3D printing in rubber
3D Print Rubber - 3D Printing Gaskets
Rubber and rubber-like materials are everywhere in modern industry. Soft materials like latex, silicone, and thermoplastic elastomer are useful in applications that demand flexibility and durability for industrial parts and consumer goods alike.
While rubber manufacturing has historically been the domain of casting and injection molding, modern advances in 3D printers and 3D printed materials have made additive manufacturing the ideal solution for producing small to medium quantities of rubber-like parts.
Our 3D printed rubber services can manufacture high-quality rubber-like parts in as few as two days―all you need is a 3D model! Start your project by getting a quote or keep reading to learn more.
Get a quote for your project using our quoting tools. Our engineers will review your project and get back to you 24 hours or less. 3D printed rubber parts ship in as few as two days!
3D Printed Rubber Applications, From Prototyping to Production
3D printed rubber parts can be used in place of molded rubber for just about any application. Like other methods of 3D printing, rubber prints accurately produce complex internal geometries like lattices and tubes at no extra cost, easily achieving designs that would be impossible with other types of manufacturing.
And because 3D printing doesn’t require any costly molds or tooling, 3D printed rubber parts can be manufactured in just a few days compared to multiple weeks of lead time for injection molding. This combination of high agility and no start-up costs allows rubber 3D printing to excel for both prototyping and small- to medium-sized production runs.
3D printed rubber is ideal for:
Prototypes
Gaskets
Seals
Hoses
Grips
Lids
Plugs
Connectors
Footwear
Tires
Medical Devices
Sporting Goods
Advantages of 3D Printed Rubber vs.
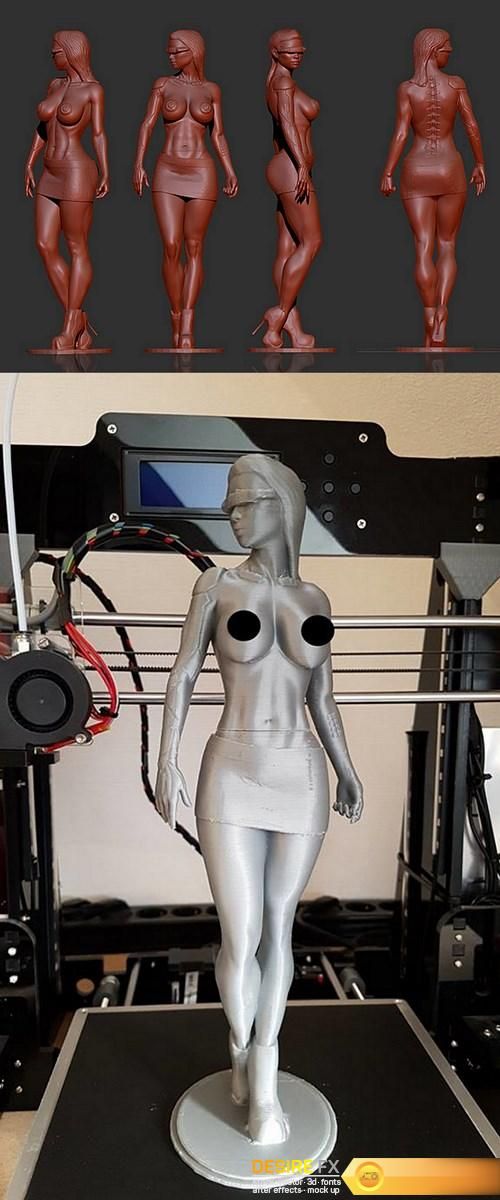
Traditionally, rubber manufacturing has required injection molding, casting, or sheet lamination. Rubber-like materials are far too soft to machine, and 3D printing was restricted to harder plastics for most of its development. Now, new developments in 3D printers and materials have opened up a wide range of new possibilities for 3D printed rubber products. So how does 3D printing compare to casting or injection molding for manufacturing rubber?
Short Lead Times and No Setup Costs
Injection molding requires machined metal molds that cost tens of thousands of dollars and take months to produce. Any design changes require new tools, making adjustments extremely expensive and time-consuming.
In contrast, 3D printing requires no tooling or other setup costs and can begin production immediately. This leads to parts that can be manufactured in as little as one day and much greater affordability at low quantities, making 3D printing Moreover, design changes are easy and can be executed at no additional cost.
The Best Choice for Rubber Prototypes
When it comes to product development, 3D printed rubber is a godsend. Even under the most ideal conditions, traditional technologies take weeks of lead time and tens of thousands of dollars for each new design.
Because 3D printing doesn’t require any tooling or setup, 3D printed parts can quickly be designed and redesigned at no additional cost. This agility has made 3D printing an indispensable part of prototyping and product development.
A Question of Quantity
As a result of these differences in lead times and setup costs, 3D printing is much more economical for small- to medium-volume production, while casting and injection molding provide greater value for productions of 1000 parts or more.
Although metal molds are expensive, molded parts become very cheap to produce once the tooling is made. When those initial costs are spread out over thousands of parts, individual part costs plummet, making injection molding the least expensive technology around for high-volume manufacturing.
3D printing, on the other hand, generally stops providing additional per part savings once part quantities exceed the capacity of a single machine. As a result, 3D printing has a much flatter cost curve that makes it a great option for small to medium quantities but significantly less economical for large production runs.
Unlimited Design Possibilities
Rubber 3D printing can easily achieve complicated designs that would simply not be possible with other manufacturing technologies. From interior cavities and lattices to variable wall thicknesses, organic shapes and built-in hoses—all of which are difficult or impossible to create with injection molding—3D printed rubber parts unlock endless new design options. You can even combine multi-part assemblies into single pieces, saving costs and improving functionality.
Plus, 3D printed parts can be highly customized, down to single parts at a time, without additional costs. This is especially useful for industries like medicine or athletics that have a high demand for products customized to each individual user. Needless to say, this would be extraordinarily expensive with casting or injection molding.
To learn more about the unique design capabilities of 3D printing, check out our Design for Additive Manufacturing (DfAM) Guide.
Is It Really Rubber?
3D Printed Rubber Materials
The answer to whether 3D printed rubber is really rubber depends who you ask. There are a lot of materials that are referred to as rubber: thermoplastic polyurethane, thermoplastic elastomer, silicone, and, of course, natural rubber!
Natural rubber, also known as latex, cannot be liquefied and re-solidified in the manner required by 3D printers. However, thermoplastic elastomers can achieve similar levels of flexibility and softness to rubber and have the thermal properties necessary for 3D printing.
The most effective rubber-like materials for 3D printing are thermoplastic polyurethane (TPU) and thermoplastic elastomer (TPE). It’s important to note, however, that both TPU and TPE refer to multiple materials. In fact, TPU is really a type of TPE―distinguished by its use of polyurethane and increased hardness.
Thermoplastic Polyurethane (TPU)
Thermoplastic polyurethane (TPU) is valued by engineers for its flexibility and strength. Not only does TPU’s hardness (Shore 85A to 95A) make it easier to print than TPE, but it also provides higher abrasion, chemical and thermal resistance. Moreover, its resistance to oil and grease makes it a great fit for hoses, gaskets and seals. While not as soft as natural rubber, printed TPU can achieve thinner walls than molded parts to create a similar level of flexibility.
TPU can be 3D printed with Multi Jet Fusion or selective laser sintering and is widely used in transportation, medicine, home goods, consumer electronics, and more.
Thermoplastic Elastomer (TPE)
Thermoplastic elastomer (TPE) is softer than TPU―Shore 40A to 70A—and offers moderate abrasion, chemical and thermal resistance. TPE parts can be trickier to print than TPU due to the material’s softness, but it offers a smoother finish.
Nylon TPE is available for selective laser sintering and is used in many of the same industries as TPU. However, because softer TPE materials are not yet available for Multi Jet Fusion, TPE parts are more expensive and slower to produce.
Rubber Printing Services
Multi Jet Fusion (MJF)
Multi Jet Fusion 3D printing is the fastest, most affordable, and most effective option for most 3D printing projects. It is also the newest printing technology to allow rubber printing, with TPU01 options available in black or gray.
MJF prints combine industrial strength, accurate fine details and a high-quality finish to create parts that are equally suited to industrial parts and commercial products. With lead times as little as one day, MJF is the premier printing option for prototypes and small- to medium-sized production runs.
Selective Laser Sintering (SLS)
Selective laser sintering prints nylon TPE parts with excellent mechanical strength but is more expensive and slower than MJF. SLS parts have a medium-quality finish and larger surfaces can warp.
This technology scales relatively well at medium volumes and is generally cheaper than FDM at those quantities. SLS can achieve slightly larger part sizes than MJF.
Start Rubber 3D Printing Today
If you need rubber manufacturing for your business, RapidMade can help you take your projects from 3D models to high-quality 3D printed rubber parts in as few as two days. When you work with RapidMade, you get a team of 3D printed experts dedicated to helping you succeed.
Learn more about our 3D Printing Services and get started today by requesting a quote. We’ll review your project and get back to you within one day!
3D printing rubber - 3D printing with rubber: is it possible?
Is it possible to print with rubber?The answer is simple: no. Rubber is a type of sticky material that is pressed hot into a mold in which it cools and vulcanizes. When rubber vulcanizes, it becomes solid and holds its shape. However, after vulcanizing, rubber will never become liquid again. If rubber is heated again, it will burn. For 3D printing, you need a material that liquefies in a controlled way. This is not possible with rubber, so rubber is not suitable for printing.
What is possible, though?
Synthetic materials such as Thermoplastic Elastomers (TPEs) are good replacements for rubber. TPEs are suitable for printing. TPU filament is such a TPE, it has the same flexibility as rubber but it already melts at 60°C. Rubber is an organic material: the properties of rubber cannot be influenced. However, with TPU we can determine, for example, hardness, heat resistance and wear resistance. We imitate the organic material, but we ensure that we get the desired and most optimal properties.
TPEs, including TPU, are used for various applications in industry. You can think of shoe soles, but industrial applications such as sealing rings are also a good example.
What do I need to consider when printing with TPU?
Printing with TPU is difficult. Therefore, it is necessary to practice with PLA first before printing with TPU. TPU needs more time to melt and flow. If you print too fast, the material will collapse. Therefore, it is important to reduce the printing speed. The type of printer you use is also relevant to printing TPU. If the drive motor is at the back of the printer, the material is pushed through the extruder to eventually melt into the print head. With direct-drive printers, where the motor is located in the print head, the filament does not have to be pushed through the entire extruder. It only has to travel a short distance until it is melted. Imagine pushing a rubber band through a pipe, the rubber band will accumulate: the greater the distance, the harder it gets. If the drive motor is in the print head, the filament has to travel a shorter distance. So you need a printer with a direct drive to print well with TPU filament.
How do you affect flexibility?
There are different TPEs available: the ones that are really stiff and others that are really elastic. However, the elasticity of the final product is not only influenced by the filament used. The printing technique also affects the elasticity. The thinner you print, the more elastic your product becomes. For example: printing a honeycomb structure creates thin layers with air in between. In this way you can determine which part is more flexible than the other. Thanks to the printing technique, you can achieve different levels of flexibility. When rubber is vulcanized, the end product is always solid. So it is not possible to play with the elasticity of rubber.
Can I combine support material with TPU?
When you use support material, you have to pay attention to the print and bed temperatures. These should be about the same temperature as the filament being used. PVA needs about the same temperature as TPU and therefore PVA is the best option to combine with this filament. Is it possible to combine TPU with a material other than the carrier material? Yes, but in this case both must also have the same print and bed temperature. ABS needs a higher temperature than TPU. Therefore, this would not be a good combination because the TPU filament will melt on the print bed. We also recommend that when printing with two materials, the parts should be mechanically joined. That way, the parts will stick together even if the print adhesion does not. More information on printing with support materials can be found here.
Our dddrop RAPID ONE features a direct drive, so it’s suitable for printing TPU. Furthermore, for optimum print quality, we offer our own dddrop TPU filament. In case you have any questions, please feel free to contact us: [email protected]. We would love to help you.
All dddrop administrator content is written and edited by the dddrop marketing team.
3D Printing Knowledge Base
"rPETG GF - Printing Options, Material Properties and Tips"
rPETG GF is an engineering thermoplastic made from recycled PETG with the addition of glass fiber filler. The filament allows it to be used for tasks that require increased strength and wear resistance of end products.
Continue reading →
"Ten Ways to Save Filaments, Money and Nature"
In this article, we'll share some tips for saving 3D printing plastic so that 3D printers stay full, wallets thick, and nature clean.
Continue reading →
Web-Free 3D Printing: Adjusting Retract in Cura Slicer
If you've experienced thin filaments around web-like prints, it's most likely a problem with sub-optimal retract settings. We tell you what it is and how to deal with it.
Continue reading →
Miniature 3D Printing Tips
Hobby 3D printing is a popular use for 3D printers, often involving the production of small toys, souvenirs, and fine art objects. The task is not easy, and in this article we will share tips for 3D printing miniatures.
Continue reading →
Cura Slicer Infill Types
One of the advantages of 3D printing over injection molding is that 3D printed products can be made partially hollow, saving time and material, and at the same time reducing weight. In this article, we will deal with different filling options - how it happens and how it is used.
Continue reading →
"Lithophany on a 3D printer: how to make translucent images"
Lithophany is an artistic technique for creating translucent photographs or drawings, for example, to decorate unique lamps. 3D printing technologies are great for artisanal production of such images, called lithophanes. We'll tell you how it's done.
Continue reading →
"Calibration cubes, or How to train a 3D printer"
If immediately after starting FDM/FFF, the 3D printer produces arbitrary shapes to the envy of the best abstract artists, do not rush to panic. Most likely, the equipment just needs to be calibrated, and we’ll tell you how to do it under the cut.
Continue reading →
"Buying a used 3D printer: how to save money and not get into trouble"
Used FDM 3D printers are a good option, especially when more capable or modern hardware is needed, but the budget leaves a lot to be desired. In this article, we will share tips for purchasing 3D printers in the secondary market and tell you what you need to pay attention to before buying.
Continue reading →
“Painting products after FDM 3D printing”
Nowadays, there are enough 3D printers with multiple extruders or filament switching systems, but if this is not enough, you can increase the presentability, and often the durability of 3D printed products painting. In this article, we will deal with the main points of coating and pigmentation.
Continue reading →
"Ten Interesting Hobby 3D Printing Projects"
We can talk about the possibilities of additive technologies as much as we like, but it's better to see once than hear a hundred times. Better yet, print your own! We offer a selection of interesting projects that can be implemented using a home 3D printer.
Continue reading →
Support structures in FDM 3D printing
Supports are a necessary evil: they cause a lot of inconvenience, but often it is simply impossible to get products without them, especially when it comes to 3D printing models with hinged structures. In this article, we will talk about supports - what they are, how to avoid them and what to do if you cannot do without supports.
Continue reading →
"Best 3D Printers of 2022"
Today's additive market is saturated with all kinds of 3D printing equipment, and sorting through all this variety can be very difficult. We have prepared a list of a dozen of the most interesting, in our opinion, FDM and photopolymer 3D printers for amateurs and professionals.
Continue reading →
FDM 3D Printer Basics
Thinking about buying a 3D printer and don't know where to start? Then you are welcome under the cat: in this article we will try to explain as clearly as possible what FDM 3D printing is and how to work with FDM 3D printers.
Continue reading →
"How to deal with deformations in 3D printing"
Any production process that involves cooling polymers or metals will be accompanied by shrinkage of materials, whether it is plastic injection molding, metal casting or 3D printing. In this article, we will share tricks to help combat the unwanted effects of shrinkage - deformation, cracking and peeling off.
Continue reading →
“How to clean the nozzles of FDM 3D printers”
The nozzle is one of the simplest and at the same time the most critical parts of an FDM 3D printer, since the ability of the equipment to lay material depends on the correct operation of the nozzle. In fact, everything is not so simple: a lot depends on the material from which the nozzle is made, the filaments used, the operating temperature, the shape and even the diameter. In addition, the nozzles are often clogged. In this article, we will figure out how to correctly identify problems and take care of a small but important detail.
Continue reading →
"Top Ten Parameters of FDM 3D Printing"
In the last article, we talked about the best 3D printing software in 2022. Today we will talk about preparing a 3D model for printing. Slicers are used to prepare 3D models for 3D printing. These programs not only convert digital models into machine code, but also allow you to adjust all the parameters of the FDM 3D printers. The key settings will be discussed in this article.
Continue reading →
"Best 3D printing software in 2022"
3D printing is a multi-step process, because you first need to design a 3D model, check it for errors, convert it to machine code, and only then into it's a 3D printer. In this article, we will share examples of programs that can help at every stage of preparatory work and directly during 3D printing.
Continue reading →
"G-Code Basics: Basic Command Reference for FDM 3D Printers"
G-code or Gcode is machine code, that is, a sequential set of commands for 3D printers generated by slicers. At the same time, the G-code often has to be edited manually if the slicer does not have the appropriate functionality or the user simply needs to change the behavior of the 3D printer. In this article, we will share a list of the most widely used commands.
Continue reading →
Getting Started with FDM 3D Printing: A Beginner's Guide
Especially for those who are just starting to comprehend the basics of 3D printing, we offer a selection of useful tips to solve the most common problems when working with FDM 3D printers.
Continue reading →
"The best programs for 3D modeling for 3D printing"
the most popular free and commercial programs of different levels of complexity and functionality.
Continue reading →
"The most popular slicers for FDM 3D printing and more"
What is a "slicer"? This is a program that converts digital 3D models (usually in STL, OBJ, or M3F formats) into machine code (G-code), a series of commands that a 3D printer understands. Do not even try to make the 3D printer figure out what is required of it from the 3D model. Instead, use one of the solutions on our list, especially since most of them are free.
Continue reading →
"PrusaSlicer: overview of the program, functionality and basic settings"
PrusaSlicer is a free, feature rich slicer from Prusa Research based on the Slic3r system by Alessandro Ranellucci. The slicer was originally called Slic3r PE (Prusa Edition), but as it moved more and more away from the source, Prusa officially renamed it in May 2019 to avoid confusion. Since then, PrusaSlicer has continued to evolve and be updated every few months.
Continue reading →
"Who and how makes money on 3D printing"
Are you ready to make money with direct hands and a 3D printer? Okay, but before diving head first into the business, it would be nice to understand exactly how 3D printing is changing the face of the industries around us in order to find its niche. Let's watch.
Continue reading →
"The Best Professional Storage Solutions for 3D Printing Plastics"
3D printing results.
Continue reading →
"PEEK: how to print, characteristics and properties"
Polyetheretherketone (PEEK, PEEK) is a special polymer with outstanding properties, which in some cases can replace metals, for example in the production of aircraft parts or implants.
Continue reading →
“How to properly (and not) dry filaments for 3D printers”
As we found out in the previous article, the best option is not to let the filaments absorb moisture at all, but in practice this is almost unrealistic. So, before 3D printing, it is advisable to play it safe and start drying the plastic. We'll talk about this under the cut.
Continue reading →
“Post-processing of 3D FDM printed products”
In most cases, 3D printed models do not need post-processing, but this applies mainly to functional products. In many cases, surfaces are required to be processed to a finished look using various tools, and in this article we will look at the basic techniques.
Continue reading →
"The most common extrusion 3D printing problems and solutions"
FDM/FFF A 3D printer is a complex machine, and plastics for 3D printing can vary greatly in properties. As a result, it may be difficult for a novice user to identify the causes of defects in printed products. Especially for such cases, we have prepared a guide with a list of the most common problems and solutions.
Continue reading →
"How to properly store 3D printer filaments"
When it comes to storing 3D printing plastic, it's better to be safe than sorry. If you protect filaments for FDM 3D printers from moisture and dirt, you can count on better and trouble-free 3D printing, and this is not at all difficult to do. We tell you how and why.
Continue reading →
"Resin 3D printing in industry"
In this article, we will look at the industrial use of extrusion 3D printing technologies with polymers and composites. No whistles and gnomes, only serious application!
Continue reading →
"Top 10 3D Model Sites for 3D Printing"
If you already have a 3D printer and 3D printing plastic, all you have to do is find digital models. Do-it-yourself 3D modeling is interesting, but mastering this skill will take a lot of time. In the meantime, we suggest looking for something interesting on the sites in our selection.
Continue reading →
Selecting Plastic for 3D Printing: A Guide to REC Materials and Applications
This article collects basic information on commercial 3D printing plastics and composites under the REC brand.
Continue reading →
REC Multi-Material 3D Printing Guide
Especially for those who practice 3D printing of composite products and soluble supports on FDM 3D printers, we have prepared a handy guide to help predict results in terms of adhesion and shrinkage when working with two different materials at the same time.
Continue reading →
"Composite materials for 3D printing"
Over the past few years, the intensive development of additive technologies has allowed the introduction of 3D printing in most industries, and this, in turn, has led to new requirements for 3D printers and the emergence of brand new, customized consumables. The expansion of the line of consumables mainly affected the most popular and affordable 3D printing technology — FDM/FFF.
Continue reading →
"Adhesion and 3D printing: everything you need to know"
@media screen and (min-width: 991px){ . mobil{ display: none; } Many 3D printer owners experience parts coming off the table during 3D printing. Let's take a look at the causes and solutions.
Continue reading →
"X-Line UltraX - printing parameters, characteristics and material properties"
UltraX is an engineering thermoplastic capable of withstanding high loads. This composite material is based on structural polyamide-6 filled with short carbon fibers.
Continue reading →
"PETG Biocide - material description, print settings and properties"
REC Biocide PETG is a special composite material that has disinfecting properties due to additives in the form of special nanoparticles distributed over the polymer matrix.
Continue reading →
"X-Line FormaX - print parameters, material properties and tips"
Formax is an engineering thermoplastic based on ABS with the addition of carbon fibers (up to 15%), capable of withstanding heavy loads and high temperatures.
Continue reading →
“Flex to flex: what are flexible filaments and how to work with them on a 3D printer”
Flex is just a general name for 3D printing materials with a characteristic flexibility. This group includes a variety of filaments with a wide variety of compositions, so disputes on the topic “which flex is better” are often meaningless. We decided to approach the practical side of the matter and collect in one article useful information on the options that are produced under our brand, that is, REC, and at the same time explain how to work with them.
Continue reading →
REC PP+: print parameters, features and properties
REC PP+ is a modified polypropylene filament that allows you to print strong and durable products with high chemical and impact resistance. Continue reading → Main advantages and disadvantages of REC PP+ Polypropylene is one of the most common polymers due to a number of positive characteristics. This polymer is non-toxic and has a low specific gravity (with the same volume, polypropylene is about a third lighter than the popular PLA plastic), excellent resistance to abrasion, shock loads and mechanical...
"PVA - print parameters, characteristics and properties"
REC PVA is a special filament capable of facilitating the 3D printing of complex parts. It is a specialized support material that is soluble in water and does not require mechanical processing.
Continue reading →
«REC Friction: printing parameters, characteristics»
REC Friction is a structural composite in the form of a wear-resistant glass-filled filament based on polyamide-12.
Continue reading →
"5D printers, description, features, types"
A five-axis 3D printer or 5D printer is the next generation of conventional 3D printers. Their difference is that they have five axes of mobility, which means many new possibilities in printing.
Continue reading →
"PMMA-plastic (REC Cast): printing parameters, properties and characteristics"
REC Cast is a specialized material designed for 3D printing of burnt foundry master models.
Continue reading →
"TPU plastic (REC Easy Flex): how to print, characteristics and properties"
TPU filament (REC Easy Flex) makes it possible to print flexible, elastic and durable TPU parts.
Continue reading →
"Flex plastic: how to print, characteristics and properties"
REC Flex is a material that resembles hard silicone in performance and is suitable for the manufacture of durable flexible parts suitable for outdoor use.
Continue reading →
"REC Rubber: print settings, description and specifications"
synthetic rubber filament.
Continue reading →
"ASA (REC Eternal): description, advantages, printing options"
Acrylonitrile styrene acrylate (ASA, ASA), offered by our company under the name REC Eternal, is a close relative of ABS plastic, but with a number of advantages, the most important of which is the possibility of long-term operation in the open air.
Continue reading →
«HIPS: description, printing parameters, storage and post-processing of the material»
In modern industry, polystyrene is one of the most common polymers used in the production of household appliances, household supplies, packaging and containers, including food. In 3D printing, polystyrene plays another important role as a support material for the popular ABS plastic.
Continue reading →
"PLA plastic: characteristics, print settings, tips"
Polylactide (PLA, PLA) is a biopolymer that is very popular among 3D printing enthusiasts for two main reasons.
Tags: PLA plastic
Continue reading →
Choosing a liquid photopolymer for a 3D printer. Classification of materials for SLA/DLP 3D printing.
Contents:
- Introduction
- SLA Overview
- SLA standard resins
- Standard photopolymer resin - Standard
- Clear photopolymer resin - Clear
- Engineering photopolymer resins
- Rigid photopolymer resin - Tough (like ABS)
- Durable photopolymer resin - Durable (PP-like)
- Heat resistant photopolymer resin - Heat resistant
- Rubber-like photopolymer resin - Rubber-like (Elastic)
- Ceramic photopolymer resin - Ceramic filled (Hard)
- How to choose the right resin for your application
- Dental and medical SLA resins
- Medical Device Photopolymer Resin - Custom Medical Appliances (Class I Biocompatibility)
- Dental Long Term Biocompatible Resin (Class IIa Biocompatible)
- Class I biocompatibility vs Class IIa biocompatibility
- Cast SLA resins
- Cast resin for jewelry making
- Generalized rules
Hello everyone, Friends! With you 3DTool!
This article compares photopolymer resins using Formlabs SLA 3D Printing Products - standard standard
Catalog of photopolymer 3D printers
Photopolymers from FormLabs
Detailed review of the Formlabs Form 3 3D printer
Introduction
The stereolithography prints plastic parts with high resolution, good fine detail, and a smooth surface. Due to the variety of photopolymer resins available for SLA, this technology is used in many different industries:
-
"Standard" photopolymers are used for prototyping
-
Engineering photopolymers have certain mechanical and thermal properties
-
Dental and medical photopolymers have biocompatibility certificates.
-
Cast photopolymers have a zero ash content after burning.
SLA 3D printing resin overview
SLA uses a laser to cure a liquid photopolymer resin. This process is called photopolymerization. Various combinations of polymers and other additives that are part of the resin allow you to get different material properties.
The main advantages and limitations that are common to all resins in SLA 3D printing are:
Benefits:
Weaknesses:
Base Resins for SLA
Post-Processing SLA/DLP 3D Printing Article
Standard photopolymer resin - Standard
Standard resins produce parts with high stiffness, detail and a smooth surface. The low cost of resins, from $250 per liter, makes them ideal for prototypes.
The color of the resin also affects its properties. For example, in FormLabs products, gray resin is suitable for models with fine details, and white resin for parts that require the smoothest possible surface.
Benefits of using Standard grade resins:
Cons Standard:
Also included in the class of "Standard" photopolymer resins from FormLabs is the Color KIT - a set of special dyes and "Color Base" photopolymer resin for mixing and obtaining a variety of color solutions. This eliminates the need for painting parts after 3D printing.
FormLabs Engineering Photopolymer Resins
Engineering resins have a range of properties for injection molded plastics.
All engineering resins require additional UV curing, such as using the Form Cure, to achieve their maximum properties.
Tough photopolymer resin - Tough (ABS equivalent)
Tough resin was developed for models that need to withstand high loads and be durable.
This material produces strong, shatter-resistant parts and functional prototypes such as snap-on housings.
Pros:
Cons:
Ideal for: functional prototypes, mechanical parts
Durable photopolymer resin - Durable
Durable resin is a wear-resistant and flexible material with mechanical properties similar to polypropylene.
Durable photopolymer produces models with a smooth glossy surface and high resistance to deformation.
Durable Resin is ideal for:
- Bushings and bearings;
- Various functional compounds
Pros:
Cons:
-
Not suitable for thin wall parts (recommended minimum wall thickness 1mm)
-
Low heat distortion temperature
-
Low flexural strength (lower than hard resin)
Ideal for: functional prototypes.
Refractory Photopolymer Resin - Formlabs High Temp Resin
The heat resistant resin is ideal for parts that require high temperature resistance and operate at high temperatures.
Formlabs High Temp Resin provides the highest melting point (HDT): 238°C at 0.45 MPa.
The resin should be used to print detailed, accurate prototypes with high heat resistance.
Pros:
Cons:
Flexible Resin
Rubber-like resin allows flexible parts to be made. This material has a low tensile strength and high elongation at break and is well suited for parts that will be bent or compressed.
It can also be used to add ergonomic features to multi-material assemblies such as: dies, wearable prototypes, handles, pads and grips.
Pros:
-
High flexibility (high elongation at break)
-
Low hardness (simulates 80A durometer rubber)
-
High impact resistance
Cons:
-
Doesn't have all the properties of real rubber
-
Requires extensive support structures
-
Material properties deteriorate over time as the part is exposed to ultraviolet radiation (sunlight)
-
Not suitable for thin wall parts (recommended minimum wall thickness 1mm)
Ideal for flexible prototyping.
Ceramic photopolymer resin - Rigid Resin
This resin is reinforced with glass, which provides very high rigidity and a polished surface. The polymer is very resistant to deformation and is excellent for 3D printing thin elements.
Ideal for: molds and tooling, jigs, manifolds, retainers, electrical and automotive fixture housings
Thermal management components printed with SLA ceramic (hard) resin. Image credit: Formlabs
How to choose the right resin for your application
The table below shows the main mechanical properties of photopolymers for SLA:
Source: Formlabs
Standard resin ( standart ) has high tensile strength but is very brittle (very low elongation at break) so it is not suitable for functional parts. The ability to create a good part surface makes it ideal for visual prototypes and art models.
durable ( durable ) resin has the highest impact strength and elongation at break of any other SLA material. Best suited for prototyping parts with moving parts and latches. It lacks, however, the strength of thermoplastic 3D printing materials such as SLA nylon.
tough tough resin is a compromise between the material properties of tough and standard resin. It has a high tensile strength, so it is best suited for rigid parts that require high hardness.
heat resistant resin ( heat resistant ) can withstand temperatures above 200 o o C, but has poor impact strength and is even more brittle than standard resin.
ceramic ( ceramic reinforce ) resin has the highest tensile strength and flexural modulus, but is brittle (poor elongation at break and toughness). This resin is preferred for thin wall parts that require increased rigidity.
The graphs below compare the mechanical properties of the most common SLA materials visually:
Comparison chart for elongation at break and toughness for common SLA printing specifications and standard media. Image courtesy of Formlabs.
Stress-strain curves for conventional SLA technologies and standard materials. Image credit: Formlabs
Comparative chart of material properties of various technical resins. Image credit: Formlabs.
Dental and medical resins
Photopolymer resin for medical devices - Custom Medical Appliances (BIA Class 1 biocompatible resins can be used to make medical equipment such as surgical guides. Parts printed on this resin can be steam sterilized in an autoclave for direct use in the operating room.
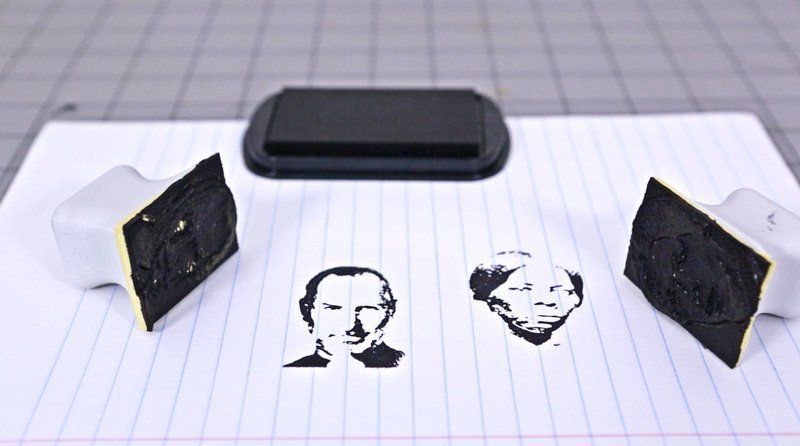
Pros:
Cons:
- Moderate wear and tear resistance
Ideal for: Surgical aids and appliances
Dental Long Term Biocompatible Resin - Dental Long Term (Class 2A biocompatible) 3 60416
These resins are specially formulated for long term dental fixtures. Class 2A biocompatible resins can come into contact with the human body for up to a year.
High resistance to breakage and wear make this resin ideal for making rigid cotter pins or retainers.
Pros:
Cons:
-
High price
Ideal for: durable dental instruments, fracture and wear resistant medical parts, rigid cotter pins, retainers
What is the difference between class 1 and class 2a biocompatibility?
Class 1 biocompatibility rules apply to materials that are allowed to be used for:
-
non-invasive devices that come into contact with intact skin
-
devices for temporary use or short-term use in the mouth or ear canal or in the nasal cavity
-
reusable surgical instruments
Class 2a biocompatibility rules apply to materials that are allowed to be used for:
-
devices that come into contact with bodily fluids or open wounds
-
devices used to introduce substances into or remove substances from the human body
-
invasive short-term devices such as invasive surgical items
-
long-term implantable devices placed in the teeth
Photopolymer resin in SLA 3D printing for jewelers
Jewelry resins
This material allows you to print models with fine details and a smooth surface without leaving ash or residue after burning.