Cheap 3d printer enclosure
DIY 3D Printer Enclosures: 7 Best Cheap & Free Projects
Is your printer not pairing nicely with heat sensitive filaments like ABS? Warping problems rearing their ugly head? Or do you need to quieten the noise when printing your latest creation?
These are common issues that all makers encounter at one point or another, that generally require a pricey enclosure to fix.
Top Picks
Best 3D Printer Enclosures – Full Round-Up
Best Cheap, DIY 3D Printer Enclosures
IKEA Lack Table: Best Repurposed DIY 3D Printer Enclosure
Exercise and Kids Mats: Best Basic DIY 3D Printer Enclosure
Wood Enclosure: Best DIY 3D Printer Enclosure for Large-Format 3D Printers
Sound Proof Enclosure: Best DIY 3D Printer Enclosure for Noise Reduction
Best Ready-Made 3D Printer Enclosures
Official Creality Enclosure
Wham Bam HotBox V2 Enclosure
Repurposed Photography Tent Enclosure
3DSourced is reader-supported. When you buy through links on our site, we may earn an affiliate commission. Learn more
But, if you’re on a tight budget, then it’s possible to fashion a cheap and easy DIY or homemade 3D printer enclosure that works just as well as the manufactured alternatives.
In this guide, we’ll walk you through the best cheap DIY 3D printer enclosure projects out there in an effort to help you save money. And, for those that shudder at the thought of a DIY project, we’ve included a couple cheap buyable options that won’t cost you an arm and a leg.
What Is a 3D Printer Enclosure?An enclosure sits over and on top of your 3D printer, creating an insulated cocoon that protects it from temperature changes by trapping heat inside, effectively transforming an open-frame printer into a fully enclosed printer.
The main goal of an enclosure is the space around the printer warm and consistent, which opens the door to better quality prints and more sensitive filaments like Nylon, ABS, and PC.
An enclosure also shields the printer from airborne debris like dust, and keeps in pungent smells and toxic fumes that can be harmful to users. Additionally, certain enclosures can also act as noise dampeners to help contain the noise during printing.
Best 3D Printer Enclosures
Best Cheap, DIY 3D Printer Enclosures
Best Repurposed DIY 3D Printer Enclosure – IKEA Lack Table
- Price: Check latest price at Amazon here
The IKEA Lack enclosure is an absolute classic DIY project among makers, especially those around for the early days of 3D printing’s resurgence in the early 2010s.
The idea is simple: repurpose a sturdy, and cheap, IKEA Lack table by fitting it with panels, usually acrylic, using a set of 3D printed brackets to hold them in place.
You can either source and cut the panels yourself, or buy one of the many pre-cut kits available on sites like Amazon. The kits typically include panels cut to size with cabling holes, mounting hardware, and even magnets to create latched doorsAs for the brackets, Thingiverse comes to rescue as it so often does with no shortage of options, including this one.
Once pieced together, the IKEA Lack is large enough to accommodate most small to average-sized printers and works to create the perfect temperature to print with ABS, PC, Nylon, and more. With see-through panels, visibility is among the best out there and you can monitor prints from all angles. Fashioning a door for access shouldn’t be too much trouble either, and, as above, most kits come with a hinged door or removable front panel.
As the frame is made of wood, it’s also fairly easy to attach add-ons like a thermometer or LED lights, for example. If you want to push the boat out, you can also stack several IKEA Lack tables for extra storage, another printer, an external spool holder, or a filament storage shelf.
An IKEA Lack enclosure plus shelves for holding 3D printing supplies.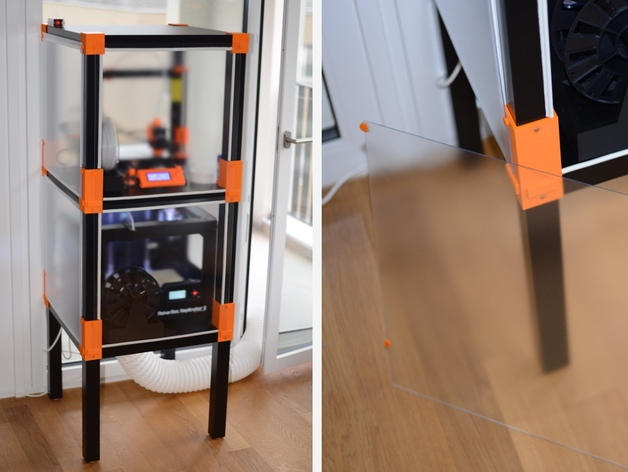
The only downside of this DIY 3D printer enclosure project is that it’s quite hands-on compared to the mats above or a pre-made alternative. The kits help somewhat, but expect some troubleshooting along the way and creative problem-solving, especially if you’re customizing the enclosure with extra features.
Best Basic DIY 3D Printer Enclosure – Exercise and Kids Mats
Rather curiously, foam exercise and kid’s play mats make for a solid DIY 3D printer enclosure option. These tend to have interlocking teeth that allow you to piece together a cube that can house a standard size printer, like an Ender 3 or Anycubic Kobra, in a matter of seconds. There’s no need for tools, screws, or any additional components.
These mats are typically made of ethylene vinyl acetate, which is up there with materials like glass for insulation – they do a good job of keeping the air from escaping. As such, they are able to maintain enough of a stable environment for printing the likes of ABS, and per regulations in most countries they are non-flammable.
That said, the manufacturing process means the teeth don’t always provide a perfect seal, so some external air can seep into – but not enough to spoil a print.
Furthermore, access isn’t all that great as you’ll need to remove a panel to reach the printer, though it’s possible to carve out a whole and put in an acrylic window if you’re that way inclined.The user built this enclosure for noise suppression primarily. Source: Reddit
At roughly $20 for a pack of six panels, kids mats are hands down the cheapest, and yes basic, DIY enclosure option out there. A go-to for makers reluctant to spend a lot of money on an enclosure and for those daunted by a hands-on DIY project. The mats make for surprisingly solid noise cancellers due to the density of the foam, so another advantage to this option.
Best DIY 3D Printer Enclosure for Large-Format 3D Printers – Wood Enclosure
While the above options are a great way to save on costs, they are well suited to large format printers. If you own a big printer like an Ender 5 Plus, then a wood enclosure may very well do the job. Wood offers flexibility when it comes to dimensions, allowing you to make a box that fits your printer.
Beyond the size advantage, wood enclosures also surpass other options for overall aesthetics, insulation, and to a certain extent visibility. Wood is a reliable insulator and will prevent warping, keeping the space around your printer toasty as long as you fill in any air gaps.
As for visibility, you can either construct a wooden frame then attach acrylic panels on all sides, or use wood panels and fit a see-through front panel for monitoring and access.
All this does come at a cost, though having spare wood suitable for the project lying around can help keep the bill down. Otherwise, there are components like glue, screws, brackets, and trim to consider. Overall, and being thrifty, it’s possible to keep the budget to between $50 and $100.Plywood enclosure built for an Ender 3. Source: Reddit
As for assembly, some DIY experience is recommended, but it all depends on the complexity of your plans. It’s also worth noting that wood is workable, you will need tools such as a drill and saw.
Best DIY 3D Printer Enclosure for Noise Reduction – Sound Proof Enclosure
The project comes to us from an Instructables post – with plans, measurements, and list of materials included. It’s an involved project that likely requires several days to complete, positioning it as one for the experienced tinkerers and builders out there.
Once constructed, it excels at noise dampening thanks to a combination of MDF panels, wooden slats, and ample insulation foam. The enclosure is designed to have mirrored latched front doors that open for easy access to the printer, while see-through panels on the doors giving you an unobstructed view of the printer at work. The enclosure has a massive footprint compared to most other enclosures, and is likely to dominate any room where it’s set up.
Aside from keeping noise from creeping out, the foam also works to keep a stable temperature inside the chamber, while the whole design also proves excellent at keeping moisture, dust, and other external unwanted debris from getting in.Source: Instructables
Due to its size, which you can adapt to house all types of printers, you can customize the interior to your liking: mounted spool holder and LED lighting being two popular options for those who’ve undertaken the project.
For all that it offers the estimated $150-$200 building and material costs are reasonable and packed with value in our opinion. The beauty is that you can adapt the project to your needs to save money.
Best Ready-Made 3D Printer Enclosures
While DIY 3D printer enclosures made at home offer the most cost-effective route, there are pre-made options for those that want an easy and quick option who are happy to pay a reasonable price.
Official Creality Enclosure
- Price: Check latest price at Creality here / Amazon here
The Official Creality Enclosure is a straightforward and affordable enclosure option designed specifically for 3D printers by one of the largest manufacturers in the industry.
The enclosure takes on a tent format – simply position the printer inside and zip the enclosure to create a heat-sustaining space. It consists of a rigid iron frame that takes a matter of minutes to piece together (or take down for storage), along a fabric tent that consists of a heat-retaining aluminum film and flame retardant outer layer.
Access is well covered with a front-facing zip door, and velcro openings positioned on the side and top of the enclosure. A front-facing window means you can monitor prints without opening the enclosure and releasing heat. Source: Creality
There’s even a tool holder pocket to help keep your printing space tidy. This composition offers a degree of sound proofing, but it’s by no means the best option if you’re looking to keep noise down in a small apartment or at night.
Creality’s enclosure comes in two sizes:
- One suited to mid-format printers like the Ender 3 (480 x 500 x 720 mm)
- And a larger variant with space to house a large-format printer like an Ender 5 Plus (750 x 700 x 900 mm)
Depending on the size you choose, expect to pay anywhere from $60 to $90 for Creality’s Official Enclosure.
Wham Bam HotBox V2 Enclosure
The Wham Bam HotBox V2 enclosure is a step up from the Creality Enclosure in both construction and price, for the DIY-averse out there. The focus is on an easily-assembled and hassle-free enclosure solution for those wanting the convenience of a paid-for option.
The Wham Bam HotBox V2 comes fully assembled, and setting it up is a matter of closing two zips to create the enclosure cube. Slide the printer in and you’re good to go. When you’re done, the enclosure folds flat for easy storage.
The HotBox V2 features a semi-rigid, lightweight polymer honeycomb structure that’s also insulative, consisting of a Nylon 600D outer layer and insulating internal lining. These work well to keep the heat in and block out externals like drafts and dust. Access is through a front-facing velcro panel when the printer is working away, but you can open up the enclosure fully via the zips mentioned above. Source: WhamBam3D
Elsewhere, the Wham Bam HotBox V2 includes several metal-lined filament passages giving you the option to mount the spool holder externally, and even plug seals should you decide not to use the passages. There’s also an air vent port should you want to install an air-filtration system, a thermostat for monitoring, and a cable passage for your power supply cabling.
The enclosure measures up to 568mm x 568mm x 484mm, which is enough for average-sized printers, so not a great option if you’re running a large-format printer. In that case, consider the HotBox’s larger sibling, the Wham Bam HotBox Mega enclosure.
Repurposed Photography Tent Enclosure
Sitting mid-way between a DIY enclosure and pre-made, it’s possible to repurpose a cheap, standard photography tent into a viable 3D printer enclosure.
There’s no set formula, but the gist is to buy a low-cost photography tent off Amazon, ideally one with zips or velcro to create a sealed inside, pop the printer inside, and print away with heat sensitive filaments.
These cost anywhere from $20 to $40 so even those on a tight budget can sidestep an involved DIY project and have an enclosure. They are also available in a range of sizes, so even a hulking large-format printer should fit with space to spare.
These tents have surprisingly respectable insulative properties and can quite comfortably maintain the 30-35° needed for materials like ABS. There’s next to no assembly and setup involves reacting the tent, making it the least DIY of our DIY options.A photography tent repurposed into a 3D printer enclosure. Source: Mikolas Zuza
There is one downside, photography tents aren’t exactly known for their fire retardant properties, so it’s worth taking time or paying a tad more for a material that won’t burst into flames when temperatures crank up. Visibility isn’t near inexistent as most tents have an opaque white color that isn’t see-through, but at this price, this is a minor complaint.
All things considered, we’d suggest the photography tent option for those that want an enclosure for the sole purpose of storing and protecting their printer from dust and debris while it isn’t in use.
DIY 3D Printer Enclosures – Buying Guide
Here are a few tips to keep in mind when building or buying a 3D printer enclosure.
Size
An obvious one, but make sure the enclosure is large enough to house your printer. This is especially important if you have a large-format printer or if the filament spool holder is located above the printer.
Does it fit inside the printer or is there a way to house the spool outside of the chamber and route it into the enclosure?
If space allows it, we recommend an enclosure that’s slightly larger than the printer to give you room to work and move the printer. Be careful here: too big and the space will take longer to heat up and it will be harder to maintain higher temperatures.
Build Time
The length of time needed to complete an enclosure differs depending on the project. A from scratch chamber where you need to build the frame and paneling will naturally take longer than working with an IKEA Lack table as a foundation.
Similarly, using a photography tent should take minutes to set up compared to the hours required for most other enclosure projects.
Build Costs
Though DIY projects almost always work out cheaper than buying a pre-made enclosure, it’s worth getting an idea of the cost involved. These include any materials, hardware, and pre-built components you may need.
Accessibility
Make sure the enclosure build allows you to access the printer to remove prints, load filament, tighten bolts, and level the bed. Look for hinged doors or removable panels for ease of use.
You may also want to consider whether the enclosure sits over the printer to easily move it when printing with filaments like PLA that don’t benefit from an enclosure.
Visibility
Not all makers are fussed about having a perfect view of their printer through an enclosure, but having good visibility can help monitor prints. Consider using see-through materials like acrylic panels or plexiglass, or installing windows, for example.
Safety
- Is an enclosure safe?
- Are you using fire retardant materials?
- Can the materials sustain the temperatures you expect to maintain inside the exposure?
- Are pets/children able to get inside the enclosure?
- Is the printer/enclosure located next to a window or in a well ventilated space?
Safety is vital so it’s important to spend some time mulling over these points.
Noise Reduction
If your need for an enclosure is driven by a desire to lower noise levels that consider the noise dampening properties of the materials used.
Do you need to spend more and include sound dampening? Multiple layers?
Optional Extras
Optional extras like an air-filtration system, thermostat, cameras, LED strips, and so on are worth considering for remote monitoring of your prints, visibility, or for safety reasons.
Do You Need an Enclosure For Your 3D Printer?
It depends on what you’re printing with. If you’re printing exclusively with PLA, you’re unlikely to see much benefit to equipping your printer with an enclosure. However, with ABS, for example, an enclosure can greatly enhance the quality of your prints and prevent warping.
The other benefits mean that some still use 3D printer enclosures with PLA: protecting your printer from dust and quietening down operational noise – but beyond these, there are no other benefits.
Another situation where an enclosure easily proves its worth is if you’re printing in a busy environment such as an educational setting or in a home with children and pets. An enclosure protects not just people/pets from high temperature components and fumes but also the printer itself from curious interfering hands and paws.
Read more: the best 3D printers for kids.
Benefits of a 3D Printer Enclosure
Improved Print Results
An enclosure is all about creating a controlled environment around your printer so it can thrive.
This is achieved by shielding the printing from drafts, guts, and temperature fluctuations to create a stable thermal environment. Temperature control this mitigates instances of warping and layer adhesion issues, which translates to improved print quality and results.
Broader Filament Compatibility
Though budget 3D printer manufacturers love to plump their filament compatibility list with as many materials as possible to tempt sales, in most cases this isn’t the case.
Certain filaments, mainly heat sensitive filaments like ABS, Nylon, ASA, HIPS, and PC, are extremely susceptible to changes in temperature and gusts of cool air. Ender 3 enclosure made from repurposed IKEA drawer. Source: Reddit
Open-frame printers simply aren’t designed to work well with these materials. To create decent quality prints with these filaments, a 3D printer enclosure is a must-have accessory.
For more details, be sure to check out our guide to the best enclosed 3D printers.
Noise Reduction
The whirr of fans and mechanical whizz of stepper motors can combine to produce substantial amounts of noise.
Having an enclosure provides a degree of noise dampening and isolation that’s useful if you’re printing at night, when you’re working, in a small apartment where it’s hard to avoid the noise, or near other people bothered by the noise.
Contain Smelly and Toxic Fumes
By offering a sealed environment, an enclosure contains fumes and odors produced during 3D printing.
This can be particularly beneficial when working with toxic filaments like ABS, which emit fumes that can cause irritation and smell. You can even install an air filtration system, carbon filter, and vent fumes outdoors as an extra safety step.
Keeps You Printer Clean and Free of Dust
Whether it’s the lubricant on the rods that seems to attract dust like a black hole gobbling up light, or the layer of dust that always seems to settle on the print bed between printing sessions, there’s always dirt and grime gunning to spoil your pristine printer.
A 3D printing enclosure provides protection from external debris, extending the lifespan of your machine and increasing the quality of your prints. It also offers a convenient storage solution for when the printer isn’t in use.
FAQs
Do You Need an Enclosure for a 3D Printer?If you want to print using heat sensitive temperatures like ABS and Nylon, you will need an enclosure for your 3D printer. The enclosure ensures the environment around the printer maintains the stable thermal environment needed to avoid common issues related to insufficient temperatures like warping.
There’s no need to heat a 3D printer enclosure. The heat generated by your 3D printer will produce the increase in temperature required for the enclosure to function as intended, which is to maintain a stable temperature and cut out drafts and cold air. The aim is to prevent heat escaping rather than providing additional heat.
How to Build a 3D Printer Enclosure?There are many ways to build a 3D printer enclosure using a variety of materials. Popular options include repurposing old furniture like IKEA Lack tables in a 3D printing cabinet, using photography tents, building a sealed box from acrylic panels and/or wood, mdf, plexiglass, and even old household appliances like dishwashers.
Do 3D Printer Enclosures Need Ventilation?In an ideal world, a 3D printer enclosure will have an air filter and a vent funneling fumes and particulates to the outdoors, especially when using noxious filament types like ABS. However, this setup tends to introduce cool air into the enclosure chamber, reducing its capacity to maintain a steady temperature. Due to the cost of these features and their potentially negative impact on print quality, it’s possible to do without as long as the printer and enclosure is set up in a well-ventilated area.
No, you don’t need a 3D printer enclosure for PLA. If anything, PLA suffers from the additional heat maintained by an enclosure, which can affect the rate at which the filament cools as it’s printed leading to issues like elephant’s foot. For the best results using PLA, print without an enclosure.
Do You Need a 3D Printer Enclosure for PETG?No, you don’t need a 3D printer enclosure to print with PETG and get good quality prints. Much like PLA, it melts at a relatively low temperature, so having an enclosure can push temperatures high enough to cause issues like elephant’s foot. That said, PETG is susceptible to poorly dialed cooling and an enclosure can help if tweaking settings fails to fix the issue.
Yes, a 3D printer enclosure is a must-have when printing ABS. The filament requires a stable thermal environment free of drafts, which is exactly what a 3D printer enclosure is designed to do. ABS needs to cool slowly and steadily to produce good quality prints, which isn’t possible without an enclosure.
Do You Need a 3D Printer Enclosure for Nylon?Yes, when printing with Nylon, a 3D printer enclosure is necessary. As a high temperature filament Nylon, you need to print in an environment when the temperature fluctuates very little otherwise issues like warping and stringing will pop up ruining prints.
How Do You Insulate a 3D Printer Enclosure?While it’s possible to insulate a DIY 3D printer enclosure with a material like foam, cardboard, and cork, the best option is to build the enclosure using materials with naturally solid insulative properties such as glass.
If you enjoyed this post, also check out our other DIY and 3D printer enclosure articles:
- Ranking The Top DIY and Ready-to-use Enclosures For Your Ender 5 (and Pro / Plus)
- Our List of The Best Prusa Enclosures: Buyable & DIY Options
- Buy or DIY These Ender 3 Enclosures (Pro/V2)
- Fun and Easy 3D Printing Projects For Beginners
- Make It Yourself: Filament Dry Box Projects You Can Make at Home
- Make It Yourself: 3D Printed Home Décor Projects For Your Home Or Give Away As Gifts
How to build a simple, cheap enclosure for your 3D printer
Maybe you have already seen some of those fancy enclosures people build for their printers. How do they work? And do they work? Today, we will shed some light on this matter! Plus, we are going to dive into patent wars and explain why not all printers come with an enclosure. To top things off, we will even give you a full guide with information on how to build an enclosure for your own printer. But first, let’s start with the fundamental question: what is it good for?
- Stable printing environment – Drafts can negatively impact your print. An enclosure will keep the temperature stable and high. Big differences in ambient and printing temperatures can lead to warping and shrinking of the printed object, especially when printing with ABS. Layer adhesion may also improve with higher ambient temps.
- Reduce and contain smell – Some filaments (looking at you, ABS!) can release unpleasant fumes during printing. An enclosure will contain these fumes, and you can quickly vent them outside through an open window when the print finishes.
- Noise reduction – As if you needed the MK3 to be any quieter 🙂 But another level of sound isolation can’t hurt, especially if you place the enclosure next to your work desk or in a living room.
- Dust collection – The bearings and smooth rods will appreciate the reduced amount of dust that settles on your printer.
- It’s fun to build 🙂
However, if you’re not printing with ABS or other high-temperature filaments that suffer from warping, you won’t see much of a difference. You might actually want to keep the enclosure open with, for example, PLA to ensure there’s enough cool air around the printer for the part cooling fan.
Enclosure for the MMU2S
If you own the MMU2S, we created a modified version of the enclosure – check it out here.
Why aren’t all the printers on the market enclosed by default?
There are two factors here – price and patents. There is no doubt that the rise of consumer 3D printers was delayed by patents. Companies like Stratasys, Zcorp or 3D Systems have patented nearly every 3D printing technology you can think of. It’s pretty crazy when you look at the sketches from 1980s-1990s and realize just how much some of the current 3D printers are similar to them.
It was only after these key patents expired in 2009 (20 years after application) that the RepRap movement started. And cheap, easy-to-build 3D printers quickly started to be developed. Even though most of these basic patents have already expired, some of them (most importantly the ones owned by Stratasys) are either still active, or have just recently expired. For example, Stratasys’s (still active) patent describes an apparatus “That builds up three-dimensional objects in a heated build chamber” (…) “The motion control components of the apparatus are external to and thermally isolated from the build chamber.” That means if you put the stepper motors outside of an enclosure, you can’t sell the product, as it would violate the patent.
Another obstacle is the price. We have considered and even developed a Prusa enclosure quite a while ago. It was made mostly of Plexiglass. Our target was $90 price tag and considering the packing, shipping and material cost, we just couldn’t make it work. It makes much more sense to build the enclosure yourself from locally sourced materials.
How hot should the enclosure be and can the PSU stay inside?
Let’s get something straight, we are not targeting really high temperatures inside the enclosure. You don’t need an extra heater. The printer itself produces a lot of heat and all you have to do is to not let it escape. The goal is to achieve stable temperatures without any sudden changes from wind or draught. Even just 35°C inside the enclosure will make a massive difference, increase layer adhesion and may prevent ABS from warping.
The PSU is not made to work in extremely hot environments. By keeping the PSU in temperatures above 40-50°C can significantly shorten its lifespan. Ideally, you’d place the PSU outside the enclosure. You can even place the LCD outside to be able to control the printer without letting the hot air out.
2 simple enclosures
Photo studio tent – no work required at all
An enclosure can often be created from an object originally made for a completely different purpose. This photo (80×80) tent can be bought on eBay or Aliexpress for about $15-20. And all you have to do is place the printer inside the tent. It’s made of textile material, which means it’s porous. A textile enclosure won’t let you reach crazy high temperatures, so you can even keep the PSU inside. We reached temperatures around 38°C after 10 minutes of printing inside a room with the ambient temp. of 26°C – that’s a significant improvement. And as a bonus, you have a photo tent for your prints 🙂
Ikea Lack – when you care about looks as well
Using Ikea Lack as an enclosure is the most popular choice among the 3D printing community. If you search online, you’ll find dozens of Ikea Lack enclosure designs. The table can be bought for under $10 and has almost the perfect size for Prusa printers. You can stack the tables on top of each other to create bays for multiple printers, or use one as filament and tools storage. Even though some of the existing enclosure designs are pretty good, we wanted to give it our own spin.
Advantages of our enclosure
- PSU placed outside in a clip-on holder, but easily placed back if you need to move the printer
- LED lighting connected to the printer’s PSU
- Hinges built into corner extensions
- Double-door opening
- Individual tables can be lifted at any time
What you’ll need
Printable parts
Ikea Lack enclosure main parts
Frame brace replacing the PSU for the MK3 (silver PSU)
Frame brace replacing the PSU for the MK3 (black PSU)
Frame brace replacing the PSU for the MK2/S (remix by Martin Schnur)
60 degree heatbed cable cover for the MK3
45 degree heatbed cable cover for the MK2/S
Construction
- 2x or 3x Ikea LACK table
- 4x Neodymium magnets 20mm x 6mm x 2mm
- 3x Plexi 440 x 440 mm, 3mm thick (if you’re in the US, try Queen City Polymers)
- 2x Plexi 220 x 440 mm, 3mm thick
Electronics
- Fire/smoke detector
- Indoor/Outdoor Thermometer
- LED stripe 24V, 30 cm
- 24V for MK3, 12V for MK2/S
- If you want to use a 12V LED strip with the MK3, use a separate power supply.
- Twin cable, 100 cm
- 2x WAGO 221 or similar compact lever connector
Screws
- 12x 6×20 mm (12 x 3/4″)
- 4x 6×50 mm (12 x 2″)
Printed parts
- Upper table (enclosure box)
- Lower table (support table)
- Spool holders
Tools
- Philips screwdriver
- Allen keys
- Super Glue
- Drill + 3 mm wood drill + 10 mm wood drill
- Measuring tape
- Marker
Enclosure (upper table) assembly
Upper corner standoffs installation
Attaching the legs
LED stripe
For about $12, you can buy an LED strip with a power supply, like this one. However, if you’re feeling a bit adventurous and have some experience with wiring up electronics, you can power the LEDs directly from the printers power supply. Remember, that the MK3 runs on 24V, whereas MK2/S runs on 12V, so make sure you buy the correct LEDs.
Spool holders
Smoke detector installation
Place the smoke detector in the rear part of the table so it will not obstruct filament insertion or won’t get in the way when you’re taking the printer out from the box.
Bottom corner standoffs installation
Before you start screwing the bottom standoffs, make sure you place the Plexiglass in first. As soon as you tighten the standoffs, the Plexiglass will be fixed in place, and you won’t be able to remove it. This means you can easily lift this section of the enclosure without worrying that the glass would fall out. Note, that one of the four standoffs has a hole for cable pass-through. Make sure you place this standoff on the left side so that the cables can be routed directly to the EINSY board.
Support table (lower table) assembly
PSU holder
Electronics do not thrive in higher temperatures inside the enclosure. To preserve PSU in good condition, it’s better to place it out of the box. It is even safer!
- Unplug the printer from the power socket. Remove zip ties on the frame to release PSU cables. (Tighten the rest of the cables with new zip ties.)
- Disconnect the cables from the EINSY board. Do not forget to unplug the Power panic sensor as well.
- Unscrew the PSU form the frame.
- Hold the PSU next to the rear left leg (the one with the cable pass-through). Tighten the PSU holder printed part with two screws and then install PSU catcher printed part.
- PSU is now fixed, but it is possible to slide it out when you need it.
- You can replace the PSU on the frame with this printed part to ensure the rigidity of the frame.
Frame brace and right-angle cable cover
After removing the power supply from the frame, it’s possible to replace it with a printed part and ensure frame stiffness. The heatbed cables may hit the plexiglass in the back of the enclosure. To prevent this from happening, print an alternative 60 degree heatbed cable cover. (EDIT: Users reported several problems with the right angle one shown in the video and on the pictures below, so we switched the suggestion to the 60 degree one).
Plugs fixing and magnetic handles
Fix the four bottom plugs. One of them has a hole for cable pass-through. Place it in the rear left corner of the enclosure. Glue two magnets to the door stopper and screw it to the front of the table. Leave enough space for the plexiglass and the handles (1 cm).
Finished enclosure
Now just stack the two tables on top of each other and the enclosure is complete. Optionally, you can add another Ikea Lack table to the bottom to raise the printer to a more comfortable height.
3D printed cases. Which technology is right for you?
Contents
- Introduction
- Key Benefits of 3D Printing Enclosures
- Quick release
- Any geometry
- Cheap production
- Features of the choice of technology and material
- FDM
- SLS
- SLA/DLP
- SLM
- Stratasys Polyjet
- Ceramic printing
- Material requirements
- Post-processing
- Enclosure Design Features
- Terminals
Introduction
3D printing of housings for household appliances and electronic devices is one of the most in-demand applications of additive manufacturing today. If you look closely, every device around us that we use every day has a case. With the advent and development of additive technologies, the production of prototypes and small-scale production of cases has completely switched to 3D printing, and it successfully copes with this task.
3D printing of enclosures is used for two purposes: for the production of prototypes and for mass production of final products. It provides design freedom, allows you to print a prototype or finished part in just a few hours, and significantly saves resources compared to traditional production methods. Printing a prototype allows you to quickly assess the conformity of its shape and dimensions to the original project, and in case of discrepancy, make adjustments and print a new prototype in a short time. Unlike traditional technologies, this manufacturing method will take a couple of hours, a maximum of several days.
Modern 3D printers also work with materials suitable for printing end products, which helps to optimize and scale the process of manufacturing cases. If we talk about mass production, then depending on the size of the part, it is economically profitable to print small series of cases up to 1000 products. Further, it is already worth switching to casting in silicone molds and working with injection molding machines, but we will talk about this in the following articles.
In this article, we will highlight the most common 3D printing technologies used by modern companies to print cases. We will also look at some design recommendations for optimizing the design of the hull during its modeling stage.
Key Benefits of 3D Printing Enclosures
Fast Manufacturing
3D printing is the fastest way to prototyping because it allows you to create unique prototypes without using molds. High speed printing of cases with complex design and construction leads to an increase in production volume, and therefore - to an increase in profits and business expansion.
Any geometry
3D printing gives you the freedom to experiment with case design and appearance. During the modeling phase, you can take into account all the functions that the part must cope with and adapt it to the specific needs of the client. The geometry of products offered by additive manufacturing is practically unlimited. No other technology can offer this flexibility. For example, using injection molding, you cannot quickly change the design of the mold to make changes in the design of the part. If the client needs even minor modifications to the body design, you will have to go through the process from the very beginning: from the creation of the mold to the manufacture of the final product.
Cheap production
The price of the case ultimately depends on the amount of material spent on printing one piece. With the ability to create multiple versions of the same part, you can achieve the highest degree of efficiency and cost-effectiveness at a low cost. Printing a prototype allows you to quickly evaluate the ergonomics of the case and the consistency of all its elements. With the help of prototyping, you can see the behavior of the material when printed and visually evaluate its final look, color and structure. Rapid prototyping has made 3D printing the most cost-effective manufacturing method compared to traditional technologies.
Features of the choice of technology and material
Various printing technologies are used for the manufacture of cases, the choice depends on the task. In this article, we will briefly talk about the application of such technologies, but we will not be able to cover many important parameters, such as accuracy and roughness.
FDM
Material extrusion is the most affordable 3D printing method and is great for inexpensive and fast prototyping, completing the task in 1-2 days. It is also suitable for printing finished cases, if the part is in a static position, not subjected to loads and pressure. FDM allows you to print a variety of materials and their composites: ABS, PLA, Nylon 12, TPU, PETG, ULTEM, etc. The latter is especially important for the aerospace industry - the construction of aircraft and rockets.
The thickness of the laid layer varies from 100 to 300 microns, the dimensional error is plus or minus 0.5% with a lower limit of 0.5 mm. Compared to products obtained by casting, FDM parts do not have a beautiful appearance - the joints of the layers are visible on them, therefore, after printing, polishing or painting is sometimes used. Supports must also be removed upon completion of printing.
SLS
Selective powder laser sintering can be used for both prototyping and finished products. Among all the technologies presented, only SLS is suitable for small-scale production of plastic cases. The method is distinguished by high accuracy and fast printing speed. It is used to produce functional enclosures with good mechanical properties, abrasion resistance and resistance to aggressive environments, especially if they are known to be constantly opened and closed. Typically, standard nylon 12 and fiberglass nylon are chosen for this purpose, which gives greater rigidity and improved abrasion resistance.
Despite the higher cost and longer lead times compared to FDM, SLS printing does not require the construction of supports and can produce cases with complex designs and shapes. The layer height is 100 μm, and the deviation from the specified dimensions tends to 0.3%. Printed products have a matte, rough surface that is slightly grainy to the touch. If the product is post-processed on the PostPro machine, it can fully compete with the part made on the injection molding machine.
SLA/DLP
Stereolithography produces the highest surface quality and requires little to no post-processing, resulting in a smooth and even surface from the 3D printer. SLA is not exactly suitable for small-scale production, but it is an ideal solution for prototyping. The deviation from the original dimensions does not exceed 0.5% with a lower limit of 0. 15 mm. The layer height is 25-100 µm. After printing is completed, it is required to clean the hollow sections from the photopolymer, remove the supports and grind the places where the supports are attached to the part.
SLA works with a wide range of photopolymer resins, all of which have different characteristics and properties. For example, elastic resins can be used to create flexible cases that allow pushing buttons or moving switches. In 2021, Boston Micro Fabrication introduced the latest 3D printing equipment, which makes high-precision printing of micro-cases at mass scale possible. BMF 3D printers print fine products with excellent detail at a resolution of up to two microns, and for this purpose they use new generation engineering and ceramic photopolymers with exceptional mechanical properties.
SLM
If the case will be subjected to heavy loads or must be reliably protected, then it is better to make it from metal by selective laser sintering. Of course, SLM technology is significantly more expensive, but the metal case will last much longer than the plastic one. SLM makes it possible to manufacture cases of any complexity from almost all known metals, including aluminum, titanium, nickel, steel, various metal alloys and superalloys. Compared to the casting method, SLM has higher strength values, and the part itself has a significantly lower weight. The minimum layer thickness is 20 microns, the maximum possible size is 600 x 600 x 600 mm.
Stratasys Polyjet
Polyjet technology has opened up new possibilities in 3D printing. Polyjet works with liquid photopolymers to create complex colored parts with very smooth surfaces and high resolution. Stratasys equipment can combine colors and combine multiple materials in one product, which helps to obtain cases with unique mechanical properties. Some Stratasys models support over 500,000 shades, reproduce different textures and interact with a huge range of materials. On such 3D printers, you can print both hard and soft cases in a wide variety of colors and unusual textures. But you need to keep in mind that when printing, only materials from Stratasys' own line, designed specifically for their equipment, are allowed to be used.
Polyjet creates a perfectly flat surface without visible joints between the layers and works out the smallest elements of the future hull. The layer thickness is only 16 microns. Despite the fact that the technology requires supports, the products are printed quickly, and the supports are easily removed with water or a special solution.
Ceramic Printing
Above we have covered the basic technologies for printing plastics and metals, but in some cases ceramic bodies are printed. Ceramic printing is available in many different technologies and the choice must be made based on the required accuracy and body size. At present, it is possible to print any ceramic package, including micro-sized ones.
Requirements for materials
If we are talking about the final product, it is necessary to choose materials with ESD safe protection against static electricity. These are materials that prevent the accumulation of electrostatic charges. We are all familiar with electrostatic discharge ESD (electrostatic discharge), sometimes when touching electrical devices, it gives us discomfort. The problem is that such discharges can damage electrical components and endanger human life. Additive manufacturing has already learned how to use engineering plastics that do not accumulate electrostatic charges. Such materials are most in demand in the field of electronics and for printing products that operate in an explosive environment.
Post-processing
The choice of finishing method depends on many factors, such as printing technology, size, material and purpose of the part, cost and lead time. Some post-processing methods are better for prototypes, others better for final products. Therefore, there are several ways to achieve a certain texture and appearance of the case.
Painting . Improves the appearance of the part and makes it aesthetically pleasing. This is important for exhibition prototypes, samples and final products. Usually, before painting, the part is well sanded to a smooth surface, and then a primer layer is applied to better adhere the paint to the surface. If you skip this step, the paint may partially soak into the material, which will only worsen the appearance. Primer and paint increase the volume of the product, with special requirements for dimensions, this point should be taken into account even at the stage of model development. Painting products printed with FDM technology can be done with acrylic paints or an aerosol can. If we talk about painting SLS products, then the etching method is used here, that is, the part is completely immersed in a bath with a hot color solution. Due to the high porosity of SLS, the paint remains not only on the surface of the product, but also penetrates into the pores, filling the product from the inside. Thus, staining gives the part a bright color and reduces its porosity.
Flocking . This is the process of coating products with electrified flock particles using special equipment - a flocker. Any surface can be flocked, this is done so that the final product does not conduct electricity. The principle of processing is to apply negatively charged flock particles to a positively charged part. Preliminarily, an adhesive base is applied to the part, in contact with which the flying particles of the flock are securely fixed on its surface. Flock differs in particle length (usually 1 or 2 mm), color and quality, so this coating can be one-color or multi-color. In view of this, flocking can perform an additional aesthetic function.
Sanding . The easiest, most affordable and efficient way to process finished plastic products. Surface smoothing can be done manually or using a grinder. This method is especially good for products printed using FDM technology, which have joints between layers. If accurate dimensions are important to you, then throughout the process it is necessary to adjust the amount of material removed. The human factor is very high here, so this method is not suitable for the manufacture of unified products; rather, it is suitable for processing prototypes, samples or mock-ups. Often sanding is a preparatory step before painting.
Tumbling . This type of processing occurs by mixing finished products with a filler (abrasive material) in special containers that are rotated or driven by vibration. Rocks, sand, sawdust, sandpaper and other materials can act as an abrasive. Tumbling well polishes the surface of parts and is suitable for processing various materials, it allows you to achieve the required level of roughness and a given surface quality. This is especially noticeable on metal: metal parts processed by tumbling acquire a shiny smooth surface. Tumbling can be performed not only in a dry environment (with bulk materials), but also in a wet one - with special solutions.
Case design features
3D printing case design usually consists of two main steps:
-
Determining the dimensions and location of the internal components of the device
3D modeling of the housing with the placement of the internal components of the device for which it is created will help determine its optimal dimensions and clearances. -
Hull Structure Design
While tolerance and setback recommendations vary by technology, there are general design principles that you should follow to achieve a good result:
-
Decide on housing dimensions
The first step is to design the chassis profile and position the components you want to enclose inside it. This will help you determine where you need clearance for connectors, buttons, and cables. The optimal indentation of the internal components from the case is 0.5 mm, 0.25 mm must be added to the gaps and holes. -
Choose the right wall thickness
Wall thickness ultimately affects the weight, strength, and stiffness of your hull.The minimum thickness must be 2 mm. It is this value that provides high structural strength with its lowest weight.
-
Avoid sharp and right angles
Corner rounding is a key feature of 3D printing because rounding helps reduce stress concentration in the corners, simplifies the printing process, and improves the functionality of the case. Even a small rounding can have a significant impact. -
Think over the fixing elements of the housing
It is worth considering how you provide access to the internal components of the case. If access to the internal contents is not required, appropriate fasteners can be designed or adhesive can be used to completely seal the case. If access is still necessary and the case will need to be opened, you can use different fasteners: snap and push connections, locking connections, threaded fasteners and movable hinges.
The multiple opening connection must be resistant to wear, threaded fasteners work well for this task. Live loops are also often used in combination with snap-on connections.
-
Improve hole diameter accuracy for fasteners and self-tapping screws
If your design contains holes for screws and fasteners, make sure that the diameter of the hole matches the diameter of the screw as closely as possible. To obtain an accurate diameter after printing, it is recommended to drill a hole or cut a thread with a machining tool. On the other hand, if you want the screw or fastener to fit firmly into the housing, reduce the diameter of the holes by 0.25mm. -
Thicken the screw holes
To reduce the chance of bulging and deformation of the housing, it is recommended to increase the wall thickness in places where it is planned to make holes for bolts and use threaded fasteners. -
Add extra volume if you need the most even hole for the screw
Conclusions
In this article, we analyzed the advantages of 3D printing and the basic principles of case design, examined modern materials and technologies for their production. Practice shows that 3D printing does an excellent job with this task, the most important thing is to choose the right technology for the manufacture of your particular case. Contact our company and you will receive competent advice from our experts. We will produce high-quality prototypes of your product or help you choose equipment specifically for your task. Our experts will install, start up and train you to work with the new purchased equipment.
For all questions, our specialists will be happy to advise you, you can contact them in any convenient way:
- E-mail: [email protected]
- Via chat on site
- Phone: 8 (800) 500-33-91
- Or by leaving a request on any page of our website
Welcome to NIOZ.RU
Sort by
Product name +/-
Product price
Featured Items
Item Availability
Showing 1 - 60 of 662
153060150
Items
3D Scanner Ciclop
RUB 8500. 00
Notify me when available
Product description
400 ml
RUB 1940.00
Product description
RUB 390.00
Product description
350 ml
RUB 850.00
Product description
Ready to print
RUB 23700.00
Item description
Ready to print out of the box
RUB 14500.00
Notify me when available
Product description
Ready to print
RUB 19900.00
Item description
Ready to print
20900.00 RUB
Notify me when available
Product description
Ready to print
RUB 23900.00
Item description
Ready to print out of the box
RUB 43500.00
Item description
Ready to print
RUB 39000.00
Item description
LCD 0.7/1.75 mm
RUB 1550.00
Notify me when available
Product description
OLED, 0.6/1.75mm, USB
RUB 2150. 00
Notify me when available
Product description
RUB 650.00
Product Description
Wiznet W5100 Arduino Shield
RUB 650.00
Notify me when available
Product description
RUB 550.00
Product description
Assembly kit
2500.00 RUB
Notify me when available
Product description
Volume: 1 l.
RUB 3100.00
Product description
Boscam 200mW, 5.8GHz
£4550
Chimera, e3d
RUB 1700.00
Product description
Print head 1.75mm 0.4mm
1100.00 RUB
Product description
Dual printhead 1.75mm 0.4mm
2500.00 RUB
Notify me when available
Product description
Long
RUB 750.00
Item Description
Short
RUB 700.00
Product description
RUB 100.00
Notify me when available
Product description
LERDGE 2IN1
Call for Quote
Notify me when available
Product description
Call for a quote
Notify me when available
Product description
Quantity: 1 set Weight: 10 g
RUB 100. 00
Product description
RUB 1900.00
Notify me when available
Product description
APM2.6 mavlink
RUB 1350.00
Product description
ESP8266 is a highly integrated chip
Product Description
RUB 250.00
Product description
Call for a quote
Notify when available
Product description
11.1V, 20C
RUB 1900.00
Product description
11.1V, 25C
RUB 1250.00
Notify me when available
Product description
11.1V, 25C
RUB 2100.00
Product description
Heat block v6
RUB 150.00
Product description
cartridge type thermistor
190.00 RUB
Item description
Heat block Volcano
170.00 RUB
Product description
Output parameters: 24 V, 600 W.
RUB 3300.00
Product description
12V 20A
RUB 1550. 00
Product description
12V 30A
RUB 1950.00
Notify me when available
Product description
12V 5A
RUB 450.00
Notify me when available
Product description
24V 15A
RUB 2100.00
Notify me when available
Product description
RUB 250.00
Product description
Hobbed bolt
RUB 150.00
Product description
Price for 10mm (free cutting)
RUB 13.00
Product description
Price per 10mm (free cutting)
RUB 17.00
Product description
Section 400mm
RUB 650.00
Description of item
Price for 10mm (free cutting)
RUB 25.00
Product description
10mm (cut to size)
RUB 70.00
Item description
10mm (cut to size)
RUB 90.00
Item description
Price per 10mm (free cutting)
RUB 7.00
Product Description
Price for 10mm (free cutting)
RUB 10.