3D printing speaker cabinet
3D Printed Speakers: An Overview - 3DPrint.com
One unforeseen 3D printing application is in the production of speaker parts and even entire speakers. This particular area is surprisingly vibrant, with many hobbyists using 3D printing to make their very own designs come to life. But, commercial companies are also making money off of 3D printed speaker components in very high-end applications. So, we thought it was time to look at the field as a whole to see what has been going on in 3D printed speakers.
In 2009 Cornell researchers 3D printed a fully functional speaker:
“We’re trying to move the printing away from just printing passive parts made of plastic or metal, to printing integrated systems, active systems that can do something,” says associate professor of mechanical and aerospace engineering, Hod Lipson. Lipson led the project with graduate students Apoorva Kiran and Robert MacCurdy… the loudspeaker is a relatively simple object, consisting of plastic for the housing, a conductive coil, and a magnet.
Silver ink was used as the conductor and a viscous blend of strontium ferrite was used to create the magnet.”
Hod again showing us that he’s lightyears ahead.
This dodecahedron speaker was shared in Thingiverse in 2012. Projects such as this Raspberry Pi based speaker have been created a number of times as well. And many people have made speaker rings, other spare parts for speakers or things such as wall mounts.
People have even produced horn based speakers, as shown above, or holders for Google Minis. It’s clear that the maker community is really working towards making speakers more extensible and integrating them into our lives. There’s even a Reddit community devoted to DIY audio.
Paul Ellis’s Polymate3D is doing something much more advanced by creating speaker drivers, magnets, and designs and sharing them. The open design movement has not really taken off, but this kind of thing could enable many more people to build much more advanced speakers. In contrast to most of the projects listed in this post, this could truly revolutionize speakers. Below, we can see how Thomas Sanlanderer 3D prints an entire Paul Ellis speaker.
Mass Portal material extrusion printers and Covestro TPU were used for a sieve to reduce interference on these Audiolens speakers.
Disney showed off 3D printed speakers in 2014. Their idea was to use 3D printing for housing to integrate the speakers into our every day lives and, of course, give them mouse ears and the like. They also wanted to show that “both audible sound and inaudible ultrasound can be produced with the same design, allowing for identifying and tracking 3D printed objects in space using common integrated microphones. ”
In 2015, Formlabs showcased flexible SLA resin in its speaker design.
Boaz Dekel’s Aleph speaker has been in development since around 2015. 3D printed on a Stratasys Connex PolyJet machine, the unique design integrates a diffuser, reduces resonance, and is optimized so that it “allows wavefront diffraction to propagate the sound cleanly in a room.”
In 2019, Czech design studio DEEPTIME showed off its speakers, 3D printed from sand. The shape of its Spirula speakers were inspired by ammonite shells. The team touts their unibody design and unique forms.
in 2020, IKEA, together with Teenage Engineering, encouraged us to design and 3D print add-ons to the Swedish furniture giant’s Frekvens speakers. I really believed that IKEA was going to go huge with this, but they didn’t.
26 hour print.
Available on Thingiverse, the Back Load Horn speakers are a doozy of a project, if you’ve got a week to spare. Here you can learn how one user made them.
Node Audio’s super high end HYLIXYA speakers are a now very recognized form. Made with 3D Systems’ powder bed fusion, they’re futuristic and use a radical new shape to engineer superior sound. 3DPrint.com was even given a virtual walkthrough tour of their production process. You can watch that below.
All in all, we can see that there are a number of trends in 3D printing speakers that are notable.
- People are using 3D printing to integrate speakers into cars, their homes, and surround them with enclosures to make them fit into their world.
- There is real open source and maker activity going on, which aims to democratize the fabrication of speakers. This seems rather far off, but it would be quite exciting if we could produce an entire speaker. This has been demonstrated a few times, but it is not yet easy or perfect.
- High-end companies are using 3D printing’s design freedom to manufacture better speaker components, housings, and parts, such as diffusers, to increase the performance of their sound products. Increasingly, 3D printing could play a part in high-end audio and we may at one point see more of this occurring.
Will we all 3D print our speakers at home? This is very unlikely, as we’re mostly lazy and/or busy. Will every speaker be 3D printed? Also highly unlikely, since traditional methods make for inexpensive high-performance products already. Will we change the sound landscape somewhat with uniquely performing shapes and components? This is probably the most likely scenario. Listen to this space.
Stay up-to-date on all the latest news from the 3D printing industry and receive information and offers from third party vendors.
Tagged with: 3d printed speaker • 3D printing speakers • Aleph Zero • aleph2 • diffusers • hylixya\ • hylizya • mass portal • Node Audio • sound • speaker components • speakers
Please enable JavaScript to view the comments powered by Disqus.
3D printing - RD Physics
The first version of our 3D printed coaxial CX loudspeaker series was made using the Desktop Metal Forust method, which is, at the moment, too expensive for most DIY audio enthusiasts. Therefore, the CX2 was designed based on fused filament fabrication (FFF).
3D printing gives design freedom
The starting point for the design is simple but effective: sealed enclosure and coaxial driver. This inherently gives us controlled cone displacement in the low-frequency region and a coherent radiation source in the crossover region. 3D printing allows to easily implement two more acoustically beneficial geometries: large roundovers and compound curved walls. These translate into a Minimal Edge Diffraction Enclosure (MEDE™) and reduced panel vibrations, respectively. Curved walls mean that the loudspeaker requires a stand. This requirement can be turned into a benefit: the symmetric loudspeaker can be tilted or laid on its side when placed on a so-called Isopodd stand 3D printed from soft TPU material. 3D printing allows complex shapes at no extra manufacturing cost. For example, the front baffle is stiffened on the inside with a honeycomb strucure that acts also as support for the overhangs, but robs very little internal volume.
What you need to build your own CX2
- 3D files for 3D printing, sold on Etsy. Dimensions 210x273x170 mm, ~1200 grams of filament.
- SB Acoustics SB13PFCR25-4 COAX or SEAS MP15 (contact us)
- Active crossover, miniDSP recommended
- Two channels of amplification per speaker, ICEpower module recommended
- Neutrik NL4MPR SpeakON connectors and fastON crimp connectors
- 4.2 mm wood screws
- Bitumen or similar visco-elastic damping sheet and fibrous damping material such as pillow stuffing
- Soldering capability (super easy)
How to build it
3D print the enclosures using the files mentioned above. It’s a single-piece print with no support needed. Wood-filled PLA or similar material is easy to sand and no other surface finish besides sanding is needed. If you are using the SEAS drivers you also need to print the TPU gasket/adapter. The speaker can be tilted and rotated when you print a small stand for it from TPU material. Some rubber feet on a plate will do the same job just fine. The assembly order is as follows:
- Finish the outside of the enclosure and make sure the driver and SpeakON connector fit.
- Line the inside with bitumen damping material and fill it quite densily with wadding.
- Solder wires to the speaker drivers and crimp fastON connectors at the other end. Mark woofer and tweeter positive and negative wires.
- Feed the wires through the SpeakON connector opening and mount the driver using wood screws. Use gasket/adaptor if you have the SEAS driver.
- Connect the fastON connectors to you SpeakON connector and mount it.
- Setup your bi-amping and crossover configuration. A good starting point for crossover frequency is 2 kHz. On-axis response will be bright, so keep that in mind when equalizing.
Some toe-in may be beneficial.
Video
3D printed bluetooth speakerWhat’s wrong with having batteries in your portable boombox?
Wireless electronics, such as bluetooth speakers, are extremely popular nowadays. All such devices must have a power source and typically it is a lithium-ion battery. However, the demand for battery raw materials is rising at an alarming rate:
The supply of some of these [battery] materials, in particular cobalt, natural graphite and lithium, is of concern today and for the future in view of the large quantities needed and/or very concentrated supply sources.
European Battery Alliance (EU)
As we have discussed earlier, when launching our Circular Sound program, the best solution for reducing reliance on critical raw materials is to reduce their use. The RD Physics BB1 boombox enables you to do just that. It is designed to use existing external power sources and therefore no new batteries are needed. Battery service-life or battery replacement is no longer a concern.
Alternatives to dedicated batteries
The BB-project started by looking at how power tools are sold without accompanying batteries. The idea being that the user needs only one battery (plus spares) that fits all tools. While this approach reduces the amount of batteries needed, it is also used to tie the customer to a specific brand. We wanted a universal solution and therefore the USB-C standard was chosen. The BB1 and BB2 boomboxes use a USB-C port as an interface to feed power to the amplifier. The boombox can be connected to any USB port: power banks, phone chargers, laptops, extension cords, solar panels etc. Obviously, the input voltage and current draw is limited, which leads to limited sound pressure level (SPL).
Components
What you will need to build your own batteryless boombox:
- Geometry files for 3D printing (free under Creative Commons License at Thingiverse)
- 3D printer big enough to fit a 235 mm diameter sphere
- Slightly over 1 kg of filament depending on your settings
- Two active drivers. Either Peerless 3″ (BB1) or Dayton Audio 4″ (BB2)
- One 6½” Dayton Audio passive resonator
- A Sure (Wondom) bluetooth board with additional cables set
- USB-C panel mount plug (from eBay) and 6 mm DC plug
- Wood screws (4.2 mm for the drivers and resonator, 3 mm for the BT board)
- Drawer handle, IKEA Eneryda 703.475.16
- Damping material (bitumen or similar automotive damping mat and fibrous wadding, for example pillow stuffing)
- Optional: Wall mount bracket, Genelec 4000-410B
- Minimal soldering capabilites
The enclosure for the BB1 and BB2 can be downloaded from the link above. Assembling everything takes 30 minutes.
How to build the BB1/BB2 bluetooth speaker
- Start by soldering the 6 mm DC plug to the USB connector. Red (+) goes to center pin and black (-) to outer shell.
- Connect DC power and speaker cables to bluetooth board and fasten the board inside the enclosure by tightening the screws via the driver openings.
- Mount the USB connector and handle.
- Line the inside of the enclosure with bitumen or similar visco-elastic damping material. Heat will aid in conforming to internal shapes. Make sure the damping material is fully bonded to the walls.
- Bring the speaker wires through the driver openings and solder them to the drivers. Make sure polarity is the same for both drivers. Then fasten the drivers using wood screws.
- Fill the enclosure with fibers (cotton, polyester, wool etc.) and fasten the passive resonator.
- Optional: Attach the wall mount bracket.
- Connect a USB port and the bluetooth board powers on automatically.
Pair your signal source with the device (“WONDOM”). Enjoy!
Assembly instructions
Concept and sound test
3D printed enclosure from BrightBio material and natural blue dyeIntroduction
The loudspeaker industry, like all other industries, needs to transform into a circular economy model. Why? because only 8.6% of the materials we use circulate back into the economy, according to the Circularity Gap Report 2021. We need to increase this number in order to reach the Sustainability Development Goal 12.5 set by the United Nations:
By 2030, substantially reduce waste generation through prevention, reduction, recycling, and reuse.
United Nations Sustainability Development Goal SDG 12.5
Circular Economy of Loudspeakers
Some loudspeaker manufacturers use recycled or renewable enclosure materials, but the biggest problem is circulating the electronics and loudspeaker drivers back into the economy. There is an abundance of old loudspeakers being discarded or sold very cheap every year, because demand for old models has diminished. Buying new loudspeakers made from virgin materials is not sustainable, especially due to the rare-earth elements (REE) used in loudspeaker magnets.
Rare earth elements (REEs) are essential for manufacturing permanent magnets. Permanent magnets are critical components in most decarbonisation technologies.
European Union EIT Raw Materials![]()
The European Union is dependent on imported magnets and REEs. A circular economy model would not only be good for the environment, but also for the reliability of supply chains.
Additive manufacturing enables circular economy
Additive manufacturing offers many opportunities for a circular economy, where repair and remanufacturing are some of the best options to reduce the consumption of mass-produced products made in far-away lands. Circular economy can be described by the 6 REs:
- REduce – Don’t buy anything
- REuse – Buy second-hand
- REpair – Fix it, if it’s broken
- REmanufacture – Make something new using old components
- REcycle – Cycle the raw material back into the economy
- REcover – Burn for energy
As far as loudspeakers are concerned, the best option is of course not to buy anything. The second and third best options are to buy used loudspeakers or fix broken loudspeakers. These two options, however, do not consider the fact that the user may want something different compared to their current product or what is available second-hand. In other words, it does not help if a product can be used forever if nobody wants it anymore. Circular Sound tackles this issue by relying on remanufacturing with the help of 3D printing. In this context, remanufacturing means using the drivers and electronics from old loudspeakers and 3D printing a new enclosure. Obviously, the material of the new enclosure needs to be sustainable, too. Recycled and bio-based plastics are promising, but require special design considerations to obtain the necessary acoustic properties from the enclosure.
RD Physics CS-012 proof-of-concept prototype
The RD Physics CS-012 is the first loudspeaker design in the Circular Sound line-up. The donor components come from an old Yamaha YST-SW012 bass-reflex subwoofer. Additive manufacturing was used to produce a smaller, sealed enclosure loudspeaker. The material used in the prototype is a bio-based material produced by BrightPlus. It has a natural dye made from woad by Natural Indigo Finland. The original Yamaha loudspeaker is designed to be used as a single subwoofer unit placed somewhere on the floor out of sight. The new product, on the other hand, is designed to be used in stereo configuration (2 pcs) and placed under the main speakers. It serves a different function compared to the original product, but no new materials need to be consumed. We are not injecting a new product made from virgin materials into the economy. Instead, we are taking two old ones out and replacing them with one value-added product. This is what Circular Sound is about. You don’t have to wait for distributors to bring sustainable products to your local market.
You can start making these today. The files are shared for free under a Creative Commons license on Thingiverse.
3D printed loudspeakers do not have to be made out of plastic anymore. There is a new way of 3D printing wood called Forust. It is a binder jetting process where upcycled sawdust is used together with a binder to form the closest thing we have to 3D printed wood. We are particularly interested in the possibilities this offers loudspeaker manufacturers.
RD Physics CX1 – A coaxial loudspeaker
RD Physics has been developing speakers with full-range drivers for some time now and while they have their inherent benefits, it is time to look what coaxial drivers have to offer. The starting point was a spherical shape, which is known for its benefits. However, the limitations in build volume favored a shape closer to a rectangular cuboid. The shape of the CX1 has the largest possible roundovers, with the constraints imposed by driver size and maximum baffle dimensions. This is to reduce edge diffraction. The sides are compound curved to maximize stiffness. There is also internal ribbing to stiffen the enclosure without taking up internal volume like a sandwich structure would. The enclosure is made in two parts; the front baffle has a separate cover that conceals the driver flange and mounting screws. The driver is a proprietary SEAS unit designated MP15 (15 cm diameter). The idea is to have an external active crossover and bi-amp the loudspeaker via the Neutrik SpeakOn 4-pin connectors at the back.
3D printing a loudspeaker using Desktop Metal Forust method
The geometry files were sent to Forust for 3D printing. The chosen colour is “natural” with the artificial wood grain introduced during manufacturing. The result is a structure that looks like plywood. Parts can be ordered without the grain and with darker colours, too. The grain is more interesting, however, because various surface texture effects can be achieved by aligning the layers at low angles relative to the principal axes of the printed shape giving a zebra stripe effect.
Post-processing of 3D printed wood
The parts printed with the Forust method can be sanded smooth, but it is not like sanding natural wood. The surface can be varnished, but not stained. The Forust material does not absorb wood stain. It does not tolerate ethanol and perhaps other solvents either. Long-term exposure to water should be avoided, otherwise there will be is a sticky brown residue on the surface. Although a wooden look can be mimicked, post-processing is not similar to wood. Instead, it resembles the wood-filled polymers used in our previous builds. This is not a serious drawback, it just means that 3D printing skills are more useful than woodworking skills. In terms of aesthetics this is the closest thing available for increasing the acceptance of 3D printed loudspeakers in the audio community, where wood veneer is the go-to solution.
Video
- Tags 3d printed, desktop metal, diy audio, forust, Loudspeaker, speaker, wood
The third version of our 3D printed full-range FR loudspeaker series used metal-filled filament to add density and stiffness to the enclosure. It worked in that regard, but the material was unpractial due to brittleness both during printing and in the final product.
What has changed compared to the FR3 speaker
For the fourth version we switched to wood-filled filament, which is more ductile and easier to process. The surface is quite nice straight out of the printer thanks to the matte surface. A quick touch with an orbital sander gives a smooth finish. The spherical shape of the enclosure remains the same as in the FR3 speaker, because it was proven to be very good in terms of resonances and edge diffraction. The diameter of the driver, enclosure and tripod legs was reduced to obtain a more slender design for desktop use. The binding posts are upgraded to sturdy Dayton Audio binding posts. The driver used is the Tang Band W3-1878, and the leadscrews for the legs are 12 mm. Leadscrew nuts are bonded into recesses in the enclosure and allow for adjustment of the legs. Small TPU feet can be printed and placed at the ends of the leadscrews in order to avoid scratching the desktop. These are satellite speakers and need a subwoofer to compliment the lower frequency spectrum.
You can 3D print your own sub and satellite system by purchasing the STL files from our Etsy Shop.
Video
Subwoofer Concept
Our previous 3d printed subwoofer, the SW1, is a 13 liter subwoofer with a 6.5″ driver, a matching passive radiator and a plate amp. We wanted to develop something smaller that would still offer the bass extension that satellite speakers so badly need. The result is the SW2 using a Tang Band W5-1138 5″ long-throw driver and the same Dayton Audio DSA175 passive radiator as in the SW1. The enclosure is now only 5 liters and much easier to fit on a desktop. The passive resonator allows tuning the resonance frequency to avoid overlap with room modes, for example. The spherical shape is optimal for material use and stiffness. Combined with the small diameter driver with large surrounds, the appearance is quite unique. If a traditional box is what you want, then this build is not for you.
Measurements
The measured resonance frequency of the passive radiator indicates that some air-coupling occurs due to the downward firing placement. Simulated resonance frequency matches the measured value (53 Hz) when 16 grams of added mass is used. Mass can be further added using washers to tune the response. In practice, the frequency response starts to drop below 50 Hz. The Arylic amplifier offers DSP capabilites and using a computer as the source allows unlimited DSP with zero cost. Therefore, frequency response in not that meaningful especially when considering the room effects, but we have included some measurements to give an idea of the natural response especially around the lower cut-off.
3D printing
The enclosure is printed in one part (234 mm diameter) and takes approximately 1.5 kg of filament. Print time is about 48 hours. The mass can be increased by lining the walls with sound deadening mat. Although the external wall is spherical, there is a cylindrical inner wall that braces the woofer to the passive resonator and, thanks to a single curvature surface, allows easy installment of thick sound deadening mat. The drivers are fastened using 4.2 mm wood screws. There is a geometry file for a gasket for the woofer which can be printed from TPU. Traditional gasketing methods will work, but the 3D printed gasket is seamless and has the screw hole pattern accurately incorporated. The binding posts are recessed deep into the enclosure and only accept banana plugs in that configuration. An O-ring under the binding post washer is recommended and there is a chamfer for it. 3D printing using a wood-filled filament allows easy sanding for a smooth surface finish. The photos show 15 minutes worth of post-processing making this a very easy and fast build without compromising in function and looks.
Images
Sound quality
The subwoofer was compared to the much larger, THX certified Logitech Z623 subwoofer. The sound is very similar, but in a much smaller package. The SW2 is a great companion for small satellite speakers and brings fullness to the bass. Electronic music will benefit from the “boom” offered by this small unit, while other types of music may require turning down the level a bit for a tighter bass.
Links and video
The 3D files can be found in Etsy store:
https://www.etsy.com/shop/RDPhysics
Please support us by using the affiliate link below just before ordering the components:
TangBand W5-1138 on SoundImports.eu
Dayton Audio DSA175-PR on SoundImports.eu
Arylic 2.1 BT amp on SoundImports.eu
Our 3D printed full-range speakers needed something to beef up the lower end of the frequency spectrum. We set out to design a compact subwoofer that can be used together with our FR3 speakers. The result is a 13 liter enclosure with a 6.5″ driver, a matching passive resonator and a plate amp. The passive resonator allows tuning the resonance frequency to match room modes, for example. The plate amp can power satellite speakers and has a fixed high-pass filter. The low-pass cut-off frequency for the subwoofer can be adjusted and the level too, which means that this system can be easily mated with signal sources that do not have equalizing or DSP capabilities in themselves.
3D printing
The enclosure consists of two parts, which are glued together after printing. Total print time is about 100 hours and uses about 4 kg of filament. Support is only needed for the small recess where the plate amp is mounted. Dual-material printing is not needed. The mass of the enclosure can be increased by filling the walls with epoxy through the holes in the back. A geometry file for 3D printing a matching funnel is provided, too. 2 kg additional mass can be obtained this way.
The 3D files can be found on Thingiverse for free:
https://www.thingiverse.com/thing:4802531
Please support us by using the affiliate link below just before ordering the components:
Dayton Audio DSA175 on SoundImports. eu
Dayton Audio DSA175-PR on SoundImports.eu
Lepai LP210PA amp on SoundImports.eu
Video
The video below explains the concept in more detail.
Metal-filled filament and internal support add significant mass and rigidity.
The first version used internal ribbing and bitumen paint to reduce enclosure resonance. The second version used an external carbon fiber shell. Both approaches were a bit cumbersome. For the third version we wanted to fully use the capabilities of 3D-printing. Therefore, a high-density metal-filled filament was used and internal gyroid-shaped support was used even where overhanging surfaces would not have required it. In addition, height and tilt can be adjusted using three threaded rods that form a tripod. The finished enclosure with three 14 mm trapezoid-threaded nuts bonded to it weighs 1.2 kg.
Please support us by using the affiliate link below for ordering the Dayton Audio RS-100 drivers:
SoundImports.eu
Full-range speaker with carbon fiber skinAdditive manufacturing
Using additive manufacturing (AM) has many benefits over traditional construction methods, such as design freedom, fast product development and integration of functions into one part. There are drawbacks as well. The plastic AM parts tend to be low in mass and not very stiff. Air-tight walls are sometimes difficult to achieve, too. Adding mass by increasing fill density of the print is not a good solution, since it adds build time and material cost. Stiffeners and bitumen paint were used in (Version 1). However, the stiffeners were cumbersome to paint with bitumen and it did not add significant weight. For Version 2, we used the vent as a part of the mechanical structure and used a thicker wall. But some additional means were needed to bring 3D printed enclosures on par with traditional cabinet materials.
Carbon fiber in loudspeker building
Dry carbon fiber tow was wound around the enclosure and then wetted with epoxy resin. The composite skin was sanded after curing and additional coats of epoxy were added. The result is a unique unidirectional carbon fiber surface finish. The composite shell adds mass and stiffness to the enclosure. The loudspeaker sits on four feet printed from TPU material, which allows rotating the speaker.
Make them yourself
The following changes were made to Thingiverse:
- Updating the driver dimensions and screw pattern to the latest Alpair 7 MS.
- The weight of the loudspeaker will try to bend the speaker stand. It was therefore changed from a shell-like structure to a solid.
If you plan to order the drivers, please support us by using the affiliate link below:
SoundImports.eu
Video
Construction
The first version of #3D-Fi speakers are spherical (180 mm diameter) full-range loudspeakers with 3 liter internal volume. The box is vented with two rectangular ports on both sides. The ports act as stiffeners and also give more space to assemble the connectors and amplifier inside the enclosure. Internal wall stiffeners are used in order to maximize internal volume as opposed to simply increasing wall thickness, since a small external size is typically desired while internal volume needs to be high enough for the driver to work properly. We use bitumen paint to both seal the enclosure and also to add mass. The enclosure is printed as one part using UPM Formi3D cellulose composite filament. Metallic nuts are pressed on the backside of the flange to receive the machine threaded screws that hold the emitter.
Setup
Our setup uses a laptop PC as a source which allows equalizing the frequency response at the digital source. The signal is transferred via USB to a USB-powered DAC/pre-amplifier with volume control and a power switch. The analog signal is then transferred to one of the speakers where it is amplified using a two-channel chip amplifier board that is powered by a 65 W laptop charger. The amplified signal of the other channel is then transferred to the other speaker for reproduction. The design uses 6 cm full-range emitters without any analog filters or corrections.
The design was updated for Thingiverse:
- Machine screws and nuts replaced with 2.5 mm hole for wood screws
- Fully passive design without the amp.
Instead, 4 mm holes for binding posts only
- Sealed enclosure
If you like the design and plan on building one yourself, please support us by using the affiliate link below for ordering the components:
MarkAudio Alpair 6 on SoundImports.eu
Sound
A reference system with Genelec 8040 speakers was used for comparison. The sound of the 3D-Fi speakers is very unique and quite tricky to get the most out of. The full-range emitters are very sensitive to off-axis listening and the listening distance also changes the sound markedly. Even slightly tilting one’s head has an effect. It seems that finding the best spot is challenging and takes time. It’s hard to remember not to move an inch while listening to these speakers. However, all the effort pays off, because there is a reward at the end. The sound stage is unbelievably good and there is a huge presence from such a tiny speaker. The Genelecs sound distant and all over the place compared to the very precise and point-like sound of the 3D-Fi speakers. Obviously the bass is not very deep and the sound pressure levels achievable with 6 cm cones is limited. On the other hand, they seem to tolerate significant bass boost without distortion and in normal listening the cone travel stays in check. Overall, a very difficult set of speakers to get into and they are quite picky with the type of music played, but once a good recording is found together with the right listening conditions…Bliss!
Acknowledgements: We wish to thank UPM for the materials and support. J-P Virtanen took the studio pictures and Markus Markkanen the ones in the library.
6 models for 3D printing of speakers. Realize your idea
What is a speaker? This is not just an opportunity to immerse yourself in the world of music. The 3D printed models are a broad view of the solution, from Star Wars-inspired designs to physics-based designs. We have compiled our rating of 3D printed speaker models that pump the most
As a rule, speakers are mostly made of wood and have a boring rectangular shape. And only a few commercial projects have managed to change this by creating products of a higher level and interesting design. Next, we present to your attention a range of desktop speakers with an interesting design. Although in fact, who can forbid you to print products on a larger scale? But before we start, here are some tips:
• The walls of the 3D printed speaker enclosure should be as rigid as possible. This will avoid resonance, which means that the sound will be cleaner.
• A 5mm thick wall with more than 50% fill can provide the basis for a compact cabinet that delivers quality sound.
• The inside of the speaker cabinet should be covered with a soft material. You can use acoustic wool used for damping in loudspeakers. It can even be ordinary wool or glass wool. The sound will be softer, warmer, as the unwanted resonance that creates a piercing sound will be leveled.
Let's get straight to the models...
Model - Spirula
Akemake has introduced a model inspired by the most emblematic design in the field of high-quality sound. We are talking, of course, about the famous Bowers & Wilkins Nautilus speakers. To eliminate negative side effects, they still need some kind of additions. That is why the body took a spiral shape. As a result, unwanted resonances are significantly attenuated, resulting in a much cleaner sound. The best solution is to complement the design with quality material. Wood is ideal for this, as it has the best acoustic characteristics. And for printing, you can use Wood PLA, which will also achieve relative success.
Model - Nomoon
The sphere is one of the most difficult shapes to make, especially when there is some other design on the surface in addition to everything. In this case, 3D printing is the ideal solution. Through 3D printing, it is very easy to create a variety of spherical products with a design.
Initially, Nomoon was not supposed to imitate the Death Star, at least, Rich Olsen, the creator of the design, did not pursue such a goal. But as it turned out, the image of a frightening space station came in handy for solving this problem. The model can be adjusted to the size of the speaker, which is also a big plus.
Model - Super Bass Speaker
This model allows you to increase the reproduction of low frequencies, which is very useful when it comes to jazz or modern dance music. And everything is based on physical laws.
At the very beginning, we noted that for high-quality sound it is necessary to acoustically isolate the front surface from the back. The Super Bass Speaker has a so-called transmission line that shifts the sound wave until it matches the front wave. This is how frequencies are amplified.
Model — Egg-shaped speakers
These speakers are distinguished not only by their original design, but, as practice shows, they are also capable of reproducing very high-quality acoustics. Everything is explained again by physics. In standard rectangular speakers, parallel walls can create negative effects in sound that detract from the overall quality. As a result, the waves are reflected, superimposed, and can interfere with each other, as they are in each other's way. The most ambitious form in the field of Hi-Fi and Hi-End is the egg. The speaker also accompanies the egg-shaped Heine Nielsen, which creates a bass reflex. In simple terms, the speakers are equipped with a hole in the front, which outputs the bass frequencies.
Model - Dodecahedron
Sean Michael Ragana invites you to surprise yourself and your friends with a dodecahedron speaker equipped with 12 speakers. Each of them is directed in its own direction. A very interesting model that allows you to achieve the effect of "sound around".
Model - Modular speaker
Modular speaker offers Paul de Jong for building. This model uses an interesting acoustic effect. You can print a rod of any length, resulting in different performance. If the speakers are placed side by side and connected to the same channel of the amplifier, then the acoustic effect increases in proportion to the number of speakers - that's the math. That is, if you place two speakers side by side, you can get the effect of 4 working freestanding speakers. Such rulers can often be seen at large concerts that are held on the street.
All models presented in the article can be downloaded for FREE at thingiverse.com
More examples of work are presented on our website in the PORTFOLIO section
3D printed speakers - 6 projects that pump the most
3D printed speakers - 6 projects that pump the most
From Star Wars-inspired designs to complex designs using physical phenomena. Let's take a look at some of the coolest 3D printed speakers out there. Immerse yourself in the exciting world of sound!
Traditionally, most hobbyist speakers have been made of wood and shaped like boring rectangular prisms. Only commercial and high-level projects have dared to be more complex and exotic.
Next, we'll take a look at some fun and interesting 3D printed desktop speakers, but there's nothing stopping you from printing larger volume speaker boxes!
Before we dive into the list, here are some general tips for 3D printed speakers:
• The stiffer the cabinet walls, the less unwanted resonance, and therefore the sound will be cleaner. A 5mm wall with more than 50% infill will create a compact enclosure with good sonic properties.
• Acoustic wool for damping loudspeaker enclosures: The interior of the enclosure should be covered with a soft sound-absorbing material such as wool or glass wool. This will produce a softer and warmer sound as it eliminates the resonances that produce a piercing sound.
1. Spirula
Akemake's Spirula is inspired by one of the most iconic designs in the world of high fidelity sound: Bowers & Wilkins' famous Nautilus loudspeakers make the most of their listening experience, but they still need something to eliminate the negative side effects.
To this end, this "box" takes on a helical shape, attenuating unwanted resonances and producing a cleaner sound. In addition to the characteristics of its shape, it is best if this design is made of wood, mainly because of the better acoustic properties. Plastic-printed Wood PLA has also been a relative success.
Thingiverse user Renaud Renaud suggests https://www.thingiverse.com/thing:27
2. Nomoon
One of the hardest shapes to build is the sphere, especially if the surface needs to have a specific design. Once again, additive manufacturing comes to the rescue. With 3D printing, it's easy to create spherical designs with all kinds of customization.
Rich Olsen, the creator of Nomoon, didn't intend to imitate the image of the Death Star, but the frightening space station was perfect for the task. What's more, the design is fully parameterizable, allowing adjustment of the speaker bore diameter.
https://www.thingiverse.com/thing:590871
3.
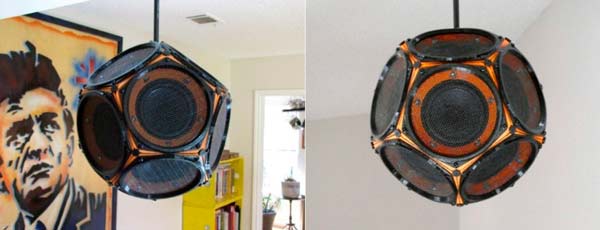
Early on in our journey, we saw the need to acoustically isolate the front of the speaker from its back to avoid sound cancellation. One of the ideas based on the principles of physics is the famous "transmission line".
Here the backward sound wave has to pass through a long channel in the hope that it will be completely extinguished. Since this is practically impossible, the transmission line must at least "shift" the wave to match the frontal wave front, resulting in amplification rather than attenuation. The
Super Bass Speaker by Ozkal Özsoy is supposed to boost low frequencies, giving excellent reproduction of jazz and dance music.
https://www.thingiverse.com/thing:2664657/makes
4. Egg speakers
These egg-shaped speakers not only have a unique design, but also provide a very remarkable acoustic effect.
In traditional rectangular prism speakers, parallel walls create undesirable sound reproduction effects. This is due to the fact that inside the acoustic box, the waves are reflected and interfere with each other when they are on the same path. The solution to this problem is one of the most ambitious shapes in the hi-fi and hi-end world: the 9 egg shape0005 In addition to the roundness of the egg-shaped Heine Nielsen speaker, this is what is known as the bass reflex. This means it has a hole that allows low frequency sounds to contribute to the front sound.
https://www.thingiverse.com/dr_frost_dk/about
5. Dodecahedron columns
If you want to surprise your friends, we recommend this design.
The Dodecahedron Speaker by Thingiverse user Sean Michael Ragan actually has twelve speakers, each pointing in a different direction. This configuration makes it possible to approximate the effect of point source radiation, i.e. sound emitted in all possible directions. Thus, the speaker allows you to study the acoustic characteristics of the room.
https://www.