Abs filament for 3d printer
3D Printing ABS Filament - Gizmo Dorks
Gizmo Dorks
$20.95
Size *
1.75mm 3mm (2.85mm)
Color *
Pick one...BeigeBlackBlueBrownColor Change Blue to White (Heat Activated)Color Change Green to Yellow (Heat Activated)Color Change Grey to White (Heat Activated)Color Change Purple to Pink (Heat Activated)Conductive BlackDark BlueDark PurpleFluorescent Blue (Black Light Reactive)Fluorescent Green (Black Light Reactive)Fluorescent Hot Pink (Black Light Reactive)Fluorescent Orange (Black Light Reactive)Fluorescent Yellow (Black Light Reactive)Glow in the DarkGoldGreenGreyGrass GreenOrangePinkPink RosePurpleRedRed LavaSilverTransparentVioletWhiteYellowLight Yellow
Qty:
Share:
Add to Wishlist
Current stock: 0
ABS Filament
ABS (Acrylonitrile Butadiene Styrene) plastic filament is a polymer used in 3D printing because it can be molded and engineered. It falls under a family of other plastics known as thermoplastics. These plastics have the ability to become soft and moldable when heated at high temperatures and returning to it's normal solid state when at cooler temperatures, making it an ideal 3D printing filament.
ABS filament is a favorite for 3D printing because it is light weight and durable. It can be injection molded which makes it perfect for 3D printing extruders. It has a high glass transition temperature to reduce deformation but low enough to be safely attainable with 3D printers. ABS filament needs to be printed on a heated bed because the filament will curl upwards of the surface. The heated build platform as well as a smooth flat surface helps reduce the deformation.
ABS filament is a hard strong plastic with some flexibility when compared to PLA filament. It is also soluble in acetone, and it can be easily sanded and machined. It has ideal strength, machinability, and temperature resistance making it a favorite filament among 3D printer users.
Please store ABS filament in a cool dry place. ABS, if exposed to moisture, will bubble and spurt from the extruding nozzle. ABS filament can be dried from a food dehydrator, oven, or from any source of hot air.
ABS Filament Specifications
- **Net weight: 1 kg or 2.2 lbs
- Diameter: +/- 0.05mm
- Roundness: +/- 0.07mm
- Print Temperature: 230 - 250°C
- Heated Bed Temp: 110°C
ABS Filament Colors Types and Sizes
We have 21 normal colors of ABS filament and an additional 9 specialty colors. All 30 color variants come in two sizes.
- 1.75mm ABS filament
- 3mm (2.85mm) ABS filament
The 9 specialty colors of ABS filament can be categorized into the 4 following types.
Conductive ABS filament
Right now there is one color for conductive ABS filament, which is black. The filament can be used for anti-static, dissipative, or the conduction of electric current. Sizes come in 1.75mm ABS and 3mm ABS.
Glow in the dark ABS filament
As the name implies, the glow in the dark ABS filament will shine in the dark. Please allow the filament or print to retain light or charge in regular light first. Currently, we have one color for glow in the dark, which is green. We experimented with glow in the dark blue, but the blue version did not glow brightly. Sizes come in 1.75mm ABS and 3mm ABS.
Fluorescent ABS filament
The fluorescent ABS filament colors will glow under UV light, which is also known as black light. We have four fluorescent colors, which are fluorescent orange, fluorescent green, fluorescent yellow, and fluorescent blue. We did have a fifth fluorescent color which was fluorescent red, but it did not shine brightly under UV light. We renamed fluorescent red to red ruby. Sizes come in 1.75mm ABS and 3mm ABS.
Color change by heat ABS filament
This type of ABS filament (hyper color) will change colors depending on the temperature of the filament. The ABS filaments change color at approximately 31°C (88°F). Below 31°C the filaments are one color; above 31°C the filaments are a different color. Therefore, this ABS filament is heat activated. The easiest way to visualize this change is to simply blow a hair dryer on the filament. We currently have three variants of this type of ABS filament, which are green to yellow, gray to white, and purple to pink. Please see the below video for illustration of the color changing effect. Sizes come in 1.75mm ABS and 3mm ABS.
- Videos
Videos
account Account wishlist Wishlist cart Shopping bagPLA vs.
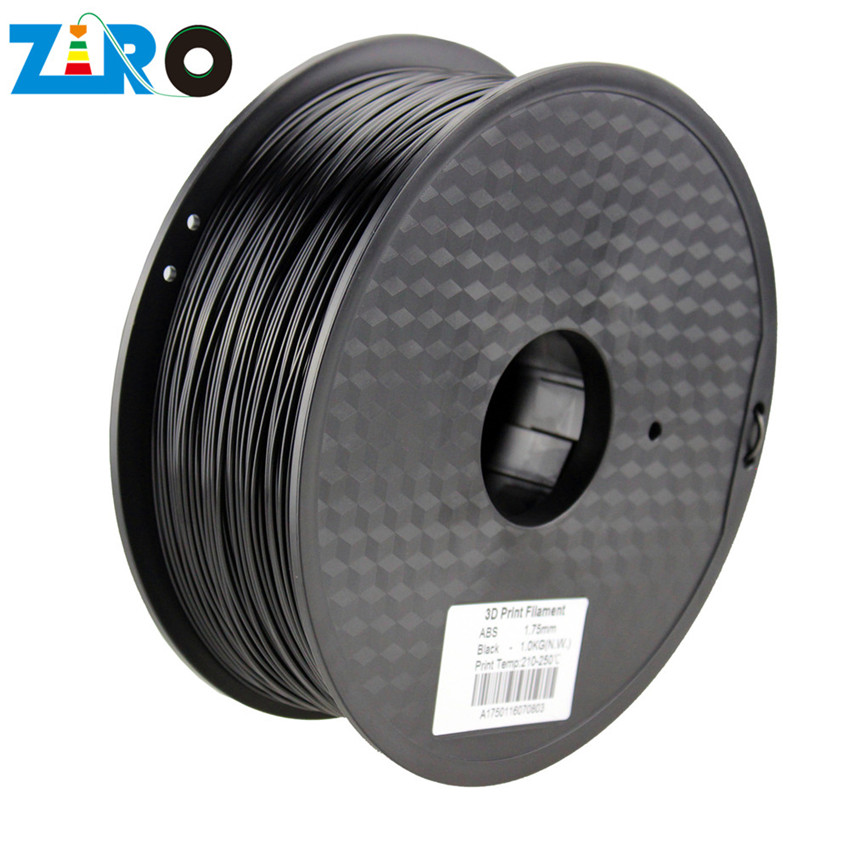
PLA and ABS filaments are the most commonly used ones out there.
But which one should you pick? And are there other filament options for your application?
The power of 3D printing is the ability to produce impossible designs that lead to enhanced functionality and performance. While it’s important to evaluate different technologies and processes, never underestimate material selection and capabilities.
With so many different 3D printing options in the marketplace and countless material options available, what makes the most sense for you? In this post we will compare several FDM materials and how these thermoplastics can be augmented to service a wider range of manufacturing applications. PLA vs. ABS, ASA, PLX, PRO HT, HI-TEMP, Carbon Fiber, Bio-ABS, and more.
ABS Filament
The most commonly used 3D printing material is ABS (Acrylonitrile Butadiene Styrene). ABS variations are used in every industry imaginable (transportation, consumer products, electronics, etc.). For example, plastic components make up 50 percent of a vehicle’s volume, but only about 10 percent of its weight. Therefore, prototypers, product developers, and production engineers feel comfortable printing materials that mimic the end-use product or purpose. 3D printing with ABS is an acceptable and easy solution for many manufacturers.
- Excellent mechanical strength and durability properties
- Cost effective & recyclable
- Better heat performance compared to PLA
- Great for 3D printing prototypes that require multiple iterations or low volume production requests
PLA Filament & PLX
Second only to ABS, PLA (Polylactic Acid) is a highly preferred 3D printing material because it is inexpensive, easy to use, and accessible on many platforms. Compared to ABS, PLA has slightly better tensile strength properties but generally doesn’t have enough flex strength. Both materials are comparable when it comes to pricing. However, under the right conditions, PLA is biodegradable and oftentimes used for food and packaging products making it rather attractive for many consumer product industries. In many instances, PLA is the preferred material choice. PLX, a PLA derivative, was recently introduced by BigRep and available on all platforms. PLX prints up to 80% faster and produces excellent surface features, eliminating the need for post processing.
- Biodegradable
- Up to 80% faster extrusion throughput
- Tensile strength (ISO 527) | 48 MPa
- Key industries: Consumer products, food packaging, prototyping, form, fit, and function
ASA Filament
ASA (Acrylonitrile Styrene Acrylate) is an ABS alternative material with improved weather resistance properties that make it ideal for many outdoor applications. Compared to ABS, ASA has better mechanical properties, superior aesthetics, and it’s UV resistant. Printing with ASA is advantageous for industrial and end-use parts, oftentimes used for automotive, sporting goods, and consumer appliances. The downside is that ASA is slightly more expensive than ABS and produces toxic smoke when burned. Many UAV (unmanned aerial vehicle) developers will prototype with ASA material and even consider using it in the final product due to its UV stability and weather resistance.
- Enhanced UV stability
- Ideal for outdoor applications
- Improved aesthetics compared to ABS and PLA
- Key industries: Consumer products, defense applications, automotive, and aviation
PRO HT: High Temperature Filament
PRO HT, BigRep’s flagship material, is the most popular filament amongst BigRep customers and users. With a softening resistance up to 115 °C, it has significant increase in temperature resistance compared to the average PLA, making it ideal for practical, end-use applications. In addition, PRO HT is FDA compliant for food safety and meets all requirements of EU Directives for food contact. Derived from organic compounds, PRO HT is biodegradable under the correct conditions and has a much lower ecological impact than other plastics derived from fossil fuels. Most common applications include consumer products, packaging, general prototyping, manufacturing and low production tooling.
- Simple to print and easy post processing
- Low warping and shrinkage
- Biodegradable
- Heat deflection temperature up to 115 °C
HI-TEMP CF: Carbon Fiber Filament
Carbon fiber materials are unique and fairly new to the 3D printing industry. Highly stiff and incredibly durable, HI-TEMP CF has a heat deflection temperature of up to 115 °C and is perfect for many tooling applications. For example, thermoforming, pattern and mold making will use HI-TEMP CF for class A surface finish and low moisture absorption.
Compared to many other thermoplastics, the carbon fiber attributes provide significant strength capabilities (>65 MPa) and is recommended as a superior alternative to ASA for functional prototyping or production. HI-TEMP CF is robust and resilient to withstand harsh manufacturing environments.
- Jigs, Fixtures, and Tooling
- Automotive prototyping and production
- Assembly line, manufacturing, and production
- Tensile strength (ISO 527) | 65 MPa
Positioning jig for car production 3D printed with HI-TEMP CF
Conclusion
How to truly maximize the right filament for your application? When it comes to general prototyping, all of these materials can be considered and will most likely yield positive results for your product development. However, prototyping goes beyond just form, fit and function so we recommend taking a deeper dive into specific material characteristics to determine which makes the most sense for you. When it comes to production, it’s very important to consider the mechanical properties of your chosen material and how it will perform. Tooling or end-use products are required to meet certain standards and more often than not, sacrifices cannot be made.
To simplify, we recommend:
- PLA and ABS for simple prototype development.
- If you own BigRep 3D printer equipment, reach out to us to learn about PLX and the time savings it can provide.
- If you’re looking for UV stability or slightly better strength performance for prototyping or production, we recommend ASA.
- Finally, PRO HT and HI-TEMP CF are the most robust materials for low volume production, tooling or any other application that requires parts to perform in harsh environments.
Check out our wide range of 3D printing filaments and find the right material for your application:
Filaments
About the author:
Dominik Stürzer
SEO Manager
Dominik is a mechanical engineer whose passion to share knowledge turned him to content creation. His first 3D prints started in university. Back then the 3D printers were big on the outside and small on the inside. With BigRep the machines are finally big in their possibilities.
Making ABS filament at home
Consumables
All good. It so happened that I got a 3D printer. Having indulged in it, I realized that it is difficult or very expensive to find ABS threads for it in our area. In some places there is 1.75mm at an exorbitant price, 3mm is nowhere to be found. After looking at an article by Lyman about his extruder, I decided to do something similar. Ordered with a bag of granules. While he was walking, he built an apparatus from the remnants of the plastic that was bundled with the printer)))) since China is nearby. Thermocouple, heater, motor drivers were delivered in about a week. I made a screw pair from 2 parts. The hot part was ordered from local turners, who turned it for me from a single piece of iron in a couple of hours. Thermal insert made of fiberglass. The so-called part was printed from the remnants of former luxury. An ordinary wood drill, a pair of simple bearings, one thrust. Puffed for several days. In the end, here's what happened.
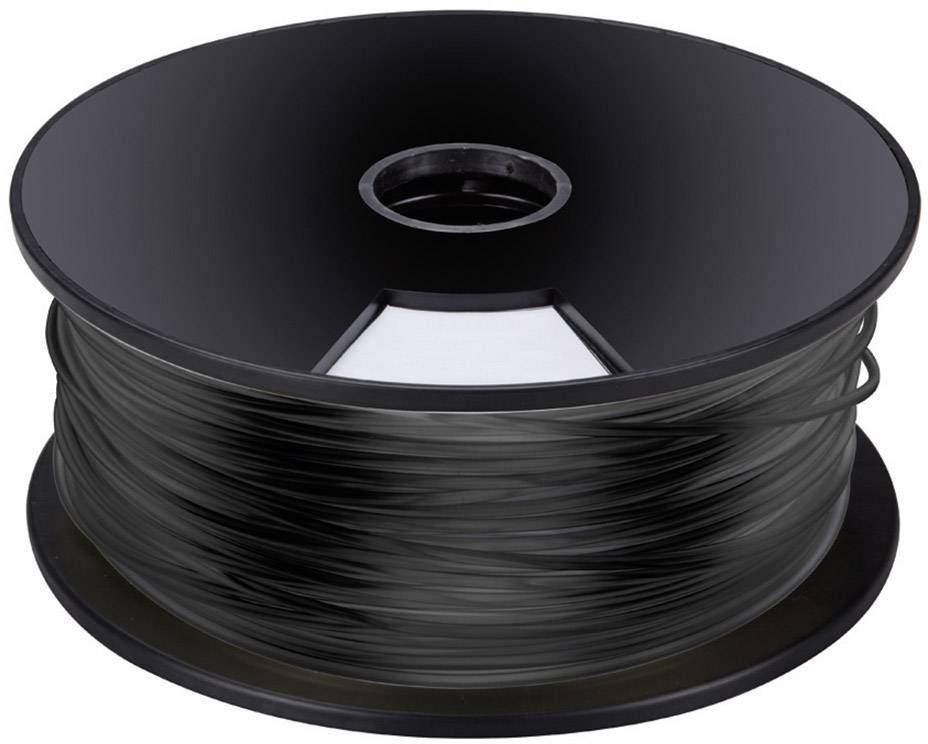
If you have any questions or suggestions, please contact us.
The device is still being perfected.
Plans to make motor cooling, because. during prolonged operation, it warms up to 100-120 degrees. The gears in the gearbox are plastic, I'm afraid that they won't last long at this temperature.
automatic winding, because it is very difficult to manually wind about 500 meters of rod onto a spool.
Yes, and I would like to remake the 'cold' part of the screw pair a bit, it turned out to be a bit unsuccessful.
PS: I don't like to write a lot of text and I don't know how, so don't kick me too hard.
control unit, so to speak. thermocouple enable button, auger motor enable button, and auger rotation control or filament thickness control.
Automatic pellet feeding system... LoL holds exactly 1 kg of plastic
The device itself . ...
is the 'inspirer' for the creation of the extruder
is a piece of the legend of the Japanese car industry))))0035 Nissan Skyline (R 33 )
Finished product!!! The upper coil, I already got sick of winding a coil to coil and wound it how to wind
Follow author
Follow
Don't want
53
More interesting articles
27
Subscribe to the author
Subscribe
Don't want
Buttermilk for a catapult, or shaggy carbon
My next print research visit...
Read more
four
Subscribe to the author
Subscribe
Don't want
About two weeks ago I received new items - three-color PLA plastic from Eryone. ...
Read more Loading
05/03/2017
16365
97
Subscribe to the author
Subscribe
Don't want to
There was a need to bring all the well-known domestic manufacturers of consumables into a table....
Read more
ABS plastic, ABS + for 3D printing. Advantages, disadvantages, alternatives
ABS. Introduction
You are most likely familiar with ABS because it is the most commonly used plastic. Today you can find it everywhere. ABS plastic is used to make bicycle helmets, LEGO bricks, piping systems, musical instruments, carpentry, household appliances, keyboards, toys, canoes, medical equipment, and even flat-screen TVs and monitors. ABS plastic (Acrylonitrile Butadiene Styrene) for 3D printing, it is mainly made in the form of threads wound on a spool. Standard diameters of plastic threads are 1. 75 mm and 2.85-3.0 mm. The average permissible deviation is in the range of 0.05-0.1 mm. In this form, plastic is very convenient to use on modern desktop 3D printers.
ABS is one of the world's most popular 3D printing materials because it is strong enough and relatively easy to print. It can be used to make functional 3D printed parts and prototypes. ABS printed parts can be sanded or smoothed with acetone. Advanced users have found that the visible layer aliasing created by 3D printing with ABS plastic can be significantly reduced by exposing the finished part to acetone vapor. This method allows users to achieve smooth glossy ABS prototypes. Also, under the influence of acetone vapor, some of the finished parts of the model can be combined. The glass transition temperature (the temperature at which the plastic begins to soften) ABS is 105 ºC. Therefore, when developing a prototype part, it is necessary to take into account the operating temperature of the finished product. If the part is used at temperatures above 105 ºC, ABS plastic will soften and deform. Due to its natural characteristics, ABS filament has a uniform structure, which makes it easy to melt in the extruder without clogging the nozzle. However, once it exits the extruder, it shrinks as it cools. The shrinkage of ABS plastic can cause the layers to crack or split as the height of the object increases. It is for this reason that a heated platform is a prerequisite. It is also preferable that the room is maintained at a constant temperature, and there are no drafts, which can accelerate the cooling and, consequently, the deformation of the material.
ABS. Benefits for 3D printing
- ABS is a fairly strong plastic when printed under certain conditions to obtain good layer adhesion.
- ABS is flexible enough that under pressure it bends rather than cracks.
- ABS is heat resistant and impact resistant, making it suitable for car accessories and phone cases.
- The mechanical strength and toughness of ABS allow it to be used in many industries. It is excellent for use at high temperatures, in conditions of increased damage to parts of spare parts and other adverse conditions. At the same time, ABS plastic can print toys, wedding rings, office sets, phone cases, knife handles, all kinds of household appliances and much more. In general, ABS is an ideal material for most objects.
ABS. Disadvantages for 3D Printing
Whatever advantages ABS plastic has, you still need to consider some disadvantages when 3D printing ABS plastic.
Temperature control. ABS 3D printing must be cooled very slowly, otherwise the product may crack or delaminate. If your 3D printer is equipped with a closed case, the chance of getting a perfect print is greatly increased.
General problems. Curl and warp are also a common problem when 3D printing ABS plastic. This is especially true for tall objects.
Sunshine. Exposing your object to direct sunlight can also cause damage, so PET (PETG) may be more appropriate for some outdoor parts.
Odor. ABS plastic emits an unpleasant odor when heated. Therefore, when 3D printing ABS plastic, you should take care of the hood or organize remote control.
If you have any difficulties with 3D printing with ABS plastic, you can order 3D printing on the 3D4U website.
ABS. Disposal
ABS filament is not made from renewable sources and is not biodegradable. Theoretically, 3D prints can be recycled, but you use a lot of energy and a lot of waste. If you are an environmentalist, think twice before recycling ABS filament.
ABS plastic is non-toxic for 3D printing. Only at very high temperatures (400 °C) does the material decompose into butadiene (it is carcinogenic to humans), acrylonitrile (also a potential carcinogen) and styrene.
ABS products are not safe to use with food, especially warm or hot.
ABS. What are the alternatives?
PLA is a good alternative to ABS filament. It is made from a biopolymer (such as corn or sugar cane), is easy to print, and is made with all sorts of composites. For example, metal powders (steel, copper, bronze), wood, sand, coffee, and even hemp are added to PLA.
PET and PETG are also considered suitable alternatives to ABS. It is not hydrophobic, does not curl or warp as it cools, and is much more durable than ABS. You are most likely familiar with this material. It is made from plastic bottles.
ABS. Price
The price for 1 kg ranges from $14 to $60. This price range is due to the quality of the 3D printing filament. Buying ABS plastic at lower prices, you endanger your health, as well as the quality and durability of the final product. Manufacturers of high-quality ABS filament strictly follow the standards for the chemical composition of the filament, its geometric dimensions and smooth winding on the bobbin.
On the 3D4U website you can buy premium quality ABS plastic from the global brand Verbatim, as well as ABS+ plastic from the Polish manufacturer Devil Design. The cost for 1 kg of net fluctuates between $ 23-33.
ABS. Correct settings for 3D printing?
Beginners may have a significant problem finding the right settings for ABS 3D printing. There are no identical coils and the characteristics of plastics, even from one manufacturer, may differ.
Make sure you meet the following basic conditions:
Close the 3D printer. ABS glass transition temperature 105°C. If you maintain a temperature of 105 ± 15 °C inside the 3D printer chamber during the 3D printing process, you will get a high-quality and durable product without cracking and delamination.
Use a heated platform (bed). Set the temperature to about 110 °C. Additionally, 3D Printing Lacquer (3DLac) or Kapton will help you increase adhesion. If the product still comes off - use a raft (raft).
Experiment with temperature. Set the nozzle temperature to 230°C and start your journey from there.
If at this temperature you see a lot of thin plastic threads between the elements of your project, and the plastic flows out - lower the temperature by 5 °C
If the plastic comes off, the parts are not strong, and the surface is rough, increase the temperature by 5 °C.
ABS. What colors are available?
Great news - the choice of colors is quite large. In the 3D4U store, ABS plastic is available in a wide range of colors (25+ shades), including translucent options.
ABS. How to store it correctly?
ABS must be stored in a dry, covered area with a desiccant because the plastic absorbs moisture from the air, making it difficult or even impossible to reuse the spool for 3D printing. If your ABS spool gets wet, you can even hear it during the printing process. Wet ABS loses its mechanical properties and becomes brittle and brittle.