Battletech 3d printer
A Guide for those who are interested in 3D printing : battletech
My Personal Guide to 3D Printing Battletech Minis
FIRST AND FOREMOST: If you decide to 3D print, STILL SUPPORT CATALYST / IRON WIND METALS - they are the reason this game still exists! (and if you can spend $ on a 3D printer, you can buy some box sets / minis.)
SECONDMOST: This process requires a few things to be a viable endeavor:
A degree of technical ability - you will need to use basic hand tools (allen wrenches, screw drives, craft knives, etc)
A willingness to work with (somewhat) hazardous materials - you won’t be handling spent nuclear fuel rods or uncleaned medical testing equipment from a foreign virus lab (wink wink), but you will be handling concentrated isopropyl alcohol, and resin that can be very irritating to skin / eyes. Gloves are a must, goggles / mask strongly encouraged.
Some spending money - I’ve spent about $500 (USD) so far, though it CAN be done cheaper (printers have gone down a lot recently, and a lot of things I bought are optional or you may already have.
) The actual cost of materials per mini is about $0.25-0.50, most of the cost is setup.
So onto the guide!
There are many great general guides to 3D printing, and r/3Dprinting has an awesome beginners guide. So I won’t repeat them here. Instead, I will provide insights specific to Battletech.
There are two main types of 3D printers available to hobby-level consumers: Filament (FDM), and Resin (SLA/DLP). For Battletech (or any tabletop miniature, really) Resin is better - higher resolution and clarity of details. See: https://www.windowscentral.com/resin-or-filament-3d-printing-which-best-you for more in-depth info.
There are many great resin printers available for under $300. I personally bought an AnyCubic Photon Mono (not the X or the SE, just plain mono - their product naming kind of sucks) which is a great deal for the $.
MY PROCESS:
Begin with the “Seven P’s”: “Prior Proper Planning Prevents Piss Poor Performance” - setting up a semi-permanent workspace, and doing all your design work ahead of time.
STEP 1 - ACQUIRE STUFF
You will need:
A 3D printer (duh)
Liquid resin (I prefer Elegoo to AnyCubic, there are a lot of posts about this debate, but the Elegoo Standard Grey works fine for BT minis.)
Isopropyl Alcohol (most sites say use 99%, I’ve been using the 91% available at Walmart. Works well.)
Safety Goggles / Mask (optional, but strongly recommended)
Medical Gloves (Nitrile are the best, about $20/box, nylon are ok, but can’t really be reused. Haven’t tried latex, some people are allergic.)
A UV-lamp (optional, but recommended. The “official” ones are like $100, I bought a cheap one with a rotating stand for like $20. Or you can use sunlight, but it takes a while and winter is coming.) (Second note: UV barely travels through glass, so can't be indoors, that why you don't get a tan through the window.)
A LOT of paper towels (there are some things you shouldn’t use these on, but for everything else…)
A few microfiber rags (for the stuff you can’t use paper towels on.
)
Some paint filters and funnel (most printers come with a few, and if you follow this guide, you won’t need a ton.)
A plastic pickling container with strainer (completely optional, but makes cleaning models a lot easier)
X-acto / craft knife.
“Nippers” (precision wire cutters.)
A level workstation away from kids / pets / other disturbances.
STEP 2 - ACQUIRE MORE (digital) STUFF
Before you print something, you need a blueprint. For 3D printing, they use files called STLs. If you have 3D modeling experience you can design your own. But for the rest of us:
Piranha Games has made the 3D models used for Mechwarrior Online open source, this has created some great opportunities with a few caveats: They are free for PERSONAL USE, you CANNOT SELL BATTLETECH prints.
Some great places to search for .stl files are MyMiniFactory.com, and Cults3D.com. Thingiverse is the biggest repository of STL files, but has had some issues. Search for “American Mecha” if you are having trouble finding what you want. You will have to find hex bases separately. The official bases are 29.5mm across. Most files are about 50mb. I downloaded a LOT of them :)
You also need the software to edit / slice them. Anycubic printers come with a software that has a few very useful features, but isn’t the best overall. Personal I use three different programs for each mini: Anycubic Photon Workshop (comes with printer, also avail free), PrusaSlicer (free version), and ChituBox (free).
STEP 3 - GET EVERYTHING READY
Setup your printer according to instructions. If you want some how-to videos, I found “3D Print Farm” on youtube especially helpful. My setup is pictured here: https://imgur.com/a/NEKjzBx
For the mini’s STL files: Firstly, I open the STL in ChituBox and before anything, “slice” it. (there are lots of guides on what this means, and should show up in your instructions also.) This isn’t to print, but to find out the volume of the mini. While almost all the minis I’ve found are ‘good enough’ size wise, I wanted more, and using the Wolverine WVR-6R as a baseline (Because I have the 3rd edition, beginner box, and Syllogy’s STL to compare) reached the conclusion that models should be almost exactly .1ml per ton (the 55-ton WVR is 5.49ml).
I included a comparison image here: https://imgur.com/a/NEKjzBx
You can use a volumetric formula to figure out exactly how much to increase or decrease size to get to that, but trial and error works for me. A discussion on this from a few years ago is available here : https://www.reddit.com/r/battletech/comments/9w2kyd/battletech_miniature_sizes_3d_printing_need_help/
Then using ChituBox I added the base, and save the file as an STL (NOT save project).
Then I open it with Anycubic Photon Workshop software, because it has a very convenient feature to add text. I found that font size 2 (if you type 2, it will default to 20, so you have to fix it) and font height of . 5 works perfect to type on the bases. Re-save the file.
Next I open it with Prusa Slicer, because it has the best (and frankly only good) auto-support tool. This guy has a great 10-min video about it: https://www.youtube.com/watch?v=S4KRazqrMjE
Export the STL with supports, and save (I save using a different filename in case I don’t like the job the auto-supports did.)
Finally, I open the supported STL back with ChituBox. I have found that, to save time, I could fit THREE mechs on my printer at a time, and since it only matters how tall the print is, not how much material it uses, this saves a TON of time (and wear on the printer.)
STEP 4 - SLICE IT AND PRINT IT!
Do what step 4 says.
There’s a bunch of post printing clean-up, and touch-up stuff, but that should be covered easily in the instructions, and other beginner guides.
Pro Tip: plan to print en masse - my printer takes about 2.5-3 hours per print (at three mechs per), you don't have to stand over it, just be ready with the files to start the next one each time. As long as the resin in the printer keeps getting topped off, you don't have to worry about filtering it back, or having it separate from sitting too long. Filter and clean the VAT only when it's going to sit unused for several days.
STEP 5 - PRIME, PAINT, SEAL
I am still working on painting techniques, but it seems like this community already has that part down!
STEP 6 - FIND FRIENDS AND PLAY!
Thank you guys for reading this! I will keep this updated with any feedback or corrections people have!
Happy Hunting!
-DaCrazyJamez
Battletech, 3d Printers, and Automation
Some of my earliest gaming memories are frantically erasing paper mech sheets so I can play another round of Battletech in my grandparents basement. Following a long lapse whilst I whittled away the time in Mechwarrior Online or in the HBS Battletech game, I have finally returned to my gaming roots. Except the paper and pencil is gone and I’m printing my own mechs… Battletech is in an entirely new place and it’ll blow you away.
Battletech is a game of grandeur. In your mind is a picture of Clan dropships depositing lances of mechs, dozens of them, all duking it out at point blank range on some Federated Suns planet. But, as anyone who tried to juggle a dozen units in Battletech… it was a mess. It is a mess. First off you almost never have all the mechs you need, 2nd you had to photocopy dozens of sheets, and lastly you’d get bogged down. Never mind if you had a few supplemental rulebooks and had to calculate artillery and air support.
The dream is there. And now you can make it happen.
3d Printed Resin Mechs
My first 3d printer was a Prusa Mk2 and it did an amazing job with a lot of things. Mechs was not one of them. It did some great terrain for my meager collection of mechs. Resin 3d printers were a thing but they were kind of pricy at the time. Fast forward a couple of years and I finally bit the bullet and got a Photon Mono. This little guy allows me to print miniatures and mechs that are indistinguishable from an injection molded battlemech.
There are two primary sources for 3d printed files, one is Thingiverse and the other is Myminifactory. Thingiverse was once the big boy on the block but suffered from a serious lack of support that drove a lot of people to Myminifactory. As with any online ecosystem size drives more size and today you can find a ridiculous quantity of mechs to print. For free.
This is the core of the new mech era. You go and download an STL, slice it, and print it. Generic resins tend to be a bit on the brittle side but this is manageable if you don’t smash all your mechs about like green army men. You can also blend resins to get a more robust product with some minor lack of detail. I haven’t tested it out yet but have seen good results.
On top of all of the mechs on Myminifactory is Patreon. The most interesting Patreon I’ve seen is from Polygon Masterworks. This guy has “Not Battletech” battlemechs in a mind boggling variety. You know all of those variants produced over the hundreds of years of the game?
Here we have the Wackmaster in 19 variants. 19. 19. Granted you need to be quite a Battletech enthusiast to need 19 varieties of a mech but it’s available.
The printer itself will run you a few hundred bucks and each mech will cost maybe $0.25 in resin. The process I follow is pretty easy. Slice and generate supports in Prusaslicer. Export stl to Photon Workshop and slice. Print. For ease of removal I installed a magnetic Wham-Bam plate that makes popping off those mechs super easy. (If you’d like to see more on the process let me know and I’ll expand on it. It’s easier than you think.)
Battletech Automation
Once you have a couple of dozen mechs you run into an issue.
Accounting.
We could call it something different but it becomes accounting. You account for movement. You account for pilot skill. You account for attacks. Damage. Heat. Internal Damage. Physical attacks. The system, in my eyes, breaks down after more than 4 mechs per player. You run into futziness once you need to mark out who ran, walked, was stationary, heat etc. For an experienced player it is quick, but a mondo sized game becomes a hassle. Yes, I’ve seen some awesome Excel sheets, but that sticks this in the realm of accounting even more.
“Hey honey, why don’t you get the spreadsheet set up while I get out the mechs?” Said no happy couple ever.
Try teaching the game to an avid boardgamer that doesn’t have Battletech nostalgia. Battletech, for all of its’ character is a system designed 30 years ago. Board games and war games have made leaps and bounds to streamline design and enhance gameplay. But for all of its flaws it’s a functional system, it’s just kind of clunky.
This is Flechs Sheets. It is a digital automation tool to assist you playing on the tabletop or in a virtual space like Tabletop Simulator. It is not a total replacement as it does not track position. You, the player must still interact with your mechs in one way or the other and feed some basic information to the sheet.
After setting up your table (with your 3d printed mechs) you start working through the sheet phase by phase. In this case my Warhammer IIC is walking 2 hexes.
Then we fire on the Mad Cat. You just select the weapons, designate the target, range, and variables and fire.
The combat is resolved and if we switch to the Mad Cat we can declare its attacks. Remember, in Battletech combat is simultaneous, resolution occurs after everyone fires. In this case we’ll have the Mad Cat fire back at the Warhammer.
In classic Battletech style… the Mad Cat misses. Everything. So lets resolve the fire and see how the Mad Cat looks.
The Mad Cat gets thoroughly wrecked. A headshot from the Warhammer’s ER PPC kills the pilot. Now I have not played this multiplayer but you can go up against a friend online. Combine this with something like Tabletop Simulator and you have one fairly amazing Battletech game.
It plays really well on an iPad too. You can create your battle lists, print sheets if you’d like, and still use Flechs to do the dirty work. It just remembers to make you fall down after your leg is blown off.
It’s got a certain charm that MegaMek (another awesome program) doesn’t. Where Megamek is crunchy and dense, Flechs covers just the bare essentials and still gives you the tabletop experience. My greatest triumph has been getting my 10 year old son to play and have it be interesting for him. Seeing the attacks resolve on the iPad and watching as he destroys my mechs bit by bit is much easier for him to visualize than coloring circles on a sheet. This basic enhanced reality is eye catching and engaging.
Lots of board game manufactures have tried to meld the iPad to the boardgame. Fantasy Flight Games did it with Destiny and it just felt flat. Flechs though really hits the sweet spot. Even if you aren’t familiar with Battletech you can hammer through the interface and get a pretty good idea of what an Atlas would do to a Locust.
Now it doesn’t do it all. Missing is the crunchy nuance of more advanced systems but it’s flexible enough to let you integrate your own modifications.
A Shift in Business Model
Battletech has a long and fractious history, and that’s not just inside of the game. If you look at the 40k model they design models, injection mold them at a very high quality level, and then sell you sourcebooks and models to go with it. Games Workshop has some of the best sculpts in the industry and a very robust shipping network. Catalyst in comparison has some kind of crappy old school sculpts and some very new, and much better ones.
By inserting a superior 3d print system a good deal of the business model falls apart. Now they must create strictly IP as it’ll be a tough sell for you to buy a metal battlemech for approximately $15. Kickstarter has done a great deal to bring in new players and generate buzz. (11,200 backers for $2.5 million). But can they do more to grow the base?
This is a Thunderbolt that I printed and painted (poorly and simply). Resin cost was about $0.25. I think it took a couple of hours to print. (An interesting fact on resin 3d printers is it takes just as long to print a plate of mechs as it does a single mech. )
This is a metal miniature with a different sculpt. (Check this link for the crazy history of battletech miniatures). Most of these require assembly and even though they are metal, I’ve found metal miniatures to be fragile and finicky. My first preference is injection molded plastic and then resin as I don’t have to do any assembly other than glue them to a base.
Here is the other three from that print batch. I’m not a terribly good painter and these were mostly to allow me to practice some schemes. If I purchased these 4 mechs in metal, it’d run me about $50. Now I could get them through one of the Battletech sets, if I’m lucky enough to get it in the mystery box.
Resin printers are popping up all over in the gaming communities. People that are way more talented than I am are pumping out amazing dioramas, battlescapes, gaming tables, and stuff that I don’t even know what it is. But it’s awesome. The greatest thing I can see is Catalyst Game Labs embrace the future and create amazing battles, fiction, lore, and supplements all the while growing with stuff like Flechs and Myminifactory.
It’s a symbiotic relationship that can help Battletech become greater than it ever was. The challenge is the 3d printer side of things remove a profit generating aspect of the business. That challenge isn’t going away. Even if there is DMA takedowns then the printer files will go onto torrents or pirated sites hosted in places where DMA has no power. Here is a good link on the legal aspects of this situation. To no ones surprise the law has not kept pace with the technology.
Polygon Masterworks designing a Wackmaster has side-stepped any IP issues that are directly in conflict with Battletech’s IP. He’s just designed a big fighting robot. Rather like the million different variants of dwarves or orcs or “not space marines” you see.
There are 3d printer sites like Gambody that offer 3d models that are licensed (I think?) These are vanity scale models and not tabletop size. Think 10″ tall units printed in many sections.
A friend of mine has done this, and many more like it for his local gaming club.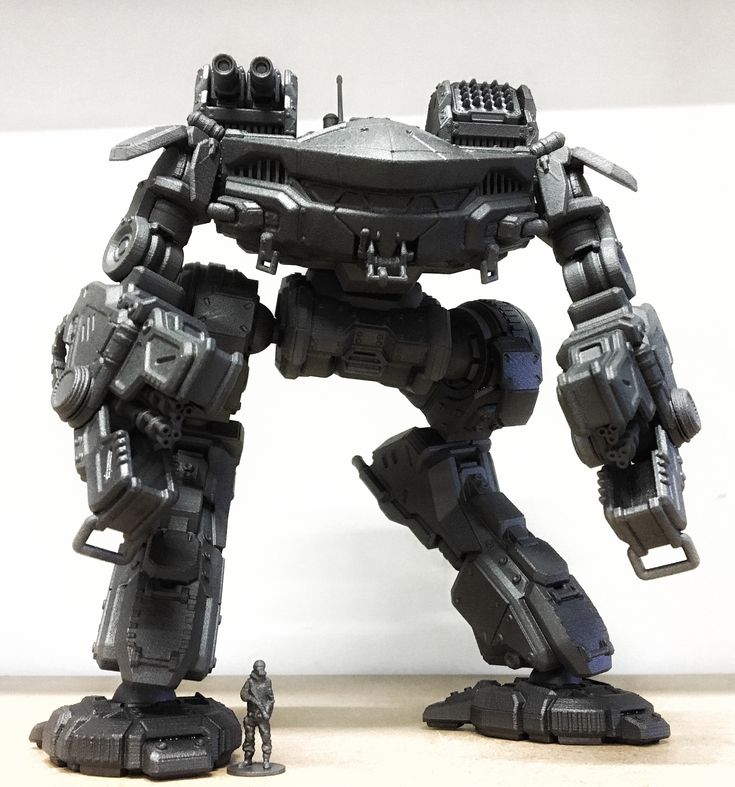
I encourage you at least to give Flechs Sheets a try with your own mechs and maps. You can even print your sheets right there. It really lets you embrace the battle and the story of what is unfolding in front of you and handles all the starting-and-stopping you get from digging in a rule book.
The best part for us, the Battletech consumer, is a resurgence in interest and content. You have more tools at your disposal to play more games with less hassle. So go, get your giant stompy robot play on.
3D Printer Pistols are Back and Unstoppable / Sudo Null IT News They anonymously share drawings, tips, and create their own community. And there is no easy way to stop them.
In the United States, a network of supporters of printing weapons on a 3D printer is growing again - but now everything is different. Unlike previous attempts to popularize weapons that can be printed on a 3D printer, this operation is completely decentralized. It has no headquarters, no trademarks and no leader. And the people behind it believe that this state of affairs guarantees the inability of governments to stop them.
“If they want to come after me, they'll have to find me first,” says Ivan the Troll, a member of the group. “I am one of many like-minded people doing this work.”
The troll Ivan is known only by his network pseudonym, and is the de facto representative of an underground organization of gunsmiths working on 3D printers. Ivan says he knows at least 100 people actively developing weapon 3D printing technology, and claims that thousands of people are involved in the network. And this loosely connected network spans the entire world.
They communicate on different digital platforms - Signal, Twitter, IRC and Discord. They critique each other's work, trade weapon CAD files, give advice, talk theory, and collaborate on new blueprints. Enthusiasts of printed guns - who share similar ideas and political views on gun control - mostly meet on subreddits and forums dedicated to this topic.
Ivan himself is only a small part of this network. He says he comes from Illinois and is about the age of a "college student," but otherwise keeps quiet about himself to keep his head down. In doing so, he launched some amazing commercials showing new handgun parts he printed out in his garage, including the Glock 17 pistol frame.0006
On the last video [ , the video is deleted from YouTube, but the videos can be found on other hostings / approx. transl. ] shows the Glock 17 resin frame in various stages of production in the workshop. The footage is sounded with fast synthwave music, and passed through a VHS filter for greater aesthetics. By the end of the video, Ivan fires several shots from a ready-made pistol, and the captions that appear at the same time read: "Anyone can do this", "Live free or die", "Let's try to stop this, you dirty etatists." He also uploaded a complete CAD model of the AR-15 assault rifle to a file sharing site. It is clear that Ivan is trying to provoke his detractors to the maximum.
In February of this year, Ivan and his group decided to call themselves "Distributed Deterrence" transl. ], which is an allusion to the name of the company Defense Distributed [distributed protection], which was previously headed by Texas crypto-anarchist Cody Wilson.
In September 2018, Wilson, aged 30, was arrested and charged with sexually abusing a minor. He allegedly paid $500 for sex with a 16-year-old girl in his hometown of Austin, Texas. Naturally, this arrest took Wilson completely out of the world of 3D printed guns. Many of the people who admired him were either disgusted or realized that his time had passed. He retired from Defense Distributed, which used to be the main driver behind 3D weapon printing, since its inception in 2012. Wilson was released on $150,000 bail, but hasn't been in touch since.
Defense Distributed has many other legal issues. Attorneys in more than 20 US states are currently suing the company - which has filed counterclaims - in an attempt to undo the company's win in court that allowed the company to upload and share 3D weapon blueprints online. All these processes are long and tedious (New York State just passed a law to ban 3D printed weapons).
But for Ivan's group, Deterrence Dispensed, none of that matters. They upload their files singly to services like Spee.ch, a media hosting site powered by the LBRY blockchain, without waiting for anyone's permission. They themselves make blueprints for printing weapons, tweak old ones, and distribute all blueprints from Defense Distributed for free.
“Even if no government forbade me to do this, I think I would still do it,” says Ivan. “Some people enjoy video games, but I like to spend time drawing things in CAD.”
But Ivan doesn't just "draw things" in CAD. He's giving away files for free to help anyone with a decent Fused Deposition Modeling (FDM) 3D printer and certain tools build a working gun. Once the CAD file is downloaded, it is opened in a slicing program that translates the CAD files into instructions that the 3D printer can understand. After the parts are ready, they can be assembled, getting a fully working weapon.
The blueprints that Deterrence Dispensed shares with the world are so good, according to Ivan, that they are not just "working", they are of excellent quality. “Our AR15 model is the best available to the public without a doubt,” says Ivan.
Despite active antagonism with the authorities, Ivan has had no problems with them so far. His Twitter account was permanently shut down by Senator Bob Menendez of New Jersey, but so far, from the point of view of law enforcement and government, all has been quiet.
Ivan considers himself and other radical gun printing groups like FOSSCAD to be hobbyists who want to do something “wrong”. He believes that the problems of 3D printing weapons are overblown. He points out that while printable gun parts can be used to kill people, homemade guns have always existed and are probably more lethal. From his point of view, all this hysteria and backlash is directed to the wrong address.
"Trust me as a gun maker. A semi-automatic shotgun is 100 times easier, faster and cheaper to make than a regular pistol. I can go to Home Depot and buy a shotgun for $8."
In 2019, 156 people have already died in mass shootings in the United States, and in principle, the number of deaths related to weapons is a 20-year high. In March, a terrorist armed with two semi-automatic rifles and two shotguns killed 51 Muslims in Christchurch, New Zealand. Does the US (and the rest of the world) need more weapons in these circumstances, homemade, printed or otherwise? Ivan thinks so.
“The police killed more people last year than were killed in all the mass shootings in the last 10 years,” he says. “We in America live in a society where there is always the risk that a cop will shoot your ass off for nothing. And you don't even have to pose a threat to him. A cop can kill you just because he wants to, and he can get away with it."
He cited numerous examples of policemen shooting at unarmed black Americans, especially Steven Clarke. Clark, 22, was shot and killed by police in his garden with only his cell phone in hand. “I think it’s extremely important that everyone has the opportunity to have a gun,” Ivan continued. “Everyone should have the same legal options as the cops using them to control you.”
However, the facts are undeniable. Slightly more than half of deaths from firearms occur in six countries, incl. in the USA. And analysis from Harvard University shows that the more guns there are, the more murders there are.
Opponents of weapons, of course, are not satisfied with the concept of a downloadable pistol. Avery Gardiner, one of the presidents of the Brady Campaign, said that 3D-printed weapons "pose the greatest threat to our security." Following the court ruling in August, Gardiner said, "There is already a wave of dangerous individuals trying to illegally post blueprints on the Internet."
Members of this decentralized 3D printed weapon society are often motivated by a mixture of libertarian views and the pleasure of designing and creating tangible items as a hobby. They upload drawings to the Internet, share them, improve diagrams and make it easier to print, while remaining out of sight. Ivan states that he does this for the love of freedom and radical adherence to the first two amendments to the US Constitution: freedom of speech and freedom to bear arms.
However, his radicality goes as far as to talk about the right to have his own Tomahawk-class missiles, saying that they would be safer in his hands than in the hands of the US Army and its allies - given the history of accidental killing of civilians by the military, including a wedding in Afghanistan and a school bus in Yemen.
Describing the growing list of civilians who died at the hands of the US military in foreign wars, Ivan often comes across as more of a radical leftist than the right-wing gun fanatic that many think he is. However, he rejects any particular ideology, saying, "I myself am special and unique."
So far, Troll Ivan, Deterrence Dispensed and thousands of 3D weapon printing enthusiasts, united by a worldwide network, have let the genie out of the bottle. Unable to stop anonymous file sharing for weapon 3D printing. Whether they are hiding behind freedom in the process or not, one thing is clear: it is too late to stop them.
Is it possible to print airguns and firearms
Is it possible to make a gun on a 3D printer and is it legal?
Today's 3D printers offer enormous possibilities. They can print products of almost any complexity. Until quite recently, it was difficult to even imagine that a plastic weapon could shoot. However, it is already possible to make a pistol on a 3D printer, which, although not reliable, still fires live ammunition.
Can firearms be 3D printed?
Back in 2013, a young American activist for the free sale and distribution of weapons proved that plastic weapons can be printed on a 3D printer. He was the first in the world to make a pistol in this way, in which only the striker was made separately from metal. All other parts were printed on an FDM printer.
Today's 3D printers are capable of printing any CAD model, and these models of firearms have been available for over 10 years. If in previous years their printing required professional skills, now almost any user can master them. With a 3D printer and a finished model, it became quite possible to print a gun. Another thing is that such "creativity" is punishable by the laws of most countries.
The evolution of 3D printed weapons
Despite all the prohibitions and restrictions, the evolution of 3D printed firearms is moving at a great speed. The beginning was laid by the single-shot plastic pistol Liberator by American K. Wilson, which appeared in 2013. It had a simple design and was chambered for 380 ACP. Already after 10-12 shots, this weapon became unusable. However, the very possibility of printing firearms served as an impetus for the development of the idea. The author of the first pistol himself founded the Defense Distributed company, which began to actively improve the technology.
One of the ways to increase the durability of weapons was to increase the number of their barrels. At the beginning of 2014, the Japanese Y. Imura makes a 38 caliber Zig Zag pistol. He was able to fire up to 6 shots non-stop. The author of the weapon was recognized as a criminal and convicted.
The next step was the production of a six-shot revolver by J. Patrick in 2015. The PM522 Washbear has been shown in action on YouTube. The weapon was noticeably safer for the shooter compared to previous versions, but still allowed to fire only a few dozen rounds.
The first 9mm semi-automatic pistol appeared in 2016 under the name Shuty-MP1. It was developed by a handicraft gunsmith who hid under the pseudonym Derwood. It wasn't exactly a plastic weapon. The author used some metal parts from factory pistols - a barrel, a firing pin, a bolt and several springs. This made it possible to ensure a rate of fire of more than 46 rounds / min. However, when changing the store, the plastic case had to be cooled. In 2017, the same master proposed an improved model - Shuty AP-9.
The main contribution to the development of 3D printed weapon printing technology was made by Defense Distributed, which brought together a group of like-minded activists. First, these enthusiasts won legal proceedings in the United States and obtained permission to 3D-print weapons, which greatly expanded their capabilities. Secondly, they were able to set up a professional business with product testing and quality control. As a result, in 2018–19 they developed numerous models of a variety of firearms - from pistols to carbines. They posted over 30 files for printing original gun parts. Most of them were plastic, and the metal parts were not made from purchased, ready-made elements, but from simple metal profiles (tubes, strips, etc.), which are sold in ordinary hardware stores. This made it possible to exclude the use of parts patented by gunsmiths.
At the moment, the semi-automatic carbine FGC-9, developed on the basis of the Shuty AP-9, has become the pinnacle of "creativity" of Defense Distributed. At the same time, there is not a single factory part in it. The barrel for the 9 mm cartridge is made of steel pipe using electrochemical processing.
Where can I get drawings and what should I look for?
Gun manufacturing bans make it much more difficult to access blueprints and models of guns for 3D printing. The right to free placement of information was achieved only by Defense Distributed. Their website provides free access to drawings, models and technologies. Other information can be found on the Internet, but they are usually illegal.
When choosing a model, pay attention to the following information:
- material used;
- cartridge for which the model is designed;
- number of cartridges in the magazine, rate of fire;
- duration of operation before failure.
It is important to clarify which metal parts will need to be purchased separately, in addition to plastic for printing on a printer.
What does the law say in different countries?
The only country where firearms can be 3D printed is the United States. Gun Control Act 19 applies here68, giving Americans the right to make weapons, but only for personal use. Only one limitation is put forward: it must be determined by metal detectors, that is, it must have a metal element. In virtually all other countries, homemade manufacture and repair of weapons for any purpose is prohibited by law. In Russia, printing it on a 3D printer falls under the Criminal Code of the Russian Federation and is punishable by imprisonment.
Should we be afraid of plastic weapons?
The question of how dangerous a weapon printed on a printer is becoming increasingly important. Despite all the prohibitions, it is extremely difficult to control the spread of technology around the world. The availability of 3D printers and the increase in their functionality make it possible to master the production of plastic guns at home. How dangerous is such a weapon?
Most experts agree that currently printed weapons are more of an interesting toy. It is quite expensive and is designed to carry out only a few dozen shots. Moreover, such pistols are quite dangerous for the shooter himself with live ammunition, because they can explode in their hands.
However, the danger cannot be underestimated. It is easier and cheaper for a "serious" criminal to buy illegal military weapons than to make them on a printer. At the same time, there may be "enthusiasts" who, for their own interest, can make a pistol and try it out in action. Such inadequate people represent an undoubted danger. In addition, the temptation is great for terrorists. Metal detectors do not detect a plastic gun, which means that it is easier to carry it, for example, on an airplane.
Important! Plastic weapons have a very small resource. At the same time, sometimes just one shot is enough to kill a person.
3D printed firearms have the following advantages:
- the ability to make military weapons at home;
- light weight;
- availability of materials;
- ability to copy famous weapon models.
Always remember that there are significant disadvantages:
- illegal manufacture;
- high cost of weapons;
- very small resource and limited rate of fire;
- danger to the shooter himself.
Currently, plastic weapons have more disadvantages than advantages, and most importantly, you can get a real prison term for making them.
Prospects for printing weapons
The potential for 3D printing of firearms is far from exhausted. The expansion of equipment capabilities and the development of innovative materials indicate that in the near future such weapons may approach military weapons in terms of characteristics. In the future - a significant increase in the resource and the provision of automatic firing.
Significantly increases the reliability of printed pistols and carbines SLS technology using metal powder. Such weapons already differ little from the factory metal models. While it is very expensive, which significantly limits the application.