3D printer in space station
Airbus sending 3D printer to space station next year to pave way for off-Earth factories
When you purchase through links on our site, we may earn an affiliate commission. Here’s how it works.
European aerospace manufacturer Airbus wants to make satellites in orbit from space junk in four years. (Image credit: Airbus)European aerospace company Airbus will send a metal-crafting 3D printer to the International Space Station next year as a first step in its plans to set up an orbital satellite factory.
The printer, called Metal3D, can work with metals that melt at temperatures of up to 2,100 degrees Fahrenheit (1,200 degrees Celsius). It will be the first metal 3D printer on the space station, Airbus said in a statement , and will enable astronauts to print parts such as radiation shields and various tools. (American company Made In Space, now a subsidiary of Redwire, has sent several 3D printers to the space station, but none of them can print metal. )
Future versions of the 3D printer, the company added, will be able to make objects using lunar soil and also recycle parts from old satellites.
Related: 3D printed satellite antennas can be made in space with help of sunlight
The Metal3D printer is only one component in a range of technologies developed by Airbus with the goal of setting up a space factory. In a series of videos, Airbus showed off a robotic manipulator designed to assemble spacecraft.
"Airbus' solution is to launch kit parts that will be assembled in space by the robotic arms from our space factory," the company said in the statement.
The robotic arms will be able to build each other in orbit, Airbus said, but could also be used to repair and refuel spacecraft.
The company said it would like to be able to manufacture entire satellites in space in the "next three to four years."
Related stories:
"Since there is enough space in space, it will be possible to build bigger structures such as huge reflectors, allowing telecom satellites to cover the entire planet," Airbus said in the statement.
Moreover, producing satellites in space will also be kinder to the environment, the company said, as fewer polluting rocket launches will be needed.
"The material for production can be sourced from the space debris floating around," Airbus said. "So with the space factory, Airbus is also helping to clean up space and ensure a sustainable future for the industry."
When it comes to the Metal3D printer, the space station is only its first destination. By the end of this decade, Airbus said, a similar device might be churning out parts of lunar rovers and habitats directly on the surface of the moon.
Follow Tereza Pultarova on Twitter @TerezaPultarova. Follow us on Twitter @Spacedotcom and on Facebook.
Join our Space Forums to keep talking space on the latest missions, night sky and more! And if you have a news tip, correction or comment, let us know at: [email protected].
Tereza is a London-based science and technology journalist, aspiring fiction writer and amateur gymnast. Originally from Prague, the Czech Republic, she spent the first seven years of her career working as a reporter, script-writer and presenter for various TV programmes of the Czech Public Service Television. She later took a career break to pursue further education and added a Master's in Science from the International Space University, France, to her Bachelor's in Journalism and Master's in Cultural Anthropology from Prague's Charles University. She worked as a reporter at the Engineering and Technology magazine, freelanced for a range of publications including Live Science, Space.com, Professional Engineering, Via Satellite and Space News and served as a maternity cover science editor at the European Space Agency.
3D printing in space - 3D printers for the space industry
Why is 3D printing important for the space industry?
3D printing could revolutionize space exploration by helping astronauts create objects in space and on-demand: replacement parts for repairs, custom equipment for scientific experiments, and even things like food or buildings!
Indeed, while space is an extreme environment with very few exploitable raw materials, there is plenty of dust floating around. 3D printing technology can allow you to build solid structures from aggregated dust and microscopic particles. The European Space Agency (ESA) is considering 3D printing their base on the moon.
As for 3D printed meals for astronauts in space, NASA is funding a Systems and Materials Research Corporation project to develop a 3D food printer that can be used in a zero-gravity environment.
3D printing replacement parts in space
One of the main challenges that astronauts face is the lack of specific replacement parts on-board the space station.
A zero-gravity 3D printer
Thanks to 3D printing technology, it is now possible to manufacture spare parts in space. NASA and Made in Space are collaborating to solve that problem. The result of their experiments is the zero-G 3D printer, a 3D printer that can operate in zero-gravity environments.
They managed to produce a ratchet wrench from a 3D file that was emailed from Earth to the space station. This 3D printer uses the Fused Filament Fabrication technology (filament extrusion) and can print objects in plastic.
Ratchet 3D printed in space by the Zero G 3D printer.“Right now if something breaks, we’re completely dependent on launching a replacement from the ground. Imagine launching everything you might ever need for a mission to Mars or an asteroid, it would be challenging or impossible.”
Niki Werkheiser, Nasa project Manager
Future evolutions
In less than a week, the 3D file of the custom ratchet was designed, sent in space, and then manufactured by the 3D printer.
The next goal is to have a database of 3D files (STL files) of all the parts needed in the space station, in order to save time in case one of them breaks.
Being able to recycle 3D printed objects that are no longer needed and then reuse the material is also a big focus.
Solving the food problem with 3D printing
3D printing food in space
3D printers have the capacity to create a variety of products with a small amount of raw materials.
Thus, engineers found here the perfect technology for feeding astronauts on long-term space missions. NASA has invested $125,000 in SMRC, an ambitious project led by Anjan Contractor.
He succeeded in creating a food 3D printer able to 3D print pizza in space.
The different steps involved in 3D printing a pizza.Pizzas are ideal for 3D printer because they’re made of different layers on top of each other (great for additive technology process like 3D printing):
- A layer of dough is first deposited on the 3D printer’s heating bed to be directly cooked
- Second, a layer of water, oil, and tomato powder is applied (tomato sauce)
- Then, a layer of cheese is deposited
- Finally, animal and vegetal proteins are added to provide essential nutrients
This process allows to cook a pizza in a few minutes and, according to Anjan Contractor, to print carbs, proteins, macronutrients, and micronutrients that are stored in powder form within a special cartridge. These powders remain edible for around 30 years, long enough for a mission to Mars.
3D printing a lunar base
Building a lunar habitation to ease exploration and research
Thanks to the 3D printing technology, the European Space Agency hopes it will be one day able to 3D print a base on the moon. International architecture studio Foster + Partner designed such a structure in partnership with Monolite UK, which provides the 3D printer.
According to Foster + Partner, the base must be assembled around a dome built on Earth. This dome will filter gamma rays, solar radiation and meteorites impacts. On the moon, two 3D printers would finish the build and strengthen the structure by using raw materials found on the spot.
Monolite UK says that their construction 3D printer is able to achieve a complete base in less than two weeks. The next generation is claimed to be twice as fast as this one.
Case studies: 3D technology for spacecraft
The 3D printed thruster chamber from the European Space Agency
In June 2015, the ESA unveiled the world’s first 3D printed spacecraft thruster, including a platinum combustion chamber. The use of 3D printing offered several advantages:
- Similar performances to a traditional thruster
- Possibility to use new build materials
- Lower production cost and turnover
The 3D printed oxidizer valve from the Falcon 9 rocket by SpaceX
SpaceX announced in July 2014 that they had successfully 3D printed an oxidizer valve for the 1D engine used in the Falcon 9 rocket. The oxidizer valve is a crucial part of a rocket engine– it controls the flow of liquid oxygen as it enters the engine’s combustion chamber. It took only two days to 3D print this valve, while traditional manufacturing processes take up to months to build such parts.
The SpaceX rocket engine using the 3D printed oxidizer valve during a test phase.In addition, the 3D printed valve offers some key advantages, which have led SpaceX to decide to 3D print all of their oxidizer valves:
- Higher overall performances versus traditional manufacturing processes
- Higher resistance to fracture
- Superior ductility
The SuperDraco engine by SpaceX
SpaceX announced in May 2014 that their new rocket engine, the SuperDraco, had passed all the qualification tests (certifying metal 3D printed parts is a challenge).
The SuperDraco boasts 3D printed combustion chamber, which was 3D printed using the Direct Metal Laser Sintering process (DMLS). Elon Musk is enthusiastic about the future of additive manufacturing for the space industry:
“Through 3D printing, robust and high-performing engine parts can be created at a fraction of the cost and time of traditional manufacturing methods. SpaceX is pushing the boundaries of what additive manufacturing can do in the 21st century, ultimately making our vehicles more efficient, reliable, and robust than ever before.”
Elon Musk
Cosmonauts on the ISS printed the first part on a Russian 3D printer / Sudo Null IT News
Cosmonaut Dmitry Petelin explained to the media that Prokopiev was able to print a test part on the printer using a recently obtained filament. The part model was sent to the printer by RSC Energia specialists from the MCC.
RSC Energia engineers sent sets of thermoplastic polymers for printing with polymer thread to the ISS as part of the payload on the Progress MS-21 transport cargo spacecraft in October.
On August 3, cosmonaut Oleg Artemiev announced the successful activation and testing of a Russian 3D printer on the ISS.
Photo source: Oleg Artemyev/TASS, ISS.
Then the cosmonauts only prepared the printer for printing, and the Russian crew had not yet begun the main work with the printer. The astronauts were waiting for a special material for printing, which should be delivered to the ISS as part of the scientific cargo on the Soyuz MS-22 spacecraft in September.
The astronauts will try to print simple cubes on a 3D printer, and then they will experimentally print different shapes, including details according to the drawings of Russian students. Then the resulting 3D printing samples will be returned to Earth. Roscosmos experts will study their characteristics under various laboratory conditions in order to comprehensively investigate the impact of microgravity on 3D printing.
In case of successful application of the device, the spacecraft can become part of the standard equipment of the ISS Russian Segment.
The Russian 3D printer was delivered to the ISS for experiments on the Progress MS-20 spacecraft in June. The device was specially created for the ISS by RSC Energia in cooperation with Tomsk Polytechnic University and Tomsk State University. Samples and parts that are used in large quantities on board the station will be printed on it from thermoplastic polymers by layer-by-layer imposition of a molten polymer thread (filament).
“This technology will allow astronauts to manufacture, for example, covers for electrical connectors of various nomenclature, research blades, wrenches and other tools, fasteners (nuts, bolts, etc.) necessary for work on the ISS,” — said a representative of the Department of Radiophysics of Tomsk State University.
“The development of additive technologies at the station will open up new opportunities for the domestic astronautics to use 3D printing in the future. For example, in lunar expeditions, cosmonauts will no longer depend on the delivery of the necessary components and structures on transport ships from Earth, but will be able to print them directly in space, which will allow reaching a new level of performing various kinds of tasks, ”the Roscosmos added.
In November 2021, Russian cosmonauts complained that the sockets for hexagons were missing on the ISS and asked to send them, if possible, sockets for tools for 8, 10 and 12. With a printer, they will be able to print them on the station themselves.
Last August, NASA began testing a 3D printer with lunar soil on the ISS. The project aims to test the strength and wear resistance of regolith, from which they plan to build colonies on the moon.
In September 2014, the Zero G 3D printer, also developed by Made In Space, was delivered to the ISS. In November, he became the first printer to print a three-dimensional product in space - a plate with the inscription "Made In Space NASA". Two years later, the researchers sent an improved printer model to the station.
3D printers provide astronauts with the necessary tools and parts for various designs. For example, in 2014, astronaut Berry Wilmore 3D printed a socket wrench.
Russian 3D printer on the ISS produced the first working part
News
scientists with the participation of the Energia Rocket and Space Corporation.
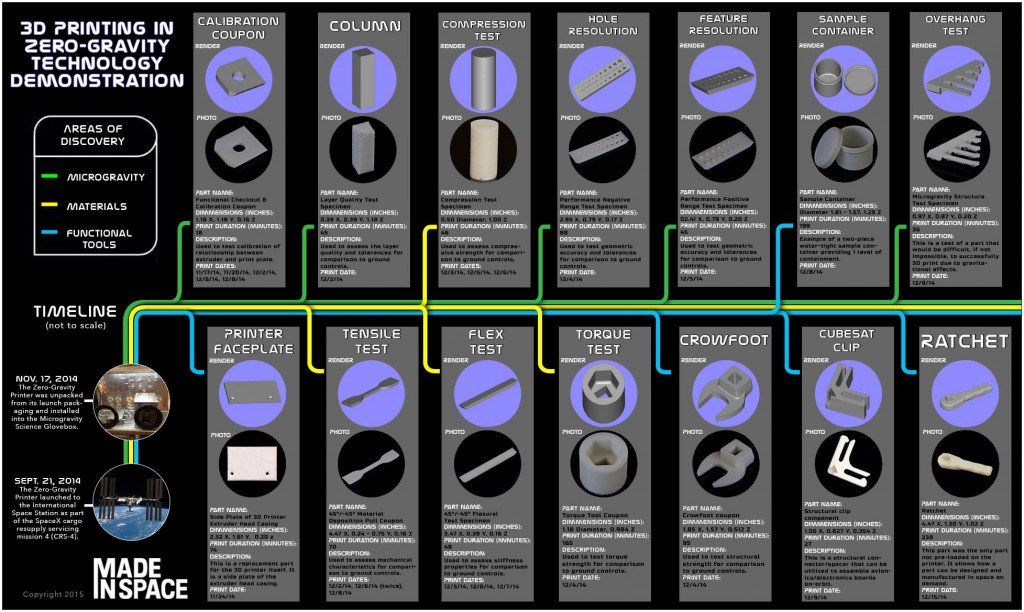
“A control camera will be installed on the porthole of the Nauka multi-purpose laboratory module inside the station to monitor the docking process of the airlock,” cosmonaut Dmitry Petelin told TASS.
The 3D printer was designed by scientists from Tomsk Polytechnic University and Tomsk State University together with specialists from Energia Rocket and Space Corporation. The equipment was delivered to the International Space Station in June last year.
The experiment is devoted to the development of additive technologies for the production of products from polymeric materials in space conditions. The developers expect that in the future, the use of 3D printing technologies will allow astronauts at near-Earth orbital stations to produce the necessary parts and tools directly in space, without waiting for delivery on transport ships from Earth.
Do you have interesting news? Share your developments with us, and we will tell the whole world about them! We are waiting for your ideas at news@3Dtoday. ru.
ISS FFF fdm TPU TSU Roskosmos
Subscribe to the author
Subscribe
Don't want
22
Article comments
More interesting articles
5
Subscribe to the author
Subscribe
Don't want
In 2022, the Moscow company "Lasers and Apparatus" increased the production of laser systems almost...
Read more
5
Follow the author
Subscribe
Don't want
The Belarusian state television channel ONT has released a report about 3D food printing and supposedly Belarusian.