New 3d printing tech
New 3D printer promises faster, multi-material creations
Stanford engineers have designed a method of 3D printing that is 5 to 10 times faster than the quickest high-resolution printer currently available and is capable of using multiple types of resin in a single object.
By Laura Castañón
Advancements in 3D printing have made it easier for designers and engineers to customize projects, create physical prototypes at different scales, and produce structures that can’t be made with more traditional manufacturing techniques. But the technology still faces limitations – the process is slow and requires specific materials which, for the most part, must be used one at a time.
A model of Kyiv’s Saint Sophia Cathedral in the blue and yellow of the Ukrainian flag, made using the iCLIP method for 3D printing, which allows for the use of multiple types – or colors – of resin in a single object. (Image credit: William Pan)
Researchers at Stanford have developed a method of 3D printing that promises to create prints faster, using multiple types of resin in a single object. Their design, published recently in Science Advances, is 5 to 10 times faster than the quickest high-resolution printing method currently available and could potentially allow researchers to use thicker resins with better mechanical and electrical properties.
“This new technology will help to fully realize the potential of 3D printing,” says Joseph DeSimone, the Sanjiv Sam Gambhir Professor in Translational Medicine and professor of radiology and of chemical engineering at Stanford and corresponding author on the paper. “It will allow us to print much faster, helping to usher in a new era of digital manufacturing, as well as to enable the fabrication of complex, multi-material objects in a single step.”
Controlling the flow of resin
The new design improves on a method of 3D printing created by DeSimone and his colleagues in 2015 called continuous liquid interface production, or CLIP. CLIP printing looks like it belongs in a science fiction movie – a rising platform smoothly pulls the object, seemingly fully formed, from a thin pool of resin. The resin at the surface is hardened into the right shape by a sequence of UV images projected through the pool, while a layer of oxygen prevents curing at the bottom of the pool and creates a “dead zone” where the resin remains in liquid form.
The dead zone is the key to CLIP’s speed. As the solid piece rises, the liquid resin is supposed to fill in behind it, allowing for smooth, continuous printing. But this doesn’t always happen, especially if the piece rises too quickly or the resin is particularly viscous. With this new method, called injection CLIP, or iCLIP, the researchers have mounted syringe pumps on top of the rising platform to add additional resin at key points.
“The resin flow in CLIP is a very passive process – you’re just pulling the object up and hoping that suction can bring material to the area where it’s needed,” says Gabriel Lipkowitz, a PhD student in mechanical engineering at Stanford and lead author on the paper. “With this new technology, we actively inject resin onto the areas of the printer where it’s needed.”
The resin is delivered through conduits that are printed simultaneously with the design. The conduits can be removed after the object is completed or they can be incorporated into the design the same way that veins and arteries are built into our own body.
Multi-material printing
By injecting additional resin separately, iCLIP presents the opportunity to print with multiple types of resin over the course of the printing process – each new resin simply requires its own syringe. The researchers tested the printer with as many as three different syringes, each filled with resin dyed a different color. They successfully printed models of famous buildings from several countries in the color of each country’s flag, including Saint Sophia Cathedral in the blue and yellow of the Ukrainian flag and Independence Hall in American red, white, and blue.
“The ability to make objects with variegated material or mechanical properties is a holy grail of 3D printing,” Lipkowitz says. “The applications range from very efficient energy-absorbing structures to objects with different optical properties and advanced sensors.”
Having successfully demonstrated that iCLIP has the potential to print with multiple resins, DeSimone, Lipkowitz, and their colleagues are working on software to optimize the design of the fluid distribution network for each printed piece. They want to ensure that designers have fine control over the boundaries between resin types and potentially speed up the printing process even further.
“A designer shouldn’t have to understand fluid dynamics to print an object extremely quickly,” Lipkowitz says. “We’re trying to create efficient software that can take a part that a designer wants to print and automatically generate not only the distribution network, but also determine the flow rates to administer different resins to achieve a multi-material goal.”
DeSimone is a member of Stanford Bio-X, the Wu Tsai Human Performance Alliance, and the Stanford Cancer Institute; he is a faculty fellow of Stanford’s Sarafan ChEM-H; and he holds appointments in the departments of Radiology and Chemical Engineering.
Additional Stanford co-authors of this research include Eric S. G. Shaqfeh, the Lester Levi Carter Professor in the School of Engineering and professor of chemical engineering and of mechanical engineering; senior research scientist Maria T. Dulay; postdoctoral scholars Kaiwen Hsiao and Brian Lee; graduate students Tim Samuelson, Ian Coates, and Harrison Lin; and undergraduate student William Pan. Other co-authors are from Sungkyunkwan University and Digital Light Innovations.
This work was funded by the Precourt Institute for Energy at Stanford, the Stanford Woods Institute for the Environment, and the National Science Foundation.
To read all stories about Stanford science, subscribe to the biweekly Stanford Science Digest.
FAQ
How long will my project take?
We turn projects around as fast as possible and can complete some work same-day, but the timeline depends entirely on the scope of work. Here are some averages to give you a better idea:
Single 3D Prints: 1-3 business days if the job is small to medium size, 2-5 business days for large prints, 4-8 business days for SLS prints.
Short-Run Manufacturing: Production runs are heavily dependent on what is bring printed and how many. We oftentimes fulfill as prints are completed if parts are needed ASAP. Contact us for a specific quote.
3D Modeling: 1-5 business days, depending on the complexity of the design and the number of concurrent design jobs.
3D Scanning: 1-5 business days.
If you have a tight deadline, please contact us ASAP so that we can make a quick assessment for you.
What is the build size of your printers?
We often build objects that are larger than our build sizes by printing objects in parts and assembling. That being said, we have build sizes as large as 12 feet and as small as 2 inches and are constantly increasing our printing capacity.
How much does it cost?
3D printing, modeling, and scanning projects rely on the scope of work to determine the price, but we have provided some averages below. We offer free consultations in which we can provide a ballpark figure to help determine whether you would like to move forward with a formal proposal.
On average,
3D printing jobs are between $100 and $1000 (with a minimum of $25). Short-run manufacturing and production run prints can cost as low as $1 per unit with an average of $5-25 per unit.
3D modeling is $125/hour and our average modeling projects are 2-6 hours.
3D scanning is $500 for a half-day session which can include multiple parts in that same half-day session, and if the job takes less than two hours we will prorate that down to $250.
How does scanning work?
Currently we are able to scan non-moving objects. Scanning is labor-intensive so we prefer to carve out a half-day session per client, and can typically scan multiple items in that half-day session. The result of a scan is a point cloud file (OBJ, STL, etc.) that can be manipulated in mesh-based software but not directly-edited parametric CAD software. If you need an editable file for reverse engineering or specific changes, the scan data needs to be converted (manually) to a CAD model which would add additional modeling hours to the project.We prefer to know our clients’ end goals with a scan so that we can confirm that the output we provide will meet the needs of the project. For instance, if the scan is intended to then go to manufacturing, a point cloud will not likely suffice and a CAD model will need to be created from the point cloud data.
What materials do you print with?
The most common materials we print with are PLA, ABS, PET, Flexible, Polycarbonate, Nylon, and SLA Resins (standard, tough, high-temp, dental, castable, flexible).
Do you print flyers, signs, shirts, etc.?
We get asked this a lot, but the answer is “no”.
We only print physical objects utilizing various additive manufacturing technologies (commonly called 3D printing) but do not print 2D objects that appear to be 3D.
Printing
$10-40/hr
Pricing dependent on project
Discounts available for bulk orders
Get Started
Scanning
$500/half day
Most projects take one session
Post-scan modeling may be needed
Get Started
Modeling
$125/hr
3D modeling or
file repair
Projects take 2-10 hours depending on complexity
Get Started
3D Printing Technology Guide
Today, there are about 10 major 3D printing technologies. They differ in speed, accuracy, material used and other parameters. The choice of 3D printing technology depends on the tasks that you set for the 3D printer, on the requirements for the resulting products.
- FDM/FFF
- SLA
- SLM
- SLS
- CJP
- PolyJet
- FDM0006
- SLM
- SLS
- CJP
- PolyJet
FDM (Fused Deposition Modeling) / FFF (Fused Filament Fabrication)
Operating principle: layer-by-layer construction of a product from molten plastic material.
Features:
- Various types of plastics (durable, flexible, heat resistant, etc.)
- Strength and durability of finished products
- 3D printers with large cameras
- Low cost and high productivity
More about FDM technology >>
FDM (Fused Deposition Modeling) / FFF (Fused Filament Fabrication)
Operating principle: layer-by-layer construction of a product from molten plastic material.
Features:
- Various types of plastics (durable, flexible, heat resistant, etc.)
- Strength and durability of finished products
- 3D printers with large cameras
- Low cost and high productivity
More about FDM technology >>
SLA (stereolithography)
Operating principle: layer-by-layer curing of a liquid polymer material under the action of a laser beam.
Features:
- Materials: polymer resins with different properties
- Laser curing
- High print speed
- High precision and detail
- Smooth surfaces
Learn more about SLA technology >>
SLA (Stereolithography)
Operating principle: layer-by-layer curing of a liquid polymer material under the action of a laser beam.
Features:
- Materials: polymer resins with different properties
- Laser curing
- High print speed
- High precision and detail
- Smooth surfaces
More about SLA technology >>
SLM (Selective Laser Melting)
Other names: DMP, DMLS, EBM, etc.
Operating principle: layer-by-layer fusion of metal powders under the influence of a laser
Features:
- Working with various metals and alloys
- Unique Product Features
- Any geometry
More about SLM technology and its analogues >>
SLM (Selective Laser Melting)
Other names: DMP, DMLS, EBM and others0003
Features:
- Working with various metals and alloys
- Unique Product Features
- Any geometry
More about SLM technology and its analogues >>
SLS (Selective Laser Sintering)
Operating principle: layer-by-layer sintering of polyamide powders under the influence of a laser
Features:
- Material: polyamide powders
- Any geometry
- Durability and precision
- High performance
Find out more about the SLS technology >>
SLS (Selective Laser Sintering)
Operating principle: laser-assisted layer-by-layer sintering of polyamide powders
Features:
- Material: polyamide powders
- Any geometry
- Strength and precision
- High performance
Learn more about SLS technology >>
CJP (Color-Jet Printing)
Function: layer-by-layer bonding and coloring of composite powder
Features:
- Composite powder based on gypsum
- 3D full color CMYK
- Realistic prototypes for visual evaluation
- Complex geometries
- Low cost
More about CJP technology >>
CJP (Color-Jet Printing)
How it works: layer-by-layer bonding and coloring of composite powder
Features:
- Composite powder based on gypsum
- 3D full color CMYK
- Realistic prototypes for visual evaluation
- Complex geometries
- Low cost
Learn more about CJP technology >>
PolyJet
How it works: curing liquid photopolymer material under UV radiation
Features:
- Photopolymer materials with different properties (transparent, rubber-like, biocompatible, etc.
)
- High detail, smooth surfaces
- Color 3D printing available
- Products do not require post-processing
Learn more about PolyJet technology >>
PolyJet
How it works: curing liquid photopolymer material under UV light
Features:
- Photopolymer materials with different properties (transparent, rubbery, biocompatible, etc.)
- High detail, smooth surfaces
- Color 3D printing available
- Products do not require post-processing
Learn more about PolyJet technology >>
We will help you choose a professional 3D printer the information I entered and I consent to the processing of my personal data in accordance with the privacy policy and user agreement. nine0003
Comparison of 3D printing technologies: FDM, SLA and SLS
Additive manufacturing or 3D printing reduces costs, saves time and expands the technological possibilities in product development. 3D printing technologies offer versatile solutions for applications ranging from rapid concept and functional prototypes in the field of prototyping to fixtures and clamps or even final parts in manufacturing.
Over the past few years, high resolution 3D printers have become more affordable, more reliable and easier to use. As a result, more companies have been able to use 3D printing technology, but choosing between different competing 3D printing solutions can be difficult. nine0003
Which technology is right for your needs? What materials are available for her? What equipment and training is needed to get started? What are the costs and payback?
In this article, we take a closer look at three of today's most well-known plastic 3D printing technologies: Fused Deposition Modeling (FDM), Stereolithography (SLA), and Selective Laser Sintering (SLS).
Choosing between FDM and SLA 3D printer? Check out our detailed comparison of FDM and SLA technologies. nine0278
You can download this high resolution infographic here.
VIDEO MANUAL
Can't find the 3D printing technology that best suits your needs? In this video tutorial, we compare Fused Deposition Modeling (FDM), Stereolithography (SLA), and Selective Laser Sintering (SLS) technologies in terms of the top factors to consider when purchasing.
Watch Video
Fused Deposition Modeling (FDM), also known as Fused Filament Manufacturing (FFF), is the most widely used form of 3D printing at the consumer level, fueled by the rise of consumer 3D printers. On FDM printers, models are made by melting and extruding a thermoplastic filament, which the printer's nozzle applies layer by layer to the model being built. nine0003
The FDM method uses a range of standard plastics such as ABS, PLA and their various blends. It is well suited for making basic experimental models, as well as for quickly and inexpensively prototyping simple parts, such as parts that are usually machined.
FDM models often show layer lines and may have inaccuracies around complex features. This sample was printed on a Stratasys uPrint FDM industrial 3D printer with soluble support structures (printer price starting at $15,900).
FDM printers have the lowest resolution and accuracy of SLA or SLS and are not the best option for printing complex designs or parts with complex features. Surface quality can be improved by chemical and mechanical polishing processes. To address these issues, industrial FDM 3D printers use soluble support structures and offer a wider range of engineering thermoplastics, but they are also expensive. nine0003
FDM printers do not handle complex designs or parts with complex features well (left) compared to SLA printers (right).
Invented in the 1980s, stereolithography is the world's first 3D printing technology and is still one of the most popular technologies among professionals today. SLA printers use a process called photopolymerization, which is the conversion of liquid polymers into hardened plastic using a laser.
See stereolithography in action.
Models printed on SLA printers have the highest resolution and accuracy, the sharpest detail and the smoothest surface of all plastic 3D printing technologies, but the main advantage of the SLA method is its versatility. Materials manufacturers have developed innovative formulas for SLA polymers with a wide range of optical, mechanical and thermal properties that match those of standard, engineering and industrial thermoplastics. nine0003
Models created using SLA technology have sharp edges, a smooth surface and almost invisible layer lines. This sample was printed on a Formlabs Form 3 Desktop Stereolithographic 3D Printer (price starting at $3499).
SLA is an excellent option for making highly detailed prototypes that require tight tolerances and smooth surfaces such as molds, templates and functional parts. SLA technology is widely used in industries ranging from engineering and design to manufacturing, dentistry, jewelry, modeling, and education. nine0003
White Paper
Download our in-depth white paper to learn how SLA printing works, why thousands of professionals use it today, and how this 3D printing technology can help your job.
Download white paper
free sample
Experience Formlabs print quality firsthand. We will send a free 3D printing sample directly to your office.
Request a free sample
Selective laser sintering is the most common additive manufacturing technology used in industry.
Selective Laser Sintering (SLS) 3D printers use a high power laser to sinter fine polymer powder particles. The unsprayed powder supports the model during printing and eliminates the need for special support structures. This makes SLS ideal for complex geometries, including internal features, grooves, thin walls, and negative taper. Models produced using SLS printing have excellent mechanical characteristics: their strength can be compared with the strength of injection molded parts. nine0003
Models created with SLS technology have a slightly rough surface, but almost no visible layer lines. This sample was printed on the Formlabs Fuse 1 SLS workshop 3D printer (price starting at $18,500).
The most common selective laser sintering material is nylon, a popular engineering thermoplastic with excellent mechanical properties. Nylon is light, strong and flexible, resistant to impact, heat, chemicals, UV radiation, water and dirt. nine0003
The combination of low part cost, high productivity, and widely used materials makes SLS a popular method for engineering functional prototyping and a cost-effective alternative to injection molding in cases where production runs are limited.
White Paper
Looking for a 3D printer to create durable, functional models? Download our white paper to learn how selective laser sintering (SLS) technology works and why it is popular in 3D printing for functional prototypes and end-use products. nine0363
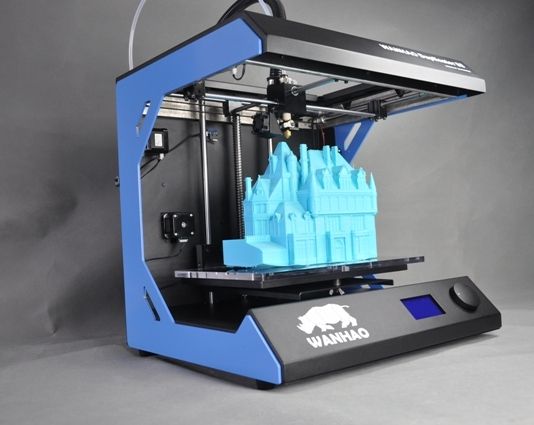
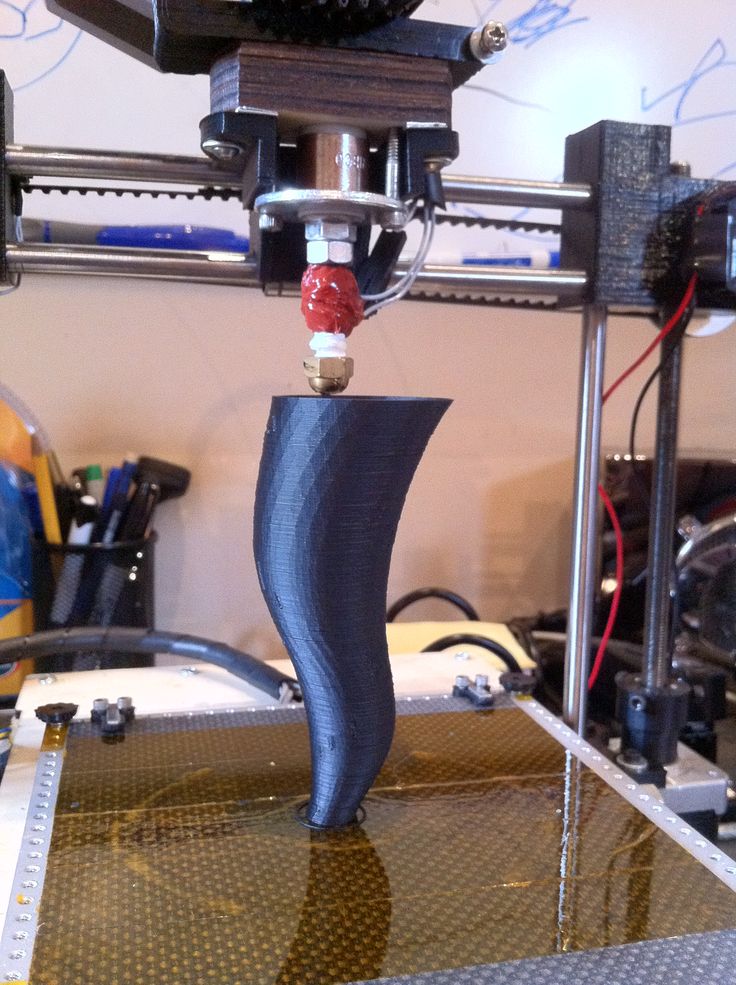
Either way, you should choose the technology that best suits your business. Prices have dropped significantly in recent years, and today all three technologies are offered in compact and affordable systems.
3D printing costing doesn't end with initial equipment costs. Material and labor costs have a significant impact on the cost of each part, depending on the application and production needs. nine0370

INTERACTIVE
Try our interactive ROI tool to see how much time and money you can save by printing with Formlabs 3D printers.
Calculate savings
FDM, SLA and SLS printed ski goggle frame prototypes (left to right).
We hope this article has helped you narrow down your search for the 3D printing technology best suited to your needs.