3D printer project runway
Cubify 3D Printing Struts the Catwalk of Project Runway
0Shares
It’s been almost two years since Justin LeBlanc’s 3D printed wares graced the catwalk on Lifetime’s hit series, Project Runway. Since then, a countless number of designers have found ways to integrate the technology into their clothing, shoes, and accessories. But, given the inherit 3D modeling skills necessary to create such pieces and the time it takes to 3D print such elaborate pieces as Dita Von Teese’s 3D printed gown, the tech just wasn’t quite fit for a true Project Runway challenge. Tonight, the show proved, however, that they could make it work, but that they’d need 3D Systems’ new Fabricate line of 3D printed textiles to do so.
As 3DPI’s Tyler Koslow learned first-hand at a 3D Systems’ workshop in New York City, the Fabricate line is meant to enable broad access to 3D printed fashion by blending 3D printed textures with traditional fabrics. Users begin by 3D printing PLA plate layer, before applying a bit of glue and a swatch of specialty fabric and resuming the printing process, using one of a handful of patterns on Cubify.com. The resulting textile can then be sewn into any piece of clothing the way that any fabric might, allowing any fashion designer to take advantage of futuristic, Bitonti or van Herpen-type, 3D printed designs.
On tonight’s episode of season 14 of Project Runway, the five remaining contestants were challenged to implement Fabricate textiles into their final pieces, inspired by an iconic New York City bridge. When introduced to the technology, some were baffled (“I don’t know what that means. I don’t even own a 2D printer.”) and some were stoked (“I love 3D! I walk around and the world is in 3D!”). After being paired with some 3D modelers from 3D Systems, the designers were able to sketch their ideas for 3D printed textiles, which the 3DS crew transformed into printable designs. Then, with a suite of Cube 3D printers back at the studio, they 3D printed their textiles and incorporated them into their final looks.
I don’t want to spoil the winner of the challenge for you here, but I can say that some of the results were stunning.
Ashley Nell Tipton: Manhattan Bridge. Photo credit: Greg Endries.Edmond Newton: Manhattan Bridge. Photo credit: Greg Endries.Candice Cuoco: Queensborough Bridge. Photo credit: Greg Endries.Though my regular top contestant is Merline Labissiere, my personal favorite look tonight was Kelly Dempsey’s Brooklyn Bridge-inspired piece, definitely her best work of the season. Her 3D printed appliqué was inspired by the bridge’s bricks, complementing the texture of her wild crocodile skin dress.
Kelly Dempsey: Brooklyn Bridge. Photo credit: Greg Endries.Whether you caught the episode or not, you can actually 3D print your own version of some of the contestants’ designs at home! As part of the Fabricate Project Runway collection, textiles from tonight’s show are now available for purchase online and 3D printing at home, so that anyone can combine their own designs with the contestant’s look. The winning contestant got to take home a Cube 3D printer and a package of Fabricate supplies.
As a personal fan of the show and, you might have guessed, a heavy 3D printing enthusiast, this episode was the highlight of the entire season, jumping just ahead of Justin’s 3D printed accessories from season 12 and that time that Santino did an uncanny impression of Tim Gunn in season 2 (my wife and I named our cat after Andrae Gonzalo for this impression alone). Head over to Cubify to learn more or check out the 3D printed textiles created by Project Runway season 14’s final five.
Michael Molitch-Hou
Michael Molitch-Hou previously served as Editor-in-Chief of 3D Printing Industry, he is now the Editor of Engineering . com's 3D printing section. He has covered additive manufacturing technology day in and day out since 2012 and has hundreds of article to his credit. He is the founder of The Reality Institute.
3D Printing Hits Project Runway as Designers Look Toward NYC Bridges for Inspiration - 3DPrint.
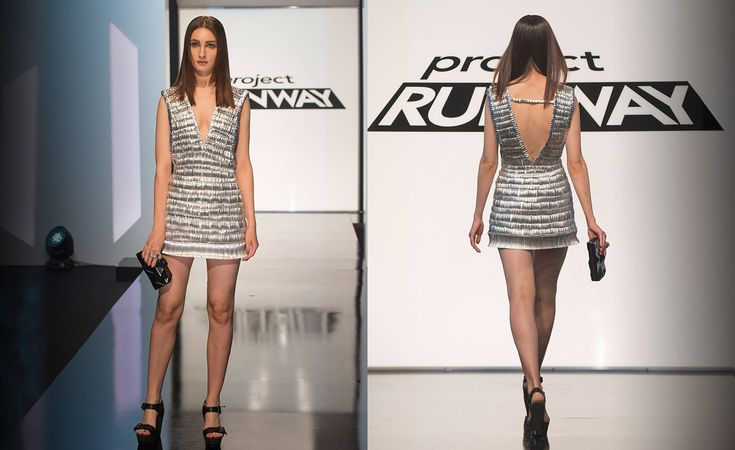
The world of fashion is one that intermingles with that of art and design, and presents the same infinite opportunities in creativity. Often the same tools are used too, but with very different results, as for fashion they are being used more delicately and thoughtfully to accentuate the human body. When a fashion designer turns to the 3D printer, the results are usually very different and exciting.
While 3D printing is used in many very serious applications, from the medical industry where in fact it is sometimes responsible for helping to save lives, to helping further missions and even future colonization into space–it’s always fun and inspirational to take a break and check out what’s going on with 3D printing and fashion. While at first the Dita von Teese 3D printed dress was the most well-known, and indeed also the benchmark for 3D printing in apparel, 3D printing has begun to hit the mainstream so much that we now see a continual stream of dresses, shoes, and accessories hitting the runway.
So, it’s no surprise that the powers to be at Project Runway presented this season’s charges with their own 3D printing lab to get busy in; after all, these budding designers wouldn’t be very well-rounded without knowledge of the technology in regards to fashion. Using a very industrial slant, the group was instructed by Tim Gunn to use the famous bridges of New York City as their inspiration for design.
The Cube 3D printers did seem to be an initial source of curiosity, anxiety, and excitement, however, for the five designers left in this season’s challenge who were instructed to come up with something amazing for the 3D printing avant-garde challenge.
After initial murmurings regarding what the heck 3D printing even is, the show brought in Annie Shaw, Creative Director of 3D Systems. She informed them that her team would lead them through creating designs, 3D files, and then in 3D printing pieces that would come out in approximate five-inch squares. With a budget of $200, the designers had a mere two days to complete their work using the new 3D Systems Fabricate line of 3D printed textiles to do so. The line, Fabricate, meant only for the Cube 3D printer, is a logical progression for the meeting of minds in 3D printing and fashion as it allows for a mixture of 3D printing materials and traditional textiles such as leather.
With the project scope offering the group much inspiration for different motifs and angles dreamt up from looking at the Queensboro Bridge, the Manhattan Bridge, and the Brooklyn Bridge, they came up with dresses, ponchos, and bracelets. Enthusiasm for both digital design and the 3D printing process grew exponentially as the show progressed. All of the designers experimented with and produced 3D prints showing off texture, shape, and enviable originality. One designer was the standout, however, with her obviously architecturally inspired dress, rocking an angular and brown crocodile skin type piece. [Spoiler for the episode below!]
“Congratulations. You are the winner of this challenge.”
With the words that every designer on Project Runway dreams of hearing, Kelly Dempsey was lauded for her efforts in 3D print on this week’s episode. She also ended up with a Cube 3D printer–and all the trimmings from 3D Systems–as a reward for her efforts, which duly impressed the judges, who as we are all aware, have extremely high expectations. It’s always unpredictable as to which way things are going to go on the show, however–and we all hold our breath waiting to see who the winners will be–and who will go home.
Check out Dempsey’s post-win interview:
“I’m so excited. I don’t even know what I’m going to do with this thing,” said Dempsey, tongue-in-cheek, regarding her new Cube 3D printer. “I’m going to have like a 3D bedroom by the end of the year. I’m going to 3D my bed, my mirror, and my car…that I don’t have.”
This is not the first time 3D printing has been used on Project Runway, but it is the first time it was required as a group challenge, certainly exposing not only the designers to the technology, but all of the viewers around the world, whether catching it on prime time or streaming it later. The designers really warmed up to the technology and were able to produce some wonderful pieces right off the bat, leading us to hope they keep the Cubes around.
Let us know your thoughts on Project Runway utilizing 3D Printing in the Project Runway forum thread on 3DPB.com.
Stay up-to-date on all the latest news from the 3D printing industry and receive information and offers from third party vendors.
Tagged with: 3d printed accessories • 3d printed dress • 3d printed fashion • 3D printed fashion contest • 3d printed fashion design • 3D Printing Challenge • 3d systems • cubify • cubify cube • Cubify Fabricate • Fabricate • industrial 3d printing • Project Runway
Please enable JavaScript to view the comments powered by Disqus.
A 3D-printed prototype of a landing pad for the Moon was tested / Sudo Null IT News
It is almost impossible to imagine space exploration without the use of local resources. Lunar base projects were buried under the surface, sprinkled with soil or surrounded by printed walls. But less attention was paid to the buildings of the lunar cosmodrome - at best, flat areas are drawn in the illustrations. They will have a minus - the engine exhaust will corrode the surface and raise dust. To address these potential challenges, a team of students from ten U.S. universities and colleges, with support from NASA and 3D printing company ICON, designed, built, and successfully tested a large-scale prototype of the Lunar PAD airstrip.
In the summer of 2019, a team of students from the NASA L'SPACE Virtual Academy won a round of the 12-week NASA NPWEE Technology Concept Proposal course and received funding to develop their concept for protecting lunar landers from dust using robotic construction. The goals of both L'SPACE and NPWEE are to expand the pool of high-quality proposals of new concepts and technologies that can then be useful to NASA. In 2020, the team submitted a revised concept to an online technology readiness review and received funds to build and test a scale model. After spending hundreds of working hours consulting with NASA experts, the students went from idea to implementation of a model of the potentially important task of creating a safe reusable landing site for the Moon. In autumn, a scale model was built at Camp Swift, Texas, and successfully tested by a geophysical rocket engine in early March.
The project, originally called the Dust Devil ("dust whirl"), is eventually called the Lunar Plume Alleviation Device ("Lunar device to soften the exhaust") or, for short, Lunar PAD (playing on what that in English "pad" also means "a platform for launch / landing"). Structurally, the Lunar PAD consists of two levels: the upper one is a flat platform with small slots for exhaust gases to drain.
Ready site with test rocket engine installed, photo ICON The lower level combines load-bearing structures and flues for exhaust gases to the sides. A feature of the project is the use of 3D printing. First, a 3D construction printer forms a frame, which, as is often the case in additive manufacturing, uses complex surfaces and looks aesthetically pleasing.
The printed frame is then filled with filler. The test mock-up used a cement-based material, but for lunar conditions, it would be logical to produce a hardening or sintering regolith building material in situ. The structure built is strong enough to withstand the takeoff and landing of the lunar modules, and produces less dust by diverting engine exhaust into the gas ducts.
Even at the construction stage, sensors were installed in the model to determine temperatures, loads and gas flow. In early March, a geophysical rocket team from Texas A&M University delivered a solid rocket motor to a test site. It was installed above the site, launched and looked at the information recorded by the sensors. The tests were successful - the Lunar PAD pad successfully withstood the takeoff / landing simulation, the data obtained do not contradict the calculated ones.
Inspection of the site after testing.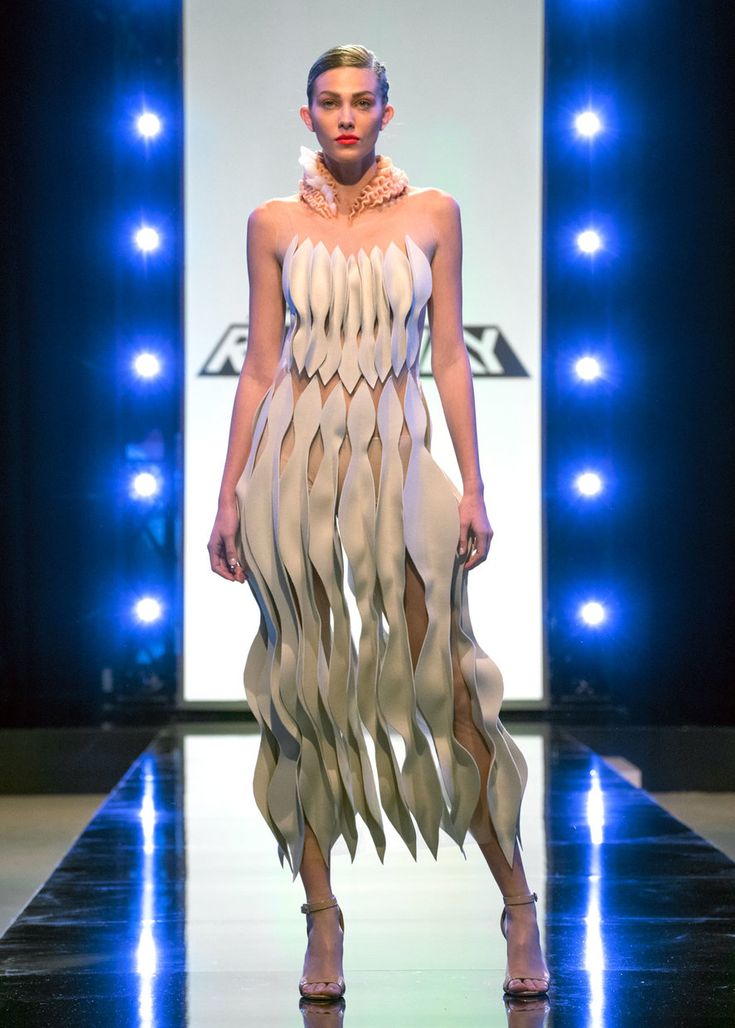
The project has already received its first scientific publication in the AIAA SciTech Forum materials, and a very diverse group of college and university students scattered throughout the United States can take part in a full-fledged and successful scientific and technical project, potentially in demand in future projects moon bases.
It is also interesting to note that ICON, which provided the gantry 3D printer for the project, is also 3D printing houses and other structures. The company also received a contract from NASA last fall to research and develop a construction system that could be used on the moon. Under this contract and, potentially, other space projects, a special division of the company was created. The project was named "Olympus". And it's time to redo the freshly drawn renders - thanks to the efforts of the students who created the Lunar PAD, the depicted landing pads already look outdated.
Fake history and 3D printing in the jungle
From time to time, news appears on the Internet that another lost temple of some Aztec god has been discovered in the jungle. And even reliable photos and beautiful legends are given.
I'll tell you how this business works (sometimes).
There are people who have a lot of money, so much that they cannot legally spend it.
Over the past few years, offshore wool, and many banks prefer to get rid of problem customers. It’s just that the account owner receives a letter that “they say your account is closed and take your millions within a month.” No reason given. I know this firsthand. There was a case that my account was closed just because of too frequent flights between countries. And this is happening all over the world, not only with the Russians. . In general, the night is dark and the fat must be hidden. By the way, remember that the rise of bitcoin magically coincided in time with the nix of Panamanian offshores? The ability to save big money today is no less difficult task than the ability to earn it.
An attempt to hide from offshore to China also failed, many fell for it, but in the end the Chinese hid it and now do not give it back under any pretext.
I recently received an offer to 3D print some buildings in the deep jungle.
Upon arrival at the place, I was surprised to find freshly built incomprehensible antique structures in the form of pyramids. The first thought that came to mind was that an entertainment complex was being built here, but after a while the specifics of the project became clear: an ancient temple was being built on the sly in the jungle. The fact is that in a tropical climate, in just a few years, any building is overgrown with moss, lianas and other vegetation so that in 10-15 years it will be almost impossible to distinguish it from antique buildings outwardly, especially if concrete is aged with special solutions and some lianas are planted in such a way so that they penetrate buildings through windows and doors.
By the time the 3D printer was delivered, 50% of the antique buildings had already been made in the traditional way. But the task was to print a few more. The main task was to equip a zone for receiving tourists, i.e. print all sorts of small hotels. During this, trees were cut down in parallel for the construction of a small runway, since all this is located in the depths of the jungle, and driving a car takes a lot of time.
From the point of view of normal investments, such projects look, to put it mildly, risky, because to invest decent money, build, and then wait another 10-20 years for everything to grow, and only then start accepting tourists, in my opinion, this - masochism ... Since during this time the money was invested (but they do not work), then, logically, the profit is lost. This is only from the point of view of ordinary investors in a normal capitalist system. If we consider that this is an investment that will bring profit to the family, children, grandchildren and great-grandchildren for another 100 years, or even more, then this decision is simply brilliant. In any case, this is more reliable than investing in an incomprehensible mystical crypt that can evaporate within a second. I have seen everything well organized, no doubt, so they can arrange at the right time the right media coverage, the supply of tourists and the right examination of authenticity. For a good amount, historians will present this discovery as it should (there were historians and archaeologists at the construction site), they will take samples from the building in the right place and the dating will be correct, and other very curious 'wrong' researchers will simply not be allowed closer than 100m, and certainly will not be allowed to take samples. There is tight control. And a few years after the opening, no one will ask questions, people will just go to see and relax, finding an advertisement on the Internet or in a travel agency without really delving into it ... after all, the primitivization of consciousness is in full swing.
According to the contract, my initial task was to bring equipment and teach printing methods to local workers, but as usual, everything dragged on and I had to work harder, to implement, so to speak, some ideas. Initially, according to the project, hotels and houses were quite standard, and with the help of a 3D printer, we managed to print more interesting, from the point of view of architecture, various bungalows, wigwams, gazebos, etc. for the same money. The work was, of course, interesting, but the climate is terrible, and it’s dangerous all the same ... everything in the jungle is trying to devour you. At night, there are such sounds that chill the blood, and you can forget about sleep for the first week. In the nearest thickets, someone constantly ate someone. I will never forget how I once dozed off on a hammock. I knew it wasn't a good idea, but since you have to control the printer and watch the monitor during the night, you can't sit in a chair for long. I pulled a hammock 5 meters from the printer, put a monitor in front of my eyes and, under the quiet lulling buzz of steppers, sailed away to communicate with Morpheus ... I feel through a dream that someone is staring, opened my eyes, and at 30 cm, right in front of my nose, my muzzle a monkey that studies me.
I started screaming out of fear and surprise, she got scared because of my scream and also started yelling, only even louder, and her teeth are not sickly, I’ll tell you .. I’ll definitely never be able to sleep on a hammock again ... As soon as the locals learned manage the equipment normally, and we unpacked the first hotel and several houses, I hurried to get away from sin as quickly as possible.
Unfortunately, according to the terms of the contract, it was strictly forbidden to take pictures of anything, I won’t be able to show pictures of the work for many years to come. Nevertheless, it seemed to me that it would be interesting for someone to know that there is such a business as fake history on the scale of the construction of complexes, and not just in the form of fake paintings.
Life is full of surprises. And 3D printing technology is really changing the world.
On the video is the control unit for the LAByrinth and StroyBot printers that were used to print objects.