3D printer life size person
Iron Man 3D Print: Life-Size Statue Painting Guide
Bringing home an incredible 1:1 scale 3D printed life-size statue is fantastic. Not everyone can make such a dream come true. Still, if you have a 3D printer, nothing is impossible for you. You can scale up your favourite 3D printing character! For example, Iron Man 3D print will capture everyone’s imagination and bring many positive emotions to its owner. Talented hobbyist David Maeseele is happy to show the photos of his fantastic Iron Man life-size figure that is 191 cm (75 inches) tall and talk about its creation.
If you ever dreamt of 3D printing something life-size, David’s tips can be useful to you. Explore his vision on how to 3D print a life-size Iron Man statue and learn the secrets of painting such giant projects.
Iron Man 3D Print
Many fans of Marvel Comics are fond of Tony Stark, and his fictional alter ego, Iron Man. According to the original story, this genius inventor builds a powerful suit and uses the Iron Man Mark 46 costume for performing good deeds.
The 3D printed Iron Man figure always looks impressive and is easily recognized by its red and gold colours when painted.
You can download the Iron Man 3D model STL files for 3D printing on Gambody – Premium 3D printing marketplace. 3D designer Rodman created this fantastic figurine, which you can turn into a life-size Iron Man 3D print just as David Maeseele did it.
Maker: David MaeseeleGet inspired by David’s 1:1 scale figure of Iron Man and learn more about how to 3D print a life-size statue that reaches 191 cm.
3D Print Life-Size Statue of Iron Man: How to
The Iron Man 3D print created by David is pretty heavy. The hobbyist spent about 16 kg (35 lbs) of PLA, many working hours, much paint and introduced LED lights to this fantastic project.
Life-size statue by David Maeseele1. David, it is nice to meet you! Can you please introduce yourself to Gambody community? How many years have you been fond of 3D printing?
Hello, I am 43 years old, and I live in France. I am passionate about cinema, music, fishing and of course 3D printing that I have been practising for two years.
2. How popular is 3D printing in your country and hometown?
In France, there are a lot of 3D makers.
Maker: David Maeseele3. Your life-size Iron Man 3D print is fantastic! Do you usually build everything life-size? Or is it a unique project for a contest, show or personal collection?
Thank you so much.
I started printing small pieces of 20 cm (8 inches). Like everyone else, in the beginning, I found them already to be huge.
Then once I started printing a DBZ figure and noticed that I was wrong in the size. So, I went to the end of the project, and my figurine was 60 cm (24 inches) tall. Since that time, I have gained confidence, and I have been printing increasingly large figures.
Life-size head by David MaeseeleThen I made other big action figures for the movie theatre, and finally, I made this life-size Iron Man statue. I think it will be the only one in my collection because it is very expensive to have this quality.
4. Your life-size Iron Man 3D print is 191 cm tall. Can you please recollect the process of scaling up each part of the 3D model? How much time did it take you to prepare each STL file for 3D printing? Which software did you use?
I collected all the Iron Man 3D model STL files in the 3D Builder software. Then I increased the size to 755% and got the one I wanted.
I spent about 100 hours slicing all the files so that I could save printing time and material while 3D printing a life-size statue of Iron Man.
David’s video on how to 3D print Iron Man5. You mentioned that you 3D printed Iron Man files with two machines. Which 3D printers did you use?
For this life-size Iron Man figure, I used Alfawise U20 and Creality Ender-3 printers.
3D printed Iron Man parts by David Maeseele6. It would be incredible if you could please share the printing settings used on Creality Ender-3 and Alfawise U20 with hobbyists who never tried to 3D print anything life-size. Which settings worked perfectly for your 3D printed Iron Man figure?
I can’t remember the exact settings.
I know I chose to 3D print Iron Man at 0.22mm layer height, 8% infill, speed of 60 m/s, bed at 0°C and a 0.6mm nozzle.
Maker: David MaeseeleToday as I have made further progress, I think I could print at 0.32mm layer height (always with the same machines).
7. Do you remember the size of the biggest 3D printing part of this 3D printed life-size statue?
The most significant pieces were parts of the Iron Man life-size bust. I had to cut it into eight pieces.
8. Did you do test prints? And you used a piece of paper for writing down mathematic formulas. What did you count or keep track of?
I printed the Iron Man figure in 20 cm (less than 8 inches) to see if the interlocking was perfect. Then I started with the smaller pieces of the Iron Man life-size statue.
3D printed Iron Man figure by David MaeseeleI located all the parts and wrote down the times on a piece of paper so that I could organize myself.
9. You spent several weeks making the life-size Iron Man 3D print. Did you work on it every day, from dawn to midnight? Or did it occupy you a couple of hours a day?
If memory serves me well, I spent a total of 7 weeks 3D printing it.
I worked every day before I left for work and when I got home from work. As soon as a part came out, I began working on it.
Maker: David Maeseele10. How did you control the quality of each 3D printing piece to make sure the printers are doing their job well and no errors occur during the process?
I just let the machines work. I had small problems, but I caught them in post-processing.
11. How simple or challenging was the sanding, post-processing and assembly? Did you face any issues? Or was everything smooth?
For the post-processing, I only had one big problem. I was almost done, but there was a reaction of the varnish and the paint. I had to start sanding the grey and gold parts of Iron Man 3D print again. I lost one week of work because of this.
3D printed Iron Man by David Maeseele12. Which painting technique did you use while working on the 191-cm life-size Iron Man 3D print? Did it take you just one night to paint this giant model, or was it longer?
I painted the silver and gold parts of this 3D printed life-size statue in my garage and applied the varnish on them.
Then the red was done in a paint booth by a professional. I could have painted it myself, but I was afraid of having small flaws. I wanted it to be perfect. And since the paint was very expensive, I didn’t risk with the red.
The painting of the 3D printed Iron Man figure took over two days.
13. How did you pick up the right colour for red and gold? Can you recollect your painting tests?
I saw this video of Iron Man life-size model:
The life-size Iron Man figure that motivated DavidAnd I said to myself, “this is the colour I want!”
I talked to the body painter about it, and he showed me samples of colours.
Maker: David Maeseele14. Did you have to mix paints on your own to achieve the right shade?
No, I let the professional do it.
15. Did you add lights and shadows to the 191-cm Iron Man statue?
I hesitated to shade at first. But I added very light accents on the silver parts. I did them with an airbrush.
16. At which stage did you introduce LED lights inside this 3D printed life-size statue? Can you please describe this process in detail as it was your first ever experience in adding lights to the model?
Yes, it was the first experience for me. I prepared everything before painting. And after the painting, I fixed everything.
Maker: David Maeseele17. Did you make the platform for the 3D printed Iron Man figure yourself? Did you design it? Does it hold the batteries for LED lights?
I found the 3D print files on Thingiverse and edited them. I added a polycarbonate plate and LED tape.
Maker: David Maeseele18. Where do you display the impressive 3D printed Iron Man model? It looks like it requires some space.
At first, I wanted to display it in my cinema room, but it does not fit. So, the Iron Man 3D print is on display in my dining room.
19. Do you have plans to showcase your project in a museum or exhibition in your city or a nearby area?
No, because I wouldn’t want it to be damaged.
Iron Man 3D model printed by David Maeseele20. How do you think, can a hobbyist 3D print a life-size statue at home? Or is a big workshop a must for such giant projects?
Not everyone can do it. You have to have special tools for post-processing. It also takes much place to paint it. Besides, it makes dust.
21. Which life-size statue are you working on now?
I have no current project at the moment. I just made some small figurines that can be found on Instagram (@davidmaeseele) or my YouTube channel:
David’s YouTube channel22. Thank you so much for your time! Is there anything else you would like to say to Gambody readers?
Thanks to you for this interview.
To make great prints, be patient and do a lot of research. Have a good print, everyone!
We hope you love David’s 3D printed life-size statue as much as we do. This Iron Man 3D print is a fantastic one! It shows that you can scale up the highly-detailed 3D print files found on Gambody – Premium 3D printing marketplace and create impressive figures. Make sure to join Gambody community on Facebook to let other hobbyists adore your giant and regular 3D prints as well as miniatures.
(Visited 10,076 times, 1 visits today)
Author
Life Sized 3D Printed Models of Yourself!
0Shares
This mother’s day, there was a rather eerie deal that was going around as a rather zany Groupon deal. This deal claimed that if you were willing to spend around thirty thousand dollars, you would have gotten the chance to send a one of a kind gift to your mother- a life sized version of herself, custom 3D printed just to see that smile on her face. We are not quite sure whether mom is going to beam at you or faint in your arms, but apparently, two 3D printing Startup Company was smitten by this wild yet expensive idea. They now run their own service which prints life sized models of people, only at a price tag of $3000.
This might still be a considered as a wild idea by some, but this has been made possible, and is actually much more reasonable. Thanks to the joint initiative of design firm Voodoo Manufacturing and Body Labs based in New York, the companies found out that they too could create life sized and realistic models of actual people at a cost much less than that outrageous $30,000 sum. With the help of innovative 3D scanning and 3D printing, Body Labs facilitates this idea. A demonstration of how these life sized 3D printed models were made was given by Jonathan Schwartz, Co-founder of Voodoo Manufacturing. He did so by 3D scanning his own body which was later 3D printed into eighty eight different segments, to be reassembled into an uncanny, life sized Jonathan Schwartz model.
Situated in Brooklyn, New York, Voodoo Manufacturing’s very own factory is where the individual 3D printing of the parts was done; that too with the help of 150 MakerBot 3D printers. The company admits that they use desktop 3D printers instead of industrial sized ones; hence it is not possible to print out a life sized human being in one piece. In order to solve this problem, the body model was separated into 88 pieces which are small enough to be printed out of a single desktop 3D printer. These were all individually prepared for printing with the help of the company’s in house cloud slicer. Also, there was absolutely no need to manually prepare the 88 different files; the company could offload the computing of these files to the cloud, which made the process faster and hassle free.
A significant advantage of dividing the portions instead of printing out an entire model in a single big printer is that, the printing of all 88 components can now be streamlined across 88 different printers, which is helping to speed up the process. This rapid prototyping is bringing down manufacturing time to 30 times lesser compared to a printing a single model. This is why the entire 3D printed replica can be printed out in just under a day, taking a total 14.7 kg of plastic and 623 printer hours to get the whole thing printed.
Body Labs ensures that the 3D modeling and scanning are nothing like the traditional 3D scanning technologies. Their advanced system of scanning is an incorporation of research from Germany and the US. Once these scans are generated into 3D models, there is scope to make the figures animated and capable of moving at will.
The entire process begins with a body scan in 3D. For this particular purpose, the idea is to produce a scan as a 3D point cloud, digitally representing the object that is being scanned. The scanner then collects the XYZ coordinates of the physical points of the body in three dimensional spaces. Hence, the computer recognized the position of our limbs with the help of some points in space. After obtaining the 3D scan, these collections of three dimensional points are then processed by Body Labs. This is done using their statistical model which combines machine learning and the world’s most accurate database containing human pose and shape. The resulting products are what are called the ‘body models’.
These new capabilities to scan in 3D have opened door to a number of opportunities in terms of custom model designing. The US military has even teamed up with Body Labs to perform research and create a giant database of soldier’s body measurements, in order to design customized gear. The fashion industry could hugely benefit from this technology as customers’ clothing can be designed with a fully customized, virtually tested and fitted for a wide range of motions. Gaming and animation industries too could benefit from this 3D scanning method. Needless to say, these models could be a whimsical addition to your living room or mind boggling gifts as well. Yet Voodoo and Body Labs are aiming to reach out to some industries that could potentially make use of life sized, accurate and animated human models.
Tags 3D Printed human
Ronan Ye
Ronan Ye is the founder and managing director of 3E-RP which is one of China's leaders in rapid prototyping and 3D printing. Upon completing his college degree at Guangzhou University in International Business with honors, Ronan has been heavily involved in China's fast growing rapid prototyping and manufacturing industry. He really has grown up in and with the industry here in China learning about it at a young age. Hence, his knowledge of the overall industry is second to none and hence why many global companies like BMW, VW, and Lamborghini rely on his technical as well as design expertise.
When will we be able to print new organs on a 3D printer? In China alone, there are 1.
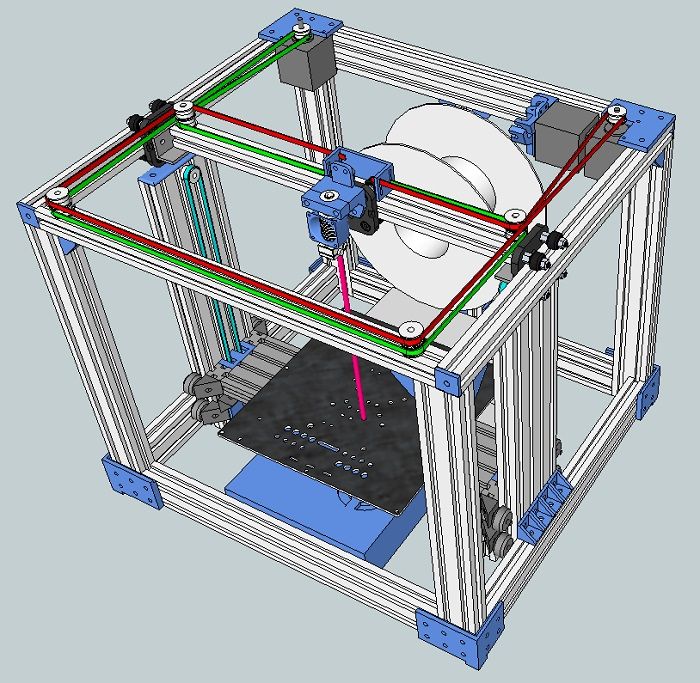
True, not earlier than the next ten years.
Bioprinting technology: how and why are organs printed today?
(Video: RBC)
The principle is about the same as in conventional 3D printing: we get a three-dimensional object on a special printer.
The first stage is preprinting : first, a digital model of the future organ or tissue is created. For this, images obtained on MRI or CT are used.
Then they print, layer by layer - this technology is called additive. Only instead of a conventional 3D printer, there is a special bioprinter, and instead of ink, there are biomaterials. These can be human stem cells, which in the body perform the role of any cells; porcine collagen protein or seaweed-based cell material.
If the cells are alive, they are biopsied and prepared in a bioreactor until they multiply by division to the desired number. During printing, the bioprinter polymerizes the cellular structure - that is, binds it with the help of ultraviolet light, heating or cooling. Cell layers are connected using a hydrogel - organic or artificial.
The resulting structure is then placed in a biological environment where it "ripens" before transplanting. This is the longest stage: it can last several weeks. During this time, the structure stabilizes, and the cells are ready to perform their functions.
Then the organ is transplanted and they monitor how it takes root.
Bioprinting: how living organs are printed on a 3D printer
(Video: RBC)
In addition to conventional additive bioprinters, there are other bioprinters. Some of them print collagen directly on an open wound: this way you can quickly build up new skin even in the field. In this case, the ripening (post-printing) step is skipped.
There are also printers that print in outer space, in zero gravity. In the future, they can be used on the ISS:
There are more than 100 companies in the world that produce 3D bioprinters. 39% of them are in the USA, 35% are in Europe (of which more than half are in France and Germany), 17% are in Asia, 5% are in Latin America.
In Russia, bioprinters are produced by 3D Bioprinting Solutions, which is also engaged in research in the field of bioprinting.
The cheapest and most compact bioprinter - Tissue Scribe by American 3D Cultures, costs from $1.5 thousand
In second place - Australian Rastrum from Inventia for $5,000.
Aether bioprinter from the USA can be bought from $9,000. biosystems.
3D Bioplotters from the German EnvisionTEC cost from $100,000, and the Russian FABION (3D Bioprinting Solutions) is even more expensive.
Finally, the most expensive bioprinters — more than $200,000 — are NovoGen MMX from Organovo (USA) and NGB-R from Poietis (France).
In addition to the cost of the printer, the printing process itself is an additional 15-20% of the cost of the entire project. It will cost even more to obtain the necessary cell material.
So far, the most successful experience has been the transplantation of cartilage - the very ears of Chinese children.
Small artificial cell bones are printed on a printer and then coated with a layer. They are planned to be transplanted instead of a broken or damaged area, after which they completely regenerate in three months. In the future, they want to use the technology for spinal injuries.
The most promising direction is 3D printing of leather. Already in five years they promise that this can be done directly on a person, over or instead of the damaged area. Skin and other tissues are being printed from cells from cancer patients to test various therapies.
More complex organs, such as kidneys or hearts, have so far only been printed as prototypes or transplanted into mice, not humans.
In order for the organs to take root and function well in the human body, they take the patient's cells, and then they divide until they are enough for printing. There are entire institutes that create cell lines for bioprinting. But the problem is that cells have a division limit, after which they are no longer usable. Therefore, it is possible to print a model of the heart, but not life-size - that is, it is not suitable for transplantation into a person.
The second problem is that the printed organ must function in conjunction with the rest of the body : digest food, secrete hormones, deliver blood and oxygen. A complex system of cells, tissues, nerves and blood vessels is responsible for all this. So far, it has not been possible to reproduce it exactly.
Finally, bioprinting technologies are not yet regulated in any way. All research must go through all stages of testing, including on humans, and then obtaining patents.
So far, experts predict the introduction of technology not earlier than in 10-15 years. By then, bioprinters and cellular materials will be widely available, and even the most remote regions will be able to use bioprinting.
More to read:
- History and technology of bioprinting (ENG)
- Overview of the current state of bioprinting and major challenges
- How bioprinting will change our lives (ENG)
- Video: what the bioprinting process looks like (ENG)
- Video: Graphic explaining the printing process from living cells (ENG)
- Video: Ear 3D printing (ENG)
Subscribe and follow us on Yandex.Zen — technology, innovation, economics, education and sharing in one channel.
BB-8 life-size droid from Star Wars 9 3D printed0001
As a rule, after Halloween, attention almost immediately focuses on Christmas, when shops, malls and offices suddenly turn into huge holiday windows. However, things are a little different this year as another major event has entered the calendar: the release of the new Star Wars episode the week before Christmas. It's still more than a month away from this point, but tensions and expectations are growing.
Community 3D printed is getting ready to premiere in its own way - with a lot of cool movie-related projects. The most impressive one I've seen so far is the amazing life-size 3D printed by designer Jason Lou, the BB-8 droid that will be the key droid in the new episode of the saga.
Twenty-five-year-old Jason has a background in industrial design and is very into movie props and toys, so it's only natural that he's one of the millions of Star Wars fans. Jason currently works for a local toy company MightyJaxx , and he is no stranger to design. Working on numerous versions of props, he hopes to build his career in the film industry in the future, and his latest project will surely help him in this.
Jason was obviously inspired by the BB-8 robot trailer. "I've been working on a Sphero version of the BB-8 after seeing the trailer, but unfortunately Sphero has announced their BB-8 toy and I'm already thinking about finishing the project," he said. In fact, Jason is one of those people who got hooked on Star Wars as a kid after watching The Phantom Menace. - Episode one was the film that plunged me into a new world of movie magic. After watching the movie, I really wanted to recreate the world I had just stepped out of."
Luckily, he came across an open community of like-minded Star Wars fans called "BB 8 Builders Club" . As the name suggests, they worked on a full scale version of the droid and also shared their 3D printable files online.
“Because I have a 3D printer, I decided to give this project a try,” he adds.
Luckily, some of the files didn't need to be edited, so Jason sent them to his Zortrax M200 3D printer rather quickly. However, during this process, he kept a close eye on the images and trailers that emerged.
Almost every part that can be seen in the photos has been 3D printed, from the domed head to the body parts. Jason 3D printed everything out of ABS plastic. The domed head took 60 hours to build and the body 500 hours. But the result is very cool. The process of creating a robot did not end there.
Each individual printed piece had to be sanded before priming and painting.
“Aside from the endless sanding, I think the main challenge was to keep going and complete the project,” said the Singaporean designer. “There are a lot of repetitive pieces that need to be brought together, and during this work you will very often have the desire to quit.”
Fortunately, the collaboration with the BB8 Builders community was a huge boost to his enthusiasm. “It provided a much needed level of motivation that spurred me on to complete the project ASAP!” - says the designer.