American 3d printers
Best USA 3D Printer Manufacturer | American Made 3D Printer
OUR HISTORYFusion3 was conceived in 2012 in North Carolina, anticipating that 3D printing and 3D printer companies would eventually see mainstream adoption not necessarily by consumers, but by businesses and other organizations that will require an end-to-end experience that delivers both performance and reliability as a mission-critical tool for the organization. We set our goal to become one of the country’s best 3D printer companies, consistently producing the very best American made 3D printers.
3D PRINTERS MADE IN THE USASince our founding, Fusion3 has grown to become a leader in the design and manufacture of American made, professional 3D printers. All production takes place at our Greensboro, North Carolina, USA factory, ensuring both innovation and the highest quality in every device we ship to our customers.
3D printing is not overly difficult and we at Fusion3 are working to develop technologies to make the process easier and more reliable with each product generation.
For first time users in can feel overwhelming to adopt 3D printing technologies. In response, we at Fusion3 the best warranty and strive to provide the highest quality of technical service and support of any 3D printer company in the industry. Our technical support teams are also based out of our USA 3D printer factory and staffed by employees who have expert knowledge of the product as they too build and operate our American made 3D printers on a daily basis.
Do you know the manufacturing locations for each of these 3D printer manufacturers? | |
Raise3D | China |
Ultimaker | Netherlands |
Makerbot | China |
Zortrax | Poland |
Provide
world-class, USA-Made 3D printers,to customers at best-in-class prices.
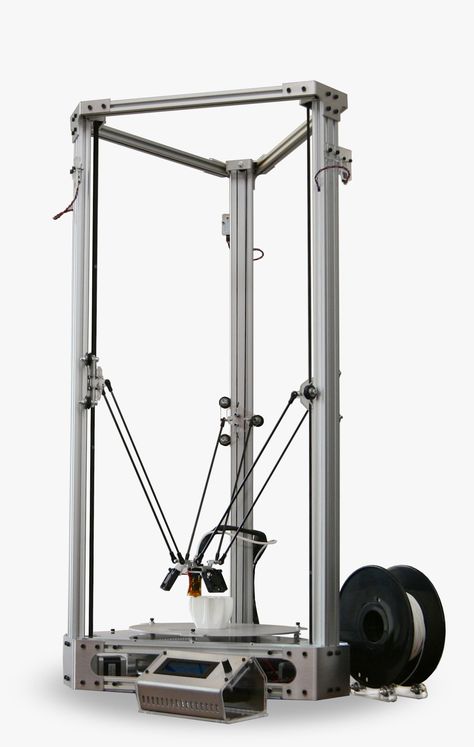
We accomplish this by building US 3D printers that delight the end-user AND
demonstrate value to the purchasing executive through:
Continual Improvement
Our customers require a product that works reliably AND provide best-in-class performance. We continually identify ways to improve the speed, print quality, reliability, and ease of use of our printers, ensuring we are consistently at the forefront of improvement among all 3D printer companies.
Features, Not Flash
Sexy industrial design is expensive and translates into a higher priced product for the customer. Unlike other 3D printer companies, Fusion3 invests its resources to improve performance. When we invest in industrial design, its because we see an opportunity to improve performance and reduce operating costs for the customer.
Customer Satisfaction
Not only do we strive to build a great American made 3D printer that can operate for thousands of hours, but we also make sure that the customer is able to generate great printing results. We’re happy to take your call whether solving an issue or helping you imagine ways to get more from our printers.
HEADQUARTERS / FACTORY
MAILING/SHIPPING ADDRESS:
Fusion3 3D Printers
130 South Walnut Circle
Greensboro, NC 27409
Visits by appointment only
Phone / Main Switchboard:
877-452-0010
MAILING/SHIPPING ADDRESS:
Fusion3 3D Printers
620A South Elm Street
Greensboro, NC 27406
Visits by appointment only
Phone:
877-452-0010×1
how to add a map to wordpress
KEY CONTACTSSales: [email protected]
Technical Support: [email protected]
Reseller Inquiries: resellers@fusion3design. com
Testing of 3D Printable Materials: [email protected]
Shipping & Accounts Receivable: [email protected]
Accounts Payable: [email protected]
Corporate Inquiries / Partnerships: [email protected]
Employment: [email protected]
FREQUENTLY ASKED QUESTIONS:ABOUT FUSION3 3D PRINTERS
;">Where is Fusion3 based?
Fusion3 is based in the US in Greensboro, North Carolina. All of our production takes place in North Carolina and we are proud to produce some of the best USA made 3D printers.
;">What 3D printers are made in the USA?
If buying a USA-made 3D printer is important to you, you should make sure the 3D company you are evaluating manufactures in the US. While many 3D printer companies have corporate offices based in the US, they often outsource their manufacturing to other countries. At Fusion3, we are proud to not only have our office located in the USA, but also our manufacturing in the USA.
Home |
|
• 3D Printing • 3D Scanning • 3D Copying • 3D Design • 3D Printer Sales • 3D Scanner Sales • 3D Printing Supplies |
|
What's New: American
3D Printing brand TPU just $47. We also now have American 3D Printing brand ASA (Acrylonitrile Styrene Acrylate) is similar to ABS, but is stiffer and is UV-resistant. Same price as ABS, $35.95/kg. In addition to PLA and ABS, we now have Makeshaper brand PETg for only $35.95/kg, less than half the price of Taulman T-Glase. We have the carbon fiber reinforced HTPLA from Protopasta. This stuff is REALLY rigid! Speaking of carbon fiber, we have super-strong carbon fiber reinforced nylon from Colorfabb. And speaking of Colorfabb, in addition to their specialty brass, bronze, and copper filaments, we also have glow in the dark PLA! We
are now officially Tiertime resellers, and stock the new UP Mini
2! At only $599, it features a fully enclosed build chamber,
WiFi and a color touch screen! This is an ideal starter 3D
printer for the student or hobbiest. American 3D Printing is now an official Mcor reseller. Come see our Iris full-color paper based 3D printer!
Ribbon cutting at our 2nd birthday party open house on August 27 2015 Proud members of the Evergreen Area Chamber of Commerce since 2015. We have partnered with one of the largest filament filament manufacturers in the USA (yes that's right, made-in-the-USA quality!) to bring you our own American 3D Printing branded filament. It
is MUCH higher quality than that Chinese stuff you see everywhere,
yet we can bring this to you for only $35. In the News: Spyder Bytes Mountain Connection Canyon Courier Denver Post
|
3D
Printing: 3D
Scanning: Engineering,
Design, Post Processing, Consultation and Training: Material : Varies, see latest list
New! ASA 3mm Black PLA: Taulman Nylon 618 1.75mm & 3mm High
Impact Polystyrene (HIPS) 1. PETg:
Laybrick 3mm Natural TPU 1.75 & 3mm 7 Colors PVA 1.75mm Natural Aquatek 3mm Natural Protopasta Stainless Steel 1.75 & 3mm Natural Colorfabb Copper 1.75 & 3mm Natural Colorfabb Bronze 1.75 & 3mm Natural Colorfabb Brass 1.75 & 3mm Natural Carbon Fiber Polyamide 1.75 & 3mm Black Equipment - In Stock, take one home today!: Lulzbot TAZ Workhorse $2,950 Sense 3D Scanners $499 Makerbot Replicator+ $2,099 Makerbot Replicator 2 $2,199 Lulzbot TAZ Pro $4,950 Tiertime UP Mini 2 $599 Lulzbot Mini 2 $1,500 Ask about our education discounts! Blowout Prices on Used Equipment! 1/2 Price from list! Z-Morph Personal Fabricator $999 |
3D Printer Review UP! Mini
3D printers have long ceased to be expensive, bulky and noisy devices used only in industrial production, various institutions and large companies. Printing and modeling volumetric objects at home no longer requires high costs and in-depth knowledge. There are many types of 3D printers now: self-assembly kits, expensive European and American 3D printers, high-precision 3D printers with a large print area, for jewelers and dentistry, etc. But among all the models available and with stable high print quality, there are not so many. One of them, compact and elegant - 3D printer UP! mini.
The Mini has been on the market since 2013 and is still one of the best compact 3d printers around. Model UP! Mini - developed by PP3DP. Because Since PP3DP is part of Tiertime, a large Chinese corporation that produces industrial 3D printers, you don’t have to worry about build quality and reliability. Serious production control and the absence of marriage are confirmed by numerous world awards, including the authoritative MAKE magazine for the best printer in the "get it and print" class.
Design
UP! Mini is a closed chamber 3D printer that has a positive effect on print quality, filters possible unpleasant odors, reduces the noise of moving parts inside the printer, and protects you and your children from burns if you accidentally touch the nozzle or 3D printer platform. With a modern design, UP! The Mini looks more like a coffee machine or something like that, rather than a modern machine that prints three-dimensional models from plastic.
Another advantage of this model is the patented perforated working surface of the platform with Teflon coating. Thanks to it, adhesion increases, stability and a stable position of the printed model increase. You do not need to spend money and time on the purchase of special coatings: adhesive tape, glue, varnish, special film, etc. which are widely used on many 3D printers from other manufacturers.
Getting Started
UP! Mini does not require you to seriously and deeply study the instructions for assembly, configuration and calibration. All you need to start printing is to take the printer out of the box, install the spool of plastic and the build platform, and start printing. Everything you need to run your 3D printer smoothly is included. Together with the device you get: a spare platform, a plastic coil and special tools for setting up and maintaining the device.
UP! The Mini is only 240 x 340 x 355 mm and weighs 6 kg. As mentioned above, according to these parameters, the device rather resembles an elegant and stylish household appliance that will complement and decorate your interior. With this in mind, you can safely place it anywhere in your home or office.
UP! Mini uses its own software, which any user can understand, the program is simple and intuitive, fully Russified and allows you to change and customize:
- Print speed
- Material type
- Percentage of material filling of the internal cavities of the model
- Scaling and rotation of the model
- The operating temperature of the extruder and platform.
- Size, type of supports and rafts
Or just select the type of plastic and start printing, all other values recommended for this type of plastic, the program will change on its own. All current operating systems are supported - Windows from XP to 8.1, and Mac OS X.
One of the main advantages of the UP 3d printer! Mini - is the presence of the "Pause" function, when during operation you can pause printing, replace the material and continue printing with a different color, which allows you to create bright and multi-colored models.
Getting started
So, you have connected the printer, loaded the model into the program and start printing. After sending the model for printing, the printer will need some time to load and prepare the virtual model for printing, the extruder and platform heat up, the layers of the model are calculated programmatically. After starting printing, you can safely disconnect the computer from the printer, then the printer will work autonomously.
Worktop size UP! Mini - 120x120x120mm. very good figure for such a small 3d printer. And don't let those numbers scare you, you can always print a large multi-part model. Special programs allow you to divide your virtual model into components already prepared and configured for 3D printing, print, and then glue. We recommend this method due to the fact that when printing on devices with a large print volume, any power outage, power surges, or suddenly running out of plastic will stop the printer and printing, which took several hours, will have to start over.
Maximum print resolution UP! Mini - 200 microns, or 0.2 mm. On our own, we add that due to the special closed design, uniform heating of the surface and the extruder, visually the models look comparable to those produced on 3D printers with a higher resolution (for example, 150 microns) and an open circuit. And do not forget that the higher the resolution, the longer it will take to print. For example, printing a model on printers with a resolution of 20 microns will take 10 times longer.
UP! Mini uses the most common consumables ABS (Acrylonitrile Butadiene Styrene) or PLA (Polyactide). But thanks to the heated bed and high extruder temperature, you can print flexible, engineering and decorative plastics. The printer comes with branded plastic, but you can use third-party plastics without loss of warranty and quality, the only condition is a diameter of 1.75 mm.
When UP! The Mini emits a short, rather loud and unpleasant squeak, but this is where all the unpleasant things from the printer end - both in terms of smell and noise from it, as expected, no problems. The printing process is monitored visually by the color of a single button. The backlight of the button changes color depending on the stage. And thanks to the backlight inside the case, you can observe the printing process without opening the printer door.
Output
UP! Mini is a full-fledged and serious device, perfect for both a beginner and an experienced professional. If you don't want to tinker with assembling, setting up, modifying the device, adding additional components, then the UP! Mini just for you. With a closed, safe design, no odors, and low printing noise, the UP! Mini is ideal for educational institutions, or use at home.
According to doctors, after the operation, the bird recovered quickly, the surgical intervention did not affect her appetite and habits. After some time, the protective mask printed on a 3D printer acquired the color of a beak, which became possible due to the secretions of special glands produced by the body of hornbills. The inventors of a medical 3D printer and a biocompatible resin said that in the future it is possible to use prostheses and artificial organs created individually for each patient with a specific disease.
3D printed hornbill implant
Photo: ZooTampa at Lowry Park
2
3D printing solves the problem of creating high-quality and affordable prostheses
Experts estimate that hundreds of thousands of people lose limbs and become waiting for a prosthesis. Mass-market prostheses are only available in a few sizes, so wearers have to adapt to the features of the medical equipment. In addition, they are short-lived and expensive to manufacture. 3D printing allows you to create an almost perfect prosthesis according to individual drawings. In this case, he can successfully replace the lost arm or leg.
Also, prosthetics services are usually available to patients in the developed world with good health insurance. Formlabs experts note that the problem lies in the lack of manufacturing processes that allow the production of non-standard parts at an affordable price. 3D printing could make prosthetics more affordable. For example, the non-profit initiative e-NABLE offers free blueprints, mockups, and open source programs to create medical devices using printers. In this case, the cost of one custom-made prosthesis can be only about $50.
3
Medical 3D printing requires a special resin that is compatible with living organisms
Modern 3D printers print blanks based on photopolymer resin, a special liquid substance that hardens when exposed to light. In medical printing, everything is much more serious, since it is believed that a person will be in direct contact with an object created using a 3D printer for quite a long time. Scientists explain that printed prostheses must have an ideal shape, taking into account the structural features of the body, and also consist of safe materials that will not cause an allergic reaction or rejection.
“The importance of 3D printing in healthcare cannot be overestimated,” says Gaurav Manchanda, director of medical market development at Formlabs. For example, medical "live" resin essentially resembles the material for printing conventional 3D blanks, but differs in detail from them. Firstly, it allows you to print more accurate objects - about a hundred microns in size. Secondly, it is designed for prolonged contact with the skin or mucous membranes. Thirdly, the resin can be given absolutely any shade, which is especially important in dentistry. For example, Formlabs has BioMed Clear Resin, which has a high degree of transparency, which may be required to produce parts that show internal anatomy.
4
3D printing will eliminate organ transplants
When organ transplants are needed, patients may face the same problem as when creating a prosthesis: the supply of suitable biomaterials is extremely limited, and the cost of transplantation is very high. In addition, the body may not accept a new organ, in which case the efforts to find a donor and prepare the patient for surgery will go down the drain. Theoretical medicine proposes to create the necessary organs on order, literally printing them on the basis of the patient's biomaterial.
Experts describe the use of bioink, a special material and a kind of raw material for medical 3D printers. Bio-ink is created using tissue engineering techniques based on samples received from the patient. Doctors take a part of the patient's tissue and place it in a bioreactor, where, with the help of nutrients, the material acquires the mechanical and biological properties of organic tissue. Bioengineers can direct cell growth in such a way that the desired tissue or organ type is obtained as a result. The probability that the resulting organ will take root in the patient's body is extremely high. Also, scientists from around the world offer to grow organs in the body of animals. According to Genotek CEO Valery Ilyinsky, such technologies will become a reality in five to ten years. However, the production of individual kidneys, liver or heart based on the patient's biomaterial still seems to be a more reliable way to replace a damaged organ - due to the maximum compatibility of the printed organ and the patient's body.