3D printer shock absorber
These 3D Printer Shock Absorbers Will Reduce Vibrations and Keep Your House Silent at Night - 3DPrint.com
Did you ever imagine what it would be like to drive in a car that wasn’t equipped with a suspension? We have a tendency to take the shock absorbers on our automobiles for granted. In reality, they are responsible for ensuring that we get to our desired destination without having our backs thrown out of place.
Shock absorbers aren’t just used in cars. They are used in many other mechanical devices and equipment as well, to absorb shock by converting the kinetic energy into another less aggressive form of energy (usually heat).
For one IT manager, named Simon Chan, he is used to finding solutions to problems on a daily basis. After all it is his job.
“I believe that even if something works, there’s always a better way of doing it,” Chan tells 3DPrint.com. “The constant desire to improve will drive innovation and I would be happy if people find ways to improve on my designs because I’m sure these are not the ultimate solutions.
”
Chan’s latest design is something that he created in order to aid in his obsession of 3D printing. Chan, like many of us, has a desktop 3D printer, and he has a tendency to run it at all hours of the day and night. However, he was having a problem that he couldn’t seem to solve.
“In spite of sitting the printer on a foam mat, the vibrations from infills and rapid axis changes would rattle even the heavy sideboard it sits on,” Chan tells us. “In turn, low-frequency vibrations could be heard even a couple of floors below my apartment. I did consider putting a rug or some insulation under the sideboard but it wouldn’t solve a generic problem that I’m sure many 3D hobbyists face.”
So being the problem solver that he is, Chan set out to not only find a solution, but to design one that could actually be 3D printed itself. Starting with Google SketchUp, he drew out a design for what he called the “Printer Shock Absorbers.” His design was based on research that he did on how to earthquake-proof buildings. He wanted a product that would be durable, easy to produce, and would support any 3D printer on the market.
“I went with a hybrid solution of 3D prints, coupled with tough extruder springs,” Chan explains. “The base units are the heart of the system, and any user with a different printer simply needs to adapt a mount for their printer’s feet to join the shock absorber’s base unit.”
The four small devices, which consist of five springs each, rest under the four corners of the 3D printer. In turn, when the printer is running, and is making rapid X/Y axis movements and directional changes, it dampens the vibrations, dissipating the energy instead of letting it create noise and/or long-term issues of jarring the printer’s components loose.
“This design allows 360 degree movement and I no longer feel or hear the vibrations I used to get on the table,” said Chan. “I’ve kept the old foam mat until I have time to get some nice fitting rubber feet.
”
In all, it it took about 6 hours for Chan to complete his 10 prints on his Printrbot Simple Metal 1403 3D printer. He has since made the files available for others to download as well on Thingiverse. Other than the 3D printed parts, the shock absorbers consist of the aforementioned springs as well as 16 M3*8mm screws to lock the printer feet clips to the base units.
What do you think about this clever idea? Do you wish to reduce the vibration-caused sounds of your 3D printer? Discuss in the 3D printed shock absorber forum thread on 3DPB.com. Check out the video of the shock absorbers in action below.
Stay up-to-date on all the latest news from the 3D printing industry and receive information and offers from third party vendors.
Tagged with: 3d printer shock absorbers • 3d printer shocks • google sketchup • shock absorbers • springs • thingiverse
Please enable JavaScript to view the comments powered by Disqus.
Part of the Week – 3D Printed Shock Absorber
As you’ve seen from a few of our previous posts, every Friday we see what interesting things our creative employees have made at Part of the Week. Since the recent launch of our new Onyx filament, our applications team has been testing the limits of this industrial strength 3D printing material and discovering new ways to use it. Last Friday, Part of the Week went to my 3D printed shock absorber.
While I haven’t determined the spring constant yet, this 3D printed shock absorber springs back to its equilibrium position after being loaded.So lets start from the beginning. As you may have seen from my reinforced living hinges post, I’ve been experimenting with the flexibility of our filaments. While Onyx is stiffer than Tough Nylon, when it is not reinforced it is still a bit pliable. When originally testing its overhang tolerance to showcase dimensional stability, I printed this part:
Originally printed as an overhang test, this print also shows you can make 3D printed springs with Onyx!Initially to show how it handled overhangs, I then realized…it also functioned as a spring! It turns out that Onyx is strong enough and flexible enough in the Z direction to actually allow for 3D printed springs, both for extension and compression.
By altering the dimensions: thickness, coil diameter, pitch, etc, I figure you can adjust the spring constant to create different damping behaviors, but this has yet to be tested. The compression spring was just a 3D printed coil with no support material, while the extension spring I actually designed with two coils, essentially making two springs in parallel. Both were printed without support material, so in the extension spring design, each section of coil is actually resting on the section below it.
A few slices of the Extension spring in Eiger – each coil rested upon the one below it.I then took this another step further to create the shock absorber. Instead of printing the springs exposed, I enclosed them in a cylinder and added a shaft and mounting holes.Everything in Onyx is actually a single part, so it is all connected. This had to be printed with no supports, or else it would be impossible to remove the ones on the inside! Here’s a cross section view of the shock absorber, modeled in Autodesk Fusion 360:
The cross section of the 3D printed shock absorber.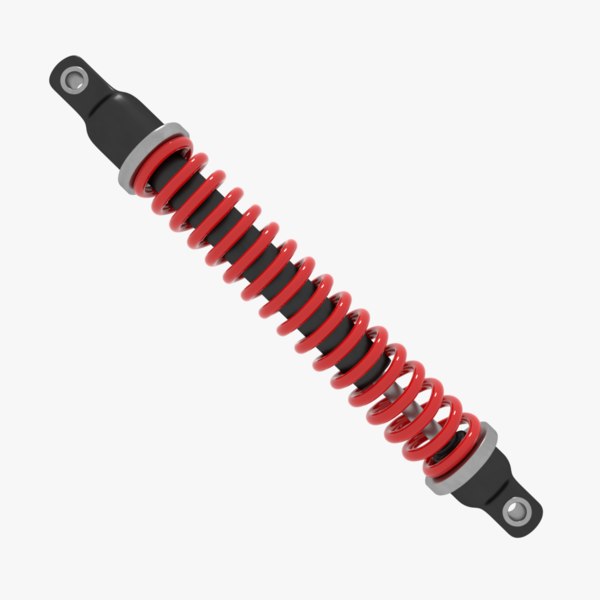
Note that there are actually three parts in this shock: the largest part is the main body, which includes the cylinder, shaft, and spring all connected and printed as one piece in Onyx. I was concerned for the friction between a few of the surfaces – including the spring contacting the inside wall of the cylinder, and the shaft rubbing against its hole through the top of the cylinder, so the other two pieces are printed in nylon. One is a sleeve to slide in to the inside of the cylinder, and the other a bushing for the hole in the top. our Tough Nylon is a bit smoother than our Onyx filament, and nylon is commonly used for bushing material, so I figured it’d be a neat way to use it.
The 3D printed nylon sleeve and bushing to reduce friction in the shock absorber.To avoid support material, I kept all angles under 60 degrees from the overhang, and calculated the pitch of the spring to ensure that it was an overhang the printer could tolerate. Like the extension spring above, I actually used two coils in this design to support the shaft of the shock.
You’ll notice in the cross section view that the nylon sleeve is entirely encased in the shock body. To get it in, I printed the nylon sleeve and bushing first, out of nylon on a Mark Two. I then added two pauses to the shock absorber print. The first one was on the layer directly above where the nylon sleeve ends, to slide the nylon sleeve in. I then started the shock absorber print out of Onyx on a Mark Two Enterprise Printer, and waited (a long time) for the first pause.
A shot of the part mid-print, just after the nylon sleeve is put in. The Onyx prints directly over it.I slipped the nylon sleeve in, resumed the print, and the Onyx filament printed right over the nylon. The next pause was after the top of the cylinder had finished printing, so that I could slide the bushing on. Once the print is complete, the bushing and sleeve are entirely encased in the shock absorber. With a little superglue, I fixed the bushing in place to prevent it from popping off.
And there you have it, a fully 3D printed shock absorber. I’d like to cycle test this at some point to see when it starts to fail, but the problem is, now that it’s fully enclosed I can’t really tell how it’s behaving…please comment or share if you have ideas for interesting ways to use this property of Onyx!
The full 3D printed shock absorber, with integrated nylon sleeves and bearings.If you end up 3D printing anything cool with your Markforged printer don’t forget to share it with us on Twitter or Instagram!
Here are all the STL files and MFP files you’ll need to make the shock absorber:Shock Body: STL and MFP (remember, if you use the STL, print with no supports! The pauses are in the mfp file at layers 758 and 880.)Nylon Sleeve STLNylon Bushing STLSleeve and Bushing MFP
Unique shock absorber made of 3 different materials / 3d printing / 3Dmag.
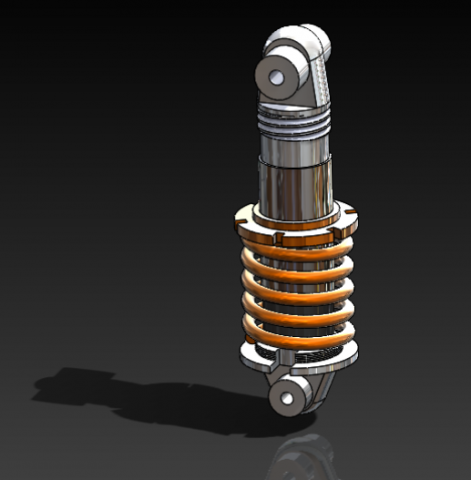
Covestro are known for developing various resin materials for 3D printing over the years. Combining all its experience, the company at Fakuma 2018 is going to present to the public a complex demonstrator - a shock absorber obtained from various materials using different 3D printing technologies.
The outer spring of the device, measuring 40x7 cm, is made of thermoplastic polyurethane TPU. It was formed in layers using selective laser sintering, which made it elastic and resistant to wear. The adjusting screw inside the shock absorber must be strong and rigid. It is these properties that correspond to the polycarbonate thread from the developer. FFF was chosen as the 3D printing method. Finally, the air chamber was made from liquid polyurethane resin using a light curing method.
All of these components were subsequently connected to each other in a single design. “This complex structure is impossible to manufacture with conventional manufacturing processes,” explains Lukas Breuers, marketing manager for 2D and 3D printing at Covestro. “Another new development is the combination of different materials with different individual properties, which has allowed us to significantly expand the possibilities of 3D printing and its applications.”
Related entries:
-
just4fun
3d printing → $443,000 Iron Man flying suit 0 -
hedin
3d printing → Radio receiver without power supply 0 -
hedin
3d printing → 3D models of figures from Madame Tussauds 0 -
just4fun
3d printing → Slot Car Racing 0 -
just4fun
3d printing → Large printed skeleton at the Mexico Light Festival 0
Only registered and authorized users can leave comments.
Best STL Files for Amortisseur・Cults 3D Printer
STRUT GOLF IV GTI
5 €
CR-10 Racquetball Legs
Free
PISTON MEN
0,50 €
NEMA17 - damper
Free
Small Monitor Damper Stand (ADAM A3X)
Free
Shock Valve Knob for Ski-doo freeride
Free
LAOTIE ES18 Steering Damper Front Support Bracket
Free
Damper for Mini Kossel/2020 extruders
Free
Shock Absorber 1:10 RC Car (Suitable for Tarmo4)
Free
Anet a8+ shock absorbing feet
Free
spring air piston
€0. 50
Damper for standard profile 2020
Free
Carrea Power Machine Shock Absorber Spare Part
Free
shock absorber keychain
Free
Y Damper Support for Ender 3
Free
Xiaomi M365 Damper Adapter
1 €
Friction ring for Peugeot 103 fork
1,50 €
Shock absorber
1 €
Shock absorber with coil and reservoir
2.56 €
RC 9 SHOCK ABSORBER INFLATION BRACKET0059
5 €
COMPRESSION BUSHING KAYABA KYB
4,99 €
Anycubic Kobra Max Squashball Legs / Feet (shock/vibration damper)
Free
Matt shock absorber
2. 05 €
Car front suspension
3.07 €
Yamaha XJ 550 Side cover bracket kit
0,50 €
RC car shock eyelet insert
Free
Shock absorber cover for Ryker 600 and 900 ACE
3 €
SL_ST STABLE FPV
Free
Artillery Genius Pro Foot Silencer
Free
RC SHOCK ABSORBER FILLING SUPPORT
0,80 €
CNC frame leg 2020
Free
Shock absorber Suspension
10 €
Silencer GY6, 139QMB 37 mm
Free
Vibration damper
2,50 €
Van cabinet door damper
Free
Matt shock absorber
3,25 €
stand filling shock absorber car rc
2 €
RC shock absorber repair broken
Free
shock absorber
9.