3D printing belgium
The Game Changer in Aluminum Additive Manufacturing for sustainable serial production
Vision
Unlock the next level of manufacturingcapabilities unveiling unprecedented products
Mission
Be the Game Changer in metal additivemanufacturing for serial production
Molten Metal Deposition
Molten Metal Deposition is our disruptive metal additive manufacturing technology. Just like the world’s most known plastic 3D printing process (FDM), ValCUN produces parts directly with liquid metal.
Our process is developed with a fully automated production chain in mind. It’s the only metal additive manufacturing technology suited for your factory floor without intervention and interruption.
- Reduced manufacturing lead times
- Easy and affordable operation
- Cost-effective and environment friendly
Patented technology
ValCUN reduces investment and operating costs by developing a patented technology that uses safe to handle feedstock material instead of metal powders and operates without high-lasers.Active Industries
Our cutting-edge technology is able to serve multiple industries. Curious to find out if Molten Metal Deposition can get you an advantage? Get in touch and we’ll spark your imagination.Compared to machining, when fly-to-buy ratio is over 70%, near net-shaping with ValCUN’s technology is more economical & sustainable.
Heat exchangers and heat sinks for electric vehicles, IT infrastructure, semiconductors, and more.
Unique surface structures for casings, housings, lamp shades, and other surfaces with unique properties.
Meet the A-team
Bound by passion and ambition. These beautiful faces are the brains and the hands behind ValCUN.Strengthened by a ton of experience
The ValCUN team is strengthened by a high level of experience. The board of directors consists of a multidisciplinary team of investors who bring in complementary knowledge in the fields of market intelligence, IP and entrepreneurship.Wim Beazar
Experienced Entrepreneur
Paul Maeyaert
IP Lawyer Fencer
Piet D’Haeyer
CEO Pedeo
Jan Robrechts
CEO Lavetan
Guido Beazar
Experienced Director
Our Partners
Psst… want to join this prestigious list?
Just send us a message and don’t miss our updates.
Contact Us
Any questions? Leave us a note and we’ll get back to you as soon as possible for a free consultation. ValCUN, Langerbruggestraat 33, 9041 Gent, Belgium
Not to brag… but we’ve received some honors & awards
Feel free to follow us.
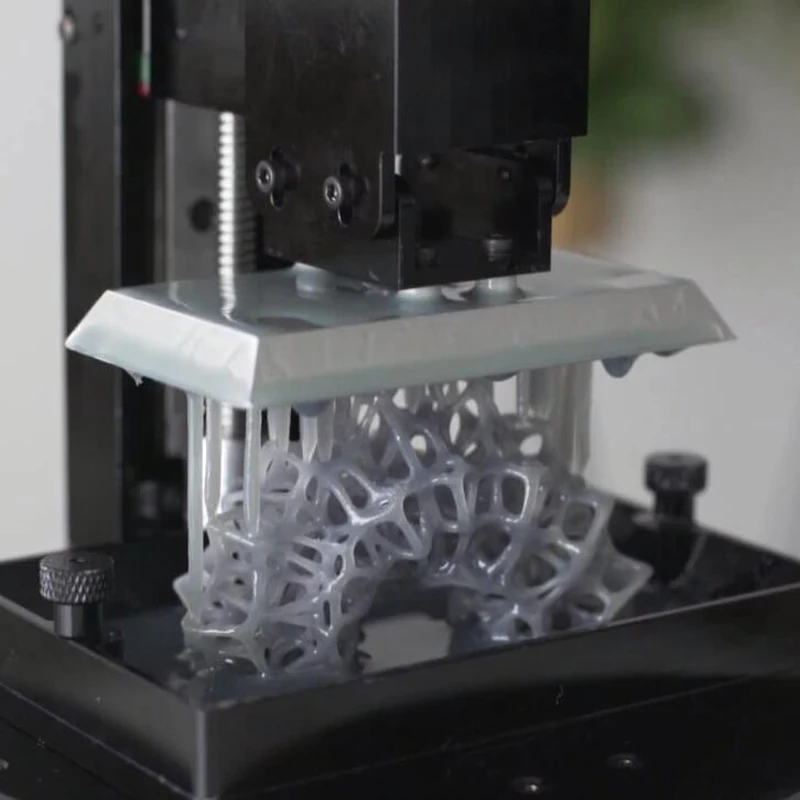
Follow us on LinkedIn
3D Printing Service Near You
33 3D Printing Services are currently ready to take your order and deliver custom parts to Antwerp, Flanders, Belgium. Through our platform, you can order 3D printed prototypes, replacement parts and many other custom projects without any minimal size or quantity requirements. If you have an idea of what technology, material or application suits your order, use filters to narrow down the search. You can also explore vendors’ portfolios with printed examples and customer ratings for a full perspective on their experience with different types of parts.
Upload files to compare instant quotes from local 3D printing services
Upload filesor contact us directly to get a volume discount.
If you’re looking to get something 3D printed and delivered to Antwerp, Flanders, Belgium, you’re in the right place. All companies that provide prototyping and printing near you are listed above.
How much does it cost to 3D print my parts?
To check out the pricing instantly, choose a vendor and hit the “Instant order” button. From a 3D model file such as STL, PLY, OBJ or 3MF we are able to calculate the price automatically. If you aren’t sure which vendor to choose, you can “Get instant quote” at the very bottom of the page with the list of all available 3D printing bureaus.
What if I don’t have a 3D file?
3D printing starts from a model, so it is necessary to have a file. Fortunately, many companies that provide additive manufacturing can help you design the parts. For more complex modeling tasks, consider hiring a professional 3D designer.
How do I choose a vendor?
Treatstock aims for transparent workflow between 3D printing companies and customers for great results. To make sure you have all the information needed to choose your manufacturing partner, we include a list of vendor’s machines and customer ratings for each service provider. The full list of their capabilities is included on their business page as well.
How does it work?
- Upload a 3D file to instant order;
- Select specifications and fill in the delivery details;
- Finalize the order process;
- Monitor progress in your Purchases;
- Get your custom parts delivered to your door.
Our support team is always available for assistance. To learn more about 3D printing technologies, visit our manufacturing guide. And the material guides will help you find out more about all available manufacturing mediums.
Printing locations
- Antwerp
- Brussels
- Charleroi
- Ghent
- Liège
Product Application
- Prototype
- HD Prototype
- Jewelry
- Dental
- Multi-color
- Metal
- Miniatures
Materials
- PLA
- ABS
- Nylon
- Wood PLA
- ASA
- Resin
- Rubber-like (TPU)
- PA12 Nylon
- PETG
Technology
- FDM (Fused Deposition Modeling)
- DMLS (Direct Metal Laser Sintering)
- SLS (Selective Laser Sintering)
- PolyJet and PolyJetMatrix
- SLA (Stereolithography)
- CJP (ColorJet Printing)
- DLP (Digital Light Processing)
- DUP (LCD-based Direct UV Printing)
Belgium is the birthplace of 3D printed elephants
News
Belgian company Materialize has completed a massive project to 3D print a full-size replica of a mammoth skeleton.
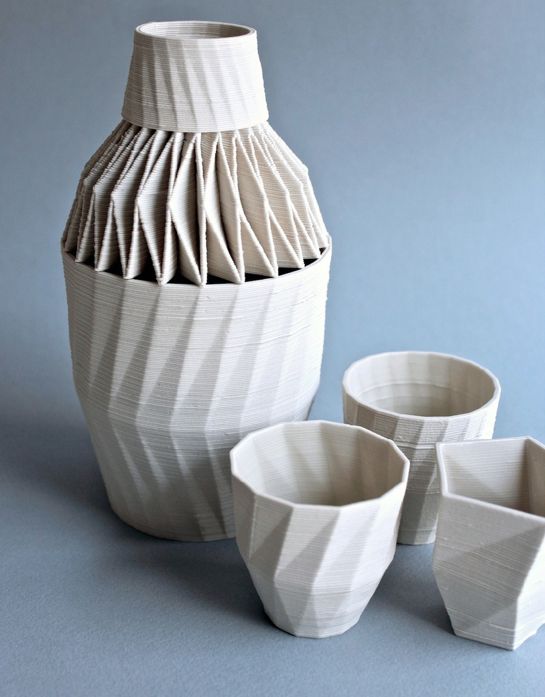
Back in 1860, Belgian workers, who were digging a bypass water canal, suddenly became paleontologists, having discovered the bones of a mysterious creature in the depths of the province of Antwerp. Mysterious in the sense that the huge horns of the skeleton turned out to be tusks. While the brigadier was toasting the elephants' new homeland, a military doctor named François-Joseph Skokhi, who was fond of archeology, came to the rescue and identified mammoth bones in the remains, which made the find even more valuable. The fact is that until then, scientists had only one well-preserved skeleton of an ancient giant, and it was in the zoological museum of distant St. Petersburg.
Nine years later, a more or less restored find ( in the illustration above ) was exhibited at the Belgian Royal Museum of Natural Sciences. Why more or less? The fact is that at that time there was still no clear idea of the anatomy of ancient animals, and therefore the missing bones were reproduced in the image of African elephants with the ensuing inaccuracies. In addition, the fragments had to be made by hand, mostly from wood, so the appearance of the exhibit left much to be desired.
Nakhodka was named “Lier's mammoth” in honor of the city in whose vicinity the excavations were carried out. Even after a century and a half, they decided to return the mammoth "to their homeland", but not the original skeleton. The original was left in the Brussels Museum, and an improved replica made using 3D printing technologies went to Lier. An order to reproduce a valuable exhibit was transferred to the Belgian 3D printing bureau Materialise. The project was handled by a team of nineteen people, including engineers, designers, printing technicians and post-processing specialists. The archaeologist, paleontologist and curator of the paleontological department of the Belgian Royal Museum of Natural Sciences, Professor Methieu Hermonpre commanded the parade.
The task turned out to be difficult, because the skeleton consists of more than three hundred bones, and some of them are more than one and a half meters long. On top of that, it only took a couple of months to complete. In order not to suffer with gluing, the team decided to use special stereolithographic 3D printers, developed by Materialize engineers specifically for the production of large-sized parts. Coincidentally, such additive installations are called by the same name as the ancient mammal. What did we do today? Printed mammoth. On Mammoth!
The first step was a 3D scan of the original skeleton. The resulting digital models were edited under the supervision of Professor Hermonpre to more accurately match the anatomy of the animal: the tail was slightly shortened, the missing left tusk was filled with a mirror image of the right one, the missing fragments of the upper jaw were added, and so on. In total, experts processed 320 bones, and then sent 3D models for printing.
Huge stereolithographic 3D printers and their operators have already had to work hard here. Mammoth 3D printers work on the well-known principle of curing photopolymer resins with laser emitters by amateur printers, but these machines inscribe layers with multiple lasers at the same time for increased productivity. It is understandable, because the size of the construction area reaches 2100x700x800 mm. The units exist in several versions, differing in size, have been in operation since 2001, and, according to the developers, still have no direct analogues.
The most difficult task turned out to be not even 3D printing of the bones, but the manufacture of a light, but at the same time strong and inconspicuous support structure that connects the bones into a skeleton. In other words, a skeleton for a skeleton. The integrated frame was made from carbon fiber links connected by 3D printed polyamide fasteners, and cavities were provided in the bones so that the frame could be inserted inside. It took fifty-two days and nine 3D printers to 3D print all the elements. The resulting bones were sanded, painted and varnished to mimic the textures of the original remains.
The replica is already on display at the Lier City Museum of Fine Arts, so if you pass by, stop by and take a look!
Do you have interesting news? Share your developments with us, and we will tell the whole world about them! We are waiting for your ideas at [email protected].
Subscribe author
Subscribe
Don't want
6
Doctors in Belgium use MCor 3D printer to significantly reduce surgery time
“We save an extra hour in every operation, which is a huge benefit for our patients,” says Prof. Rafael Olzheshki, surgeon and head of the University of Oral and Maxillofacial Surgery.
The challenge: reducing operating time
Time is a critical factor in operating on patients. The longer the operation takes, the higher the risk. When the patient can be quickly operated on and sent to recovery, the chances of a successful outcome are much greater.
This is what the staff of the University of Oral and Maxillofacial Surgery in Belgium are thinking about, who very often have to restore the bones of the face, for example, after cancer of the jaws or when the eye fossa is destroyed after an accident.
Strategy: 3D printed bone models
Surgeons have started using MCor's printer to save hours during operations. By working with the patient's 3D bone models on the computer, the doctor can simply press a button to use as a pre-surgery guide.
Because the model is an exact replica of the patient's real bone, clinicians can use it to create replicas of metal inserts to restore bone remnants. The insert can be a plate that supports the jaw or a titanium cell to restore the eye socket. Without a 3D model, doctors can only hope that the prepared insert will fit the patient exactly, and there will be no problems in the future.
Results: higher quality, saving money and time
“We save an extra hour in every operation, which is a huge benefit for our patients,” says Prof. Rafael Olzheshki, surgeon and head of the University of Oral and Maxillofacial Surgery. “We open up the patient, install a ready-made insert, check it, and after that the patient is immediately sent for recovery.”
Models of the jaws and bones of the face are produced on the Mcor Matrix 300+ printer. To get a 3D model on the computer, Olzheshki and his team do a CT scan of the required bone. They immediately turn the 3D model into a physical waterproof product using 3D printing.
Making a difference
A team of doctors ordered the MCor printer after five years of using the ZPrinter, which uses photoresin as the printing material. Printing models on this printer was too expensive, and toxic cyanoacrylic impurities were used to process the models. The use of these chemicals required obtaining a special license and a special room for processing models. Olzheshka's team found the use of these impurities incompatible with the work of doctors.
“We started looking for a more environmentally friendly solution and turned our attention to the MCor printer,” says Olzheshki. Mcor 3D printers are the only ones that can create models from regular A4 sheets. The sheets are cut and interlocked with each other, and the model is strong, accurate and stable. After using the model, it can simply be thrown away for further processing, just like regular paper.
MCor 3D printers use a special water-based adhesive, without the need for any additives, lasers, powder or toxic polymers, making it easy to install the model in an office or classroom. In addition, the cost of printing is the lowest compared to all other offers on the market.
Olzheshki estimates that a model made on an MCor printer costs three times less than a model made on a ZPrinter printer and 10 times cheaper than one made on an SLA printer. Since the models are made every day, the savings reach an average of 20,000 euros per year.