Ceramic 3d printer
3D Printing Materials: Ceramic Resin
Skip to Main Content
3D print parts with a stone-like finish and fire them to create a fully ceramic piece with Ceramic Resin, an experimental material that pushes what’s possible with the Form 2. Fabricate ceramic parts for engineering research, or create distinctive art and design pieces.
Download the Usage Guide
Formlabs is excited to offer the first affordable ceramic 3D printing material for the world’s most popular desktop stereolithography (SLA) system. Be one of the first to work with a material at the forefront of SLA polymer development, previously only available in industrial and research environments at prohibitively high costs.
Ceramic Resin is a silica-filled photopolymer. After firing, the photopolymer network burns out to form a true ceramic part. Fired parts have unique properties that can be leveraged for applications where fired part accuracy is not critical.
View Technical Data (PDF)
Digital artists and designers can use Ceramic Resin to fabricate complex geometries that wouldn’t be possible by hand. Pieces printed in Ceramic Resin can be fired and glazed to produce functional objects.
Order Now
Ceramic Resin is a Form X product. This material is more complex to work with than other Formlabs products and requires extra steps and additional experimentation for successful printing. It may take a few iterations to create a final fired part that meets your specifications.
Make sure to read the Usage Guide in full before using this material.
WATCH THE PROCESS VIDEO
1. Design
Ceramic Resin requires designing within specific constraints for successful printing and firing. Start small, follow the usage guidelines, and experiment.
2. Prep
Sand your build platform to increase print adherence, shake the cartridge to mix the material, and clear the bite valve.
3. Print
Scale your parts in PreForm to accommodate for shrinkage during firing. Send your design to the Form 2 and press print.
4. Post-process
Wash your prints in isopropyl alcohol (IPA) and remove supports (no post-curing necessary). Ensure that parts are completely dry before firing.
5. Fire
Fire your part in an actively ventilated kiln that fires to at least cone 8 to burn out the photopolymer from the material and create a fully ceramic final part. Parts will shrink by around 15% in XY and 29% in Z during firing.
6. Glaze
If desired, apply a glaze of your choosing, following the manufacturer’s instructions.
Ready to start working with Ceramic Resin?
Order Ceramic Resin Now
Data Sheets
Download safety and technical data sheets for all Formlabs materials.
Handling & Safety
Handling & Safety
Resin should be handled with care. Proper handling will ensure safe printing and efficient use. Our resins have been designed to be similar or safer to handle as other household chemicals or adhesives. Formlabs materials do not contain volatile solvents so special ventilation is not required. Skin contact should be avoided.
The Safety Data Sheets (SDS) are up to date for every resin product and follow the latest government guidelines. Always consult the SDS as the primary source of information to understand safety and handling of Formlabs materials. For more information about handling resin, learn more tips for resin maintenance in our Help Center.
Technical Data
Technical Data
Plastics are complex materials, and finding the right one for your specific application requires balancing multiple attributes. Our library of resins is ideal for product development, rapid prototyping, and a variety of specialized applications. Download our Technical Data Sheets to explore the mechanical properties of each material.
Material
– Select –BioMed AmberBioMed BlackBioMed ClearBioMed WhiteBlackCastableCastable WaxCastable Wax 40CeramicClearColor BaseColor PigmentsCustom TrayDental LT ClearDental LT Clear V2Dental SGDigital DenturesDraftDurableESDElasticElastic 50AFlexibleFlexible 80AFull Materials LibraryGreyGrey ProHigh TempIBTModelModel V3Nylon 11Nylon 11 CFNylon 12Nylon 12 GFPU Rigid 1000PU Rigid 650Permanent CrownReboundRigid 10KRigid 4000Soft TissueSurgical GuideTemporary CBToughTough 1500Tough 2000White
Language
– Select –BulgarianChineseCroatianCzechDanishDutchEnglishEstonianFinnishFrenchGermanGreekHungarianIrishItalianJapaneseKoreanLatvianLithuanianMalteseNorwegianPolishPortugueseRomanianRussianSlovakSlovenianSpanishSwedishTurkish
Technical Data Sheets
There is no technical data sheet available for the chosen material.
Safety Data Sheets
There is no safety data sheet available for the chosen material.
3D Potter - Real Clay 3D Ceramic Printers
Our line of 3D Clay printers have some unique features when compared to other 3D printers. We use a cardinal axis system, rather than a delta printer configuration. This allows for precise control with minimal effort. Most clay printers use a pressurized system using compressed air, with a 3D Potterbot a high-pressure system is not needed.
3D Printing Cement is here! We have combined our Scara Elite and Small 50 pump with Sikacrete® 3D printer cement developed by Sika USA. This is a versatile and convenient way of printing large-scale architecture and structures.
The Scara Elite is the first viable large-scale ceramic 3D printer using 3D printing material. It is capable of printing multiple objects non-stop. The Elite with the Small 50 can pump up to 3.5 gallons of material per minute through 85 feet of 1″ hose.
They work together so well, we decided to make them a package.
The possibilities are endless!
PR Articles/Videos
Great entry-level printer
More info
10 Proreliable and accurate
More info
Full size, Full control
More info
View this post on Instagram
A post shared by Hybrid Objects (@hybrid.obj) featuring non-planar printing.
View this post on Instagram
A post shared by Arina Erdélyi (@arinaerdeyli) featuring a print taken to new heights.
View this post on Instagram
A post shared by Atlas of Lost Finds (@atlas_of_lost_finds) featuring large-scale printing.
![]()
See More
3D Potter is proud to offer assembly tutorials and troubleshooting videos for our printers. Our printers can be used with Potterware, a beginner-friendly program to design pots and vases of all shapes, sizes, and patterns.Check out our Youtube channels to see our videos!Assembly Videos
Main Channel
3D Potter accepts payment of Bitcoin (BTC) for our products. If you wish to pay by BTC, please contact us.bitcoincash:qr5wmqhnylzr0hcewfrla852xxy9zhp94uugrxy9ay
Here at 3D Potter, we like forward-thinking and preserving the environment.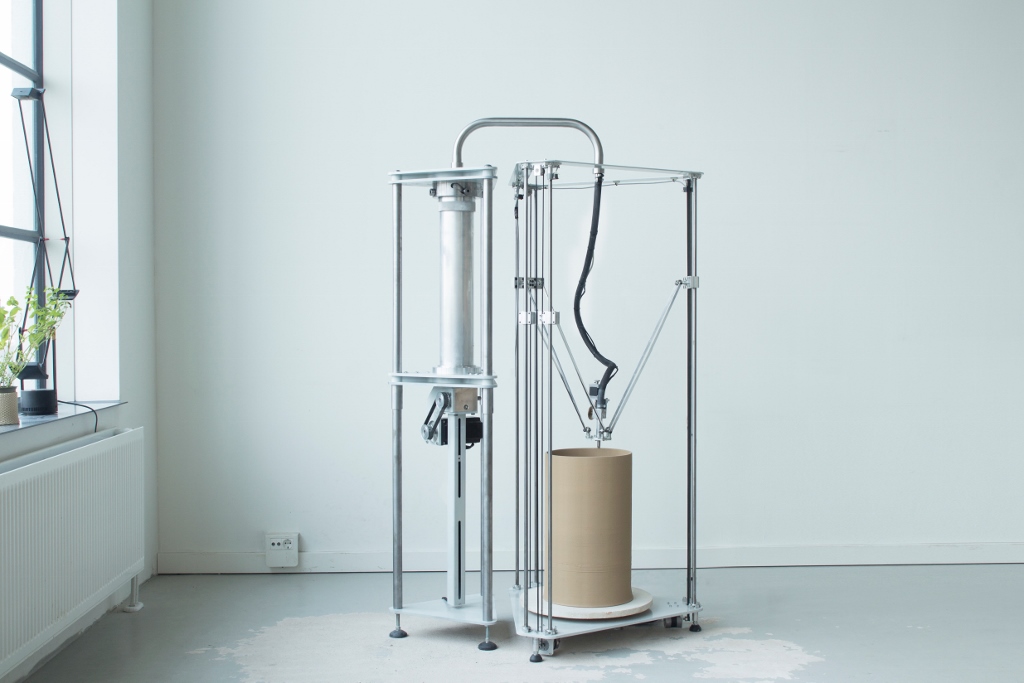
https://www.tesla.com/referral/dan47410
Ceramic 3D printing | Alumina Systems GmbH
Ceramic 3D printing has been on everyone's lips for several years and has several hypotheses and names such as Rapid Prototyping (RP), Solid Freeform Fabrication (SFF), Additive Manufacturing (AM) or whatever is currently popular name 3D printing. Hypotheses have been born again and again from the idea that with the help of a 3D printer, Al2O3 printed components can be produced by anyone in the shortest possible time, and that conventional production will be redundant in the future.
Each new hype disappeared when it became clear that this would not happen. Despite all this, technical ceramics with 3D printing technology, especially for materials of the metal and plastic class, have been used in industry for many years. The market is yielding to stable growth. Especially at trade shows such as the annual Formnext trade show in Frankfurt am Main, it is always clear how high the proportion of 3D printing equipment suppliers and service providers is. The field of ceramic 3D printing, especially technical ceramics, is lagging behind metal and plastic. This is mainly due to the high demands placed on technical ceramics and their non-trivial manufacturing process.
Alumina ceramics 3D printing
There are currently only two major suppliers of technical ceramics 3D printing equipment on the market: Lithoz, which developed LCM technology based on photocrosslinkable polymers, and 3DCERAM, which successfully applies the same physical basis for laser stereolithography in the production of technical ceramics. Alumina Systems has worked closely with Lithoz for over 5 years and has brought LCM technology to the industry in a matter of months.
3D printed ceramic components
Alumina's in-house 3D printing has been enhanced by the acquisition of 3DCERAM's largest commercially available 3D printer. The printer has a construction area of 600mm x 600mm, which allows the production of 3D printing components in unprecedented dimensions. In addition, it is possible to manufacture special parts in small or series production. Alumina Systems claims to be the undisputed leader in technical ceramics 3D printing due to innovation and customer proximity. To do this, Alumina Systems acquired a dedicated IP address to develop their own 3D printing process for industrial use.
A new process that will be available as an alpha tool from Alumina in early 2020 is the laser-induced casting of plain bearings. This process processes many times cheaper ceramic materials than any other printer on the market. In addition, the assembly time is less and the geometry of the components in terms of wall thickness and dimensions is practically unlimited physically. Because this produces a "green" body with a low binder content, the long and delicate debinding process required by other processes is obsolete. It follows that the reliability of the process is greatly increased and the costs and time for heat treatment are significantly reduced.
Ceramic Prototyping in Ceramic 3D Printing
In terms of innovation and component geometries, Alumina Systems is already a leading company in ceramic 3D printing and will continue to do so in the future.
Ceramic 3D printing - Al2O3 condenser
Ceramic 3D printing - Al2O3 heat exchanger
Ceramic 3D printing - Al2O3 mixing section
Ceramic 3D printing - Al2O3 separation column
Industrial 3D ceramic printers
SLS-C ceramic 3D printer
SLS-C industrial 3D printer specifications for ceramics
Model | SLS-250С | |
CO2 laser, Power W | 55 | 100 |
Scan speed | 5 m/s | 5 m/s |
Print Layer Thickness | 0. | 0.06-0.15mm |
Laser spot size | ≤0.4mm | ≤0.2mm |
Print Accuracy | ±0.2mm | ±0.1mm |
Print chamber size mm | 250*250*250 | |
Powder supply | Two pistons on both sides | |
Print material | Corundum, zirconium oxide, silicon carbide and other ceramic materials with the addition of a binder nanopowder. | |
Operating system | Windows XP | |
Software | HUST 3DP | |
File Format | stl, layer thickness change, scanning. |