3D printing liquid bath
With This 3-D Printer, Objects Emerge From a Plastic Soup
It might be the future of manufacturing, but 3-D printing is built on a 2-D foundation: A MakerBot is essentially an inkjet printer that spits out plastic instead of ink. Keep printing in the same spot, over and over, and the layers will eventually form a 3-D object from the bottom up. But an outfit called Carbon3D is taking the opposite tack: Its new rig creates objects from the top down, in one continuous motion. It’s faster and eliminates the layering that can result in weak, jagged objects.
Inspired by the mercurial T-1000 bot from Terminator 2, University of North Carolina professor Joseph DeSimone wanted to make objects emerge from liquid. The process is based on a 30-year-old printing technology called stereolithography. It starts with a bath of liquid resin that hardens when exposed to UV light. A projector underneath delivers targeted blasts of UV to shape the form from below as the overhead platform lifts, drawing the object out of the soup.
The method has some limits. Oxygen inhibits the chemical reaction that solidifies the resin, slowing the process somewhat. But rather than fighting that limitation, DeSimone harnessed it. A sheet of glass between the projector and the resin is gas-permeable like a contact lens, and the oxygen keeps the resin from hardening too soon, before the object is complete.
1. Object-building platform
2. UV-curable liquid resin
3. Microthin layer of oxygenated resin
4. Oxygen-permeable glass
5. Ultraviolet-light projector
BROWN BIRD DESIGN
Even with this effect, the Carbon3D can print up to 100 times faster than leading 3-D and stereolithographic printers. In a video that ricocheted around the Internet after DeSimone presented it at TED, the device pulls a model of the Eiffel Tower out of the goo, as if it had just been sitting in the liquid all along.
Carbon3D has a team developing new materials for the printer. “We're pioneering new resins for our machine and also working with the chemical industry to evolve what’s already available,” says Rob Schoeben, the company’s chief marketing and strategy officer. “As long as a material is in the polymer family, we should be able to do it.”
The machine has vast potential. Rather than warehousing and shipping car parts, technicians could make components for older models on the spot from designs stored in the cloud. Aeronautical engineers could print high-strength, low-weight lattice structures to replace, for example, components in passenger seats, lightening the payload and increasing fuel efficiency in planes. And Carbon3D could prove invaluable for medical applications: Custom molds could be made onsite at a dentist’s office, and stents or other emergency implants could be custom-printed on-demand in the hospital.
Right now, Carbon3D has prototypes running at auto behemoth Ford in Dearborn, Michigan, at an athletic apparel company, and at a special-effects house in San Fernando, California, with an eye to hitting the market in 2016. But it has no shape-shifting bots that are hell bent on destroying humanity. Yet.
New Multimaterial SLA 3D Printing Method: Skipping the Liquid Bath with Aerosol Jet Printing - 3DPrint.
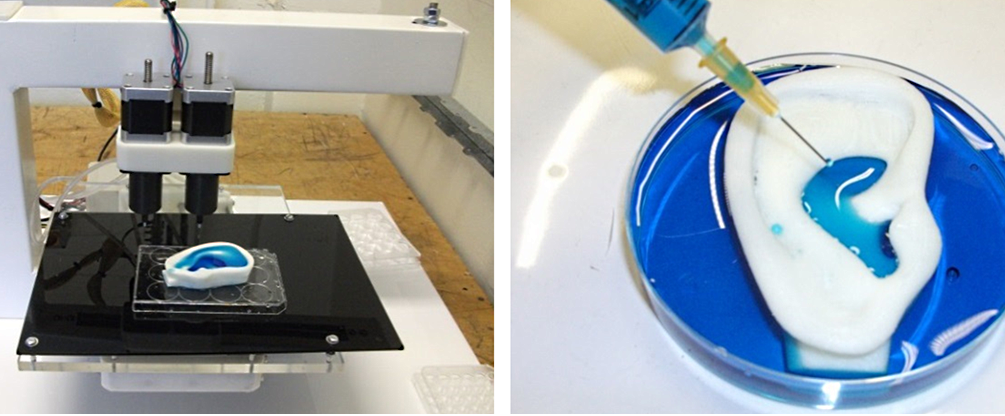
While SLA 3D printing is extremely popular among many different types of users today, there are drawbacks in post processing, as users are forced to take a more laborious step following the layer-by-layer method in using a liquid bath. While many are glad to continue this way, and are used to conforming to this traditional process, it is also limiting. German researchers have created a hybrid form of SLA 3D printing to streamline and expand production, which they explain in their recently published work, ‘Multimaterial bathless stereolithography using aerosol jet printing and UV laser based polymerization.’
Iterative layer-by-layer process of hybrid stereolithography
Rather than continuing with the normal bath used in SLA 3D printing, the authors have created a spray coating device instead:
“The AJS is able to process inks in the range between 10 and 1000 mPa s,” state the researchers. “Therefore, UV curable materials with greater viscosity compared to inkjet based raw materials can be used to establish a material layer and open the field for a wide range of materials.
![]()
“The modified system allows the mixing of two different materials through the addition of a second spray generator. This enables the printing of two pure materials as well as a theoretically continuous gradient.”
The AJS system is made up of:
- Two atomizers
- Two virtual impactors
- Mixing module
- Nozzle
Compared with a conventional inkjet system, the AJS is superior in processing liquids, relying on two atomizers. These components competently control the flow of materials, ultimately mixing the two (with one flow coming from each atomizer). The system also ensures good performance in printing as the combining of flows is exact, and with no backflow present. As the authors explain, push flow must be the same in both mixing areas, with the flow then accelerated by the nitrogen.
The ‘working distance’ created manages proper deposition and eliminates any chance for clogging. In conclusion, the researchers stated the following regarding potential for this process:
“This enables the freeform fabrication of parts with undercuts, as demonstrated in a 3D printed part.
Due to two available atomizers in the AJS device, the materials are mixed on the fly for desired material compositions. Hence, a transition from one pure material to the other is demonstrated with three intermediate material compositions. This opens the possibility to fabricate parts with varying material properties. This is a promising technique to establish multimaterial printing for the stereolithography and widens the range for possible applications.”
Hearing aid component, CAD file (left), printed by hybrid stereolithography (right).
The SLA 3D printer is known as the original 3D printing system, created in the 80s; yet while it may be one of the oldest methods of 3D printing, it is still one of the frontrunners behind innovations today. Researchers and manufacturers continue to forge ahead with this technology, reformulating resins, improving multi-material processes, and creating useful products like ceramic molds. What do you think of this latest technology news? Let us know your thoughts! Join the discussion of this and other 3D printing topics at 3DPrintBoard. com.
Modules of the hybrid stereolithography (deposition, polymerization, and stages).
[Source / Images: ‘Multimaterial bathless stereolithography using aerosol jet printing and UV laser based polymerization’]
Stay up-to-date on all the latest news from the 3D printing industry and receive information and offers from third party vendors.
Tagged with: 3d printing research • AJS • Hybrid SLA system • multimaterial 3d printing • sla 3d printing • SLA hybrid 3D printing • stereolithography
Please enable JavaScript to view the comments powered by Disqus.
Choosing a liquid photopolymer for a 3D printer. Classification of materials for SLA/DLP 3D printing.
Contents:
- Introduction
- SLA Overview
- SLA Standard Resins
- Standard photopolymer resin - Standard
- Clear Photopolymer Resin - Clear
- Engineering photopolymer resins
- Rigid photopolymer resin - Tough (like ABS)
- Durable photopolymer resin - Durable (PP-like)
- Heat resistant photopolymer resin - Heat resistant
- Rubber-like photopolymer resin - Rubber-like (Elastic)
- Ceramic photopolymer resin - Ceramic filled (Hard)
- How to choose the right resin for your application
- Dental and medical SLA resins
- Medical Device Photopolymer Resin - Custom Medical Appliances (Class I Biocompatibility)
- Dental Long Term Biocompatible Resin (Class IIa Biocompatible)
- Biocompatibility class I vs biocompatibility class IIa
- Cast SLA resins
- Cast resin for jewelry making
- Generalized rules
Hello everyone, Friends! With you 3DTool!
This article compares photopolymer resins using Formlabs SLA 3D printing products –
Catalog of photopolymer 3D printers
Photopolymers from FormLabs
Detailed review of the Formlabs Form 3 3D printer
Introduction
The stereolithography prints plastic parts with high resolution, good fine detail and smooth surface. Due to the variety of photopolymer resins available for SLA, this technology is used in many different industries:
-
"Standard" photopolymers are used for prototyping
-
Engineering photopolymers have certain mechanical and thermal properties
-
Dental and medical photopolymers have biocompatibility certificates.
-
Cast photopolymers have a zero ash content after burning.
SLA 3D Printing Resin Overview
SLA uses a laser to cure a liquid photopolymer resin. This process is called photopolymerization. Various combinations of polymers and other additives that are part of the resin allow you to get different material properties.
The main advantages and limitations that are common to all resins in SLA 3D printing are:
Benefits:
Weaknesses:
Base Resins for SLA
Post-Processing SLA/DLP 3D Printing Article
Standard photopolymer resin - Standard
Standard resins produce parts with high stiffness, detail and a smooth surface. The low cost of resins, from $250 per liter, makes them ideal for prototypes.
The color of the resin also affects its properties. For example, in FormLabs products, gray resin is suitable for models with fine details, and white resin for parts that require the smoothest possible surface.
Benefits of using Standard grade resins:
Cons Standard:
Also included in the class of "Standard" photopolymer resins from FormLabs is the Color KIT - a set of special dyes and "Color Base" photopolymer resin for mixing and obtaining a variety of color solutions. This eliminates the need for painting parts after 3D printing.
FormLabs Engineering Photopolymer Resins
Engineering resins have a range of properties for injection molded plastics.
All engineering resins require additional UV curing, such as using the Form Cure, to achieve their maximum properties.
Tough photopolymer resin - Tough (ABS equivalent)
Tough resin was developed for models that need to withstand high loads and be durable.
This material produces strong, shatter-resistant parts and functional prototypes such as snap-on housings.
Pros:
Cons:
Ideal for: functional prototypes, mechanical parts
Durable photopolymer resin - Durable
Durable resin is a wear-resistant and flexible material with mechanical properties similar to polypropylene.
Durable photopolymer produces models with a smooth glossy surface and high resistance to deformation.
Durable Resin is ideal for:
- Bushings and bearings;
- Various functional compounds
Pros:
Cons:
-
Not suitable for thin wall parts (recommended minimum wall thickness 1mm)
-
Low heat distortion temperature
-
Low flexural strength (lower than hard resin)
Ideal for: functional prototypes.
Refractory Photopolymer Resin - Formlabs High Temp Resin
The heat resistant resin is ideal for parts that require high temperature resistance and operate at high temperatures.
Formlabs High Temp Resin provides the highest melting point (HDT): 238°C at 0.45 MPa.
The resin should be used to print detailed, accurate prototypes with high heat resistance.
Pros:
Cons:
Flexible Resin
Rubber-like resin allows flexible parts to be made. This material has a low tensile strength and high elongation at break and is well suited for parts that will be bent or compressed.
It can also be used to add ergonomic features to multi-material assemblies such as: dies, wearable prototypes, handles, pads and grips.
Pros:
-
High flexibility (high elongation at break)
-
Low hardness (simulates 80A durometer rubber)
-
High impact resistance
Cons:
-
Doesn't have all the properties of real rubber
-
Requires extensive support structures
-
Material properties deteriorate over time as the part is exposed to ultraviolet radiation (sunlight)
-
Not suitable for thin wall parts (recommended minimum wall thickness 1mm)
Ideal for flexible prototyping.
Ceramic photopolymer resin - Rigid Resin
This resin is reinforced with glass, which provides very high rigidity and a polished surface. The polymer is very resistant to deformation and is excellent for 3D printing thin elements.
Ideal for: molds and tooling, jigs, manifolds, retainers, electrical and automotive fixture housings
Thermal management components printed with SLA ceramic (hard) resin. Image credit: Formlabs
How to choose the right resin for your application
The table below shows the main mechanical properties of photopolymers for SLA:
Source: Formlabs
Standard resin ( standart ) has high tensile strength but is very brittle (very low elongation at break) so it is not suitable for functional parts. The ability to create a good part surface makes it ideal for visual prototypes and art models.
Durable ( durable ) resin has the highest impact strength and elongation at break of any other SLA material. Best suited for prototyping parts with moving parts and latches. It lacks, however, the strength of thermoplastic 3D printing materials such as SLA nylon.
tough tough resin is a compromise between the material properties of tough and standard resin. It has a high tensile strength, so it is best suited for rigid parts that require high hardness.
heat resistant resin ( heat resistant ) can withstand temperatures above 200 o C, but has poor toughness and is even more brittle than standard resin.
ceramic ( ceramic reinforce ) resin has the highest tensile strength and flexural modulus, but is brittle (poor elongation at break and toughness). This resin is preferred for thin wall parts that require increased rigidity.
The graphs below compare the mechanical properties of the most common SLA materials visually:
Comparison chart for elongation at break and toughness for common SLA printing specifications and standard media. Image courtesy of Formlabs.
Stress-strain curves for conventional SLA technologies and standard materials. Image credit: Formlabs
Pros:
Cons:
- Moderate wear and tear resistance
Ideal for: Surgical aids and appliances
Dental Long Term Biocompatible Resin - Dental Long Term (Class 2A biocompatible)
0114
These resins are specially formulated for long term dental fixtures. Class 2A biocompatible resins can come into contact with the human body for up to a year.
High resistance to breakage and wear make this resin ideal for making rigid cotter pins or retainers.
Pros:
Cons:
-
High price
Ideal for: durable dental instruments, fracture and wear resistant medical parts, rigid cotter pins, retainers
What is the difference between class 1 and class 2a biocompatibility?
Class 1 biocompatibility rules apply to materials that are allowed to be used for:
-
non-invasive devices that come into contact with intact skin
-
devices for temporary use or short-term use in the mouth or ear canal or in the nasal cavity
-
reusable surgical instruments
Class 2a biocompatibility rules apply to materials that are allowed to be used for:
-
devices that come into contact with bodily fluids or open wounds
-
devices used to introduce substances into or remove substances from the human body
-
invasive short-term devices such as invasive surgical items
-
long-term implantable devices placed in the teeth
Photopolymer resins in SLA 3D printing for jewelers
Jewelry resins
This material allows you to print models with fine details and a smooth surface without leaving ash or residue after burning.
Cast resin allows you to get the finished product directly from design to precision casting with just one 3D printed part. It is suitable for making jewelry and other small and complex components.
Pros:
Cons:
Ideal for: investment casting, jewelry making
SLA/DLP 3D printer catalog
Photopolymers from FormLabs
Post-Processing SLA/DLP 3D Printing Article
Well, that's all we have! We hope this article was useful for you!
You can order Formlabs SLA 3D printers or ask your questions and find out the status of your order, you can
- Email: [email protected]
- By phone: 8(800)775-86-69
- Or on our website: http://3dtool.ru
-
Don't forget to subscribe to our YouTube channel:
Subscribe to our groups in social networks:
In contact with
A new 3D printing method 25-100 times faster than the traditional one / Habr
marks
Time to read 2 min
Number of views41K
Gadgets Computer hardware Popular science 3D printers Physics
The 3D printing method proposed by the California company Carbon 3D may well become the "killer" of the traditional method familiar to many. The thing is that the new technology is 25-100 times faster than the old methods of creating 3D objects. The company has been developing its technology since its founding in 2013.
The technology is called Continuous Liquid Interface Productiongo technology (CLIP), the principle of the new method is the use of light and oxygen to cure a photosensitive material (a special type of resin). The method of exposing the photosensitive material to light is similar to what we see in the traditional SLA process. But there are differences, and significant ones.
There is no layer-by-layer work here, when plastic is applied to the base layer by layer until a whole object is obtained.
Instead, human-safe spectrum and strength of light is used to cure the resin. Oxygen is also used as an inhibitor.
The use of oxygen allows you to control the photochemical reaction while speeding up the printing process. At the same time, there is no layered structure of the created object, the figure turns out to be whole, single. When printing using this method, a special transparent and permeable "window" is required, through which both light and oxygen pass simultaneously. You can think of it like a big contact lens. The device can control the exact amount of oxygen entering the resin tank. The oxygen then acts as an inhibitor during the photochemical reaction, leaving the necessary parts of the object in liquid. Light allows solidification only to those parts of the system where oxygen does not enter.
Thus, oxygen in this system can create a "dead" zone tens of microns thick. And just in this zone, photopolymerization is impossible. The device, on the other hand, projects a series of overlapping images using ultraviolet light.