3D printer microfluidics
3D printed microfluidic devices: enablers and barriers
Sidra Waheed,ab Joan M. Cabot,ab Niall P. Macdonald,ab Trevor Lewis,b Rosanne M. Guijt,c Brett Paullab and Michael C. Breadmore*ab
Author affiliations
* Corresponding authors
a
Australian Centre for Research on Separation Sciences (ACROSS), School of Physical Sciences, University of Tasmania, Hobart, TAS, Australia
E-mail:
mcb@utas. edu.au
Fax: +61 3 6226 2858
Tel: +61 3 6226 2154
b ARC Centre of Excellence for Electromaterials Science (ACES), School of Physical Sciences, University of Tasmania, Hobart, TAS, Australia
c Australian Centre for Research on Separation Sciences (ACROSS), Pharmacy School of Medicine, University of Tasmania, Hobart, TAS, Australia
Abstract
3D printing has the potential to significantly change the field of microfluidics. The ability to fabricate a complete microfluidic device in a single step from a computer model has obvious attractions, but it is the ability to create truly three dimensional structures that will provide new microfluidic capability that is challenging, if not impossible to make with existing approaches. This critical review covers the current state of 3D printing for microfluidics, focusing on the four most frequently used printing approaches: inkjet (i3DP), stereolithography (SLA), two photon polymerisation (2PP) and extrusion printing (focusing on fused deposition modeling). It discusses current achievements and limitations, and opportunities for advancement to reach 3D printing's full potential.
- This article is part of the themed collections: Lab on a Chip Recent Review Articles, RACI100: Celebrating Australian Chemistry, 3D Printing and Lab on a Chip 2016 Most Downloaded Articles
Researchers open up low-cost open-source microfluidics 3D printing
0Shares
A team of researchers from the University of Bristol has developed a novel low-cost and open-source 3D printing process for producing microfluidic devices.
A microfluidic chip is a set of micro-channels etched or molded into a material, such as glass, silicon, or in this case, PolyDimethylSiloxane (PDMS), which are connected to the outside world by inputs and outputs pierced through the chip. Through these holes, liquids or gases can be injected and removed by external active or passive systems for biomedical field applications such as laboratories-on-a-chip (LOC), cell biology research, and protein crystallization.
Requiring only simple domestic equipment and a standard desktop 3D printer, and having been developed in free-to-use software, the researchers’ process reduces the cost and complexity of fabricating microfluidics to make the field more accessible.
The team believes their approach could drastically lower the threshold for research and education into microfluidics while making the rapid prototyping of affordable LOC diagnostic technology possible at the point-of-care (POC).
Proposed microfluidic master mould fabrication process.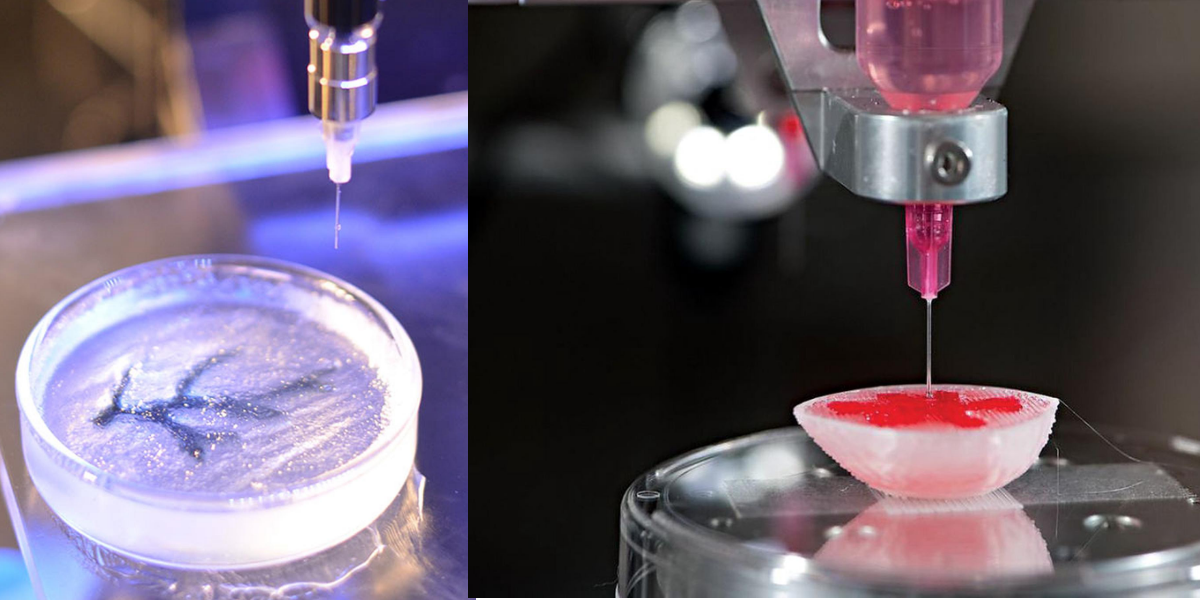
3D printing and microfluidics
For decades, LOC technology has been heralded to answer a range of biological, chemical, and healthcare challenges. However, it is yet to see meaningful adoption and deployment due to the cost both at the research level and the mass-manufacturing stage.
LOC technologies are supported by the field of microfluidics, which is seeing an increasing exploration of 3D printing techniques to advance the technology and increase its accessibility.
In 2018, researchers from New York Genome Center and New York University developed an open-source 3D printed droplet microfluidic control instrument which was reportedly up to 200 times cheaper than other comparable instruments. Designed to identify and target the correct cells to treat diseases such as Rheumatoid Arthritis, the instrument could be obtained and assembled for around $600.
Elsewhere, a process has been developed to 3D print microfluidic devices integrated with fluid handling and functional components. Developed by the Singapore University of Technology and Design, the technique aimed to enable the rapid prototyping of microfluidics for LOC applications in chemical testing and cell analysis.
Most recently, researchers from UC Davis unveiled a new approach to 3D printing using microfluidics, which involved deploying a droplet-based microfluidic system to efficiently 3D print finely-tuned flexible materials. Possible applications for the technology include soft robotics, tissue engineering, and wearable technology.
Material printed with UC Davis’ new droplet-based 3D printing method. Photo via Jiandi Wan.Fabricating the microfluidic devices
The researchers began by 3D printing interconnecting microchannel scaffolds with an Ultimaker 3 Extended 3D printer using PLA, which were then thermally bonded to a glass substrate in the desired configuration to create a microfluidic device master mold.
The microchannels were designed in a range of modular patterns, with each featuring interlocking ball-socket connector ends, using Ultimaker’s Cura open-source slicing software. These ends were developed to mimic puzzle pieces. Successive modules could be arranged in any desired configuration, enabling creating more sophisticated microfluidic systems using a small number of simple modules. A key aspect of this part of the researchers’ process is that it is easy and clear to replicate for non-expert users.
The 3D printed microchannel modules were then mounted onto standard 1mm-thick glass microscope slides into the desired configuration, using the ball-and-socket connectors. The channels were then heated for around a minute to bind them to the glass with a weighted slide placed on top to prevent deforming and shrinking. After heating, the slides were partially fused and placed weighted-side down onto a metal plate to rapidly cool the weighted slide and remove it from the mold.
The master mold can be used again and again to produce microfluidic devices in PDMS. Post-printing, the master mold fabrication process can be completed in less than five minutes, allowing the method to be used for both formal and informal learning environments.
Open-source microfluidics
To ensure the proposed technique is fully democratized, the researchers developed an open-source Autodesk Fusion add-in which allows any user to design and export interconnecting microfluidic channel scaffolds for 3D printing. Using this plugin, a user can go from a microfluidic channel design to a completed microfluidic channel without requiring CAD software expertise or time and resource-intensive techniques or equipment.
Users can prototype interconnecting microfluidic channels down to 100 μm resolution in width, either through printing their own designs or choosing from a vast library of microchannel scaffolds listed in the add-in. A protocols.io instruction set has also been made available detailing the researchers’ full process, with links to the up-to-date add-in and profiles.
Using this technique, users can fabricate microfluidic devices from PDMS with only household equipment and no hazardous chemicals, thereby making microfluidic experimentation accessible to schools, hobbyists, and researchers no matter their resources. The team hopes that this approach will be adopted by researchers and educators worldwide to “help to inspire the next generation of lab-on-a-chip developers.”
Furthermore, the researchers believe their technique could pave the way for “truly affordable” LOC healthcare diagnostic testing, which can be performed at the point-of-care, through applying the microfluidic PDMS channels directly to any cleaned glass surface, such as a mobile phone screen or a car windshield.
Further details on the study can be found in the paper titled “Negligible-cost microfluidic device fabrication using 3D printed interconnecting channel scaffolds” published in the Plos One journal. The study is co-authored by H. Felton, R. Hughes, and A. Diaz-Gaxiola.
Subscribe to the 3D Printing Industry newsletter for the latest news in additive manufacturing. You can also stay connected by following us on Twitter and liking us on Facebook.
Looking for a career in additive manufacturing? Visit 3D Printing Jobs for a selection of roles in the industry.
Featured image shows proposed microfluidic master mould fabrication process. Image via University of Bristol.
Tags A. Diaz-Gaxiola H. Felton lab-on-a-chip Microfluidics New York Genome Center New York University R. Hughes Singapore University of Technology and Design UC Davis Ultimaker Ultimaker 3 Ultimaker Cura University of Bristol
Hayley Everett
Hayley is a Technology Journalist for 3DPI and has a background in B2B publications spanning manufacturing, tools and cycling. Writing news and features, she holds a keen interest in emerging technologies which are impacting the world we live in.
3D printing helps to create record thin microfluidic channels
A team of scientists from Brigham Young University (USA) proposed a 3D printing method to create microfluidic laboratories-on-a-chip with record thin channels. Thanks to DLP (“digital light processing”) technology and careful selection of the printing material, the authors achieved a 100% yield when creating channels with a cross section of 18 × 20 square microns - 10 times smaller than what has been possible so far. The study was published in a specialized journal on microfluidics Lab on a Chip .
Microfluidics is the field of study of the behavior of fluids in micron-thick channels. Due to their small size, microfluidic devices make it possible to carry out complex multi-stage manipulations with liquids and objects placed in them (cells, bubbles, particles, drops) using chips several millimeters in size. Hence the name of the most popular microfluidic devices - "laboratories on a chip".
Compared to macrosystems - the usual "pipes" and relatively thick (mm) capillaries - in microfluidics, the behavior of the liquid changes somewhat. For example, viscous resistance and surface properties play an important role. A separate problem is the production of thin channels, because, as in microelectronics, each chip consists of numerous "tracks" (channels for liquids) with "crossroads", valves and sections with a special shape and relief of the walls. nine0005 Soft lithography methods are traditionally used to create microfluidic systems, but 3D printing has also gained popularity recently. However, until now, she lacked the accuracy and resolution to seriously compete with lithography. The authors of the new work created their own modification of a commercial 3D printer and selected a specific material for printing, as a result of which they were able to achieve a record resolution.
Wall materials in microfluidics are usually polymers, which are formed from a liquid solution during photopolymerization. To do this, each layer applied during printing must be irradiated with light with a certain wavelength. In this case, the illuminated sections of the layer will freeze and become walls, and the unlit sections will then be washed away, and in this place there will be a “void”, that is, the channel itself. In order to accurately illuminate only the required areas of the layer, the authors used the method
DLP
, which is widely used in projectors, both home and industrial. These devices have a system of prisms and mirrors that creates the necessary sequence of pixels in each image. The light source in the work was an LED with a wavelength of 385 nanometers, which is lower than the commonly used 405 nanometers - this allowed us to consider a larger range of materials suitable for printing.
The authors paid special attention to the light-absorbing additive, which solved one of the main problems of 3D printing of microchannels. Imagine that the printer has just printed a layer that has a void (channel) in it, and the next layer should be solid (top cover, for example). When illuminating a "pixel" located above the void, the light can penetrate the previous layer, resulting in a wall instead of a void. To avoid this, a photo-absorbing additive is added, which prevents light from penetrating further than required. nine0005 The authors selected the photoabsorbent from 20 candidates, which were compared according to 6 criteria: solubility in the base material, absorption spectrum (compatibility with a light source), critical temperature, mechanical strength after polymerization of the sample, fluorescence ability (parasitic and unnecessary in this work) and the print resolution provided, i. e. the depth of light penetration. After such selection, scientists left only one substance - NPS (2-nitrophenyl phenyl sulfide).
In order to test the finished method, the authors printed several typical microfluidic systems: a serpentine, as well as a channel with a large vertical aspect ratio - 25 microns wide and 3 millimeters high. Scientists also estimated the width of one "pixel" in the print plane - 7.6 microns, and the minimum achievable channel cross section was 18 × 20 square microns. The article notes that lithography methods can also achieve lower values, but they lack many of the possibilities of three-dimensional printing, for example, creating full-fledged 3D devices in which the channels do not lie in the same plane. nine0008
The range of applications for 3D printing today remains very wide: from
microfluidics
and printing
organs
to construction
buildings
. The range of materials used is just as great: in addition to plastic, systems for printing
with metal
or
with glass
are known.
Taras Molotilin
Found a typo? Select the fragment and press Ctrl+Enter. nine0008
Researchers 3D printed unique liquid microchannels
1992
Bookmark
These fluid channels can automate production of diagnostic tools, sensors and analyses, used for various medical tests and for other applications, writes eurekalert.org with link to Science Advances. nine0008
The study was conducted by scientists from the University of Minnesota in cooperation with the Center for Soldiers Command Development combat capabilities of the US Army.
The team printed these structures on a curved surface for the first time. on a 3D printer, and this is the first step to ever print them directly on the skin to analyze bodily fluids in real time.
Microfluidics is a rapidly developing field involving liquid flow control on a micron scale (one millionth meters). Microfluidics is used in a wide range of fields, including environmental sensing, medical diagnostics (e.g. COVID-19and cancer), pregnancy test, screening, drug delivery and other biological assays.
The value of the global microfluidics market is currently valued in the billions of dollars. Microfluidic Devices usually produced in a controlled environment clean room with using a complex multi-step technique called photolithography. In the process of making silicone fluid flows over the patterned surface and then hardens so that the patterns form channels in the hardened silicone sheet. nine0008
In this new study, microfluidic channels are created in one step by 3D printing. The team used a manufactured order 3D printer for direct printing of microfluidic channels on surfaces in an open laboratory environment. The channels have a diameter about 300 microns - about three times the size of a human hair (one hundredth of an inch). The team showed that the fluid flow through the channels can be controlled, pumped and redirected from with a series of valves.
Printing these microfluidic channels outside of cleanrooms can provide robot-based automation and mobility in the manufacture of these devices. For the first time, researchers were able to print the microfluidic directly onto a curved surface. In addition, they have integrated them with electronic sensors for lab-on-a-chip measurement capabilities.
“This new study opens up many future possibilities. for microfluidic devices, said Michael McAlpine, professor Mechanical Engineering University of Minnesota and Senior Fellow research. - Possibility to print these devices on 3D printer outside the clean room means that the diagnostic instruments can be printed by a doctor right in their office or remotely printed out by soldiers in the field." nine0008
[Photo: ru.123rf.com/profile_luchschen]
Author Prepared by Anna Yudina
3D printer fluid channels microfluidics
Source: www.eurekalert.org
Information provided by the Information Agency "Scientific Russia".