3D printer sharing
Remote 3d printing - Software for remote 3d printing
FlexiHub Team uses cookies to personalize your experience on our website. By continuing to use this site, you agree to our cookie policy. Click here to learn more.
There’s no doubt that with their endless possibilities, 3D printers will change the way we manufacture things today. The technology of 3D printing has a potential to replace traditional factory production lines with a single machine. Moreover, a big number of modern additive machines are designed with a mainstream user in mind.
Considering all the hype attached to 3D printing, the problem of remote access and management of these devices is becoming crucial for both casual users and businesses.
Typically, high end printing machines come with a built-in remote access technology, which allows printing something big and especially beautiful remotely. However, such equipment not only takes up a large chunk of desk space but costs a small fortune.
But what if there’s another way to share 3D printer through network? Well, the solution is simpler than one can imagine. A dedicated software like FlexiHub or USB Network Gate will help you expand the feature-set of more affordable machines and resolve the problem of remote access to 3D printers.
OpenSource remote 3D printing solution
OctoPrint is an open-source software solution that enables 3D printers to be controlled remotely. We think it is one of the best applications for remotely controlling 3D printers. You will need to connect a Raspberry Pi to your printer to use the software, but it is well worth the effort for the functionality the app provides.
OctoPrint’s features include the ability to start, stop, or pause a print job remotely and manage the position of the print head. There is also an embedded webcam feed for monitoring print bed temperatures. Using this software adds versatility to your 3D printer by making it accessible from any location.
3d Printer Remote Сontrol
30-day demo period
Remote 3D printer access with USB Network Gate
USB Network Gate is a great alternative for sharing USB devices across the network. If you have no Internet connection and need to share your 3D printer over LAN, this software will be good for you. The ability to share multiple devices with multiple network users at a time as well as the support for USB devices of virtually any type is what sets USB Network Gate apart from much of other USB sharing software.
Why choose USB Network Gate?
- Compatibility with virtualization software. USB Network Gate will easily redirect your 3D printer to VMware, VMware ESX, Citrix XenDesktop, or Microsoft Hyper-V guest OS.
- Working in RDP sessions. The software allows you to not only work with any local 3D printer in a remote session but also set your remote computer to automatically detect and connect to shared USB devices.
- USB device isolation in multi-user environment. With USB Network Gate you’ll be able to assign your 3D printer to a specific user while working in a multi-user environment of terminal servers.
How to use software for remote 3D printing:
- Download USB Network Gate and install it on both the device server (a computer with the 3D printer connected) and the client machine that will access the equipment remotely.
- On the server computer, launch the software, find the printer in the list of available devices, and hit "Share".
- On the client side, find the 3D printer in the “Remote USB devices” window and click "Connect" next to it.
This is it! Starting from this moment, you’ll be able to access the full functionality of the remote USB printer without having it physically attached to your PC.
3D Hubs – Building a Global 3D Printing Network
By HA
Student
Modified Nov 13, 2018
Next:
Tesla: How Machines Are Now Driving Our Cars
3D Hubs is the world’s largest network of manufacturing services – www.3dhubs.com
In essence, the company being discussed (3D Hubs) created a network of 3D printer owners, allowing them to generate revenues using their privately-owned devices through a Peer-to-Peer (P2P) network. With 10,000 different 3D printers available in more than 80 countries, 3D Hubs connects people who want to use the technology to 3D print parts, but buying a 3D printer does not make financial sense for them, to communities who have 3D printers and excess capacity to print for them their parts for a fee. After parts are made, they are shipped using the company’s logistics infrastructure to the respective party.
For communities who are significantly involved, 3D Hubs rewards them with platforms to meet with like-minded individuals to share thoughts, collide ideas, showcase printers, discuss new trends in the industry and meet with current and potential clients. As patents continue to break, many startups are going to make noise in the industry. Iterating on the existing technology and building cheaper 3D printers. This will give the ability for freelancers and hardware hackers to redo a prototype, no matter where they are in the world and have a product within hours. This allows creators to continuously work while they travel and promote their products.
The concept of a “shared economy” is a fairly recent idea. Ride-sharing services like Uber/ Lyft are disrupting the Taxi industry. Airbnb enables people with an empty home, or even a spare room, an opportunity to make extra money. This concept is optimizing the efficiency of the resources. Why not apply it to 3D printers too?
3D Hubs took advantage of the “90% downtime” – the theory that people who own 3D printers only use them 10% of the time. It transformed the desktop 3D printer to be an investment, providing access to people who want to print, developing it into a community building, resource sharing, and overall evangelization of 3D printing.
To start, the 3D Hubs team consisted of only 35 employees. Since initially, they wanted to keep overheads low, while testing the viability of the platform, the website functionality was quite limited and had little more than a simple landing page. Google sheets was used to monitor transactions. Transactions are processed by hand, while delivery was done initially by the founders.
Operating the platform without automated systems proved to be important to gain a better understanding of the user experience. Additionally, it also highlighted the weaknesses in the system and focused attention on areas of improvement to accelerate growth as they scale. Also, during this initial phase, the founders were able to meet many other like-minded individuals and got introduced to the many tightly-knit and passionate 3D printing communities in their area, who also shared common views about “democratizing” additive manufacturing.
In the near-to-medium future, 3D Hubs should start to get the industry leaders on board by communicating directly with the 3D printer manufacturers. Since the founders had already spent time in the industry working with some of these manufacturers, they have a high chance of being able to convince them to represent their brands on the 3D Hubs platform. Satisfied 3D printer owners will probably talk highly of their machines within their local community, creating good publicity for the manufacturer brands.
Also, approaching manufacturers and encouraging them to add 3D Hubs promotional flyers with their sold printers to help encourage their customers to put their new 3D printer on our platform would be a feasible approach to reach more of their target audience. If adopted, within a few months, this promotional strategy can quickly be implemented with several 3D printer manufacturers.
Since many of the customers pick up their orders locally, often watching a live demonstration of the 3D printer manufacturing their part, this will excite them to consider buying the same 3D printer for themselves. Also, since 3D Hubs publishes performance data of 3D printers on their platform, manufacturers have an incentive to get more of their 3D printers signed up to the network as it increases their visibility within their target community. This would enable manufacturers to tap into the growing 3D Hubs community, and vice versa, creating a win-win situation with minimal cost.
Moving forward, a few things that 3D Hubs needs to consider are:
- What steps does 3D Hubs need to take in order to become an industry thought leader?
- How will 3D Hubs be able to scale and have a more global presence?
(Word count: 735)
References
[1] C. Schellya, G. Anzaloneb, B. Wijnenb, J. Pearcebc, Open-source 3-D printing technologies for education: Bringing additive manufacturing to the classroom.
[2] I. Vernera, A. Merksamerb, Digital Design and 3D Printing in Technology Teacher Education.
[3] B. Zwart, Five things we learned from building a global 3d printing network. Accessed November 12, 2018.
[4] B. Roca et al., Getting past the hype about 3-D printing. MIT Sloan Management Review 58, no. 3 (Spring 2017): 57–62.
[5] https://www.3dhubs.com. Accessed November 12, 2018.
[6] https://www.facebook.com/3dHubs. Accessed November 12, 2018.
[7] https://en.wikipedia.org/wiki/3D_Hubs. Accessed November 12, 2018.
Previous:
Stitch Fix: Using Machine Learning to Help The Grinch
Next:
Tesla: How Machines Are Now Driving Our Cars
3D Printer Comparison Guide 2020
The market for 3D printing and additive manufacturing has changed significantly in recent years. While technology used to be mostly a hobbyist business, high-end desktop machines have turned it into an indispensable tool for businesses. After 3D printing became the main tool for prototyping and product design, it has become widely used in manufacturing, dentistry, jewelry and many other fields.
Fused Deposition Modeling (FDM) and Stereolithography (SLA) printers are the two most popular types of 3D printers on the market. Both 3D printing technologies have been adapted and enhanced for desktop use, increasing their accessibility, functionality and usability.
In this comprehensive buyer's guide, we take a closer look at FDM and SLA 3D printers and compare them in terms of print quality, materials, application, workflow, speed, cost, and more to help you determine which method is the most suitable for your business.
VIDEO MANUAL
Can't find the 3D printing technology that best suits your needs? In this video tutorial, we compare Fused Deposition Modeling (FDM), Stereolithography (SLA), and Selective Laser Sintering (SLS) technologies in terms of the top factors to consider when purchasing.
Watch Video
Fused Deposition Modeling (FDM), also known as Fused Filament Manufacturing (FFF), is the most widely used form of 3D printing at the consumer level. The working principle of FDM 3D printers is to extrude thermoplastic filaments such as ABS (Acrylonitrile Butadiene Styrene), PLA (Polylactide) through a heated nozzle, melt the material, and deposit the plastic on the build platform layer by layer. Layers are applied sequentially one after another until the model is ready.
See how FDM 3D printing is done.
FDM 3D printers are well suited for making basic experimental models, as well as for quickly and inexpensively prototyping simple parts, such as parts that are usually machined.
Invented in the 1980s, stereolithography is the world's first 3D printing technology and is still one of the most popular technologies among professionals today. SLA 3D printers use a process called photopolymerization, which is the conversion of liquid polymers into hardened plastic using a laser.
See how SLA 3D printing is done.
Resin-based SLA 3D printers have become extremely popular due to their ability to produce highly accurate, isotropic and waterproof prototypes and models with excellent detail and smooth surfaces. SLA polymers offer a wide range of optical, mechanical and thermal properties that match those of standard, engineering and industrial thermoplastics.
Resin 3D printing is an excellent option for producing highly detailed prototypes that require tight tolerances and smooth surfaces such as molds, templates and functional parts. SLA 3D printers are widely used in industries ranging from engineering and design to manufacturing, dentistry, jewelry, modeling, and education.
White Paper
Download our white paper to find out how SLA printing works, why thousands of professionals use it today, and how this 3D printing technology can be useful in your work.
Download white paper
When additive manufacturing builds a model layer by layer, each layer contains the potential for inaccuracies. The layering process affects the surface quality, the level of accuracy and correctness of each layer, and therefore the overall print quality.
FDM 3D printers form layers by applying lines of molten material. During this process, the resolution of the model is determined by the size of the extrusion nozzle, and when lines are drawn with the nozzle, voids are created between the rounded lines. As a result, the layers may not be completely adjacent to each other, they are usually clearly visible on the surface, and, in addition, there is no ability to reproduce the complex details that other technologies offer.
In SLA 3D printing, each layer is formed by curing a liquid polymer with a high-precision laser, which allows you to get models with greater detail and achieve high quality on a consistent basis. As a result, SLA 3D printing is known for excellent detail, smooth surfaces, high precision models and accurate rendering.
3D Printing Accuracy, Accuracy and Tolerance are terms that are not entirely clear and often misunderstood. Find out what they mean to get a better idea of 3D printing quality.
Models created using SLA technology have sharp edges, smooth surfaces and almost invisible layer lines. This sample was printed on a Formlabs Form 3 desktop stereolithography 3D printer.
Using light instead of heat in the printing process is another way to ensure the print quality of SLA printers. Since 3D models are printed at close to room temperature, they do not suffer from the thermal expansion and contraction distortions that can occur during FDM printing.
Due to the high-precision laser, SLA 3D printers are better suited for making complex parts (FDM printed part on the left, SLA printed part on the right).
While FDM printers create a mechanical bond between layers, SLA 3D printers create chemical bonds between photopolymers by cross-linking photopolymers, resulting in dense, waterproof and airtight models. These bonds provide a high degree of shear strength resulting in isotropic parts, which means that the strength of the parts does not change depending on the direction. This makes the use of SLA 3D printing especially useful in the field of engineering and manufacturing, where material properties are important.
The quality difference is less noticeable on relatively simple parts. However, SLA parts are dense and isotropic, so they find more use in design and manufacturing (left - FDM printed part on the left, right - SLA printed part on the right).
free sample
Experience Formlabs print quality firsthand. We will send a free 3D printing sample directly to your office.
Request a Free Sample
Extrusion 3D printers use a range of standard thermoplastic filaments such as ABS, PLA and various blends thereof. The popularity of FDM 3D printing among hobbyists has led to a large number of colors available. There are also various experimental mixtures of plastic threads designed to create models with a surface that mimics wood or metal.
Engineering materials such as nylon, PETG, PA or TPU and high strength thermoplastics such as PEEK or PEI are also available, but in most cases only certain professional FDM printers support them.
FDM filaments and blends offer various color options. (source: All3DP.com)
The advantage of SLA polymers is 's wide range of formulations offering a variety of characteristics: they can be soft or hard, contain additives such as glass and ceramic, have special mechanical properties such as high bending temperature under load or shock resistance. The polymers offer a wide range of optical, mechanical and thermal properties that match those of standard, engineering and industrial thermoplastics.
SLA 3D printers provide access to a variety of materials for design and production.
In some cases, it is this combination of versatility and functionality that leads businesses to adopt SLA 3D printing in-house. Once a solution has been found with a particular functional polymer, other applications are usually quickly discovered, and the printer becomes a tool for exploiting the diverse properties of different polymers.
Some properties of SLA polymers are unique. Among them:
SLA is the only 3D printing technology that allows you to create transparent models on a desktop printer. Ideal for enhancing the visibility of complex assemblies, (micro)fluidic elements, mold making, optics, lighting elements and any product requiring transparency.
Learn more
Parts printed with this material look and feel like silicone; They are durable enough to be used multiple times.
Learn more
Provides the highest HDT of 238°C at 0.45 MPa, the highest temperature resistance of any desktop 3D printing material.
Learn more
Resin with 20% wax for investment casting and pressing of dental and jewellery.
Learn more
Specialty resins for dental products such as biocompatible surgical guides, splints, permanent casts and dentures, clear aligner patterns, and complete dentures.
Learn more
Resin for 3D printing of models with a stone-like texture and subsequent production of a ceramic product by firing.
Learn more
Material selection
Our interactive materials wizard helps you select the right material from our growing range of polymers based on the future application of the material and the properties that matter most to you.
Get material recommendations
Both FDM and SLA 3D printing workflow consists of three steps: design, 3D printing, and post-processing.
First, a model is designed using CAD software or 3D scan data and exported to a 3D print file format (STL or OBJ). Then you need to use the software to prepare the 3D model for printing, in particular, set the print parameters and separate the digital model into layers.
Budget 3D FDM or SLA printers are not very convenient in terms of usability: finding the right print settings for them requires experimentation and often takes hours. Even so, when using a new design or material, the print result may change, and the probability of rejection remains high. This not only causes delays in projects, but can also cause printer failure that will take a long time to resolve.
Professional SLA 3D printers such as the Form 3 and some professional FDM printers come with their own proprietary software and presets for each material that have been rigorously tested to ensure the best printing results.
With advanced print preparation tools such as PreForm, print setup is plug and play. PreForm software is available as a free download and you can try it right now. .
Once the 3D printing process has started, most 3D printers can run it without an operator, even overnight, until the model is finished. Advanced SLA 3D printers such as the Form 3 automatically refill resins from cartridges.
The last step in the workflow is post-processing. Models produced by SLA require rinsing with isopropyl alcohol (IPA) or alternative solvents to remove uncured polymers from their surface. The standard workflow involves first removing the models from the build platform and then manually soaking them in a solvent bath to remove excess resin.
Professional solutions such as Form Wash automate this process. Models from the printer are transferred to the Form Wash station, which cleans the models by stirring the solvent around them and automatically removes the models from the alcohol bath when the process is complete.
After washed models have dried, some SLA resins require final polymerization , a process that helps models achieve the highest possible strength and stability.
The advantage of the FDM method is that it does not require cleaning; models without supporting structures are ready for use or post-processing immediately after the printing process is completed.
In both FDM and SLA printing, support structures can be used to facilitate 3D printing of complex shapes, and their removal is the last step in post-processing.
On FDM models, the supporting structures must be separated manually or dissolved in water, depending on the material of the structure.
Obtaining a high quality surface on FDM models with supporting structures requires additional post-processing (source: 3D Hubs).
Removal of the supporting structures on SLA models consists of cutting off the supporting structures and lightly sanding the models to remove traces of the supports. Formlabs Low Force Stereolithography (LFS) ™ technology offers easy-to-release supports that allow separation of the object from the supporting structure in seconds and with minimal marks, reducing post-processing costs.
In additional post-processing, both FDM and SLA models can be machined, primed, painted or assembled depending on the application. However, before priming or painting, FDM models require additional sanding, and for machining or drilling, a higher filling density is required.
Use our easy-to-use interactive tool to help you calculate model costs and lead times using your Form 2 3D printer and compare time and cost savings with other manufacturing methods.
One of the main advantages of FDM 3D printers is the low cost of the device. Entry-level FDM printers are available for as little as a few hundred dollars, giving hobbyists and small businesses a chance to see 3D printing in action and decide whether to add the technology to their toolbox. For novice users, the lower cost of an entry-level FDM printer is often an argument for making a purchase. However, inexpensive FDM printers can be unreliable and often require specialized knowledge for long-term use.
Professional desktop FDM printers are easier to use and more suitable for business applications and are priced between $2,000 and $8,000. Such 3D printers typically offer higher reliability, higher print quality, and higher print volumes. Although these devices are suitable for the production of functional models, competition in this price category is strong, since the scope of SLA printers is wider and the print quality is better.
SLA 3D printers start at $3750 and only Formlabs releases SLA Large Format 3D Printer priced under $11,000.
In terms of materials, FDM filaments also have a relatively low cost compared to materials used in other 3D printing technologies. Commonly used FDM materials such as ABS, PLA and their various blends typically cost around $50/kg, while specialized FDM filaments for engineering applications can cost $100-150/kg. Soluble support materials for dual extrusion FDM 3D printers sell for $100-200/kg. By comparison, most standard and engineered resins for SLA 3D printers cost $50-$150/L.
Labor is the last and often overlooked part of the equation. FDM models of simple form, which do not need support structures when printed, require almost no post-processing. For FDM models with supporting structures and parts where high surface quality is important, lengthy manual post-processing is required.
SLA models require rinsing and, depending on the material, also final polymerization, but in most cases both processes can be carried out to automate with accessories , thus minimizing labor costs. SLA models with support structures require only minimal sanding to remove support marks and achieve a high quality finish.
INTERACTIVE
Try our interactive ROI tool to see how much time and money you can save by printing with Formlabs 3D printers.
Calculate savings
FDM printers can print thicker layers and typically use lower infill density, which speeds up the 3D printing process. FDM also has fewer post-processing steps for simple models. Depending on the specific project, this means that the models are ready for use shortly after printing is completed. This is very useful for tasks such as rapid prototyping - users can quickly evaluate the result and move on to printing another model or project.
However, the speed advantage of FDM is currently waning due to the emergence of faster SLA resins such as Draft Resin , which prints 40% faster than FDM 3D printers. With a layer thickness of 300 µm, Draft Resin achieves sufficient precision to meet the needs of prototyping while enabling faster design iteration cycles. If the model occupies the entire working volume, it can take up to 20 hours for the SLA printer to produce it using standard resins, which will require printing at night. Printing the same part in 300 micron layers with Draft Resin takes less than six hours.
These are six prototype pump housings printed using Draft Resin. It took 3 hours and 7 minutes to print one prototype with standard resins, and 47 minutes with Draft Resin. The final model was printed using Tough Resin and Rigid Resin.
With the same layer thickness, the print speed of FDM and SLA printers becomes comparable. Please note that due to the way the layers are formed, a part printed with 100 micron layers on an FDM printer is very different from a part printed with 100 micron layers on an SLA printer. Achieving comparable quality on an FDM printer would require a thinner layer—which means two to four times longer print times—or more and longer post-processing to improve surface quality.
Webinar
In this webinar, two Formlabs experts will teach you when to use Draft Resin and how to incorporate this resin into your 3D printing workflow to speed up your 3D printing workflow and shorten your product development cycle.
Watch the webinar now
Print volume is an area where FDM printers have traditionally dominated. Due to the specifics of the technology, the production of large-format FDM printers is less complicated. There are many large format FDM solutions on the market for applications that require 3D printing of large parts.
Inverted stereolithography used in desktop SLA printers reduces printer footprint and cost, but the intensive layer separation process creates material and print volume limitations, and strong support structures are required to successfully print larger parts.
The development of Formlabs Low Force Stereolithography (LFS) technology, used in the Form 3 and Form 3L printers, has revolutionized the approach to resin 3D printing and drastically reduced the forces on models during the printing process. Uniform linear illumination and a force-reducing elastic reservoir mean that Low Force Stereolithography technology can be seamlessly scaled to a wider print area using the same powerful print engine.
The first affordable large-format stereolithography printer, the Form 3L prints large details quickly using two stepped Light Processing Units (LPUs) that work simultaneously on an optimized print path. Offering up to five times the print volume of current SLA printers, the Form 3L eliminates size constraints that can be found on small desktop devices at a competitive price.
9The 0002 Form 3L offers five times the print volume of existing SLA printers at a competitive price.Each 3D printing technology has its strengths, weaknesses, limitations and applications. The following table summarizes the key characteristics and factors.
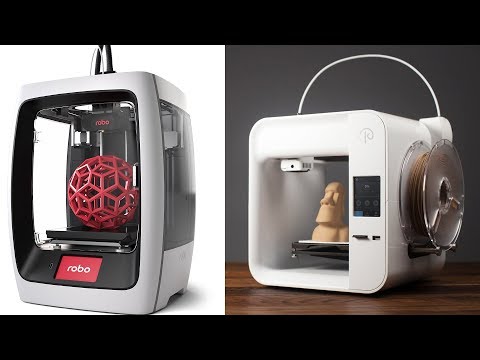
Comparing the two technologies, we can conclude that FDM and SLA printers have similar, often complementary features. These two types of 3D printers are not always in competition; many companies use both FDM and SLA 3D printers. In this way, you can get the best of both worlds: inexpensive rapid prototyping combined with high-quality functional model production allows you to solve a wide range of problems.
Some practical examples:
-
When developing products, FDM models or SLA printing with Draft Resin are ideal for basic proof-of-concept testing and faster iteration. As you move into the next stages of development, SLA 3D printing is indispensable for producing detailed concept models or functional prototypes that may require higher quality and materials with different properties.
-
Both FDM and SLA 3D printing are often used in manufacturing to make clamps, fasteners and other tooling. FDM is best suited for large and simple parts, SLA for complex fixtures, precision fixtures and molds.
-
FDM and SLA printers are being used effectively in education.
Many schools are starting out with FDM printing because its low cost allows it to offer students quick drafts and hands-on experience with the technology. SLA technology is popular among technical schools, universities, research institutes, as well as in the teaching of dentistry and to jewelry because of the higher quality and wider range of applications.
The University of Sheffield's Advanced Manufacturing Research Center (AMRC) uses a fleet of 12 stereolithographic 3D printers for most engineering and manufacturing tasks and five industrial FDM printers for large parts.
Check out our white paper, , for a detailed overview of SLA ecosystems and a step-by-step 3D printing workflow.
Want to see the quality of the SLA with your own eyes? Select an application from our list and request a free sample of to find the right material for your application.
Request a free sample
3D printers in building applications
At first glance, 3D printed structures look like the shell of a half-finished building. But upon closer examination, you will not find even a brick. Layers of material seem to build up one on top of the other - this is how a complex structure is created. It's a futuristic world of 3D printing where robotic arms automatically layer and compress layers of concrete or plastic or any other material into a foundation and build a structure.
This construction method is quite niche today - only a few prototypes of 3D houses and offices have been printed in the world. However, this technology represents an exciting and potentially powerful solution to building change.
What is 3D printing in construction, what is the potential, and will we be working on 3D printed projects in the near future?
- What is 3d printing in construction?
- 3D printers in construction: how is it done?
- 5 examples of innovation
- How can 3d printed projects help construction companies?
- 3D printing distribution
- 3D printing in civil engineering
- Wiki House technology - an open source project for 3D printing: what is behind the concept
- Reverse side of the coin
- How can 3D printing be integrated into construction
- About PlanRadar
3D printing in construction - what kind of technology?
3D printing for construction uses both a 3D printer, which has a robotic "crane-arm" that builds structures right on the construction site, and the creation of certain elements by printers at the factory, which are already assembled into a structure on site.
The concept of 3D printing is not new: it first appeared in the 80s. But it's only in the last decade that this technology has been improved enough (and the cost significantly reduced) to become a real mainstream.
3D printers are not much different from regular inkjet office printers. The software tells the printer about the dimensions of the final product. And then the printer starts to output the material to the platform according to the plan. 3D printers often use liquid metals, plastics, cement, and variations of various materials that, when cooled and dried, form a structure.
In a 3D construction printer, the CAD or BIM programs tell the device what to print, and the machine starts layering the material according to the design plan.
3D printers in construction: how do they work?
3D printing concept - The printer extrudes a defined liquid mixture in layers, layer by layer, creating a design based on a 3D model. The prepared mix of concrete, filler, plasticizer and other components is loaded into the hopper of the device and fed to the print head. The mixture is applied to the surface of the site or to the previous printed layers. This is how most 3D printers work. Among them, there are three types of devices for 3D printing:
Robotic printer
Read also: New technologies in construction 2021
5 innovative examples of 3D printing
To date, only a few 3D printing projects have been implemented in the construction industry. Here are five of the most impressive and promising projects:
Dubai City Hall Office Building, UAE
1. Dubai City Hall Office Building, UAE
3D printed building. The office block built in the UAE is 9,5 meter high building with an area of 640 m2.
An Apis Cor 3D printer moved around an open-air construction site with a crane and erected various parts of the structure.
2. Office of the Future, UAE
Office of the Future, UAE
Another impressive 3D printed building in the UAE, the Office of the Future is a unique, fairly large structure that currently houses a temporary headquarters organization Dubai Future Foundation.
For this building, the elements were not created on site and were printed in 17 days, while the building itself was assembled in 48 hours.
3. WinSun 3D Printer Homes, China
WinSun 3D Printer Homes, China
WinSun 3D Printing Company in China has also applied factory-built 3D printers to build residential buildings. The company has created several house projects, including a small multi-storey building. All construction details can be printed quickly and cheaply and then quickly assembled on the construction site.
The company estimated that it would cost as little as $161,000 to build and print their five-story building.
4. 3D printed license plate at Lewis Grand Hotel, Philippines
3D printed license plate at Lewis Grand Hotel, Philippines
When planning a trip to the Philippines, consider staying at the Lewis Grand Hotel in Angeles City , Pampanga, where visitors will be greeted with the world's first 3D printed hotel suite. The hotel room was designed by Lewis Jakich, hotel owner and materials engineer, in collaboration with 3D printing specialist Anthony Rudenko. They created a massive 3D printer that prints sand and concrete based on volcanic ash. The room was printed in 100 hours.
5. Two-story mansion in Beckum, Germany
Two-story mansion in Beckum, Germany
The first 3D-printed residential building with an area of about 80 square meters - the brainchild of the German construction company PERI GmbH and the architectural design bureau MENSE-KORTE ingenieure + architecture. A BOD2 3D printer was used to print one square meter of double wall cladding in 5 minutes. The building is a structure with three-layer hollow walls filled with insulating mass. Installation of hollow pipes and connections during printing was carried out manually.
3D printing in construction seems really impressive, but what are the real benefits of such technology?
How can 3D printed designs help construction companies?
Proponents of 3D printing houses and commercial offices point to several advantages of this method of construction:
- Waste-free construction
In the UK, almost a third of the waste comes from the construction industry. According to the Transparency Market Research Group, the construction industry worldwide will produce 2.2 billion tons of construction waste by 2025. And although most of the waste is related to the demolition of buildings, the construction sites themselves produce a lot of waste.
In contrast, 3D printing can reduce waste to almost zero. A 3D printer uses a well-defined amount of material that is required to print a design - no more, no less. This can be a big savings.
- Reduced energy consumption
3D printing in construction encourages the use of locally available materials and natural ingredients. This practice can reduce energy costs in transportation, construction and manufacturing, as most local materials require less energy to process or install. If traditional materials with toxic chemical impurities are replaced with natural ones, then the toxicity of the entire construction can be reduced. In addition, local materials are often better suited to local climates and can reduce a building's heating or cooling load, which also reduces construction costs.
- Save time and money
As with AI in construction, a 3D printer can run 24 hours a day, 7 days a week. This means construction projects have the potential to be completed much faster and a number of low-skilled labor costs can be avoided. What's more, 3D printing eliminates the need for temporary structures, such as formwork and scaffolding, that are commonly used in traditional construction. Studies of 3D printed concrete structures have shown a significant reduction in formwork requirements, reducing costs by 35-60%.
- Can realize unusual design shapes
One of the most attractive characteristics of 3D printers is their ability to create complex and unusual design designs, including the only one that is unique. Since the job of a 3D printer is to layer the material, they can be programmed into absolutely any unusual shape that would be much more difficult to create with traditional techniques.
- Minimize human error and improve safety
The published injury statistics at the workplace by the American agency BLS in 2020 indicates that construction is one of the injury-prone areas and a high incidence of diseases. Every day, about 5333 workers die on the construction site. And with the advent of 3D printing, the number of work injuries and fatalities will obviously decrease, as it makes construction more programmable and automated. Robotic construction requires standardized, accurate and complete digital building information, making this technology more accurate and efficient, with minimal rework due to human error or any information inconsistencies. The usual problems with materials and components that need to be stored somewhere, protected from damage are leveled out, problems with installation and work in progress due to damage also disappear - 3D elements are created as they are built, they do not need to be moved and stored.
- Exploring new markets
The use of a 3D printer also allows construction companies to enter new market sectors that were previously inaccessible to them. And for start-up companies, having a 3D printer will be a competitive advantage. What's more, 3D printing is a brilliant way to elevate or improve the reputation of a construction company's brand among those who believe that concrete production has an impact on the planet's environment.
Distribution of structural 3D printing
3D printing for structural reinforcement, small scale components and structural steel could revolutionize design, construction and space exploration. In addition, the European Space Agency (ESA) believes that using 3D printed metals to create high-quality complex shapes can significantly reduce their cost, and they will become very common.
ESA has developed a project with the European Commission to improve the printing of metal components that can be used in space. In total, 28 European partners have united for the joint project AMAZE (Additive Manufacturing Aiming Towards Zero - layer-by-layer 3D printing for zero waste from production and efficient production of high-tech metal products).
Almost everything can be designed on a computer, so AMAZE plans to install a 3D printer on board the spacecraft, and as soon as an astronaut needs any part, a tool, he can simply print it.
Structural 3D printing
Civil engineering 3D printing
Civil engineering 3D printing has been gaining popularity over the past decade, as has the aerospace and biomedical industries. This revolutionary manufacturing technique is based on its unique ability to create any geometric shape without any formal restrictions, minimizing waste but increasing productivity and results. The construction industry's push towards automation has recently reached important milestones, including the creation of the first structures using robotic "arms" and 3D printing technology.
The use of 3D printing in the creation of structural elements from polymer materials, concrete and metals is becoming more common.
These civil engineering technicians can create free-form and innovative architectural designs using CAD-integrated software.
However, despite significant research in the aerospace and bioengineering industries to evaluate and analyze this mechanism, there is still a lack of understanding of its use, the impact of 3D printed materials in civil structures, both in terms of material properties and structural response.
Imperial College London
Read also: Best Building Apps in 2021
WIKI HOUSE - 3D printing in construction: what is the concept behind
Wiki House is an innovative project created by a small group of architects in London in 2011 . It offers an open source digital house design system that allows users to create, upload and share designs and print their own houses.
The kit does not require any special knowledge and training and can be created in 1 day. Elements are digitally cut from ordinary sheet material, like plywood, using a CNC machine. And it's much faster, less costly, and doesn't require the involvement of experts, as in conventional traditional construction.
A standard two bedroom house can be built for less than £50,000 and additional components such as cladding, insulation, windows and more can be added to the main frame of the structure. The first house that was built on the basis of the open source Wiki House technology was a two-story building. The 3D printed house was presented at the London Design Festival in 2014.
The Wiki House movement was spearheaded by Alastair Parvin, whose TED presentation "Architecture for People, Built by People" talked about the promise of 3D printing in construction. The creator of this project believes that Wiki House can help solve the housing problem, especially in emergency situations such as earthquakes (there is already evidence that 3D-printed houses can withstand shocks up to magnitude 8).
In the future, this could become a real alternative to low-cost houses while allowing the customer to control the design of the project.
3D building built using Wiki House
Will 3D printing be the sustainable future of building?
3D printing has the potential to revolutionize the supply chain and structure through a new method of design and manufacturing. According to the study, 3D printing can help the construction industry become more economical, more efficient and greener.
Saxon University of Applied Sciences scientists Ivo Kotman and Neils Faber claim that 3D printing technology will be a "game changer". They explored the possibilities of 3D printing concrete, and their conclusions are:
- 3D printing shortens the supply chain and the overall design process. 3D printing right on the job site eliminates time-consuming steps in the design process. The architects, engineers, contractors, clients, and executives who normally have to be actively involved in a project are no longer needed in 3D printing.
Since all tasks can be combined in one figure of the architect, who uses the modeling method and reproduces the exact holistic designs.
- Pipe fitting and electrical wiring become easier and more efficient. Heating systems, insulation, plumbing and electricity all require the laborious on-site installation of conventional construction. However, in 3D printing, some of these features can be incorporated into the 3D printing process. Cavity wall printing is less resource intensive, improves insulation, and allows the use of 3D-printed hot or cold water channels. Moreover, the need for on-site installation is eliminated, which directly affects the reduction of waste.
- The best logistics. 3D printing eliminates 3 logistics and shipping issues. Firstly, a lot of materials and elements often deteriorate upon delivery, and if everything is printed on site, then damage is minimized
Secondly, in order to withstand transportation, the parts must be with increased technical characteristics, which by default increases the cost of them, and therefore the entire project. 3D printing right on the construction site will help to avoid such additional costs.
- Creation of individual house designs available to the general market. Usually, building a house with the involvement of an architect is an expensive pleasure for most consumers. But with concrete 3D printing, you don't have to worry about the chosen shape, it won't cost more. In fact, this means that in the future, more people will be able to buy houses of their own design, according to their individual needs
Reverse side of the coin
While 3D printing is definitely attractive, it's still important to look at it impartially, removing some of the promotional stimulus. Skeptics note several disadvantages of this technology.
- Research and development costs
Most construction companies operate with relatively low profitability. To start using 3D printing everywhere, significant investments will be required.
- Will consumers see this as a marketing ploy?
3D printed houses, offices, shops and other infrastructure are often impressive. But do most people really want to live or work in one? For most people, brick houses are much more familiar and attractive. Other technologies such as prefabricated houses also seemed like an attractive technology of the future for some time, but have not been widely adopted, despite the fact that in many cases they were cheaper than traditional ones.
- Difficulty integrating with other components
3D printers can create unique and interesting designs. However, if you need a building that will use different materials or different elements that will not be suitable for 3D printing, then it will be a challenge to include a 3D printer for the building process.
- Skilled labor shortage
With the current problem of a shortage of skilled labor in the construction sector in general, 3D printing will require an even larger set of specialized knowledge and skills, which will have to be selected from an already small niche of candidates. So finding specialists to work in 3D printing for construction may be another difficult task in the future.
- Construction quality control
Weather conditions can slow down the traditional building process, but things are even worse for 3D printing. The environmental factor for commercial construction may reduce the demand for 3D printing. What's more, quality control can be a much more serious task, requiring constant monitoring of the process by real people at the construction site.
- No standards and regulations
Despite the regular mention of 3D printing in the media, it still has not had a significant impact on the construction sector. There is an obvious liability issue when using these printers, even more so than human liability when doing some construction work. And quite a few other ambiguities regarding this technology. So until norms and standards are established, as well as rules in this area, 3D printing is unlikely to become mainstream in the construction industry.
Read also: New technologies in construction 2021
How can 3D printing be integrated with construction?
At the moment there is strong evidence that 3D printing is worthy of attention and can be applied in the construction segment, and it is likely that this technology will be used more in the coming years. True, it is not known how widely these devices will be used on the construction site, or whether they will remain only a tool for the manufacture of block elements for prefabricated structures. But for certain projects, it is reasonable to assume that 3D printers and this technology in construction will be a must-have tool in the arsenal of builders.