3D printer filtration system
Nevermore Is What You Get When Engineers Design Air Filters For 3D Printers
- by: Donald Papp
What happens when an air filter for 3D printers gets designed by engineers with a passion for function, a refusal to compromise, and a desire to do without bad smells or fumes? You get the Nevermore, a design for a recirculating active-carbon filtration system to deal with VOCs (volatile organic compounds) from 3D printing.
3D-printable parts and an easy-to-fill chamber for bulk-activated carbon make this recirculating air filter for VOCs a smart, space-saving design.The Nevermore Micro (and larger Nevermore Max) were originally intended to complement the Voron 3D printer design, but are made such that they can be used with just about anything else. These filters use 3D-printable parts, and are designed to be easily filled (and refilled) using bulk-activated carbon instead of some kind of proprietary pre-packed filter like most commercial offerings. The Voron project is all about a printer without compromises, and the Nevermore comes from that same design ethos.
A Nevermore filter sits inside the build chamber, and works by recirculating air inside while passing it through the activated carbon. The idea is that by concentrating on dealing with the problem at the source inside a relatively small build chamber, one doesn’t need a lot of airflow. A small recirculating air filter can do the job efficiently, though for best results, the build chamber should be as sealed as possible.
One interesting caution is that it seems not all activated carbon is the same, and it is absolutely crucial to use only acid-free, steam-activated (not acid-washed) carbon in a recirculating filter like the Nevermore. There are horrifying photos of oxidized metal surfaces resulting from using acid-residue carbon, some of which took only minutes to occur. Thankfully, there are pointers to trusted sources for the known-good stuff.
It’s known that 3D printing results in chemical and particle emissions. These differ significantly depending on both material and type of printer, but it’s enough of an issue to warrant attention. One deals with particulates with something like a HEPA filter, but VOCs require a carbon filter. This is where the Nevermore comes in. Active carbon filters will wear out simply from exposure to the air, so if one is serious about cleaning VOCs when printing, it is definitely worth looking into bulk carbon with a design like the Nevermore.
Building an Air Filtration System for a 3D Printer
How I used a microcontroller, a fan, and a bunch of sensors to create a smart filtration system.
Posted on January 6, 2021 by Mike Buss
I was thinking of projects to work on, and I thought, gee, it would be nice if our 3D printer didn’t kill us.
I had researched the potential health side effects of owning a 3D printer when I bought it - it turns out they can malfunction and catch fire or release harmful chemicals into the air - but I made excuses. I’m only printing in Polyactic Acid (PLA), one of the least harmful filaments - it’s probably fine. Sure, maybe it releases some tiny plastic into the air, but it’s a big room, and sometimes I keep the windows open. Our smoke detectors are brand new and well tested. We’re probably fine.
Now that we welcomed Theodore, our now 3-month-old, into the world, I wanted to be on the safe side. So, I set out to build an air filtration system and some other safety features.
The Start of an Idea
As with most of my hobby projects, it started out simple. I thought of strapping a fan to a HEPA filter and maybe adding a carbon filter for extra protection. Then I thought: wouldn’t it be cool if it turned on and off automatically when a print started? Surely that wouldn’t be too difficult to build.
And wouldn’t it be even better if the system could tell when the volatile organic compounds (VOC) levels were high and adjust the fan speed accordingly? Since the goal is to make this box less likely to kill everyone in our sleep, why not add a fire sensor and an electric cutoff?
The fan I started with: a 140mm NZXT fan for PC's.Eventually, I landed on building a totally ridiculous, completely overkill air filtration system for our 3D printer that probably wasn’t necessary in the first place. And it was lots of fun.
Here’s how I did it.
Sketching It Out
I’m a firm believer in “measure twice, cut once”, so I started with a sketch of the system. I measured my 3D printer - an Ultimaker S3 - and jotted down a plan for the top enclosure. Then, I sketched out what components I wanted to use and how they’d connect.
Next, I printed the parts I needed to assemble the box and the filtration panel. Isn’t it cool how a printer can print things to augment itself? Next step: Skynet.
Everything except the electronics and Lexan was printed.Building the Partial Enclosure
I bought some Lexan from Home Depot, scored the sheets with a box cutter, and snapped them off using the edge of my workbench. It worked surprisingly well.
If you plan to do this at home, wear protective gear, including glasses.
I used Lexan because it was readily available at the local Home Depot.After cutting the Lexan, I connected all the pieces with 3D-printed parts. Special thanks to Hans Peter for building something similar and releasing the designs on Thingiverse.
The connecting parts were 3D printed. The final Lexan enclosure.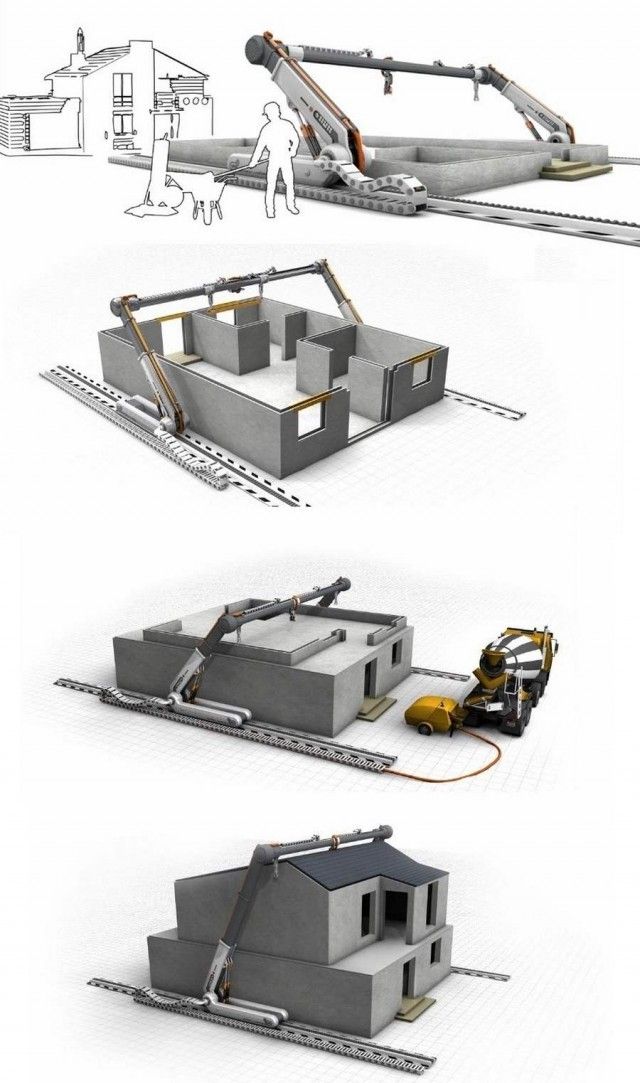
Now that I had the shell, it was time for the guts: the electronics.
Wiring Everything Up
The first rule of wiring electronics is don’t accidentally put 12V into a pin that expects 5V. You’ll get lots of smoke and heat and generally feel bad. After you’ve learned that rule, continue reading.
No electronics project would be complete without a prototype that looks like a rat's nest (top right). I cleaned this up later!I managed to assemble a gaggle of electronics that all needed power. Some needed 12V to work. Others needed 3.3V. Some were controlled with pulse width modulation, others with I2C. Getting them powered and conducting a symphony of functions was, in my opinion, the best part of this project.
I started with a 12V 3A power supply. This, wired into my Arduino Nano 33 IoT, a relay, and (via the relay) the fan, gave life to the essential components. I could now turn the fan on and off through the Arduino, but only at full speed.
To control the fan’s speed, I connected its PWM pin to a PWM pin on the Arduino. It took some math to change the Arduino’s built-in PWM frequency to 25 kHz, but the slower fan speed significantly reduced noise.
Now that the Arduino could control the fan, I wanted to have it start and stop automatically. To do this, I used the built-in WiFi module poll the Ultimaker S3’s API periodically.
The Ultimaker S3 comes with an excellent API.Then, because everyone loves data, I added some logging to my creation. I equipped the inside and outside of the chamber with sensors that measure temperature, humidity, and VOC levels. This data is sent over WiFi to a server running on my NAS (a Synology DS918+). Eventually, I’d like to use this data in real-time to control the fan speed, but for now, it’s just filed away along with information on what was printed and when.
Adding two temperature sensors was a little tricky, considering they share the same hardcoded I2C address. Because of this, the Arduino can’t address them individually. My solution was to use an I2C multiplexer to let me switch between sensors and query them individually.
While all of this is happening, the Arduino is also checking a flame sensor that hovers over the printer. If this sensor detects a fire, the power to the Ultimaker is immediately shut off, and a piezo alarm starts blaring. It’s not as cool as those automatic fire suppression kits you can buy, but the alarm can be heard throughout the house.
The flame sensor (left) will report if it detects a fire in the print chamber. This photo was taken when I was still breadboarding the prototype.Filtration
The fan pulls air out of the chamber, through a HEPA filter and a carbon filter, and then out the back. You can find all the parts I used here.
Future Improvements
The fan I have probably isn’t pushing as much air as I’d like through the two filters. I’d like to upgrade it to something better in the future.
All said and done, this project was fun to build and gives my wife and me some peace of mind. If you’ve created something similar, I would love to hear about it!
Share:
Welcoming Our First
Today, my wife and I welcomed Theodore Frederick Buss into the world!
Fixing the Worst USB Hub in the World
Hewlett Packard makes the world's worst USB hub. No, really. It's truly awful.
Mike Buss is a software engineer from Ohio who works primarily in the healthcare space. His work has been featured on Apple.com and helped hundreds of thousands of patients. In his spare time, he writes about software development and more.
Follow @michaeltbuss on Twitter as he continues to document his software development journey.
Alveo3D, a filter kit for safe 3D printing at home and in the office
Alveo3D is a young French company that has developed a nanoparticle filtering system for 3D printers. Its goal is to reduce toxic emissions from machines by reducing the risk of air pollution when they operate in poorly ventilated environments. Ultimately, these particles can be hazardous to the health of users. These small filters are installed in small boxes, also developed by the startup. The whole system is made of plastic elements printed on a 3D printer. They are now available as kits or ready to use with boxes that can be customized to fit the size of the 3D printer. We caught up with Lucas Martini, CEO of Alveo3D, to learn more about these solutions.
3DN: Could you introduce yourself and your relationship with 3D printing?
My name is Lukas and I represent Flexee System, the company behind the Alveo3D project, which addresses the issue of toxic emissions from 3D printers. We are the three partners behind this project, which started back in 2018. Victor is an industrial product designer and Laurent is a team developer. 3D printing has become an important tool in our arsenal for prototyping our models and demonstrators.
3DN: Why did you create Alveo3D?
We quickly started using 3D printers in small spaces like our workshop or home. We have become aware of the potential hazard associated with our machines due to throat and eye irritation and the unpleasant smell of melted plastic. We know of some manufacturers that have mentioned the same symptoms, especially when using thermoplastics such as ABS or HIPS. Some reported headaches, and the symptoms were more severe in smaller, less ventilated spaces. The same descriptions were found on the forums, with some members suggesting homemade filter solutions.
During 3D printing, we can actually encounter two types of harmful emissions: toxic emissions associated with volatile organic compounds (VOCs) and nanoparticles. That's all it took to convince us to equip our 3D printer with a filter system. Speaking a little about toxic emissions, it is important to point out that this is a long-term risk with potential chronic consequences. Pollutant emissions enter the air in low concentrations, and the regular presence of a 3D printer can be harmful. When 3D printers are used in poorly ventilated areas, the accumulation of nanoparticles and VOCs can pose a risk of air pollution.
The risk associated with volatile organic compounds is well known to industry and air quality authorities. Some gases emitted by thermoplastics are known to be carcinogenic. Even in PLA, which is naturally based, the amount of additives added to it makes it toxic. Other filaments, such as POM, naturally release formaldehyde and there is a risk of inhaling toxic air when opening a bag from a spool. For nanoparticles, the risk is less well defined, but probably even more dangerous. They can be found in the body, organs and brain and are difficult to eliminate by the human body.
CNRS recommends using a HEPA filter for nanoparticles and activated carbon for VOCs. We searched for existing filtering solutions and were surprised to find that there were few 3D printing solutions available for less than 150 euros. Many manufacturers create their own air filtration systems that they place on the body of their printer to draw air in and filter it before it enters the room.
The first version of our filtration system was made by hand. HEPA filter, granular activated carbon and 3D model to fit everything on our printer body. The results were encouraging, but we wanted to make sure we were dealing effectively with all the toxic emissions. What should have been a simple accessory for our 3D printer turned out to be a real piece of work. We then mapped the risks associated with most of the gases we could detect during printing. We synthesized the results of studies on the release of nanoparticles and realized that the processing of these elements of the order of several tens of nanometers would require further development.
Over the course of 3-4 months, we tested dozens of filter configurations on our test machine. We have worked with European and Chinese manufacturers to find the right combination for capturing VOCs and nanoparticles. We wanted our work to remain accessible to all users, because the danger is no different from an entry-level machine or a professional model.
3DN: How do Alveo3D air filters work?
Alveo3D filter blocks have been designed for 3D printing, for easy use and easy replacement of filter cartridges. They combine a powerful high pressure fan and a filter cartridge specifically designed to combat harmful emissions from FDM 3D printing. This filtration system includes an activated carbon bed that allows it to handle a wide range of VOCs.
We are often asked about the life cycle of our filters, but the answer depends on many factors, the main ones being printing time, filament type and extrusion temperature. As a precaution, we recommend 600 hours of use. This is mainly due to activated charcoal. When it is saturated, it will let all the VOCs through, so it is important to change the filter regularly until saturation is reached. 600 hours of filtration is approximately one change every 6 months for printers that operate occasionally and every 3 months for printers that operate regularly.
Our filtration systems are mounted on the 3D printer body. It's an essential tool to protect your equipment and print successfully, especially with some plastics that are harder to print like ABS. It also reduces the noise level of the machine. First of all, it allows you to capture all the vapors even after the plastic has cooled down. In fact, we have 3 goals: to maintain a stable ambient temperature, to limit the negative effects of deformation, and to process the air in general. We produce custom boxes according to the dimensions of each printer. Conventional design with aluminum frame and plexiglass or polycarbonate fronts. The boxes are equipped with our filtration system and we can add options according to the specific needs of our clients.
Finally, as I said, all the plastic parts of our boxes are 3D printed, allowing us to make continuous technical improvements as well as customize the final solution. They are available as kits or ready to use.
Two models have now been developed. The alveoONE filtration model is used with a box equipped with an air intake that does not need to be closed. It draws air into the case, creating a small vacuum, and exhausts clean air. It is suitable for printing common thermoplastics, PLA, ABS, PET. The alveoONE-R filtration model is used with a waterproof housing and works with internal processing. If you require an ambient temperature above 40°C, this type of internal processing allows you to increase the temperature.
3DN: Do you think users are aware of the dangers of 3D printing?
We did a little research on this topic, and according to our results, half of the users are not aware of the risks. Both professionals and novices are aware of bad odor and irritation after a few uses. The adoption of security measures is not yet automatic. However, some of them believe that the use of PLA is enough to protect against toxic emissions. Although PLA is less harmful than other thermoplastics, it does contain additives to improve certain performance and technical properties. Therefore, it can be toxic. One of Alveo3D's mission is to provide information about security risks and best practices.
3DN: What are the future projects of Alveo3D?
We have several areas of development for the coming months. By the end of July we will be able to deliver our first V2 e-cards. They are used to monitor filter housings and monitor filter wear. We are also preparing a model specially designed for companies, alveoONE PRO. This will be a filtration system capable of handling the air of two printers at the same time, or a high volume printer with individually tested and certified filters.
3DN: A few words for our readers?
Basically we have a few more agreed projects for the future. But we must also monitor current demand and developments for 2020. You can find our various solutions on our website HERE.
4/
STL file Filter system for 3D printer body・Model for download and 3D printing・Cults
8-bit star
1.25 €
Festive decoration 8-bit star
1.25 €
The best files for 3D printers in the Tools category
3D SCAN STAND
2 €
UP! / Afinia Filament Guide
Free
Pocket Tapping Handle
Free
Simple Spool Holder for Printrbot Metal
Free
Tool Organizer
Free
Vernier - Pie de Rey - Rule
Free
Kate Brush | ergonomic handles for brushes
Free
Raspberry Pi 2 Cover
Free
Bestsellers in the Tools category
Paint stand with scissors
5,30 €
Display holder FLSUN v400
€4. 99
UNIVERSAL BED LEVELING INDICATOR FOR VERY ALL PRINTERS
2,87 €
Grinder | Grinder
€1.50
Rapid print paint bottle rack (6 sizes)
€2.91
Cooling system Minimus Hotend
€2.38 -thirty% 1.67 €
Ender 3, 3 V2, 3 pro, 3 max, double 40 mm axial fan hot end duct / fang. CR-10, Micro Swiss direct drive and bowden compatible. No support required for printing
1.62 €
telephone ring holder
0.90 €
PRECISE DIAL INDICATOR 3D PRINT DIY
1,90 €
Quick print stackable parts containers / storage boxes
2. 91 €
well designed: Hemera fan duct
2.50 €
ARTEMIS -> Shop for Alligator 2 || 6.5" Arrows || Repeating Crossbow
€6.25
Cut-Man - PET bottle cutter with handle!
€3.49
PET-Machine, make your own plastic bottle filament at home!
15 €
SUPERBOX
1,50 €
Business card embossing system
3 €
Do you want to support Cults?
Do you like Cults and want to help us continue our journey on our own ? Please note that we are a small team of 3 people, so it is very easy to support us in maintaining activities and creating future developments.