3D printing machine pdf
Make: 3D Printing Projects - PDF
Jam-packed with eight different projects contributed by a roster of experienced Makers, this book uses 3D printers as a starting point for a number of creative challenges.
$14.99 $7.50 / Sale
Shipping calculated at checkout.
Jam-packed with eight different projects contributed by a roster of experienced Makers, this book uses 3D printers as a starting point for a number of creative challenges. Perfect for the intermediate Maker with some 3D-printing, soldering, and electronics experience, this book utilizes all of the core Maker skills—from electronics to soldering, software to hand assembly—to sharpen your techniques, guarantee success, and get you thinking about the next thing you’d like to build. Some projects you'll build from scratch; others take you through the process of modifying a store-bought item. All have free files for download on Github. Whether you’ve never used a 3D printer or simply let yours gather dust in the workshop, this book will get you Making—and get you thinking about what you’d like to make next!
Projects Included
- A 3D-printed LED lamp
- A '50s-style Raygun pen
- A smart SkyCam
- Animatronic eyes
- An inverted trike RC
- Chauncey the Wrylon Flower Care Robot (first envisioned in 1913!)
- A two-axis camera gimbal
- A BubbleBot
Meet the Authors
Brook Drumm
Brook is the founder and CEO of Printrbot, Inc. Brook is an American maker who set out to start a side business in his garage. After a wildly successful Kickstarter in 2011, Brook was catapulted to the white-hot intersection of crowd funding, 3D printing, and the exploding maker culture. Printrbot is an example of what blood, sweat, and tears can produce if you set your mind and heart on what you are passionate about.
James Floyd Kelly
James is a writer who lives in Atlanta, GA with his wife and two young sons. He has degrees in Industrial Engineering and English and enjoys making things, writing about those things, and training young makers. He has written over 25 books on a variety of subjects from Lego robotics to open source software to building your own CNC machine and 3D printer.
John Edgar Park
John is a producer at Disney Research. He has worked in animation production at Disney for 10 years and has worked in computer graphics since 1994 at various companies, including IBM, Novalogic game studio, and Sony Pictures Imageworks. John was the host and co-writer of the Emmy Award-nominated series Make: Television. He regularly demos his projects at Maker Faires, and builds and writes about technology projects for Make: magazine and other places online and in print.
Brian Roe
Brian is a tinkerer at heart and a Mechanical Designer by trade. His diverse career has led him down many interesting paths. He has worked as a creature creator for Hollywood films, and was part of a successful combat robot team for the show Battlebots. He also assisted with the design of the 3D cameras used for the film Avatar. Currently, he’s an engineer at Printrbot and working on The 10,000 Year Clock project for The Long Now Foundation.
Steven Bolin
Steven is Printrbot’s Production Manager and R&D department assistant. He has always enjoyed working with his hands, from construction to just projects around the house, and finds designing and building 3D printers an absolute joy. As a father of two kids and a former Youth Pastor, he loves making and playing with toys and 3D printing naturally lends itself to this hobby. Steven hopes to continue developing new products that incorporate 3D printing into everyday life.
Rick Winscot
Rick has code in brain, soldering iron in hand, and Art Blakey blaring in the background. He transforms techno-babble into reality… and is strangely fond of the ellipsis.
John Baichtal
John writes books about toys, tools, robots, and hobby electronics. His first book was The Cult of Lego, an exploration of the culture and work of adult Lego builders. He’s also the author of Maker Pro, Robot Builder, and The Locksmith’s Apprentice, a fantasy novel. He lives in Minneapolis with his wife and three children.
Nick Ernst
Nick served in the Marine Corps for eight years, then decided to go back toschool to pursue a career in Electronics Engineering. Before working on electronics at Printrbot Inc., he spent two years at Parallax Inc. as the lead developer of the Elev-8 multi-rotor platform. He’s a Maker at heart, and enjoys tinkering and hacking on all shapes and sizes of electronics. He believes that if it ain’t broken, you haven’t tinkered enough!
Caleb Cotter
Caleb is an R&D Specialist at Printrbot. He’s a maker with a passion for 3D printing and rapid prototyping, and is fascinated with the opportunities presented by desktop manufacturing. When he’s not in his garage hacking—he’s still in his garage wrenching on his car.
What is 3D printing? How does a 3D printer work? Learn 3D printing
3D printing or additive manufacturing is a process of making three dimensional solid objects from a digital file.
The creation of a 3D printed object is achieved using additive processes. In an additive process an object is created by laying down successive layers of material until the object is created. Each of these layers can be seen as a thinly sliced cross-section of the object.
3D printing is the opposite of subtractive manufacturing which is cutting out / hollowing out a piece of metal or plastic with for instance a milling machine.
3D printing enables you to produce complex shapes using less material than traditional manufacturing methods.
Table of Contents
- How Does 3D Printing Work?
- 3D Printing Industry
- Examples of 3D Printing
- 3D Printing Technologies & Processes
- Materials
- Services
Jump to your field of interest:
- Rapid Prototyping & Manufacturing
- Automotive
- Aviation
- Construction
- Consumer Products
- Healthcare
- Food
- Education
Jump to process:
- All Technologies & Processes
- Vat Photopolymerisation
- Material Jetting
- Binder Jetting
- Material Extrusion
- Powder Bed Fusion
- Sheet Lamination
- Directed Energy Deposition
How Does 3D Printing Work?
It all starts with a 3D model. You can opt to create one from the ground up or download it from a 3D library.
3D Software
There are many different software tools available. From industrial grade to open source. We’ve created an overview on our 3D software page.
We often recommend beginners to start with Tinkercad. Tinkercad is free and works in your browser, you don’t have to install it on your computer. Tinkercad offers beginner lessons and has a built-in feature to export your model as a printable file e.g .STL or .OBJ.
Now that you have a printable file, the next step is to prepare it for your 3D printer. This is called slicing.
Slicing: From printable file to 3D Printer
Slicing basically means slicing up a 3D model into hundreds or thousands of layers and is done with slicing software.
When your file is sliced, it’s ready for your 3D printer. Feeding the file to your printer can be done via USB, SD or Wi-Fi. Your sliced file is now ready to be 3D printed layer by layer.
3D Printing Industry
Adoption of 3D printing has reached critical mass as those who have yet to integrate additive manufacturing somewhere in their supply chain are now part of an ever-shrinking minority. Where 3D printing was only suitable for prototyping and one-off manufacturing in the early stages, it is now rapidly transforming into a production technology.
Most of the current demand for 3D printing is industrial in nature. Acumen Research and Consulting forecasts the global 3D printing market to reach $41 billion by 2026.
As it evolves, 3D printing technology is destined to transform almost every major industry and change the way we live, work, and play in the future.
Examples of 3D Printing
3D printing encompasses many forms of technologies and materials as 3D printing is being used in almost all industries you could think of. It’s important to see it as a cluster of diverse industries with a myriad of different applications.
A few examples:
- – consumer products (eyewear, footwear, design, furniture)
- – industrial products (manufacturing tools, prototypes, functional end-use parts)
- – dental products
- – prosthetics
- – architectural scale models & maquettes
- – reconstructing fossils
- – replicating ancient artefacts
- – reconstructing evidence in forensic pathology
- – movie props
Rapid Prototyping & Rapid Manufacturing
Companies have used 3D printers in their design process to create prototypes since the late seventies. Using 3D printers for these purposes is called rapid prototyping.
Why use 3D Printers for Rapid Prototyping?
In short: it’s fast and relatively cheap. From idea, to 3D model to holding a prototype in your hands is a matter of days instead of weeks. Iterations are easier and cheaper to make and you don’t need expensive molds or tools.
Besides rapid prototyping, 3D printing is also used for rapid manufacturing. Rapid manufacturing is a new method of manufacturing where businesses use 3D printers for short run / small batch custom manufacturing.
Automotive
Car manufacturers have been utilizing 3D printing for a long time. Automotive companies are printing spare parts, tools, jigs and fixtures but also end-use parts. 3D printing has enabled on-demand manufacturing which has lead to lower stock levels and has shortened design and production cycles.
Automotive enthusiasts all over the world are using 3D printed parts to restore old cars. One such example is when Australian engineers printed parts to bring a Delage Type-C back to life. In doing so, they had to print parts that were out of production for decades.
Aviation
The aviation industry uses 3D printing in many different ways. The following example marks a significant 3D printing manufacturing milestone: GE Aviation has 3D printed 30,000 Cobalt-chrome fuel nozzles for its LEAP aircraft engines. They achieved that milestone in October of 2018, and considering that they produce 600 per week on forty 3D printers, it’s likely much higher than that now.
Around twenty individual parts that previously had to be welded together were consolidated into one 3D printed component that weighs 25% less and is five times stronger. The LEAP engine is the best selling engine in the aerospace industry due to its high level of efficiency and GE saves $3 million per aircraft by 3D printing the fuel nozzles, so this single 3D printed part generates hundreds of millions of dollars of financial benefit.
GE’s fuel nozzles also made their way into the Boeing 787 Dreamliner, but it’s not the only 3D printed part in the 787. The 33-centimeter-long structural fittings that hold the aft kitchen galley to the airframe are 3D printed by a company called Norsk Titanium. Norsk chose to specialize in titanium because it has a very high strength-to-weight ratio and is rather expensive, meaning the reduction in waste enabled by 3D printing has a more significant financial impact than compared to cheaper metals where the costs of material waste are easier to absorb. Rather than sintering metal powder with a laser like most metal 3D printers, the Norsk Merke 4 uses a plasma arc to melt a metal wire in a process called Rapid Plasma Deposition (a form of Directed Energy Deposition) that can deposit up to 10kg of titanium per hour. A 2kg titanium part would generally require a 30kg block of titanium to machine it from, generating 28kg of waste, but 3D printing the same part requires only 6kg of titanium wire.
Construction
Is it possible to print a building? – yes it is. 3D printed houses are already commercially available. Some companies print parts prefab and others do it on-site.
Most of the concrete printing stories we look at on this website are focused on large scale concrete printing systems with fairly large nozzles for a large flow rate. It’s great for laying down concrete layers in a fairly quick and repeatable manner. But for truly intricate concrete work that makes full use of the capabilities of 3D printing requires something a little more nimble, and with a finer touch.
Consumer Products
When we first started blogging about 3D printing back in 2011, 3D printing wasn’t ready to be used as a production method for large volumes. Nowadays there are numerous examples of end-use 3D printed consumer products.
Footwear
Adidas’ 4D range has a fully 3D printed midsole and is being printed in large volumes. We did an article back then, explaining how Adidas were initially releasing just 5,000 pairs of the shoes to the public, and had aimed to sell 100,000 pairs of the AM-infused designs by 2018.
With their latest iterations of the shoe, it seems that they have surpassed that goal, or are on their way to surpassing it. The shoes are available all around the world from local Adidas stores and also from various 3rd party online outlets.
Eyewear
The market of 3D printed eyewear is forecasted to reach $3.4 billion by 2028. A rapidly increasing section is that of end-use frames. 3D printing is a particularly suitable production method for eyewear frames because the measurements of an individual are easy to process in the end product.
But did you know it’s also possible to 3D print lenses? Traditional glass lenses don’t start out thin and light; they’re cut from a much larger block of material called a blank, about 80% of which goes to waste. When we consider how many people wear glasses and how often they need to get a new pair, 80% of those numbers is a lot of waste. On top of that, labs have to keep huge inventories of blanks to meet the custom vision needs of their clients. Finally, however, 3D printing technology has advanced enough to provide high-quality, custom ophthalmic lenses, doing away with the waste and inventory costs of the past. The Luxexcel VisionEngine 3D printer uses a UV-curable acrylate monomer to print two pairs of lenses per hour that require no polishing or post-processing of any kind. The focal areas can also be completely customized so that a certain area of the lens can provide better clarity at a distance while a different area of the lens provides better vision up close.
Jewelry
There are two ways of producing jewelry with a 3D printer. You can either use a direct or indirect production process. Direct refers to the creation of an object straight from the 3D design while indirect manufacturing means that the object (pattern) that is 3D printed eventually is used to create a mold for investment casting.
Healthcare
It’s not uncommon these days to see headlines about 3D printed implants. Often, those cases are experimental, which can make it seem like 3D printing is still a fringe technology in the medical and healthcare sectors, but that’s not the case anymore. Over the last decade, more than 100,000 hip replacements have been 3D printed by GE Additive.
The Delta-TT Cup designed by Dr. Guido Grappiolo and LimaCorporate is made of Trabecular Titanium, which is characterized by a regular, three-dimensional, hexagonal cell structure that imitates trabecular bone morphology. The trabecular structure increases the biocompatibility of the titanium by encouraging bone growth into the implant. Some of the first Delta-TT implants are still running strong over a decade later.
Another 3D printed healthcare component that does a good job of being undetectable is the hearing aid. Nearly every hearing aid in the last 17 years has been 3D printed thanks to a collaboration between Materialise and Phonak. Phonak developed Rapid Shell Modeling (RSM) in 2001. Prior to RSM, making one hearing aid required nine laborious steps involving hand sculpting and mold making, and the results were often ill-fitting. With RSM, a technician uses silicone to take an impression of the ear canal, that impression is 3D scanned, and after some minor tweaking the model is 3D printed with a resin 3D printer. The electronics are added and then it’s shipped to the user. Using this process, hundreds of thousands of hearing aids are 3D printed each year.
Dental
In the dental industry, we see molds for clear aligners being possibly the most 3D printed objects in the world. Currently, the molds are 3D printed with both resin and powder based 3D printing processes, but also via material jetting. Crowns and dentures are already directly 3D printed, along with surgical guides.
Bio-printing
As of the early two-thousands 3D printing technology has been studied by biotech firms and academia for possible use in tissue engineering applications where organs and body parts are built using inkjet techniques. Layers of living cells are deposited onto a gel medium and slowly built up to form three dimensional structures. We refer to this field of research with the term: bio-printing.
Food
Additive manufacturing invaded the food industry long time ago. Restaurants like Food Ink and Melisse use this as a unique selling point to attract customers from across the world.
Education
Educators and students have long been using 3D printers in the classroom. 3D printing enables students to materialize their ideas in a fast and affordable way.
While additive manufacturing-specific degrees are fairly new, universities have long been using 3D printers in other disciplines. There are many educational courses one can take to engage with 3D printing. Universities offer courses on things that are adjacent to 3D printing like CAD and 3D design, which can be applied to 3D printing at a certain stage.
In terms of prototyping, many university programs are turning to printers. There are specializations in additive manufacturing one can attain through architecture or industrial design degrees. Printed prototypes are also very common in the arts, animation and fashion studies as well.
Types of 3D Printing Technologies and Processes
The American Society for Testing and Materials (ASTM), developed a set of standards that classify additive manufacturing processes into 7 categories. These are:
- Vat Photopolymerisation
- Stereolithography (SLA)
- Digital Light Processing (DLP)
- Continuous Liquid Interface Production (CLIP)
- Material Jetting
- Binder Jetting
- Material Extrusion
- Fused Deposition Modeling (FDM)
- Fused Filament Fabrication (FFF)
- Powder Bed Fusion
- Multi Jet Fusion (MJF)
- Selective Laser Sintering (SLS)
- Direct Metal Laser Sintering (DMLS)
- Sheet Lamination
- Directed Energy Deposition
Vat Photopolymerisation
A 3D printer based on the Vat Photopolymerisation method has a container filled with photopolymer resin. The resin is hardened with a UV light source.
Stereolithography (SLA)
SLA was invented in 1986 by Charles Hull, who also at the time founded the company, 3D Systems. Stereolithography employs a vat of liquid curable photopolymer resin and an ultraviolet laser to build the object’s layers one at a time. For each layer, the laser beam traces a cross-section of the part pattern on the surface of the liquid resin. Exposure to the ultraviolet laser light cures and solidifies the pattern traced on the resin and fuses it to the layer below.
After the pattern has been traced, the SLA’s elevator platform descends by a distance equal to the thickness of a single layer, typically 0.05 mm to 0.15 mm (0.002″ to 0.006″). Then, a resin-filled blade sweeps across the cross section of the part, re-coating it with fresh material. On this new liquid surface, the subsequent layer pattern is traced, joining the previous layer. Depending on the object & print orientation, SLA often requires the use of support structures.
Digital Light Processing (DLP)
DLP or Digital Light Processing refers to a method of printing that makes use of light and photosensitive polymers. While it is very similar to SLA, the key difference is the light source. DLP utilizes other light sources like arc lamps. DLP is relatively quick compared to other 3D printing technologies.
Continuous Liquid Interface Production (CLIP)
One of the fastest processes using Vat Photopolymerisation is called CLIP, short for Continuous Liquid Interface Production, developed by Carbon.
Digital Light Synthesis
The heart of the CLIP process is Digital Light Synthesis technology. In this technology, light from a custom high performance LED light engine projects a sequence of UV images exposing a cross section of the 3D printed part causing the UV curable resin to partially cure in a precisely controlled way. Oxygen passes through the oxygen permeable window creating a thin liquid interface of uncured resin between the window and the printed part known as the dead zone. The dead zone is as thin as ten of microns. Inside the dead zone, oxygen prohibits light from curing the resin situated closest to the window therefore allowing the continuous flow of liquid beneath the printed part. Just above the dead zone the UV projected light upwards causes a cascade like curing of the part.
Simply printing with Carbon’s hardware alone does not allow for end use properties with real world applications. Once the light has shaped the part, a second programmable curing process achieves the desired mechanical properties by baking the 3d printed part in a thermal bath or oven. Programmed thermal curing sets the mechanical properties by triggering a secondary chemical reaction causing the material to strengthen achieving the desired final properties.
Components printed with Carbon’s technology are on par with injection molded parts. Digital Light Synthesis produces consistent and predictable mechanical properties, creating parts that are truly isotropic.
Material Jetting
In this process, material is applied in droplets through a small diameter nozzle, similar to the way a common inkjet paper printer works, but it is applied layer-by-layer to a build platform and then hardened by UV light.
Material Jetting schematics. Image source: custompartnet.comBinder Jetting
With binder jetting two materials are used: powder base material and a liquid binder. In the build chamber, powder is spread in equal layers and binder is applied through jet nozzles that “glue” the powder particles in the required shape. After the print is finished, the remaining powder is cleaned off which often can be re-used printing the next object. This technology was first developed at the Massachusetts Institute of Technology in 1993.
Binder Jetting schematicsMaterial Extrusion
Fused Deposition Modeling (FDM)
FDM schematics (Image credit: Wikipedia, made by user Zureks)FDM works using a plastic filament which is unwound from a spool and is supplied to an extrusion nozzle which can turn the flow on and off. The nozzle is heated to melt the material and can be moved in both horizontal and vertical directions by a numerically controlled mechanism. The object is produced by extruding melted material to form layers as the material hardens immediately after extrusion from the nozzle.
FDM was invented by Scott Crump in the late 80’s. After patenting this technology he started the company Stratasys in 1988. The term Fused Deposition Modeling and its abbreviation to FDM are trademarked by Stratasys Inc.
Fused Filament Fabrication (FFF)
The exactly equivalent term, Fused Filament Fabrication (FFF), was coined by the members of the RepRap project to give a phrase that would be legally unconstrained in its use.
Powder Bed Fusion
Selective Laser Sintering (SLS)
SLS uses a high power laser to fuse small particles of powder into a mass that has the desired three dimensional shape. The laser selectively fuses powder by first scanning the cross-sections (or layers) on the surface of a powder bed. After each cross-section is scanned, the powder bed is lowered by one layer thickness. Then a new layer of material is applied on top and the process is repeated until the object is completed.
Multi Jet Fusion (MJF)
Multi Jet Fusion technology was developed by Hewlett Packard and works with a sweeping arm which deposits a layer of powder and then another arm equipped with inkjets which selectively applies a binder agent over the material. The inkjets also deposit a detailing agent around the binder to ensure precise dimensionality and smooth surfaces. Finally, the layer is exposed to a burst of thermal energy that causes the agents to react.
Direct Metal Laser Sintering (DMLS)
DMLS is basically the same as SLS, but uses metal powder instead. All unused powder remains as it is and becomes a support structure for the object. Unused powder can be re-used for the next print.
Due to of increased laser power, DMLS has evolved into a laser melting process. Read more about that and other metal technologies on our metal technologies overview page.
Sheet Lamination
Sheet lamination involves material in sheets which is bound together with external force. Sheets can be metal, paper or a form of polymer. Metal sheets are welded together by ultrasonic welding in layers and then CNC milled into a proper shape. Paper sheets can be used also, but they are glued by adhesive glue and cut in shape by precise blades.
Simplified schematics of ultrasonic sheet metal process (Image credit: Wikipedia from user Mmrjf3)Directed Energy Deposition
This process is mostly used in the metal industry and in rapid manufacturing applications. The 3D printing apparatus is usually attached to a multi-axis robotic arm and consists of a nozzle that deposits metal powder or wire on a surface and an energy source (laser, electron beam or plasma arc) that melts it, forming a solid object.
Materials
Multiple materials can be used in additive manufacturing: plastics, metals, concrete, ceramics, paper and certain edibles (e.g. chocolate). Materials are often produced in wire feedstock a.k.a. filament, powder form or liquid resin. Learn more about our featured materials on our materials page.
Services
Looking to implement 3D printing in your production process? Get a quote for a custom part or order samples on our 3D print service page.
Page not found - Wall Printer
10/25/2020. UV Wall Printer Upgrades.
All the UV wall printers can be upgraded to the latest version software, which will significantly improve your printing quality.
11/01/2020. PhotoPrint RIP Software Available
All wall printers can be installed by PhotoPrint RIP Software as optional. If you need it, contact your engineer.
03/12/2021 Ink Level Alarm Tank is Available
UV wall printer has equipped with the ink level alarm tank. 5 ink tanks, 260ml each. White ink will be with the stirrer.
04/12/2021 The World's First Floor Printer is Ready
The Floor Printer can print directly on the ground. Check more: 3D parking spot printer machine
Jan.14th, 2022 The latest LED UV Wall Printer "T series" has been released
T series is the most portable UV wall printer HKHR tech has been made. It can be split into 6 parts and each one is no more than 15kg. What’s more, it also combined the rails driving system and wheel driving system in one model. Introducing the "T series" UV wall printer
For technical support, please contact our engineer Adam: tech@wallpaintingmachine. com
For sales inquiry, please contact our sales director Alex: [email protected]
Everything You should Know About Wall Printer
The Ultimate Guide For How to Choose the Best Wall Printing Machine
Everything you should know about the wall printer.
Support
SAi FlexiPrint RIP SoftwareWe can pre-installed the US PhotoPrint RIP software for all UV printers and water-based ink printers.
After printing tests and calibration curves, the output ink quality of all series of HKHR wall printers has been significantly improved.
Language: English, Portuguese, French, Italian, German, Spanish, Chinese, Japanese, Korean, Dutch, Danish, Finnish, Russian uses 5 basic colors of CMYK+White , which can print on dark background walls (such as gray, blue, black, etc.).
At the same time, it can also print white colors independently, which is more suitable for some special scenes.
How to Unpack & Assemble & Operate The Wall Printer
We have packed 6 UV wall printing machines in the factory. Three of them were sent to the United States. The unboxing video was shot and edited in the United States.
This video also shows how to operate our wall printer .
High Resolution Printing
All series of our wall printers support up to 16pass, 2880dpi printing resolution.
The original scene of the picture is vividly restored, which is full of praise.
Portable UV Wall Printer—The Best Selling Wall Printer
You can choose a wheeled wall printer. It can move on its own automatically and can be applied to flat indoor floors.
Equipped with height-adjustable guide rails, allowing you to print easily outdoors. Disassembly, transportation, and installation are very convenient, 10 minutes is enough! (TWP is our distributor for North America)
Watch the video tutorial for taking down and setting up the Wheeled UV wall printer
You will Never Be worried About Power Cut and Sudden Accidents for stopping Printing
We have developed the power -off supplement function .
It allows you to set up the software to continue to finish your work next time when power is lost, raining, and various emergency situations have to be suspended. nine0009
There is no need to return the guide rail to its original position, it can be completed by software and laser calibration.
Check the supplement tutorial --->>
Amazing Stitching Ability Allows You to Print Murals Up to 10 Meters High
Excellent expansion performance.
We can customize the vertical rail of the wall printing machine for you to adapt to the indoor height of different countries.
At the same time, we can add an extension rod for you to obtain a one-time printing height of up to 3 meters. nine0009
And through powerful operating software, you can use stitching technology to obtain larger-format pictures.
Four Printheads and The Fastest Wall Printing Speed You Have Never Seen
The water-based model of wall printer machine is equipped with up to 4 Epson print heads, each of which works independently and can print 80m2 per hour in the 2 Pass mode.
Such an amazing high-speed printing technology is already ranked first in the world in the field of vertical inkjet printers. nine0009
UV Curing System with Air-Cooled UV Lamp
that of the water-cooled UV lamp.
At the same time, the UV curing effect is more efficient, suitable for printing on various materials. Such as walls of any material, metal, glass, wood, canvas, plastic, ceramic tiles, etc.
The Seventh Generation
EPSON Micro-Piezo Printhead We use high-quality EPSON micro-piezo print heads for all series of printers. We refuse to use cheap, inferior, and second-hand EPSON print heads.
Because we know that the quality of the nozzle directly affects the printing effect and the life of the wall printer.
High-Quality and Stable Components
We use 3 independent power supplies to avoid interference; The frame uses high-quality steel to increase its rigidity and precision; At the same time, we use large wheels to increase precision and anti-skid. . . nine0009
We only purchase top-quality accessories to provide customers with safe, assured, durable products, and user experience. Save Your Time, Save Your Money
Only the colored areas are printed. And the white area, the print head no longer scans to save time. nine0009
Watch carefully at the end printing for the tail, the printhead just prints the area for the tail, not scan other white areas.
Eco-friendly ink
Our printer uses environmentally friendly and durable highly colored pigment ink, which can be used in any scene.
At the same time, you can purchase high-quality printer inks suitable for our machines worldwide.
Tracking System to keep the right distance to the wall
The entire series of our wall printers are equipped with two American Banner ultrasonic sensors so that the print head can print on curved and uneven surfaces. nine0009
Which means it can automatically follow the wall without worrying about the flatness of the wall.
Manual Laser Calibration Function
The manual laser calibration function allows you to better grasp the status of the machine.
Come Follow The Lens And Visit Our Factory
We are a vertical printing technology company with R&D capabilities. We are not a trading company or an assembly company for the wall printer .
You deserve to have a professional after-sales guarantee.
Pantents and Certifications
We have the most comprehensive certifications and patents, two invention patents for the wall printer, and 8 other patents.
In addition, we have a CE certificate, ink certificate, and so on. We prove ourselves through strength and service, not sales words.
R&D Ability
All the PCB motherboards for wall printer and programming systems for wall printers are developed by us, so our machine update iteration is very fast.
After-sales support is more convenient, and there is no need to contact the motherboard supplier to resolve customer questions.
The motherboard and program are very stable. As we have been supplying the inkjet printer market for more than 10 years.
Market Share
We have more than 2,000 customers in China, this is just a part of these cases. nine0009
Dealership and Agents
We have very good partners in the United States, Russia, and the Czech Republic. . .
—> Dealership network over the world
We provide high-quality products and reliable services to win more and more partners.
Do you want to join us too?
Aging Test
We will do 24 hours aging test for all the wall printers before shipping, making sure they are all in good condition. nine0009
After-sales Guarantee And Technical Support
We provide a one-year after-sales guarantee . Our after-sales team has rich experience , has served the Chinese market for a long time, and can speak Good English. They Can solve technical problems for you through video calls.
We send accessories through FedEx and DHL, and we will bear the first year’s cost. WhatsApp: 86 15952051055
How to print 10m * 12m photo wallpaper on the wall with a wall printer? nine0070
BlogBy Alex Wang
Our smart Chinese customers have printed a HUGE 10m x 12m mural on the wall using the stitching function of the software wall printer. The standard print height of the wall printer is 2 meters, but we have developed the STAPLE FUNCTION in the software. If you want to print a large mural on the wall, you just need to lift the printer by the platform and print...
Read more
CMYK + White Wall Mounted UV Printer with Wheel and Guide Show Show
BlogBy Alex Wang
This is a great video made by our partner in Ukraine. If you want to know more about them and our dealers and agents around the world, please click here: Worldwide Wall Printer Agents and Dealers By watching this video, you can see how amazing the S Series UV Wall Printer can do. Using white ink, he…
Read more
Everything you need to know about the wall printer
BlogBy Alex Wang
This article is contributed by our engineer Adam. Now he works for Beijing Huake Hengrun Intelligent Technology Company, which is the most professional wall printer manufacturer in China. We sell wall printer abroad. I have been designing and manufacturing wall printers since 2011. I have witnessed how the scale of this industry has grown from small to large, and ...
Read more
Russia UV Wall Printer, Steel Wall Printing
BlogBy Alex Wang
This video has been verified by our Russian agent. They use UV S series wall printer to print on the steel wall.
Read more
King of Oman print on wall with wall printer
BlogBy Alex Wang
We use HK-K2 wall printer, a water based pigment ink wall printer with 2 print heads. Seal of the King of Oman on the wall. nine0009
Read more
Wall print depicting the Hindu god - Lord Ganesha
BlogBy Alex Wang
The HK-K2 #wallprintingmachine has two Epson nozzles to print high quality posters quickly and efficiently.
Read more
Universal UV Wall Printer[2021 Updatd]
BlogBy Alex Wang
How to choose the right wall printer for you? What to choose: a printer with water-based ink or UV curing ink? I suggest you choose an all-in-one UV printer if your printing business has a lot of different print materials. What materials can UV wall printers print on? In theory, UV wall printers can print on any material. Such as walls, acrylic, glass,…
Read more
Page not found - Wall Printer
10/25/2020.
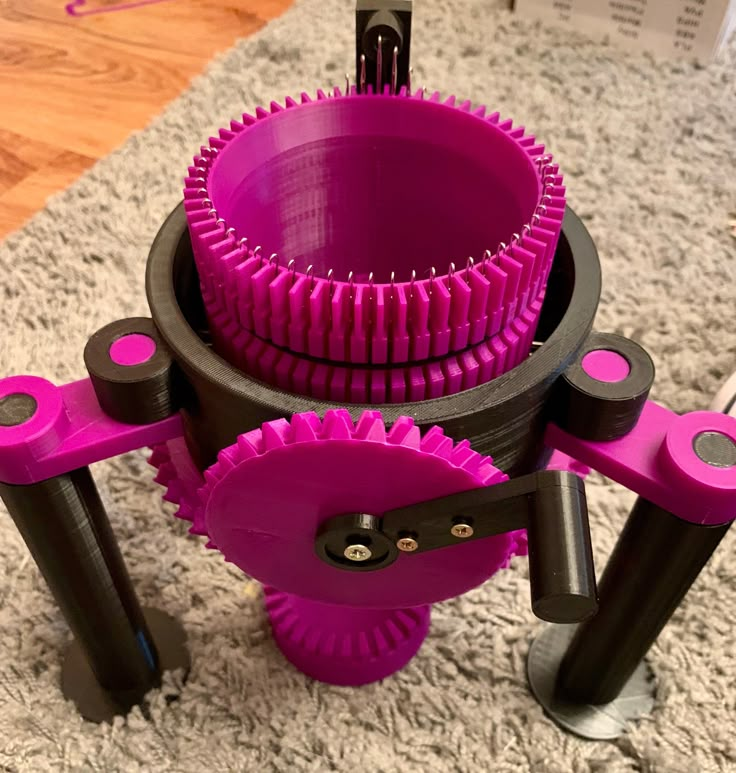
All the UV wall printers can be upgraded to the latest version software, which will significantly improve your printing quality.
11/01/2020. PhotoPrint RIP Software Available
All wall printers can be installed by PhotoPrint RIP Software as optional. If you need it, contact your engineer. nine0009
03/12/2021 Ink Level Alarm Tank is Available
UV wall printer has equipped with the ink level alarm tank. 5 ink tanks, 260ml each. White ink will be with the stirrer.
04/12/2021 The World's First Floor Printer is Ready
The Floor Printer can print directly on the ground. Check more: 3D parking spot printer machine
Jan.
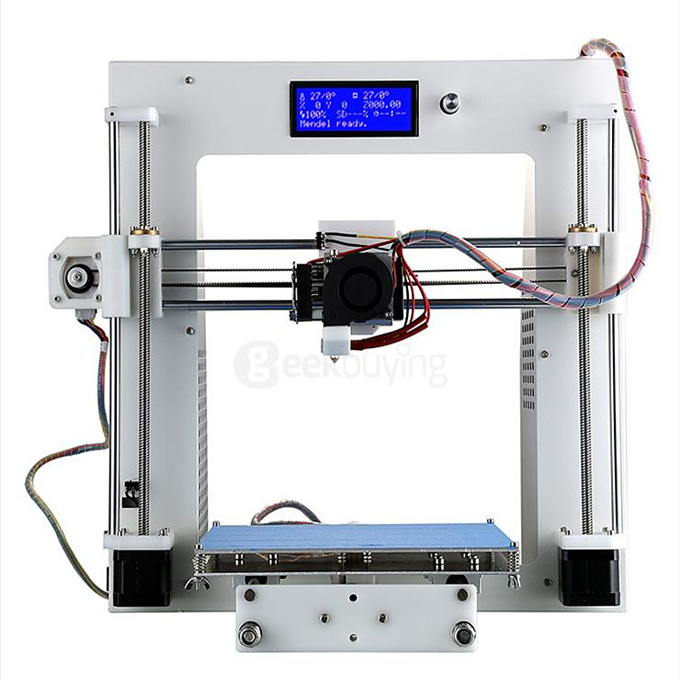
T series is the most portable UV wall printer HKHR tech has been made. It can be split into 6 parts and each one is no more than 15kg. What’s more, it also combined the rails driving system and wheel driving system in one model. Introducing the "T series" UV wall printer
For technical support, please contact our engineer Adam: [email protected]
For sales inquiry, please contact our sales director Alex: [email protected]
Everything You should Know About Wall Printer
The Ultimate Guide For How to Choose the Best Wall Printing Machine
Everything you should know about the wall printer.
Support
SAi FlexiPrint RIP Software We can pre-installed the US PhotoPrint RIP software for all UV printers and water-based ink printers.
After printing tests and calibration curves, the output ink quality of all series of HKHR wall printers has been significantly improved.
Language: English, Portuguese, French, Italian, German, Spanish, Chinese, Japanese, Korean, Dutch, Danish, Finnish, Russian uses 5 basic colors of CMYK+White , which can print on dark background walls (such as gray, blue, black, etc.).
At the same time, it can also print white colors independently, which is more suitable for some special scenes.
How to Unpack & Assemble & Operate The Wall Printer
We have packed 6 UV wall printing machines in the factory. Three of them were sent to the United States. The unboxing video was shot and edited in the United States.
This video also shows how to operate our wall printer .
High Resolution Printing
All series of our wall printers support up to 16pass, 2880dpi printing resolution.
The original scene of the picture is vividly restored, which is full of praise.
Portable UV Wall Printer—The Best Selling Wall Printer
You can choose a wheeled wall printer. It can move on its own automatically and can be applied to flat indoor floors.
Equipped with height-adjustable guide rails, allowing you to print easily outdoors. Disassembly, transportation, and installation are very convenient, 10 minutes is enough! (TWP is our distributor for North America)
Watch the video tutorial for taking down and setting up the Wheeled UV wall printer
You will Never Be worried About Power Cut and Sudden Accidents for stopping Printing
We have developed the power -off supplement function .
It allows you to set up the software to continue to finish your work next time when power is lost, raining, and various emergency situations have to be suspended. nine0009
There is no need to return the guide rail to its original position, it can be completed by software and laser calibration.
Check the supplement tutorial --->>
Amazing Stitching Ability Allows You to Print Murals Up to 10 Meters High
Excellent expansion performance.
We can customize the vertical rail of the wall printing machine for you to adapt to the indoor height of different countries.
At the same time, we can add an extension rod for you to obtain a one-time printing height of up to 3 meters. nine0009
And through powerful operating software, you can use stitching technology to obtain larger-format pictures.
Four Printheads and The Fastest Wall Printing Speed You Have Never Seen
The water-based model of wall printer machine is equipped with up to 4 Epson print heads, each of which works independently and can print 80m2 per hour in the 2 Pass mode.
Such an amazing high-speed printing technology is already ranked first in the world in the field of vertical inkjet printers. nine0009
UV Curing System with Air-Cooled UV Lamp
that of the water-cooled UV lamp.
At the same time, the UV curing effect is more efficient, suitable for printing on various materials. Such as walls of any material, metal, glass, wood, canvas, plastic, ceramic tiles, etc.
The Seventh Generation
EPSON Micro-Piezo Printhead We use high-quality EPSON micro-piezo print heads for all series of printers. We refuse to use cheap, inferior, and second-hand EPSON print heads.
Because we know that the quality of the nozzle directly affects the printing effect and the life of the wall printer.
High-Quality and Stable Components
We use 3 independent power supplies to avoid interference; The frame uses high-quality steel to increase its rigidity and precision; At the same time, we use large wheels to increase precision and anti-skid. . . nine0009
We only purchase top-quality accessories to provide customers with safe, assured, durable products, and user experience. Save Your Time, Save Your Money
Only the colored areas are printed. And the white area, the print head no longer scans to save time. nine0009
Watch carefully at the end printing for the tail, the printhead just prints the area for the tail, not scan other white areas.
Eco-friendly ink
Our printer uses environmentally friendly and durable highly colored pigment ink, which can be used in any scene.
At the same time, you can purchase high-quality printer inks suitable for our machines worldwide.
Tracking System to keep the right distance to the wall
The entire series of our wall printers are equipped with two American Banner ultrasonic sensors so that the print head can print on curved and uneven surfaces. nine0009
Which means it can automatically follow the wall without worrying about the flatness of the wall.
Manual Laser Calibration Function
The manual laser calibration function allows you to better grasp the status of the machine.
Come Follow The Lens And Visit Our Factory
We are a vertical printing technology company with R&D capabilities. We are not a trading company or an assembly company for the wall printer .
You deserve to have a professional after-sales guarantee.
Pantents and Certifications
We have the most comprehensive certifications and patents, two invention patents for the wall printer, and 8 other patents.
In addition, we have a CE certificate, ink certificate, and so on. We prove ourselves through strength and service, not sales words.
R&D Ability
All the PCB motherboards for wall printer and programming systems for wall printers are developed by us, so our machine update iteration is very fast.
After-sales support is more convenient, and there is no need to contact the motherboard supplier to resolve customer questions.
The motherboard and program are very stable. As we have been supplying the inkjet printer market for more than 10 years.
Market Share
We have more than 2,000 customers in China, this is just a part of these cases. nine0009
Dealership and Agents
We have very good partners in the United States, Russia, and the Czech Republic. . .
—> Dealership network over the world
We provide high-quality products and reliable services to win more and more partners.
Do you want to join us too?
Aging Test
We will do 24 hours aging test for all the wall printers before shipping, making sure they are all in good condition. nine0009
After-sales Guarantee And Technical Support
We provide a one-year after-sales guarantee . Our after-sales team has rich experience , has served the Chinese market for a long time, and can speak Good English. They Can solve technical problems for you through video calls.
We send accessories through FedEx and DHL, and we will bear the first year’s cost. WhatsApp: 86 15952051055
How to print 10m * 12m photo wallpaper on the wall with a wall printer? nine0070
BlogBy Alex Wang
Our smart Chinese customers have printed a HUGE 10m x 12m mural on the wall using the stitching function of the software wall printer. The standard print height of the wall printer is 2 meters, but we have developed the STAPLE FUNCTION in the software. If you want to print a large mural on the wall, you just need to lift the printer by the platform and print...
Read more
CMYK + White Wall Mounted UV Printer with Wheel and Guide Show Show
BlogBy Alex Wang
This is a great video made by our partner in Ukraine. If you want to know more about them and our dealers and agents around the world, please click here: Worldwide Wall Printer Agents and Dealers By watching this video, you can see how amazing the S Series UV Wall Printer can do. Using white ink, he…
Read more
Everything you need to know about the wall printer
BlogBy Alex Wang
This article is contributed by our engineer Adam. Now he works for Beijing Huake Hengrun Intelligent Technology Company, which is the most professional wall printer manufacturer in China. We sell wall printer abroad. I have been designing and manufacturing wall printers since 2011. I have witnessed how the scale of this industry has grown from small to large, and ...
Read more
Russia UV Wall Printer, Steel Wall Printing
BlogBy Alex Wang
This video has been verified by our Russian agent. They use UV S series wall printer to print on the steel wall.
Read more
King of Oman print on wall with wall printer
BlogBy Alex Wang
We use HK-K2 wall printer, a water based pigment ink wall printer with 2 print heads. Seal of the King of Oman on the wall.