3D printer tiny house
These tiny homes are 3D printed from 100,000 recycled plastic bottles
These tiny homes are 3D printed from 100,000 recycled plastic bottlesHomepage
Co.Design
Tech
Work Life
News
Impact
Podcasts
Video
Innovation Festival 360
Subscribe
Help Center
fastco works
AWS
Deloitte
Dept
Elevate Prize
EY
IBM
Klarna
Visa
FastCo Works
An award-winning team of journalists, designers, and videographers who tell brand stories through Fast Company's distinctive lens
FC Executive Board
collections
Fast Government
The future of innovation and technology in government for the greater good
Most Innovative Companies
Fast Company's annual ranking of businesses that are making an outsize impact
Most Creative People
Leaders who are shaping the future of business in creative ways
World Changing Ideas
New workplaces, new food sources, new medicine--even an entirely new economic system
Innovation By Design
Celebrating the best ideas in business
Newsletter
Events
Innovation Festival
Courses and LearningAdvertiseCurrent Issue
SUBSCRIBE
Follow us:
By Adele Peters2 minute Read
Backyard cottages have been hailed as a way to quickly add new rental space in cities with a shortage of housing. But they’re typically expensive to build.
In L.A., where the city government has been trying to nudge homeowners to build more ADUs, or accessory dwelling units, the average construction price for a new cottage starts at $150,000 and goes up to around $350,000, not including building plans, engineering work, and other expenses.
A startup called Azure Printed Homes is taking a different approach: By 3D-printing the roof, floor, and walls with recycled plastic, and building the rest of the home inside a factory, it keeps costs lower. A simple backyard studio apartment, with a tiny kitchen and a bathroom, starts at $39,900. The foundation, delivery, utility hookups, and other costs add about 25% to 30% to the total, but it’s still far less expensive than most alternatives.
In its factory in Culver City, near LAX Airport, the company is getting ready to print its first homes. The 3D printer can print the shell of the house—the floor, roof, and two walls—in a single day. In the walls, the printer includes channels for plumbing and wiring. The two other walls aren’t 3D printed, but pre-engineered panels with doors and windows.
“Day one is the print itself that creates that module shell,” says Ross Maguire, cofounder of Azure Printed Homes. “Then, by day two, we’re already wiring and plumbing inside that shell.” The robot squeezes out lines of plastic, a little like toothpaste from a tube, to form the structure. Other companies, including the nonprofit New Story and the startup Icon, have pioneered 3D-printed homes with concrete.
Azure wanted to use a lightweight material so homes can be built in its factory and then delivered to the site. Both 3D printing and prefab construction in a factory can speed up construction time and reduce labor, ultimately reducing costs. Azure also wanted to make use of a waste material and “repurpose a waste product that is kind of causing a headache globally,” Maguire says. A 180-square-foot ADU can use the equivalent of around 100,000 recycled water bottles. The company is working with various suppliers, and says there is no shortage, at least for now, of recycled plastic to use.
In one of its first projects, the company is working with a developer to build a small group of cottages that can be used for short-term rentals, and it will be working through a waiting list of backyard cottage for homeowners. But it’s also in talks with groups that want to build tiny homes for people experiencing homelessness. The company can build larger single-family homes, and smaller modules could be stacked together to build multifamily housing. “You’re restricted by what you can ship, but there’s obviously no end to how many modules you can connect together to create different designs,” says Maguire.
Tech
TechFitbit integrates new technology linking people in recovery to caregivers
TechDelta Air Lines and Joby Aviation want to fly you to the airport before your flight
TechThe future of the metaverse hinges on interoperability
News
NewsMore than a dozen states recognize Indigenous Peoples’ Day. Should New York be next?
NewsGlassdoor is making it easier for employees to find a job that lines up with their values
NewsBlack Friday and Cyber Monday are coming: These are the hottest gifts for 2022
Co.
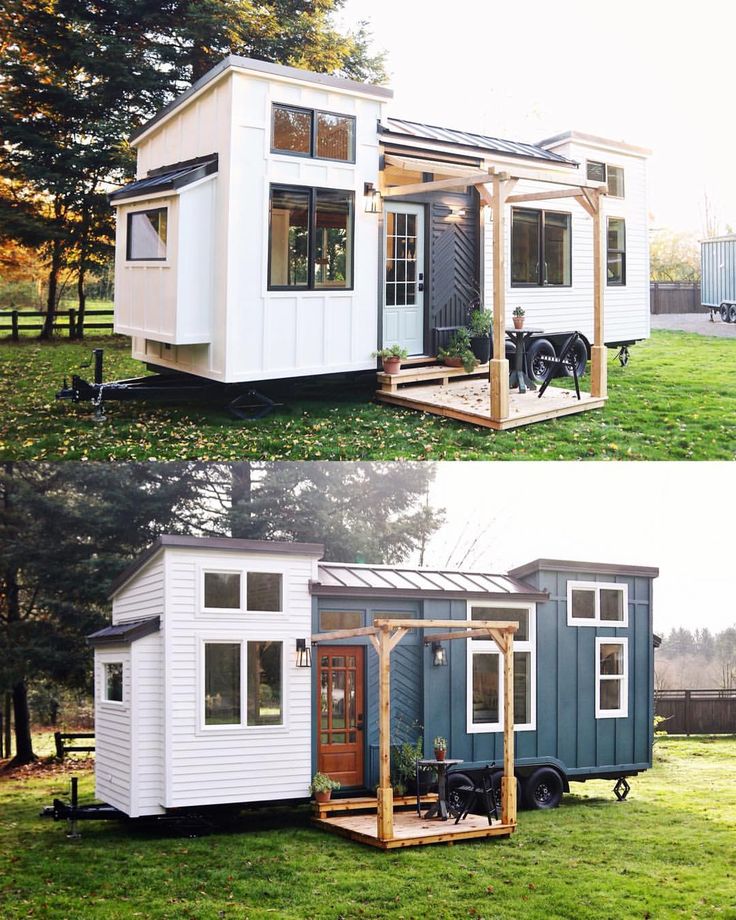
Pop culture itself is plunging into bizarro alternate realities
Co.DesignHow to make a design prototype
Co.DesignFortune 500 companies are are wasting millions on unused office space
Work Life
Work LifeDo these 5 things to land your next internship
Work LifeDiscomfort is a feature, not a flaw, of returning to the workplace
Work LifeHow workplace discrimination has changed over the last generation
LA Startup Is Using Recycled Plastic to 3D Print Prefab Homes
Photos: LA Startup Is Using Recycled Plastic to 3D Print Prefab Homes Search iconA magnifying glass. It indicates, "Click to perform a search". Insider logoThe word "Insider".US Markets Loading... H M S In the news
Chevron iconIt indicates an expandable section or menu, or sometimes previous / next navigation options.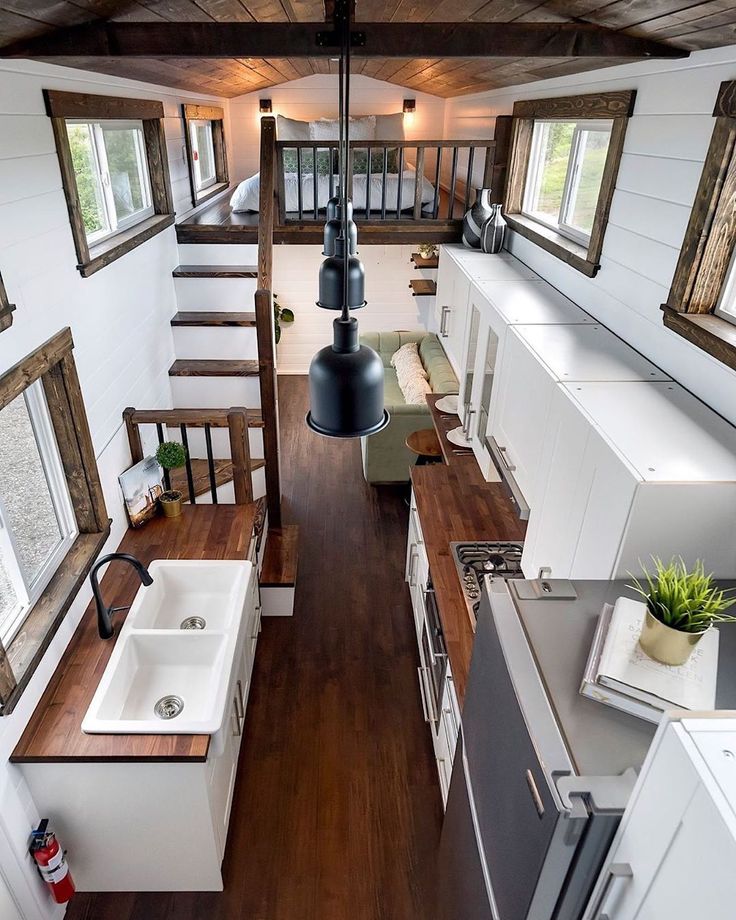
Download the app
Azure Printed Homes- Los Angeles-based startup Azure is using recycled plastic to 3D print prefab homes.
- The startup is now selling several models ranging from a backyard studio to a two-bedroom ADU.
- Azure says it can build homes 70% faster and 30% cheaper than "traditional home construction methods."
Why "reduce, reuse, recycle" when you can just turn your plastic waste into homes?
A worker stands in front of a pile of plastic waste as machinery processes it at a facility in Japan.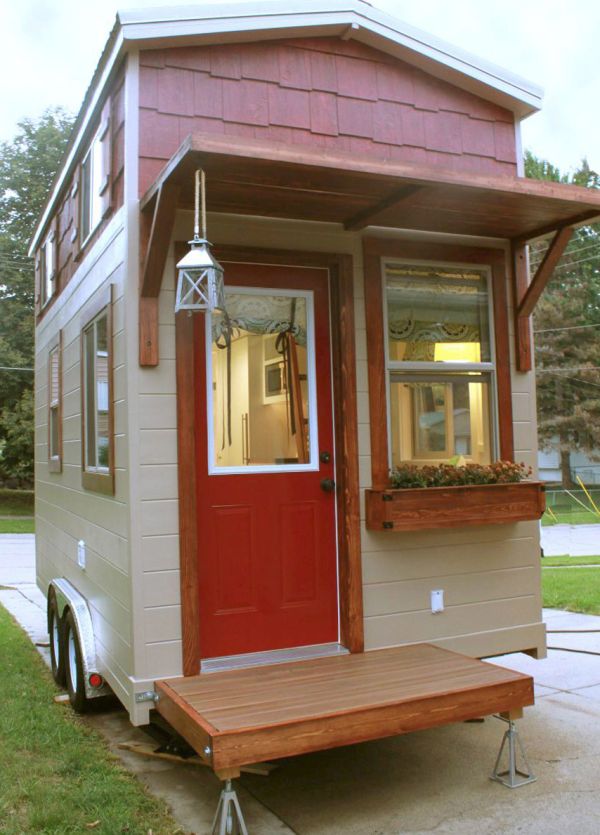
This may sound like a far-fetched idea, but that's exactly what one 3D printing home construction startup in Los Angeles is trying to do.
Azure Printed HomesIn April, Azure unveiled what it called the world's first 3D printed "backyard studio" made with recycled plastic materials.

Source: Azure
And its plastic-printed studios and accessory dwelling units (ADUs) are now available for preorder as the startup prepares to ramp up its production line in the Culver City neighborhood of Los Angeles.
Azure Printed HomesMost 3D printing home builders currently use a form of concrete to create their homes, whether it be a proprietary mix or pure concrete.
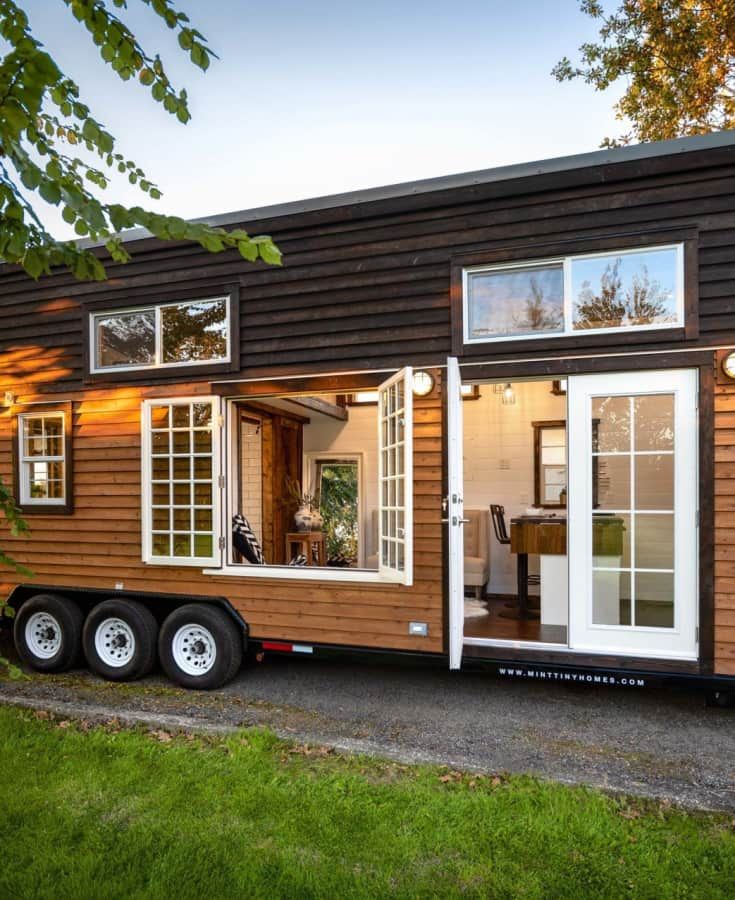
Source: Insider, Insider
But Azure is saying goodbye to this drab grey look by taking a more sustainable approach …
Azure Printed Homes… giving a second life to plastic once destined for landfills or incineration.
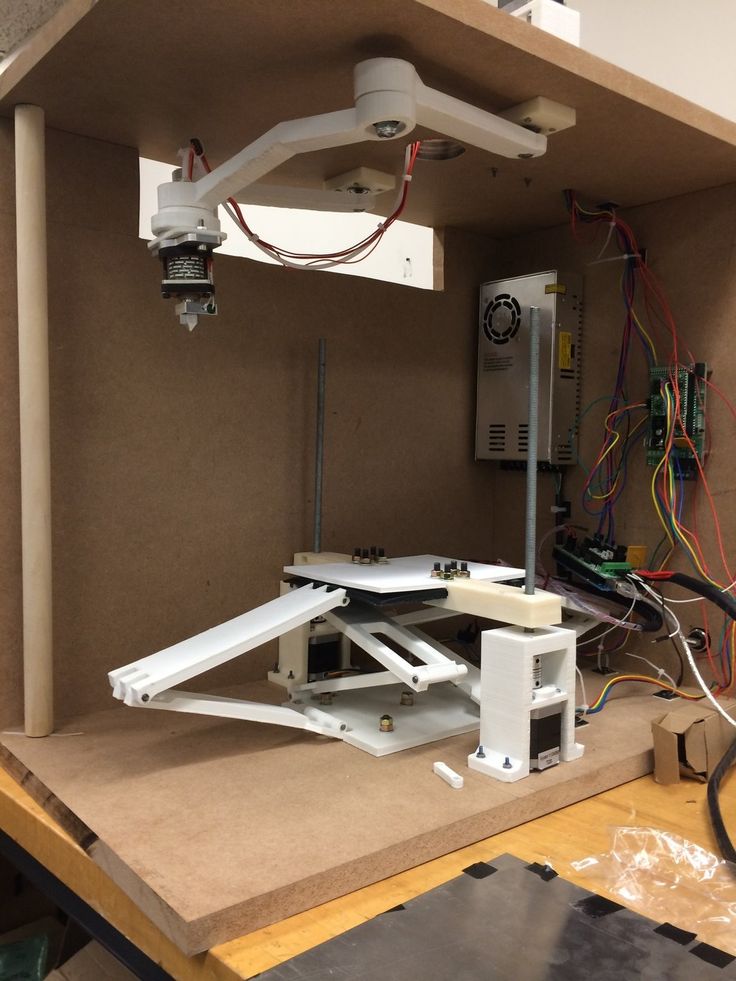
Over 60% of Azure's printing material will use the inherently waterproof plastic polymer often found in plastic bottles and packaging for food, according to the startup.
Azure Printed HomesSource: Azure
It's currently working with three suppliers to source "post-industrial plastic" for its printing mix, Ross Maguire, who cofounded Azure to make construction more efficient and sustainable, told Insider.
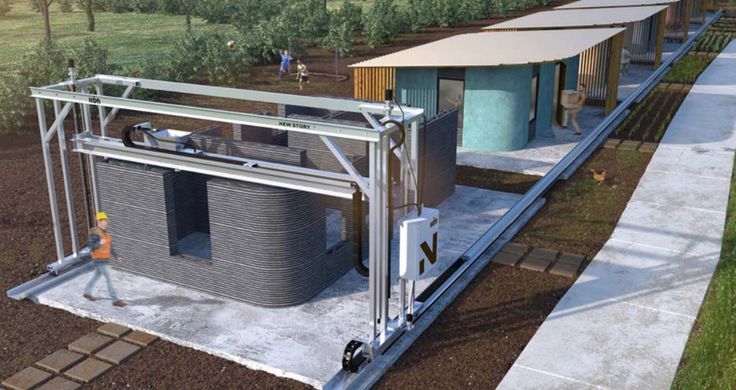
But in the future, the goal is to use post-consumer plastic: "Our supply chain should never be short in our lifetime," he said.
A volunteer with Dominion Tabernacle Ministries prepares cold water bottles to hand out in Dallas, Texas on June 12, 2022. Shelby Tauber/ReutersEven without the use of recycled plastic, the nascent 3D printing homebuilding industry has already been heralded as a more sustainable and efficient construction method.
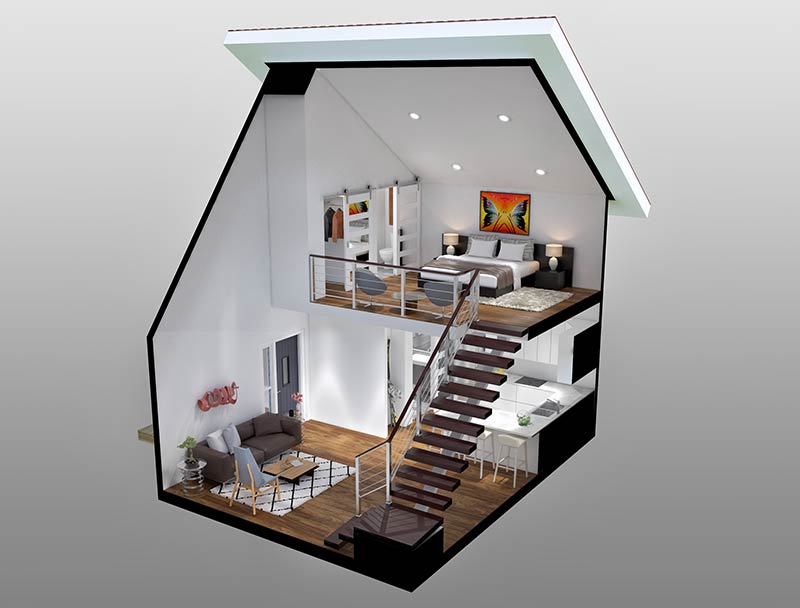
According to its biggest proponents, by using printers instead of people, homes can be built more efficiently using less waste, materials, and time.
Mense-KorteSource: Insider
And Azure will be no different: The startup says it can build homes 70% faster and 30% cheaper than "traditional home construction methods" by 3D printing the floor, roof, and walls of its models inside its factory.
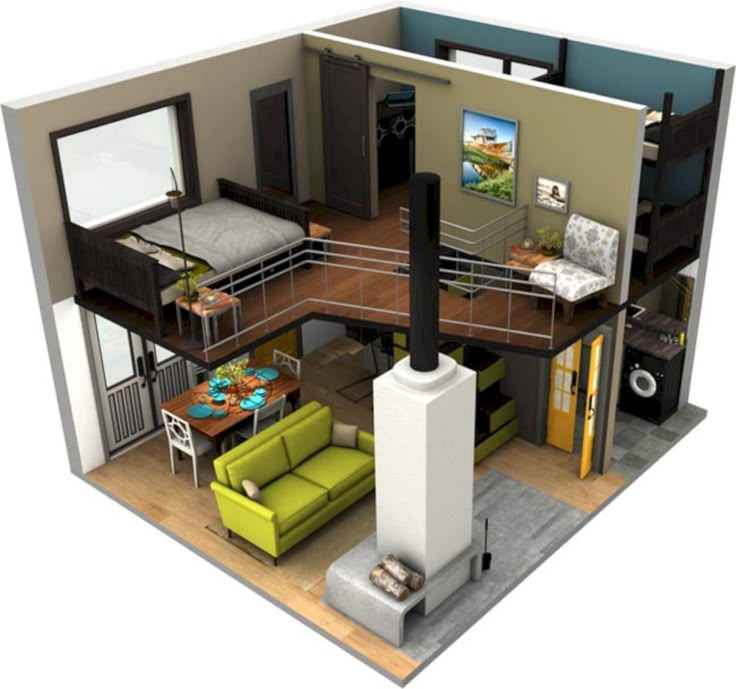
Source: Azure
And with the help of prefabrication, before a unit leaves Azure's 10,000-square-foot factory in Los Angeles, 99% of its finishes will be complete, Maguire said.
Azure Printed HomesSo when it arrives on site via a flatbed truck, the only necessary on-site work will be to connect the home to its foundation and utilities.

Azure currently has several customizable models ranging from small studios to 900-square-foot two-bedroom ADUs.
Azure Printed HomesAnd these builds are now available for pre-order to be delivered as soon as early November.
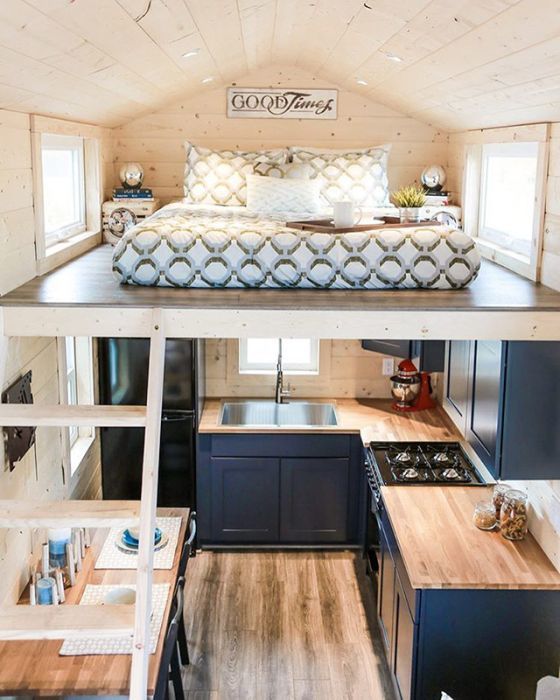
But no matter the model or size, these units will all be prefabricated and built using connectable modules that can each be printed in under 24 hours.
Azure Printed HomesThe floor and ceiling are connected by a flowing wall with curved corners, a trademark of 3D printers.
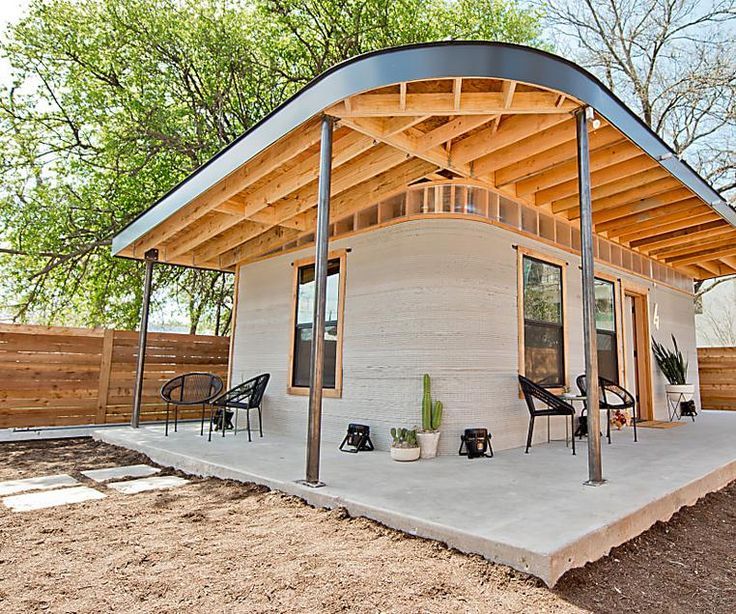
Given its smaller size, these studios can be printed within day one, wired by day two, insulated by day three, and then delivered on-site in two weeks, Maguire told Insider.
Azure Printed HomesBut if you're looking for something more substantial, Azure also prints ADUs, which skyrocketed in popularity in 2020.
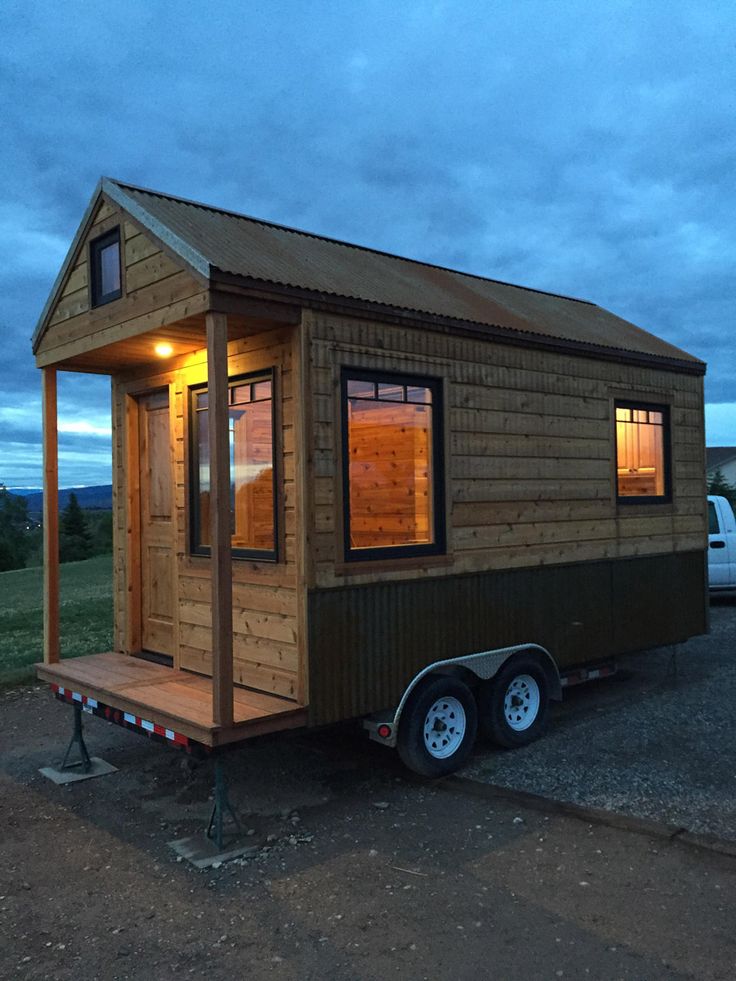
ADUs extend the square footage of the main home by serving as a backyard guest home or Airbnb.
Azure Printed HomesAnd Azure's comes in multiple sizes: a studio, one-bedroom, or two-bedroom.
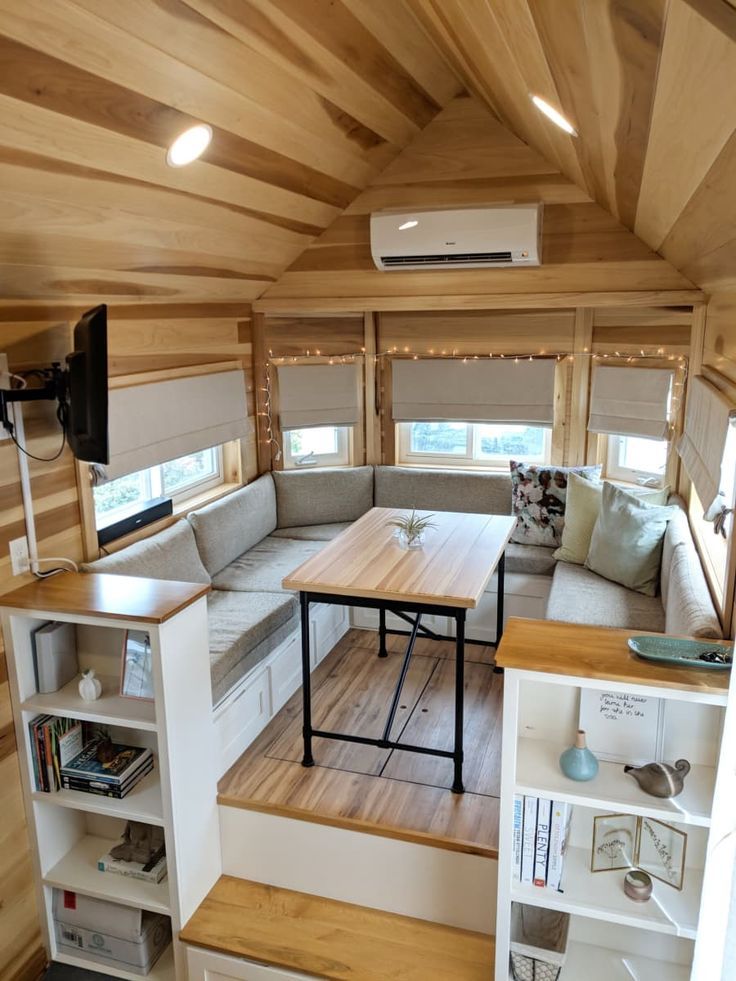
These units range from 180 square feet to 900 square feet…
Azure Printed Homes… although the smallest $39,900 option already has a three-month waitlist, according to local news reports.
Source: Spectrum News 1
Inside, there are spaces like a bedroom, living room, bathroom, and even a laundry room in the larger builds.
Azure Printed HomesThe smaller ADU has a more traditional appearance with a pointed roof (shown below), while the size up features the same futuristic aesthetic as the backyard studio.
When the startup debuted the former look, it saw a "big rush of preorders," Maguire told Insider.
Azure Printed HomesAnd moving forward, he believes the company will sell more of this traditional-passing ADU.
Azure has only printed one model so far, although it does have another in the works.
Azure Printed HomesBut next month, the startup will receive the last bits of equipment it needs to begin rolling out the production line .
... which should help address its "big backlog of orders" that has already been overloading its one printer, Maguire said.
Azure Printed HomesAnd in 2024, the startup will begin rolling out larger homes.
Further down the line, Azure may also explore printing housing for the unhoused or for overseas clients …
Azure Printed Homes… and in the future, if the company decides to expand, you could find a pop-up-like Azure production line near you.
"3D printing is a more efficient way of building and it should only get better as we develop the processes, technology, and materials further," Maguire said. "I can only see it becoming more and more prominent in [construction] as we move forward."
Azure Printed HomesRead next
LoadingSomething is loading.Thanks for signing up!
Access your favorite topics in a personalized feed while you're on the go.
FeaturesMini house built in 2 weeks using a 3D printer and a car robot
A unique tiny house has appeared in upstate New York. To bring this innovative marvel to the world, Cornell University faculty and students have not only developed a 3D printer, but also upgraded a robotic arm previously used to assemble cars for General Motors. Using gravel, clay, cement and damaged ash wood that goes to scrap, they managed to "print" a rather original mini-house that meets all the criteria for "sustainable" architecture.
Using a 3D printer and a car robot, American architects created a house from wood waste (Ashen Cabin, Ithaca). | Photo: newatlas.com/ inhabitat.com.
Located in Ithaca, New York, USA, Ashen Cabin is an innovative tiny home that stands out for its looks and interesting shape. Thanks to the ash façade, it blends in perfectly with the forest landscape, even though the bizarre wood paneling and thick triangular concrete columns give it a futuristic, spaceship-like appearance. Explicit, one might even say, deliberately emphasized highlighting of ash wood was chosen for a reason.
This fantastically shaped 3D printed house is located near the Cornell University campus (Ashen Cabin, Ithaca). | Photo: dezeen.com.
An interesting fact from the Novate.ru editors: Ash emerald narrow-bodied borer (Agrilus planipennis), penetrating into the bark of ash trees, lays larvae that ruthlessly damage the wood. The tunnels they form make the wood unsuitable for use in construction. Instead of sending 8.7 billion trees for sawing, they have to be burned whole or left to decompose. Scientists are sounding the alarm, claiming that at the moment one in 10 ash trees in New York State are not suitable for use as lumber. A similar problem is familiar in Russia.
Leslie Lok and Sasa Zivkovic, together with their students, developed a special 3D printer and reprogrammed the robot arm. | Photo: archpaper.com.
New York-based architecture firm Hannah has been developing ways to use wood damaged by the emerald ash borer for years. With this problem, they turned to assistant professors of architecture Leslie Locke and Sasha Zivkovic, who teach at Cornell University in New York.
A repurposed robotic arm helped cut damaged ash wood. | Photo: dezeen.com.
Scientists and their students have been developing especially economical 3D printers and creating special forms of foundations for more than one year. They themselves say this about their developments: “A team of students and I created a printer from scratch at RCL in 2016 and have since improved it several times. We also developed a special 3D printing technique and our own concrete mix, which includes only gravel, cement and sand, which can be purchased anywhere. It is this special composition that allows you to create “cantilever legs” instead of a foundation.”
Thanks to the robotic arm, even the most curved branches and trunks of ash trees were sawn. | Photo: inhabitat.com.
But university scientists are also concerned about the disposal of damaged wood unsuitable for further use. As a rule, such specimens are burned or simply left in the forest to rot, spreading the pest population and releasing carbon dioxide. These two options have a very negative impact on the environment, so everyone is trying to find a way out.
Despite the small area, the house turned out to be quite cozy (Ashen Cabin, Ithaca). | Photo: dezeen.com.
To prepare unusable wood for use, the firm and a team at the university upgraded a robotic arm bought on eBay that had previously been used to assemble cars for General Motors. They reprogrammed the robot and built a platform to prepare and saw through unusable ash trees. After reprogramming, the arm-manipulator thinly cut the wood of the required size and shape. When creating walls, these thin curved boards could be put together like puzzles.
All concrete elements of the house were created from special concrete in the workshop, and these segments were assembled at the edge (Ashen Cabin, Ithaca). | Photo: archpaper.com.
In parallel with the process of filigree sawing, the structural foundation of the house was created, including not only a platform on cantilever legs, but also a chimney, a cabinet with a sink, a kind of armchair and several chairs for the barbecue area. For these purposes, the same 3D printer was used, which squeezed out a special cement mixture from the nozzle in layers, creating nine interconnected concrete segments. This process took about two weeks to ensure that the use of concrete, which is detrimental to the environment, is minimal.
The timber frame was assembled by architecture students at Cornell University (Ashen Cabin, Ithaca). | Photo: inhabitat.com.
After the mortar hardened, the students assembled the wooden parts of this simple hut in the forest in a matter of days. Considering that this is an experimental object, Ashen Cabin was made quite tiny at 3 x 3 m, and its interior is very simple. It turned out to be just one room, which has a real fireplace, a cabinet with a sink that acts as a mini-table, several shelves for cutlery and two platforms. One can be used as a single bed, and the other will fit instead of a chair.
Live fire and a cup of hot tea will make your stay at the edge of the forest more intimate (Ashen Cabin, Ithaca). | Photo: dezeen.com.
Hannah and the faculty at the university hope that the project has a future and will be used to build sustainable housing on a larger scale. In the meantime, this Ashen Cabin will delight those who, walking through the forest, will see it in a clearing and can even take a break.
Given today's realities, the construction industry keeps pace with the times, developing innovative projects that make it possible to create houses with a "sustainable" architecture. And the following 6 examples will prove that housing construction can also be ultra-modern.
Source
Printing a house on a 3d printer: How to print a house on a 3d printer
Is it possible that in a progressive version of the future for a new house, we will all go not to builders, but to a 3D printer?
3D printing is one of the most talked about technologies of the last decade. Some see it as the beginning of the third industrial revolution, others are more inclined to see the flaws. So how realistic is 3D printing houses? In this article, we will talk about the level of development of 3D printing in different countries and look at the fragile pavilions made of composite material in China; concrete pillars in Italy, inspired by classical architecture, and "thinking" houses in Germany.
Eva Zimmermann
Archived: This is one of the articles in our "most popular" section
What is 3 D -print? 3D printing technology was invented by American engineer Chuck Hull. He patented the process in 1986 and first called it stereolithography. The method involved joining molecules with a laser to transform polymers into solid forms.
The first use of 3D printing was found in the automotive industry - with its help they began to make so-called "rapid prototypes". The main advantage of the technology was that from now on it was not necessary to cast molds, which significantly reduced design costs. In addition, compared to sawing a prototype out of wood, there is significantly less waste, because before all the remaining material had to be disposed of. In a 3D printer, objects are printed in layers, somewhat repeating the idea of inkjet printing on paper. Only the process is repeated many times, and instead of ink, a harder material is taken. With a slight shift between the layers, a volume appears, or, as they say now, a 3D effect.
Materials used in 3D printing range from synthetic resins and plastics (most commonly) to steel and concrete. Today, compact models of 3D printers are increasingly appearing in design studios, schools, and even in private homes.
Eva Zimmermann
Large-scale application 3 D printing in China
China is a country where superlatives are considered a sign of progress in all areas of life. Therefore, it is not surprising that the largest architectural object created using a 3D printer appeared in this country. The Volcano Pavilion (pictured) opened to the public in 2015 during Beijing Design Week 2015. The architects of the project were Xu Feng and Yu Lei. Of course, the 8.08 m long and 2.88 m high pavilion was not printed in one go. In fact, it was assembled from 1023 individual parts, each of which was printed on a 3D printer.
Although this achievement was awarded the Guinness Book of Records, it also showed that the scope of 3D printing is still quite limited. To create an entire house on a 3D printer, the printer must be gigantic, or at least be able to drive along specially constructed scaffolding. Scale is the reason why 3D printing is still in its infancy when it comes to architecture.
Eva Zimmermann
How to print a whole house
In Amsterdam, however, DUS Architects is currently printing layer by layer a house called the Canal House. Completion of the project is scheduled for 2017.
“China is also printing entire houses,” says Dr. Jane Barry, associate professor at the Spatial Information Architecture Laboratory at the Royal Melbourne University of Technology. “Although at this stage they still look raw. ” She is referring to a project by Winsun, which has already printed several concrete houses in China. This project is the most commonly cited example when it comes to 3D printing in construction. Representatives of the company declare significant savings. So, compared to traditional construction, the printing of a new house requires 60% less materials, 70% less time and 80% less labor costs. The printer itself at the same time has gigantic dimensions - 150x10x6.6 m!
Eva Zimmermann
Or shut down the building process
“It's all about what you mean by 3D printing,” says Benedikt Gotze, public relations specialist for the Association of German Architects (Bund Deutscher Architekten). His expert opinion on 3D printing in architecture is far from universal euphoria: “The idea of printing entire houses is a childish fantasy, this will never happen. But what will really happen is the digital control of the production of building parts in factories, from where they will, as before, be delivered to construction sites. Chinese 3D houses, which are so often cited as an example, seem to me an unnecessary measure in the struggle for everyone's attention.
Professor Jane Barry from Melbourne Tech says: “The main advantage of 3D printing is not mass production, but the ability to create individual designs and a variety of options. At our university, we pay special attention to printing from metals, for example, in the production of key elements of building structures to individual measurements. If you reduce the amount of material in the finished product, then its weight and the overall load on the foundation will decrease accordingly, not to mention saving the energy expended. In this area, 3D printing is a real find, because the production of key elements of the house structure in another way, such as casting, can be very expensive, and with the new technology, for much less cost, you can even print a few spare parts in case of repairs.
Benedikt Gotze questions the practicality of the very idea of 3D printing houses: “All this enthusiasm reminds me of manned space flights – doable, but is it necessary? Omega is still building advertisements for Speedmaster watches based on the fact that they went to the moon. ”
But the British architectural firm Foster & Partners and the European Space Research Agency can argue with Gotze about flights to the moon. Together they are exploring ideas for applying 3D printing to a lunar base as part of the Lunar Habitation project, which is expected to be completed by 2024.
Eva Zimmermann
Back to Earth
While Foster & Partners' lunar base is arguably the most ambitious program in existence, there are projects on Earth that deserve your attention. One of them is the bridge in Amsterdam, which was the result of a collaboration between designer Joris Laarman, MX3D, which makes 3D printers that print steel objects, and CAD software developer Autodesk.
Looking at this photo, it may look like the new steel bridge is being built right on the spot, over the Oudezijds Achterburgwal canal, but it is actually made in a workshop. Work began in the fall of 2015 in a huge space rented by MX3D. Through trial and error, employees try to print the entire structure. Completion is scheduled for 2017, which means that in just a year we will see the first real steel bridge, fully 3D printed and open to the public - another race for a world record.
Eva Zimmermann
This little detail shows how the bridge will look after the 3D printing process is complete. Two undoubted advantages of steel printing are that, compared to casting, the contours are more organic and fluid, and the absence of the need to make injection molds significantly reduces the cost of production.
WASProject
Fine concrete printing in Italy
The collaboration between the University of Naples and WASP, a modern technology company, combines the beauty of Italian architecture with modular construction techniques.
WASP was founded in 2012 by Italian entrepreneur Massimo Moretti. Its main activity is to promote energy-efficient building methods and support the production of building modules on site. Together with the University of Naples, its specialists have developed concrete supports that can be 3D printed and used in a wide variety of construction projects.
Domenico Asprone (pictured), assistant professor of structural design at the University of Naples, took part in this project as a structural engineer: “The idea was to print a curved concrete support, optimizing the amount of concrete used and reducing the cost of producing a complex formwork. The approach is based on dividing the support into several concrete segments, which are printed separately and then assembled into a single monolithic element, along with steel reinforcement, according to the Lego principle. This method is designed to facilitate the production of complex parts with a wide variety of profiles, which in turn will lead to greater creative freedom for design engineers,” he says.
WASProject
“The segments are printed individually. As soon as the concrete hardens a little, reinforcing bars are inserted into them, reinforcing the beam and combining several segments into a whole support,” says Domenico.
Simultaneously with the already established production, WASP specialists are developing a technology for one-time printing of reinforced poles with a length of 3.2 m. To this end, they use concrete with a lower viscosity index. “We have more than a century of history in the production of concrete products. We just adapted existing technologies for 3D printing,” says Domenico. “Today, we use cement and other binders, such as environmentally friendly clay-based compounds (geopolymers), to create waterproof products that are suitable for building gutters.”
What are the future plans of WASP? In the near future, they are going to print a footbridge similar to Joris Laarman's design in Holland, but not from steel, but from concrete.
CJSC SPETSAVIA 3D printing of buildings
Decorative parts from Russia
Like the Italian company WASP, the Russian manufacturer Spetsavia uses 3D printers to print concrete products.
Construction contractors are among the main clients of this company. CEO Alexander Maslov talks about the products that can be printed on his printers: “Printers of the 06044 series can print individual structural elements up to 12.3 m long. This is more than enough to print products of complex shape for the construction and design of all kinds of towers, arches, partitions and other decorative elements of buildings. Already today we have experience in printing such elements of landscape design as a small swimming pool and a children's playground. Also, the printer can be used to print fireplaces, stoves, barbecues and other refractory products from kaolin mixtures.
CJSC SPETSAVIA 3D printing of buildings
According to Alexander, from a technical point of view, it would be possible to print the whole house, but still he treats this idea pragmatically: “As far as I understand, we are talking about printing individual elements and their subsequent assembly at the construction site. The advantage of this method is that you can move the production of parts indoors and thereby reduce the effects of temperature, humidity, and so on. And the disadvantages are in the cost of transportation and extended construction time. Plus, the assembly of individual elements is a technologically complex process that requires additional solutions to strengthen the structure.”
Despite the fact that Alexander considers himself a pragmatist and prefers not to look too far ahead, he still admits that new building technologies, like the one offered by his company, will become an integral part of any construction project in a few years.
A bold vision for the future from Germany
Professor Akim Menges is the head of the renowned Institute for Computational Design at the University of Stuttgart. The real possibilities of the new technology are already being applied here in full and are the subject of study in his research projects. He knows better than anyone that innovation is an invitation to leave behind all old ideas. “First, you use the latest invention to build traditional objects, as they did in China, where familiar-looking houses are built using 3D printers,” says Akim Menges. “But at the second stage of development, structures appear that can only be created through new technology.”
This means, for example, that "3D printing will make it possible to use complex geometries in construction without increasing cost or labor." “Awareness of this fact will set a new direction in design,” explains the professor. The advent of 3D modeling software has already changed the aesthetics of architecture, and 3D printing is the next step in that direction.
In addition, the printed elements may physically have heterogeneous layers. “We have the ability to create very complex parts with gradient characteristics,” says Professor Menges. “That is, the finished object can be soft on one side and hard on the other, due to the fact that different materials are loaded into the multifunctional printer right during the printing process. ”
Eva Zimmermann
Buildings that can think
Prof. Menges is currently developing building parts that can change shape, just like in nature. “Just imagine a pinecone. When it grows on a tree, its scales are closed, but when it falls to the ground and dries, they open like petals, he says. “With 3D printing, we can simulate this effect by using different materials, soft and hard, that respond differently to atmospheric changes, such as humidity. In this way, we can create building parts that will adapt to climatic conditions without the need for forced control using manual or electronic mechanisms.” The photo shows a prototype of one of these parts.
Many people go one step further. “Today there is a lot of talk about Industry 4.0, in other words, the fourth industrial revolution,” says Professor Menges. “It involves the mutual penetration of the material and digital world through the so-called cyber-physical systems. ” In such systems, software is connected to mechanical and electronic components through a data infrastructure, such as the Internet (adherents of this idea love the phrase “Internet of things”). This kind of building technology could completely change the way we live, the whole everyday world we know.
Eva Zimmermann
Conclusion: 3D - euphoria or a sober look at the future?
Admirers of new technology are literally pushing us to the threshold of a new era. If scientists start sharing their designs and the technology is available to everyone, 3D printing can really change the world. The production of necessary items can move into kitchens and living rooms, and then we will pollute the environment less, since the need to transport and deliver goods will decrease many times over.
But if we talk about architecture, here size continues to be a serious obstacle to the further development of technology. In addition, the list of building materials that can be refilled into 3D printers is still very limited.
Dr. Jane Barry also talks about the serious competition of technologies in the construction industry: “I expect that in the next ten years 3D printing will develop in parallel with other technologies, but I would not invest my own money in it, but in wood construction,” this is the most obvious trend.” In her opinion, laminated wood with a longitudinal-transverse arrangement of layers is like “plywood on steroids”. Such a material is somewhat reminiscent of concrete in the sense that it is possible to build a whole house from it, without an internal frame. This means that houses can potentially be built faster and cheaper. “I'm not saying these technologies can't coexist,” she adds. “At the end of the day, a 3D printer can also be filled with wood-based material.”
We still have a lot to learn and experience. We may not be printing houses on the Moon in the near future, but 3D printing will definitely make it possible to build houses with more complex geometries.