3D printing cost per cm3
How Much Does 3D Printing Cost?
There are several variables that contribute to the cost of 3D printing, including print time, the type of material used, and post-processing labor. Many 3D printing service companies will bill based on an hourly rate, while others may bill according to cubic inches or a combination of both.
For sake of clarity, this article will discuss 3D printing cost factors as they pertain to the industrial level. Below, we will discuss how the print time, type of material, and post-processing labor factor in to the cost of a 3D printed part.
Print Time
Many factors influence the time it takes to complete a 3D print. These factors primarily stem from the part’s design specifications, including its complexity, overall size, layer height, and resolution. Below, we’ll discuss what these elements are and how they can affect the build time:
Complexity
The complexity of a part’s geometry largely determines the shape of the cross-sectional layers that the 3D printer uses to create the part. If the layers are simple, such as single-island layers for a cube, the printer can complete them quickly. However, where there are small features, the printer will have to stop, move to the next location where the material continues, and start again. This creates islands that the printer must form boundaries for before continuing. Furthermore, some 3D printing technologies utilize support material for complex designs, and creating a layer made up of both model material and support material will take longer than a layer composed of only model material.
Overall Size
A part’s size can shorten or extend the print time drastically. Every 3D printer has a point of origin where the print head nozzle, laser, or light beam starts each layer. A large part requires this print head to move a farther distance from its starting point and, thus, the layer takes longer to complete than a part with a smaller footprint. Tall parts are also often time consuming because they require more layers to build them. For small parts, however, the printer can move through layer creation rapidly because the print head requires less movement from its starting position.
Z Height
In addition to overall size, your chosen Z height, or layer height, is an indicator of how long it will take to print your part. Every 3D printer will produce your part’s layers with a specified height so that all the layers are uniform in thickness. Thicker layers will allow the part to be printed more quickly than it would with thinner layers. However, thinner layers may be desired for a higher quality appearance in the part.
Resolution
A part’s quality, which is affected by the 3D printer’s resolution, is also worth considering when calculating print time. Resolution is primarily determined by the layer height used by the 3D printer, which can be adjusted for a finer resolution as desired. It is important to note, however, that a finer resolution will mean more layers, which means more time to print your part.
Furthermore, you may note that if you are planning to produce your part with a Fused Deposition Modelling (FDM) 3D printer you will also need to account for infill influencing your part’s build time. FDM printers come with automatic settings to control your part’s infill, and it may be crucial to determine which infill will best suit your part’s application requirements while still accounting for time lost or gained from the selection.
Material
In addition to how much material you are using, your cost will also depend on what type of material you select. The majority of 3D printing materials can be categorized as one of four types: thermoplastics, photopolymers, polymers, and metals. Cost will fluctuate based on the specific material and the manufacturer, but for the most part, the estimates below are what you can expect each type of material to cost.
For these cost estimates, we are using numbers for raw materials only. A 3D printing service company will typically mark up costs 2-3 times these amounts, which you should factor into your total cost if producing via that route.
Thermoplastics
Thermoplastics are rigid, widely used materials that must be melted prior to extrusion. They are used in FDM 3D printers, which is the most common type of 3D printing. Because they are so commonly used, the cost of these materials is one of the lowest available. The average cost for thermoplastic model filament will range from $3.50 to $7.50 per cubic inch. Because FDM printers require the use of support material, it is necessary to include the cost of support material filament, which will cost around the same as model filament. However, only a fraction of the part’s overall volume will be comprised of this support material.
Photopolymers
Photopolymers are liquid resin thermosets that must be cured by UV light. They are used in PolyJet, MultiJet, and Stereolithography (SLA) 3D printers. Photopolymer model material will run $0.32 to $0.36 per gram, and support material may be between $0.11 and $0.21 per gram. This cost is based on the fact that photopolymer resins are made for these specific 3D printing processes and are not as widely used as thermoplastics. Keep in mind that SLA uses the model material for support structures and, therefore, will not need any additional support material to be purchased.
Polymers
Polymers are similar to thermoplastics, but they exist in a fine powdered state and are sintered together via a laser with Selective Laser Sintering (SLS). This powdered material is very cheap, costing around $0.10 per gram. Due to the nature of the SLS process supporting the parts with a type of powder “cake” of unsintered material, other support material is not needed.
Metals
Metal 3D printing materials are essentially the same as polymers in that they exist in a powdered form and are melted together via a laser with Direct Metal Laser Sintering (DMLS). However, metal material is highly expensive, reaching around $0.60 per gram. Additionally, even though the DMLS printing process forms a powder cake like that of SLS, support structures are needed because metal is more dense than plastic.
Post-Processing Labor
After a print is done, the part will still have to go through more steps to make it ready to use. Some of these steps, such as the removal of support material, washing, sandblasting, sanding, drying, and gluing, will be mandatory for some parts and will not cost any extra fee. However, most all add-on steps, such as priming, dyeing, painting, coating, and more, will require extra time and manual labor to complete the part, which will factor into and result in a higher total cost.
3D Printing at 3 Space
Here at 3 Space, we aim to provide quality 3D printing services at an affordable price. Our expert engineers are happy to help advise you in how to get the best bang for your buck. For a personalized quote, contact us today.
How much does 3D printing cost?
3D Printing Cost Keyfacts:- A single 3D printed part can cost anywhere from 0.75 up to hundreds of dollars/euros
- A 3D model is compulsory to get a precise pricing
- Material, model morphology and delivery time can greatly affect the price
If you already have a 3D model click here to get a quote immediately and without signup
4 Cost Facts About 3D Printing You Probably Didn't Know
1.
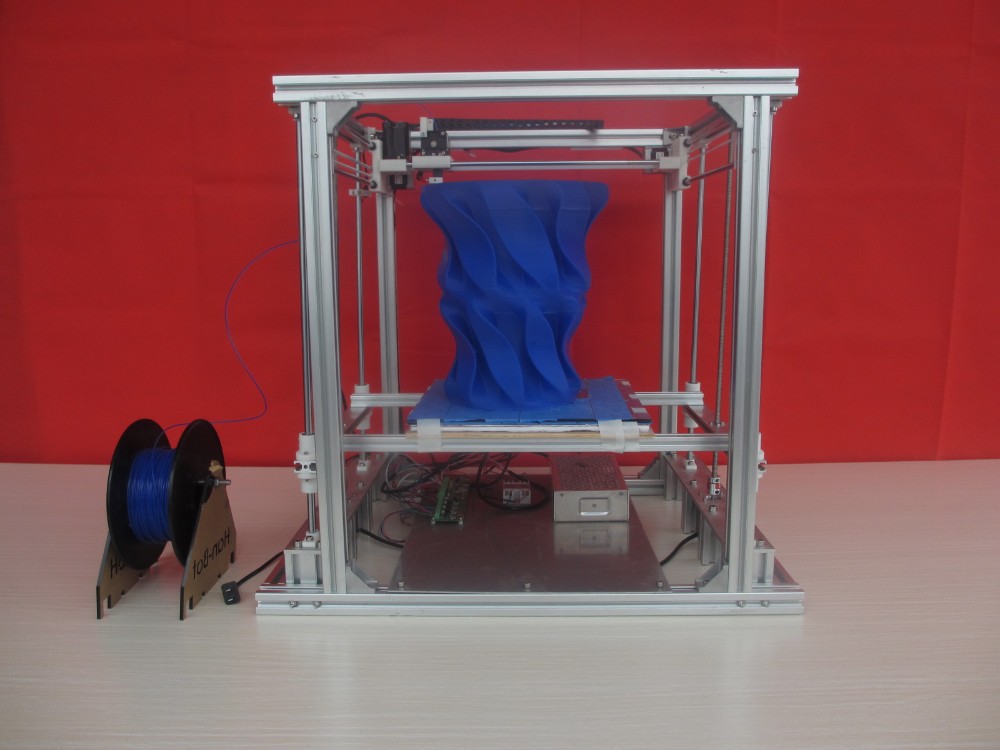
A 3D printer can cost from 150$/€ for a cheap FDM or MSLA printer to almost 1 million$/€ for a top metal 3d printer and in addition to this it requires maintenance costs, electricity, etc. which, however, we neglect here to simplify. First of all consider that in the current market you cannot think of making sense of a 3D printer by using it less than 8 hours a day for 250 working days (if you have the purpose of making money and you are not one of those types who buy 3d printers because they like to have them around) it is better and much cheaper to have the parts done by an external 3D printing service.
So let's say you purchased a $/€1500 3D printer that you plan to use 8 hrs/day for 2 years.
8 x 250 x 2 = 2000 hours of printing
$/€ 1500 / 2000 hrs = $/€ 0.75/hr
All this means almost nothing, why?
Because it is not so important how much a machine costs per hour but how much it PRODUCES per hour in terms of cm3 of usable part:
Considering that the machine in the example as a FDM printer we can say that it can reasonably produce 10cm3 / h (I know it can also go faster but with this speed we are sure not to have to redo the piece because it turned out badly).
$/€ 0.75/hr / 10cm3/hr = 0.075$/€ per cm3
Since a 3Dbenchy has a volume of about 16 cm3 it would cost around:
0.075$/€ per cm3 x 16 cm3 = 1,2 $/€
Keep in mind that in this case we have not calculated the time necessary to prepare the file, the material and the maintenance costs, nor have we taken into consideration the fact that if you will use this machine few hours per week and not 8 hours a day, producing a single 3Dbenchy could quickly get to a real cost of 30 $/€.
#3DBenchy is a 3D model specifically designed for testing and benchmarking 3D printers.
Upload and quote now your 3DBenchy
2. Model volume
Obviously the larger the part, the more material and time needed for the printing, the more it costs: it must be said that there is no direct proportionality because a part with double volume will not cost double but a little less than double because there are economies of scale linked to the preparation time that is spread on a larger piece.
You can reduce the cost by using a cheaper material or by partially emptying the part but this is not always technically and mechanically acceptable.
Larger is more expensive: 3D printing is a matter of size and material: larger parts need more time and material and are consequently more expensive
3. Material: huge differences
The material makes a huge difference on the final cost of the part: think that you can start from a PLA of 15 $/€ per kg to 500 $/€ of PEEK and even more. Moreover it should also be considered, at least for some technologies such as FDM and SLA, the cost of the supports that can be in a material (for example BVOH) normally more expensive than the printing material itself. Just to give you a value, our tiny 16 cm3 3DBenchy can cost, material only, from about 0.25 $/€ if made with cheap PLA to 8 $/€ made with 500 $/€ x kg PEEK.
Material matters: with the same 3D printer and production capacity the cost of the material can vary enormously.
Courtesy 3Dnative. See here the list of materials available from Weerg.
4. Post-processing
Contrary to what one might think, post processing is mandatory for any 3D printer and it has the serious flaw of being a considerable cost that is often seriously underestimated. In fact, finishing is not just the removal of supports in FDM or SLA printing which takes time and often can lead to damage to the part.
Post processing is also required by MJF and SLS printers: in this case the part just produced are covered by construction dust residues that must be removed with a good (read expensive) shoot peening technology.
Post-processing is a major cost in 3d printing: not only do FDM or SLA 3D printers require supports removal but also powder printers (MJF and the old SLS) need thorough cleaning. Quote instantly your 3D part
Conclusion
Should you buy a 3D printer or hire a 3D printing service?
As you have seen, there are many elements that contribute to forming the cost of a 3D printed part.
- If you are a hobbyist, and you're only printing for fun and because you are fascinated by 3D printing and by the part that is created before your eyes you can have great satisfaction with an investment of a couple of hundred dollars/euros FDM or MSLA printer.
- if you are a professional and you need functional parts in different materials and without defects in a few days, prepare to invest at least 250 / 300k $/€ in mixed FDM SLA and powder technology and be sure that you will use these machines each for at least 2,000 hrs a year, otherwise a 3D printing service or a 3D printing service online it will surely be more convenient.
Printing of ABS (ABS) plastic using FDM technology to order
Printing of ABS (ABS) plastic using FDM technology to orderPrinting ABS (ABS) with plastic using FDM technology to order
Technology: 3D PRINT
Loading . ..
Loading ...
Loading ...
Loading ...
Loading ...
Loading ...
Loading ...
Loading ...
Loading ...
Loading ...
Loading ...
Price
no more than 20 o/cm 3
Processing cost
+ fifty o for processing 1 item
Printing time
from 1 to 3 days
Calculate the cost
+ fifty o for processing 1 item
Printing time
from 1 to 3 days
Calculate the cost
Price
no more than 30 o/cm 3
Processing cost
+ fifty o for processing 1 item
Printing time
We print on the day of order*
Calculate the cost
Price
no more than 70 o/cm 3
Cost for processing
+ 500 o for processing 1 item
Printing time
from 5 to 7 days
Calculate the cost
Price
no more than 30 o/cm 3
Processing cost
+ fifty o for processing 1 item
Printing time
We print on the day of the order*
Calculate the cost
Price
no more than 20 o/cm 3
Cost per treatment
+ fifty o for processing 1 item
Printing time
from 1 to 3 days
Calculate the cost
Price
no more than 70 o/cm 3
Cost per treatment
+ 500 o for processing 1 item
Printing time
from 5 to 7 days
Calculate the cost
Price
no more than 50 o/cm 3
Cost per treatment
+ fifty o for processing 1 item
Printing time
from 1 to 3 days
Calculate the cost
Need an alternative?
More accurate
Photopolymer
Higher quality
Polyamide
Beneficial for series production
Molding plastic into silicone
Feedback form for calculating the cost of 3D printing
If you have a finished 3D model, upload it to the online form to calculate the cost of 3D printing.
If you do not have a 3D model or need a preliminary consultation, contact us by phone +7 (499) 390-03-77, send a 3D model with questions to our mail [email protected] or fill out an application, we will contact you and answer all your questions.
Fields marked with an asterisk (*) are required
- Cost of commercial 3D printing
- What is not profitable to print
- Examples of commercial printing
For some ideas, 3D printing is the fastest and easiest solution. In some situations, purchasing your own 3D printer can be a good solution, but sometimes it is much more profitable and faster to order the necessary product from a company specializing in 3D printing. Yes, and many owners of a 3D printer are thinking about how to “monetize” their hobby, but how to correctly calculate their costs?
Despite the fact that it is customary to indicate the price per gram of working material, simply multiplying the weight of the model by the cost of 1 gram will be wrong. In addition to the cost of consumables, many more, at first glance, non-obvious costs are added to the price of the product.
Each 3D printing technology uses its own consumables. Let's analyze the most popular and affordable of them.
Available technologies and key differences
Currently, a huge number of 3D devices have appeared, from small desktop ones that fit on the desktop to huge industrial machines. Among the most affordable, 2 technologies can be distinguished - FDM and photopolymer printers (LCD / DLP / SLA).
FDM 3D printing
Today, the most affordable 3D printing technology is FDM. A variety of materials and 3D printers allow FDM to be applied to a wide range of applications.
Schematic operation of FDM printer
A large selection makes it easy to choose a 3D printer for a specific task or find a universal device.
The material for printing is a plastic thread - filament. On the market you can find filament for various tasks, for every “taste” and budget. These can be very inexpensive ABS and PLA plastics or specific ones - conductive, burnable, etc.
Pros:
Cons:
Despite the fact that FDM allows you to print a wide range of plastics with different properties, the technology has some limitations. For example, it is impossible to obtain a perfectly smooth surface, to produce miniature and very thin elements, or to produce parts with very complex internal geometry with high accuracy.
Photopolymer printing
Photopolymer printers can work on one of 3 technologies - SLA, DLP or LCD. These devices will come to the rescue if you need to make a small but very detailed model with many small details.
How photopolymer printers work
As a consumable material, a photopolymer resin hardened by UV radiation is used. Now there is a wide variety of photopolymer resins for every taste. From particularly strong and precise engineering or jewelry resins to soft flexes.
Pros:
-
High print precision
-
Good surface quality
-
A wide variety of printers and consumables
Minuses:
Photopolymer printers have shown themselves well in a variety of industries that require a perfectly smooth surface and high accuracy. They are used in dentistry, the jewelry industry, for making miniature master models for casting, and much more.
Industrial printers
These are already industrial machines, which require a separate room and sometimes certain requirements for ventilation, etc. In this article, we will not analyze these devices in detail, but briefly consider the most popular technologies.
FDM
In addition to desktop devices using FDM technology, industrial printers that work on the same principle are common.
This category includes devices with a large print area (from 30x30x30 cm and more). For example, Raise Pro2 with a print area of 30x30x30 cm.
Raise Pro2
Or machines designed for printing with refractory materials (eg PEEK). Such 3D printers usually have an active thermal chamber, and the extruder can be heated above 400 degrees.
CreatBot F160-PEEK for high melting plastics
Photopolymer printers
Industrial photopolymer devices usually have a much larger working area, compared to their "home" brothers. In addition, many processes have been optimized and automated for faster operation. On such printers, you can quickly and accurately produce a small batch of models, a large prototype or a master model.
Large Area Prismlab Industrial Resin Printer Family
Free Shipping
Add to compare
Product added to compare Go
Manufacturer | CreatBot |
Free Shipping
Add to compare
Item added to compare Go
Manufacturer | Raise3D |
Free Shipping
Add to compare
Item added to compare Go
Manufacturer | Prismlab |
Free Shipping
Add to compare
Item added to compare Go
Manufacturer | Prismlab |
3DP
3DP - Three-Dimensional Printing (translated as three-dimensional printing) is a logical continuation of conventional two-dimensional printers. Printing is done using nozzles that selectively apply a binder to the material (usually gypsum). A dye can be added to the binder and the model will be colored.
Colored plaster model
Since the plaster model is fragile, a similar principle is used for printing with metals. Only the finished product needs to be treated in an oven to remove the binder and improve strength. But despite the processing, such metal prints will still be inferior in strength to cast products.
MJM
This is a proprietary technology of 3D Systems. MJM is a mix of FDM, 3DP and sometimes SLA (depending on material chosen). Printing is done using a variety of small nozzles (from 96 to 488) located on the head of the machine. The accuracy and quality of the surface of models made in this way is in no way inferior to photopolymer printers.
Models made with MJM technology
Such devices can work with photopolymer resins, wax or thermoplastics. You can combine several materials at once - for example, for complex models, you can use wax as a support.
SLM
SLM is the layer-by-layer sintering of metal powder using a powerful laser. There are several similar technologies - SHS/SLS. The principle of operation is the same, only a thermal print head is used instead of a laser beam.
SLM Turbine
As a material for printing, you can use powders of various metals - gold, stainless steel, aluminum, various alloys, etc.
During printing, the working chamber is filled with an inert gas to prevent oxidation of metals. This allows printing even with titanium powder.
Models made by this method are in no way inferior, and sometimes even superior, to cast products. SLM allows you to produce models with complex internal geometry that cannot be produced by another method (casting or milling).
Cost of 3D printing
The cost of a model usually consists of several factors.
-
Equipment depreciation. The printer, like any machine, requires maintenance and periodic replacement of some parts. During operation, belts gradually stretch, bushings or linear bearings wear out. For example, when bushings or linear bearings are worn; shafts may wear out and need to be replaced.
Cost of materials
The main cost item for a 3D printer is, of course, the printed material.;
FDM (plastic filament)
Since FDM technology is by far the most common, the choice of filaments is very diverse.
-
Engineering plastics are usually nylon with various fillers added to improve the physical characteristics of the finished model. Special cost. plastics starts from 2000r per coil and above. It all depends on the manufacturer and filler (carbon fiber, fiberglass, etc.).
-
Decorative plastics are used to imitate various materials. Plastic can simply be unusually colored (luminous, transparent plastics) or a special filler is added to it (plastics with metal powder).
The cost of decorative plastics starts from 1500 rubles per coil and more, depending on the filler.
A big advantage of FDM is the diverse choice of materials to work with. This allows, having one printer, to produce almost any product - from a child's toy to a complex engineering prototype.
Photopolymers (resin)
Photopolymer resin printing technology is becoming more and more accessible. There are many different resins.
-
The cost of ordinary colored resin starts from 2500 rubles per 0.5 kg (volume +/- 0.5 l). You can find a smaller volume of resin (250 gr) on sale. You can buy several different resins in small containers and find out in practice which one is best for a particular model.
-
Engineering resins are resins with increased strength. They can be used not only for printing decorative items, but also for making functional prototypes and models. The cost for 0.5 kg starts from 5900r and above.
-
Special resins - burnable, dental, soft flexes, etc. Depending on the resin, the price for 0.5 kg can start from 4800 rubles and more. It all depends on the characteristics of the resin.
Photopolymer resins have not yet reached such a variety as FDM filaments, but they are surely catching up. Although due to the fact that a liter of resin costs significantly more than a spool of filament, the cost of the product is much higher.
Print examples
FDM
Mag Pull for G3 magazines.
The model was downloaded for free from an open source (the file can be downloaded here). Printing with engineering carbon-filled plastic (price per spool from 4700 rubles). The weight of the model with support is about 25 grams. Post-processing was not needed. The cost of the finished model is 250 rubles.
Plastic fastener
The file was downloaded from an open source (can be downloaded here). Plastic - carbon-filled nylon (price per coil from 4700r). The weight of the finished product is about 20 grams. Print without post-processing. The total cost is 200 rubles.
Model watch
The model is modeled to order (the cost of modeling is from 1000 rubles). The product is printed on an industrial printer using soluble support. Print without post-processing. The cost of the finished product - from 700 rubles per piece (depends on the number of required products).
Traction prosthesis
The model is taken from an open source (you can download the modified version of the prosthesis here). The weight of the used material is about 600 gr, printed with ABS plastic (the cost of the coil is from 800 r). After printing, post-processing and assembly took place. The total cost of the product - from 3000 r (depends on the print material, support material, filling, etc.).
Pedal layout
Production of a 3D model according to the drawing (from 1000 r). The weight of the finished model is about 200 gr. The product was printed with engineering carbon-filled plastic (the cost of the coil is from 4700 r). Post-processing was not needed. The cost of the finished product is about 3000 rubles.
Photopolymer printers
Model jaws for crowns
Files for printing were obtained using a 3D scanner and finalized in a 3D editor (the cost of scanning is from 3000 r, the cost of manual revision is from 1000 r). Printing on an industrial photopolymer printer. Post-processing is not needed. The cost of the finished product is from 80 r per gram.
Burnout resin rings
The model is made to order. Printing on a desktop SLA printer with a burnable polymer. Post-processing is not needed. The cost of the finished product is 200 rubles per product.
Miniatures
The models were bought on the myminifactory website (the cost of the model is from $2). Made with a desktop DLP printer. Post-processing was not required. The cost of the finished figurine is from 70 r per gram.
Custom 3D printing
Many owners of 3D printers are thinking about monetizing their hobby. But you should understand that the price of 3D printing “for yourself” and the price of commercial printing are very different.
When starting to print to order, it is better to have several printers working on different technologies.
Cost of commercial 3D printing
In addition to the cost of the model, to the commercial production of products, you can add:
-
Modeling. Often the client needs not only to make a part, but to pre-model it. It can be a simple cogwheel that doesn't take long to model, or it can be a complex sculpture that takes more time to model than it does to make.
-
Model post-processing. This can be simply the removal of supports, with cleaning of the place of their contact with the product, or a complete processing cycle (puttying, surface grinding, painting, etc.
).
It should be borne in mind that it is not always possible to print the model the first time. Sometimes it may take several attempts. And these are additional costs.
What is unprofitable to print
Despite the wide possibilities of 3D printing, there are models that are unprofitable to make on a 3D printer. For such models, it is better to use other manufacturing methods.
Commercial print examples
Jewelry for further casting
Manufacture of promotional items and souvenirs
Piece miniatures or master model for further casting
3D Printed Layout
Profitable to print on a 3D printer:
-
If the item is only sold as an assembly. For example, a small gear broke in the mechanism, but the mechanism is sold only “assembly”.
It is much cheaper to make the desired gear on a 3D printer than to buy the entire mechanism.
-
A small batch of parts. Small batches, especially models with complex geometry, are more profitable to produce on a 3D printer than by casting or other methods.
Totals
If you need several models or a small project, sometimes it will be more expedient to outsource manufacturing. After all, in addition to buying equipment and materials, you will have to understand the nuances of the settings and the characteristics of various materials.
Buying a 3D printer for commercial use is justified if you can fully load it with work or then it can be used for other purposes.
To print to order, you need to have several printers working on different technologies. It is better to get several devices with a smaller print area than to buy just one printer, albeit with a large working area.
#Useful
Expert in additive technologies and 3D printing with over 5 years of experience.