3D scanner for small parts
Your Guide to Choosing the Best 3D Scanner for Small Objects
Small components present particular challenges for measurement. Certain aspects of small parts contributing to these challenges include the fine level of detail required, the scale of dimensions and crevices between features, and the difficulty in setting up and positioning small objects.
If you'd like to skip to a specific section, click the section below to jump straight to it:
- Examples of Small Objects for 3D Scanning
- Budget vs. Functionality for 3D Scanners
- 3D Scanner Resolution & Quality
- 3D Scanning Versatility
- Scanning Sensor Repeatability & Precision
- 3D Scanning Ergonomics and Automation
- Handheld 3D Scanning
- Stationary Supports for 3D Scanners
- Semi and Full-Automation 3D Scanning
- Measuring Volume Options for 3D Scanners
Non-contact 3D scanning helps overcome these challenges by collecting complete measurement data, also known as full-field measurement data. Due to the ability to capture intricate details, 3D scanning is often used with smaller components such as:
• Mechanical components: often, in industrial settings, the ability to 3D scan objects gives a detailed, in-line measure of conformance to drawings and quality standards
• Jewelry: used in production, evaluation, modifications and repair
• Medical devices: due to their sensitive nature and small features, many medical devices make use of non-contact measurement and analysis in manufacturing and quality control settings
• Injection molded parts: these small, complex parts have tight tolerances, requiring the precise, accurate measurement results a metrology-grade 3D scanner delivers
While using a 3D scanner for small objects is a great way to capture fine details, not all 3D scanners are a good fit for this application. Sourcing the right 3D scanner for your purposes can be tricky, given the factors that must be considered when scanning smaller objects. In this article, we'll look at:
1. Budget & Quality Considerations
2. Handheld vs. Stationary vs. Automatic Scanners
3. Measuring Volume
Choosing the right budget for your 3D scanner is a key consideration. Inexpensive 3D scanners may work for hobbyists, but for applications requiring high data accuracy, it's crucial to invest in a high-quality 3D scanner to meet your requirements. There are specific factors that you should consider when choosing between a basic or high-quality 3D scanner.
Resolution & Quality
When selecting a 3D scanner, the first consideration is deciding the required level of detail you need to achieve based on the purpose of your scans.
• Low level: Maybe you just need a quick digital scan to create an image of an object for reference or presentation, and the details of the surfaces are not important. Capturing shapes, outlines and some rough dimensional measurements is the goal.
• Medium level: In many cases, the outline geometry plus dimensional accuracy will be enough to produce results for basic applications. Medium level resolution and quality allow some sizing and analysis and reveal defects at the edges of gross defects in a product.
• High level: Imperfections in surfaces and coating must be spotted and measured for metrology and quality control. The dimensional measurements are not only for outlining but must be precise and repeatable. Of course, this higher level of detail guides towards a different level of data quality than lower resolution 3D scanners.
Your specific application will dictate your requirements, with the level of detail and accuracy required having the most significant bearing on the cost of the system.
Versatility
Different scanners offer different levels of versatility in terms of applications, features, configurations, shapes, sizes and colors.
• Features: Budget scanners are great when you are just testing the water with 3D scanning. Handheld 3D scanners can be taken anywhere and offer a high degree of versatility and different applications. Higher-quality 3D scanners can be customized with automation to suit your application and increase throughput.
• Shapes and sizes: Many budget scanners can handle the basic scanning of large-scale objects such as construction connections, people or body parts, and large automotive components such as engine blocks. But they struggle with the smallest of objects in many instances. High-resolution stationary or automated 3D scanners are suitable for the smallest of objects with a high degree of customization on detailed sections, features, and measurements critical to quality control.
• Color and surface type: Many low-end 3D scanning systems will struggle with shiny or translucent materials. Some 3D scanners require sprays, spots or other identifiers added to the surface of an object, but a high-quality 3D scanner captures precise details without having to modify the surface. The ability to capture data from challenging surfaces is especially important for high-value components, where modifications or witness marks on surfaces are out of the question (such as jewelry or medical components).
ATOS Q offers the industry-leading standard for versatility and precision. This blue light 3D scanner captures high-definition, accurate and reliable data from objects of all sizes. Ideal for engineering, R&D and manufacturing, the ATOS Q is lightweight and portable (weighing only 4kg) and can be configured for manual or automated use.
Repeatability & Precision
The data quality your 3D scanner captures is impacted by how easily it is influenced by environmental disturbances during data acquisition. One example of an environmental disturbance that affects the quality of your measurement results comes from vibrations through the platform (or surface) upon which the component or 3D scanner is placed. A higher level of specification in your 3D scanner helps to reduce the vibration but also makes it more capable of filtering out disturbances.
Budget devices can be useful for taking quick, partial scans of surfaces and shapes for contour analysis. In many quality control applications, the measurement process itself must be calibrated (or validated) and cannot vary, so an automated or semi-automated process of positioning and scanning is necessary. Where repeatability is required, the external vibrations and variations will require clamping in place, with precise, repeatable paths and movements of the 3D scanner.
GOM Scan 1 utilizes a stereo camera principle, allowing the sensor to recognize vibrations or disturbances during scanning. The 3D scanner compensates for the variation during scanning to produce a consistent result, regardless of the environment.
Choosing Stationary vs. Automated vs. Handheld for Small Objects
The type of positioning and support of the object you are trying to measure greatly affects the results your 3D scanner collects. There are three basic types of 3D scanning configurations to choose from:
1. Handheld
2. Stationary
3. Automation/Semi-automation
Handheld
Handheld scanners are great for objects like people and their features, cars and automotive components. Low-quality handheld scanners are notorious for losing their position during a scan (especially going around a corner). This issue results in the user having to stitch two scans together or restart the entire scan again.
High-quality handheld 3D scanners produce metrology-grade inspection data with no custom setups or platforms required for the object. The ZEISS T-SCAN hawk is an excellent example of a precision handheld scanner that can be taken anywhere and can switch between scanning modes at the touch of a button. This handheld 3D scanner also rapidly feeds your measurement data into GOM Software for analysis. Handheld scanners are the most portable 3D scanning option available. These can be easily taken outside for fieldwork in the open air. They are relatively easy to transport in a bag or case (compared to some larger and more built-in solutions).
Stationary
Stationary 3D scanners hold the scanner in position, and the object rotates in front of it using a turn table. This setup can be more repeatable than scans from handheld scanners, as the object's movement is in one plane (rotation around a central axis), which leads to fewer opportunities for error.
Scans produced from stationary scanners are usually far superior to handheld scanners due to the control of the movement, resulting in finer details and higher resolution. Stationary scanners are larger than handheld units but are more portable than automated systems.
GOM Scan 1 is excellent for use as a stationary scanner. This highly portable 3D scanner is lightweight and provides industry-leading precision. Highly suitable for many small and medium-sized applications, GOM Scan 1 is a reliable tool for reverse engineering, quality control, research, art, 3D printing and more.
Automated and Semi-Automated
When using an automated 3D scanner, the object is held in place, and the relative movement of the scanner or the object (or both) is controlled by the system itself. The object can be passed in front of the scanner at different angles using different paths to precisely control the speed and motion. This highly repeatable process can be finely tuned for precise details on small components. This advantage is especially important for quality control environments where repeated measurements are compared over time for drift or changes from a baseline. These units generally take up more space than handheld or stationary scanners and aren't meant to be used as a portable solution. Automated 3D scanners are usually larger and require more preparation for moving or transporting to new locations due to their size and layout. Semi-automated systems work similarly to automated systems, but the scanning or the rotation is somewhat manual, requiring the user to rotate the platform or otherwise interact with the system to create a scan.
Measuring volume is an important factor when considering the best scanner for your application. Point clouds are the collection of individual points in space captured during a scan. These points in space are the boundaries of the object and its surface. The 3D scanning software uses these points to render the object's surface and create the digitized representation of the object that we see in the finished scan image.
Resolution is the distance between two points, with a lower distance between points giving richer detail in the end result. A greater number of points collected (a higher measuring volume) leads to higher resolution data. A high measuring volume and resolution are especially important when dealing with smaller objects because the ratio of the part's dimensions to the distance between the measurement point is much closer.
Higher measuring volume leads to more detailed data capture but also leads to large file sizes and slower rendering times. This problem is resolved when working with an advanced 3D metrology software solution such as GOM Software.
At the highest end of industry performance, ATOS 5 offers point-spacing down to 0.0236mm (the distance between two points on a scan). A single pass of this scanner captures up to 12 million measurement data points in as fast as 0.2 seconds per scan.
Find the Best 3D Scanner for the Small Objects You Work With
Contact a CAPTURE 3D team member to help you find the best 3D scanner for the small objects you work with. CAPTURE 3D carries various 3D scanners for small objects to fit your specific application. Schedule a demo of our accurate 3D scanning solutions or get a proof-of-concept to understand the benefits our technology brings to your components.
Desktop 3D Scanner for small objects
Scanner type | Desktop | Handheld | Handheld | Handheld | Handheld |
3D point accuracy, up to | 0.01 mm | 0.05 mm | 0.1 mm | 0.1 mm | 0.1 mm |
3D resolution, up to | 0.![]() | 0.1 mm | 0.2 mm | 0.5 mm | 0.2 mm |
3D accuracy over distance, up to | — | 0.05 mm + 0.3 mm/m | 0.1 mm + 0.3 mm/m | 0.1 mm + 0.3 mm/m | 0.1 mm + 0.3 mm/m |
HD Mode | N/A | N/A | Yes | No | Yes |
Hybrid geometry and texture tracking | N/A | Yes | Yes | No | Yes |
Data processing algorithms | Geometry based | Geometry and texture based | Geometry and texture based | Geometry based | Geometry and texture based |
Working distance | — | 0.2 – 0.3 m | 0.4 – 1 m | 0.4 – 1 m | 0.35 – 1.2 m |
Volume capture zone | 324 cm³ | 2,000 cm³ | 61,000 cm³ | 61,000 cm³ | 160,000 cm³ |
Ability to capture texture | Yes | Yes | Yes | No | Yes |
Texture resolution | 6.![]() | 1.3 mp | 1.3 mp | — | 2.3 mp |
Colors | 24 bpp | 24 bpp | 24 bpp | — | 24 bpp |
3D reconstruction rate for real-time fusion, up to | — | 7.5 fps | 16 fps | 16 fps | 22 fps |
3D reconstruction rate for 3D video recording, up to | — | 7.5 fps | 16 fps | 16 fps | 44 fps |
3D reconstruction rate for 3D video streaming, up to | — | — | — | — | 80 fps |
Data acquisition speed, up to | 1 mln points/s | 1 mln points/s | 18 mln points/s | 2 mln points/s | 35 mln points/s |
3D exposure time | Customizable | 0.0002 s | 0.0002 s | 0.0002 s | 0.0002 s |
2D exposure time | Customizable | 0.0002 s | 0.00035 s | 0.00035 s | 0.0002 s |
3D light source | Blue LED | Blue LED | Flashbulb | Flashbulb | VCSEL |
2D light source | RGB LED | White 6 LED array | White 12 LED array | White 12 LED array | White 12 LED array |
Interface | USB 3.![]() | 1 × USB 2.0, USB 3.0 compatible | 1 × USB 2.0, USB 3.0 compatible | 1 × USB 2.0, USB 3.0 compatible | Wi-Fi, Ethernet, SD card |
Supported OS | Windows 10 x64 | Windows 7, 8 or 10 x64 | Windows 7, 8 or 10 x64 | Windows 7, 8 or 10 x64 | Windows 7, 8, 10 x64 |
Recommended computer requirements | Intel Core i7 or i9, 64+ GB RAM, NVIDIA GPU with at least 3 GB VRAM, CUDA 3.5+ | Intel Core i7 or i9, 32 GB RAM, GPU with 2 GB VRAM | Intel Core i7 or i9, 64+ GB RAM, NVIDIA GPU with 8+ GB VRAM, CUDA 6.0+ | Intel Core i7 or i9, 32 GB RAM, GPU with 2 GB VRAM | Intel Core i7 or i9, 64+ GB RAM, NVIDIA GPU with 8+ GB VRAM, CUDA 6.0+ |
Minimum computer requirements | Intel Core i5, i7 or i9, 32GB RAM, GPU with 2 GB VRAM | Intel Core i5, i7 or i9, 18 GB RAM, GPU with 2 GB VRAM | HD: Intel Core i7 or i9, 32 GB RAM, NVIDIA GPU with CUDA 6.![]() SD: Intel Core i5, i7 or i9, 12 GB RAM, GPU with 2 GB VRAM | Intel Core i5, i7 or i9, 12 GB RAM, GPU with 2 GB VRAM | HD: Intel Core i7 or i9, 32 GB RAM, NVIDIA GPU with CUDA 6.0+ and at least 4 GB VRAM SD: Intel Core i5, i7 or i9, 32 GB RAM, GPU with 2 GB VRAMA computer is needed only for data processing. Scanning does not require a computer. |
3D mesh | OBJ, PLY, WRL, STL, AOP, ASC, PTX, E57, XYZRGB |
CAD | STEP, IGES, X_T |
Measurements | CSV, DXF, XML |
Power source | AC power | AC power or external battery pack | AC power or external battery pack | AC power or external battery pack | Built-in exchangeable battery, optional AC power |
Dimensions, HxDxW | 290 x 290 x 340 mm | 190 × 140 × 130 mm | 262 × 158 × 63 mm | 262 × 158 × 63 mm | 231 × 162 × 230 mm |
Weight | 12 kg / 26.![]() | 0.8 kg / 1.8 lb | 0.9 kg / 2 lb | 0.9 kg / 2 lb | 2.6 kg / 5.7 lb |
review of the peel 2 CAD-S handheld 3D scanner / Sudo Null IT News Compared to its predecessor, the peel 2, the device boasts higher detail when scanning small objects.
Peel 3d is a trademark of Ametek/Creaform. All of the parent company's knowledge and know-how in 3D scanning and reverse engineering has been invested in making peel 3d products more accessible to reach a different target audience.
The peer 2 scanner proved to be very functional and useful in many applications, but it lacked the ability to capture the finer details of objects. Consider the new peel 2 CAD-S model to evaluate the changes that have taken place.
peel 2 CAD-S uses the same structured white backlight technology as the previous model, but with higher resolution and therefore better suited for working with smaller elements. The recommended part size is less than 0. 5 m (for comparison, for peel 2 - from 0.3 to 3 m).
In practice, this means that when using the same sensors and cameras, the scan area is reduced from 380 x 380 mm to 142 x 108 mm. Essentially, you get the same number of pixels in a much smaller space, so peel 2 CAD-S can capture 3D shapes at 0.1mm grid resolution – in other words, five times more accurate than peel 2.
Setup and first use 3D Scanner
The setup process is almost the same as for all other 3D scanners. The whole set comes in a regular case with a foam insert: a scanning device, software and a license key on a USB stick, as well as a switch. The cables are designed for power (from a standard power supply) and data transfer (via Hi-Speed USB 2.0). The installation process is simple: insert the flash drive into your computer, run the installation and follow the suggested steps.
For hardware requirements, you'll need a modern workstation or laptop with an Nvidia GPU and at least 2 GB of VRAM. Processor - the faster the better, but because the system is geared towards small parts, the chances of overloading a modern processor are minimal.
Calibration must be performed after installation. Calibration of this type of device is not difficult, and the general recommendation is that it should be done fairly regularly, especially as the conditions in which the scanner is used change. This may be due to light (for example, moving to another office, to another area of \u200b\u200bthe shop or workshop) or temperature. After the calibration is completed, the device is ready for use.
When the peel 3d software is launched for the first time, the user is presented with two main options. You can follow the help guide that will guide you through the entire 3D scanning process, determining how to capture the object, what resolution and positioning methods to use (geometry, texture, or position labels), and help you with your work. Another option is to do the setup yourself.
First you need to define the scan resolution. The default is 1.0 mm, but values from 0.1 mm to 2.0 mm are possible. The lower the value and the sharper the resolution, the better the scan and the larger the dataset. Given that peel 2 CAD-S is designed for small objects with fine detail, a good GPU can easily handle even 0.1mm resolution.
The next step is to set how the system will track the movement of the 3D scanner around the object. As with other similar devices, there are three options: texture, geometry, and labels. Structured light scanners equipped with texture capture can use the surface texture to track the movement of the scanner/object. peel 2 CAD-S can also use object geometry. Both of these methods work well for organic shapes and textured objects.
Regularly shaped products with uniform surfaces (most often mechanical parts) may require the use of position marks.
These are small, custom-sized reflective markers that can be stuck on or around an object. They are used to determine the position of the scanner in relation to the object using triangulation methods. As long as there are three marks in the field of view of the 3D scanner at the same time, this method usually gives a good result and ensures correct tracking of the scanner.
The peel 2 CAD-S kit includes a set of small plastic jigs with three marks that can be placed around the object for quick adjustment. These devices are very useful considering that the device is focused on digitizing small details with high detail, and sticking several 4mm marks on them is not a very practical solution. The
peel 2 CAD-S is designed to scan physical objects at high resolution and many of its features are based on the proven Creaform 9 designs.0014 Scanning process 3D scanning typically involves collecting as much data as possible in one position. The device is quite light and well balanced, which many competitors' products cannot boast of. The function of determining the distance to the object (ideally 300 mm) with color indication on the screen and on the device itself allows you to scan very quickly.
It is worth noting that the peel 3d software provides a very rough preview. Since the scanner usually collects a huge amount of data, it makes sense to gradually filter it out as you work.
As you get used to the operation of the device and get used to quickly moving the scanner around an object (or quickly rotating a part on a turntable), you will understand how to maintain continuous tracking. At any time, you can take your finger off the shutter, pause the scan and review the data, and then return to digitizing the missing areas.
There are two paths after the initial scan. If there is enough data, then you can start the cleaning process and remove excess data. There are a number of tools available for this and the procedure is quite simple - this is one area where all the investment in Creaform know-how is worth it. Then the meshing and further cleaning is performed.
Otherwise, especially for complex parts, a more thorough rescan may be required. This repeats the same process, resulting in two or more data sets that need to be matched. Once again, Creaform's knowledge and technology comes into play, allowing you to use common dots (you must select three common dots between two or more images) to combine multiple scans.
After the scan (or set of scans) is ready, the next step is to prepare for data post-processing. You may just need to create a mesh, fill holes, and export the data to OBJ or STL format. In this case, the available tools will help smooth surfaces, remove noise and fill in all holes to ensure reliable export.
You may also need to build analytical surfaces from the point/mesh data, either to get a point of reference to reuse the mesh in CAD (surfaces allow you to align and reassemble the model) or to create reference geometry to build a more complete model.
The peel 3d software is not really designed to build a fully sealed solid model. Its purpose is to help build a set of reference surfaces that are consistent with point and grid data. This view of the scanned data can be imported into a full-featured 3D design system and the 3D model can be completed.
Although it may seem a little complicated, in fact, in most cases, other surfaces (such as cylinders, spheres, planes) can be added to the prismatic model almost instantly etc.).
These surfaces and points can then be loaded into CAD. This usually requires two exports: first a mesh data file in STL or OBJ format, then a surface data file in STEP or IGES format (for example). The result should be a set of two types of geometry that can be used to build the required model.
Conclusions
At first glance, the peel 2 3D scanner makes a strong impression. Relatively low price, excellent build quality and, last but not least, reliable and simple software. The main problem was that it is not suitable for those who require higher resolution scans. The
peel 2 CAD-S takes the same approach as its predecessor but focuses (both literally and figuratively) on smaller objects and capturing finer details while maintaining the same ease of use when combined with software by Creform.
The resulting scans are of excellent detail, and by mastering the art of multiple scans, stitching and alignment, as well as the practicalities of working with reflective surfaces, you can achieve impressive results.
peel 2 CAD-S and peel 2 complement each other perfectly, and it makes sense to have both scanners at the workplace. In practice, this option is very common. If you are interested in 3D scanning solutions, the peel 3d line deserves a deeper look.
Source: Develop3d.com
Select 3D scanner: Types, advantages, Tasks for
3D scanners
Fundamentals 3D
Reverse Engineering
Geometry Control
The best according to
Automation Automation Automation quality control
Author: Semyon Popadyuk
Author: Semyon Popadyuk
Benefits of 3D Scanners | What tasks does 3D scanning solve | Criteria for choosing a 3D scanner | Professional 3D scanning for fast and efficient production solutions
Modern 3D scanners have a wide range of features and a variety of functionality. They are used everywhere - in manufacturing, construction, education, the entertainment industry and are used even in everyday life. In order to choose the scanner that suits your needs, there are a number of aspects to consider, which we will discuss in this article.
Order a free test 3D-scan using the equipment of the world's leading manufacturers:
Leave a request
Benefits of 3D Scanners
What is a 3D scanner? This is a device designed to quickly analyze a physical object and create its accurate 3D computer model. The principle of its operation is based on calculating the distance to the object using two cameras. In addition to the cameras, a backlight is used - LED or laser.
3D scanners are classified both according to their form of execution (stationary and portable) and according to the areas of use, mainly divided into professional and household.
3D scanners make it possible to significantly reduce the time and costs at the development stage, improve the quality of products and, ultimately, speed up the release of the product to the market. They can be used at any stage of product lifecycle management and will help to optimize the production process of enterprises in various industries, including:
- automotive,
- mechanical engineering,
- aerospace industry,
- oil and gas industry,
- shipbuilding,
- building and architecture,
- arts and culture,
- medicine,
- jewelry,
- science and education.
3D scanning devices remove many of the limitations of traditional measuring equipment. Such tools familiar to the metrologist as templates, micrometers, calipers are inexpensive, but they are characterized by subjective readings and are not suitable for complex measurements. Coordinate measuring machines are more accurate than 3D scanners, but they are more expensive, larger, and require specialized operator training.
Optical inspection systems, which include 3D scanners, are the best solution in terms of price and quality, as they provide:
- measurement speed,
- high accuracy of digitizing objects of complex geometry,
- can work autonomously,
- are easy to operate.
Thanks to a 3D scanner, the work of a designer, technologist, and constructor is greatly facilitated: the performance of time-consuming complex measurements and the creation of a design from scratch are a thing of the past.
What tasks does 3D scanning solve
- Quality control: the ability to check any geometric parameters, including input and output control, metrological control of parts and production equipment.
- Reverse engineering of products for prompt receipt of project documentation and product upgrades.
- Design and simulation for the purpose of prototyping and evaluation of the appearance of products, modernization of production facilities and equipment.
- Digital archiving of any required assortment (eg discontinued parts). Models stored in digital libraries are available remotely from anywhere in the world.
3D scanner selection criteria
The main criterion is scanning accuracy . High-precision devices (10-30 microns) will help to get a phenomenal result: they are able to transfer the most complex surface geometry into 3D with minimal errors. Such 3D scanners are used in reverse engineering, quality control, medicine, and are used to digitize molds, device parts, etc. 3D scanners with an accuracy of 30–100 engineering.
ZG AtlaScan is the world's first 3D scanner with hole capture
When choosing a 3D scanner, you should also consider resolution (detail) , i. e. the degree of discreteness that is available when digitizing an object. The highest level of detail allows you to display the smallest elements in the 3D model.
Р the size of the scanned objects and, accordingly, the mobility of the 3D scanner directly depend on the type of device that you select. When digitizing parts and objects of small and medium parameters, hand-held scanners are usually used. Stationary scanners are suitable for capturing complex small and medium-sized products with small details. Scanning of large objects (buildings, structures, communications) is performed using ground-based laser devices (range finders).
When studying the functionality of 3D scanners, pay attention to such points as the conditions of use, scanning speed, the surface of the scanned object, and color.
Please note that the next step after scanning is to obtain and further work with the CAD model, and for this you will need specialized software.
Processing 3D Scan Data for Reverse Engineering in Geomagic Design X Software
Professional 3D scanning for fast and efficient production solutions
iQB offers cutting-edge solutions that successfully operate in leading enterprises around the world:
- Portable devices for metrological 3D measurements from ZG Technology (China). The line includes a wide range of instruments, from an affordable handheld 3D scanner to a powerful optical tracking measurement system, as well as photogrammetry and portable CMM. ZG's unique strengths include the world's first handheld MarvelScan solution with three cameras for markless laser scanning and tracker, and proprietary instant hole capture technology. ZG Technology 3D scanners provide measurement speed up to 1 million 350 thousand points per second and accuracy up to 0.01 mm.
- Stationary Russian-made RangeVision PRO 3D optical scanner is an industrial solution for metrology, available to companies of any level.
The device is designed to digitize objects from 1 mm to 5 m and offers the highest level of accuracy (up to 0.018 mm) and 3D resolution (up to 0.04 mm). This is the first domestic 3D scanner approved by the Federal Agency for Technical Regulation and Metrology as a type of measuring instrument.
- Creaform handheld 3D scanners for digitizing products ranging in size from a few centimeters to 6 meters. The Go!SCAN series devices (including the latest Go!SCAN SPARK) are based on structured illumination technology; HandySCAN 3D and MetraSCAN 3D are laser devices that are certified industrial grade metrology tools. The new generation MetraSCAN BLACK|Elite model is the fastest handheld 3D laser scanner on the market (1.8 million measurements per second). The volumetric accuracy that Creaform technology can provide is up to 80 microns per 16 cc.
m.
- Creaform also produces 3D scanners and software under the peel 3d brand, combining affordability, ease of use and high quality. The line is designed to solve the problems of reverse engineering and digitalization of objects in such areas as art, preservation of cultural values, consumer goods, science and education, human body scanning. Peel 3d devices are capable of measuring objects from 0.3 to 3 m with an accuracy of 0.1 mm.
RangeVision PRO Fixed Scanner Creates Yamaha R3 Sport Fairings with Improved Aerodynamics, High Strength and Lighter Weight
- Solutionix fixed optical 3D scanners for small objects (10-500mm) with many small parts. Allow to receive an error less than 8 microns.
- FARO Focus 3D geodetic laser scanners perform fast and accurate scanning of large objects, complex structures, premises and landscapes. They operate in the range from 0.6 to 350 m, they are distinguished by increased accuracy, ease of operation and the ability to operate in the most difficult environmental conditions.
- EPiC budget 3D terrestrial laser scanners are based on the principles of simplicity, convenience and affordability.
Their main advantages are super light weight, high shooting speed (from 30 to 90 seconds), 360-degree panoramic camera and the ability to control from a mobile device.
Many of the above scanners are included in the register of measuring instruments of the Russian Federation and have the appropriate certificates.
Robotic 3D scanning systems, such as Creaform MetraSCAN 3D-R, allow you to increase the speed and efficiency of quality control directly on the conveyor
A variety of 3D scanning devices on the market will allow you to choose exactly the model that is needed for solving specific problems. The price range is also wide: from simple devices costing up to $500 to high-precision professional 3D scanners costing tens and even hundreds of thousands of dollars.
Contact iQB Technologies experts! We will select the optimal solution that will optimize product development and production in your enterprise, design office or research center.
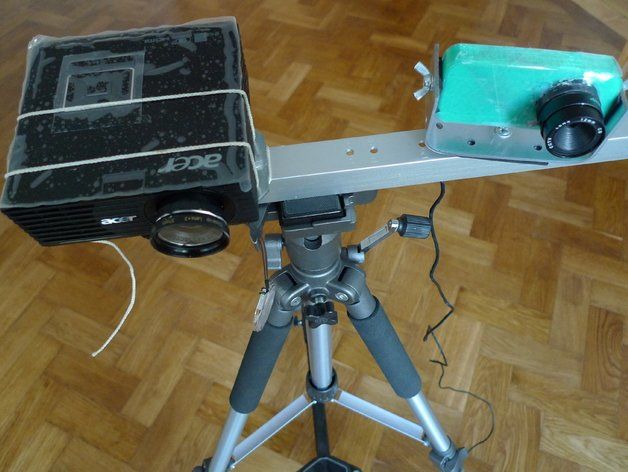