Working 3d printed jet engine
Electric Jet Engine Uses 3D Printed Compressor, Skips The Turbine Altogether.
- by: Ryan Flowers
Turbojet engines are an incredible piece of 20th century engineering that except for some edge cases, have mostly been replaced by Turbofans. Still, even the most basic early designs were groundbreaking in their time. Material science was applied to make them more reliable, more powerful, and lighter. But all of those incredible advances go completely out the window when you’re [Joel] of [Integza], and you prefer to build your internal combustion engines using repurposed butane canisters and 3d printed parts as you see in the video below the break.
Emoscopes, CC BY-SA 3.0 via Wikimedia CommonsTo understand [Integza]’s engine, a quick explanation of Turbojet engines is helpful. Just like any other internal combustion engine, air is compressed, fuel is burned, and the reaction produces work. In a turbojet, a compressor compresses air. Fuel is added in a combustor and ignited, and the expanding exhaust drives a turbine that in turn drives the compressor since both are attached to the same shaft. Exhaust whose energy isn’t spent in turning the turbine is expelled and produces thrust, which propels the engine and the vehicle it’s attached to in the opposite direction. Simple, right? Right! Until the 3d printer comes in.
Sadly for 3d printed parts, they are made of plastic. Last we checked, plastic isn’t metal, and so 3d printing a turbine to give the extremely hot exhaust something turn just isn’t going to work. But what if you just skipped the whole turbine part, and powered the compressor with an electric motor? And instead of using an axial compressor with tons of tiny blades that would likely be impossible to 3d print with enough strength, you went with a sturdy, easy to print centrifugal compressor? Of course, that’s exactly what [Integza] did, or we wouldn’t be talking about it. The results are fantastic, especially considering that the entire machine was built with 3d printing and a home made spot welder.
If you want to build a full jet turbine, we won’t say it’s easy, but you might appreciate this jet turbine whose components include a toilet paper holder as proof that once a technology is understood, it can be built in the worst ways possible and still work. Sort of.
This Tiny 3D Printed Jet Engine Could Have Big Promise
Ozy
Call it the little engine that could. Last year, a team of engineers at GE Aviation’s Additive Technology Center built an almost entirely 3D printed miniature jet engine — a backpack-size powerhouse that hits 33,000 rotations per minute.
While this little guy — it measures 1 foot, 8 inches — isn’t going to propel a commercial airliner anytime soon, it did demonstrate that a powerful, functioning engine built mainly from 3D printed parts isn’t a flight of fancy so much as the future of flight.
Additive manufacturing is hardly new to aviation. Parts of full-size aircrafts already incorporate 3D printed parts. CFM’s LEAP engine — a best-seller since it entered into service last year — has 3D printed fuel nozzles. In April, Reuters reported that Boeing would start using 3D printed parts for structural components of its 787 Dreamliner. Though petite, GE’s mini engine could have big implications. It represents the promise that one day, you could be sitting on a plane, and the engine keeping you in the sky will have been entirely 3D printed.
Coolness factor aside, 3D printed jet engines are considerably lighter, and reducing the weight of an aircraft has the knock-on effect of reducing the amount of fuel needed to keep a plane in the sky — and less fuel means a more cost-effective flight, and less emissions.
Boeing estimates that by incorporating additive manufacturing in the production of up to 1,000 Dreamliners, the company could potentially reduce costs by up to $3 million per plane. Imagine the savings if the technology were rolled out on a greater scale.
Using 3D printing to manufacture parts also means less material waste, which further reduces the cost and complexity of production. For example, the process GE used to print its mini engine — direct metal laser melting, or DMLM — involves melting metal powder layer upon layer and building a part from the ground up, rather than cutting it from one large piece of material.
Additive manufacturing also means a quicker, more custom design. GE says that 3D printing fuel nozzles for the LEAP engine allowed engineers to reduce the number of brazes and welds in the design from 25 to just five.
“You get speed because there’s less need for tooling and you go right from a model or idea to making a part,” says Matt Benvie, a spokesman for GE Aviation. “You can also get geometries that just can’t be made any other way.”
There are still limits to what 3D printing can achieve, of course. The new technology is not yet as fast nor as cheap as hoped; it took GE years to build a small, simple prototype. The materials needed for 3D printing can sometimes be too expensive for mass production. And we’re not yet in a place where 3D printed parts are coming out perfect — post-processing work is often required.
Still, for aircraft manufacturers, the benefits of eventually 3D printing most, if not all, aircraft parts are too great not to pursue. Airbus has gone so far as to say the technology could reduce both raw material and energy used in production by 90 percent; it has also been reported that 3D printing all the possible components of an A350 would reduce the weight of the aircraft by more than a ton. For a feel of just how much fuel that would save, consider that back in 2014, Virgin Atlantic slimmed the design of its meal trays to trim 300 pounds of weight per flight — enough to save millions of dollars on fuel (not to mention reducing carbon emissions).
Even more interesting, it could be that size does matter. In December, Pune, India–based market research company ReportsnReports said miniaturizing aircraft components through 3D printing would be key to improving fuel efficiency and operating costs in years to come. Perhaps the future is all about thinking small.
3D-printed Moon landing pad prototype tested
It is almost impossible to imagine space exploration without using local resources. Lunar base projects were buried under the surface, sprinkled with soil, or surrounded by printed walls. But less attention was paid to the buildings of the lunar cosmodrome - at best, flat areas are drawn in the illustrations. They will have a minus - the engine exhaust will corrode the surface and raise dust. To address these potential challenges, a team of students from ten U.S. universities and colleges, with support from NASA and 3D printing company ICON, designed, built, and successfully tested a large-scale prototype of the Lunar PAD airstrip.
Photo: ICON
In the summer of 2019, a team of students from NASA's L'SPACE Virtual Academy won a round of NASA NPWEE's 12-week technology concept proposal course and received funding to develop their concept for shielding landers from lunar dust using robotic construction. The goals of both L'SPACE and NPWEE are to expand the pool of high-quality proposals of new concepts and technologies that can then be useful to NASA. In 2020, the team submitted a revised concept to an online technology readiness review and received funds to build and test a scale model. After spending hundreds of working hours consulting with NASA experts, the students went from idea to implementation of a model of the potentially important task of creating a safe reusable landing site for the Moon. In autumn, a scale model was built at Camp Swift, Texas, and successfully tested by a geophysical rocket engine in early March.
A team of students at work, photo ICON
The project, originally named Dust Devil ("dust whirl"), is eventually called the Lunar Plume Alleviation Device ("Lunar device for mitigating exhaust") or, for short, Lunar PAD (playing on the fact that in English "pad" also means "a platform for launch / landing"). Structurally, the Lunar PAD consists of two levels: the upper one is a flat platform with small slots for exhaust gases to drain.
Finished site with a test rocket engine installed, photo ICON
The lower level combines supporting structures and gas ducts for exhaust gases to the sides. A feature of the project is the use of 3D printing. First, a 3D construction printer forms a frame, which, as is often the case in additive manufacturing, uses complex surfaces and looks aesthetically pleasing.
Frame and student team, photo ICON
Printing process, top view, photo ICON
The printed frame is then filled with filler. The test mock-up used a cement-based material, but for lunar conditions, it would be logical to produce a hardening or sintering regolith building material in situ. The structure built is strong enough to withstand the takeoff and landing of the lunar modules, and produces less dust by diverting engine exhaust into the gas ducts.
Even at the construction stage, sensors were installed in the model to determine temperatures, loads and gas flow. In early March, a geophysical rocket team from Texas A&M University delivered a solid rocket motor to a test site. It was installed above the site, launched and looked at the information recorded by the sensors. The tests were successful - the Lunar PAD pad successfully withstood the takeoff / landing simulation, the data obtained do not contradict the calculated ones.
Site inspection after testing. Pay attention to the side along the edges, reflecting the exhaust up. Photo ICON
The project has already published its first scientific publication in the AIAA SciTech Forum materials, and a very diverse group of college and university students scattered throughout the United States can chalk up participation in a full-fledged and successful scientific and technical project, potentially in demand in future lunar base projects.
It is also interesting to note that ICON, which provided the gantry 3D printer for the project, is also 3D printing houses and other structures. The company also received a contract from NASA last fall to research and develop a construction system that could be used on the moon. Under this contract and, potentially, other space projects, a special division of the company was created. The project was named "Olympus". And it's time to redo the freshly drawn renders - thanks to the efforts of the students who created the Lunar PAD, the depicted landing pads already look outdated.
Click this button and you will be notified when my new post comes out.
I am on social networks: VKontakte, Facebook, Twitter, Instagram, YouTube
Thank money: Yandex.Money, PayPal, Webmoney
Tags: exploration of the Moon Moons
It is almost impossible to imagine space exploration without the use of local resources. Lunar base projects were buried under the surface, sprinkled with soil or surrounded by printed walls. But less attention was paid to the buildings of the lunar cosmodrome - at best, flat areas are drawn in the illustrations. They will have a minus - the engine exhaust will corrode the surface and raise dust. To address these potential challenges, a team of students from ten U.S. universities and colleges, with support from NASA and 3D printing company ICON, designed, built, and successfully tested a large-scale prototype of the Lunar PAD airstrip.
In the summer of 2019, a team of students from NASA's L'SPACE Virtual Academy won a round of the 12-week NASA NPWEE Technology Concept Proposal course and received funding to develop their concept for shielding lunar dust landers using robotic construction. The goals of both L'SPACE and NPWEE are to expand the pool of high-quality proposals of new concepts and technologies that can then be useful to NASA. In 2020, the team submitted a revised concept to an online technology readiness review and received funds to build and test a scale model. After spending hundreds of working hours consulting with NASA experts, the students went from idea to implementation of a model of the potentially important task of creating a safe reusable landing site for the Moon. In autumn, a scale model was built at Camp Swift, Texas, and successfully tested by a geophysical rocket engine in early March.
The project, originally named Dust Devil ("dust whirlwind"), in the end is called the Lunar Plume Alleviation Device ("Lunar device to soften the exhaust") or, for short, Lunar PAD (playing on what that in English "pad" also means "a platform for launch / landing"). Structurally, the Lunar PAD consists of two levels: the upper one is a flat platform with small slots for exhaust gases to drain.
Ready site with test rocket engine installed, photo ICON The lower level combines load-bearing structures and flues for exhaust gases to the sides. A feature of the project is the use of 3D printing. First, a 3D construction printer forms a frame, which, as is often the case in additive manufacturing, uses complex surfaces and looks aesthetically pleasing.
The printed frame is then filled with filler. The test mock-up used a cement-based material, but for lunar conditions, it would be logical to produce a hardening or sintering regolith building material in situ. The structure built is strong enough to withstand the takeoff and landing of the lunar modules, and produces less dust by diverting engine exhaust into the gas ducts.
Even at the construction stage, sensors were installed in the model to determine temperatures, loads and gas flow. In early March, a geophysical rocket team from Texas A&M University delivered a solid rocket motor to a test site. It was installed above the site, launched and looked at the information recorded by the sensors. The tests were successful - the Lunar PAD pad successfully withstood the takeoff / landing simulation, the data obtained do not contradict the calculated ones.
Inspection of the site after testing.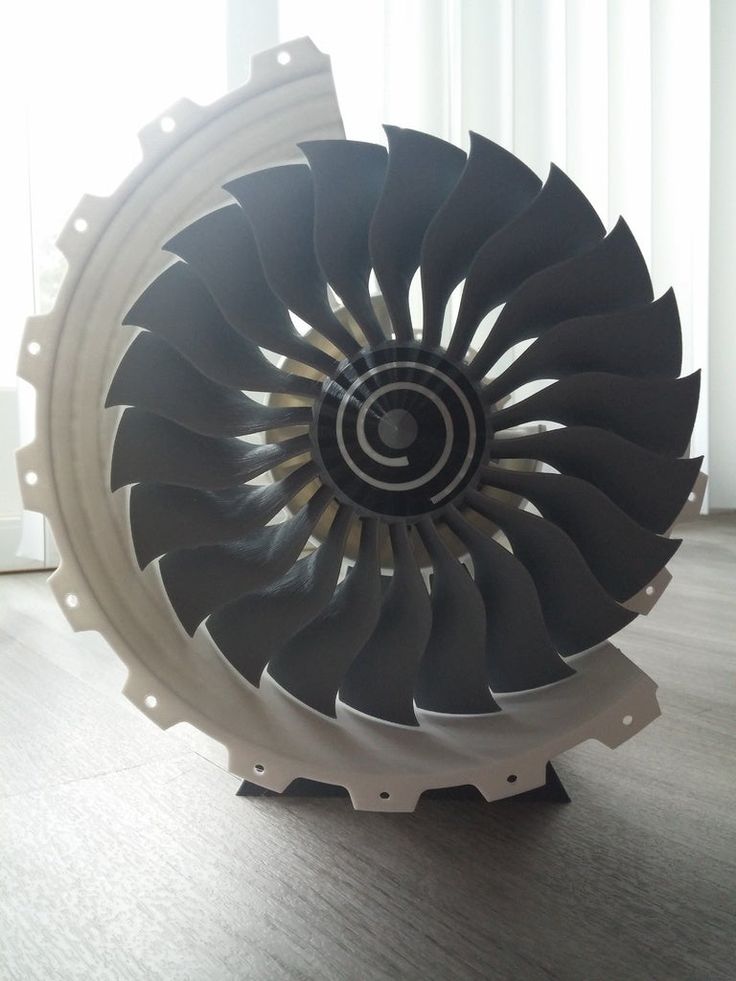
The project has already published its first scientific publication in the materials of the AIAA SciTech Forum, and a very diverse group of college and university students scattered throughout the United States can take part in a full-fledged and successful scientific and technical project, potentially in demand in future projects moon bases.
It is also interesting to note that ICON, which provided the gantry 3D printer for the project, is also 3D printing houses and other structures. The company also received a contract from NASA last fall to research and develop a construction system that could be used on the moon. Under this contract and, potentially, other space projects, a special division of the company was created. The project was named "Olympus". And it's time to redo the freshly drawn renders - thanks to the efforts of the students who created the Lunar PAD, the depicted landing pads already look outdated.