Best 3d print stock
Top 3D Printing Stocks for Q4 2022
Table of Contents
Table of Contents
-
Best Value 3D Printing Stocks
-
Fastest Growing 3D Printing Stocks
-
3D Printing Stocks With the Best Performance
SSYS is top for value and performance and NNDM is top for growth
By
Noah Bolton
Full Bio
Noah has about a year of freelance writing experience. He's worked on his investing website dealing with topics such as the stock market and financial advice for beginners.
Learn about our editorial policies
Updated October 06, 2022
The 3D printing industry is made up of companies that provide products and services capable of manufacturing a range of products. 3D printing, also known as additive manufacturing, creates physical objects from digital designs. The printing process works by laying down thin layers of material in the form of liquid or powdered plastic, metal, or cement, and then fusing the layers together. Though still too slow for mass production, it is a revolutionary technology that has the potential to disrupt the manufacturing logistics and inventory management industries. The 3D printing industry is comprised of only a handful of companies, including players such as Proto Labs Inc., Faro Technologies Inc., and Desktop Metal Inc.
The industry is so young that it has no meaningful benchmark index. But the performance of these stocks can be compared to the broader market as represented by the Russell 1000 Index. These stocks have not performed well. Stratasys Ltd. (SSYS), the best performing 3D printing stock, has dramatically underperformed the Russell 1000, which has provided a total return of -12.5% over the past 12 months. This market performance number and all statistics in the tables below are as of Sept. 20, 2022.
Here are the top three 3D printing stocks with the best value, fastest sales growth, and the best performance.
These are the 3D printing stocks with the lowest 12-month trailing price-to-sales (P/S) ratio. For companies in early stages of development or industries suffering from major shocks, this metric can be substituted as a rough measure of a business's value. A business with higher sales could eventually produce more profit when it achieves (or returns to) profitability. The price-to-sales ratio shows how much you're paying for the stock for each dollar of sales generated.
Best Value 3D Printing Stocks | |||
---|---|---|---|
Price ($) | Market Cap ($B) | 12-Month Trailing P/S Ratio | |
Stratasys Ltd. (SSYS) | 15.49 | 1.0 | 1.6 |
3D Systems Corp. (DDD) | 9.00 | 1.2 | 2.0 |
Proto Labs Inc. (PRLB) | 37.49 | 1.0 | 2.1 |
Source: YCharts
- Stratasys Ltd.: Stratasys offers 3D printing solutions, such as 3D printers, polymer materials, a software ecosystem, and related parts.
It serves a variety of industries, including aerospace, automotive, consumer products, and healthcare. On Sept. 13, Stratasys completed the merger of its MakerBot subsidiary with Ultimaker, which offers platforms used to make 3-D printers. Ultimaker is backed by NPM Capital. The merged company will keep the Ultimaker name and focus on providing solutions, hardware, software and materials to the industry. NPM Capital will have majority ownership of the new company at 53.5%, and Stratasys will own 46.5%.
- 3D Systems Corp.: 3D Systems provides 3D printing solutions. The company offers a range of hardware, software, and materials designed for additive manufacturing. Its products and services are used in a variety of industries and sectors, including aerospace, automotive, semiconductor, healthcare, and more.
- Proto Labs Inc.: Proto Labs is an e-commerce-based company that provides digital manufacturing services. It offers 3D printing, injection molding, CNC machining, and sheet metal fabrication.
On Aug. 5, Proto Labs announced financial results for Q2 2022, the three-month period ending on June 30, 2022. Net income fell more than 80% to $2.6 million from the prior-year quarter while revenue rose 3.1%.
These are the 3D printing stocks with the highest YOY sales growth for the most recent quarter. Rising sales can help investors identify companies that are able to grow revenue organically or through other means and find growing companies that have not yet reached profitability. In addition, accounting factors that may not reflect the overall strength of the business can significantly influence earnings per share. However, sales growth can also be potentially misleading about the strength of a business, because growing sales on money-losing businesses can be harmful if the company has no plan to reach profitability.
Fastest Growing 3D Printing Stocks | |||
---|---|---|---|
Price ($) | Market Cap ($B) | Revenue Growth (%) | |
Nano Dimension Ltd.![]() | 2.45 | 0.6 | 1,270 |
Desktop Metal Inc. (DM) | 3.07 | 1.0 | 203.9 |
Stratasys Ltd. (SSYS) | 15.49 | 1.0 | 13.3 |
Source: YCharts
- Nano Dimension Ltd.: Nano Dimension is an Israel-based 3D printing company focused on developing equipment and software for 3D-printed electronics. It develops printers for multilayer printed circuit boards and nanotechnology-based inks. The company serves a range of industries, including consumer electronics, healthcare, aerospace, and automotive. On Sept. 1, Nano Dimension released Q2 2022 results. The company's net loss widened sharply to $40.0 million from a loss of $13.6 million in the same quarter a year earlier even as revenue soared more than 13-fold. The larger second-quarter loss was fueled partly by $10.9 million in non-cash adjustments for depreciation and amortization expenses, and share-based payments.
- Desktop Metal Inc.: Desktop Metal manufactures 3D printers and related equipment used to build complex parts from metal. It also offers 3D printing software. The company serves a range of industries, including automotive, consumer products, education, and heavy industry. On Aug. 08, the company reported Q2 2022 results. Desktop Metals' net loss increase nearly seven-fold to $297.3 million compared to the same quarter a year earlier even as revenue tripled.
- Stratasys Ltd.: See above for company description.
These are the 3D printing stocks that had the smallest declines in total return over the past 12 months out of the companies we looked at.
3D Printing Stocks With the Best Performance | |||
---|---|---|---|
Price ($) | Market Cap ($B) | 12-Month Trailing Total Return (%) | |
Stratasys Ltd.![]() | 15.49 | 1.0 | -34.5 |
Proto Labs Inc. (PRLB) | 37.49 | 1.0 | -50.6 |
Materialise NV (MTLS) | 10.95 | 0.6 | -53.9 |
Russell 1000 | N/A | N/A | -12.5 |
Source: YCharts
- Stratasys Ltd.: See above for company description.
- Proto Labs Inc.: See above for company description.
- Materialise NV: Materialise is a Belgium-based provider of additive manufacturing software and 3D printing services. It serves a range of industries, including healthcare, aerospace, and automotive. On Sept. 7, Materialise completed its acquisition of Identity3D, which makes products that encrypt, distribute, and track digital parts as they move through supply-chains. The value of the deal was not specified in the announcement.
The comments, opinions, and analyses expressed herein are for informational purposes only and should not be considered individual investment advice or recommendations to invest in any security or to adopt any investment strategy. Though we believe the information provided herein is reliable, we do not warrant its accuracy or completeness. The views and strategies described in our content may not be suitable for all investors. Because market and economic conditions are subject to rapid change, all comments, opinions, and analyses contained within our content are rendered as of the date of the posting and may change without notice. The material is not intended as a complete analysis of every material fact regarding any country, region, market, industry, investment, or strategy.
Article Sources
Investopedia requires writers to use primary sources to support their work. These include white papers, government data, original reporting, and interviews with industry experts. We also reference original research from other reputable publishers where appropriate. You can learn more about the standards we follow in producing accurate, unbiased content in our editorial policy.
YCharts. "Financial Data.
"
Stratasys Ltd. "Stratasys Completes Merger of MakerBot with Ultimaker."
Proto Labs Inc. "Proto Labs Q2 2022 Earnings Release."
Nano Dimension Ltd. "Earnings Press Release for Q2 2022."
Desktop Metals Inc. " Desktop Metals Second Quarter 2022 Earnings."
Materialise NV. "Materialise Acquires Indenity3D."
5 3D Printing Stocks to Consider in 2022
An in-depth look at the leading 3D printing stocks in the U.S stock market this year. Here’s what you need to know.
By Nicholas Rossolillo – Updated Jul 11, 2022 at 2:42PM
Back in the early 2010s, stocks were booming for 3D printing -- also known as additive manufacturing, a computer-controlled process in which three-dimensional objects are made. But the boom was followed by a bust as many pure-play 3D printing companies didn't immediately deliver on lofty expectations.
Rumors of the manufacturing technology's demise are clearly premature. These days, 3D printing is a high-growth niche that is steadily reshaping the manufacturing and industrial sectors. Some estimates point to a doubling in annual revenue from additive manufacturing between 2022 and 2026. Even growth investor Cathie Wood has launched a fund focused on manufacturing tech, The 3D Printing ETF (NYSEMKT:PRNT), via her company ARK Invest.
Here's what you need to know about 3D printing and additive manufacturing stocks for 2022:
Image source: Getty Images.
Investing in 3D printing stocks
The manufacturing of products in all corners of the economy is being revolutionized by 3D printing, from healthcare equipment to metal fabrication to housing construction. It's invading so many sectors that tech giants such as Microsoft (NASDAQ:MSFT), Autodesk (NASDAQ:ADSK), and HP (NYSE:HPQ) have launched products aimed at 3D printing and additive manufacturing. Other engineering and software outfits such as Dassault Systemes (OTC:DASTY), ANSYS (NASDAQ:ANSS), and Trimble (NASDAQ:TRMB) have also gotten involved in 3D printing technology.
Here are five key players to consider for 2022 that are a more focused bet on 3D printing:
Company | Market Cap | Description |
---|---|---|
Desktop Metal (NYSE:DM) | $1.3 billion | Recent IPO that focuses on metal fabrication technology. |
Stratasys (NASDAQ:SSYS) | $1.5 billion | One of the original 3D printing pioneers, with a wide array of printers and supporting design software. |
Xometry (NASDAQ:XMTR) | $1.9 billion | A manufacturing marketplace, including access to on-demand 3D printing services.![]() |
3D Systems (NYSE:DDD) | $1.9 billion | Another original 3D printing pioneer and the largest pure-play stock on 3D printing technology. |
PTC (NASDAQ:PTC) | $11.7 billion | A manufacturing technology provider with a suite of software and related services for industrial businesses. |
1. Desktop Metal
This company is a recent entry into the 3D printing space after going public via a SPAC at the end of 2020. The stock has been a terrible market underperformer since then, losing three-quarters of its value as of spring 2022. However, Desktop Metal could still be a promising investment for the long term.
As its name implies, Desktop Metal develops 3D printing hardware and accompanying design software for metal and carbon fiber parts. The company's smaller systems can handle prototyping and one-off parts, and larger printers are production grade-designed for manufacturing facilities. Desktop Metal serves companies operating in automotive, consumer goods, and heavy industrial equipment businesses.
Despite a tenuous start as a public company, Desktop Metal was actually increasing revenue at a torrid triple-digit pace in 2021. Gross profit margins are thin, and the company generated a steep net loss, but that should improve over time as the business scales its operation. Desktop Metal also has several hundred million dollars in cash and investments to fund its expansion. It used some of these funds to acquire additive manufacturing peer ExOne at the end of 2021.
2. Stratasys
Stratasys was part of the early 2010s 3D printing stock boom and bust, but its business has endured. Sales took a dip early in the COVID-19 pandemic but are rebounding as the Israel-based company picks up new manufacturing contracts.
Stratasys serves a diverse set of customers, including aerospace and automotive parts manufacturers, medical and dental companies, and makers of basic consumer products. In addition to a wide array of 3D printer models, Stratasys develops software to help users accelerate the time between design and final printing.
It isn't the highest-growth name on this list, but Stratasys is profitable (on a free cash flow basis) and has more than $500 million in cash and investments on its balance sheet, as well as no debt. Management thinks its payoff from years of research and development into additive manufacturing will accelerate in 2022.
3. Xometry
This is another newcomer to public markets. Xometry completed its initial public offering (IPO) over the summer of 2021, raising almost $350 million in cash in the process. As is often the case with new IPOs, the stock has underperformed since then. It has lost over half of its value from the time it started trading on public markets, but the business itself is rapidly growing.
Xometry is a marketplace for on-demand manufacturing of prototyping and mass production. It has a network of more than 5,000 suppliers that companies can call on to meet their fabrication needs. Among the suppliers on the Xometry platform are 3D printing companies, injection molding, and automated machining. The company reported having more than 28,000 active buyers utilizing its platform at the end of 2021.
Although it isn't profitable yet, Xometry's unique approach to the 3D printing and additive manufacturing industry is growing fast. Like other names on this list, it has a sizable war chest of cash and short-term investments that it can spend on research and marketing as it tries to attract more suppliers and buyers to its marketplace.
4. 3D Systems
3D Systems was another early player in the 3D printing industry, and while it suffered through the boom-and-bust period of the early 2010s, its business has held steady for much of the past decade. After a brief dip during the early days of the pandemic, 3D Systems is back in growth mode.
The company develops printers and design software for all sorts of materials and industries (medical device makers, dental labs, semiconductor designers, aerospace, and automotive manufacturers). It claims leadership among independent 3D printing companies (as measured by sales). As the 3D printing industry expands in the coming years, 3D Systems thinks it will be able to attract lots of new business with its extensive experience and global reach.
As an established tech outfit in the manufacturing sector, 3D Systems offers investors the prospect of more stable growth, along with profitability. It also has a large net cash position from which it can consolidate its lead in 3D printers and software technology.
5. PTC
By far the largest company on this list, PTC is a longtime technology partner of manufacturing and industrial enterprises. Fast approaching $2 billion in annualized sales and highly profitable, PTC has all the tools needed to digitally transform industrial businesses.
Besides 3D printing computer-aided design software (ANSYS is a peer and software partner that also operates in this space), PTC specializes in augmented reality, industrial IoT (Internet of Things), and product life-cycle management software. Most of its revenue is subscription-based (including its Creo software that enables 3D printing), making for a stable and steadily growing business model that generates ample cash flow. PTC puts spare cash to work developing new products for its partners and makes bolt-on acquisitions of other software companies that enhance its overall portfolio.
As a larger company, PTC won't be the fastest-growing stock in the additive manufacturing and 3D printing space. However, the company has established itself as a leader in industrial technology and should be a primary beneficiary as the production of manufactured goods gets more efficient.
The future of 3D printing
Manufacturing technology is making inroads throughout the global economy by reducing the cost of production and localizing and speeding up the time it takes to deliver customer orders. This is far from mere hype. Nevertheless, as is the case with all technology investments, progress won't go straight up. Expect twists and turns in these stocks as they develop new methods to design and make products.
If you decide to invest, do so in a measured way. Maintain a diversified portfolio, be wary of stocks benefiting from investor over-optimism, and always leave spare cash to invest more when there are inevitable dips. Given enough time -- years and decades -- investing in 3D printing could eventually provide a big payoff.
Related communication stocks topics
Investing in 5G Stocks
As the 5G technology rollout continues, these companies look like winners.
Investing in Top Telecommunications Stocks
Our world is increasingly interconnected, and these companies make it happen.
Investing in Communication Stocks
Communications has a broad definition. These companies are the leaders in the space.
Investing in Top Consumer Discretionary Stocks
When people have a little extra cash, they indulge in offerings from these companies.
Nicholas Rossolillo has positions in Autodesk and PTC. The Motley Fool has positions in and recommends Autodesk, HP, and Microsoft. The Motley Fool recommends 3D Systems, ANSYS, Dassault Systemes, PTC, and Trimble Inc. The Motley Fool has a disclosure policy.
Motley Fool Investing Philosophy
- #1 Buy 25+ Companies
- #2 Hold Stocks for 5+ Years
- #3 Add New Savings Regularly
- #4 Hold Through Market Volatility
- #5 Let Winners Run
- #6 Target Long-Term Returns
Why do we invest this way? Learn More
Related Articles
3 Dividend-Paying Tech Stocks to Buy in November
3 Robinhood Stocks to Buy Right Now
Better Buy: Microsoft vs. Alphabet
2 Growth Stocks to Buy and Hold Forever
PTC (PTC) Q4 2022 Earnings Call Transcript
Why Is Everyone Talking About Microsoft?
3 Things About Microsoft That Smart Investors Know
Premium Investing Services
Invest better with The Motley Fool. Get stock recommendations, portfolio guidance, and more from The Motley Fool's premium services.
View Premium Services
Selection of materials for 3D printing. Part 1.
Hello fellow printers!
In touch 3DMindex.
I am a frequent user of the portal 3DToday.ru , and every time I see another article called “another technological plastic” I get a slight shiver. In the period from 2019 to 2020, so many materials were published that it will be very difficult for even an experienced user to figure out why and for what this or that material is needed.
In my article tetralogy, I decided to make a detailed review of the materials presented by various manufacturers, excluding those that do not deserve special attention. I will make my own rating, according to which I will recommend this or that material from key manufacturers for purchase, and I will tell you about the experience of using them on various 3D printers. The following material manufacturers were chosen by me: Filamentarno, REC, PrintProduct, BestFilament and FD Plast (as the most popular manufacturer among garage craftsmen)
Equipment I work on : Hercules Strong . In my work, I came across many printers, such printers as Ultimaker S2 , Up Mini , Picaso Designer ( different versions ), Magnum Create , Zenith , Raise N2 , VolgoBot version A4 PRO, and others.
I searched for information bit by bit from different sites, and seasoned them with a little touch of subjective opinion, and also tried to combine everything in my (several) articles.
Let's start:
In this article I will talk about the most famous materials from which everyone begins to get acquainted with the 3D industry. I’ll tell you what to expect and what to fear when working with this or that material, indirectly go through the print parameters, talk about the technical characteristics, application, touch on the economic component when working with a certain material, list some features and sum up my “TOP manufacturers” for production materials and printers( in the high price category ) when working with these materials.
#1 ABS
ABS High impact engineering thermoplastic resin. In 3D printing is the most one of the most popular material.
Print options:
- Extrusion temperature - 210-245°C
- Table temperature - 90-120°C
- Interlayer cohesion - medium
- Table adhesion - medium
This is one of those materials that must be printed in a closed chamber. Fortunately, all modern manufacturers equip printers with a closed case (with the exception of Magnum 'a). In this regard, the printing becomes less toxic, and also (which is no less important) there is a better sintering of the layers (cohesion). For the better, I can note the company Volgobot , they developed an active thermostatic chamber in the PRO version on their printer. In other words, in addition to a heated table (up to 150°C), they have a heating element with a convection fan, thanks to which a single temperature is maintained throughout the entire print volume. According to the manufacturer, the temperature difference in the chamber varies by ± 2°C at 100°C. With this thermal chamber, new frontiers can be opened for use ABS plastic. For example, you can put a model with 100% infill on the entire print area, and their print area is about 297/210/200mm. How does Picaso behave when printed? So in terms of print quality ABS ’om ( as well as other materials ), they are objectively the first in Russia in this parameter, but the issue of stable operation is acute for them. I know that they are very worried about this, and this is their key merit, but my friends and I who work with this printer have malfunctions, in general, the issue of malfunctions can be attributed to any technique, but once it happened like this that Picaso did not start working out of the box yet ( this happens sometimes in case of careless transportation, and applies to all manufacturers of 3D printers ), but fast ( like-nowhere ) and qualified ( especially ) technical support helped to solve this and not only problems, thanks to them for that.
As for other manufacturers, some print “good”, and some “satisfactory”, the question is more about how much manufacturers sell their goods for, and which goods are worth their money and which are not.
Specifications:
- Melting point - 175-210°C
- Softening point - 100°C
- Operating temperature -40+80°C
- Hardness (Rockwell) - R105-R110
- Elongation at break - 6%
- Bending strength - 41 MPa
- Tensile strength - 22 MPa
- Tensile modulus - 1.6 GPa
- Flexural modulus - 2.1 GPa
- Density - 1.1 g/cm³
- Shrinkage in the manufacture of products - up to 0.8%
- Moisture absorption - 0.45%
Application:
This material is found everywhere in our lives. It is widely used in industry, it is used to make large car parts (dashboards, radiator grilles), cases of large household appliances, sports equipment, plumbing products. In 3D printing, it was the first polymer used. Unfortunately, in this area it is not as easy to handle as we would like. Due to the specifics of the technology, it is difficult to make large objects from it due to shrinkage, detachment and delamination of the model occur. A closed print chamber partially solves this problem, in order to almost completely get rid of it, it is necessary to have a thermostatic chamber.
Pros:
- Good combination of strength and elasticity makes it suitable for mechanical applications.
- A wide range of temperatures used allows the use of products from it for technical purposes.
- Ease of machining, combined with chemical smoothing of the surface with inexpensive solvents such as acetone, allows you to make decorative items or cases with a high surface quality.
Cons:
- Does not tolerate UV radiation well, turns yellow in sunlight, which limits the use of unpainted surfaces outdoors
- Does not like drafts when printing, which limits the use of cheap printers with an open case.
- Due to relatively high shrinkage it is prone to delamination (separation), requires a heated bed, without it there are problems with the first layer sticking to the bed.
- During the printing process, an unpleasant odor may form, it is better to print in a ventilated room, or to equip the printer with a special exhaust ventilation system, with output outside the apartment.
Economic component:
Here is a table with manufacturers, with current prices for January 21. Since manufacturers sell coils in different weights, I decided to find the cost of the material per gram of the product by the ratio of price to weight. The result is presented in column “ ₽/M ”. The column “ Quality ” is completely subjective, because I gave points in it absolutely arbitrarily, based on the experience of working with material from one or another representative, but in general, the quality of the current mastodons of production is ± on the same level, and the problems that I have with printing can be associated with the storage conditions of materials. Column “ Recommendation ” - is the ratio of “ Quality ” to “ ₽/M ”, it is needed in order to reduce these values to a common denominator, the higher the score in it, the more I recommend the material from this manufacturer.
What is the result?
1st place - FD Plast (Recommended for test printing)
2nd place - Filamentarno (I highly recommend)
3rd place - PrintProduct
4th place - Bestfilament
5th place - REC
To my surprise, FD Plast has the first place in this championship, and REC is outsiders. What are the reasons? Of course in price. About 5 years ago, REC was the top quality with corresponding prices, but over the past couple of years, other manufacturers have pulled up in this parameter, but the prices are kept lower than REC, hence the connection. Maybe after this article, REC will stop slightly jacking up prices for their material, and will be more accessible to ordinary buyers.
As for FD Plast, in my opinion, their material is suitable for test or home printing, but if you have a serious large-scale project and tight deadlines, then it is better to contact trusted manufacturers. It will turn out more expensive, but spend less time and nerves in case the seal fails.
It is also worth noting that there are many brands and composites based on ABS, and therefore the prices for the material can vary so much, unfortunately, the manufacturer does not offer a technological map for the material, which is why it is impossible to fully find the answer to Question: Why is it so expensive?
If you order 3D printing from various companies, then on average in the provinces the price for printing with this plastic is from 10 to 30 rubles per gram, if you order from top3Dshop, then the price for ABS is 45 rubles per gram.
In general, using this plastic is quite a profitable business if you are going to fulfill orders for 3D printing.
Top ABS 3D Printer:
1 Place - Picaso
2 Place - Hercules (slightly not up to Picaso in quality, I think the price tag for equipment is too high, I took it myself solely from the recommendations of comrades and a large (high) print area. )
3rd place - Volgobot (the quality is comparable to Hercules strong, but the price tag is lower, I put it in 3rd place due to the fact that the company is not as large as direct competitors, although it has its own development vector, and their thermal chamber works wonders with ABS, however, this is not their only worthy development, they have a configurator with a large list of options in which you can assemble a printer for your tasks, however, you should contact the manufacturer for all the details. but the guys try and keep in touch with all their customers.)
All other printers have approximately the same level of printing with ABS, fortunately for 5-8 years of existence of companies, all ± have learned to work with this material.
Worth mentioning: Ultimaker / Raise Pro 2 I am not satisfied, and the price tag is also not small)
#2 PLA
PLA-plastic (polylactide, PLA) is a biodegradable thermoplastic aliphatic polyester, the structural unit of which is lactic acid. PLA plastic is made from corn, sugar cane, potato or corn starch, and cellulose. It is one of the most popular materials for 3D printing. Due to its natural raw materials in the composition of the polymer, it can be used for various purposes without a threat to humans.
Print options:
- Extrusion temperature - 190-230°C
- Table temperature - 20-60°C
- Interlayer cohesion - good
- Table adhesion - good
- It is essential to dry the filament spool before use for more stable printing.
Specifications:
- Melting point - 175-180°C
- Softening point - 50°C
- Product operating temperature -20+40°C
- Hardness (Rockwell) - R70-R90
- Elongation at break - 3.8%
- Bending strength - 55.3 MPa
- Tensile strength - 57.8 MPa
- Tensile modulus - 3.3 GPa
- Flexural modulus - 2.3 GPa
- Density - 1.
23-1.25 g/cm³
- Manufacturing shrinkage - no
- Moisture absorption - 0.2-0.4%
Application:
PLA plastic shows itself excellently in mock-up workshops and in creating master models that are not designed to bear long-term mechanical loads. With it, models with careful detail are obtained, and are also used when working with children.
Pros:
- Does not shrink during printing, which allows you to get an exact match of the dimensions of the printed product to the simulated one.
- Does not require a heated bed and is not afraid of drafts when printing, which means it can be used for printing on the cheapest Chinese printer with an open case.
- Non-toxic. During printing, it smells pleasant and slightly, which allows you to print it in the apartment without using a special hood.
- Hard, durable and slippery, wide range of applications.
- Produced from natural ingredients, can be used in food contact.
- Biodegradable, this plastic does not harm the environment when disposed of.
Cons:
- Exposure to air and ultraviolet light, like any natural material, becomes more brittle over time, so it is not recommended for long-term use at high physical exertion or use without a protective coating in the open air.
- Low softening temperature (50°C) - in the inside of a car left in the sun on a hot day, easily softens and loses its shape.
- Narrow temperature range (-20 to +40°C).
- The high hardness of the plastic makes it difficult to machine.
- Due to the high content of residual monomers, plastics from some manufacturers are prone to plugging in all-metal hot ends.
Economic component:
PLA prices are slightly higher, and therefore our TOP has shifted slightly:
1st place - Filamentarno (Recommended)
2 Place - FD Plast (Worth a try for a test print)
3rd place - PrintProduct
4th place - REC
5th place - BestFilament
PLA is a material that absorbs a lot of moisture, due to which its characteristics drop significantly, and the already fragile material becomes almost glassy. FD Plast once again takes its price, bypassing its competitors by 1.5, or even almost 2 times, but I suffered a lot with it, it draws moisture from the air, probably as much as silica gel from shoes.
If you order 3D printing from various companies, then on average in the provinces the price for printing with this plastic is from 10 to 20 rubles per gram, if you order from top3Dshop, then the price for PLA is 35 rubles per gram.
Based on the issue of profit, the use of this plastic brings less money per 1 gram of material, but due to its features, there are much fewer problems in printing with this plastic than with the same ABS.
Top 3D printers for PLA:
1st place - Picaso (In the past they had problems with printing these materials, the extruder often clogged, now as far as I know this problem has been fixed)
2nd place - All remaining manufacturers. (As of January 21, all manufacturers have learned to produce approximately the same print quality for PLA, in principle, this is one of the easiest materials to work with, and I don’t see much point in crucifying, put more airflow and print on health)
Worthy of mention: Raise PRO 2 (this is perhaps one of the worst printers for PLA printing, I tried to print on it in one CMIT, and from the stuffy room the extruders clogged literally on every print, in general, it also depends on the material manufacturer, but one and the same coil on different printers showed itself in completely different ways, and therefore I highly do not recommend printing with PLA plastic on this printer)
#3 PET-G
PETG (polyethylene tereflatate glycol, PETG) highly impact resistant plastic, due to glycol modification it does not crystallize, making deep drawing thermoforming more possible. At the moment, plastic is actively gaining popularity, all because it combines the positive qualities of many other polymers.
For some manufacturers you will not find such material as PET in the catalog, this is due to the fact that marketers probably decided to rename this material, and therefore Filamentarno has Prototyper as an analogue of PET, and RELAX for REC.
Print options:
- Extrusion temperature - 215-245°C
- Table temperature - 20-80°C
- Interlayer cohesion - very high
- Table Adhesion - Medium
Specifications:
- Extrusion temperature - 215-245°C
- Table temperature - 20-80°C
- Interlayer cohesion - very high
- Table Adhesion - Medium
- Specifications
- Melting point - 222-225°C
- Softening point - 80°C
- Operating temperature -40+70°C
- Hardness (Rockwell) - R106
- Elongation at break - 50%
- Bending strength - 76.
1 MPa
- Tensile strength - 36.5 MPa
- Tensile modulus - 2.6 GPa
- Flexural modulus - 1.12 GPa
- Density - 1.3 g/cm³
- Manufacturing shrinkage - no
- Moisture absorption - 0.12%
Application:
In everyday life PET is used to make plastic bottles, due to its chemical neutrality it is used in the food industry. By itself, PET-G is similar to PET material. In 3D printing, it has proven itself as a versatile material that can be used both in technical parts bearing low loads and in prototyping.
Pros:
- Odorless Printing - Allows you to print at home without the need for an optional exhaust fan.
- No shrinkage for high dimensional accuracy.
- Very strong sintering between layers - can print thin-walled products with high strength.
- UV resistant - printed designs can be used outdoors.
- Wide operating temperature range.
- Printing does not require a closed chamber.
- Good slip and impact resistance - can print gears, bushings and other machine parts.
- Non-toxic, can be printed on articles intended for contact with food.
Cons:
- High fluidity requires careful adjustment of the retracts.
- High printing temperature quickly disables the fluoroplastic insert in the hot end and makes you think about switching to all-metal thermal barriers.
- Strength and softening point lower than ABS.
- A fairly versatile material, good print behavior but not outstanding performance.
Economic component:
1st place - FD Plast
2nd place - Filamentarno
3rd place - BestFilament
4th place - PrintProduct
5th place - REC
Surprisingly, the PET-G rating is, in my opinion, the most honest. Due to the fact that PET is more stable in terms of storage and printing material, there was a large increase in points in the “Quality” column. REC is again an outsider, once again I repeat that this is due to the high cost of the material, and it hurts me to see this company at the end of the top.
If you order 3D printing from various companies, then on average in the provinces the price for printing with this plastic is from 15 to 35 rubles per gram, if you order from top3Dshop, then the price for PET-G is about 40 rubles per gram (I did not find the exact price ).
Based on the issue of profit, the use of this plastic brings less money per 1 gram of material, but due to its features, there are much fewer problems in using this plastic than with the same ABS.
Top 3D printers for PET-G:
NOT top by PLA)
#4 HIPS
HIPS (High Strength Polystyrene) is a fairly soft plastic designed to be used with ABS to support dual extruder 3D printing. This was facilitated by its following properties: the same extrusion temperature as ABS, low caking with ABS, the presence of a solvent (D-Limonene), which dissolves HIPS and does not dissolve ABS. Some manufacturers do not have this material in their catalog, in fact, I do not see its widespread use at the present time, and therefore it is not a pity.
Print options:
- Extrusion temperature - 210-245°C
- Table temperature - 90-120°C
- Interlayer cohesion - medium
- Table Adhesion - Medium
Do not start work without drying the coil!
Specifications:
- Extrusion Temperature - 210-245°C
- Table temperature - 90-120°C
- Interlayer cohesion - medium
- Table Adhesion - Medium
- Do not start work without drying the coil!
- Specifications:
- Melting point - 175-210°C
- Softening point - 97°C
- Operating temperature -40+70°C
- Hardness (Rockwell) - L79
- Elongation at break - 64%
- Bending strength - 37.6 MPa
- Tensile strength - 16.
4 MPa
- Tensile modulus - 0.93 GPa
- Flexural modulus - 1.35 GPa
- Density - 1.05 g/cm³
- Manufacturing shrinkage - 0.4%
- Moisture absorption - 1%
Pros:
- Less shrinkage than ABS, making it suitable for precision printing.
- Lighter density than PLA, allowing for prints where lightness is required.
- Softness of the surface, which guarantees ease of machining.
- A matte finish that gives a smooth effect to garments.
- Almost same softening point as ABS, making it suitable for outdoor use.
Cons:
- Like ABS, it requires a heated platform and is prone to delamination, although to a lesser extent.
- Lower bending strength than ABS and, as a result, more brittle products.
- Poor UV resistance, which limits the use of products in sunlight.
- All this makes it possible to use this plastic for the production of furniture decor and interior decorations.
Application: once this material appeared it was used to print supports on 2 extruder printers, the supports themselves were dissolved in limonene. To date, this is no longer so relevant, due to the appearance of such material as PVA, the material itself is completely unnecessary today. The material itself is quite stable, although it requires careful drying.
Economic component:
1st Place - FD Plast
2nd place - Bestfilament
3rd place - REC
As far as buying recommendations, it can be safely replaced with PVA, in general I consider HIPS already out of fashion, so I doubt that anyone spends it in large quantities.
Top 3D Printers for HIPS:
1 Place - Hercules / Volgobot
2nd place - Picaso (Picaso dropped to second place due to the fact that slippage occurs when printing with HIPS, it is quite possible that they got rid of this problem on new printers, but in 2019 it was like that)
№5 SBS
SBS (styrene butadiene styrene) is another relatively new player in the 3D printing plastics market. It is characterized by low toxicity and shrinkage, as well as high strength. Its main advantage is its transparency. Products printed with this plastic and treated with a solvent acquire the transparency of colored glass.
This material has different names for different manufacturers, for example, for BestFilament it is called WATSON, and for some manufacturers it is not presented at all.
Print options:
- Extrusion temperature - 220-240°C
- Table temperature - 70-90°C
- Interlayer cohesion - low
- Table Adhesion - Medium
Specifications:
- Melting point - 190-210°C
- Softening point - 76°C
- Operating temperature - -80+65°C
- Hardness (Rockwell) - R118
- Elongation at break - 250%
- Bending strength - 36 MPa
- Tensile strength - 34 MPa
- Tensile modulus - 1.35 GPa
- Flexural modulus - 1.
45 GPa
- Density - 1.01 g/cm³
- Shrinkage in the manufacture of products - 0.2
- Moisture absorption - 0.07%
Pros:
- Relatively low shrinkage, allowing printing in open frame printers.
- High adhesion to the table.
- Potential for food contact.
- Impact resistant.
- Beautiful colors for creating unique decor items.
- Transparency after processing, can be used in luminaires.
- Wide operating temperature range, frost resistance.
- Easy post-processing by both chemical and mechanical methods.
Cons:
- Poor intercoat cohesion, requires large orifice nozzles or 100% coverage.
- Relatively high print temperature, similar to PETG.
- Applications: Most often used in decorative elements and creating custom lamps.
Economic component:
1 Place - FD Plast
2nd place - Filamentarno
3rd place - BestFilament
Top 3D printers for SBS:
1st Place - Picaso
2nd place - VolgoBot
3rd place - Hercules
Conclusion:
As for the article: it turned out to be shorter than I planned, this category of materials did not include such materials as Flex (various modifications), Nylon and other At the time of the final editing of the article, I realized that not all printers are capable of printing with these materials, Flex’a needs special extruders capable of printing rubber-like materials, for a PC, the presence of a closed case does not mean success in work, and the material loves temperature very much. Therefore, if the article receives some response, I will talk about “engineering plastics”, composites created on their basis, and also talk about materials that are at the forefront of progress, so my dear reader, adequate criticism is welcome.
As for material manufacturers, a few words about each:
FD Plast : wins in public domain although I don't agree with it because I think their policy of dumping the market is wrong, but the company has many followers who prefer goods from the “cheap and cheerful” category.
Filamentarno: for me personally is the best manufacturer with an adequate price, not a small list of products, and with a constant quality that has never let me down.
Print Product: before switching to Filamentary, he mainly used the products of this company, in the past the company had a colossal list of products, but in the last year they decided to change the vector of development, and relied on materials whose quality can be sufficiently ensured .
REC : in the past, the clear favorite in terms of the quality of the materials provided, now the quality is at the same level, but the price tag bites.
Best filament it seems to me that the quality floats slightly from batch to batch, gaps form on Hercules when printing with ABS plastic.
types, applications and properties
3D printing enables fast and cost-effective prototyping and production of models for a wide range of applications. But choosing the right 3D printing technology is only one side of the coin. Ultimately, the ability to create models with the required mechanical properties, functional characteristics or appearance will depend on the materials.
This comprehensive guide provides information on the most popular plastic and metal 3D printing materials available, compares their properties and applications, and provides guidance on how to select the most appropriate material for your project.
Interactive Material
Need help choosing your 3D printing material? Our new interactive materials wizard will help you select the right material from our growing range of polymers, based on your intended application and the properties that matter most to you.
Get material recommendations
Dozens of plastic materials are available for 3D printing. Each of them has unique properties suitable for specific applications. To make it easier to find the best material for a particular model or product, let's first look at the main types of plastics and the various 3D printing processes.
There are two main types of plastics:
-
thermoplastics are the most common type of plastics. The main feature that distinguishes them from thermosetting plastics is their ability to withstand multiple melting and solidification cycles. Thermoplastics can be heated and shaped into desired shapes. This process is reversible because no chemical bond is formed. As a result, they can be recycled or melted down and reused. Thermoplastics can be compared to butter: it melts and hardens many times. With each melting cycle, the properties of thermoplastics change slightly.
-
thermoset plastics (also called thermosets) remain permanently solid after polymerization.
The polymers in thermosetting plastics are crosslinked during the polymerization process, which is induced by heat, light, or appropriate radiation. Thermoset plastics decompose when heated, rather than melt. In addition, they do not change their shape when cooled. It is not possible to recycle thermosetting plastics or restore the material to its original state. Thermosetting is like pie dough: once baked, the pie cannot be melted back into dough.
The three most common plastic 3D printing processes today are:
-
The Fused Deposition Modeling (FDM) 3D printer melts and extrudes thermoplastic filaments, which the printer's nozzle deposits layer by layer on the work area.
-
The Stereolithography (SLA) 3D Printer uses a laser to photopolymerize thermoset liquid polymers into a hardened plastic.
-
The Selective Laser Sintering (SLS) 3D Printer is equipped with a high power laser to sinter fine particles of thermoplastic powder.
How-to video
Can't find the 3D printing technology that best suits your needs? In this video tutorial, we compare Fused Deposition Modeling (FDM), Stereolithography (SLA), and Selective Laser Sintering (SLS) technologies in terms of the top factors to consider when purchasing.
Watch video
Fused deposition modeling (FDM), also known as Fused Filament Manufacturing (FFF), is the most common form of consumer grade 3D printing, fueled by the proliferation of hobbyist 3D printers.
This method is well suited for making basic experimental models, as well as for quickly and inexpensively prototyping simple products, such as parts that are usually machined.
Consumer grade FDM has the lowest resolution and accuracy of any other plastic 3D printing process, making it unsuitable for printing complex designs or models with intricate features. It is possible to improve the surface quality of models printed using this technology using chemical and mechanical polishing processes. FDM-based industrial 3D printers, which offer a wider range of engineering thermoplastics, can solve these problems, but are also much more expensive.
Each layer is formed with a thermoplastic thread. Sometimes, if the layers are not completely adjacent to each other, there may be voids between them. As a result, anisotropic models are obtained, which is important to consider when designing products that must withstand load and be resistant to tension.
FDM 3D printing materials are available in a variety of colors. There are also various experimental mixtures of thermoplastic threads designed to create models with a surface that mimics wood or metal.
The most common materials for 3D printing in FDM technology are ABS (acrylonitrile butadiene styrene), PLA (polylactic acid) and various mixtures of these polymers. More advanced FDM printers can also print on other materials with different properties, such as increased temperature and chemical resistance, impact resistance, and rigidity.
Material | Features | Material for supporting structures | |
---|---|---|---|
impact -resistant polystyrene | Material for the creation of soluble supporting structures, most frequently used with ABS . Kevlar, fiber optic) | Strong, tough and incredibly hard Only compatible with some expensive industrial 3D printers based on FDM technology | Functional prototypes Clamping fixtures, fixtures, tooling |
Invented in the 1980s, stereolithography is the world's first 3D printing technology and is still one of the most popular among professionals today.
Models printed with stereolithography printers have the highest resolution and accuracy, the sharpest detail and the smoothest surface of any other plastic 3D printing technology. Resin 3D printing is a great option for producing highly detailed prototypes that require tight tolerances and smooth surfaces such as molds, templates, and functional models. Models printed using SLA technology can be easily polished and/or painted after printing, resulting in highly detailed finished products.
Models printed on SLA 3D printers are generally isotropic: their strength is more or less constant and independent of orientation, since chemical bonds occur between each layer. This results in models with predictable mechanical characteristics that are critical for applications such as fasteners, fixtures, finished products, and functional prototypes.
Stereolithography supports a wide range of plastic 3D printing materials.
SLA 3D printing is versatile and provides a wide range of optical, mechanical and thermal properties that match those of standard, engineering and industrial thermoplastics.
Materials of Formlabs | Descriptions | Methods of use |
---|---|---|
Standard polymers | General resolution Glavo0980 | Initial prototypes Rapid iterations |
Tough Resin and Durable Resin | Materials that are tough, strong, functional and dynamic Able to withstand compression, tension, bending and impact without breaking Various materials with properties similar to ABS | Enclosures and Enclosures Clamps and Mounting Devices Connectors Wear Prototypes |
Rigid Resins | Highly filled, stiff and strong material that resists bending Resistant to temperature and chemicals Maintains dimension under load | Clamping and clamping fixtures, tooling Turbines and fan blades Fluid/air components Electrical enclosures and enclosures used in the automotive industry |
High Temp Resin | High temperature resistant High Precision | Hot Air, Gas, and Liquid Components Heat Resistant Fasteners, Enclosures, and Fixtures Molds and Inserts |
Flexible Resin and Elastic Resin | Flexibility of Rubber, TPU, or Silicone compression Withstand many successive cycles without wear | Consumer product prototypes Foldable structures for robotics Medical devices and anatomy models Props and models for special effects |
Medical and dental resins | A wide range of biocompatible resins for the manufacture of medical and dental products | Dental and medical products, including surgical templates, dentures and prosthetic limbs | 3 Jewelry resins | Lost wax and vulcanized rubber casting materials Easy to cast with intricate features and good shape retention Request a free sample
Selective laser sintering (SLS) 3D printing is a technology trusted by engineers and manufacturers across industries to create durable and functional models. The green powder supports the model during printing and eliminates the need for special support structures. As a result, SLS is ideal for complex geometries, including internal features, undercuts, thin walls, and negative draft features. Like stereolithography, SLS produces more isotropic models than FDM models. Models created with SLS technology have a slightly rough surface due to powder particles, but have almost no visible layer lines. SLS 3D printing materials are ideal for a range of functional applications, from consumer product design to manufacturing and healthcare applications. Compared to FDM and SLA technologies, SLS technology allows the use of a limited number of materials. However, the available materials have excellent mechanical properties. | Functional Prototypes Structural End-Use Products |
Sample
Experience Formlabs SLS print quality for yourself We will send a free print sample directly to your office.
Request a free sample
Different 3D printing materials and processes have their own advantages and disadvantages that make them suitable for different scenarios. The following table provides a brief overview of some of the main features and factors to consider.
Poor detail
Limited fit to design
High cost of industrial devices if precision and high performance materials are needed
Basic experimental models
Production of special end-use products using professional industrial devices and materials
Templates, molds and tooling
Dental products
Prototypes and molds for casting jewelry
Props and models
Small-scale production, production of limited trial runs, creation of products to order
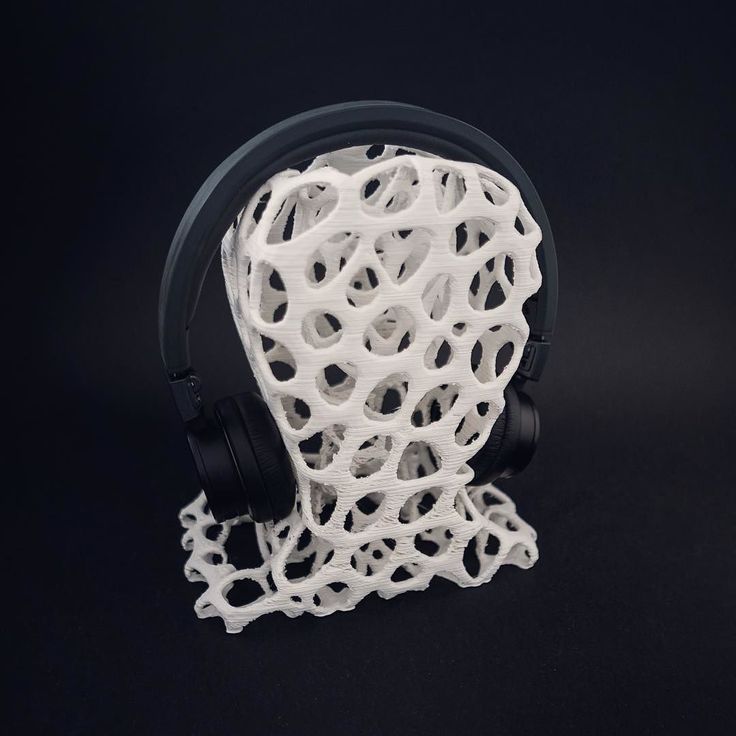
There are several 3D printing processes not only from plastics, but also from metals.
Metal FDM printers are similar in design to traditional FDM printers, but use extruded metal rods held in place by a resin binder. The finished models are in an intermediate state and then sintered in an oven to remove the binder.
SLM and DMLS printers are similar to SLS printers, but instead of polymer powders, they fuse metal powder particles layer by layer using a laser. SLM and DMLS-based 3D printers create strong, precise, and complex metal products, making the process ideal for the aerospace, automotive, and medical industries.
-
Titanium is a light metal with excellent mechanical properties. It is strong, hard and highly resistant to heat, oxidation and acids.
-
stainless steel has high strength, ductility and corrosion resistance.
-
aluminum is a lightweight, durable, strong metal with good thermal properties.
-
Tool Steel is a hard, scratch-resistant material that can be used to print end-use tools and other high-strength products.
- nickel alloys have high tensile, creep and tensile strength, as well as heat and corrosion resistance.
Compared to plastic 3D printing technologies, metal 3D printing is much more expensive and difficult, so it is beyond the reach of most companies.
As an alternative to casting workflows that produce metal models cheaper and faster than traditional methods and provide greater design freedom, SLA 3D printing is well suited.
Another alternative is galvanization of SLA printed models. It involves applying a layer of metal to plastic using electrolysis. This combines some of the best qualities of metal (strength, electrical conductivity, corrosion and abrasion resistance) with the special properties of the base (usually plastic) material.
Plastic 3D printing is well suited for creating templates that can be cast to produce metal models.
With so many materials and options available for 3D printing, making the right choice can be difficult.
We provide a 3-step process for selecting the right material for 3D printing.
Plastics used for 3D printing have different chemical, optical, mechanical and thermal characteristics that affect the properties of 3D printed models. As you move from the intended use case to the actual operating environment, the performance requirements increase accordingly.
Requirement | Description | Recommendations |
---|---|---|
Low Efficiency | Example: Prototype mold for a ladle for ergonomic testing. | FDM PLA SLA: Standard Resins, Clear Resin (transparency), Draft Resin (fast) |
Medium Efficiency | For validation or pre-production use, printed models should have properties as close as possible to those of final production models , for functional testing, but do not meet stringent requirements regarding service life. Example: housing for electronic components to protect against sudden impacts. Functional characteristics include the ability to absorb impact energy. In addition, the body must snap into place and retain its shape. | FDM ABS SLA: Engineering Resins SLS: Nylon 11 Powder, Nylon 12 Powder, TPU |
High Efficiency | Final 3D printed models must be highly stable to achieve end use products to wear and tear over a certain period of time, whether it be a day, a week or several years.![]() Example: shoe soles. Features include rigorous cycling and unloading life testing, color fastness over many years, and tear resistance, among other things. | FDM Composites SLA: Engineering, Medical, Dental or Jewelry Resins SLS: Nylon 11 Powder, Nylon 12 Powder, TPU, Nylon Composites |
material requirements: material properties that will satisfy these requirements. These indicators are usually given in the technical specifications of the material.
Requirement | Description | Recommendations | |
---|---|---|---|
Tensile strength | Resistance of material to fracture under tension. High tensile strength is important for structural, load-bearing, mechanical or static models. | FDM PLA SLA: Clear Resin, Rigid Resin SLS: Nylon 12 Powder, Nylon Composites | |
Flex Modulus | Material resistance to bending under load.![]() | FDM PLA (High), ABS (Medium) SLA: Rigid Resin (High), Tough Resin and Durable Resin (Medium), Flexible Resin and Elastic Resin (Low) SLS: Nylon composite materials (high value), Nylon 12 Powder (medium value) | |
Extension | Material resistance to tensile failure. Allows you to compare the degree of stretching of flexible materials. It also indicates whether the material is stretched or immediately destroyed. | FDM ABS (medium), TPU (high) SLA: Tough Resin and Durable Resin (medium), Flexible Resin and Elastic Resin (high) SLS: Nylon 12 Powder (medium), Nylon 11 Powder (Medium), TPU (High) | |
Impact | The ability of a material to absorb impacts and their energy without breaking. Shows toughness and durability. Allows you to determine how easily the material breaks when it falls to the ground or collides with another object.![]() | FDM ABS, Nylon SLA: Tough 2000 Resin, Tough 1500 Resin, Gray Pro Resin, Durable Resin SLS: Nylon 12 Powder, Nylon 11 Powder a certain load. Indicates whether the material is suitable for high temperature applications. | SLA: High Temp Resin, Rigid Resin SLS: Nylon 12 Powder, nylon composites |
Hardness (durometer) | Material resistance to surface deformation. Allows you to determine the right degree of plasticity for soft plastics such as rubber and elastomers for a particular application. | FDM TPU SLA: Flexible Resin, Elastic Resin SLS: TPU | |
Tear resistance | Material resistance to notching under tension. This indicator is important for evaluating the durability and wear resistance of soft plastics and flexible materials such as rubber. | FDM TPU SLA: Flexible Resin, Elastic Resin, Durable Resin SLS: Nylon 11 Powder, TPU | |
Creep | Creep is the tendency of a material to permanently deform under the influence of constant stress: tension or bending, compression, shear .![]() | FDM ABS SLA: Rigid Resin SLS: Nylon 12 Powder, Nylon 9 composites0980 | |
Compression set | Irreversible deformation after material compression. An important indicator for soft plastics and applications where flexibility is needed. Indicates whether the material will restore its original shape after the load is removed. | FDM TPU SLA: Flexible Resin, Elastic Resin SLS: TPU |
For more information on material properties, see our guide to the most common mechanical and thermal properties.
By converting functional characteristics into material requirements, you can most likely find out which material or small group of materials is suitable for your application.
If more than one material meets your basic requirements, a broader range of desirable characteristics, as well as the advantages and disadvantages of these materials and processes, can be considered for the final selection.