3D printing wiki
3D printing - Wiki | Golden
3D printing, also known as additive manufacturing or additive layer manufacturing, is the construction of a three-dimensional object from a digital 3D model. The name additive manufacturing comes from the differentiation of 3D printing, which adds material layers upon each other to build an object, from the more traditional process of subtractive manufacturing, which removes material through milling, machining, carving, and shaping to create an object.
Traditionally, subtractive manufacturing has been used for high production volume manufacturing, while additive manufacturing has been reserved for prototyping and rapid tooling. However, the increased cost-effectiveness of additive manufacturing, the reduction of material waste, and the increased mainstream adoption of 3D printing systems has increased the use of additive manufacturing systems. These, along with the increased precision, repeatability, and material range of 3D printing, have increased the use of the technology for higher volume production.
In the case of most 3D printers, a user creates a design using computer aided design software or by scanning an object to print. Software translates the design into the printed layers and framework for the machine to follow. The plan is sent to the printer, which begins creating the object. The materials capable of being printed include polymers, metals, ceramics, foams, gels, and biomaterials.
Processes
Material extrusion
Material extrusion printing, or fused filament fabrication, also known by the trademarked term "fused deposition modeling," is a 3D printing process using a continuous filament of a thermoplastic material. Through this method, filament is fed through a moving, heated printer extruder head and deposited on a growing work. Printers using this method use a computer to control the printed shape. And printers of this type layer the printed object one horizontal layer at a time before making a small vertical move to start the next layer. The extruder head speed can be controlled to start and stop deposition in order to form an interrupted plane without stringing or dribbling between sections. Fused filament fabrication is the more popular printing process (by number of machines) for hobbyist-grade 3D printing.
The fused deposition modeling technique was developed by S. Scott Crump, the co-founder of Stratasys, in 1988. The patent on the technology expired in 2009 and presented the beginning of people using the type of printing without paying rights to Stratasys. This allowed commercial, hobbyist, and open-source 3D printer applications to grow.
The materials capable of being extruded by fused filament fabrication machines include thermoplastics, such as acrylonitrile butadiene styrene (ABS), polylactic acid (PLA), high-impact polystyrene (HIPS), thermoplastic polyurethane (TPU), and aliphatic polyamides (nylon).
Stereolithography (SLA)
Stereolithography (SLA), also known as optical fabrication, photo-solidification, VAT photopolymerisation, or resin printing, is a 3D printing technology that prints parts in a layer-by-layer fashion using photochemical processes. SLA uses light to cause chemical monomers and oligomers to cross-link and form polymers that, in turn, make the body of a three-dimensional solid. The process is fast and can produce almost any design, but can be cost prohibitive. The main fields of application include products in development, medical models, and computer hardware.
The materials used in SLA printing are referred to as resins and are thermoset polymers. These resin materials can be soft or hard, filled with secondary materials such as glass and ceramic, or imbued with mechanical properties such as heat deflection or impact resistance. In the post-process of SLA manufacturing, parts need to be removed from a support structure, and alcohol and water rinses are used to remove excess resin. At times, post processing can include scrubbing to remove additional material, and some processes use ultraviolet light for a post-cure process.
Stereolithography was first developed in the early 1980s by Hideo Kodama, who used ultraviolet light to cure photosensitive polymers. French inventors Alain Le Mehaute, Oliver de Witte, and Jean Claude Andre filed an early patent for technology that was later abandoned. The final patent, which gave the process the name "stereolithography," was filed by Chuck Hull in 1984 and granted in 1986. Chuck Hull later founded 3D Systems to commercialize the patented technology.
Powder bed fusion
The powder bed fusion manufacturing process includes the printing techniques of direct metal laser sintering, electron beam melting, selective heat sintering (SLS), selective heat sintering, and selective laser melting (SLM). All methods use either a laser or an electron beam to melt and fuse material powder together. The methods involve spreading the powder material over previous layers, using either a roller or a blade while a hopper or reservoir provides fresh material supply. In all methods, a layer, typically 0.1 millimeters thick, of material is built over the platform and the laser or electron beam fuses new material in layers or cross-sections. Materials capable of being used in powder bed fusion manufacturing processes include nylon, stainless steel, titanium, aluminum, cobalt chrome, steel, and copper.
In direct metal laser sintering, metal powders are sintered layer by layer with a range of metals available.
In electron beam melting (EBM), layers are fused using an electron beam to melt metal powders. In the EBM process, a vacuum is required with a pressure of 1×10-5 mba, and electromagnetic coils are used to control the beam. The EBM process also produces better strength properties due to even temperature during fusion. These strength properties with the high quality and finish of the product suits it to manufacturing of parts for aerospace and medical applications.
In selective laser sintering (SLS), machines are made up of three components: a heat source, a method to control the heat source, and a mechanism to add new layers of materials. The SLS process requires no additional support structure for the product being printed. In the SLS chamber, nitrogen is often used to maximize the oxidation and end quality of the model. A cool-down period is also required to ensure high tolerance and quality of fusion. Some SLS machines monitor the temperatures layer by layer and adapt the power to improve quality. SLS processes use plastic powders, rather than metal powders used in direct metal laser sintering.
Selective heat sintering uses a heated thermal printhead to fuse powder material. Layers are added with a roller between fusion of layers. The use of a thermal printhead reduces the heat and power levels required for printing. Selective heat sintering systems use thermoplastic powders and require support materials in the process of printing. The process is often used to create concepts prototypes rather than structural components.
Selective laser melting (SLM) is similar to selective laser sintering, except it is faster while requiring the use of an inert gas and requiring higher energy use with poor overall energy efficiency. Through the process, a roller or blade is used to spread new layers of powder over previous layers. In cases when a blade is used, the blade is often vibrated to encourage a more even distribution of powder.
Material jetting
Material jetting, also known as multi-jet modeling, creates objects in a similar method to an inkjet printer. The process uses droplets to build a material on a support structure, while ultraviolight light or heat cures the droplets to create a 3D object. In the technique, droplets are selectively deposited on an X, Y, and Z axis controlled by computer and based on computer-aided designs. Common materials used in material jetting machines include polymers and waxes, due to their viscous nature that can form droplets. Overall, the materials suitable for use in material jetting machines are limited. And the parts printed through material jetting printers are mainly suitable for non-functional prototypes, as the printed parts often have poor mechanical properties.
The types of material jetting technologies include PolyJet technology, NanoParticle Jetting, and Drop On Demand. PolyJet technology jets thin layers of photopolymer material onto a build tray, in which each layer is cured by ultraviolet light. PolyJet technology was the first material jetting technology introduced. The PolyJet process was developed by Object and was later bought by Stratasys.
NanoParticle jetting technology was developed by XJet and uses a dispersion methodology to deposit solid nanopoarticles suspended in a liquid and jetted onto the build tray. In the system, two printheads and thousands of nozzles spray ultrafine drops that both build and support materials onto the build trays, while high temperature in the build area evaporates the liquid jacket around the nanoparticles. The remaining nanoparticles are sintered and the support material is removed, with a thin and smooth surfaced product capable of fine details remaining.
Drop on demand (DOD) technology is a process typically used for viscous materials, and consists of deposits tiny dots of material instead of continuous lines. The printers consist of two heads for each build and support material and are often used for make wax patterns for investment casting. In the printing process, wax material is printed in layers with the support material automatically laid down and eliminating the need for designers to create support structures. The finished part is placed in a liquid bath which dissolves the support material away.
Binder Jetting
Binder jetting is a manufacturing technique in which a binding liquid is selectively deposited to join powder material to form a 3D part. The process does not require heat during the printing process. Exon, an early developer of the binder jetting technique, uses furan binder, silicate binder, phenolic binder, and aqueous-based binder for their binder jetting printers. Regardless of binder, the process of a binder jetting printer sees the application of a layer of material powder, followed by a printhead depositing the binder adhesive on the powder where required until a 3D model is finished. The unbound powder remains until it is removed.
Binder jetting processes can manufacture in a range of different colors and in a range of metal, polymers, and ceramics. The two-material process allows for many different binder-powder combinations with various mechanical properties. However, often, through the use of specific binder materials, binder jetting printed materials are not always suitable for use as structural parts.
Sheet Lamination
Sheet lamination is a process of building a 3D object by stacking and laminating thin sheets of material. The lamination method can be bonding, ultrasonic welding, or brazing while a final shape is achieved through laser cutting or CNC machining. Sheet lamination produces parts with the least additive resolution compared to other additive manufacturing processes; however, it is a low cost and offers fast manufacturing times from easily available low-cost material.
The materials involved in sheet lamination include paper, plastic, metal, and woven fiber composites. Forming methods include CNC milling, laser cutting, and aqua blasting. And the lamination techniques include adhesive bonding, thermal bonding, and ultrasonic welding. The process either follows a form then bond process, in which sheet material is cut into shape and then bonded layer on layer to create a 3D object. Or it follows a bond then form process, in which the material layers are bonded and then cut into the desired shape. Sheet lamination types, each offering some kind of variation of the above methods, can be categorized into seven types:
- Laminated object manufacturing (LOM)
- Selective lamination composite object manufacturing (SLCOM)
- Plastic sheet lamination (PSL)
- Computer-aided manufacturing of laminated engineering materials (CAM-LEM)
- Selective deposition lamination (SDL)
- Composite based additive manufacturing (CBAM)
- Ultrasonic additive manufacturing (UAM)
Directed Energy Deposition
Directed energy deposition is an additive manufacturing process that forms 3D objects by melting material as it is deposited using focused thermal energy such as laser, electron beam, or plasma. Both energy source and the material feed nozzle are manipulated using a gantry system or robotic arm. Due to the nature of direct energy deposition, even though it is possible to create 3D objects from scratch, the process is generally used for adding to an existing part or repairing existing parts. Direct energy deposition systems are used in hybrid manufacturing, in which a substrate bed is moved to create complex shapes.
Direct energy deposition systems can be used to make metal, ceramic, and polymer parts, although they are primarily used to make metal parts. The types of systems include laser-based systems, such as Optomec's laser engineering net shape system, which uses a laser as the main energy source. An electron beam based system, such as Sciaky's electron beam additive manufacturing system, uses electron beams to melt the powdered material feedstock. And the plasma or electric arc based system, such as Wire's arc additive manufacturing process use electric arcs to melt wire.
The suitable materials for direct energy deposition systems include niobium, titanium and titanium alloys, inconel, stainless steels, hastelloy, aluminum alloy, tantalum, zinc alloy, tungsten, and copper-nickel alloys. Direct energy deposition systems are used in industries such as aerospace, defense, oil and gas, and the marine industry.
Applications
The applications for 3D printing are various across industries and for hobbyist uses with the introduction of lower cost printing technology.
Housing
3D printing is being explored as a construction method that reduces the costs of on-site construction and time-to-build of a home. The application of 3D printing in home construction has been explored as an affordable housing solution for urban areas.
3D printing companies in housing industry
Aerospace
Additive manufacturing systems are capable of producing lightweight parts with complex geometric designs useful for the aerospace industry. In 2013, NASA tested SLM-printed rocket injector during a hot fire test generating 20,000 pounds of thrust. In 2015, the FAA cleared 3D-printed parts for use in commercial jet engines. In the 2017 Paris Air Show, the Boeing 787 displayed FAA-certified structural parts fabricated from 3D printing of titanium wire.
3D printing companies in aerospace industry
Automotive
The automotive industry has used 3D printing processes for rapid prototyping. As manufacturing techniques have advanced, 3D printing has been used for developing automotive parts. This includes the McLaren Formula 1 racing team using 3D printed parts in their race cars, including a rear wing replacement that took ten days to produce using 3D printers, instead of the five weeks subtractive manufacturing can take. In 2014, Koenigsegg, Swedish supercar manufacturer, used 3D printing for many components. Most of the manufacturing processes extend to the bodywork and related elements, but do not extend to the powertrain.
Healthcare
Additive manufacturing has been used in the healthcare industry to produce medical items and prosthetics. This has included medical device manufacturing company Stryker using additive manufacturing technology to create surgical implants for patients suffering from bone cancer. A clinical study done by the New York University School of Medicine is looking into the use of patient-specific, multi-colored kidney cancer models and whether they can effectively assist surgeons with pre-operative assessments.
There have been studies into the viability of 3D bio-printing for use in tissue engineering applications, including the printing of organs and body parts. In the process, layers of living cells are deposited onto a gel medium or sugar matrix to build a three-dimensional structure, including vascular systems. In May 2018, a 3D printing system was used for a kidney transplant to save a three-year-old boy.
In the pharmaceutical industry, 3D printing systems are being used by researchers as a new way to develop formulations of materials and compounds not possible with conventional techniques such as tableting or cast-molding. One of the possible uses of 3D printing in pharmaceuticals is to print personalized dosages to better target patient needs.
3D printing companies in healthcare industry
Clothing
In the clothing and fashion industry, designers and manufacturers have experimented with 3D printed clothing items, including Nike using 3D printing to prototype and manufacture their 2012 Vapor Laser Talon football shoes and New Balance 3D manufacturing custom-fit shoes for athletes.
Shoes
In 3D printing for shoes, the additive manufacturing techniques offers a chance for creators and designers in the fashion industry to create designs and collections with shapes or designs that could be otherwise unable to create in subtractive manufacturing methods. As well, there are many projects launching to develop new speakers, futuristic lightweight footwear, and customer printed shoes for specific athletes.
Food
Additive manufacturing systems, or analogues, are also being used in the manufacturing of food. The foods printed have included chocolate, candy, crackers, pasta, and pizza. NASA has pursued research into the technology to reduce food waste and design foods to fit astronauts' dietary needs. And in 2018, Giuseppe Scionti developed technology to generate fibrous plant-based meat analogues using a custom-built 3D bioprinter.
Often 3D printing in foods describes an additive manufacturing process, such as an automated pizza vending machine that is capable of extruding dough, topping the dough with tomato sauce and cheese, and sending that to an oven. Food can, especially in the case of viscous foods, be printed fairly easily. 3D printing has been used for decorating and deserts where the accuracy of the printer can create complex designs. However, in the case of other types of food, 3D printing can be more restrictive. As well, in the case of 3D printing new or novel foods, the technology is further behind its peers, as the technology can be prohibitively expensive and often is not scalable.
Firearms
Additive manufacturing has been used in the firearms industry to offer a new manufacturing method for established companies, and has produced possibilities for the do-it-yourself manufacturing of firearms.
All 3D printing companies
3d Printer Tips and Mods Wiki
What’s New
- See the donations page for information of helping support this cause (web hosting, products to review, etc).
- We have added a Review section where we will be posting reviews of boards, printers, upgrades, filament and resins.
- Added a SLA Resin information database for the Wanhao D7 where users can add curing times for others to lookup.
About Us
- Who we are and why we are doing this
Articles
The Articles page is where we will be posting any 3d printer related news, information or stories.
Safety Notices
- Wanhao I3 Plus Bed Notice
- Wanhao first batch (alpha testers) D7 LED Power Driver Fix
- Wanhao D7 Printer check on Unboxing (for common problem areas)
- Wanhao D7 v1 and v1.
2 Fan Upgrade Kit
Resources
- 3d Printing Products Store (being updated) – Parts for building 3d printers and cnc. Tools and filaments also available.
- Amazon Subscriptions and Deals
Printers
This is a list of common 3d printers and will be adding any documentation we can find along with mods and tips for these printers.
-
Wanhao Duplicator i3 (also rebranded as the Monoprice “Maker Select” and Aldi “Cocoon Create”)
-
Wanhao Duplicator i3 Plus
- Wanhao Duplicator I3 Mini
-
Wanhao Duplicator 4
-
Wanhao Duplicator 5 Series (DS/D5S/D5S Mini)
- Wanhao Duplicator 6 Series
- Wanhao Duplicator 7 Resin Printer
- Wanhao Duplicator 9 Series
-
Raise 3D N series
- Tiko3d Delta Printer
- Ultimaker
- Phrozen Resin Printer
- Flashforge Hunter Resin Printer
- Voxelab Aquila
- Zortrax
-
Cubicon Single (3DP-110F)
-
Cubicon Style (3DP-210F)
-
Makerbot TOM
-
Makerbot Replicator
-
Makerbot Replicator Mini
-
Type-A clone (Jetguy modification)
-
Kossel Mini
-
CNCMe Rostock MAX
-
Rostock custom (original Rostock design)
-
Cube Gen3 (2x)
-
New Matter Mod-t
-
M3D
-
Makerbot Replicator clone Tall
-
CoreXY Ultireplicator (Jetguy custom 4’x4’x4′)
-
CoreXY (Jetcuy custom 24“ bed)
-
CoreXY (Jetguy custom 16” bed)
-
CoreXY (Jetguy custom 13″ bed)
-
CoreXY custom
-
mUVe SLA Printer (custom build)
-
FlashForge Dreamer
-
Printrbot Metal
Printer Boards
3D Object / STL Resource List
- Sources for 3d Printable Objects
Reviews
We are a participant in the Amazon Services LLC Associates Program, an affiliate advertising program designed to provide a means for us to earn fees by linking to Amazon.
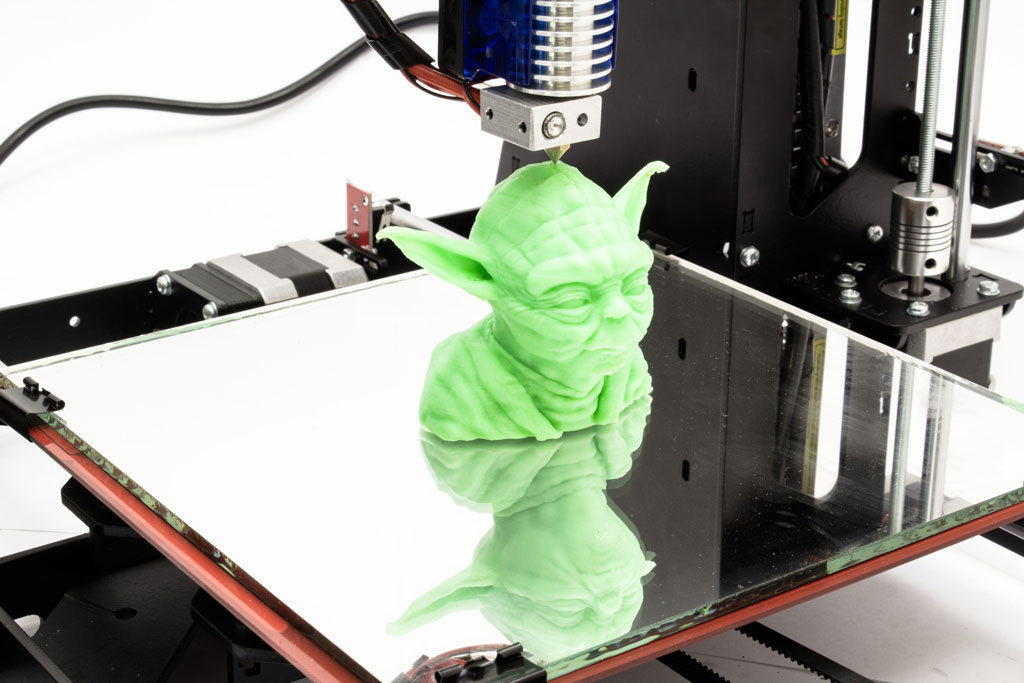
Encyclopedia of 3D printing
Welcome to the help section of our portal!
As you can see, the world of 3D printing deserves the title of "mysterious". The rapid development of technology gives rise to a lot of all kinds of terms, concepts and designs, whose essence is far from obvious to a simple layman. The main task of our site is to acquaint you with the latest news from the world of 3D printing, tell you about technological innovations and help you with the purchase of the necessary equipment. nine0009 The task is complicated by the fact that currently in Russia there is no official standard for terms related to 3D printing. As a result, many of them are differing translations of the originals, somewhat confusing to the reader. In addition, 3D printer manufacturers themselves often try to monopolize parts of the market by making fairly minor changes to existing technologies in order to obtain a patent, and supplying “new” products with new names, thereby only exacerbating the confusion. nine0009 But don't despair. In this section, we will try to explain all the nuances of the world of 3D printing: the technologies used, how they work, terminology options, and so on. Keep in mind that the world of 3D printing does not stand still, and therefore we will constantly update and supplement our help section with new information.
Reference sections:
- 1 3D printing
- 2 3D printing technologies
- 3 Consumables for 3D printers
- 4 3D equipment
- 5 SLISERS
- 6 Articles about 3D printing
- 7 Our reviews about 3D printers and about 3D printing 9002
- 9 Literature
- 10 Work with the 3DTODAY portal. Reference
3D printing
- What is a 3D printer.
- All about 3D printing. additive manufacturing. Basic concepts.
- 3D printing for dummies or "what is a 3D printer?" nine0021
- How to build a 3D printer with your own hands"
- 3D Printer & 3D Printing FAQ"
3D Printing Technologies
- Mask Stereolithography (SGC)
- Multi-Jet Modeling Technology (MJM)
- Color Inkjet (CJP)
- Digital LED Projection (DLP)
- 3D Inkjet Printing (3DP)
- Selective Laser Sintering (SLS)
- Selective laser melting (SLM)
- Stereolithography (SLA)
- Selective heat sintering (SHS)
- Lamination Object Manufacturing (LOM)
- Electron Beam Melting (EBM)
- Direct Metal Laser Sintering (DMLS)
- Electron Beam Fusion Manufacturing (EBFȝ)
- Fused Deposition Modeling (FDM)
- Selective Deposition Lamination (SDL) Technology
3D Printer Consumables
- FDM/FFF Consumables
- 3D Printing Consumables Chart.
Melting Points and Extrusion Rates
- Photopolymer consumables
- PLA plastic for 3D printing
- ABS plastic for 3D printing
- Printable PVA
- PET plastic for printing
- 3D Printable Nylon
- Laywoo-D3 for 3D printing
- NinjaFlex for 3D printing
- Laybrick for 3D printing
- Stratasys Photopolymer Resins
- 3D Ink Photopolymer Resins
- Photopolymer resins Asiga
- Photopolymer Resins Digital Wax Systems
- RapidShape 9 Photopolymer Resins0021
- MadeSolid Photopolymer Resins
- 3D Systems Photopolymer Resins
- Fun To Do Photopolymer Resins
- Polystyrene for 3D printing
- 3D printed polycarbonate
- Portable bar extruders.
Filament manufacturing. How To Make Your Own 3D Printing Consumables
nine0040 - 3D pen
- 3D printer FDM
- Catalog of DIY and OpenSource 3D printers
- Photopolymer 3D printer
- Metal 3D printing
- All versions of CURA - download
- How to avoid deformation of models when 3D printing
- How to choose high quality filament
- Processing of 3D printed models
- How to clear a clogged extruder nozzle
- "Rescue" of the product using the Repetier-Host program when 3D printing is stopped
- 3 Commandments to make 3D printed products cheaper
- Photoshop CS6 modeling and 3D printing tutorial
- We bought a 3D printer and decided to make money.
What's next?
- Cheap 3D printers for every taste
- Household 3D printers for your home
- Jewelry 3D printers or what to give your beloved man nine0020 Metal 3D printing on a home 3D printer. Technology Today and Immediate Prospects
- 3D printer and metal - the present and future of metal 3D printing
- ChefJet Confectionery 3D Printers – The End of the Sugar Cube Era
- MBot Home 3D Printer Review
- 3D printing with chocolate or how to organize your sweet business nine0020 3D Printers for Jewelers - Unparalleled Print Quality
- Set up the Marlin firmware and upload it to the 3D printer
- We print with ABS plastic without cracks and heat chambers
- Book: 3D printing - short and clear
- 3Dtoday: portal visitor guide
3D equipment
Slicers
3D printing articles
Our reviews about 3D printers and 3D printing
Technical
Literature
Working with the 3Dtoday portal.
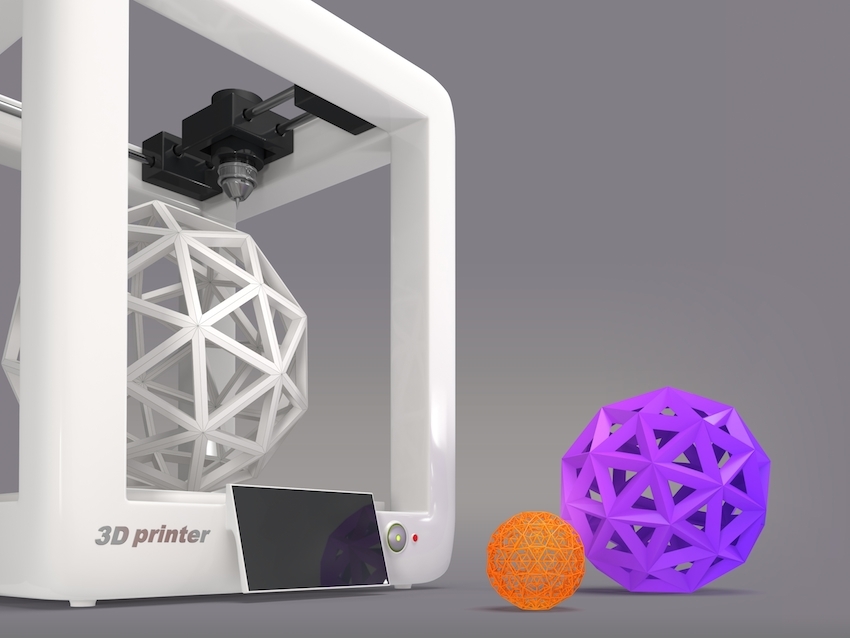
What is a 3D printer?
Popular articles
I make a normal throat out of an ordinary one
01/29/2023
2775
The other day I had the misfortune to break a bimetallic thermal barrier. I replaced it from old stock ...
Magnetic probes for printed circuit boards nine0245
01/27/2023
2797
In addition to the PCB vise, I immediately planned to make these feelers. People like me x...
New pumping of the section "We print"
01/27/2023
2439
Briefly and simply describe your 3D printed projects.
3D printing knowledge base
How to choose the right extrusion temperature
For optimal FDM 3D printing results, temperature settings need to be adjusted empirically, and in this article we will show you how to do this with a temperature tower and a Cura slicer.
Continue reading →
ABS 3D printing: settings, tips and tricks temperature and adhesive agents. In this article, we will share tips for working with ABS. nine0005
Continue reading →
"Smoothing 3D printed polylactide products"
Not everyone likes the ribbed texture of 3D printed products, which means you need to learn how to smooth surfaces. One of the most popular plastics for 3D printers is polylactide, and in this article we will understand the post-processing methods for this polymer.
Continue reading →
"3D printing of hollow models: methods and applications"
3D printing of floors x products is a great way to save time and consumables. It is not always applicable, but it has the right to exist. We'll tell you how and when it's done. nine0005
Continue reading →
"Seven Ways to Improve Adhesion in Polylactide 3D Printing"
Everyone or almost everyone loves and respects polylactide (PLA) because it is one of the easiest and safest plastics to 3D print. However, even when working with PLA, sticking problems can occur on 3D printer stages, and in this article we will figure out how to fix them.
Continue reading →
"Seven Free STL Editors: How to Modify and Repair STL Files"
You can edit STL files in two types of software - computer-aided design systems (CAD, CAD), or specialized programs for working with polygonal meshes. Consider the most popular options.
Continue reading →
"Top 15 Models for Calibrating a 3D Printer"
Calibrating before 3D printing is boring but necessary. We share a list of useful 3D models specially created for testing and debugging parameters. nine0005
Continue reading →
"Taper Slicing as a More Efficient Method for 3D Printing Hanging Structures"
Standard slicers and FDM 3D printers slice 3D models horizontally, often requiring heavy use of support structures. Is it possible to do without supports and reduce material consumption? You can if you use the conical threading method.
Continue reading →
"rPETG GF - print parameters, material properties and tips"
rPETG GF is an engineering thermoplastic made from recycled PETG with fiberglass filler. The filament allows it to be used for tasks that require increased strength and wear resistance of end products.
Continue reading →
"Ten Ways to Save Filaments, Money and Nature"
In this article, we'll share some tips for saving 3D printing plastic so that 3D printers stay full, wallets thick, and nature clean. nine0005
Continue reading →
Web-Free 3D Printing: Adjusting Retract in Cura Slicer
If you've experienced thin filaments around web-like prints, it's most likely a problem with sub-optimal retract settings. We tell you what it is and how to deal with it.
Continue reading →
Miniature 3D Printing Tips
Hobby 3D printing is a popular use for 3D printers, often involving the production of small toys, souvenirs, and fine art objects. The task is not easy, and in this article we will share tips for 3D printing miniatures. nine0005
Continue reading →
Cura Slicer Infill Types
One of the advantages of 3D printing over casting is that 3D printed products can be made partially hollow, saving time and material, and at the same time reducing weight. In this article, we will deal with different filling options - how it happens and how it is used.
Continue reading →
"Lithophany on a 3D printer: how to make translucent images"
Lithophany is an artistic technique for creating translucent photographs or drawings, for example, to decorate unique lamps. 3D printing technologies are great for artisanal production of such images, called lithophanes. We'll tell you how it's done. nine0005
Continue reading →
"Calibration cubes, or How to train a 3D printer"
If immediately after starting FDM / FFF, the 3D printer produces arbitrary shapes to the envy of the best abstract artists, do not rush to panic. Most likely, the equipment just needs to be calibrated, and we’ll tell you how to do it under the cut.
Continue reading →
"Buying a used 3D printer: how to save money and not get into trouble"
Used FDM 3D printers are a good option, especially when more capable or modern hardware is needed but the budget leaves a lot to be desired. In this article, we will share tips for purchasing 3D printers in the secondary market and tell you what you need to pay attention to before buying.
Continue reading →
“Painting products after FDM 3D printing”
Nowadays, there are enough 3D printers with multiple extruders or filament switching systems, but if this is not enough, you can increase the presentability, and often the durability of 3D printed products painting. In this article, we will deal with the main points of coating and pigmentation. nine0005
Continue reading →
"Ten Interesting Hobby 3D Printing Projects"
We can talk as much as we want about the possibilities of additive technologies, but it's better to see once than hear a hundred times. Better yet, print your own! We offer a selection of interesting projects that can be implemented using a home 3D printer.
Continue reading →
Support structures in FDM 3D printing
Supports are a necessary evil: they cause a lot of inconvenience, but often without them it is simply impossible to get products, especially when it comes to 3D printing models with hinged structures. In this article, we will talk about supports - what they are, how to avoid them and what to do if you cannot do without supports.
Continue reading →
"The Best 3D Printers of 2022"
Today's additive market is saturated with all kinds of 3D printing equipment, and sorting through all this variety can be very difficult. We have prepared a list of a dozen of the most interesting, in our opinion, FDM and photopolymer 3D printers for amateurs and professionals. nine0005
Continue reading →
FDM 3D Printer Basics
Thinking about buying a 3D printer and don't know where to start? Then you are welcome under the cat: in this article we will try to explain as clearly as possible what FDM 3D printing is and how to work with FDM 3D printers.
Continue reading →
"How to deal with deformations in 3D printing"
Any production process that involves cooling polymers or metals will be accompanied by shrinkage of materials, whether it is plastic injection molding, metal molding or 3D printing. In this article, we will share tricks to help combat the unwanted effects of shrinkage - deformation, cracking and peeling off. nine0005
Continue reading →
“How to clean the nozzles of FDM 3D printers”
The nozzle is one of the simplest and at the same time the most critical parts of an FDM 3D printer, since the ability of the equipment to lay material depends on the correct operation of the nozzle. In fact, everything is not so simple: a lot depends on the material from which the nozzle is made, the filaments used, the operating temperature, the shape and even the diameter. In addition, the nozzles are often clogged. In this article, we will figure out how to correctly identify problems and take care of a small but important detail. nine0005
Continue reading →
"Top Ten Parameters for FDM 3D Printing"
In the last article, we talked about the best 3D printing software in 2022. Today we will talk about preparing a 3D model for printing. Slicers are used to prepare 3D models for 3D printing. These programs not only convert digital models into machine code, but also allow you to adjust all the parameters of the FDM 3D printers. The key settings will be discussed in this article. nine0005
Continue reading →
"Best 3D printing software in 2022"
3D printing is a multi-step process, because you first need to design a 3D model, check it for errors, convert it to machine code, and only then into it's a 3D printer. In this article, we will share examples of programs that can help at every stage of preparatory work and directly during 3D printing.
Continue reading →
"G-Code Basics: Basic Command Reference for FDM 3D Printers"
G-code or Gcode is machine code, that is, a sequential set of commands for 3D printers generated by slicers. At the same time, the G-code often has to be edited manually if the slicer does not have the appropriate functionality or the user simply needs to change the behavior of the 3D printer. In this article, we will share a list of the most widely used commands.
Continue reading →
"First steps in FDM 3D printing: a guide for a novice user"
Especially for those who are just starting to comprehend the basics of 3D printing, we offer a selection of useful tips to solve the most common problems when working with FDM 3D printers.
Continue reading →
"The best programs for 3D modeling for 3D printing"
the most popular free and commercial programs of different levels of complexity and functionality. nine0005
Continue reading →
"The most popular slicers for FDM 3D printing and more"
What is a "slicer"? This is a program that converts digital 3D models (usually in STL, OBJ, or M3F formats) into machine code (G-code), a series of commands that a 3D printer understands. Do not even try to make the 3D printer figure out what is required of it from the 3D model. Instead, use one of the solutions on our list, especially since most of them are free. nine0005
Continue reading →
"PrusaSlicer: overview of the program, functionality and basic settings"
PrusaSlicer is a free, feature rich slicer from Prusa Research based on the Slic3r system by Alessandro Ranellucci. The slicer was originally called Slic3r PE (Prusa Edition), but as it moved more and more away from the source, Prusa officially renamed it in May 2019 to avoid confusion. Since then, PrusaSlicer has continued to evolve and be updated every few months. nine0005
Continue reading →
"Who makes money on 3D printing and how"
Ready to make money with direct hands and a 3D printer? Okay, but before diving head first into the business, it would be nice to understand exactly how 3D printing is changing the face of the industries around us in order to find its niche. Let's watch.
Continue reading →
"The Best Professional Storage Solutions for 3D Printing Plastics"
3D printing results. nine0005
Continue reading →
"PEEK: how to print, characteristics and properties"
Polyetheretherketone (PEEK, PEEK) is a special polymer with outstanding properties, which in some cases can replace metals, for example in the production of aircraft parts or implants.
Continue reading →
“How to properly (and not) dry filaments for 3D printers”
As we found out in the previous article, the best option is not to let the filaments absorb moisture at all, but in practice this is almost unrealistic. So, before 3D printing, it is advisable to play it safe and start drying the plastic. We'll talk about this under the cut. nine0005
Continue reading →
"Post-processing of 3D FDM printed products"
In most cases, 3D printed models do not need post-processing, but this applies mainly to functional products. In many cases, surfaces are required to be processed to a finished look using various tools, and in this article we will look at the basic techniques.
Continue reading →
"The most common extrusion 3D printing problems and solutions"
FDM/FFF A 3D printer is a complex mechanism, and plastics for 3D printing can vary greatly in properties. As a result, it may be difficult for a novice user to identify the causes of defects in printed products. Especially for such cases, we have prepared a guide with a list of the most common problems and solutions.
Continue reading →
"How to properly store 3D printer filaments"
When it comes to storing 3D printing plastic, it's better to be safe than sorry. If you protect filaments for FDM 3D printers from moisture and dirt, you can count on better and trouble-free 3D printing, and this is not at all difficult to do. We tell you how and why. nine0005
Continue reading →
"Resin 3D printing in industry"
In this article, we will look at the industrial use of extrusion 3D printing technologies with polymers and composites. No whistles and gnomes, only serious application!
Continue reading →
"Top 10 3D Model Sites for 3D Printing"
If you already have a 3D printer and 3D printing plastic, all you have to do is find digital models. Do-it-yourself 3D modeling is interesting, but mastering this skill will take a lot of time. In the meantime, we suggest looking for something interesting on the sites in our selection. nine0005
Continue reading →
Selecting 3D Printing Plastics: A Guide to REC Materials and Applications
This article provides basic information on REC branded commercial 3D printing plastics and composites.
Continue reading →
REC Multi-Material 3D Printing Guide
Especially for those who practice 3D printing of composite products and soluble supports on FDM 3D printers, we have prepared a handy guide to help predict results in terms of adhesion and shrinkage when working with two different materials at the same time. nine0005
Continue reading →
"Composite materials for 3D printing"
Over the past few years, the intensive development of additive technologies has allowed the introduction of 3D printing in most industries, and this, in turn, has led to new requirements for 3D printers and the emergence of brand new, customized consumables. The expansion of the line of consumables mainly affected the most popular and affordable 3D printing technology — FDM/FFF. nine0005
Continue reading →
"Adhesion and 3D printing: everything you need to know"
@media screen and (min-width: 991px){ . mobil{ display: none; } Many 3D printer owners experience parts coming off the table during 3D printing. Let's take a look at the causes and solutions.
Continue reading →
"X-Line UltraX - printing parameters, characteristics and material properties"
UltraX is an engineering thermoplastic capable of withstanding high loads. This composite material is based on structural polyamide-6 filled with short carbon fibers.
Continue reading →
"PETG Biocide - material description, print settings and properties"
REC Biocide PETG is a special composite material that has disinfecting properties due to additives in the form of special nanoparticles distributed over the polymer matrix. nine0005
Continue reading →
"X-Line FormaX - print parameters, material properties and tips"
Formax is an engineering thermoplastic based on ABS with the addition of carbon fibers (up to 15%), capable of withstanding heavy loads and high temperatures.
Continue reading →
“Flex to flex: what are flexible filaments and how to work with them on a 3D printer”
Flex is just a general name for 3D printing materials with a characteristic flexibility. This group includes a variety of filaments with a wide variety of compositions, so disputes on the topic “which flex is better” are often meaningless. We decided to approach the practical side of the matter and collect in one article useful information on the options that are produced under our brand, that is, REC, and at the same time explain how to work with them. nine0005
Continue reading →
"REC PP+: print parameters, performance and properties"
REC PP+ is a modified polypropylene filament that allows you to print strong and durable products with high chemical and impact resistance. Continue reading → Main advantages and disadvantages of REC PP+ Polypropylene is one of the most common polymers due to a number of positive characteristics.