3D printed luminaires
3d Printed Lighting - Shaper 3D Printing
The Next Big Thing… is here…
Cooper Lighting Solutions introduces a new way to manufacture lighting products using 3D printing technology,
which allows for beautiful designs, textures, colors, and shapes that are distinctive and adaptive to meet the aesthetic and performance needs of the designer’s vision.
The Shaper PrentaLux Products have already received 3 tops honors from:
Interior Design Magazine
2022 Honoree in Lighting
Best of NeoCon 2022
Gold Decorative Lighting Award
Best of NeoCon 2022
Innovation Award
“I found I could say things with color and shapes that I couldn’t say any other way – things I had no words for. ”
-Georgia O’Keefe
“Innovation is the ability to see change as an opportunity, not a threat.”
-Steve Jobs
Image Gallery
Color and Texture Gallery
Ideal for these spaces
Shaper 3D Printing products are positioned to be used in both hospitality settings as well as when performance lighting is needed. Mixing these different lighting shapes and colors will also generate the best combination of aesthetics that can help define mood, ambiance, and adequate levels of light.
Office
National Accounts
Hospitality
Education
Retail
Features and benefits
Shaper 3D Printed Luminaires offer designers the ability to customize different shapes, textures, and colors, to create their own products, in a way that has not been done before.
Product Specs
- Product range from 8”x8”x8” to 17”x17”x17”
- Four CCTs of 2700K, 3000K, 3500K, and 4000K, @ 90CRI.
- 16 or 18 neutral color options and 3 inner and 3 outer textures.
- Lumen output ranges from 1000-7000 for Performance Pendants and 100-600 for Hospitality Pendants.
Design Freedom
Similar pendant products on the market are made with materials that may cost more in both manufacturability and raw materials. For example, some of the 3D printed textures might emulate ceramic textures … With 3D printing technology, a designer can be inspired by a texture, create it digitally, then apply it to a lighting fixture.
Compliancy
Shaper PrentaLux 3D printed products are BAA, or Buy American Compliant. Products are UL and cUL listed. And, these products are RoHS compliant.
Interested in learning more?
Top3D Printing: The Next Frontier in Luminaires?
Photo Credit: Signify
There has been much discussion over the years regarding lighting and controls impact on the environment. With little debate, the LED revolution has significantly improved energy efficiency of light sources. Additionally, this has allowed for both more efficacious luminaires and creativity in fixture design due to the small footprint of the LED light source.
As light sources have shrunk over the years, luminaire manufacturers have had to consider brightness, luminous intensity, and glare, amongst other important characteristics, when designing new fixtures. Other than greater efficacy in the light source, smaller apertures, and power supplies, what else has changed within the fixture? The answer is very little until recently.
3D printed luminaires are beginning to offer more versatile and flexible options for non-recessed products. For those of us who are used to stamped housings and spun shades, the utilization of 3D printed luminaires opens a whole new world of options for fixture specification and capabilities.
THE ART OF 3D PRINTING
I was first introduced to 3D Printing at the University of Tennessee’s College of Architecture and Design’s Fab Lab. When I saw objects being designed and created in real time with a 3D Printer, it captured my imagination as to what could be created. Since then, people around the world are pushing the limits of 3D printing as homes, boats, casts for broken bones, and so many other useful products are now being explored as possibilities with this technology.
What is 3D Printing anyway? Fortunately for the design community, it all starts with a concept. The initial steps of creating a 3D object is putting your own design into AutoCAD or another animation modeling software.
In the lighting industry, one of the key things to note is that 3D printing is characterized as “additive” manufacturing. This means that a solid, three-dimensional object is constructed by adding material in layers. Decades of manufacturing in the lighting industry has consisted of subtractive manufacturing. This process is when an object is created by cutting, stamping, or otherwise removing raw material to form a specific shape. From this process scrap material is produced that ideally can either be reused or recycled.
Once you have finalized your design, the product file is sent to the 3D Printer. Depending on the printer and its capabilities, you get to choose your specific materials, including finish color(s) and texture. This selection is important more than just for finish distinction but for the substance of the material as it can impact the products rigidity, appearance, and structure. While printer processes vary, the material for lighting products is usually squeezed or otherwise transferred from the printer onto a platform.
Credit: Signify
A 3D printer then makes passes (much like an inkjet printer) over the platform, depositing layer on top of layer of material to create the finished product. This can take several hours or days depending on the size and complexity of the object and printer. For lighting products, most of the current printers are smaller so the critical variable is the complexity of the product shape.
SUPPORTING THE CIRCULAR ECONOMY
A circular economy uses resources more effectively by creating rather than wasting, using rather than owning, and reusing rather than disposing. According to the Ellen MacArthur Foundation, the circular economy model looks “beyond the current take-make-waste extractive industrial model, a circular economy aims to redefine growth, focusing on positive society-wide benefits. It entails gradually decoupling economic activity from the consumption of finite resources and designing waste out of the system.” The circular economy has three principles: design out waste and pollution, keep products and materials in use and regenerate natural systems.
Credit: Signify
A manufacturer engaged in 3D printing luminaires, or components thereof, inherently help support the circular economy. A company like Signify has invested heavily in 3D printing and is now creating luminaires through this process. With no paint, and less parts and screws, Signify and other manufacturers, significantly reduce waste. Additionally, they create a higher serviceability and products that are upgradeable due to their smart, modular design. One of the key advantages of these modular designs is that at the end of life, dismantling of these products for recycling becomes easier. Closing the material loop within a factory, especially with 3D Printing, an organization can recycle their own material almost eliminating waste.
A “Take Back” program literally takes sustainability to the next level. This concept allows you to easily update your luminaires whenever you desire and have the new luminaires printed out of the old materials. This means you can stay up to date with the latest trends while still being smart about material use – and most importantly, re-use.
ENABLING DESIGN
Understanding the technology and sustainability narrative with 3D Printed Luminaires is important but putting the technology to use is the next step. 3D Printed Luminaires enables the designer a new level of design flexibility and creativity. While “standard products” exist, one of the real opportunities with 3D printing is designing and having the ability to create the luminaire you need and that the project requires. Does your design call from a one-of-a-kind statement product with a unique finish? Perhaps it’s as simple as needing a pendant from one family in a multitude of sizes and finishes. As the range of options in a typical lighting catalogue may be limited, 3D printing’s options continue to expand.
The world before 3D printed luminaires has had a typical, repeatable story. A project specific fixture, unique, custom, or modified, is often accompanied with “set up costs”, custom finish fees, or perhaps simply an extended lead-time. With 3D printed luminaires, set up cost goes away. Finish options are available by the hundreds and product configurations by the thousands. Often the products from time of order are two to four weeks to create…and often faster. Fixture creation in this model is more focused on the product and designer’s needs than a “manufacturer’s capability and offering”. 3D printers also don’t have a timecard to punch. A manufacturer can simply start the printer at the end of the day and have products being built all night.
Credit: Signify
While the incumbent technologies and production methods aren’t going away anytime soon, 3D printed luminaires give the design community an enhanced product offering that has not previously been available. Removed are the days of long lead times, extraordinary cost, and project delays for producing “just the right product”. Today the lighting community has a technology that enables project lighting enhancements that is sustainable and cost effective.
The future of 3D Printed Luminaires won’t be held to decorative shades and bespoke designed luminaires. Track heads with specification grade optical distributions, high and low bays, surface mounted luminaires across a range of price levels and functionality are just a few of the products that we will see very soon.
Our future is bright and will continue to be driven by technology advancements. Will 3D printed luminaires be the “next frontier” in lighting? It’s possible. The 3D printed luminaire’s place as a technology option that helps enable further enhanced lighting design capabilities seems undeniable.
This article was originally featured in the April issue of designing lighting (dl)
Signify offers 3D printed lights made from recycled CDs
News
3D printer.
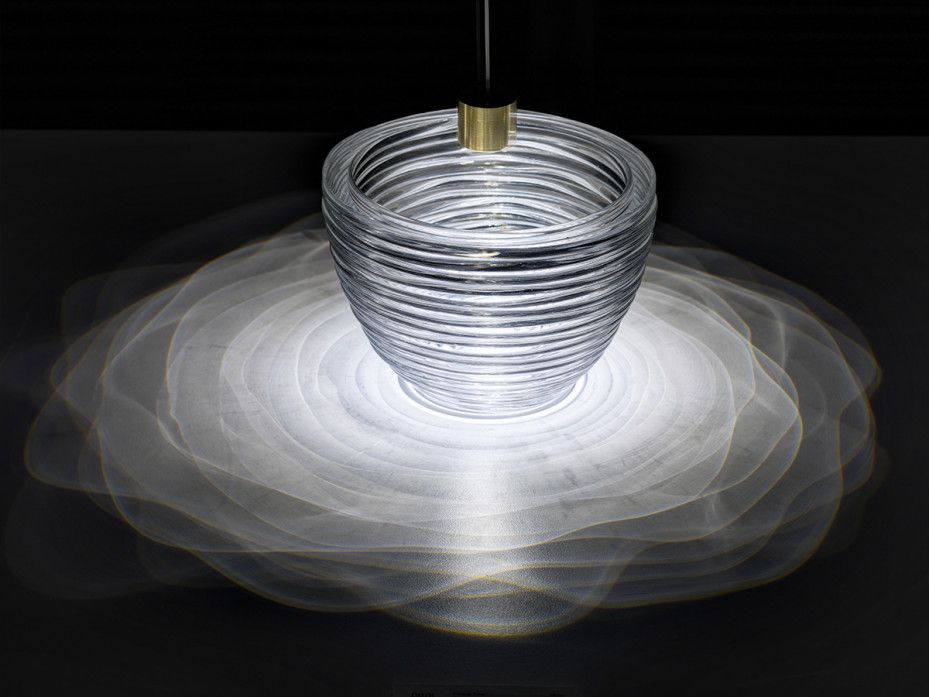
The service allows you to create decorative lamps according to individual requirements. Users get a choice of basic design with the ability to change the size, color, texture and shape of the body, as well as a choice of LED lamp type. In addition to classic LED lamps, Philips Hue smart lamps can be used in fixtures. Delivery of the finished product is carried out to the specified address within two weeks. The service has passed the pilot stage in the Benelux countries and is now available in other European countries. In Russia, Philips 3D printed luminaires are already decorating several new Pyaterochka stores.
Signify 3D printed luminaires contribute to the achievement of sustainability goals. The base material is recycled polycarbonate. The carbon footprint of such a lamp (excluding electrical elements and light bulbs) is 47% less than that of a standard metal one. It also has fewer parts, no glue, and is one-third lighter, helping to reduce the carbon footprint of shipping. In 2020, the company intends to achieve zero carbon emissions.
“This is the first online service in the consumer goods segment that allows you to create sustainable lighting fixtures according to individual requirements and taste preferences of customers. It can be easily integrated into third-party online stores, giving shoppers more choice. This is a new word in the field of lighting, which proves the global leadership of Signify in the production of innovative and sustainable lighting solutions. Philips and Sony first introduced the iconic CD technology at the beginning of 1980s. Today, we pay tribute to it by creating high-quality decorative lamps from recycled discs,” said Khalid Aziz, Head of Venture Capital at Signify.
Signify uses both virgin and recycled filaments to 3D print lights. In the latter case, old CDs serve as the main source of material. The company's first 3D printed product was a Philips LED table lamp: twenty-four disks must be recycled to produce one such lamp. Over the next year, Signify plans to add a recycled option to any 3D printed product, as well as add professional lighting solutions to its 3D printed product catalog.
Do you have interesting news? Share your developments with us, and we will tell the whole world about them! We are waiting for your ideas at [email protected].
lamp Philips lamp lighting Signify
Follow author
Follow
Don't want
2
Article comments
More interesting articles
ten
Follow the author
Follow
Don't want
German startup iFactory has announced the third model of the pipeline FDM 3D printer with unlimited. ..
Read more
6
Subscribe to the author
Subscribe
Don't want to
A new method called iCLIP was created with the participation of Professor DeSimon - co-founder and CEO ...
Read more
53
Subscribe author
Subscribe
Don't want
As we all know, a true 3D printer must have a solid acrylic body, high quality...
Read more
Philips Tailored lighting
Discover the series
3D printed lighting supporting circular economy
Signify is once again transforming the lighting industry with a revolutionary new technology that makes it easy and simple to create custom luminaires. With 3D printing, you get a customized lighting solution, contributing to a sustainable future.
Download brochure
A flexible, fast and reliable solution for your next project.
Custom design for everyone
Using our easy-to-use online tools, you can create your own 3D printed lights. Choose from a large range of color combinations, transparencies and textures for almost endless possibilities.
Learn more
Fast delivery
Once you've designed your ideal luminaires, you won't have to wait long for delivery. Thanks to local printing, shipping is fast - we can print and deliver your lights in just four weeks. And the installation is easy because the fixtures were made according to your requirements.
Learn more
Originally designed for low environmental impact
We are proud to tick many sustainability boxes with our innovative lighting products. The materials we use for printing your designs are made of 100% recyclable polycarbonate. We maintain our focus on a fully green product lifecycle – from design to production to re-use and recycle.
Learn more
Hospitality
No more searching through endless directories. Create exactly the atmosphere you are looking for, tailored to your space and your brand.
Learn more
Retail
Create a unique in-store experience that can be easily upgraded to stay on trend while maintaining sustainability practices.
Learn more
Office
Help your employees feel at home at work while facilitating the renovation process with fixtures printed to your exact specifications.