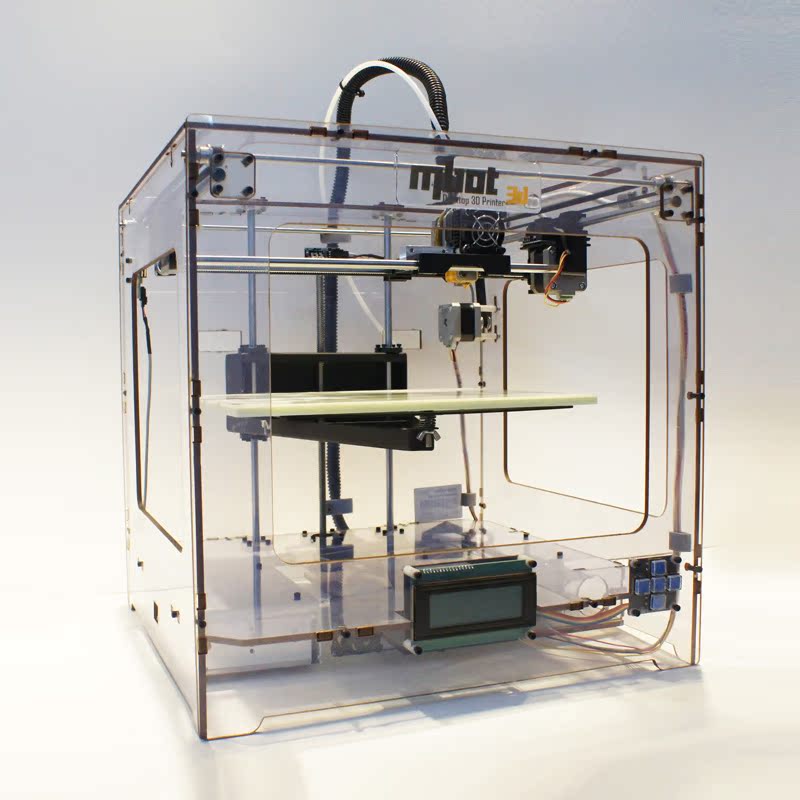
Periodically, there is a need to print parts containing a particular thread. Modeling such products requires a good understanding of what a thread is in general, as well as what corrections need to be made in your particular case, which I have already described above.
But since I've owned a metal lathe for a long time, I'm not at all happy with the 3D printed carving that looks like "something very carving-like".
I am satisfied with an exceptionally perfect carving. Therefore, I keep in stock a large set of various taps and dies, with which I cut all my threads in plastic printouts:
I posted a photo of dies and taps not to brag, but to make the reader understand that serious carving requires a serious approach (unfortunately). And considerable costs for all this thread-cutting iron ...
To create your own threads (both threaded channels and threaded pins), I recommend the following reference materials: for holes, for pins.
Well, that's where I want to end my story and note that he does not claim to be exceptionally accurate and exhaustive. Nevertheless, I tried to state a number of my observations. It will be interesting to read yours, in the comments!
Driver for 3D printer
For the correct operation of any 3D printer, you need a special device that will be responsible for controlling the stepper motor. Incorrect installation or malfunction will result in printing problems or damage to the printer itself.
What is a 3D printer driver?
The 3D printer driver is a device whose main function is to control the kinetic movement of the printer's stepper motors. The driver sends commands to the microcontroller that describe the movement of the shaft - the number of steps and direction, at the output receiving a sequence of signals specified in a certain way for the motor winding. The driver in this process is responsible for converting one signal to another.
Manufacturers offer many models of 3D printing drivers that vary greatly in quality. Top models are able to maintain high output currents while maintaining an acceptable operating temperature, and are able to control the motor so that it does not make excessive noise, does not overheat, and the print head moves smoothly, without jerks and accelerations.
Drivers are used everywhere where stepper motors are used: in all CNC machines, actuators, 3D printers, laser engravers, etc.
Modern 3D printers use kinematics and a control method, which consists in the sequential transmission of the coordinates specified for the movement of the hotend. Methods is the generally accepted standard for controlling all devices equipped with a CNC unit. Data transfer is carried out in a specially developed programming language called G-code.
Control boards and drivers are responsible for the physical movement according to the given code.
Boards, in turn, are divided into two types based on their capacity:
- 8-bit.
- 32-bit.
The first 3D printers were designed using the self-replicating mechanism used to quickly reproduce REPRAP prototypes and were based on one of the most common boards used in robotics, the Arduino. To develop the firmware of devices in these cases, a special environment was used - the Arduino IDE. In the future, in order to expand its capabilities, the RAMPS expansion board was additionally developed, which allows you to effectively control the rotation of stepper motors and take into account the zero position using limit switches.
Additionally, drivers were developed to control stepper motors that could be combined with these boards (Pololu drivers).
To date, the installation of such a driver is required for each stepper motor of a printing device controlled by the Arduino + RAMPS bundle. RAMPS is able to work effectively when connected to up to five stepper motors.
Other All-in-one boards are equipped with special pads for Pololu drivers, which are widely used among users.
Many drivers have been developed that are compatible with the boards used in today's 3D printers. The most popular are:
- Driver A4988. The manufacturer produces the device in green and red colors, the maximum divider step is 1/16.
- There are purple and blue devices on the market. The main drawback of the model is the lack of a well-thought-out hold mode, which causes the device to get very hot. Such a chip is recommended to be installed only in conjunction with a powerful heatsink that can compensate for excessive heating. The maximum divider step is 1/32.
- The original driver is made in Germany and the USA, but it is easy to buy a similar one made in China on the market. Copies differ from the original only in the accompanying piping - resistors, capacitors, etc., therefore, when using non-original devices, it may be difficult to select the voltage to power stepper motors. The device is characterized by quiet operation, background noise and engine sounds are minimized by manufacturers.
The driver is equipped with its own chip, which is able to interpolate a 1/16 divisor to 1/256 without creating additional load on the processor.
- Made in China by Makerbase. A distinctive feature of the driver is the wide possibility of adjusting the microstep divider - from full to 1/128. There is no internal share in this driver model. The device is intended for installation on 32-bit boards only.
- Manufactured by Panucatt Devices. The driver is able to support microstepping from full to 1/32 and has well-thought-out protection against excessive voltage and high temperatures. Two model options are available: in the standard version, the voltage adjustment pin pad is shorted, so voltage adjustment can be made by the user in a manual setting format using a screwdriver and a multimeter. In the version with digital adjustment, debugging is performed at the software level and can only be supported by its own controllers - Azteeg X3, X3 PRO and X5 mini V3.
- This model is also manufactured by Panucatt Devices.
The driver is equipped with a sensor that protects it from overheating and high voltage and also comes in two versions - standard and digital. The device is based on the THB6128 chip. Designed for installation on eight-bit boards.
- A new version of the driver from Trinamic and Watterott. A special board via the UART interface is responsible for dividing the microstep. The built-in board allows you to connect the driver to a computer using a USB cable and configure it using your own software.
Installing and configuring the driver for the 3D printer
For the correct operation of the 3D printer, before starting it for the first time, it is necessary to install and configure the drivers.
IMPORTANT! Before debugging, it is recommended to temporarily disable the anti-virus programs installed on the computer. This will help to avoid false triggering on files downloaded from external devices or the Internet.
The installation process takes place in several stages:
- Start the installation by downloading the driver file and running it.
To do this, you will need to log in with an administrator account and run a file called "exe file". Next, following the instructions of the installer, complete the process and connect the 3D printer to your computer using a USB cable. The program will automatically find the device and assign it a COM port.
- Next, you need to download and install a program called Repetier Host. Once the download is complete, launch the program file and wait for the download to complete. After the installation is completed, along with the program, all the necessary accompanying programs will be launched, including slicer programs. During installation, it is recommended to uncheck the box next to the item about installing the Server utility, since it will not be required for further work and will take up device resources unreasonably.
- The next step is setting up the settings for the personal computer. During this, a corrected interface in Russian will also be configured, the necessary scripts and an active link to the help section.
At this point, the Magnum 3D and Magnum 3D Vase slicing profiles will be rewritten, so any changes made by the user should be renamed before starting the process. Otherwise, they will not be saved after reinstalling the program.
- After the installation is completed and the settings are set, you should run the Repetier-Host program and select the COM port to which the printer was connected. This step is mandatory because the installer automatically assigns COM3 to the device, which can interfere with further debugging.
- Next, following the instructions of the program, you need to update the downloaded scripts and restart the computer.
- During the reboot, you will need to press the F8 button and select the "Disable Driver Enforcement Signing" option.
- After downloading, you will need to do the following: open the Start menu, open the Settings tab, go to the Update and Security section and select Recovery. Then, going to the tab "Special boot options", you must select the item "Restart now".
- When the process is completed (the reboot should go through in normal mode), you should open the "Diagnostics" tab, go to the "Advanced Options" section, select the "Boot Options" item and restart the computer again. When the device reboots, a menu will appear on the screen with a choice of parameters that will be used by the system in the future.
IMPORTANT! In order to install an unsigned driver, you must disable automatic digital signature verification by selecting the appropriate item in the menu and pressing the F7 button.
There is an alternative method for installing the driver for 3D printers. It is used if the system to which you plan to connect is 64-bit. In this case, the instructions above will not work.
In this case, when connecting the CNC device to the computer for the first time, for an unrecognized USB Serial device, you must select the driver yourself by opening the "Modems" section and selecting the "Compaq" item, and then the Ricochet Wireless USB Modem devices.
Errors and how to avoid them
During the driver installation process, some errors may occur that prevent the process from completing.
The most common reasons for their occurrence include:
- Technical malfunction of the device. Even if the driver is detected by the system when connected to a computer, if it malfunctions, the installation will not be able to proceed correctly.
- There is a problem with the program being installed. The installer may have been corrupted during download or may have been infected with malicious code. The cause of errors may also be the absence of one or more files in the archive.
- The driver version does not match the installed device. Most often, such a problem is encountered by those users who install a driver downloaded from third-party sites, and not the one that came with the device when purchased. The error may be caused by the fact that the driver version does not match the specific device or operating system version installed on the computer.
Learn more