3D printing places near me
3D Printing | 3D Print Services
Find a 3D Printing Location
Print Functional Prototypes
You can use 3D printing for prototypes or one-of-a-kind items. Let The UPS Store® bring your ideas to life. We can even use your 3D CAD file.
Construct Manufacturing Jigs and Fixtures
We understand when you do your own manufacturing, jigs and fixtures are critical for insuring high-quality and efficiency during assembly and testing. Our 3D printer can create complex parts so you are not dependent on a CNC machine.
Create Custom Accessories
Want to design your own smartphone case or money clip? Most items that are smaller than a breadbox and can be made out of single color of plastic are perfect for 3D printing.
Build Architectural Models
You can work in just about any 3D architectural design program and then export to common 3D CAD file types. The finished product is ready to show off or you can sand and paint your building to give it just the right look.
3D Printing Services Expanded Across Nation
The UPS Store continues to expand 3D printing services nationwide to meet the growing demands of its small business customers. 3D printing now available at approximately 20 The UPS Store locations. Use the interactive map below to find a participating location near you, or check out the full list of all The UPS Store locations offering 3D printing services.
3D CAD and 3D Scanning Services
The UPS Store 3D print locations can now also offer you 3D CAD and 3D scanning services through HoneyPoint3D. Getting a custom 3D print has never been easier - you dream it, HoneyPoint3D designs it, The UPS Store prints it. Enjoy the HoneyPoint3D benefits of an easy quoting process, affordable and quality engineering, online viewing of your 3D files, and efficient turn-around times. Get your 3D CAD or scan quote today!
Netfabb® at The UPS Store®
Participating The UPS Store 3D print locations are utilizing Netfabb software for 3D print file preparation and customization. Services available at these locations include:
- File fixing
- Text labeling
- Logo labeling
- Cutting
Contact or visit these Netfabb locations to learn more about their advanced 3D offerings.
3D Printing Frequently Asked Questions
Here a few questions we frequently hear about 3D Printing.
Please feel free to contact your local The UPS Store for any other questions you may have
-
What is 3D printing?
-
3D Printing is a manufacturing process that uses a digital file to create three-dimensional objects one layer at a time. We run a system that uses ABS plastic and soluble supports to create realistic prototypes and marketing models.
-
What kinds of things can I 3D print?
-
Small business owners and aspiring entrepreneurs will have the opportunity to print prototypes as part of the new product development process. With this printer, The UPS Store locations will be equipped to produce items like engineering parts, functional prototypes, acting props, architectural models, fixtures for cameras, lights and cables.
-
How long does it take to print?
-
The time it takes to print an object will depend on the complexity of the design. A simple object may take 4-5 hours, while a complex object may take 24 hours.
-
Which UPS Store locations are offering 3D printing?
-
The UPS Store is in the process of rolling out nearly 100 3D printing locations across the country. Visit /print/3d-printing/locations for more information.
3D printing - See your ideas come to life. | Staples.com®
3D printing - See your ideas come to life. | Staples.com® | Copy and Print404 Not Found- Need Help?
Federal Government Customers
10+ Employee Businesses
Back to Staples.com
See your ideas come to life.
We make it easy.
3D printing services are now available at Staples® Copy & Print. To get started, either drop off your design file at a participating store or visit our site where you can upload your file or shop our gallery of 100+ designs.
Aliso Viejo, CA
26791 Aliso Creek Rd.
Allentown, PA
4628 Broadway
Bel Air, MD
615 Bel Air Road (US Rt. 1)
Bergenfield, NJ
25 W. Central St.
Boise (Meridian), ID
6299 Eagle Road
Branford, CT
85 North Main Street (Rt.1)
Brooklyn, NY
409 Gateway Drive
2892 Ocean Avenue
Chambersburg, PA
963 Norland Ave
Commack, NY
5003 Jericho Turnpike
Danbury, CT
113 Mill Plain Rd
Doylestown, PA
436 N Main St
East Rutherford, NJ
280 Rt. 17 North
Falls Church, VA
1104 West Broad Street
Hamilton, NJ
550 Marketplace Blvd
Harrisburg, PA
4203 Union Deposit Rd
Hobbs, NM
1781 North Turner Street
Howell, NJ
4514 Rt 9 South
Huntersville, NC
10031 Biddick Lane
Londonderry, NH
41 Nashua RD
Manhasset, NY
1410 Northern Blvd
Manhattan, NY
442 5th Avenue
Mooresville, NC
615 River Highway
Mt Pleasant, SC
845 Houston Northcutt Blvd
New Castle, DE
128 Sunset Blvd
New York, NY
1280 Lexington Ave
Newark, DE
1 Chestnut Hill Plaza
Ocala, FL
1901 East Silversprings Blvd
Palm Desert, CA
72-811 Highway 111
Petaluma, CA
207 South McDowell Blvd
Ramsey, NJ
1300 Rt 17 North
Rancho Santa Margarita, CA
30511 Avenida de las Flores
Raritan, NJ
300 Route 202 @ Somerville Circle
Reading, MA
34 Walkers Brook Dr.
Redmond, WA
15790 Redmond Way
Rochester, NY
1100 Jefferson Rd Suite 12
Roseville, CA
6770 Stanford Ranch Rd.
Salem, MA
17 Paradise Road
San Antonio, TX
18203 Rim Drive 101
San Mateo, CA
2230 Bridgepoint Pkwy
Scottsdale, AZ
15657 N Hayden Rd
Shrewsbury, NJ
1021 Broad St.
Solana Beach, CA
681 San Rodolfo Drive
Staten Island, NY
Staten Island,NY
Stratham, NH
20 Portsmouth Ave.
Studio City, CA
12605 Ventura Blvd
University Park, FL
5429 University Pkwy
West Hartford, CT
2550 Albany Avenue
Westborough, MA
18 Lyman St
Williamsburg, VA
1320 Richmond Rd.
Williamsport, PA
1915 East 3rd St
Wilmington, DE
3200 Kirkwood Highway
Woodland Hills, CA
21500 Victory Blvd
The new possibilities of print.
Think you can't print life-saving medical devices? Think again. With 3D printing's ever-evolving technology, the possibilities are endless. Design and print anything from phone cases and jewelry to working guitars.
Shape your ideas.
3D printing is a simple process capable of creating complex designs that are otherwise impossible to manufacture. It starts with a digital 3D design which has been sliced into 2D layers. Layer by layer, the printer deposits liquid or powdered materials until the final piece is complete.
Test models and prototypes.
Whether you sell custom jewelry at a local boutique or are creating a model before making a full-size version, 3D printing can help increase your speed to market. Products that take months to manufacture can print in days or even hours.
Ready to see what you can create?
Upload your file or shop our gallery of 100+ designs.
Useful in everyday industry.
3D Printing Learning Center
Close
A brief excursion into 3D printing methods / Sudo Null IT News
My previous related posts:
First 3D printing event in the Netherlands
3D printing event (end)
New budget 3D printer
To answer frequently asked questions, I will describe here popular 3D printing technologies - printing with molten plastic, powder, photopolymer, laser sintering. Of course, this information is not the ultimate truth. This is the picture that has developed in my head today from various sources.
Printing with molten material (plastics, chocolate)
This is the most popular method among amateur devices. Its essence is simple. Can you imagine how a glue gun works? A plastic rod is pushed from one end of the gun, and at the other end it is heated to a fluid state and squeezed into the gluing site.
The printer is a machine with 3 axes. The print head is fixed on the machine's coordinate system. When it moves along the X/Y coordinates, the molten plastic is squeezed out of a thin (0.3-0.5mm) nozzle and solidifies. After printing one layer, the printer changes the Z coordinate (lowers platform / raises head) and prints the next layer.
Difference between printers
The main difference between printers is how 3-axis movement is implemented, how the material is fed, whether the table is heated or not, whether printing is supported by 2 materials.
Most printers of the RepRap family move the head only along the X axis. The platform with the object moves along the Y axis. The structure of the print head and the drive along the X axis move along the Z axis. Due to the movement of such a mass, accuracy and print speed suffer.
In Ultimaker and the latest version of Makerbot lit with great fanfare at CES 2012, the print head moves along two axes (X/Y) at the top of the machine, and the platform with the product descends gradually down (along Z). This achieves high quality and print speed, which can be up to 10 times higher than that of Mendel.
In addition to the classic schemes of machine tools inherited from CNC, there are experiments with delta robots.
Plastic
Various plastics are used for printing. The most popular are ABS, from which most toys are made, and PLA, a biodegradable plastic used for packaging and disposable tableware. In addition, special types are used that dissolve in water (PVA) or a special solvent. With such plastic, auxiliary structures can be printed, which are removed at the end. The black plastic in the next photo is such an auxiliary material.
Dual-extruder printer is used to print in two colors or single color with support material. To date, this technology has not yet been worked out in amateur printers. The STL format, chosen as the standard by hobbyists, does not support multiple colors. But the devices are already available, so these problems are already in the process of being solved.
Plastic for printing is sold in coils in the form of a rod of various diameters at a price of about $ 40-60 per kg, water-soluble is more expensive (9$0). Different types of plastic (and other materials such as chocolate) have different operating temperature ranges. A temperature sensor is used to maintain the optimum temperature.
To ensure printing accuracy, the part must not move from its place, therefore it is made so that it sticks to the surface of the platform.
Since the plastic part is printed for a long time, it cools unevenly. Layers printed earlier cool earlier. Therefore, the part tends to deform - to bend. On the one hand, the adhesion must be strong enough to prevent the part from tearing off the platform when cooling, on the other hand, it must be weak enough so that it can be torn off by hand at the end of the process without damaging it.
It is for this that the platform for working with ABS plastic is made heated and a thermal tape (kapton tape) is glued onto the platform, and for working with PLA plastic, masking tape is glued onto the platform (blue in the picture above). In professional printers, the process generally takes place in a closed box, where a high temperature is maintained, ensuring slow cooling and better plastic adhesion. So tape is another consumable for 3D printing.
Powder printing
This technology is used in ZCorp's professional printers. It allows you to print with high resolution in several colors at the same time. The essence is simple - a finely dispersed powder is poured in a thin layer, leveled, then the head goes and, like in an inkjet printer, pours the powder with a binder colored in the desired color. Then everything repeats - a layer of powder, alignment, binder. At the end, the remaining powder is blown out and you're done. Additional material to support hanging elements is not required here - its role is played by powder, which evenly fills the container and serves as a support for subsequent layers. Printers cost from $15k (monochrome ZPrinter 150), color ZPrinter 250 - from $25k.
In addition to plastic filler, happy owners play with other materials. I heard about the use of ceramics and metal. After annealing, a ceramic or metal product is obtained, respectively.
Laser sintering
Almost no different from powder printing. Only instead of a print head, a laser sintering powder is used instead of a binder. They sintered a layer, poured a new one, sintered - poured, etc.
The Bristol branch of the famous aerospace and defense company EADS baked a bicycle using this technology.
These openwork objects are also made using this technology.
In the same way you can make products from refractory materials. Only the laser needs more power.
In 2011, Markus Kaiser made a splash with his solar 3D printer project. Instead of sintered powder, he used sand, which he collected right there in the desert. Instead of laser beams, he used a large Fresnel lens, which concentrated the sun into a point and melted the sand. The author of the project himself acted as a filling and leveling device :) The coordinate system of the printer and the computer were powered by solar batteries. The result is a bowl like this:
The whole process is captured on video:
Photopolymer printing
The principle of operation is simple - we project a slice of the model onto the resin, it freezes where it was lit. Raise the model and add resins, highlight the next cut, and so on.
This printing method is also found among hobbyists and in laboratories due to the simplicity of the device and the accuracy of the result. Here is the device diagram:
There is a cuvette with a photopolymer and a glass bottom. On this bottom, the projector projects the image from below. The software switches images on the projector (sections of the object) and gradually raises the glass platform on which the object grows. As the photopolymer is consumed, it is added to the cuvette. From above, the apparatus is usually closed with a cap that does not transmit a certain spectrum in order to avoid parasitic illumination.
Here is the work of such a printer, created at home:
An example of an object printed on such a printer:
There are many different photopolymers. They cost differently, react to different wavelengths of light, and have different activation times. Therefore, when creating a printer, it is necessary to select the material and the lamp for illumination. Instead of a projector, you can use a laser (a flashlight with a narrow beam) and a scanning system. Then the cut will need to be drawn with a laser, as in laser sintering. If I'm not mistaken, then the consumables for the top printer cost about $300 per liter. But the community interested in building such printers also found a cheap option - about $ 20 per liter. Community, various information on photopolymers, projector, printer, etc. can be found here - 3dprinter.wikidot.com
nano-cemms.illinois.edu - here, with the help of a series of video clips, the 3D printing process in the laboratory is assembled literally on the knee. The polymer is poured into a glass and a conventional projector illuminates the polymer from above through a mirror. The platform on which the object is grown is attached to a small tripod and lowered into the glass. Manually on the projector, the pictures of the slices change and the platform gradually lowers. At the end of the process, the object is immersed in resin. Then it is removed, washed and dried. Of course, the actual process takes many hours. Printing occurs at a speed of several millimeters per hour. So there is no need for automation here.
Added later:
Industrial printers of the Objet Connex family built using this technology can use several different types of photopolymers in one product. In fact, this is a large inkjet printer, with dozens of nozzles connected to containers with different materials. During the printing process, the polymer is applied to the product and immediately illuminated.
Here are examples of objects printed on such a printer at one time:
Printing process:
Many publications point out that 3D printing is the current trend. So we are waiting for accelerated progress in this area, new printers and materials.
update 2:
Lego Chocolate 3D Printer
Update 3:
Homemade resin printer at instructables.com
Selection of materials for 3D printing.
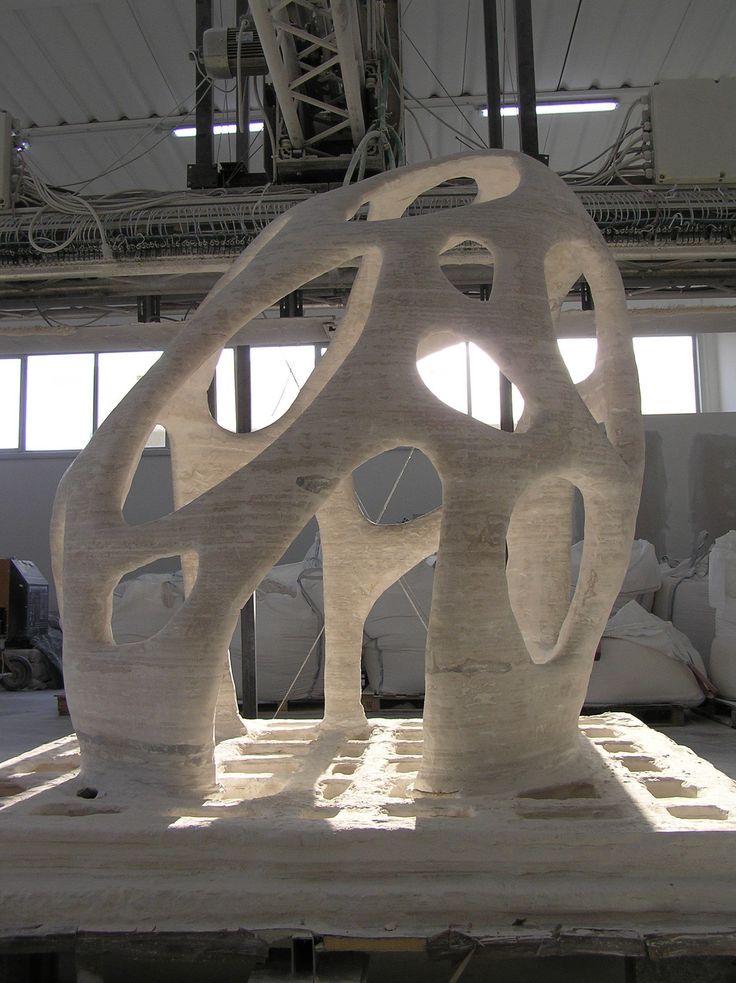
Article applies to printers:
PICASO Designer X PRO Hercules Strong Volgobot A4 ProHello fellow printers!
We are in touch with you again 3DMindex .
The last article received some response, so taking into account all the criticism, I decided to continue writing articles on this topic.
I remind you again that I write about materials for 3D printing in an accessible form, compare the same materials from different manufacturers, talk about the experience of using this material on various equipment, sum up my own rating of manufacturers and talk about the advisability of using one or another material, indirectly touching the print settings. Sem3d .
Also in the comments to the last article, many people asked why I didn’t mention other more / less popular filament manufacturers, I immediately answer this question: I meet a lot of equipment in various CMITs and FabLabs, and by coincidence, 99% of the presented filament is just for these companies, in addition to everything else in home printing, I also use filament only from these manufacturers. Accordingly, I can vouch for my own words.
By tradition, I searched for all the information from different sites, and filled them with a note of subjective opinion.
Let's start:
This article, so to speak, will be a kind of approach to “Engineering plastics”, in it I will tell you about such materials as: PC , FLEX , TPU , PA (NyLLON) , PP , ASA , the issue of composites will also be partially addressed.
To all these materials, one nuance is added, which must be strictly observed during work: ALL THESE MATERIALS MUST BE DRY BEFORE WORK
#1 ASA
ASA (acrylstyrene-acrylonitrile) - even if you are only interested in 3D printing, you are familiar with this material in absentia. This is a complete analogue of ABS - plastic with a small upgrade: ASA unlike ABS is weather resistant, resistant to UV radiation, does not become brittle or yellow in direct sunlight (like ABS ), and is also resistant to dilute acids, mineral oils, diesel fuel.
Print options:
- Extrusion temperature - 240-260°C
- Table temperature - 100-120°C
- Interlayer cohesion - medium (but slightly worse than ABS)
- Table adhesion - medium
- Drying temperature - 60-75°C (time 2-3 hours)
As well as ABS - ACA it is strictly necessary to have a closed printing chamber (preferably with a carbon air filter or have a hood). ACA smells less than ABS , but this does not appear to make it any less toxic. Due to the fact that the interlayer cohesion (sintering) is not good enough - it is recommended to use a thermostated chamber (as in VolgoBot / Creat orBot / Total Z )
Specifications:
- Melting point - 175-210°C
- Softening point - 100°C
- Operating temperature -40+90°C
- Elongation at break - 6%
- Bending strength - 24 MPa
- Tensile strength - 43 MPa
- Tensile modulus - 1.
6 GPa
- Flexural Modulus - 2.1 GPa
- Density - 1.08 g/cm³
- Shrinkage in the manufacture of products - up to 0.8%
- Moisture absorption - 0.45%
- Shore D - 83
Application:
This material has proven itself well when printing any brackets, ceiling lamps and everything else that will be outdoors without paint and any processing. Because it's a doppelgänger ABS , then the usual ABS is also suitable for hidden nodes in order to save money, the plastic itself is suitable for mechanical parts, but do not forget that it is subject to fatigue wear, so long-term loads are contraindicated for it.
Pros:
- Good combination of strength and elasticity makes it suitable for mechanical applications.
- A wide range of temperatures used allows the use of products from it for technical purposes.
- Ease of machining, in combination with chemical smoothing of the surface with inexpensive solvents such as acetone, allows you to make decorative items or cases with a high surface quality.
- Unaffected by UV radiation and various fuels and lubricants.
Cons:
- Does not like drafts when printing, which limits the use of cheap printers with an open case.
- Due to relatively high shrinkage, prone to delamination (separation), requires a heated table and a heat chamber, without them there are problems with the first layer sticking to the table and delamination
- During printing, an unpleasant odor may form, it is better to print in a ventilated room, or to equip the printer with a special exhaust ventilation system, with a conclusion outside the apartment.
Economic component:
Here is a table with manufacturers, with current prices for January 21. Since manufacturers sell coils in different weights, I decided to find the cost of the material per gram of the product by the ratio of price to weight. The result is presented in the column “ ₽/M ”. The column “ Quality ” is completely subjective, because I gave points in it absolutely arbitrarily, based on the experience of working with material from one or another representative, but in general, the quality of today's production mastodons is ± on the same level, and the problems I have with printing can be related to the storage conditions of materials. Column “ Recommendation ”- is the ratio of “ Quality ” to “ ₽ / M ”, it is needed in order to reduce these values to a common denominator, the higher the score in it, the more I recommend material from this manufacturer.
What is the result?
1 seat - Print Product
2nd place - REC
3rd place - Sem3D
4th place - Best Filament
5th place - Filamentarno
Print Product is the leader, and Filamentarno is the outsider. Everything, as always, is connected with the price of the product, perhaps at the present time, in the era of stable production, only pricing plays a key role in the final decision of the client.
For the better, I would like to note the company REC and Sem3d , because in producing this modified material, they did not raise the cost of the product as high as the competitors did. For example, the price of a coil for ABS and ASA from manufacturers such as Bestfilament remained unchanged, but the weight dropped from 1000 g to 500. In percentage terms, the price for the final product increased by 100%.
REC increased the price of this material (from the original ABS) by only 25%
Printproduct by 64%
Sem3d by 25%
Filamentarno by 215%. It would seem that the price tag of is raised up Filamentally, catches the eye, but I hasten to please - not everything is so simple. In addition, this company has not just improved ABS plastic, but a composite based on ASA modified PC (polycarbonate). This symbiosis has a high resistance to burning. Good heat resistance. High strength and impact resistance. It lends itself well to drilling, threading and better tolerates mechanical stress. In addition, the tensile strength increased to 61MPa (according to the manufacturer), which is almost 1.5 times higher than than ABS(43MPa) . In general, this is the TOP for your money, in the presence of a heat chamber (like Volgobot ) - works wonders, and with a simply closed case ( Picaso / Hercules, etc. ) it will not be a big problem like the “naked” PC .
Summing up the above, I can say the following: if you need to print some parts that do not bear mechanical loads, you can take this product from any manufacturer to which the soul lies, or the price suits.
If you are going to print something like electrical appliances, which must carry some kind of load and be protected from fire, then I advise you to take a closer look at the material ASA/PC from Filamentarno .
#2 PP
PP (polypropylene, PP) is a semi-rigid and lightweight 3D printing material that is commonly used in storage and packaging. The semi-crystalline structure of PP causes 3D printing parts to deform heavily when cooled. This makes 3D printing extremely difficult.
Polypropylene itself has been introduced to the market not so long ago. it is complex both in production and in printing. To use it, it is necessary to introduce a number of plasticizers into the composition of the material in order for the work on this material (both production and printing) to be successful. Same Filamentarno claims that their polypropylene is non-shrinking, but this is not entirely true, it is, but not as big.
Print options:
Extrusion temperature - 240-260°C
Table temperature - 45-60°C
Interlayer cohesion - medium
Table adhesion - poor
By itself, polypropylene is not as easy to print as it seems, I would even say that this is one of the most capricious materials to work with.
But there are several problems with it:
First: material ignores many table adhesives. Not a single spray-adhesive from various manufacturers contributes to successful printing, the glue stick "doodle-doodle" is also useless. The only adhesive I know for printing with polypropylene is scotch tape. Oddly enough, but polypropylene tape (brown) can curb this material for you.
Secondly: material cannot be printed with cheap printers. It requires at least a passive thermal chamber, which retains heat, and does not see through. On my Hercules Strong , I can’t make a detail higher than a centimeter at all, Picaso does a little better, because the body is smaller, and the air warms up more evenly in general. Volgobot once again took out with its thermal camera, it turned out to print more or less large parts (about 120x100x80). The most difficult thing was to find a balance between the temperature of the chamber and the airflow so that the material does not flow, and at the same time does not delaminate.
I can give advice on camera temperature, depending on the brand, you need to choose between 60°C and 65°C, as for blowing, you need to look at the model itself, sometimes it is possible to print without blowing, and sometimes it is extremely necessary .
Specifications:
Unfortunately, no manufacturer gives the technical characteristics of this material, so you will have to search the Internet for less reliable sources.
- Melting point - 160-170°C
- Softening point - 70°C
- Operating temperature -20+40°C
- Elongation at break - 200-700%
- Tensile strength - 26-49 MPa
- Density - 0.9 g/cm³
- Shrinkage in the manufacture of products - up to 1.3-3.5%
Application: due to its environmental friendliness, the material is widely used in medicine, as well as for the creation of goods for children. Also, the material shows itself well as a dielectric, so it is not uncommon to use it in mechanical engineering. In theory, this filament is strong and flexible, it is chemically and thermally stable, but for myself I have not found any use in everyday life. The material has good potential, but it is very difficult to implement, perhaps its time has not yet come, and perhaps it exists in vain.
Pros:
- Low material density. Polypropylene has the lowest density of all plastics, which compares favorably with its denser counterparts.
- Resistant to sudden changes in temperature. A quick change in temperature is also not terrible for this material. It withstands the rapid transition from minus to plus and vice versa.
- Excellent dielectric properties. The high dielectric constant together with the high dielectric strength provide ample opportunities for its use as an electrical insulating material.
- Resistant to chemical attack. This feature of the material allows it to be widely used for the needs of chemical enterprises.
It withstands the effects of hot metal, various acids and fumes. In particular, this property is used in the manufacture of air ducts and ventilation for hazardous industries.
- Environmental friendliness and safety for the environment and humans. Numerous experiments have proven the non-toxicity and absolute ecological safety of this material for the environment and humans. Therefore, it is used in the production of water containers, as well as various liquids and bulk food products. Very often it is used in the construction of facilities for water purification.
Cons:
- High print shrinkage.
- High "capriciousness" of the material, requires skill and patience.
- Due to its nature, it is not suitable for printing on non-professional equipment. Requires an active heat chamber.
- Difficult to find application in everyday life.
Economic component:
Due to the fact that not all companies produce this filament, only three manufacturers will have to be considered.
In the “ Experimental Materials ” section, REC sells polypropylene at a price of 1000r per spool. I did not publish this material, but the information is definitely worth considering.
What is the result?
1 seat - Print Product
2nd place - Filamentarno
3rd place - Rec
The pedestal of winners is in front of you. As you can see, the column “ Quality ” sank a lot due to the nature of the material. PrintProduct offers polypropylene at the most “rich” price, but from my own experience I can say that I suffered the most with the material of this manufacturer, this manufacturer also has the largest shrinkage among competitors, which is why the implementation of an already complex material becomes even harder. Regarding filament from REC and Filamentarno then, the quality can be considered at the same level, except that Filamentarno has slightly less shrinkage, but it still exists.
As for my opinion, I think that the material for the money for which we are offered is not needed. Even if we cast the financial issue into the background, the problem of printing this material becomes relevant. The material itself requires expensive equipment and a lot of experience. For certain tasks, you can find a filament cheaper, but easier to use.
#3 PC
PC (polycarbonate, PC) is one of the most common polymers in the industry today. Perhaps there is no person who has not seen this material in everyday life, because. it is widely used in mechanical engineering and just in construction.
Russian filament manufacturers not so long ago released this material for sale, as I remember it was the turn of 2018-2019. As soon as it came out, all users of 3D printers immediately faced a number of problems in working with this material, which, however, I will talk about later. Fortunately, there are modern solutions to overcome these problems.
Print options:
- Extrusion temperature - 265-280°C
- Table temperature - 120°C
- Interlayer cohesion - good
- Table adhesion - poor
One of the problems that I mentioned above is that the material requires high temperatures for printing, and if you have a task to print a body product with a large nozzle diameter and high print speed, then reach 300°C not difficult at all. Plus, printing requires a high bed temperature of up to 120°C . Even with these parameters, it will not be enough to print tall and large products, because. for such needs, an active thermal chamber will be essential (as in VolgoBot/CreatorBot/Total Z ). Shrinkage is to blame, not to say that it is huge, but it is enough so that during printing the corners begin to come off and the model delaminates.
Specifications:
Before you look at the technical specifications, I would like to note that of all the manufacturers presented, only PrintProduct makes a pure PC, while the rest make it composite based on ABS / ASA. Accordingly, many characteristics will vary from manufacturer to manufacturer.
- Melting point - 175-210°C
- Softening point - 100°C
- Operating temperature -100+110°C
- Bending strength - 104 MPa
- Tensile strength - 41 (for composite) MPa, 68 (for pure product) MPa
- Tensile modulus - 2.6 GPa
- Flexural Modulus - 2.1 GPa
- Density - 1.2 g/cm³
- Shrinkage in the manufacture of products - 0.5-0.9%
- Shore D - 83
The material itself is very strong, perhaps one of the most durable mono materials for 3D printing. Another thing that undoubtedly pleases is the large temperature range during operation. The material itself is very wear-resistant, because. it is almost not sawn with a file, so it is perfect for mechanical parts with a constant load.
Application: The material performs well in sliding parts, various bearings/gears. In the presence of an active heat chamber, it will be possible to print large-sized case products at all. PrintProduct also makes this material transparent, with extremely good light transmission, which opens up new doors for imagination and applications.
For me personally, this filament is one of the most used, in case of printing some functional products, on some low details, Hercules does a great job. Also, once there was an order for 3D printing for a functional part measuring 200x200x200 and weighing almost a kilogram, I re-ordered it at the Central Institute of Technology and printed it on a Volgobot A4 PRO printer. It worked out really, really well. As a result, acting as an intermediary, he earned a couple of pieces of silver and left all 3 parties satisfied.
Pros:
- High hardness of the material, and therefore has high strength and impact resistance.
- Good wear resistance.
- Good fire resistance.
- Large operating temperature range.
- Good for drilling and cutting if poorly machined.
Cons:
- Shrinkage during printing and high printing temperatures do not allow the use of this material on non-professional equipment (in the case of pure PC, but it is possible to print on composites). Be sure to have a heat chamber.
- Poor UV resistance. It is recommended not to expose the product to light.
Economic component:
What is the result?
1 seat - REC
2nd place - Sem3D
3rd place - BestFilament
4th place - Filamentarno
5th place - PrintProduct
Now my little comment about the result:
First: I will say that the composite with PC is easier to handle, but has a slightly worse performance.
Secondly: Filamentarno , they have a composite based on ASA / PC , I wrote about this material above, and I see no reason to add something in addition.
Thirdly: REC , deservedly takes the first place in this rating, they have an excellent composite based on ABS / PC . It has a good set of technical characteristics and is easy to use. Also REC offers a composite with PC at the lowest material cost per gram. All in all, a good choice - highly recommended. Sem3D and Bestfilament
I would also like PrintProduct to be noted for the better, as the only manufacturer that produces polycarbonate in a “pure” form. Although it is very difficult to work with, it is their material that has the best technical characteristics among competitors. If the equipment allows you, then this option is for you, I advise everyone.
#4 Nylon(PA)
Nylon (polyamide, PA) is a durable synthetic fiber based on polyamide. This is the first synthetic polymer that surpasses metals in some properties.
The material has been around for a long time, but they have only recently learned how to print it. American analogues of this material have been flooding the Russian market since 2014. The material itself is extremely interesting, and it would be extremely wrong to bypass it, but first things first. As a start, I will say that one of the Russian manufacturers produces a composite based on polyamide, the characteristics of which significantly exceed the characteristics of PEEK in various parameters.
Print options:
- Extrusion temperature - 250-270°C
- Table temperature - 120°C
- Interlayer cohesion - excellent
- Adhesion to the table - poor
- Drying temperature: 4h at T=100°C
The material has a high shrinkage coefficient, due to which it does not have the ability to stick to the table in the "draught" at all. The material is devoid of the ability to exfoliate during printing, tk. The layers stick together incredibly well. So good that the filament has approximately the same tear strength both along the print layers and across. As I said earlier, the material tends to come off the table, in order to avoid this it is necessary to have a heat chamber. On printers such as Hercules and Picaso can be printed, but high details cannot be made, also the early extruders Picaso refused to work with this material, clogged mercilessly. On VolgoBot A4 PRO printing with this material once again justifies itself one hundred percent. For me personally, the presence of this printer "side by side" is very beneficial, sometimes I can take rare, but very expensive orders for printing various power plants, where incredible indicators of strength and service life are needed.
Specifications:
As with polycarbonate, some manufacturers do not produce pure polyamide, but only as part of a composite, this should be taken into account when choosing a filament for printing. Composites are also different, I will release a more detailed article on this topic later.
- Melting point - 150-170°C
- Softening point - 100°C
- Operating temperature -40+90°C
- Tensile strength - 45-53 MPa
- Bending strength - 68 MPa
- Density - 1.07 g/cm³
- Shrinkage in the manufacture of products - 0.7-0.9%
As you can see the material has a high tensile strength (of course not the same as PC, but in combination with an even lower coefficient of friction gives a much longer life of the part). But as you remember, I promised to tell about the composite, about this at the end of the article.
Application: Due to its extremely good wear resistance, low coefficient of friction and resistance to various alcohols, oils and gasoline, the material has unlimited potential for use. For me personally, it has established itself as a material for all occasions. With the most difficult tasks, I turn to this material. Like a PC, having good filament equipment allows you to solve serious problems. In places where the ability to work with heavy loads is required, but at the same time it is advisable to save money, it is recommended to use this particular material. So classically it is used to make various bushings and gears. Compared to PEEK this material is more affordable, plus it has more elasticity, there were times in life when the elasticity of the model was a higher priority.
Pros:
- Excellent interlaminar cohesion makes the model almost cast.
- Incredibly good wear resistance.
- Good resistance to various solvents.
- Not a bad operating temperature range
Cons:
- Print shrinkage and high print temperatures prevent this material from being used on non-professional equipment. Mandatory presence of a thermal chamber.
- Highly hygroscopic.
Economic component:
What is the result?
1st place - Filamentarno
2nd place - PrintProduct
3rd place - REC
4th place - BestFilament
Now I will leave my comment:
First: from the presented manufacturers REC and Filamentarno produce exactly composites, and PrintProduct and BestFilament produce it clean.
REC adds 12% glass fiber and Filamentarno 30% to the composition.
Thanks to the fiberglass in the composition, this composite is endowed with foreign properties, while it should be taken into account that the presence of offal in the composition of the filament changes the properties of the material during printing. The presence of fiberglass in the composition of the filament reduces shrinkage during printing, while the sintering of the layers slightly suffers. It is also worth remembering that fiberglass has great abrasive properties, and therefore brass nozzles are no longer suitable for printing, they simply grind off. You will have to buy steel, or even better diamond, the price of which is extremely high (as for a consumable, but at the same time it cannot be called unjustified)
Now back to the detailed review of the composite with incredible properties. This composite is available from Filamentarno.
And according to the manufacturer, this composite has:
Maximum tensile strength - 190 MPa (PEEK has about 110)
Tensile modulus - 9000MPa
Temperature range - -60 - +250°C
From this we can conclude that this is perhaps one of the most (if not the most) durable material for 3D printing. The cost of filament is absolutely justified, and whenever I need to make a heavy-duty part, I use this material. Of course, this material requires professional equipment, and it does not tolerate inexperience. But to everything else, this material can be called one of the key ones. In my opinion, this material will be at the forefront for a long time, until PEEK, PSU, PEI won't see more use in 3D printing.
Conclusion:
Regarding article: this article does not include material such as Flex/TPU . This is due to the fact that, as for me, these materials are very boring in print. There are many problems with them in printing, they are not amenable to post-processing, and in general there are many nuances in working with them. Of course, there are good examples of printing various insulating pads or dual-extruder printing, when a kind of sleeve of TPU has been integrated into part from ABS .