Is a 3d printer easy to use
Are 3D Printers Easy or Hard To Use? Learning How to Use Them – 3D Printerly
A key question with 3D printing is, just how hard or easy is it to print something in 3D? Do you need a ton of experience to get started? I decided to put together a quick article to try and help answer this important question.
With the right information, 3D printing is a very simple process. 3D printer manufacturers realize that ease of set-up is a big factor when it comes to 3D printing beginners, so most have specifically made it easy to function from start to finish. Set up can take minutes.
This does sound extremely easy, but for beginners there can be a few barriers that you have to overcome to get a smooth printing process. I will explain these and hopefully lessen your worries about 3D printing.
Are 3D Printers Hard to Use & Learn?
3D printers are not hard to use with a good, reputable brand of 3D printer since they are pre-assembled and have many useful instructions to follow to get them up and running. Slicers such as Cura have default profiles that allow you to 3D print models without much input from users. 3D printers are getting easy to use.
In the past, there was a lot of tinkering and user input that was necessary to get 3D printers to provide a somewhat accurate model from the build plate, but nowadays, even teenagers and kids can handle a 3D printer.
The assembly process is no different than a decent DIY project, only requiring you to put the frame together, along with parts such as the hotend, screen, spool holder, most of which are pre-assembled.
Some 3D printers come completely assembled and calibrated at the factory so you don’t actually need to do much, other than plugging it in and printing from the supplied USB stick.
Nowadays, there are plenty of YouTube videos and articles that you can find to help you with getting started with 3D printing, as well as troubleshooting help that makes things simpler.
Another thing that is making 3D printing easier is how manufacturers are stepping up their skills and making 3D printers easier to assemble and operate, with automatic features, touchscreens, good build surfaces that 3D printing materials stick to nicely, and much more.
Check out the video below for a complete beginners guide to 3D printing. It takes you from step 1 to having a fresh 3D print right off the build plate.
5 Steps to Easy 3D Printing
- Get a beginner-friendly 3D printer – this should have auto-features, easy navigation panels, be compatible with most software. Ideally a pre-assembled 3D printer
- Add your filament of choice – sometimes comes with your 3D printer, or bought separately. I’d recommend using PLA filament as this is the most common, and easy to use type.
- Pick your 3D printer slicing software (Cura is the most popular) and select your 3D printer to autofill settings – keep in mind some 3D printers have brand-specific software such as Makerbot.
- Choose a 3D CAD file of your liking to print – this is the actual design you want to print and the most common place would be Thingiverse.
- Start printing!
What’s the Hard Part About 3D Printing?
3D printing can be made very easy, or very hard depending on what your goals are, how technical you want to get and your experience with DIY.
As I’ve mentioned, setting up your 3D printer and starting the print process can be very easy, but once you start designing your own prints and make unique adjustments this is where things can get difficult.
To get specific prints, it does take a unique understanding of how designs must be put together.
Designing prints can be a complicated process because you have to design your print in a way that it’s supported throughout the print, or it just won’t hold up.
Once you have that knowledge, it should be much easier to get designing and many programs have guides which tell you if your design is well-supported.
Having a high enough infill setting that your print won’t fall apart in the middle of the print is another important factor, so be aware of these things.
Luckily there are Computer-Aided Design (CAD) software out there that caters to different levels of expertise.
This ranges from simply putting shapes together in a program, to putting together small complex shapes to do anything from create a favorite action figure, to replacing a spare part on an appliance.
You can avoid this by taking a shortcut by just using designs from people who already have designs which are proven to work.
Thingiverse is a collective source of 3D print designs (STL files) which is available to everyone. A great thing you can do is look at a design from someone else and make adjustments in your own unique way, if you have the experience.
Like most things, with practice 3D printing will become very easy to do. There are things you can do which do get more complex, but the main process isn’t very hard to get started.
What If I Run Into Some Issues?
The main reason people run into issues is because they’ve jumped into things without doing research. If you bought a 3D printer kit from someone’s recommendation, a lot of the time they can be difficult to put together.
They may also not have features which really help out beginners such as auto-levelling the nozzle to the print bed to ensure precise printing, or have compatibility with beginner-friendly software. This is why it’s important to know the basic stuff before you jump into 3D printing.
There are many troubleshooting issues that people have when it comes to 3D printing, as people get further into the field. This can range from the quality of your filament where it can break, filament material not sticking to the print bed, first layers being messy, prints leaning etc.
If you do run into some issues, the 3D printing community is an extremely helpful one and many questions you have, most likely have already been answered on the many forums that are out there.
In most cases, putting together a 3D printer isn’t too hard if necessary. An example of a simple 3D printer is the Creality3D CR-10, which comes in three parts and takes only 10 minutes to put together.
Once your 3D printer is put together, most settings can be autofilled when selecting your specific 3D printer within your software, so this is a pretty simple step.
After sorting out issues a few times, you should become confident in preventing those issues, and being able to quickly solve them in the future.
Final Thought
3D printers are being used in education at many levels, so if children can do it, I’m pretty sure you can too! There is some technical know-how but once things are up and running you should be printing away.
Mistakes will be made from time to time, but they are all learning experiences. Many times, it takes a few setting adjustments and prints should come out pretty smooth.
There are many levels of knowledge that you’ll need to get to a good level of 3D printing, but this mostly comes with practical experience, and just generally learning about the field. The first few times may seem difficult, but it should get easier as time goes on.
As time goes on, I can only imagine that 3D printer manufacturers and software developers will keep on aiming to make things simpler.
This along with the development in technology and research leads me to think that it will not only become more cost-efficient, but easier to create useful and complex designs.
The Best 3D Printers for Beginners in 2023
While 3D printing has been around for a while, it’s only recently become more accessible to the mainstream consumer market. Desktop 3D printers make it simple for hobbyists to take advantage of this innovative technology, but those dipping their toes in for the first time may be wary. There’s an enormous variety when it comes to the best 3D printers for beginners, making the process of setting up, printing, and finishing your models a simpler, more digestible process.
3D printers use a process called additive manufacturing to turn digital models into three-dimensional objects. Most often, 3D printers use small nozzles and materials like plastic, resin, polymers, or metal, depositing the material layer by layer, then fusing them with an adhesive or ultraviolet light to create a 3D model.
The things you can create with a 3D printer are almost endless. These desktop devices give you the power to harness your creativity and turn digital prototypes, 3D doodles, and much more into physical objects—all from the comfort of your home. The best 3D printers for beginners will bring your digital dreams to life.
— Best Overall: Creality Ender 3 Pro 3D Printer
— Best for Speed: AnkerMake M5 3D Printer
— Best Resin: ELEGOO Saturn MSLA 3D Printer
— Best Multifunction: Snapmaker 2.0 Modular 3-in-1 A350T 3D Printer
— Most User-Friendly: Monoprice Voxel 3D Printer
— Best Premium: Robo E3 3D Printer
How 3D Printing Works
3D printers use a process called additive manufacturing (more colloquially known as 3D printing) to turn digital models into three-dimensional objects. Most often using small nozzles and materials like plastic, resin, polymers, or metal, the printer deposits the material layer by layer, then fuses them with an adhesive or ultraviolet light to create a 3D model.
The things you can create with a 3D printer are almost endless. These desktop devices give you the power to harness your creativity and turn digital prototypes, 3D doodles, and much more into physical objects—all from the comfort of your home. The best 3D printer for beginners will bring your digital dreams to life.
How We Selected the Best 3D Printers for BeginnersAs with any new consumer technology, 3D printing isn’t exactly cheap, so you’ll have to spend some money for a decent pick. We narrowed down our picks for the best 3D printer for beginners from dozens of 3D printers, paying attention to price, ease of use, and print quality.
Price: 3D printers start at a couple of hundred dollars and can range up to thousands of dollars. Most beginner hobbyists will want a budget-friendly option for testing the waters. We included several printers in a modest price range, skewing towards more affordable prices to appeal to novices.
Ease of Use: User friendliness is one of the most important features when it comes to picking the best 3D printer for beginners. We prioritized features like straightforward assembly and print material refilling, as well as a simple-to-use interface with less of a learning curve required to get started.
Print Quality: Through reviewing product specifications and consumer reviews, we chose 3D printers that create high-quality models, so your design looks exactly as intended. We prioritized 3D printers with good specifications and high user satisfaction. Get started with the best 3D printing software.
The Best 3D Printers for Beginners: Reviews and Recommendations Best Overall: Creality Ender 3 Pro 3D PrinterAn Excellent Learning Resource.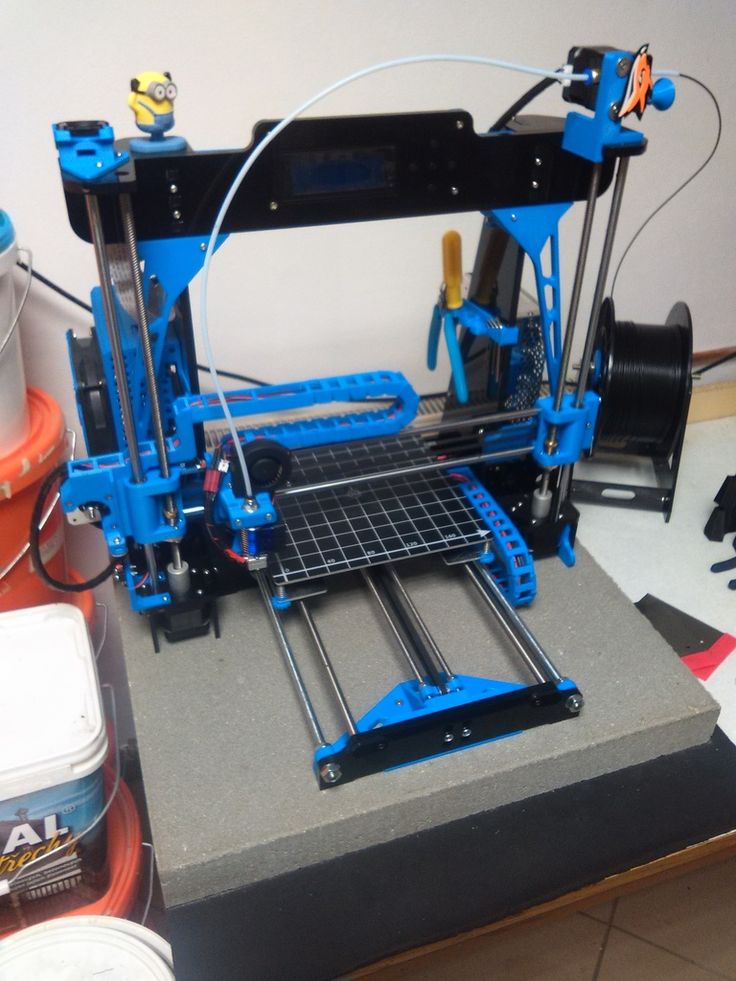
Why It Made The Cut: This beginner-friendly 3D printer is affordable, simple to use, and creates quality prints.
Specs:
— Build Volume: 8.7 inches D x 8.7 inches W x 9.8 inches H
— Weight: 14.6 pounds
— Compatible Materials: PLA (polylactic acid), ABS (acrylonitrile butadiene styrene), PETG (polyethylene terephthalate glycol) plastic
— Print Speed: Up to 180 mm/s (millimeters per second)
Pros:
— Easy to assemble
— Removable, flexible, and magnetic print bed
— Great print quality
Cons:
— Printing bed can be tricky to level
The Creality Ender 3 Pro 3D Printer is a popular 3D printer model for hobbyists, and for good reason. This printer is affordable, easy to use, and comes with several attractive features.
The printer arrives partially assembled with all the necessary tools included for easy setup. Loading the plastic filament is simple. Once assembled and switched on, the device is ready to print almost immediately, with a rapid heating feature that gets the printer ready to go in only five minutes. In case of any pauses in printing, it also has a handy ‘resume print’ function, which restarts the job where it left off.
The heated, removable, and flexible magnetic print bed makes it easier to remove completed models after they’re finished printing, although users will need to take care when re-installing the bed to make sure it’s level. Overall, this 3D printer delivers great print quality, and for its reasonable asking price, it’s our choice for the best 3D printer for beginners looking to dip their toes into 3D printing. For another great option, read out review of the Anycubic Vyper 3D Printer.
Best for speed: AnkerMake M5 3D PrinterFive Times Faster. AnkerWhy It Made The Cut: The AnkerMake M5 prints five times faster than some of its competitors and detects errors with an AI camera.
Specs:
— Build Volume: 235 x 235 x 250 mm
— Weight: 27.7 pounds
— Compatible Materials: PLA, PETG, ABS, TPU
— Print Speed: 250 mm per second
Pros:
— Faster than the competition
— AI camera allows for error detection
— Compatible with Alexa
Cons:
— Expensive
If you’re looking to make models fast, the AnkerMake M5 3D Printer is a smart choice. It prints at 250 millimeters per second—five times faster than some other 3D printers. The AnkerMake M5 is a FDM printer that operates on Linux. The integrated die-cast aluminum alloy structure provides a stable base and auto-leveling. The AnkerMake M5 is also designed with an AI camera that helps identify errors such as extruder jams and failure of the model to stick to the print bed. The system sends notifications through the AnkerMake app, a helpful feature for beginners and experienced makers alike.
The Anker Make M5’s build volume of 235 by 235 by 250 millimeters isn’t as large as some, but it works with a range of materials, including PLA, PETG, ABS, and TPU. In addition to operating the machine through the app, you can also use the AnkerMake Slicer and Amazon’s Alexa.
Best Resin: ELEGOO Saturn MSLA 3D Printer Resin Details. ELEGOOWhy It Made The Cut: This is the best resin 3D printer because it has a relatively large build volume and an accurate printing process to create detailed, sizable resin models.
Specs:
— Build Volume: 7.6 inches L x 4.7 inches W x 7.9 inches H
— Weight: 30 pounds
— Compatible Materials: DLP photopolymer resin
— Print Speed: Up to 40mm/s
Pros:
— Accurate printing results
— Simple to assemble and easy to calibrate
— Large build volume for printer type and price
— Can print multiple miniature models simultaneously
Cons:
— Test model is difficult to remove from the build plate
Compared to FDM (fused deposition modeling) 3D printers, resin printers can print higher levels of detail, which is especially ideal for printing smaller models. Instead of injecting melted materials like plastic layer by layer, resin printers use light (like ultraviolet lights) to cure liquid resin into thin layers. This method allows for finer printing details and a smoother surface. Beginners who want to take advantage of resin 3D printing should consider the ELEGOO Saturn MSLA 3D Printer, a relatively affordable choice with several attractive features.
Resin printers tend to be smaller than FDM printers. For its entry-level price, this printer has a large build volume at 7.6 inches long by 4.7 inches wide by 7.8 inches high. This larger size gives the flexibility to create larger, but still very detailed models and miniatures. The ELEGOO also prints 60 percent faster than its predecessor (the smaller Elegoo Mars 2 Pro), while still delivering excellent printing results.
Setup is simple with this printer (although beginners should keep in mind that resin printing requires more post-processing than FDM printing). An easy-to-calibrate build plate and a uniform light source create great print results with few adjustments needed.
Why It Made the Cut: This multifunction 3D printer lets you get everything done with one device, from printing, to laser engraving, cutting, and carving.
Specs:
— Build Volume: 12.59 inches x 13.77 inches x 12.99 inches
— Weight: 61.73 pounds
— Compatible Materials: PLA, Wood PLA, PTG, TPU
Pros:
— Several functions all in one machine
— Compatible with many materials
— Can create larger models with its bigger surface area
— Innovative, sturdy design that’s built to last
Cons:
— Incredibly heavy
— Not a very beginner-friendly price
With a wide array of uses, the Snapmaker 2.0 Modular 3-in-1 3D Printer is a fantastic machine to learn the basics of 3D printing on, and then keep around for the long haul as you master each function. An upgrade to Snapmaker’s previous models, the 2.0 A350T encompasses noise reduction for quieter printing, faster speeds, and precision down to .005 millimeters for a smoother finish.
This 3D printer is an absolute beast when it comes to material compatibility. Whether you’re printing with PLA, PTG, or TPU; engraving or cutting into plywood, paper, acrylic, fabric, or leather; or carving out shapes and textures with hardwood, PCB, acrylic, POM, carbon fiber sheets, or many more, the Snapmaker can handle the task. This is likely beyond the scope of what you’d be getting into as a beginner, but it opens up the possibilities as you broaden your knowledge and get more comfortable in the realm of 3D printing.
There’s a lot to applaud Snapmaker for, including its incorporation of auto-leveling, filament runout and power loss recovery, WiFi connectivity, and an all-metal, high-strength build that’s designed to last.
Most User-Friendly: Monoprice Voxel 3D Printer Smart and Easy to Use.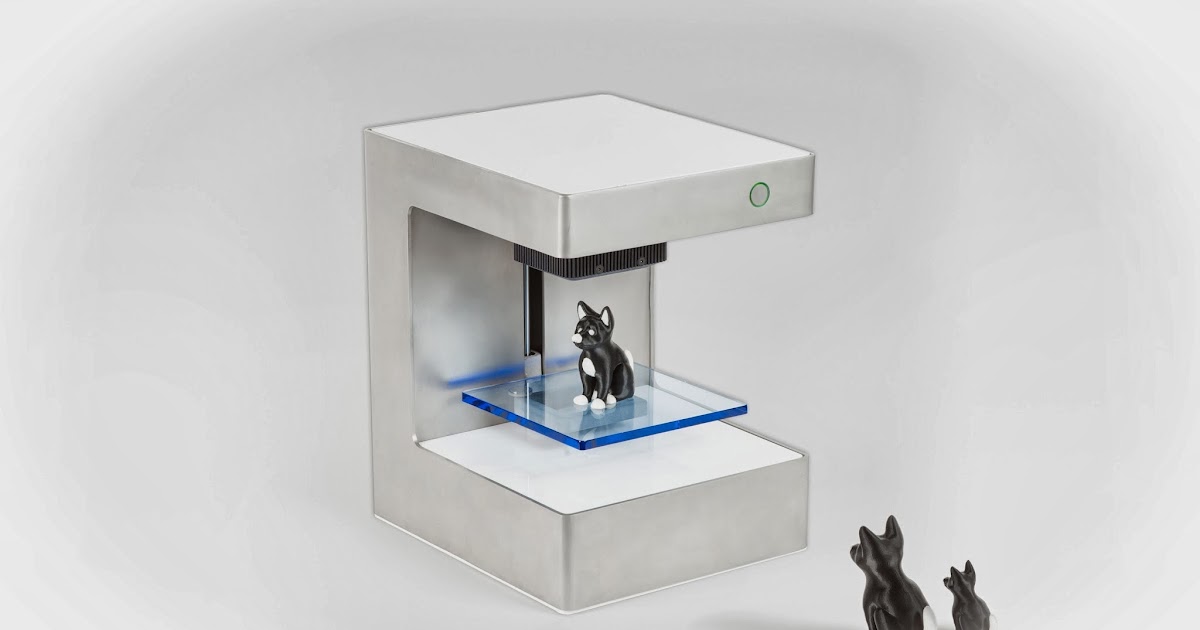
Why It Made The Cut: A fully-enclosed design, auto-leveling platform, and auto-feeding filament feature make this printer an extra user-friendly choice.
Specs:
— Build Volume: 5.9 inches L x 5.9 inches W x 5.9 inches H
— Weight: 20 pounds
— Compatible Materials: ABS, PLA, wood fill, copper fill, steel fill, and bronze fill filaments
— Print Speed: Up to 100mm/s
Pros:
— Auto-levelling platform
— Full enclosure
— WiFi-enabled
— Built-in camera for print monitoring
Cons:
— Relatively small build volume
If you want to get into 3D printing without the steep learning curve, consider the Monoprice Voxel 3D Printer. This 3D printer features several automated functions that make it extra simple to use.
The printer arrives fully calibrated and ready to print, right out of the box. An auto-leveling feature ensures that the build platform is in the right position, while an auto-feeding filament feature makes loading filament easy. The built-in filament sensor also recognizes low filament levels and pauses prints to notify you that it needs reloading. Once your creation is done printing, lift the heated, flexible, and removable build plate. With a bit of flexing, the model should pop off with ease.
This 3D printer features a closed design to keep hands (or paws) away from hot and moving parts while it’s printing. It is also Wi-Fi-enabled; its functions are controlled and monitored through its color touch screen or through your smartphone (through the Polar Cloud cloud-based platform), and you can check on printing progress through the window or with your phone via the built-in camera. If you're into making miniatures, you may also want to consider the best resin 3D printers.
Best Premium Pick: Robo E3 3D PrinterAll-In-One. Robo.Why It Made The Cut: Robo's E3 is the perfect 3D printer to get if you want to jump into making complex projects right away. It's compatible with over 20 materials, ranging from wood to metal to glass.
Specs:
— Build Volume: 5.9 inches L x 5.9 inches W x 5.9 inches H
— Weight: 19.8 pounds
— Compatible Materials: ABS, PLA, wood fill, copper fill, steel fill, brass fill, carbon fiber fill, magnetic iron, glass fill, bronze fill filaments, and more.
— Print Speed: Up to 100mm/s
Pros:
— Auto-calibrated print bed
— Can store up to 1,000 models on its internal storage
— WiFi-enabled
— Includes two spools of PLA filament.
Cons:
— Expensive
If you're serious about getting into 3D printing, and don't want to go through the process of buying an entry-level printer and then upgrading it in a year or two, Robo's E3 is the one to get. It's roughly the same size and weight as our other 3D printer recommendations, but it can work with a lot more materials.
This gives you the freedom to create 3D prints that wouldn't be possible otherwise, especially if you're making objects that require different elements, like glass and metal. If you plan on printing the same objects over and over again, the E3's built-in storage will come in handy. That's doubly true if you accidentally delete a model on your computer.
While these features add to the E3's cost, but it's still a good machine for beginners because of its auto-calibrating print bed, which improves the odds of you ending up with a satisfying print rather than one that's lopsided. By reducing the number of prints you have to discard due to quality issues, the Robo E3 is more forgiving for new 3D printer users, and a lot less wasteful. Novice 3D printers will also benefit from the two-hour online training course that comes with this printer.
It's hard to overlook the Robo E3's up-front cost, but again, it's so capable relative to the other 3D printers we're recommending for beginners that it's well worth the price. This should be the only 3D printer you'll ever get, unless you start needing one for commercial use.
Things to Consider Before Buying a 3D Printers for BeginnersThe best 3D printers for beginners give you the power to create on-demand. But as more 3D printers flood the market, it can be hard to choose the best one for your needs. When shopping for the best beginner-friendly 3D printer, consider the printer dimensions, build volume, compatible materials, and ease of use.
While consumer 3D printers are heavier than your standard all-purpose printer, they’re still a reasonably small size. Since they’re made for at-home use, most have a compact footprint to fit on a desktop or counter.
Consider the printer size and weight and how it will fit in your space. Keep in mind that the size of the printer is related to the build volume the printer is trying to accommodate; a larger printer will be able to create larger items, and a smaller one will be limited to smaller items.
Build Volume3D printers can be used to create just about anything, from giant 3D models to tiny trinkets, but at-home 3D printers are much smaller than the ones you might find in a design studio.
To help shoppers make a suitable choice, consumer 3D printers include a build volume measurement that describes the maximum width, height, and length of the print area. The build volume roughly determines the maximum size model that the printer can create. Consider the type of items you are hoping to print and choose an appropriate build volume from there.
Compatible MaterialsMost consumer 3D printers available today use fused deposition modeling (FDM), where material (usually plastic filament) is melted and extruded through a nozzle to create thin layers that make up a model. Other 3D printers, like resin printers, use curing processes, like UV light, to harden materials by layer.
The compatible materials vary by 3D printing method, but can include plastics, metals, polymers, resin, ceramics, plaster, and glass. When shopping for a 3D printer, check whether the ones you’re considering allow you to build creations with your preferred materials.
Ease Of Use3D printing can get overwhelming for those who aren’t tech-savvy, so as a beginner, it’s important to find a 3D printer that is simple to use. A beginner-friendly 3D printer should have a simple setup process, easy refilling process, and intuitive controls.
Features like a touchscreen interface, print resume functions, robust safety features, and a heated bed (which can ensure a well-made model foundation) can make a 3D printer more user-friendly. Some printers also come with included printing materials, so you can get started right away.
3D printers can include other convenient perks, like quiet operation, built-in cameras to monitor printing, and Wi-Fi connectivity so you can print and monitor progress from anywhere. Buying from a company with easy-to-reach customer support or an active online community is also a nice perk, in case you need to do any troubleshooting down the road.
FAQsQ: What brand of 3D printer is the best?There’s no singular best brand when it comes to 3D printers. We’ve selected our top picks from several reputable brands in the 3D printing industry. The brands on this list create quality 3D printers with user-friendly features that will appeal to beginners.
Yes. On a basic level, you’ll want a 3D printer that fits in your space. More specifically, you’ll want a 3D printer with a suitable build volume (the maximum print area) for your needs. Of course, as build volume increases, so does the printer size (and price).
Q: How much does a 3d printer cost?3D printers start at around $200 and can range up to many thousands of dollars. For a decent entry-level 3D printer for beginners, expect to spend between $200 to $400 for a good printer with some user-friendly features. For newbies, it’s best to start with a more basic and budget-friendly printer and you can always upgrade down the line if you decide you need more features.
Q: Is 3D printing an expensive hobby?Compared to many hobbies, 3D printing is a relatively expensive one (although it is much more affordable than it once was). Budget-friendly 3D printers still come in at a couple hundred dollars, which is a somewhat high upfront cost for testing out a new pastime. Ongoing costs include refill printer materials and possible replacements or repairs when something goes amiss. That said, you’ll be able to make some pretty cool and useful stuff, so the hobby is often well worth the price.
It depends. Do you plan to print industrial-size parts or small baubles? A good printer size is subjective and will depend on your needs. Most at-home 3D printers are small enough to fit on a desk or counter, and so are often best for smaller projects. When shopping for a 3D printer, consider its build volume, which will give you a better idea of what size models the printer can produce.
Related: Looking for more options? Here's our roundup of the best 3D printers for every kind of project.
Final Thoughts on the Best 3D Printers for BeginnersThe Creality Ender 3 Pro 3D Printer is one of the most highly-rated and popular picks for beginners. It’s a solid, budget-friendly printer that is user-friendly and creates high-quality models.
This post was created by a non-news editorial team at Recurrent Media, Futurism’s owner. Futurism may receive a portion of sales on products linked within this post.
Share This Article
How a 3D printer works, what can be printed on a 3D printer
The 3D printer is a technology that allows you to create real objects from a digital model. It all started in the 80s under the name "rapid prototyping", which was the goal of the technology: to create a prototype faster and cheaper. A lot has changed since then, and today 3D printers allow you to create anything you can imagine.
Contents:
- What is 3D printing?
- How does a 3D printer work?
- What can be printed?
The 3D printer allows you to create objects that are almost identical to their virtual models. That is why the scope of these technologies is so wide.
What is 3D printing?
3D printing is an additive manufacturing process because, unlike traditional subtractive manufacturing, 3D printing does not remove material, but adds it, layer by layer—that is, it builds or grows.
- In the first step of printing, the data from the drawing or 3D model is read by the printer.
- Next is the sequential overlay of layers.
- These layers, consisting of sheet material, liquid or powder, are combined with each other, turning into the final form.
With limited production of parts, 3D printing will be faster and cheaper. The world of 3D printing does not stand still and therefore there are more and more different technologies competing with each other on the market. The difference lies in the printing process itself. Some technologies create layers by softening or melting the material, then they provide layer-by-layer application of this same material. Other technologies involve the use of liquid materials, which acquire a solid form in the process under the influence of various factors.
In order to print something , you first need a 3D model of the object, which you can create in a 3D modeling program (CAD - Computer Aided Design), or use a 3D scanner to scan the object you want print. There are also easier options, such as looking for models on the internet that have been created and made available to other people.
Once your design is ready, all you need to do is import it into the Slicer, a program that converts the model into codes and instructions for a 3D printer, most of the programs are open source and free. The slicer will convert your project into a gcode file ready to be printed as a physical object. Simply save the file to the included SD card and insert it into your 3D printer and hit print.
The whole process can take several hours and sometimes several days. It all depends on the size, material and complexity of the model. Some 3D printers use two different materials. One of them is part of the model itself, the other acts as a prop that supports parts of the model hanging in the air. The second material is subsequently removed.
How does a 3D printer work?
Although there are several 3D printing technologies, most create an object by building up many successive thin layers of material. Typically desktop 3D printers use plastic filaments (1) which are fed into the printer by the feeder (2) . The filament melts in the print head (3) which extrudes the material onto the platform (4) creating the object layer by layer. Once the printer starts printing, all you have to do is wait - it's easy.
Of course, as you become an advanced user, playing with the settings and tweaking your printer can lead to even better results.
What can be 3D printed?
The possibilities of 3D printers are endless and they are now becoming a common tool in fields such as engineering, industrial design, manufacturing and architecture. Here are some typical usage examples:
Custom Models
Create custom products that perfectly match your needs in terms of size and shape. Do something that would be impossible with any other technology.
Rapid Prototyping
3D printing allows you to quickly create a model or prototype, helping engineers, designers and companies get feedback on their projects in a short time.
Complex geometry
Models that are hard to imagine can be easily created with a 3D printer. These models are good for teaching others about complex geometry in a fun and useful way.
Cost reduction
The cost of 3D printing end-use parts and prototypes is low due to the materials and technology used. Reduced production time and material consumption as you can print models multiple times using only the material you need.
How to choose and buy a 3D printer? →
3D printing for "dummies" or "what is a 3D printer?"
- 1 3D printing term
- 2 3D printing methods
- 2.
1 Extrusion printing
- 2.2 Melting, sintering or gluing
- 2.3 Stereolithography
- 2.4 Lamination
- 3 Fused Deposition Printing (FDM)
- 3.1 Consumables
- 3.2 Extruder
- 3.3 Working platform
- 3.4 Positioners
- 3.5 Control
- 3.6 Varieties of FDM printers
- 4 Laser stereolithography (SLA)
- 4.1 Lasers and projectors
- 4.2 Cuvette and resin
- 4.3 Types of stereolithographic printers
The term 3D printing
The term 3D printing has several synonyms, one of which quite briefly and accurately characterizes the essence of the process - "additive manufacturing", that is, production by adding material. The term was not coined by chance, because this is the main difference between multiple 3D printing technologies and the usual methods of industrial production, which in turn received the name "subtractive technologies", that is, "subtractive". If during milling, grinding, cutting and other similar procedures, excess material is removed from the workpiece, then in the case of additive manufacturing, material is gradually added until a solid model is obtained.
Soon 3D printing will even be tested on the International Space Station
Strictly speaking, many traditional methods could be classified as "additive" in the broad sense of the word - for example, casting or riveting. However, it should be borne in mind that in these cases, either the consumption of materials is required for the manufacture of specific tools used in the production of specific parts (as in the case of casting), or the whole process is reduced to joining ready-made parts (welding, riveting, etc.). In order for the technology to be classified as “3D printing”, the final product must be built from raw materials, not blanks, and the formation of objects must be arbitrary - that is, without the use of forms. The latter means that additive manufacturing requires a software component. Roughly speaking, additive manufacturing requires computer control so that the shape of final products can be determined by building digital models. It was this factor that delayed the widespread adoption of 3D printing until the moment when numerical control and 3D design became widely available and highly productive.
3D printing methods
3D printing technologies are numerous, and there are even more names for them due to patent restrictions. However, you can try to divide technologies into main areas:
Extrusion printing
This includes methods such as deposition deposition (FDM) and multi-jet printing (MJM). This method is based on the extrusion (extrusion) of consumables with the sequential formation of the finished product. As a rule, consumables consist of thermoplastics or composite materials based on them.
Melting, sintering or bonding
This approach is based on bonding powdered material together. Formation is done in different ways. The simplest is gluing, as is the case with 3D inkjet printing (3DP). Such printers deposit thin layers of powder onto the build platform, which are then selectively bonded with a binder. Powders can be made up of virtually any material that can be ground to a powder—plastic, wood, metal.
This model of James Bond's Aston Martin was successfully printed on Voxeljet's SLS printer and blown up just as successfully during the filming of Skyfall instead of the expensive original
sintering (SLS and DMLS) and smelting (SLM), which allow you to create all-metal parts. As with 3D inkjet printing, these devices apply thin layers of powder, but the material is not glued together, but sintered or melted using a laser. Laser sintering (SLS) is used to work with both plastic and metal powders, although metal pellets usually have a more fusible shell, and after printing they are additionally sintered in special ovens. DMLS is a variant of SLS installations with more powerful lasers that allow sintering metal powders directly without additives. SLM printers provide not just sintering of particles, but their complete melting, which allows you to create monolithic models that do not suffer from the relative fragility caused by the porosity of the structure. As a rule, printers for working with metal powders are equipped with vacuum working chambers, or they replace air with inert gases. Such a complication of the design is caused by the need to work with metals and alloys subject to oxidation - for example, with titanium.
Stereolithography
How an SLA printer works
Stereolithography printers use special liquid materials called "photopolymer resins". The term "photopolymerization" refers to the ability of a material to harden when exposed to light. As a rule, such materials react to ultraviolet irradiation.
Resin is poured into a special container with a movable platform, which is installed in a position near the surface of the liquid. The layer of resin covering the platform corresponds to one layer of the digital model. Then a thin layer of resin is processed by a laser beam, hardening at the points of contact. At the end of illumination, the platform together with the finished layer is immersed to the thickness of the next layer, and illumination is performed again.
Laminating
Lamination 3D printers (LOM)
Some 3D printers build models using sheet materials - paper, foil, plastic film.
Layers of material are glued on top of each other and cut along the contours of the digital model using a laser or a blade.
These machines are well suited for prototyping and can use very cheap consumables, including regular office paper. However, the complexity and noise of these printers, coupled with the limitations of the models they produce, limit their popularity.
Fused deposition modeling (FDM) and laser stereolithography (SLA) have become the most popular 3D printing methods used in the home and office.
Let's take a closer look at these technologies.
Fused Deposition Printing (FDM)
FDM is perhaps the simplest and most affordable 3D construction method, which makes it very popular.
High demand for FDM printers is driving device and consumable prices down rapidly, along with technology advances towards ease of use and improved reliability.
Consumables
ABS filament spool and finished model
FDM printers are designed to print with thermoplastics, which are usually supplied as thin filaments wound on spools. The range of "clean" plastics is very wide. One of the most popular materials is polylactide or "PLA plastic". This material is made from corn or sugar cane, which makes it non-toxic and environmentally friendly, but makes it relatively short-lived. ABS plastic, on the other hand, is very durable and wear-resistant, although it is susceptible to direct sunlight and can release small amounts of harmful fumes when heated. Many plastic items that we use on a daily basis are made from this material: housings for household appliances, plumbing fixtures, plastic cards, toys, etc.
In addition to PLA and ABS, printing is possible with nylon, polycarbonate, polyethylene and many other thermoplastics that are widely used in modern industry. More exotic materials are also possible, such as polyvinyl alcohol, known as "PVA plastic". This material dissolves in water, which makes it very useful for printing complex geometric patterns. But more on that below.
Model made from Laywoo-D3. Changing the extrusion temperature allows you to achieve different shades and simulate annual rings
It is not necessary to print with homogeneous plastics. It is also possible to use composite materials imitating wood, metals, stone. Such materials use all the same thermoplastics, but with impurities of non-plastic materials.
So, Laywoo-D3 consists partly of natural wood dust, which allows you to print "wooden" products, including furniture.
The material called BronzeFill is filled with real bronze, and models made from it can be ground and polished, achieving a high similarity to products made from pure bronze.
One has only to remember that thermoplastics serve as a binding element in composite materials - they determine the thresholds of strength, thermal stability and other physical and chemical properties of finished models.
Extruder
Extruder - FDM print head. Strictly speaking, this is not entirely true, because the head consists of several parts, of which only the feed mechanism is directly "extruder". However, by tradition, the term "extruder" is commonly used as a synonym for the entire print assembly.
FDM extruder general design
The extruder is designed for melting and applying thermoplastic thread. The first component is the thread feed mechanism, which consists of rollers and gears driven by an electric motor. The mechanism feeds the thread into a special heated metal tube with a small diameter nozzle, called a "hot end" or simply a "nozzle". The same mechanism is used to remove the thread if a change of material is needed.
The hot end is used to heat and melt the thread fed by the puller. As a rule, nozzles are made from brass or aluminum, although more heat-resistant, but also more expensive materials can be used. For printing with the most popular plastics, a brass nozzle is quite enough. The “nozzle” itself is attached to the end of the tube with a threaded connection and can be replaced with a new one in case of wear or if a change in diameter is necessary. The nozzle diameter determines the thickness of the molten filament and, as a result, affects the print resolution. The heating of the hot end is controlled by a thermistor. Temperature control is very important, because when the material is overheated, pyrolysis can occur, that is, the decomposition of plastic, which contributes both to the loss of the properties of the material itself and to clogging of the nozzle.
PrintBox3D One FDM Printer Extruder
In order to prevent the filament from melting too early, the top of the hot end is cooled by heatsinks and fans. This point is of great importance, since thermoplastics that pass the glass transition temperature significantly expand in volume and increase the friction of the material with the walls of the hot end. If the length of such a section is too long, the pulling mechanism may not have enough strength to push the thread.
The number of extruders may vary depending on the purpose of the 3D printer. The simplest options use a single print head. The dual extruder greatly expands the capabilities of the device, allowing you to print one model in two different colors, as well as using different materials. The last point is important when building complex models with overhanging structural elements: FDM printers cannot print “over the air”, since the applied layers require support. In the case of hinged elements, temporary support structures have to be printed, which are removed after printing is completed. The removal process is fraught with damage to the model itself and requires accuracy. In addition, if the model has a complex structure with internal cavities that are difficult to access, building conventional supports may not be practical due to the difficulty in removing excess material.
Finished model with supports made of PVA plastic (white) before and after washing
In such cases, the same water-soluble polyvinyl alcohol (PVA plastic) comes in handy. Using a dual extruder, you can build a model from waterproof thermoplastic using PVA to create supports.
After printing, PVA can simply be dissolved in water and a complex product of perfect quality can be obtained.
Some FDM printers can use three or even four extruders.
Work platform
Heated platform covered with removable glass work table
Models are built on a special platform, often equipped with heating elements. Preheating is required for a wide range of plastics, including the popular ABS, which are subject to a high degree of shrinkage when cooled. The rapid loss of volume by cold coats compared to freshly applied material can lead to model distortion or delamination. The heating of the platform makes it possible to significantly equalize the temperature gradient between the upper and lower layers.
Heating is not recommended for some materials. A typical example is PLA plastic, which requires a fairly long time to harden. Heating PLA can lead to deformation of the lower layers under the weight of the upper ones. When working with PLA, measures are usually taken not to heat up, but to cool the model. Such printers have characteristic open cases and additional fans blowing fresh layers of the model.
Calibration screw for work platform covered with blue masking tape
The platform needs to be calibrated before printing to ensure that the nozzle does not hit the applied layers and move too far causing air-to-air printing resulting in plastic vermicelli. The calibration process can be either manual or automatic. In manual mode, calibration is performed by positioning the nozzle at different points on the platform and adjusting the platform inclination using the support screws to achieve the optimal distance between the surface and the nozzle.
As a rule, platforms are equipped with an additional element - a removable table. This design simplifies the cleaning of the working surface and facilitates the removal of the finished model. Stages are made from various materials, including aluminum, acrylic, glass, etc. The choice of material for the manufacture of the stage depends on the presence of heating and consumables for which the printer is optimized.
For a better adhesion of the first layer of the model to the surface of the table, additional tools are often used, including polyimide film, glue and even hairspray! But the most popular tool is inexpensive, but effective masking tape. Some manufacturers make perforated tables that hold the model well but are difficult to clean. In general, the expediency of applying additional funds to the table depends on the consumable material and the material of the table itself.
Positioning mechanisms
Scheme of operation of positioning mechanisms
Of course, the print head must move relative to the working platform, and unlike conventional office printers, positioning must be carried out not in two, but in three planes, including height adjustment.
Positioning pattern may vary. The simplest and most common option involves mounting the print head on perpendicular guides driven by stepper motors and providing positioning along the X and Y axes.
Vertical positioning is carried out by moving the working platform.
On the other hand, it is possible to move the extruder in one plane and the platforms in two.
SeemeCNC ORION Delta Printer
One option that is gaining popularity is the use of a delta coordinate system.
Such devices are called "delta robots" in the industry.
In delta printers, the print head is suspended on three manipulators, each of which moves along a vertical rail.
The synchronous symmetrical movement of the manipulators allows you to change the height of the extruder above the platform, and the asymmetric movement causes the head to move in the horizontal plane.
A variant of this system is the reverse delta design, where the extruder is fixed to the ceiling of the working chamber, and the platform moves on three support arms.
Delta printers have a cylindrical build area, and their design makes it easy to increase the height of the working area with minimal design changes by extending the rails.
In the end, everything depends on the decision of the designers, but the fundamental principle does not change.
Control
Typical Arduino-based controller with add-on modules
FDM printer operation, including nozzle and platform temperature, filament feed rate, and stepper motors for positioning the extruder, is controlled by fairly simple electronic controllers. Most controllers are based on the Arduino platform, which has an open architecture.
The programming language used by printers is called G-code (G-Code) and consists of a list of commands executed in turn by the 3D printer systems. G-code is compiled by programs called "slicers" - standard 3D printer software that combines some of the features of graphics editors with the ability to set print options through a graphical interface. The choice of slicer depends on the printer model. RepRap printers use open source slicers such as Skeinforge, Replicator G and Repetier-Host. Some companies make printers that require proprietary software.
Program code for printing is generated using slicers
As an example, we can mention Cube printers from 3D Systems. There are companies that offer proprietary software but allow third-party software, as is the case with the latest generation of MakerBot 3D printers.
Slicers are not intended for 3D design per se. This task is done with CAD editors and requires some 3D design skills. Although beginners should not despair: digital models of a wide variety of designs are offered on many sites, often even for free. Finally, some companies and individuals offer 3D design services for custom printing.
Finally, 3D printers can be used in conjunction with 3D scanners to automate the process of digitizing objects. Many of these devices are designed specifically to work with 3D printers. Notable examples include the 3D Systems Sense handheld scanner and the MakerBot Digitizer handheld desktop scanner.
MakerBot Replicator 5th Generation FDM Printer with built-in control module on the top of the frame
The user interface of a 3D printer can consist of a simple USB port for connecting to a personal computer. In such cases, the device is actually controlled by the slicer.
The disadvantage of this simplification is a rather high probability of printing failure when the computer freezes or slows down.
A more advanced option includes an internal memory or memory card interface to make the process standalone.
These models are equipped with control modules that allow you to adjust many print parameters (such as print speed or extrusion temperature). The module may include a small LCD display or even a mini-tablet.
Variety of FDM printers
Professional Stratasys Fortus 360mc nylon FDM printer
FDM printers are very, very diverse, ranging from the simplest homemade RepRap printers to industrial plants capable of printing large-sized objects.
Stratasys, founded by Scott Crump, the inventor of FDM technology, is a leader in the production of industrial installations.
You can build the simplest FDM printers yourself. Such devices are called RepRap, where "Rep" indicates the possibility of "replication", that is, self-reproduction.
RepRap printers can be used to print custom built plastic parts.
Controller, rails, belts, motors and other components can be easily purchased separately.
Of course, assembling such a device on your own requires serious technical and even engineering skills.
Some manufacturers make it easy by selling DIY kits, but these kits still require a good understanding of the technology. RepRap Printers
And, despite their "homemade nature", RepRap printers are quite capable of producing models with quality at the level of expensive branded counterparts.
Ordinary users who do not want to delve into the intricacies of the process, but require only a convenient device for household use, can purchase a ready-made FDM printer.
Many companies focus on the development of the consumer segment of the market, offering 3D printers for sale that are ready to print "straight out of the box" and do not require serious computer skills.
3D Systems Cube consumer 3D printer
The most famous example of a consumer 3D printer is the 3D Systems Cube.
While it doesn't boast a huge build area, ultra-fast print speed, or unsurpassed model build quality, it's easy to use, affordable, and safe: This printer has received the necessary certification to be used even by children.
Mankati FDM printer demonstration: http://youtu.be/51rypJIK4y0
Laser Stereolithography (SLA)
Stereolithographic 3D printers are widely used in dental prosthetics
Stereolithographic printers are the second most popular and widespread after FDM printers.
These units deliver exceptional print quality.
The resolution of some SLA printers is measured in a matter of microns - it is not surprising that these devices quickly won the love of jewelers and dentists.
The software side of laser stereolithography is almost identical to FDM printing, so we will not repeat ourselves and will only touch on the distinctive features of the technology.
Lasers and projectors
Projector illumination of a photopolymer model using Kudo3D Titan DLP printer as an example
The cost of stereolithographic printers is rapidly declining, due to growing competition due to high demand and the use of new technologies that reduce the cost of construction.
Although the technology is generically referred to as "laser" stereolithography, most recent developments use UV LED projectors for the most part.
Projectors are cheaper and more reliable than lasers, do not require the use of delicate mirrors to deflect the laser beam, and have higher performance. The latter is explained by the fact that the contour of the whole layer is illuminated as a whole, and not sequentially, point by point, as is the case with laser options. This variant of the technology is called projection stereolithography, "DLP-SLA" or simply "DLP". However, both options are currently common - both laser and projector versions.
Cuvette and resin
Photopolymer resin is poured into a cuvette
A photopolymer resin that looks like epoxy is used as consumables for stereolithography printers. Resins can have a variety of characteristics, but they all share one key feature for 3D printing applications: these materials harden when exposed to ultraviolet light. Hence, in fact, the name "photopolymer".
When polymerized, resins can have a wide variety of physical characteristics. Some resins are like rubber, others are hard plastics like ABS. You can choose different colors and degrees of transparency. The main disadvantage of resins and SLA printing in general is the cost of consumables, which significantly exceeds the cost of thermoplastics.
On the other hand, stereolithographic printers are mainly used by jewelers and dentists who do not need to build large parts but appreciate the savings from fast and accurate prototyping. Thus, SLA printers and consumables pay for themselves very quickly.
An example of a model printed on a laser stereolithographic 3D printer. In this case, the printer uses a leveling device to flatten the thin layer of resin covering the platform just prior to irradiation. As the model is being made, the platform, together with the finished layers, is “embedded” in the resin. Upon completion of printing, the model is removed from the cuvette, treated with a special solution to remove liquid resin residues and placed in an ultraviolet oven, where the final illumination of the model is performed.
Some SLA and DLP printers work in an “inverted” way: the model is not immersed in the consumable, but “pulled” out of it, while the laser or projector is placed under the cuvette, and not above it. This approach eliminates the need to level the surface after each exposure, but requires the use of a cuvette made of a material transparent to ultraviolet light, such as quartz glass.
The accuracy of stereolithographic printers is extremely high. For comparison, the standard for vertical resolution for FDM printers is considered to be 100 microns, and some variants of SLA printers allow you to apply layers as thin as 15 microns. But this is not the limit. The problem, rather, is not so much in the accuracy of lasers, but in the speed of the process: the higher the resolution, the lower the print speed. The use of digital projectors allows you to significantly speed up the process, because each layer is illuminated entirely. As a result, some DLP printer manufacturers claim to be able to print with a vertical resolution of one micron!
Video from CES 2013 showing Formlabs Form1 stereolithography 3D printer in action: http://youtu.be/IjaUasw64VE
Stereolithography Printer Options
Formlabs Form1 Desktop Stereolithography Printer
As with FDM printers, SLA printers come in a wide range in terms of size, features and cost.