3D printer library near me
3D Printing in the Denver Public Library ideaLABs
We've made some changes to the way we offer 3D printing!
We're excited to let you (yes, you!) get more hands-on with the printers and run your print job yourself. This does mean we are no longer running a print queue or accepting submissions for printing - but now you will have the chance to run the entire process yourself, from design to finished print.
Use of the 3D printer is by reservation - please drop in or call the branch to reserve time. You will need a Denver Public Library card to make a reservation in advance. The maximum time you can reserve is two hours. We ask that people only make one reservation per week so as many people as possible can use the printers. Please read the full 3D Printer Policy below for details. We also have an FAQ below that for general questions about 3D printing.
Every ideaLAB has at least one Lulzbot printer. Visit your neighborhood lab to learn more! Please note that the ideaLAB at the Central Library will remain closed due to on-going renovations to the building.
Denver Public Library ideaLAB 3D Printer Policies
As the ideaLBs reopen, the use of tools may look somewhat different than in the past. One of the big changes we’re making is to give customers more of a hands-on experience using the 3D printer.
In order to help you use the 3D printer successfully (and safely), we ask that you read through the following policies:
- Please try to read through the 3D Printing Guide before your first visit if you can.
- Use of the 3D printer is by reservation only. For the present, a reservation gives you the right to use the printer for two hours, once per week. We ask that families and groups not make multiple or back-to-back reservations under different accounts - that makes it much harder for other people to get access to the 3D printers.
- Please know that if you don't show up within 10 minutes of your reservation time, the system will automatically cancel it.
- If the printer is broken when you have a reservation, we'll do our best to let you know ahead of time, but sometimes that may not be possible.
- You must check in with ideaLAB staff before using the machines so you can get the material you're using approved by lab staff and get the 3D printer toolkit. We want to make sure everyone is safe and that you're comfortable with the equipment.
- We're sorry, but you can't bring in your own filament. We want to keep jams and fumes to a minimum for everyone. We will provide free PLA+ filament, but we can't change out colors for each customer nor guarantee you a specific color.
- We'll give you some basic troubleshooting tips, but if something goes wrong, please don't do anything that involves disassembling printer hardware. Doing so will result in loss of privileges to use the machine. Please let us know if a problem pops up and we'll help!
- Things happen. Occasionally extruders will jam, beds will get scorched, and minor disasters will occur - these are understandable, and part of the process of learning how to use the printer, and will not affect your ability to reserve and use the machines.
If you do something intentionally dangerous or that we've asked you not to do - using unapproved filament, removing parts from the machines, etc. - you will lose your privilege to use the machines..
- DPL printers can not be used to print out any weapons (if it's for cosplay, talk to staff and we'll try to figure it out). Outside of that, most things should be fine, but the Library retains the right to refuse any print request for any reason.
- Set-up and clean-up time is part of your 2 hour reservation, so please plan accordingly! Please finish your 3D printing jobs at least 10 minutes before the session ends so you can clean up materials and station. Jobs can not be left running overnight or past the end of your 2 hour reservation.
3D Printing FAQ
What is 3D printing?
Start with this definitive guide where you’ll find everything you need to know about 3D printing, beginning with the very basics before diving deeper.
How much does it cost?
3D Printing is currently free at Denver Public Library!
What can be printed?
All printing is done with PLA, a bioplastic made of corn. It might get a little melty if you leave it on your car dashboard, and you may not want to use it to make shelving mounts for your prize kettlebell collection. It's possible to make your model a little bit stronger by making it's walls thicker or requesting more infill. Ask us about it and we'll try to help you out. But if the piece you're printing is really mission critical in some way, use it at your own risk.
What cannot be printed?
Due to demand and limited resources, we can't print any job that will take over two hours. If you have something you'd like to print that will take longer than that, we're happy to help you try to figure out how to break up your model into smaller jobs, scale your print, or point you to one of the many paid 3D printing services. We also will not print out any weapons. Outside of that, most things should be fine, but the Library retains the right to refuse any print request for any reason.
Who can operate the printer?
Anyone who goes through an orientation with a staff member can! Read through the 3D Printer Policy above to learn how.
How To Get Your Object Printed
-
Create a file
- You can download an object file from a site like Thingiverse, Bld3r or use some of the lab's free modeling software like Tinkercad, Blender or SketchUp to make your own designs.
- Export your object as a .stl or .obj file. Need help? Just ask!
-
Make your reservation
- Reserve time by coming by the branch, calling, or come into the ideaLAB during our open hours. You can reserve up to two hours on the machine.
-
Print out your creation
3D Printing - Prince George's County Memorial Library System
3D printing is available to anyone with a PGCMLS library card! Customers can submit a print request online and pick up a finished print at any PGCMLS branch. Submit a print below, or browse these slides to learn more about how our library community uses 3D printing.
Featured Print: Apollo Lunar Module
Staff at the Greenbelt Branch printed this lunar module based on the historic spacecraft used in the first moon landing. This model was created using NASA’s 3D resources, and is free to download from Thingiverse, a free 3D design repository.
Learn More
3D Printing Programs
Want to learn more about 3D printing and digital design? PGCMLS offers 3D printing programs for all ages throughout the library system. Keep your eye on our events calendar for a program near you!
Check out our upcoming programs!
3D Printing Resources
PGCMLS has a whole host of 3D design books and e-resources in our collection. Click the link below to visit the catalog and start learning today!
Learn More
Featured Print: Fittle Puzzles
The Fittle Project was started to introduce 3D printing and STEM education to schools for the blind in India. As part of their mission, they’ve shared open-source files to 3D printable Braille literacy puzzles so anyone can print their own. Each piece bears a single letter in Braille, forming a simple word for every letter of the alphabet.
Learn More
PGCMLS is not currently accepting 3D print submissions. We apologize for the inconvenience.
3D printing services are now available to all PGCMLS customers! Printable files may be submitted online and picked up at any PGCMLS branch.
The cost for 3D printing is $1.00 per hour and is calculated once we receive a print request. Once your print request is processed, you will receive an email with the print cost. Once you have confirmed the cost, we can schedule your file for print.
The current wait time is approximately 2 weeks from submission to pickup.
PGCMLS 3D Printing Agreement
No objects deemed dangerous, illegal or inappropriate will be printed. Prints must adhere to copyright restrictions.
Customers may submit up to 3 prints a month. Only one print request may be submitted at a time. Prints with multiple files must be submitted as separate requests. Print requests will be honored on a first come, first served basis and may be denied at PGCMLS staff’s discretion.
PGCMLS cannot guarantee model quality, stability, or confidentiality of designs. It is recommended that customers analyze print quality through a service such as Microsoft's free 3D repair tool before submitting for print
3D printing through PGCMLS costs $1.00 per hour, rounded to the nearest half hour. Once the print cost is determined, the customer must confirm by phone or email in order to begin the print process. Once confirmed, the customer is responsible for the cost of the print. Payment is due at the time of print receipt and may not be refunded. Print price is subject to change due to material costs
Prints may not be larger than 6in wide x 6in deep x 6in high. Larger prints must be submitted in parts. If a file larger than the maximum size is submitted, PGCMLS staff may contact the customer about resizing the object prior to printing.
PGCMLS will not issue refunds for prints that fail due to design error or customer dissatisfaction with the color, size or quality of prints. Any concerns regarding print or material quality should be addressed using the Online Library contact form.
PGCMLS is not responsible for post-processing of printed objects. Customers are responsible for removing supports if requested. Customers who wish to modify their finished prints further may do so at their own risk.
For questions about or assistance with 3D printing at PGCMLS, contact us using the Online Library contact form.
Download a copy of the PGCMLS 3D Printing Agreement here.
Learning Resources @ Your Library
Learn more about 3D printers using the books and electronic resources in our catalog or find an upcoming 3D printing program using the event calendar!
Printable 3D Models From The Web
Thingiverse Vast collection of models and educational resources.
Nasa 3D Resources A free growing collection of 3D models and textures from NASA.
Smithsonian X3D Models of artifacts from the Smithsonian collections.
3D Design Tools and Lessons
Questions?
Use the Online Library webform for more information
13 notes about 3D printing, after 3 years of owning a 3D printer / Habr
This article will be, first of all, of interest both to those who have directly dealt with 3D printing, that is, who owns a 3D printer, but also to those who are just about to join the ranks of 3D printers and are thinking about buying their own printer.
In the framework of this article, I want to present my observations, as a direct owner of a 3D printer, for more than 3 years.
Despite the fact that 3D printers have been known for a long time and, in my memory, have become widely used, judging by the information on various resources, starting around 2010 (I may be wrong, these are my subjective observations), for a long time I ignored this area, it’s hard to say why…
Probably thought it was some kind of "childish pampering", another hype topic for which there is simply not enough time. ..
The turning point happened when one of the wheels on my travel suitcase wore out. You know, a big plastic suitcase, with four spinning wheels on the bottom. Unfortunately, it is a “rather disposable thing”, due to the lack of bearings on the wheels, which is why the wear of the friction point of the axle and wheel allows the suitcase to last no more than one or two seasons. nine0003
And it’s like “lightning flashed in the middle of the day: 3D printer!” It is with his help that I can fix this problem! Looking ahead, I’ll say that I didn’t succeed in fixing the suitcase in this way, so I had to use a different approach ...
As a result, I “upped” it - installing wheels from unnecessary roller skates. Thanks to this “up”, the suitcase has become a real all-terrain vehicle and, even being very loaded, it rides easily - pushed forward even with “one finger”. And even in the snow, 5-6 cm thick. A tank, not a suitcase turned out! By the way - I took spinning wheeled "units" in Leroy. Then he took off and threw out his native plastic wheels from there, inserting from roller skates:
But this thought itself became a kind of trigger that allowed me to finally join the world of printers and buy my first 3D printer.
Like many, before buying it, I studied various forums and sites for a long time, delving into all the subtleties. And for some reason, I immediately liked the type of printer called the delta printer. Probably because during operation it looks like some kind of "alien device".
If at your leisure you like to sit “looking into the carpet”, then with the advent of such a printer you will have a much more interesting activity, even, one might say, hypnotizing :-))
And this, in fact, is my delta (if anyone is interested), which went through, let's say, the "ultimate up": all the electronics are placed upstairs, on a self-made welded frame, covered with polyethylene and a magnetic door is made. The coil with a bar is installed at the top, on the frame. The axis on which the coil is put on is machined on a lathe from aluminum and a bearing from the VAZ timing is inserted into it. As a result, the coil - "rotates even from the passage of a fly nearby":
Well, yes, I won’t argue for a long time, let’s start reviewing the main facts that I have accumulated as a result of owning this car ... The facts are purely subjective and may differ from your vision. In any case, I will be glad to comments, clarifications, etc. nine0003
▍ NOTE 1. Delta is good, but...
Here I should give a number of my observations regarding the delta printer:
- It contains a completely finished frame of the future box, which makes it easy to form a heat chamber. I understand that many printers are made in the form factor of a “certain box” (but this point cannot be ignored), which greatly facilitates the process of wrapping this box with heat-insulating material.
In my case, as such a material, I used a plastic film. nine0032
- Already thanks to its design, delta allows you to work at much higher speeds than XY printers. By the way, it is on the delta principle that many modern high-speed industrial robots are built to sort various parts directly on the conveyor belt:
However, this plus does not allow to fully realize the occurrence of parasitic vibrations, even despite their suppressors:
Thus, accurate printing is possible, only at speeds (at least that was the case for me), no more than 60 mm per second. A complex procedure for aligning the movement of the head parallel to the table, which is why, for many, the so-called "lens" appears. People struggle with it with varying degrees of success, but I have not encountered this on my printer and for me, therefore, the “lens” has never been a problem. At the same point, it is worth noting the calibration of the table, which was initially absent on the first deltas, and I had to use an external third-party solution from one American do-it-yourselfer called EZBED. This solution was a hardware-software complex that allows you to quickly and easily calibrate the printing table, that is, to let the printer understand its geometry. Modern printers do not have this issue as they come with a built-in calibration solution. It is worth noting that I solved this problem by attaching a limit switch to the print head, and using the Marlin-1.1.9 firmware.
▍ NOTE 2. "Size doesn't matter..." :-)
When I got the printer, I was impressed by the possibility of huge printouts, a la the handguards of some futuristic rifles, huge body parts, etc.
However, if you try to analyze the results of your many years of practice, it turns out that in most cases, rather small objects were printed that easily fit in the palm of your hand, a maximum of two palms. Despite such a seemingly small size, the printing of these details took a significant amount of time. Of course, this very much depends on which nozzle you print with. But, despite this, it is difficult to disagree with the fact that most of the printed parts will be quite utilitarian and small in size. nine0003
Therefore, to be honest, the need for a printer that allows you to print "Venus de Milo in life size" is not obvious.
Of course, you can object to me that “I’m going to buy a printer, I’ll get used to it a little and I’ll get started!!!”
One simple point must be taken into account here: there are no universal things. And in order to understand how much 3D printing in general and your printer, in particular, you will need to solve your problems, and how much it will be able to solve such problems, you just need to first try the 3D printing method personally and then a lot will become clear to you . nine0003
Therefore, for a beginner, I recommend taking a small printer that allows you to print extremely small items that fit in the palm of two. With such a device, you will definitely never lose, as it will always be needed. In addition, with its help you will be able to get used to the printing process and, if necessary, purchase a larger device, already clearly understanding its capabilities and ability to solve your set of tasks.
▍ NOTE 3. "What type of printer to get." nine0027
Based on the foregoing, I do not recommend taking a delta printer and this can be said right away.
Not because it is bad, in fact, it prints quite accurately, its main problem (in my opinion) is the inability to print rectangular flat, fairly large case components, as well as the inability to fully realize high-speed work, since the quality drops critically. Here it turns out to be a rather offensive situation - the printer can work quickly, but this cannot be done, since the quality will be “nothing”. nine0003
And then what kind to take? Depending on the budget and capabilities, I recommend taking any cube printer, for example, the same Core XY (the head moves, and the table goes down as the model “grows”, from top to bottom):
Image source: thingiverse. com
Such a printer allows you to easily print fairly large flat parts of cases, has good speed and accuracy. In addition, the presence of a rigid box-shaped frame allows it to be easily covered with polyethylene to create a sealed heat chamber. In addition, the very fact that the table does not move while working reduces the number of problems with model peeling. nine0003
However, the advantages of this printer will not be fully revealed if it has a direct extruder. On the one hand, it will allow printing with rubber-like materials, on the other -
large inertia and head weight. And these are parasitic vibrations, wear of the fur. parts, etc. (like everything in life, “we treat one thing and cripple another” :-))
At the initial stages, this may not be necessary, but in the future it may be necessary to print, for example, tires for your homemade car. And with this, the Bowden extruder has obvious problems. Although, in fairness, printing with such a rubber-like material is far from a daily need. However, whoever seeks will always find: over time, I found a way to “upgrade” my printer with a Bowden extruder to print with flexible materials. "Crutches" of course. But even so. nine0003
By the way, there are printers of a cheaper type, the so-called "drygostol", printing by moving the table and head:
They are inexpensive, moderately accurate, but they require a sufficiently high-quality gluing of the printed model to the table, because the table moves, and the model can come off when the table is jerked sharply. When printing large models, this can be a problem.
▍ NOTE 4. What to print with?
It's only a matter of taste and purpose. That is, if your printout will only stand on a shelf and should differ in some kind of aesthetic appearance, these are some requirements, if the printout is an engineering part that will be operated under conditions of increased mechanical load, these are different requirements. That is, in the first case, you can use any PLA, SBS plastics, and others with similar properties. nine0003
For engineering parts, for example, I only use ABS. It combines high hardness, strength and low price. Although I understand that now this last statement will cause a storm of comments in the style of “no! - there is even stronger, even better, the same PETG, etc. ":-)
Just here I wanted to say that thanks to the low price and the practical experiments that I conducted with ABS plastic, I realized that it is completely meets all my requirements. nine0003
However, the fact that ABS plastic releases carcinogenic substances when heated is quite annoying and forces you to take measures to prevent poisoning. For this, my printer prints completely closed and on an open balcony. After printing, the printer chamber opens, and it remains open in this form until it is completely ventilated and cools down.
▍ NOTE 5. "ABS is difficult to type on, it flakes, peels off the table, etc.
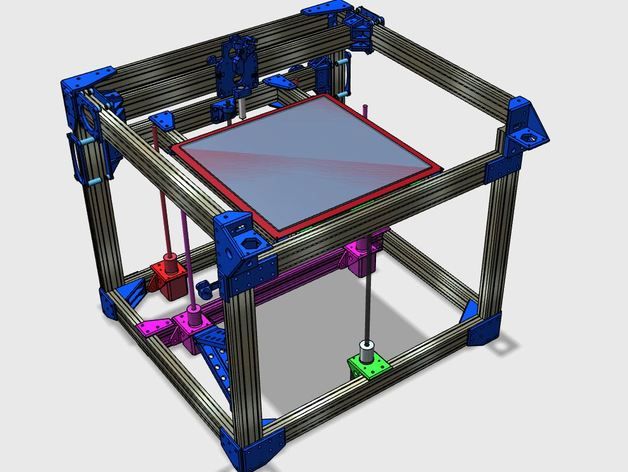
With a properly configured printer (in my case, at a print temperature of 205 degrees, a thermal chamber and a desktop temperature of 100 degrees), the use of auxiliary techniques, for example, among which, one can name the so-called ABS juice (which is ABS- plastic dissolved in acetone), you can create wear-resistant and durable things, without any hypothetical problems. nine0003
For example, my printer has been printing for many hours at temperatures well below freezing. And this happened more than once, not twice, not three! And the print quality was excellent:
12-hour ABS printing at -4 C
▍ NOTE 6. Acetone for post-processing and ABS juicing
At one time, I wrote a fairly detailed article on this topic and I will try to give the main excerpts from it. The essence of the issue here is as follows: due to the fact that different GOSTs are used for the production of acetone, acetone differs in quality. Despite the fact that it would seem that “acetone is also acetone in Africa,” nevertheless, one type of acetone can differ significantly from each other. For example, ordinary acetone, which can be bought at any hardware store, such as "1000 little things", "store near the house" and the like, is very low quality acetone, smells disgusting (although someone like it, maybe someone likes its pleasant building aroma and "aftertaste" :-))). nine0003
In contrast to it, there is a much higher quality acetone, which, however, is not found at all in any household stores, even large chain stores, such as Auchan or Leroy Merlin.
This type of acetone is found exclusively in shops that sell varnishes and paints for automotive work - that is, these are highly specialized shops for car workshops:
Acetone, which can be purchased there, is of excellent quality, smells almost like alcohol, quickly disappears,
:-) - this is a joke, of course, don't even try it.
However, its main advantage, compared to household type acetone, is that it perfectly dissolves ABS plastic and does not allow it to precipitate. For me personally, it was a very surprising observation when the same ABS plastic was perfectly dissolved with acetone from an auto shop, and completely precipitated when I tried to use household acetone (I just ran out of good acetone, and I had to use "what is "). nine0003
Therefore, if you want your results to always be excellent, then here is the right acetone. It should be labeled "for professional use":
▍ NOTE 7. What about ABS juice?
"ABS juice" is what printers call a mixture of acetone and pieces of ABS plastic dissolved in it. This mixture is smeared on the surface of the desktop before printing and allowed to dry. Thanks to this spread, the model easily sticks to the desktop and does not peel off during the printing process. After printing is completed and the platen has cooled down, the model can be easily separated. nine0003
All that needs to be said here is that, after trying different approaches over time, I settled on using flexible metal spatulas, also called "Japanese type spatulas":
According to the results of many tests, this method of spreading turned out to be one of the most convenient options, such spatulas can be cleaned very quickly and easily after work. In other words, highly recommended!
▍ NOTE 8. "Yes, nothing sensible can be done on it, I indulged a little and decided to sell it - you can't use it for anything good anyway"
I absolutely disagree with the statement above, which is periodically heard from newcomers to 3D printing. You can even say more: at the moment I can’t even imagine how I used to live without a 3D printer! Since it is he who makes it possible for any do-it-yourselfer to significantly expand their capabilities and make piece products, almost of factory quality! Of course, for this, appropriate hands must be applied to the 3D printer, but that’s another question… and take on things that I would never have thought to take on before! nine0003
For example, among my homemade products, the following can be listed:
- Heated sole for boots, which is a hose integrated into the insole (and filled with household silicone from a household store), through which water flows, heated with a catalytic type hand warmer.
Water is pumped using a small peristaltic pump. The engine with a metal gearbox, which is used in the creation of this pump, allows you to develop a force of 3 kg, which is even redundant for this homemade product. The engine is powered by Peltier elements mounted next to the catalytic heater. The project is currently in progress. nine0032
- Centrifugal water pump mounted on the shaft of an internal combustion engine that drives a high pressure wearable air compressor with a pressure of 500 bar. The pump pumps coolant through the casing of the high pressure pump, or rather its second stage. Despite the fact that the pump is 3D printed and runs at over 6000 rpm, nothing “fell apart, fell apart, didn’t break.” As you can see in the photo, the pump is installed instead of the “starter”, that is, the armstarter. The compressor scheme as a whole is as follows: 2 engines. Connected by clutch. One is heavy duty. The second is modified and turned into a high pressure compressor:
Yes, before assembling this, I also did not believe that this was possible. Moreover, even when I collected it, I did not believe my eyes :-))). However, it is a fact…
- I printed a number of Rank-Hilsch test tubes, the essence of which I have described in detail in this article.
- Printed mass of parts, more than 100 pieces, to create 10 web-controlled robots. There was also a detailed article about this here.
Well, and a bunch of all sorts of useful and not very crafts. As you can see from my crafts above, I have a special passion for creating some useful things, a utilitarian direction. That is, so that the printout is useful, and does not belong to the type “yyy breathe, Mikola, what am I doing here” :-), and then put it on the shelf and that's it. Although, engineers are also not alien to beauties, and this will be my next fact below. nine0003
▍ NOTE 9 Proper placement of the model when printing is half the battle
It would seem an obvious fact, but many underestimate it. Here I mean the following: by experience, I accidentally discovered that when printing various statues (in which I, completely unexpectedly for myself, discovered another passion of mine), it is advisable to place the statues at an angle to the printing table.
This allows the layers in the printout to run at an angle of approximately 45-50 degrees to the model. The result of this is that the printed model is almost completely invisible layers and the model looks like it has been post-processed, but at the same time retains a deep matte color, which, to my personal taste, is more like a marble than a glossy result of processing in an acetone bath : nine0003
An additional advantage of this method is that the layers going at an angle of 45-50 ° to the model give it additional strength. This is especially true for printing statues, which contain many thin elements that are easily chipped when the statue is accidentally dropped from a table or shelf (learned from bitter experience, this happened to me many times, and ruined some fairly decent prints).
That is, the layers going across the model, if the model has a large length in height, does not allow it to maintain sufficient strength. For better understanding, I tried to illustrate this point in the figures below:
▍ NOTE 10. Bleeding must be taken into account when printing, especially if the model is composed of separate parts and must be assembled by joining these parts to each other, entering into each other, etc.
I tried to illustrate this point in the figures below. The implication here is that if you're printing a composite model, you need to correct for the amount of bleed on the plastic (I'm not sure what it's called, but at least I tried to convey what I mean). If this is not taken into account, then the model will not fit. nine0003
For example, in my case this correction is 0.2 mm per diameter - if I want the model to fit more tightly; if I need a free joint, without excessive density, then 0.3 mm per diameter:
That is, suppose that the blue part has a size of 10x10mm. So it must be modeled in a CAD program as 9.8x9.8 mm (if we want it to sit tight) or 9.7x9.7 mm (to sit freely). Well, or expand the hole in the green part, and leave the blue one as it is. nine0005 This is often a problem when you download a prefabricated model from the Internet - but it is not going to, even if you crack! And because no amendments have been made…
For your particular case, the amendments may be different.
▍ NOTE 11. What if...
In fact, this note complements note number 8. Using a 3D printer allows you to create metal parts using a printed 3D model. For this, the casting method is used according to the lost wax or burnt model. In our case, we will deal mainly with metal casting on a burnt model. nine0003
Briefly, it looks like this: printing a 3D model (using PLA plastic) → pouring it with plaster → burning PLA plastic, simultaneously with burning the mold, in a conventional stove oven → pouring the resulting shape with molten metal (melted in a conventional microwave) .
Image source: 3dtopo.com
I told about a simple method of melting metals in a home microwave oven here.
There was even a good article about casting on Habré. nine0003
▍ NOTE 12. Durability?
Despite the fact that ABS plastic is called exposed to ultraviolet radiation and, accordingly, burns out, losing its strength in the sun, in my practice, even printouts that are constantly exposed to the sun have not lost their strength and color at all, continuing to be successfully used and Currently.
It should also be added here that printouts are constantly exposed not only to the rays of the sun, but also work continuously in damp conditions! nine0003
As such printouts, I can give an example of winglets for technical cranes, which I printed out, but, unfortunately, did not photograph this process; as well as fasteners on shoes that I use “both in the snow, and in the heat and in the pouring rain, and in general are always with me”:
▍ NOTE 13.
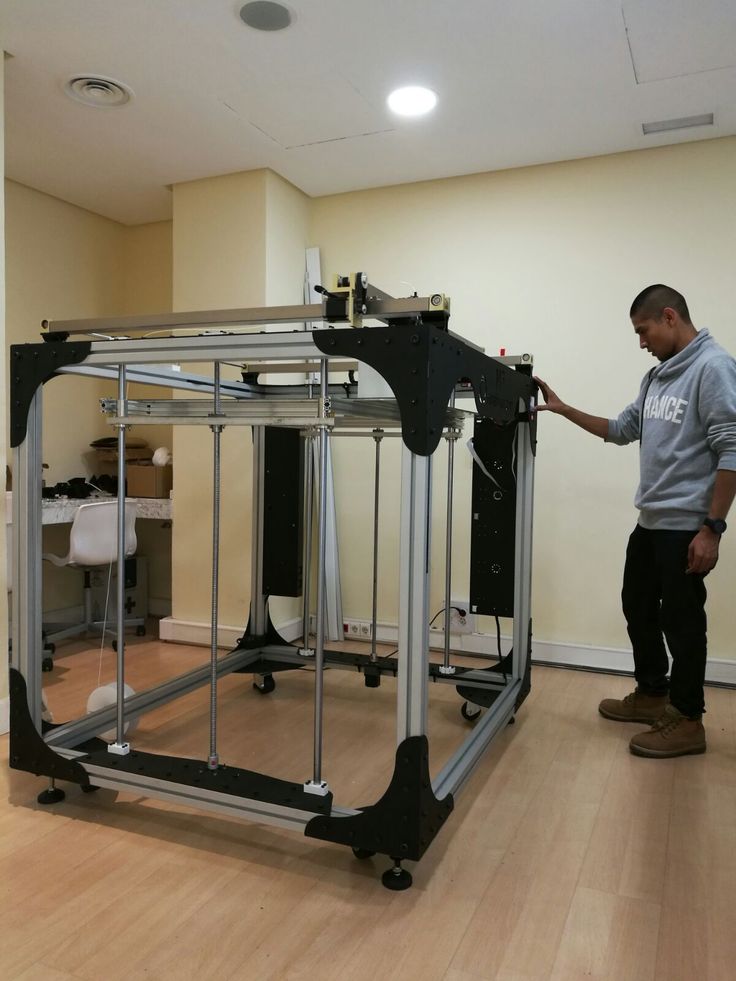
Periodically, there is a need to print parts containing a particular thread. Modeling such products requires a good understanding of what threading is in general, as well as what corrections need to be made in your particular case, which I have already described above. nine0003
But since I've owned a metal lathe for a long time, I'm not at all happy with the 3D printed carving that looks like "something very carving-like".
I am satisfied with an exceptionally perfect carving. Therefore, I keep in stock a large set of various taps and dies, with which I cut all my threads in plastic printouts:
I posted a photo of dies and taps not to brag, but to make the reader understand that serious carving requires a serious approach (unfortunately). And considerable costs for all this thread-cutting iron ...
To create your own threads (both threaded channels and threaded pins), I recommend the following reference materials: for holes, for pins.
Well, that's where I want to end my story and note that he does not claim to be exceptionally accurate and exhaustive. Nevertheless, I tried to state a number of my observations. It will be interesting to read yours, in the comments!
Printing organs: how ears, skin and noses are made with a 3D printer
- Natalka Pisnya
- BBC Russian Service, USA
Subscribe to our “Context” newsletter: it will help you understand the events.
The author of the photo, Masela family archive
Photo caption,Luc Masela with his parents one month after the artificial bladder transplant. year 2001.
Luc Masela, now 27, is an athlete with a degree in economics, works for a large exhibition company, travels a lot and recently met, in his words, "the most beautiful girl in the world." Both she and most of his current friends were extremely surprised when they learned that 17 years ago he survived a dozen and a half operations. nine0233
Luke was born with spina bifida - and although he was able to walk, his bladder was severely damaged. By the age of 10, he almost did not leave hospitals: due to improper functioning of the bladder, fluid began to return to the boy's kidneys, doctors diagnosed an irreversible pathology of the organ.
You need JavaScript enabled or a different browser to view this content
Video caption,"3D printed" organs are here
Doctors offered the family two solutions: lifelong dialysis or the creation of a new bladder from a segment of the intestine. This would guarantee Luke several years of medically supervised life and a high risk of developing cancer.
The urologist in charge of the boy invited the Masela family to take part in an experimental program: to grow a new bladder from his own cells. Then, in 2001, it sounded like science fiction: only nine people took part in the program before Luke. Despite this, his family agreed. nine0003
"The essence of the operation was reduced to two stages: first, a piece of bladder tissue was taken from me, and over the next two months, cells were grown in the laboratory in order to grow a new healthy bladder from them," says Luke.
Photo copyright, Masela family archive
Photo caption,Luc Masela, 17 years after the artificial bladder transplant
Next was the transplant operation, which, according to him, lasted 16 hours. “I opened my eyes and saw a cut through my entire stomach, tubes of all possible sizes were sticking out of me, except for them - four IVs and a bottle-feeding machine,” he recalls. “I stayed in the hospital for another month, I was prescribed bed rest, after that I stayed at home for another month. nine0003
The operation was performed by Dr. Anthony Atala, Pediatric Regenerative Surgeon. In two months, out of a hundred patient cells, scientists created one and a half billion. Further, an engineering structure was created on a collagen frame: the bladder was “sculpted” like a two-layer pie, the core of which dissolved over time, and it started working like a normal organ, taking root thanks to Luke’s own cells.
- An animal capable of regrowing its head
- The birth of a chimera: why do scientists need a human-animal hybrid? nine0032
- Swedish company 3D prints body parts
Luke and Dr. Atala haven't seen each other for 10 years after being discharged from the hospital. Once a dying child became the champion of the school wrestling team and went to college.
The professor took charge of the Wake Forest Institute of Regenerative Medicine in North Carolina in those 10 years, but he never forgot about Luke: his bladder was one of the most challenging and most successful projects in his early practice.
By 2018, Atala won the Christopher Columbus Award for "work on a discovery that will have a significant impact on society"; The Times and Scientific American magazines at various times named him "Doctor of the Year", he was also recognized as "one of the 50 scientists on the planet who in the next 10 years will change the way we live and work. "
How to print a new face
Skip the Podcast and continue reading.
Podcast
What was that? nine0003
We quickly, simply and clearly explain what happened, why it's important and what's next.
episodes
The End of the Story Podcast
In the mid-2000s, the Atala team turned their attention to an ordinary household 3D printer and wrote special software for it, later specialized machines were created for the laboratory. Now the laboratory "grows" up to 30 different types of cells and organs, as well as cartilage and bones.
One of the team's latest achievements is ears and noses grown outside the human body. nine0003
The main customer and sponsor of Atala's developments is the US Department of Defense, and many of the patients are military victims of military operations.
It works like this: first, a CT scan of the ear or nose is done. One of Atala's assistants, Joshua Corpus, jokes that at this stage, people often ask to "improve" the shape of the nose if they thought theirs was too wide or hooked, and the ears if they were too wide.
After that, a special computer code is written, and the printing of the basis of the organs begins. nine0003
For this, a bioresorbable polymer, polycaprolactam, is used. Both flexible and strong at the same time, it disintegrates in the human body within four years.
After printing, the layers of polycaprolactam resemble lace; after transplantation, their place will be taken by a person's own cartilage tissue in a few years after transplantation.
Polycaprolactam is then saturated with a gel created from the patient's cells, cooled to -18 degrees Celsius - so the cells, according to scientists, are not damaged, they are "alive and happy. " nine0003 Image caption,
Printing a test kidney sample on a bioprinter
In order for the polymer and gel structure to take shape and turn into something more durable, ultraviolet is used in the laboratory - it does not damage cells.
The future implant is printed for 4-5 hours, then it is finally formed and inserted under the epidermis.
Skin can also be grown: children affected by fires were the first to take part in the early trials of Atala - after the "printing" of the skin, scientists observed the patients for several more years. The new skin did not crack, did not burst, and grew with the children. nine0003
The most difficult work, according to the scientist, is facial wounds: it is not enough just to stretch the skin, you need to accurately calculate the geometry, align the swelling, the structure of the bones, and understand how a person will look after that.
In addition to the skin and ears, Atala can "print" the bones of the jaws, grow blood vessels and cells of some organs - the liver, kidneys, lungs.
This technology is especially appreciated by oncologists: on the basis of patient cells, it is possible to recreate the body's response to various types of chemotherapy and observe the reaction to a particular type of treatment in the laboratory, and not on a living person. nine0003
But the liver, kidneys, lungs and heart are still being tested. Atala says he raised them in miniature, but creating organs from various tissues to real size requires a lot of additional research.
But, according to him, cells were grown in the laboratory and a vagina was created for a girl who was born several years ago with a congenital deformity of the genital organs - several years have passed since the transplant.
Image caption,Bioprinted polycaprolactam ear implant base
Atala smiles and adds that his team is also working on a working penis. This research has been going on for several years, and the most troublesome for scientists is the complex structure of tissues and the specific sensitivity of the organ itself.
Among others, Igor Vasyutin, a Russian post-graduate student of the First Moscow State Medical University (MGMU) named after Sechenov, is working on this under laboratory conditions. He is a cell biologist, Atala's right hand. nine0003
Vasyutin has been in the USA for about a year - he came on an exchange. He is ready to talk about the behavior of stem cells for hours, but becomes less verbose when it comes to Russian science.
At Vasyutin's alma mater, they have not reached mass regeneration of human organs and are still training on animals: local scientists have "printed" a mouse thyroid gland on a 3D printer.
They are also involved in the study of human organs. According to the head of the Institute of Regenerative Medicine at MSMU Denis Butnar, several years ago the Institute recreated a special engineering design of the buccal mucosa. She functioned perfectly for the first six months, but subsequently had to undergo a second operation. nine0003 Image caption,
Test sample of an ear implant under ultraviolet light
In Russia, however, over the past few years, the Italian surgeon-transplantologist Paolo Macchiarini has been practicing - the man who was the first in history to perform a synthetic organ transplant - a plastic tube that replaced the patient trachea.
- Paolo Macchiarini: the rise and fall of the famous surgeon
However, seven of his nine patients died, and the breathing tubes implanted in the remaining two subsequently had to be replaced with donor ones. nine0003
Several criminal cases were brought against him, including on charges of pressure on patients and fraud, and the world's leading doctors called Macchiarini's operations "ethical Chernobyl."
Will printed organs replace donors?
At the zenith of his career, Macchiarini argued that a new perspective is opening up for humanity: you can "print" any human organ on a printer, create an engineering structure from it, enriched with the patient's stem cells, and get the perfect prosthesis. nine0003
Be that as it may, complex human organs - the liver, kidneys, heart, lungs - have not yet been able to grow any regenerative surgeon.
Bioprinting of the so-called simple organs, however, is already available in the US, Sweden, Spain and Israel - at the level of clinical trials and special programs.
The American government is actively investing in such programs - in addition to Wake Forest, cooperating with the Pentagon, the Massachusetts Institute of Technology also receives significant amounts to recreate the work of the liver, heart and lungs. nine0003 Image caption,
Skin application test on a burnt wound
According to Professor Jorge Raquela, a gastroenterologist at the Mayo Clinic Research Center, "Bioprinting is one of the most exciting branches of modern medicine, it has huge potential, and the turning point of the most important discoveries is already close."
Meanwhile, Pete Basillier, head of R&D at analytics firm Gartner, insists technology is advancing much faster than understanding the implications of 3D printing. nine0003
Such developments, according to Basilière, even if created with the best of intentions, give rise to a set of questions: what will happen when "improved" organs are created, the basis of which will not only be human cells - will they have "superpowers"? Will a regulatory body be created to monitor their production? Who will check the quality of these organs?
More than 150,000 Americans are on the waiting list for organ transplants each year, according to a report from the US National Library of Medicine. Donor organs will receive only 18% of them; every day in the United States, without waiting for a transplant, 25 people die. Organ transplants and subsequent rehabilitation cost insurance companies and patients $300 billion in 2012 alone. nine0003
- A 3D printer helped a cyclist who lost his jaw
- Genetically modified pigs - human organ donors?
- The world's first child with both hands transplanted plays baseball
Most Americans are potential donors: upon obtaining a driver's license, they voluntarily answer the question of whether they agree to donate their organs in the event of a car accident or other dangerous incident .