Can you 3d print stainless steel
Stainless Steel Material for 3D Printing: 3D Printing Metal
Are you looking for the perfect metal 3D printing material for your project? Stainless Steel 316L allows to produce corrosion-resistant and functional parts. Here are all information and advice to help you print your 3D model in our Stainless Steel 316L (metal) material.
Colors
Characteristics
Surface Look
Details
Strength
Flexibility
Stainless Steel 316L Material Guide
Overview
Design Guide
Technical Specifications
What is Stainless Steel 316L?
Objects printed in 316L stainless steel at Sculpteo are created from fine metallic powder primarily composed of iron (66-70%), enriched with chrome (16-18%), nickel (11-14%), and molybdenum (2-3%). The material provides strong resistance against corrosion and is distinguished for its high ductility. These features make it a great candidate for implementation in several industries, such as the medical field for surgical assistance, endoscopic surgery, or orthopedics; in the aerospace industry for producing mechanical parts; in the automobile industry for corrosion-resistant parts.
316L Stainless Steel printing is very accurate because of the fine coating resolution (30-40 µm) and the laser’s accuracy. Unlike polymer powder sintering, stainless steel printing through DMLS requires adding base structures in order to attach the part to the board and to strengthen distinctive geometries like overhangs. The bases themselves are made from the same powder as the piece and will be taken off afterwards.
With no particular finishing, the material gives off a granular and coarse appearance, though suiting most applications. Smooth and shiny surfaces can be acquired after printing through finishing steps. Pieces can be machined, drilled, welded, electro-eroded, granulated, polished, and coated.
Compared to the other metal 3D printing materials, stainless steel is the smoothest material.
To find out more about the mechanical properties of our stainless steel, refer to the specifications paragraph and the technical data sheet.
What can you do with Stainless Steel 316L?
Since the stainless steel is melded at a very high temperature, the additive metallic production process requires vast technical mastery for the initial studying of thermal and mechanical effects before 3D printing. It also requires excellent knowledge of finishing techniques for the object’s completion.
Successful additive production of stainless steel parts often constitute projects in which 3D printing is wholly justified given it is the best alternative when compared to other production methods (foundry, machining, cutting). We have noted that these benefits to 3D printing are often found in:
- Complex design/ Wired Geometries/ Fixed Mechanisms
- Speed, shortening assembly time
- Topology Optimization / Reduction
- Small-Volume Production
- Mass Customization
- Remote Production
To ensure the successful production of your piece, having to modify your initial design is commonplace. Even if we must be repetitive, we prefer to warn you: if you wish to create a stainless steel piece just for curiosity, you risk being disappointed when confronting the necessary effort and cost of undertaking the project!
316L Stainless Steel is a good material for printing both functional and spare parts in 3D. The material is easy to maintain because it attracts little dirt and the presence of chrome gives it the added benefit of never rusting.
316L Stainless Steel is used to offer solid pieces and essential hygienics in several industries such as the medical, aeronautical, automobile, and domestic products industries.
Pricing and delivery
The printing price of your design is calculated automatically the moment it is uploaded. As you modify your object (changing material, finishing, size, using batch control or hollowing feature, etc.) you will note that the price changes automatically. The pricing is based on a series of factors, including total volume, object size, and bounding box – to name a few.
Keep in mind that adding finishing will extend the processing time. The estimated shipping time is also calculated automatically as the object is uploaded and each time you make a modification on it. Delivery time should be added to processing time.
For more information, check our pricing page.
3D printing process of our Stainless Steel 316L
Stainless Steel 3D printing is produced by fusion or laser sintering. Two possible technologies exist for this material: DMLS and SLM. At Sculpteo, we use DMLS (Direct Metal Laser Sintering) technology, a laser sintering technique on an EOS M280 machine to print stainless steel. The laser beam brings the metal powder close to its fusion point layer after layer in order to produce your object.
Since the stainless steel is melded at a very high temperature, the additive metallic production process requires vast technical mastery for the initial studying of thermal and mechanical effects before 3D printing. It also requires excellent knowledge of finishing techniques for the object’s completion.
Printing resolution
Size limitations
Minimum thickness and geometry
Etching & embossing
Enclosed & interlocking volumes
Minimum spacing and clearances
Piece assembly restrictions
Hollowing
Files with multiple objects
Multiple objects and clusters
Standard layer thickness | 40 µm |
Accuracy | +/- 0.![]() |
Maximum size raw | 220 x 220 x 250 mm |
Minimum wall thickness | 1 mm |
Minimum thickness for particular design aspects | 1 mm |
The walls of your design must adhere to a minimum thickness of 2 mm in order to guarantee the structure will not break. If the walls of your model are less than 2 mm, we recommend you to thicken them or add a support structure to maintain stability.
To ensure the solidity of an object, a minimum thickness of 2 mm is recommended.
It is also important to keep in mind that the object is to be printed in a physical form. Thus if a thin aspect is supporting something that is too heavy for it, it may break – even though it is possible with the physics provided within the 3D printing program. We recommend adding a bit of thickness to the places that will get a lot of handling, or that support the most weight.
Minimum size of details | 1 mm |
Minimum height and width details | Embossed: 0.5 mm Engraved: 0.5 mm |
Minimum height and width for a readable text | 1 mm |
Enlargement ratio | 1/1 |
A detail’s minimum precision is mainly determined by the resolution of our printers. However, during the cleaning process, a fine layer of detail can also be lost. In order for a detail or a text to be visible, we highly suggest you follow our recommended sizes at the very least. To ensure a better powder removal (thus a better detail precision), the width of your details must be at least as big as depth.
Enclosed parts? | Not recommended |
Interlocking parts? | Not recommended |
Minimum spacing between fixed walls | 0.2 mm |
Minimum clearance between parts | 0.![]() |
For a successful 3D print a minimum clearance between objects is required to allow excess material to be sand blown out. If this space is not left within the design, the object will be solid. This is particularly important for articulated objects – as the space left between the walls will define the object’s ability to move.
Clearance should be at least 0.2 mm and depends on the size of your object. For big sizes, the clearance should be greater. This is due to the DMLS printing process. Our printer beds are heated during the process, and larger objects are heated for longer periods. A small space between objects creates the risk of melting them together as they remain under heat for a long period of time. In some other cases, holes should be added to allow us to drain for the excess powder material within the clearance.
Assembly? | No |
Hollowing? | No |
Files with Multiple Objects ? | No |
This is not possible to 3D print a 3D file containing several objects with Stainless Steel.
It is not possible to print a 3D file containing several objects, that’s why we cannot accept files that contain clusters of multiple objects. Though, if you wish to purchase more than one identical parts, you can select the number of parts you want to order during the checkout. The more parts you order, the lower your price per part gets.
You can also use our online tools and see our tricks and tips on how to reduce your 3D printing price.
To get more information on your metal additive manufacturing service, you can contact our qualified sales team.
Mechanical Properties
Documentation
Mechanical Properties | Conditions | Unit | Value |
---|---|---|---|
Ingredients | – | % | Iron: 66- 70 Chrome: 16-18 Nickel: 11- 14 Molybdenum: 2- 3 |
Density of laser-sintered part | EOS-Method | g/cm3 | 7.![]() |
Tensile strength (XY) | ISO 6892 / ASTM E8M | MPa | 640 ± 50 |
Tensile strength (Z) | ISO 6892 / ASTM E8M | MPa | 540 ± 55 |
Yield strength (XY) | ISO 6892 / ASTM E8M | MPa | 530 ± 60 |
Yield strength (Z) | ISO 6892 / ASTM E8M | MPa | 470 ± 90 |
Young’s modulus (XY) | ISO 6892 / ASTM E8M | GPa | 185 |
Young’s modulus (Z) | ISO 6892 / ASTM E8M | GPa | 180 |
Elongation at break (XY) | ISO 6892 / ASTM E8M | % | 40 ± 15 |
Elongation at break (Z) | ISO 6892 / ASTM E8M | % | 50 ± 20 |
Melting point | – | °C | 1400 |
- Datasheet
Related blog posts:
Ready to 3D print with Stainless Steel 316L?
With Sculpteo’s online 3D printing service you’re just a few clicks away from professional Stainless Steel 316L 3D printing. Your 3D model is printed with the highest quality and delivered straight to your door.
Get started now!
3D Printering: To Print Stainless, You Do Half The Work
- by: Al Williams
Everyone wants to print using metal. It is possible, but the machines to do the work are usually quite expensive. So it caught our eye when MakerBot announced a printer — armed with an experimental extruder — that can print stainless steel parts. Then we read a bit more and realized that it can only sort of do the job. It needs a lot of help. And with some reasonable, if not trivial, modifications, your printer can probably print metal as well.
The key part of the system is BASF Ultrafuse 316L Stainless Steel filament, something that’s been around for a few years. This is a polymer with metal incorporated into it. This explains the special extruder, since metal-bearing filament is hell on typical 3D printer nozzles. However, what comes out isn’t really steel — not yet. For that, you have to send the part to a post-processing facility where it is baked at 1380 °C in a pure hydrogen atmosphere using special equipment. This debinding and sintering produces a part that the company claims can be up to 96% pure metal.
It sounds as though there may be more than one post-processing facility possible, but for now everything is available from MatterHackers. However, metal printing still doesn’t come cheap. A roll of filament — it looks like a 1 kg roll — costs $465. That comes with a “ticket” for postprocessing one batch of parts that weigh up to 1 kg. Additional tickets are $50. They also suggest you use a special pen to attain bed adhesion, which costs only $18, but is out of stock as we write this.
On the other hand, if you need a part in stainless steel, this isn’t that expensive. According to Matterhackers, you can run this filament through most 3D printers, although we are betting you will want a pretty stout extruder and nozzle. You’ll also need a heated bed that can make at least 100 °C. A lot of beds can’t get that high, or have coatings that won’t tolerate that high a temperature. MakerBot’s METHOD X printer can do this, but you could probably upgrade your printer to do it as well.
So how is this better than just having someone do a metal print for you? We can print PLA models to get the design right and then send out to a service provider with a big-money metal printer. It sounds like you might get a faster turnaround by doing it yourself, but it isn’t clear to us why that has to be the case. We took a 40 mm x 40 mm x 4 mm bracket design and asked a service company for a price. In 316L steel, the part would cost $70 shipped. You could get it in aluminum for the same price, or titanium for $112. Gold was also an option, but at $6,400, we’ll pass. The same part in PLA was about $10, and at that price, we’d say it makes sense to print at home. But for metal, we’re comparing a $50 ticket and other material and wear costs with $70, delivered.
The video below shows some design tips, some of which are common sense to designers used to 3D printing. However, some appear to have to do with the sintering process and we wondered how much the part’s dimensions might change after the sintering process. The video claims you should scale your parts 120% in the X and Y dimensions and 126% in height. The video mentions a 100 cubic millimeter limit on parts, but if you read up, you’ll see they really mean a cube 100 mm on each side, which is 1,000,000 cubic millimeters, and significantly bigger.
So will you try this out? Unless you have a pretty robust machine, you’ll need some upgrades first. Then you still have to wait for your metal part to come back in the mail. As cool as it would be to print in stainless, we’ll wait until we can produce the metal part with no outside help.
If we were going to try it, we might think about a ruby nozzle. Maybe we’ll wait for the $400,000 printers to show up on the surplus market.
3D printing with stainless steel in the center of additive technologies St. Petersburg
Stainless steel is one of the most used materials for metal 3D printing. Although stainless steel is notorious for being poorly processed by classical methods, it is one of the best materials for 3D printing.
Stainless steel does not oxidize and therefore does not suffer from humidity. Metal 3D printing uses very fine metal powders, which means that the surface area relative to the volume is very high. Which, in turn, indicates a high rate of reaction between the material and the atmosphere. And the slight amount of moisture in the air can rust normal steel powder, but not 3D printing stainless steel powders.
Other materials for 3D printing, such as aluminum or titanium, become combustible or even explosive in the form of micropowders. And stainless steel remains a relatively safe material for metal 3D printing.
Also, the surface quality of a part when 3D printed with stainless steel is usually better compared to other materials.
The choice of stainless steel powder for 3D printing should begin with the alloy composition requirements specified for a particular part. The second step is to find a manufacturer of powders from this alloy. There are many different stainless steel alloys in powders for 3D printing on the market, but only a few of them are in the warehouses of manufacturers, and in order to get the powder at an affordable price and in a reasonable time, it is better to choose an alloy from those that are widely used in metal 3D printing.
Metal powder for 3D printing is not just metal dust. In order to get good results in metal 3D printing, the powder must have a certain particle size distribution and have particles of a strictly spherical shape.
Why is particle shape so important in metal 3D printing? Spherical powders have the best fluidity, which in turn affects the uniformity of the layers. Given a typical layer thickness of 20-50 µm, the layer plane can be destroyed by any non-spherical or out-of-dimensional particle.
The second reason is that spherical powders have the highest bulk density. If we consider the density of stainless steel powder for 3D printing, then it will be 1.5 times less than that of a solid part (~4.5g/cm³ for spherical powders and ~7.7g/cm³ for a solid steel part). This means that the powder is compressed to 60% of its original volume during the stainless steel 3D printing process. Thus, if you want to get dense parts devoid of porosity, you should only choose strictly spherical stainless steel powders for 3D printing.
Here you can see some of the 3D printed stainless steel samples that were produced in our Additive Technology Center (ATC) in St. Petersburg.
Usually when people talk about 3D metal printing, they only think about parts for the space or aviation industry. But 3D printing with stainless steel today can be found in completely different industries. Based on our own experience, we can highlight the following examples:
-
3D printed 316L stainless steel watch case
-
3D Printed 316L Stainless Steel Computer Port Shields
-
316L Stainless Steel and 15-5PH Printed Automotive Turbo Hose Plugs
-
3D printed stainless steel special adapter sleeves
-
3D printing stamps for stainless steel leather goods stamping
-
3D printed stainless steel housing for electronic components Ph2
-
Each of our 3D printers contains at least 10 stainless steel printed parts.
Even
-
316L stainless steel 3D printed decorative items
Steel 3D Printing - Quick Guide
Any metal 3D printing technology can print with steel. This is the most popular material. But which steel grades and which technology is best for your application? Will printed steel parts really be as strong and durable as traditionally made parts?
Let's see how a 3D printed steel part revolutionizes manufacturing and opens the door to new applications in aerospace, medical equipment, automotive, tool making, heavy industry, architecture and more. In addition, more affordable desktop printers are expanding the scope and scope of real steel 3D printed parts.
Strength of steel printed parts.
Cast steel part (left), 3D printed version (center). On the right, a fully 3D printed hinge requires no assembly. (Source: Desktop Metal) The most common question when it comes to a 3D printed metal model is "Will it be as strong as a forged or cast part?" ?". The short answer is yes... and no.
3D printed steel parts can be just as strong, and sometimes even stronger, than those made in the traditional way. It depends on many factors such as: end use, type of steel, choice of 3D printing method, post-processing and shape of the part. Also, the comparison depends on which of the strength characteristics you focus on: tensile strength, static load strength, fatigue strength, etc.
Parts printed from steel are used in the aerospace industry, for the military, and also, for example, for the manufacture of a footbridge, shown below. Therefore, the strength of printed products is beyond doubt, but let's take a closer look.
Queen Maxima of the Netherlands officially opens a 3D printed metal bridge. Photo by Adriaande Groot (Source: MX3D) A 3D printed or laser powder sintered (LPBF) steel part has a finer grain structure than cast metal products. This provides better tensile strength characteristics, but in other respects the cast parts are currently still stronger. Most often, LPBF 3D printing is used to replace cast components, but in some cases, 3D printed components can replace forged parts.
One study showed that, under certain conditions, stainless steel parts made using LPBF 3D printers were three times stronger than parts made from the same steel using the traditional method.
In experiments comparing 3D printed steel parts to traditionally made steel parts, researchers create identical parts using two methods and compare their performance. However, head-to-head comparison of details is only part of the big picture.
The main advantage of printing with steel is not only its strength, but also the unique ability to create internal channels and lattice fillings in parts, which is impossible using traditional manufacturing methods. Metal 3D printing makes it possible to produce parts faster than traditional production, since this method does not require the use of special equipment and tools, it allows you to create assemblies as a whole, eliminating the need for subsequent assembly and welding. Designing a printed part usually means that less metal is needed to make it, and therefore less weight, for the same strength.
Steel 3D printing is also more stable and cost effective as it reduces waste. When using subtractive manufacturing methods, such as CNC machining, you make a part by cutting it out of a large one, with a lot of waste. With additive manufacturing, you only use the material you need to make the finished product.
Steel 3D printing is not intended to replace traditional methods in all areas, but it may be a better choice for a wide range of applications. Particularly when the required parts are unique and designed for specific applications, such as rocket engines, racing cars or the oil and gas industry. 3D printing is the fastest and most flexible technology for mass production and prototype production. For military and industrial applications, steel 3D printing is a faster and more efficient way to create individual parts for vehicles and machines. Stainless steel 3D printing is rapidly finding applications in medicine to create unique surgical instruments and implants.
If you know what characteristics your final product should have (tensile strength, compressive strength, hardness, density, etc.), then all these parameters can be incorporated into the product at the production stage.
Types of steel for 3D printing
Metal powder is the most used metal material for 3D printing (Source: GKN Additive)There are thousands of different grades of steels and alloys with different mechanical properties, used in traditional manufacturing but in 3D printing there are only a few dozen of them, and some of them are unique, created specifically for this technology. Among the steel options, the following can be distinguished:
-
Stainless steel (316L, 304L , 17-4PH, 15-5PH, 420, 254, Ph2, GP1, 630, 410).
-
Tool steel (D2, M2, h23, h21, MS1, 1.2709).
-
Low alloy steel (4140).
-
Structural alloyed (20MnCr5).
Recently, unique alloys have been developed specifically for 3D printing, designed to solve the problems that occur with classical production methods.
For example, 3D printer manufacturer Desktop Metal released a patented stainless steel in 2022 that the company says combines the tensile strength, ductility, and corrosion resistance of 13-8 PH stainless steel, combined with the hardness low alloy steel like 4140. The company says customers can go to market with this material and skip the galvanizing step to protect products from corrosion.
ExOne offers two special blends of steel and bronze that the company says allows 3D printed steel parts to achieve increased corrosion resistance while being easy to machine and polish.
While most of the metal powders used in 3D printing are similar to those used for other manufacturing methods, their numbers are on the rise as more companies adopt the technology. Some metal powder manufacturers, such as GKN, also make custom powders for specific 3D printing applications.
How to print with steel
The strength, properties, and applications of 3D printed steel products largely depend on which 3D printing technology you use. Some methods produce stronger parts, other methods provide better hardness or abrasion resistance, and some technologies are simply very fast.
Below are the main metal 3D printing methods, their properties and some of the most common application examples.
Fused Deposition Printing (FDM)
BCN3D's Epsilon printer extrudes metal filament from stainless steel (Source: BCN3D) as more printer manufacturers certify metallic filaments for use on their printers, such as Ultimaker, BCN3D, Makerbot, Raise3D. Raise3D has recently released a complete metal printing suite - Metalfuse (3D printer, debinding oven and sintering oven). This method is still much more popular for printing plastics, but with new plastic filaments filled with stainless steel powder, strong metal parts can be produced.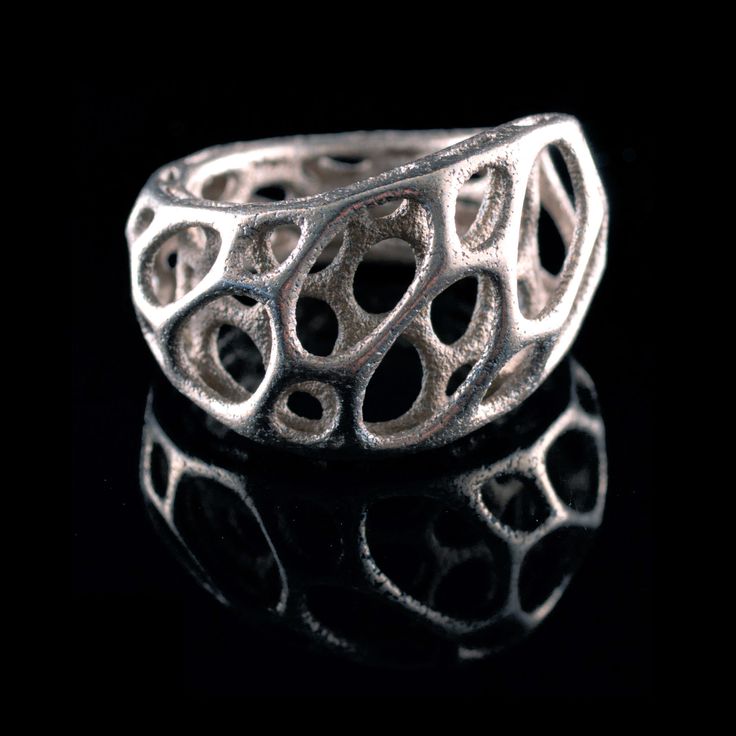
FDM media was once limited to thermoplastics. Companies like BASF Forward AM and The Virtual Foundry now offer metal filaments that can be used on almost any FDM printer as long as it has a hardened steel nozzle for abrasive media.
These materials are approximately 80% metal and 20% plastic. After printing, the post-processing process removes the plastic, resulting in 100% metal parts.
Due to the removal of the bonding plastic, FDM metal parts shrink during post-processing. The amount of shrinkage is constant and can be taken into account in CAD systems, which allows to obtain relatively accurate finished parts.
Forward AM's 316L Stainless Steel Ultrafuse filament produces finished parts with material properties that the company claims are comparable to injection molded metal parts.
(Source: BCN3D) While 3D printing with metallic materials may not be suitable for demanding applications such as aerospace, the economics of producing simple metal components without critical loads on an affordable FDM printer can outweigh the impossibility of applying them in some areas.
Metal prototype parts and finished parts that will not be subjected to extreme stress are ideal uses for this technology.
Bound Metal Deposition (BMD)
Desktop Metal's Studio System 3D printer used bonded metal bars that were extruded layer by layer to form a metal part (Source: Desktop Metal)Similar to FDM, Metal mesh deposition method (BMD) or bonded powder extrusion (BPE) is a 3D printing process based on extrusion. This method uses bonded metal rods or bonded powdered metal filaments, which consist of a much higher percentage of metal powder than the filaments used in FDM. As with FDM, post-treatment to remove the binder and heat treatment in a final sintering oven are required.
There are only a few 3D printers using this method such as Desktop Metal, Markforged and more recently 3DGence, but more companies are entering this market, so stay tuned. These printers are valued as a convenient solution for office 3D metal printing, they are more expensive than most FDM printers, but cheaper than the powder-based metal 3D printing technologies described below.
These printers use their own proprietary filament. Desktop Metal and Markforged offer four types of steel.
Ideal niches for this technology are metal prototype parts, where it is necessary to test the functionality of a part before mass production using traditional methods. Popular applications are molds, punching dies, nozzles, impellers, fasteners and heat exchangers.
For example, Shukla Medical uses Markforged's Metal X printer to print steel prototypes of its orthopedic implant removal instruments.
Laser powder sintering.
Laser powder sintering technology uses one or more lasers to melt powdered metal layer by layer into a desired shape. (Source: GE Additive) metal printing. This technology is used by 80% of all metal 3D printers on the market.This method uses powerful lasers to selectively sinter metal powder layer by layer.
LPBF 3D printers are available in a wide range of sizes, prices and laser powers. These and other characteristics affect the properties of the finished part, print speed and other parameters of the finished products.
Steel and steel alloys are the most popular material for LPBF equipment and, unlike FDM and BMD, metal powders are commercially available as they are most commonly used in traditional production methods.
LPBF is a technology that maximizes the quality of a 3D printed part. Applications include aerospace components such as monolithic thrust chambers, rocket engine components and heat exchangers, molds, tools and other applications, as well as high wear parts and surgical instruments.
Binder Jetting
Binder Jetting 3D printing technology uses powdered metal and a binder to form metal parts (Sorrce: ExOne) binder, and not with a laser. During post-processing, the binder is removed.Binder application stands out for its high printing speed compared to other 3D printing methods or traditional manufacturing, and metal parts made with this technology have material properties equivalent to those made by metal injection molding.
The number of manufacturers producing metal-bonded inkjet 3D printers is much smaller than that of LPBF machines. Leading manufacturers include ExOne, Desktop Metal, Digital Metal, GE Additive and HP.
Binder blasting is ideal for medium to high volume production of metal tools and spare parts.
In fact, HP claims that its Metal Jet 3D printer was designed specifically for mass production of 316L stainless steel products. HP has partnered with Parmatech to produce metal parts for the medical industry. Pennsylvania-based ExOne uses this technology to manufacture hard metal cutting tools and tool steels.
Electron Beam Melting (EBM)
(Source: GE Additive)Electron Beam Melting (EBM) is another powder cladding technology. It works in a similar way to selective laser melting (SLM), but instead of using a laser as the energy source, it uses a much more powerful beam of charged particles.
The recoater moves the powder onto the printing plate and an electron beam selectively melts each layer of powder. After each layer is printed, the plate is lowered and another one is applied on top of the previous layer.
EBM can be much faster than SLM, but SLM produces smoother and more accurate pieces. The electron beam is wider than the laser beam, so EBM cannot produce the same precise parts as SLM. Another difference is that the manufacturing process takes place in a vacuum chamber, which reduces the amount of impurities in the material that can lead to defects. That is why EBM is often chosen for printing components for the aerospace, automotive, defense, petrochemical and medical implant industries.
Titanium is the most popular metal for most EBM applications, however steel can be used.
Cold Spray
(Source: Impact Innovations)Cold spray 3D printing is done by injecting metal powders through a jet nozzle into a supersonic stream of pressurized gases such as air, nitrogen, or helium. The process is called "cold" because the metal particles do not melt, but hit the metal substrate and adhere to its surface during the so-called plastic deformation.
Cold spray printed products are not prone to porosity, thermal cracking and other defects associated with melt-based technologies. This method has several advantages over other production methods. The technology is used in the military and aerospace industries around the world. For example, the US Army uses cold spray to repair the mounts of a worn Bradley 25mm steel turret gun.
In the automotive industry, cold spray steel is used for crash repairs because the high strength steel substrates in cars can be susceptible to thermal repair methods such as welding.
Direct Energy Deposition (DED) and Wire Arc Additive Manufacturing (WAAM)
WAAM Steel Parts from MX3D (Source: MX3D) Direct Energy Deposition (DED) uses welding powder or wire that enters through a nozzle and is fed into the power source to melt the metal. A melt region is created and applied to the substrate. DED is a new process, reminiscent of an old building technology known as "cladding", in which a coating is applied to a substrate, often for thermal insulation or weather resistance. DED is useful for fabricating large objects as a whole, as well as complex geometries that require extensive machining. DED can get such parts much closer to finished than traditional CNC machining.
Because DED uses a coating process, it can be used to add complex geometries to existing steel parts, thus combining complexity with cost reduction. For example, the French company AddUp advertises a rocket nozzle that uses a preformed large 304 stainless steel hopper cone printed with an isogrid structure, usually made from a larger piece by traditional methods.
A technology related to DED is wire-arc additive manufacturing (WAAM). Instead of powder, WAAM uses a metal wire that is melted by an electric arc. The process is controlled by robotic arms. WAAM is also capable of producing large-sized metal parts, as demonstrated by the Dutch company MX3D and its nine thousand-pound 41-foot stainless steel bridge in Amsterdam, as well as an oil and gas equipment repair part, proving that parts can be made in the field.
Micro 3D printing
Micro parts printed from steel (Source: 3D MicroPrint) Micro scale additive manufacturing, or micro 3D printing, can produce products with a resolution of a few microns (or less).