3D printer retraction speed
How to Get the Best Retraction Length & Speed Settings – 3D Printerly
There are many settings that we can adjust and improve on our 3D printers, one of them being retraction settings. It took me a while to figure out how important they were, and once I did, my 3D printing experience changed for the better.
Many people don’t realize how important retraction can be until they are troubleshooting poor print quality in certain models.
Retraction settings are related to the speed and length at which your filament is pulled back within your extrusion path, so the melted filament at the nozzle doesn’t leak out while moving. Retraction can improve overall print quality and stop print imperfections such as blobs and zits.
What is Retraction in 3D Printing?
When you hear that rotating noise backwards and see filament actually getting pulled back, that is retraction occurring. It is a setting which you’ll find in your slicer software, but it isn’t always enabled.
After you have understood the basics of printing speed, temperature settings, layer heights and widths, then you start to get into the more nuance settings like retraction.
We can be specific on telling our 3D printer how exactly to retract, whether that be the length of retraction, or the speed at which the filament is retracted.
Accurate retraction length and distance can reduce the chances of different problems mainly the stringing and oozing.
Now that you have a basic understanding of retraction in 3D printing, let’s explain the basic retraction terms, retraction length and retraction distance.
1.

Retraction distance or retraction length specifies the length of the filament that will be extruded from the nozzle. The retraction distance should be adjusted accurately because both too low and too high retraction distance can cause printing problems.
The distance will tell the nozzle to pull back the amount of filament according to the specified length.
According to the experts, the retraction distance should be between the 2mm to 7mm distance for Bowden extruders and should not be more than the length of the printing nozzle. The default retraction distance on Cura is 5mm.
For Direct Drive extruders, retraction distance is on the lower end, of around 1mm to 3mm.
While adjusting the retraction distance, increase or decrease it in small increments to get the best suitable length because it varies depending on the type of filament you are using.
2. Retraction Speed
Retraction speed is the rate at which the filament will retract from the nozzle while printing. Just like the retraction distance, setting the most suitable retraction speed is necessary to get better results.
Retraction speed should not be too low because the filament will begin to ooze from the nozzle before it reaches the exact point.
It should not be too fast because the extruder motor will reach the next location quickly and the filament will extrude from the nozzle after a short delay. A distance too long can cause a decline in print quality because of that delay.
It can also result in the filament getting ground and chewed up when the speed generates too much biting pressure and rotation.
Most of the time the retraction speed works perfectly at its default range but you may need to adjust it while switching from one filament material to another.
How to Get the Best Retraction Length & Speed Settings?
To get the best retraction settings you can adopt one of the different ways. Implementing these processes will surely help you to get the best retraction settings and print the object just as you expected.
Notice that the retraction settings will be different depending on the fact that whether you have a Bowden setup or a Direct Drive setup.
Trial and Error
It is the best technique to get the best suitable retraction settings. Print a small object just for retraction tests that can be printed in a short period.
Start the printing process by changing the retraction speed and retraction distance step by step and see where the printer is performing well. Start printing the actual object when you are completely satisfied with the retraction tests print.
Changes Between Materials
The retraction settings are usually different for every filament material being used. You have to calibrate the retraction settings accordingly every time you use a new filament material such as PLA, ABS, etc.
If you are facing any problem even after changing the retraction setting, try to use filament materials that are comparatively flexible because these types of filament will work properly on the low retraction speed as well.
Cura has actually released a new method to dial in your retraction settings directly within the software.
The video below by CHEP explains it really well so check it out. There are specific objects that you can put on your build plate from within Cura where you can also insert scripts to best test retraction settings, one at a time.
Cura Retraction Settings on Ender 3
The Cura retraction settings on Ender 3 printers usually include different settings and the ideal and expert choice for these settings will be as follows.
- Retraction Enabling: First, go to the ‘Travel’ settings and check the ‘Enable Retraction’ box to enable it
- Retraction Speed: It is recommended to test a print at 50mm/s and if you notice any issues in the filament, try decreasing the speed by 10 mm and stop when you notice improvements.
- Retraction Distance: On Ender 3, the retraction distance should be within 2mm to 8mm. Begin at 5mm and then adjust it until the nozzle stops oozing.
- Max Retraction Cont: “10” is considered as the ideal choice, only change this count if you feel any issue in the printing process.
The best thing you can do on your Ender 3 is implement a retraction tower to calibrate the best retraction settings. How this works is you can set your Ender 3 to use increments of each setting per ‘tower’ or block to see which gives the best quality.
So you would do a retraction tower to start with a retraction distance of 2mm, then have 3mm, 4mm, 5mm, up to 8mm and see which retraction setting gives the best results.
What 3D Printing Problems Do Retraction Settings Fix?
As it is mentioned above, stringing or oozing is the major and most common problem that occurs just because of wrong retraction settings.
It is essential that the retraction settings should be calibrated accurately by keeping every aspect in mind to get a well-crafted, high-quality print.
Stringing is referred to as a problem in which the print has some strands or threads of filament between two printing points. These strands occur in an open space and can completely destroy the beauty and charm of your 3D print.
When the retraction speed or retraction length cannot match, the filament will drop or ooze from the nozzle, and these oozing results in stringing.
Most of the 3D printer experts and manufacturers suggest adjusting the retraction settings to avoid the oozing and stringing problems effectively. Calibrate retraction settings according to the filament you are using and the object you are printing.
How to Avoid Stringing in Flexible Filament (TPU, TPE)
Flexible filaments such as TPU or TPE are used for 3D printing because of their amazing non-slip and impact resistance properties. Keep this fact in mind that flexible filaments are more prone to oozing and stringing but the problem can be stopped by taking care of printing settings.
- The first and most important thing is to enable retraction settings every time you are using flexible filament.
- Set up a perfect temperature because high temperatures can cause the problem as the filament will melt quickly and may start dropping.
- Flexible filaments are soft, do a test print by adjusting retraction speed and retraction distance because a bit of difference can cause stringing.
- Adjust the cooling fan according to the printing speed.
- Focus on the flow rate of the filament from the nozzle, usually flexible filaments work well at 100% flow rate.
How to Fix Too Much Retraction in 3D Prints
It’s definitely possible to have retraction settings that are too high, leading to printing issues. One issue would be a high retraction distance, which would cause filament to retract too far back, leading to filament being closer to the hotend.
Another issue would be a high retraction speed which might reduce the grip and not actually retract properly.
To fix retractions that are too high, turn your retraction distance and speed down to a lower value to see if it fixes retraction issues. You can find some standard retraction settings for your extruder and 3D printer in places like user forums.
Stringing or Oozing
Stringing or Oozing
Stringing (otherwise known as oozing, whiskers, or “hairy” prints) occurs when small strings of plastic are left behind on a 3D printed model. This is typically due to plastic oozing out of the nozzle while the extruder is moving to a new location. Thankfully, there are several settings within Simplify3D that can help with this issue. The most common setting that is used to combat excessive stringing is something that is known as retraction. If retraction is enabled, when the extruder is done printing one section of your model, the filament will be pulled backwards into the nozzle to act as a countermeasure against oozing. When it is time to begin printing again, the filament will be pushed back into the nozzle so that plastic once again begins extruding from the tip. To ensure retraction is enabled, click “Edit Process Settings” and click on the Extruder tab. Ensure that the retraction option is enabled for each of your extruders. In the sections below, we will discuss the important retraction settings as well as several other settings that can be used to combat stringing, such as the extruder temperature settings.
Common Solutions
Retraction distance
The most important retraction setting is the retraction distance. This determines how much plastic is pulled out of the nozzle. In general, the more plastic that is retracted from the nozzle, the less likely the nozzle is to ooze while moving. Most direct-drive extruders only require a retraction distance of 0. 5-2.0mm, while some Bowden extruders may require a retraction distance as high as 15mm due to the longer distance between the extruder drive gear and the heated nozzle. If you encounter stringing with your prints, try increasing the retraction distance by 1mm and test again to see if the performance improves.
Retraction speed
The next retraction setting that you should check is the retraction speed. This determines how fast the filament is retracted from the nozzle. If you retract too slowly, the plastic will slowly ooze down through the nozzle and may start leaking before the extruder is done moving to its new destination. If you retract too quickly, the filament may separate from the hot plastic inside the nozzle, or the quick movement of the drive gear may even grind away pieces of your filament. There is usually a sweet spot somewhere between 1200-6000 mm/min (20-100 mm/s) where retraction performs best. Thankfully, Simplify3D has already provided many pre-configured profiles that can give you a starting point for what retraction speed works best, but the ideal value can vary depending on the material that you are using, so you may want to experiment to see if different speeds decrease the amount of stringing that you see.
Temperature is too high
Once you have checked your retraction settings, the next most common cause for excessive stringing is the extruder temperature. If the temperature is too high, the plastic inside the nozzle will become less viscous and will leak out of the nozzle much more easily. However, if the temperature is too low, the plastic will still be somewhat solid and will have difficulty extruding from the nozzle. If you feel you have the correct retraction settings, but you are still encountering these issues, try decreasing your extruder temperature by 5-10 degrees. This can have a significant impact on the final print quality. You can adjust these settings by clicking “Edit Process Settings” and selecting the Temperature tab. Select your extruder from the list on the left, and then double-click on the temperature setpoint you wish to edit.
Long movements over open spaces
As we discussed above, stringing occurs when the extruder is moving between two different locations, and during that move, plastic starts to ooze out of the nozzle. The length of this movement can have a large impact on how much oozing takes place. Short moves may be quick enough that the plastic does not have time to ooze out of the nozzle. However, long movements are much more likely to create strings. Thankfully, Simplify3D includes an extremely useful feature that can help minimize the length of these movements. The software is smart enough that it can automatically adjust the travel path to make sure that nozzle has a very short distance to travel over an open space. In fact, in many cases, the software may be able to find a travel path that avoids crossing an open space all together! This means that there is no possibility to create a string, because the nozzle will always be on top of the solid plastic and will never travel outside the part. To use this feature, click on the Advanced tab and enable the “Avoid crossing outline for travel movement” option.
Movement Speed
Finally, you may also find that increasing the movement speed of your machine can also reduce the amount of time that the extruder can ooze when moving between parts. You can verify what movement speeds your machine is using by clicking on the Speeds tab of your process settings. The X/Y Axis Movement Speed represents the side-to-side travel speed, and is frequently directly related to the amount of time your extruder spends moving over open air. If your machine can handle moving at higher speeds, you may find that increasing this settings can also reduce stringing between parts.
Related Topics
3D printer speed: how to set it up correctly?
3DPrintStory     3D printing process     3D printer speed: how to set it up correctly?
3D printing is often referred to as "rapid prototyping". The irony is that the creation of individual models can take up to several hours. Fortunately, 3D printing speed can be adjusted to reduce production time, but setting the speed incorrectly can also lead to defects and 3D printing failures.
In this article, we will introduce you to the general speed settings of a 3D printer. By the end of this guide, you'll know how to find the perfect balance between print speed and quality. Please be aware that different 3D printers, slicing software and materials may behave differently and retesting may be required.
Well, run the slicing software and let's get started!
3D Print Speed
3D Print Speed is the main setting that affects the printing of your 3D model. As the name suggests, print speed determines how fast your printer's motors move. This includes the motors that control the X and Y axes, as well as the motor(s) of the extruder.
To test your 3D printing speed, download the test model to determine the optimal print speed above. The description of this 3D model also contains recommendations for speed settings. In essence, the experiment is that the same model will be printed, but at a gradually increasing speed, which will allow you to visually determine the optimal speed setting.
Too low a 3D print speed can cause deformation due to the nozzle being on the plastic for too long. If too fast, other overheating artifacts may appear, caused by insufficient cooling, as well as extrusion and poor adhesion of the layers. The optimal speed should be as fast as possible for your 3D printer without compromising print quality too much. This 3D model will help you determine what speed will be optimal for your particular case.
To optimize print speed, this parameter is usually divided into several sub-parameters:
- Outer Wall/Shell 3D Print Speed : This parameter controls the print speed of the outer perimeter of the model. Usually it is slightly reduced to improve the surface quality.
- Inner Wall/Shell 3D Print Speed : This parameter controls the print speed of the inner perimeter(s) of the model.
It is usually the same as the overall print speed to reduce print time while maintaining durability.
- Infill 3D Print Speed : This parameter controls the infill print speed of the model. This is usually the same as the overall print speed to reduce 3D printing time while maintaining strength.
- Top/Bottom 3D Print Speed : This setting adjusts the print speed of the top and bottom of the model. Usually it is slightly reduced to improve the surface quality.
Travel speed (idle)
Travel speed controls how fast the print head moves when it is not extruding plastic. Increasing the movement speed can save a lot of 3D printing time, but increasing it too much can lead to many defects, including misaligned layers (and therefore 3D printing failure).
To determine the optimal idle travel speed for your printer, print this test pattern at various travel speeds, starting at 100 mm/s and working up in increments of 5 mm/s. Continue to increase the speed if the surface quality is acceptable, and decrease if the 3D print quality is deteriorating. Pay attention to defects such as mismatched layers.
Retract Speed
Retract Speed controls how fast the 3D printer pulls material back before moving. This setting is critical for reducing material waste and improving 3D print quality. Too slow and you may be left with unsightly threads and blemishes on your models. Too fast and you can get excessive material wear on the extruder drive gear, resulting in voids.
To determine the optimal retract speed for your 3D printer, print this test model at various retract speeds, starting at 25mm/s and adjusting in 5mm/s increments. Pay attention to the remnants of plastic in the form of a web, stretched between the spikes of the model. The ideal retract speed should be the maximum value that minimizes these artifacts without deforming the material in the feed mechanism.
To better tune the retract speed, this parameter is usually divided into two additional parameters:
Retraction Retract Speed : This parameter controls how fast the retraction (actually pulling the thread back) occurs. This is usually the same as your overall retract speed and is set the same way.
Retraction Prime Speed: This setting controls how fast the filament is re-feeded after the initial retraction in preparation for further printing. Increasing this speed will result in shorter 3D printing times and fewer defects due to prolonged exposure to heat on the plastic. However, increasing it too much can also cause the newly fed media to not heat up enough before printing resumes. For most cases, this setting should be left the same as Retraction Retract Speed.
To learn more about reducing retract speed defects, see our separate retract speed tuning guide.
Walls, infill and layer height
The speed of your 3D printer is not only affected by "speed". It is also significantly affected by how much and how thick plastic is extruded onto each layer of the 3D model. These settings are incredibly detailed, so we'll only cover general information about how each of them affects 3D print speed.
- Walls : The wall setting specifies how many perimeters of plastic are extruded to form the outline of your part. Increasing the number of layers increases the strength of the part, but also increases the 3D printing time.
- Infill : Infill is an internal structure designed to save material when 3D printing the interior of 3D models. The infill pattern will slightly affect the speed of 3D printing, while the density of the infill will significantly change the print time. Higher infill density increases part strength, but also increases print time.
- Layer Height : The layer height greatly affects the speed at which your parts print. The higher the layer height, the thicker each layer of your 3D models and therefore the faster they will be completed. Adjust this depending on what print resolution you need.
What is retract in 3D printing. Calibration and Adjustment
Retract is the process of pulling the filament back into the nozzle of the 3D printer before moving the extruder between the printed surfaces. This reduces the pressure in the nozzle and prevents the extrusion of molten plastic at the moment of "idle" movement from one point to another.
You can enable retraction in the slicer. This parameter tells the extruder to draw the filament the specified length back into the nozzle at the specified speed. When the material is slowly drawn into the nozzle, the chance of seepage is greatly reduced. If you make ideal retract settings in a 3D printer, then you will never see any stripes, spots or smudges on the grown model. Favorit 3D service center engineers and specialists have accumulated vast experience in setting up and customizing various FDM 3D printers. If you have any questions or need help setting up print settings, please email [email protected] or call +7(473)295-93-49 and we will be happy to help you.
In the image you can see what the printed model looks like without retraction.
What Retract is for in 3D printing
This option in the 3D printer greatly helps with melted filament leakage and poor surface quality. To all of the above, we can add one more positive aspect of the retract. As the extruder moves from one surface to another, the retraction raises the nozzle slightly in the Z-axis (most often by 0.2 mm) and thereby reduces the risk of the nozzle tip hitting the already printed elements.
We tried to make this manual as clear as possible and take as many photos as possible to make it clear how much the retract setting affects the 3D printing result.
The photo below shows the difference between printing without retraction (left photo) and printing with calibrated retraction (right).
How to turn on the retraction
In the last article, we dwelled on the Cura slicer in detail.
If you are using a different slicer, such as PrusaSlicer or Simplify3D, then the retraction setting will be slightly different, but the setting principle will remain the same.
We'll use Cura as an example. Open the slicer, go to the settings section and open the retraction options menu. If you have not yet enabled this mode, press the button "Enable retraction" .
Please note in advance that in this article we describe the instruction for retraction calibration for beginners, i.e. we will only check the correct temperature of the print and change the length of the filament retraction. Other parameters, such as speed, will not be considered here. We recommend starting with a speed of 50 mm / s no more. Any cheap extruders, as well as high-quality ones, can cope with this speed. This speed is the benchmark for filament retraction.
Be sure to check the print temperature, it must correspond to the temperature recommended by the manufacturer (as a rule, it can be found on the packaging with plastic).
Before calibrating, I recommend that you determine the optimum print temperature for your printer using the "Temperature Tower". The temperatures shown here are typical for most PLA manufacturers. If you use a different type of filament, then you need to change the operating temperature, for example, for PETG it will be 235°C, etc.
Before calibrating, you need to find out if you have a direct type extruder ("direct drive"), then it is recommended to start the retraction length from 0.2 mm .
If the printer is equipped with a Bowden extruder (filament fed through a PTFE tube), it is recommended to start with approximately 2 mm .
How to calibrate the retraction
1. Download and print the test model
Download the special calibration model from the link below. This is a fairly popular version, so keep it for yourself.
|
Download retract calibration model (Thingiverse.com) |
When the download is complete, find the downloaded file (by default it is the "Downloads" folder)
Unpack (unzip) the file.
open the folder and find the file four_square_cons.stl . Run this file in your slicer (Cura in our case).
Now check your slicer to see if you have active retraction. Then click on "Cut" and slice the model.
Click "Save to file" and copy to SD card or flash drive. Then send the model to the 3D printer.
2. Evaluate the printed model
It is very important to first evaluate the current retraction settings on the printed model.
The photo below shows that the quality of the model turned out to be very deplorable.
The model is printed from PLA plastic, which usually has no problems with threading. The photo shows that in addition to the threads, thicker tails are observed, this indicates that the plastic outlet is not configured correctly.
A typical error is insufficient length of thread rollback or too low retraction speed. All these settings need to be adjusted.
Therefore, it is very important to print a test model and make a correct assessment for further adjustment of the retract settings.
3. Adjust the length with the current temperature.
The photos below compare several models printed with different retract lengths.
Only parameter "Bend length" was changed in the settings - from 2 to 6 mm. The rest of the parameters were not changed.
If the thread remains at any value of the withdrawal length, then it is necessary to adjust the printing temperature .
3.1 Branch length - 2 mm.
3.2 Blood length - 3 mm
3.3. Dishasis length - 4 mm
3.4 Lifting length - 5 mm
33
3.

As you can see in the images above, problem threads still appear. Changing only the retraction length did not help.
Therefore, other parameters must be changed, such as temperature or retract speed.
4. Test at lower temperature. Decrease by 10°C.
Since I am printing at a fairly high speed (160-200mm/s), the temperature I use is much higher than with standard printing at about 4-40mm/s.
In any case, if the test with retract adjustment at normal temperature is not successful, I recommend lowering the temperature by 5-10°C.
The photo below shows models printed with 2 and 3 mm retraction / at 205°C. As we can see the quality has improved a lot, but the threads are still visible.
4.1 Branch length - 2 mm.
4.2 Branch length - 3 mm.
4.

Compared to the first test, where the standard temperature is set, we see a significant improvement in print quality.
However, the thread is still present on the model, so we will reduce the temperature even more.
5. Test at a lower temperature. Lower it another 10°C.
If threading still persists, reduce temperature by 5 -10°C . Here I went from 205°C to 195°C.
We see that the resulting models have finally reached their level of quality (in terms of retraction).
Unfortunately on this 3D printer I can't avoid fine filaments due to the use of the Volcano hotend, higher print speeds and a long Bowden tube (The distance between the nozzle and the extruder is about a meter).
5.1. Branch length - 2 mm.
Branch length - 3 mm. 5.3.
Branch length - 4 mm.
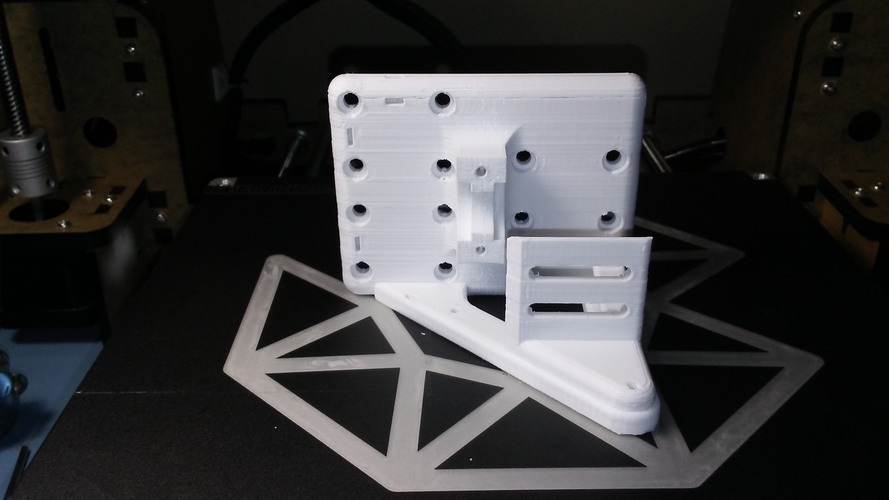